
4 minute read
World-class cleanroom solutions Dagard
WORLD-CLASS CLEANROOM SOLUTIONS
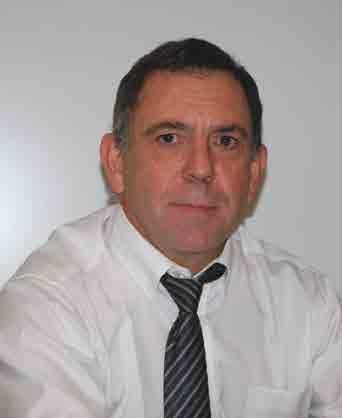
The French company Dagard designs, manufactures, installs and maintains cleanrooms, walk-in cold rooms, and insulated constructions for customers from leading universities, general research laboratories, biotechnology, microelectronics and pharmaceutical companies. Marco Siebel spoke to Marketing Director Daniel Quinet about the latest developments and expectations for the future.
Dagard, founded in 1951, offers total cleanroom solutions - from conception to completion. The company has two production plants based in France, with 400 employees.
Daniel Quinet: “Turnover for 2013 was 72 million Euro, and we expect that number to reach between 85 and 90 million Euro within the next three years. Sales of clean rooms and walk-in cold rooms are responsible for 30 per cent each, with sales of insulated constructions responsible for the remaining 40 per cent.”
Dagard has customers in the USA, Australia, Singapore, Russia, Germany and the Middle-East.
Daniel Quinet: “We see a lot of potential in the French speaking countries on the African continent. 18 per cent of turnover is generated by sales outside of France, and we expect that number to rise to between 20 and 25 per cent within the next three years.”
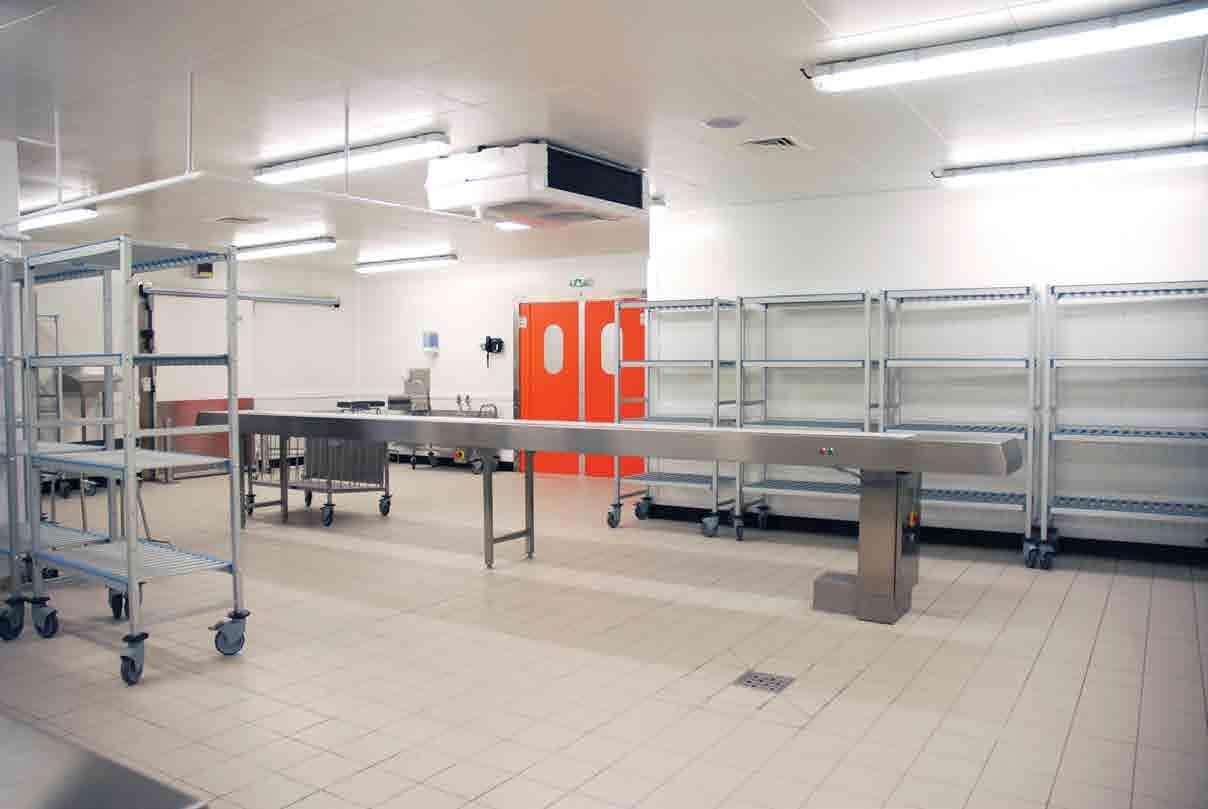
In-house design & production
Dagard’s R&D team designs generic or new innovative products and gears them up for production in one of the two factories that offer large production capacities with the necessary flexibility for each project: continuous and discontinuous production lines for panels, high precision sheet metal working, multi-purpose industrial joinery, machining, material assembling (steel, aluminium, PVC, HPL, glass), welding and painting workshops for steel and stainless steel.
Once production is completed, a team travels to the client’s site to install the cleanrooms or other constructions.
Daniel Quinet: “We have sales teams in the USA, Australia, Russia, on the African continent and in Europe. We send out our construction teams systematically to our clients’ production sites to ensure all safety regulations and quality measures are met, and that the final product can be handed over to our client with the guarantee that it will surpass all expectations. We provide a consultancy and assistance service throughout the warranty period and for the lifespan of an installation. We assist in the maintenance of the serviceability of an installation with spare parts, and can provide preventive maintenance and repair services.”
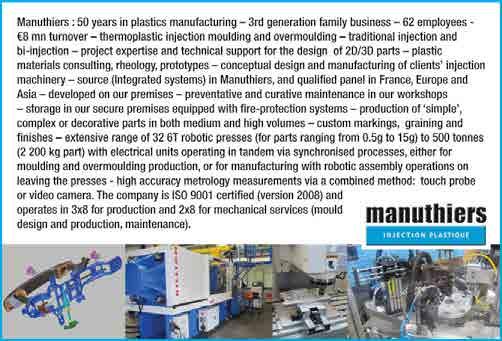
Sustainable development
The expansion agents used by the company for insulating foams are CFC-free and HCFC-free in compliance with the Kyoto Protocol to limit greenhouse gases. Dagard uses 100 per cent organic mineral wool that is made up of fibres classified as non-carcinogenic by the World Health Organization. Mineral wool scraps, pallets, and film are 100 per cent recycled, while the steel being used, from the recycling
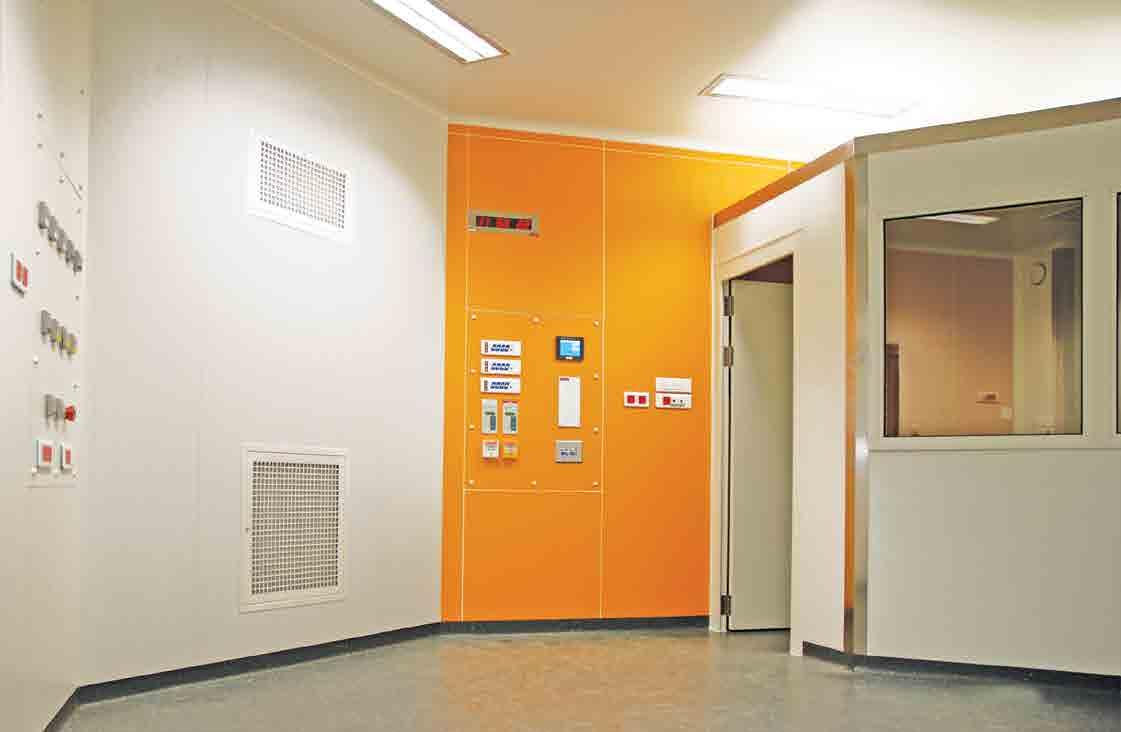
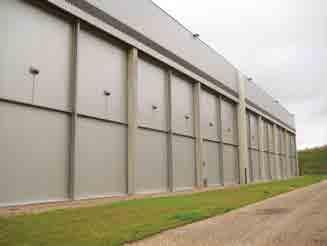
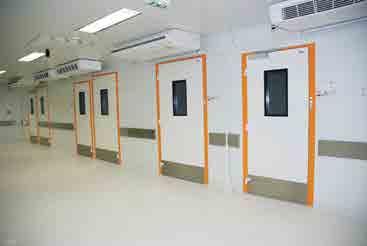

aspect and its impact on the greenhouse gas emissions inventory, is one of the most efficiently reprocessed products.
Dagard’s system of project management and close relations between production, engineering and installation departments allows optimal consumption of materials and recycling of products not used during installation.
Daniel Quinet: “A series of in-factory and on-site procedures is designed to keep the impact of company activities on the environment to a minimum: selection of materials, selection of low energy and water consumption industrial processes, use of limited quantities of non-polluting consumables, optimization of packaging materials, selective sorting of all waste, special procedures for rerouting discards and chips to authorized suppliers and processing plants. We also invest a lot of time in training programmes for our employees, in preventive safety programmes and site cleanliness verifications and culture of environment friendliness.”
Cleanrooms and cold rooms
Cleanroom technology is used in many sectors: production and packaging of drugs and cosmetics, in the nuclear industry and the aerospace industry, high tech technologies industries, in the healthcare sector, in operating theatres and surgical units, data centres, in bio-safety laboratories (P3, P4) and research laboratories...
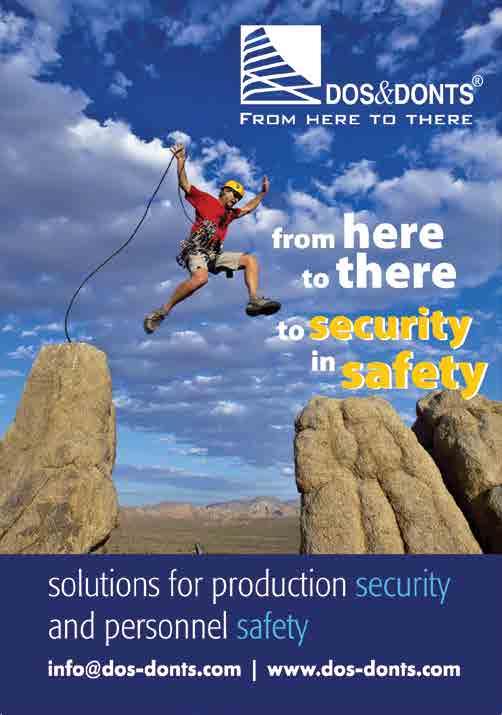
Based on the concept of modular sandwich panels, Dagard has developed airtight envelop system (walls, ceilings, doors and accessories) which, combined with efficient air treatment solutions, allows the construction of cleanrooms of any class.
Frigorific cells and modular cold rooms are used in the kitchens of restaurants , delicatessens, bakery, pastry and catering, preparation units, by florists to preserve flowers, in supermarkets and grocery stores. These refrigerating cells and cold rooms are made of insulating sandwich panels with camlocks, associated with a wide range of doors: insulated hinged doors, insulated sliding doors, glass doors, service doors, swing doors.
Insulated constructions
Based on the sandwich panel concept, Dagard designs, manufactures and installs insulated and/or fire resistant partitions and ceilings, as well as insulated and fire resistant doors. These products are intended for processing laboratories, butchers’ workshops, delicatessen, catering, cold stores, warehouses, commercial kitchens, central kitchens.
Daniel Quinet: “As we continue to expand our activities overseas, especially in the USA and in the French speaking countries on the African continent, we are determined to maintain the reputation of our brand name. We aim to keep our product range and production system as flexible as possible so that we can offer custom made cleanroom and cold room solutions to our customers the world over.” n
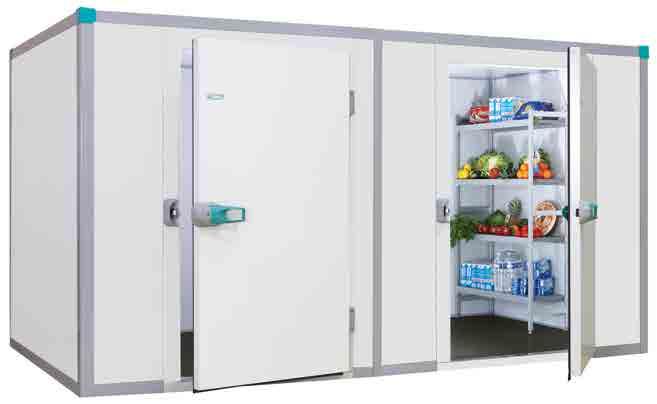
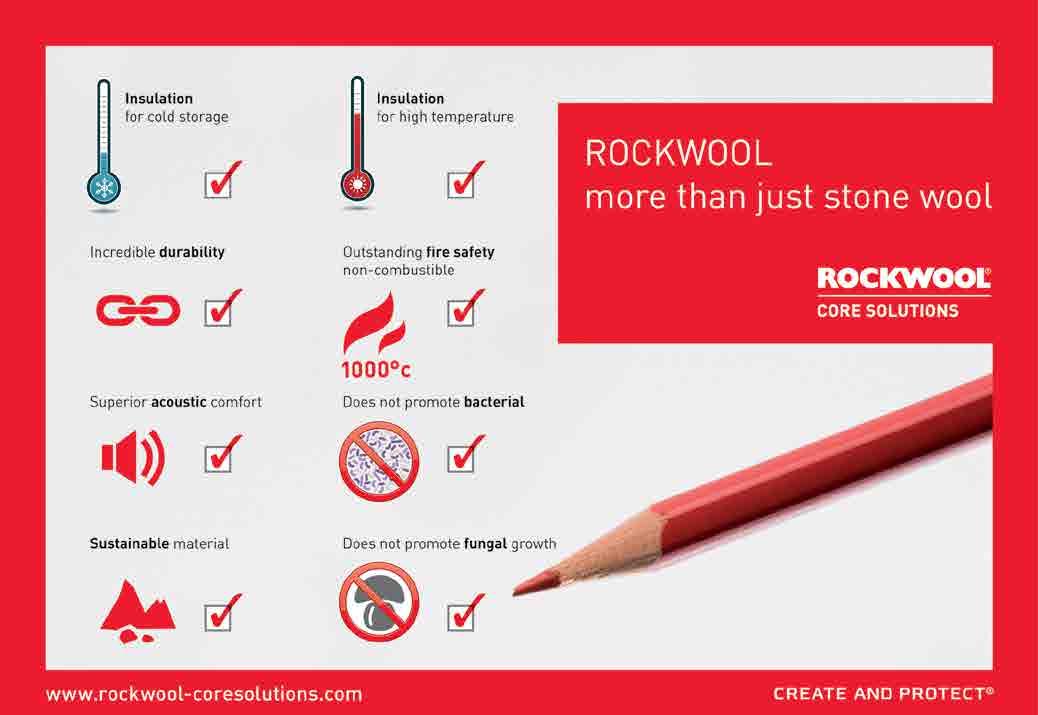