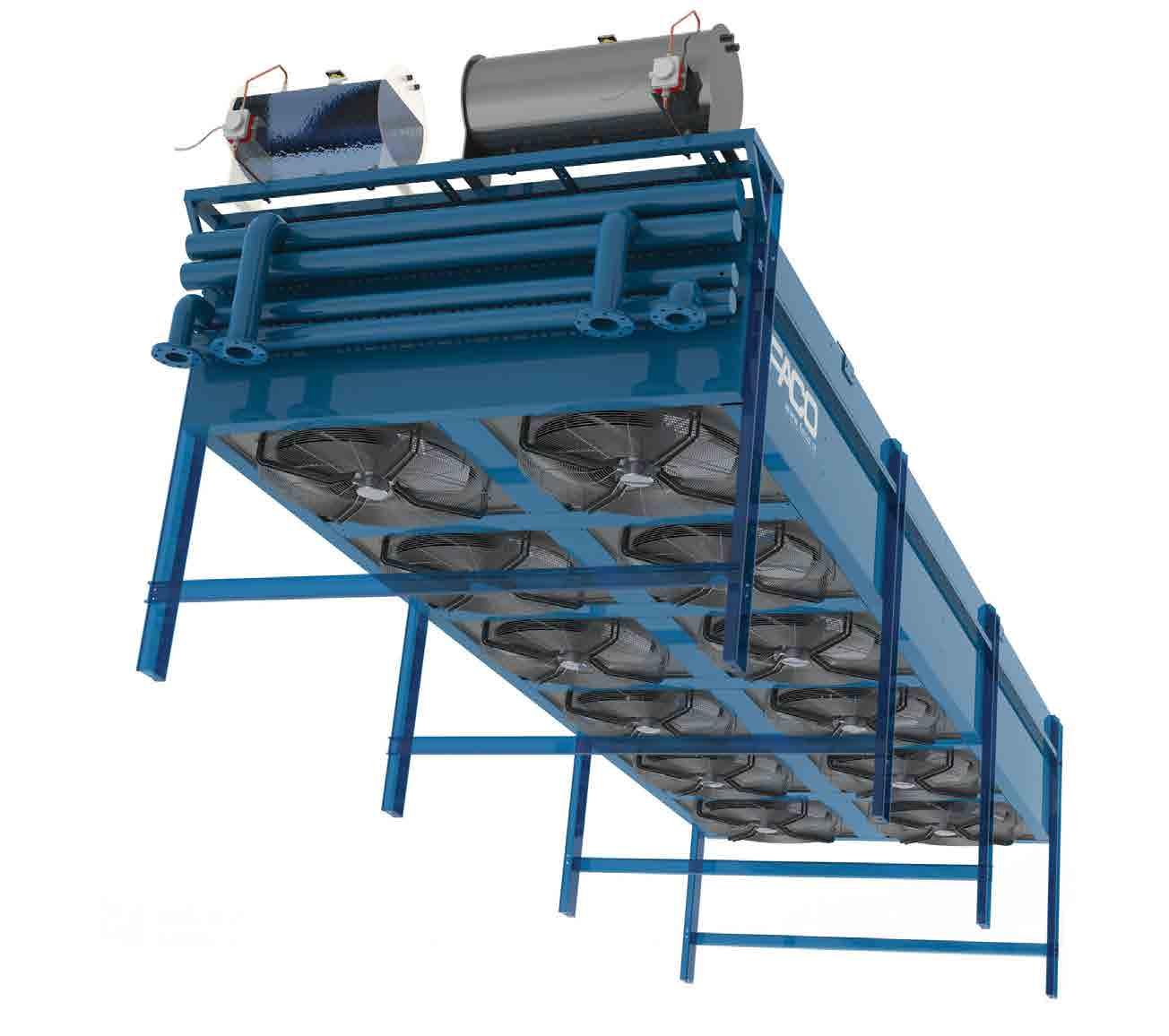
7 minute read
Taking the heat off Faco
TAKING THE HEAT OFF
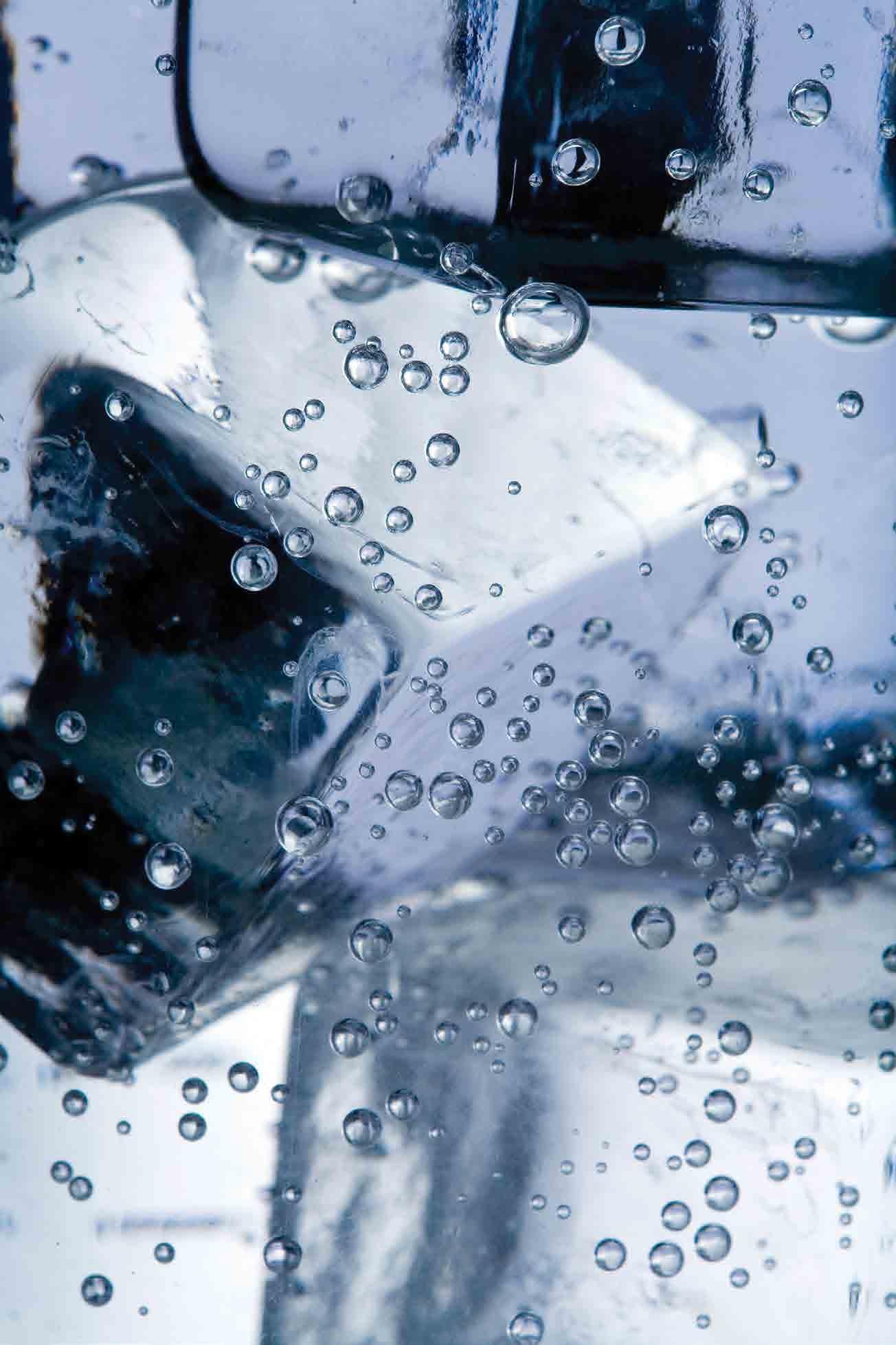
Faco celebrated its fiftieth birthday in 2013. In her conversation with Mr Marco Dalla Rosa (board member) and Mr Mario Manfredi (technical and commercial director), Barbara Rossi learns how the company is increasingly shifting its focus from individual heat exchangers to more comprehensive systems (dry cooling and condensing solutions).
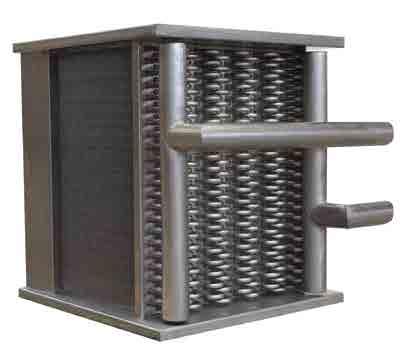
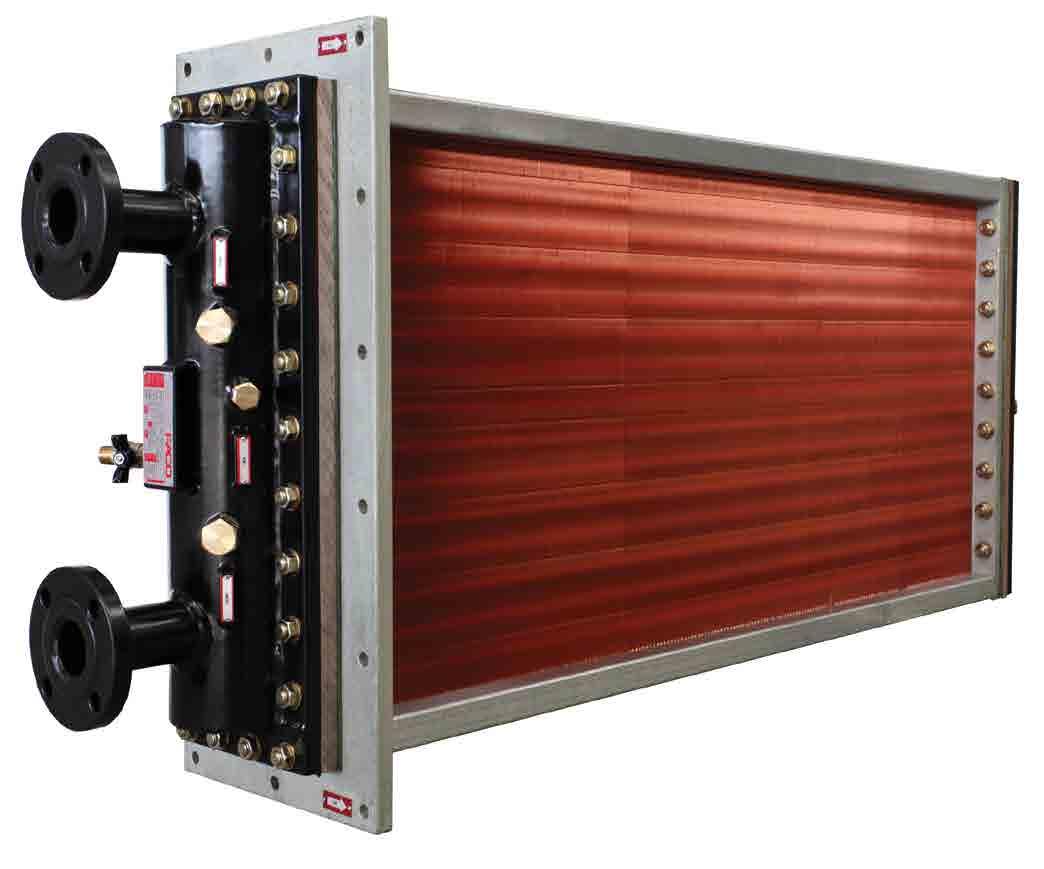

Faco is based in the Novara area of north-western Italy, very close to the border with Lombardy and within easy reach of Milan (about one hour’s drive). It designs and manufactures highly customised solutions for any heat transfer, heat recovery or cooling process application. Its range of products includes both individual heat exchangers for HVAC and industrial use and dry coolers and condensers. It also offers an engineering service, carrying out thermodynamic design, as well as fluid dynamic and noise analyses.
“We started as a family company set up by my uncle and my father in 1963, making heat exchangers, first for comfort applications and then also for industrial and naval use,” Mr Dalla Rosa explains. “We have always offered products with a customised design, increasingly so over time, and have always regarded research and development as being vital to our success. This is proven by the fact that we started employing IT systems at the end of the 1960s, when not many companies did. I believe that our will to be at the forefront of innovation is one of our main distinguishing features, underlying our success. We are still a family company, led by both members of the founding family and externally recruited managers.
“Heat exchangers are still at the foundation of what we do, even if over the years we have widened our offer range with additions in terms of materials, treatments and a new line for what we call ‘our machines’ (i.e dry cooling and condensing solutions, incorporating heat exchangers as well). We operate from our 12,000m2 site and employ a team of 180 staff.” The company supplies solutions for applications in a wide range of industries, including HVAC, heat recovery, industrial cooling, chemical and petrochemical, pharmaceutical, food, shipbuilding (military, civil and off-shore), electro-mechanics, electronics and e-microelectronics, cogeneration and power units, steel, paper and textile.
A unique laboratory
The company is equipped with its own laboratory for thermodynamic research, designed and run according to ASHRAE standards. “For each type of heat exchanger and combination of materials, we measure all actual thermodynamic parameters, which are then used in Faco’s proprietary selection software packages. This is a unique facility for a private company.” As part of its R&D facilities, Faco also has available an array of software and internal resources for fluid dynamics simulation, for finite element structural analysis, as well as predictive evaluation and measurement of noise and vibrations. Modelling tools and laboratory testing work complement each other, with mathematical modelling being followed by product testing in the lab. “In this way our products arrive at the homologation phase, obviously still carried out by independent third parties, with a head start.” Faco holds a number of certifications, including ISO9001, AHRI (Air Conditioning, Heating & Refrigeration Institute), ASME VIII, ASME IX, EN 287, EN 15614, EN 13585 and EN 13134. In addition to these, the company complies with all relevant EC directives.
“We have had our laboratory since the beginning and we have continuously improved it over the years. Now we are revamping it, because research is very important for us. In addition to this we are modernising our machinery as well as making commercial investments for further penetration of new and emerging markets,” Mr Manfredi explains.
“While we intend to carry on offering our whole range, we have increasingly focused on ‘our machines’ and on heavier industrial and energy applications. For instance, for many years now we have been developing
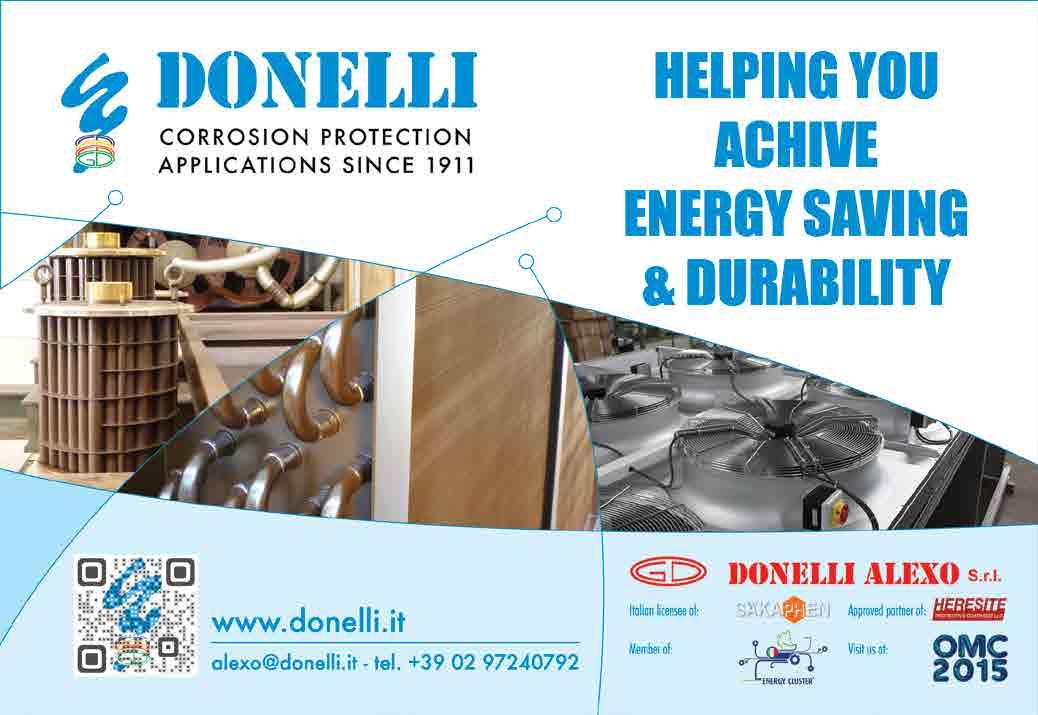

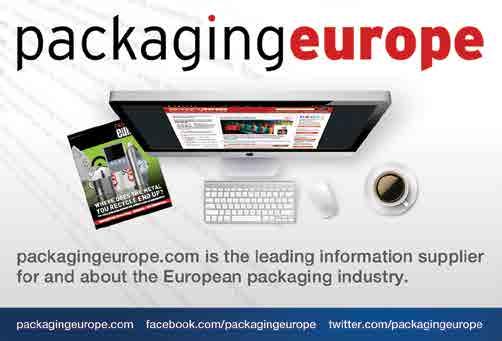
Donelli Alexo
Anticorrosion coating applications since 1911
Donelli Alexo, part of Donelli Group (est. 1911), is dedicated to meeting the most demanding anticorrosion, fireproofing and insulation needs of energy, chemical, onshore and offshore Oil&Gas facilities.
Specialized in shop and on-site HVAC/R services include: • Anticorrosion & antibacterial coating of finned pack heat exchangers with Heresite and other technologies leading to energy saving; • Casing, piping, skid, and vents coating in accordance with ISO 12944 and all major end user/engineering specification; • Shell&tube lining and tubesheet rehabilitation with Säkaphen technologies; • Heat exchangers maintenance and environmentally friendly cleaning; • Consulting services including failure analysis, customized testing and joint development programs.
Trained and experienced personnel, certified NACE/FROSIO/ACQPA inspectors, state-of-the-art painting shops in Italy and efficient equipment to operate Europe-wide at clients’ facilities represent distinctive factors. These ensure schedule fulfilment and compliance with environmental, qualitative and safety standards (i.e. Norsok, Total, EDF, Saudi Aramco, GE, Petrobras, ENI, etc…).

solutions for nuclear power station applications and have supplied heat exchangers to various plants around Europe. We have also developed many applications for the naval field, in terms of heat exchangers both for comfort and for the engine room.
“In terms of new products I would point to our SmartBox modules, designed for containerised installation. In fact, SmartBox is an extremely compact module that can be installed at one end of the container, composed of heat exchangers covering the full height of three sides and fans flushmounted on the upper panel. A dual section version of SmartBox is also available for cooling two separate circuits, such as the water jacket and the after-cooler.”
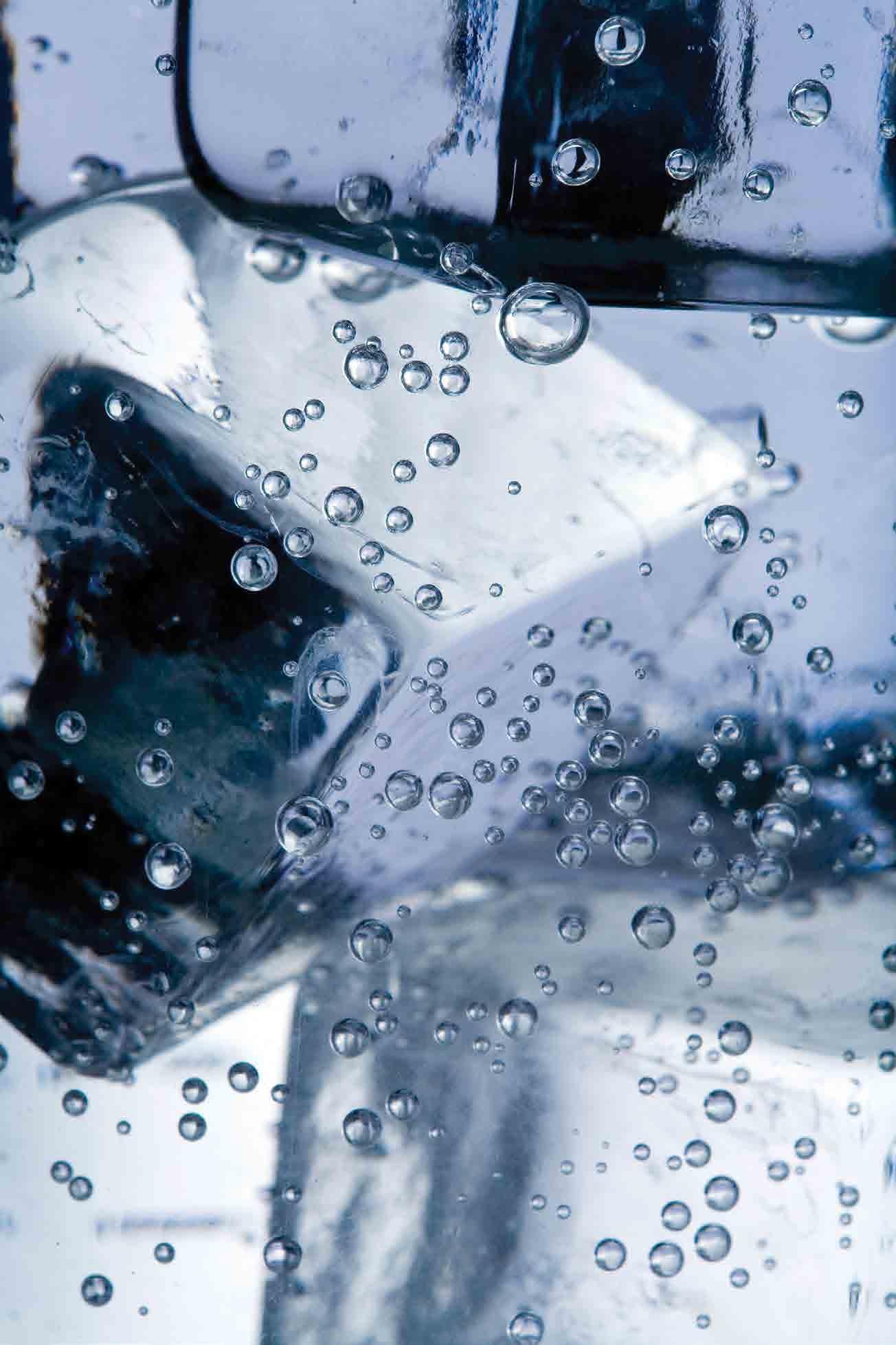
Consolidating markets
Export has had an extremely important role for the last fifteen to twenty years and today amounts to 85 per cent of the company’s output, mainly sold in Europe, Asia and Africa. Western Europe is an important, consolidated market, where Faco carries out weekly deliveries and where Germany features very highly. Western Europe is followed by Russia, the Middle East and North Africa. “We tend to serve our consolidated markets through our commercial network, while supplying new countries directly. Even in Western Europe we supply directly when we deal with more complex products,” Mr Manfredi adds.
While Faco’s aim is to sell its whole range in all of its markets, realistically it knows that most of its sales in emerging countries are centred around its more value-added products, which local competitors are not able to manufacture to the same standard. “Europe and Italy are still centres of excellence in this field. We receive requests from all over the world and, while other markets have been growing rapidly, albeit unevenly (often linked to important but transient local projects, such as the Sochi Olympic Games or the construction of a chemical plant in the Middle East), Europe still plays a predominant and reliable role. We have to consolidate our presence on our existing markets and start distributing in the Far East.”
Mr Dalla Rosa stressed how, as well as organic expansion, acquisitions could be part of the future growth strategy, although nothing of this sort is in the pipeline at present. “It could be an interesting idea, especially so as to be able to produce products in close proximity to their outlet markets. However, even if we were to pursue this strategy, we would certainly maintain all of our highly specialised production here in Italy, because we want to maintain our excellence, which is only achievable with the staff and technology that we have here. Also, any possible future foreign production would be for the sole purpose of serving local markets. Delocalisation is not something that we are interested in.”
The relationships created with its suppliers, based on collaboration aimed at fulfilling new emerging product requirements, are vital to the company. This is particularly important because Faco is continuously expanding the boundaries of the applications that it supplies. Mr Dalla Rosa concludes. “The chemical and oil and gas industries for instance are sectors that we have started supplying recently, as is offshore. We are increasingly moving towards the supply of whole systems, bypassing integrators, rather than selling individual heat exchangers.” n
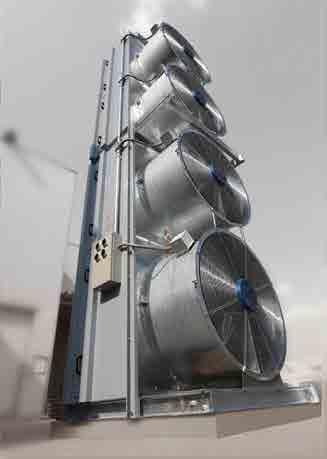