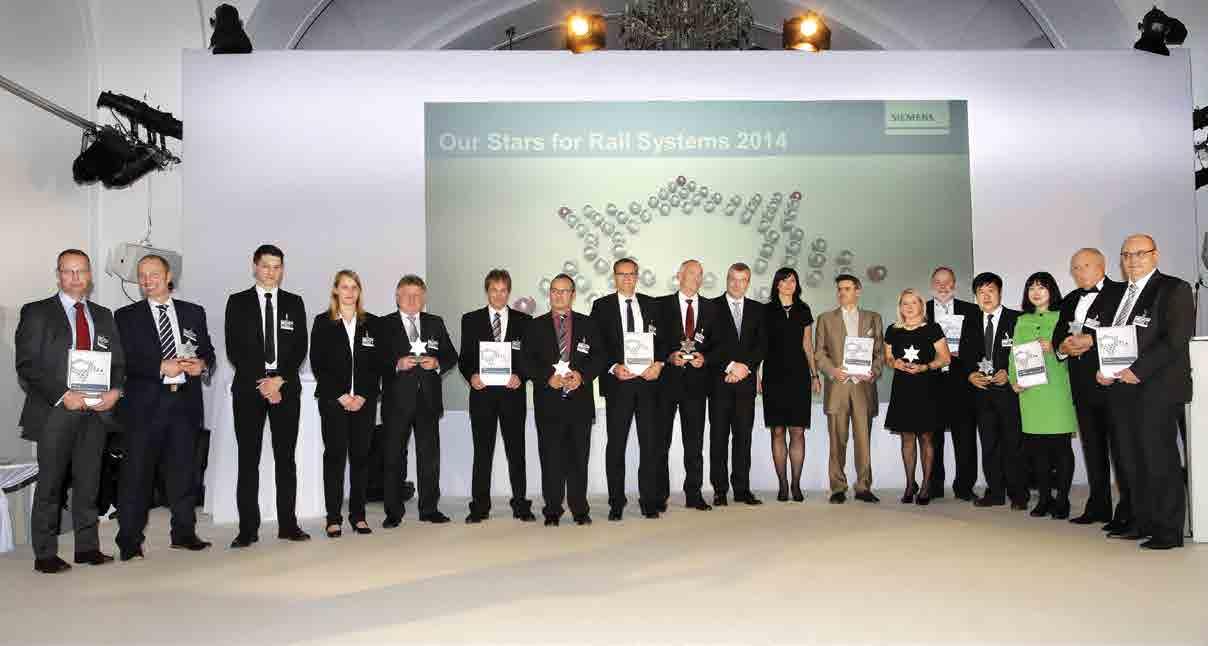
7 minute read
Fast-track to efficiency Siemens Rail
FAST-TRACK TO EFFICIENCY
The Siemens Rail Systems Division is a leading international provider of rail vehicles and related services. The company’s portfolio comprises the entire spectrum of railway rolling stock including the manufacture of advanced high-speed railway trains. Philip Yorke looks at the global company’s three business units and its latest news stories. These include the prestige Thameslink Programme, its major railway train contract in Finland and its ‘Stars for Rail Systems’ supplier awards event.
Siemens Rail Systems Division is subdivided into three business units. The company’s High-Speed and Commuter Rail unit based in Krefeld, focuses on the manufacture of intercity and high-speed trains, while in Vienna, the Urban Transport unit manages all of Siemens’ business activities in the fields of metro trains, trams, light rail vehicles, passenger coaches and mass transit vehicles for driverless operation. The company’s Locomotives and Components unit is based in Munich-Allach and is responsible for all locomotive traction units and components.
However, there is yet another support division, which is known as the Customer Service Unit which offers customers a range of infrastructure services spanning the entire lifecycle of a rail system. Siemens is also the world’s leading provider of eco-friendly technology whose sophisticated products and solutions have enabled its customers to save more than 320 million tons of carbon dioxide (CO2) in 2013. This amount corre-
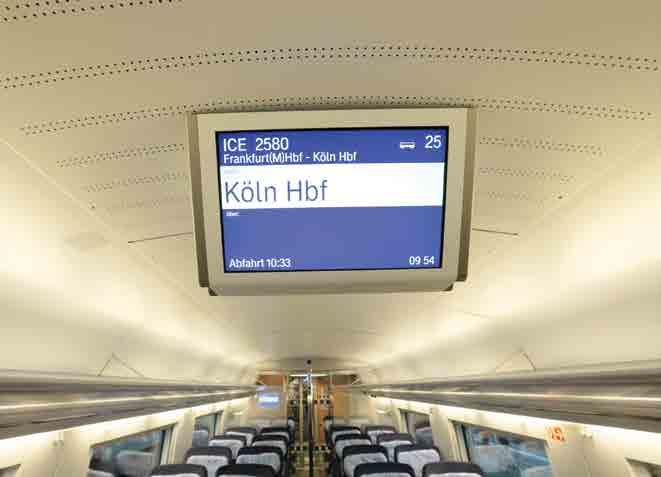
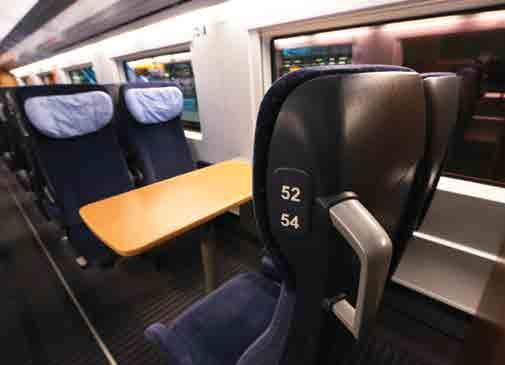
sponds to the total CO2 emissions produced by many of the world’s most populated cities combined.
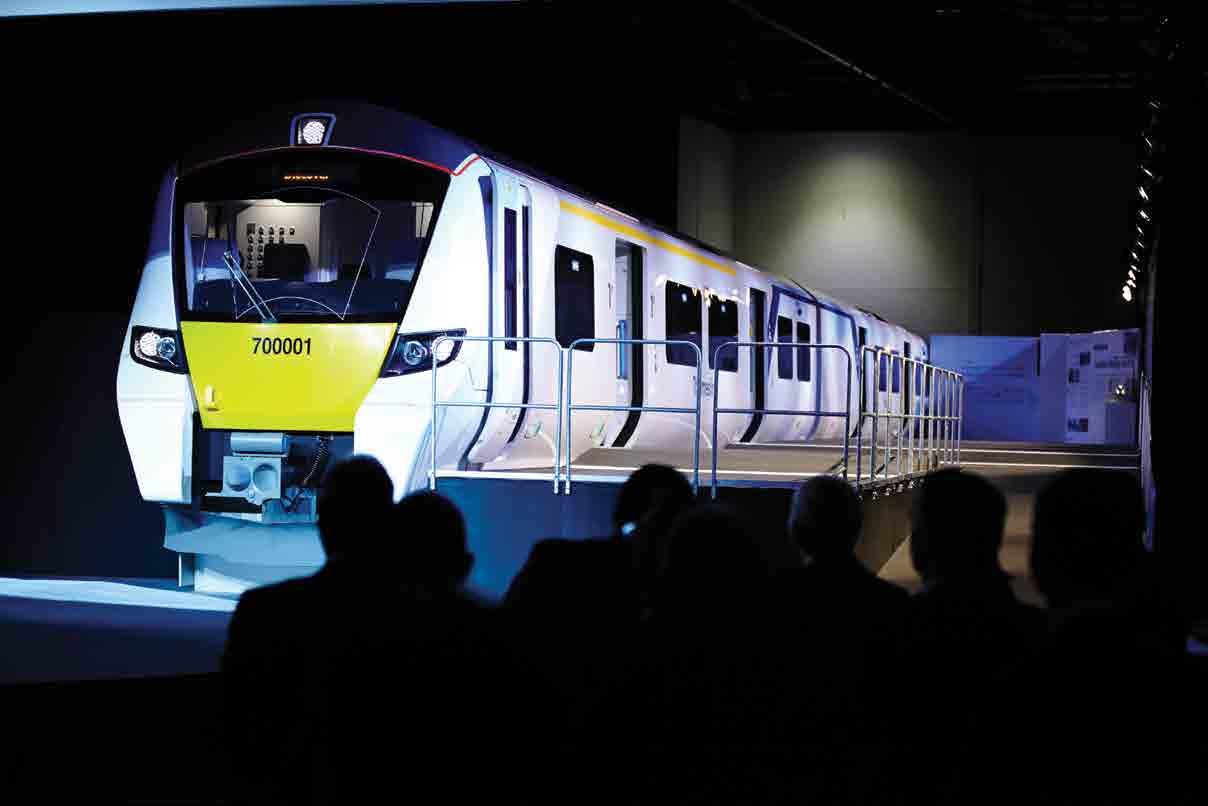
Leading in light rail vehicles
Siemens is the market leader in the supply of light rail vehicles (LRVs) in North America, having built more than 1000 rail vehicles for 17 cities in the USA and Canada. One in every three light rail vehicles in North America is a Siemens vehicle. These advanced vehicles are built at the Siemens state-ofthe-art facility in Sacramento, California. This is the only permanent light rail manufacturing plant in the USA. Having provided vehicles for the North American market since 1975, the company has constructed a new assembly facility in South Sacramento in 1992, and a further $10 million facility was added three years later. Today Siemens produces the S70 vehicle family, developed especially for the American market. With its low-floor construction and optimal passenger comfort and flow, it also offers the higher safety standards imposed on mixed traffic and main railway lines.
Desiro-City success
Siemens recently secured its biggest single contract in the UK market for its Desiro–City trains and maintenance depots for the prestige Thames link north-south commuter link. The €1.8 billion order is for the supply of 1140 new commuter rail carriages and for the long-term maintenance of the fleet. “The order is an impressive reminder of our leading position in the British rail market, where we enjoy an excellent reputation. Our commuter trains are seen as the most reliable in the country. Annually more than 350 trains travel over 80 million kilometres in Great Britain each year,” says Jochen Eickholt, CEO of Siemens Rail Systems.
For the Thameslink project, Siemens invested around €50 million in the development of a new train platform. The new Desiro City for suburban, regional and main line transport reduces overall energy consumption and track wear by up to 50 per cent compared to its predecessors.
It is not only in the UK that Siemens is able to win major contracts. In Finland the Finish State Railways placed an order worth more than €300 million for an additional 80 locomotives including maintenance. In addition there is an option for a further 97 locomotives. This was the first order placed for the new Vectron broad gauge version. The all-new locomotives are designed to operate reliably even under extreme climatic conditions in Scandinavia in their long service life. “The selection was made after long and careful examination, and the electric locomotive manufactured by Siemens is well suited to the challenging conditions in Finland,” said VR Group’s president and CEO Mikael Aro.
Authorisation for the new Vectron locomotives, which are based on a technical
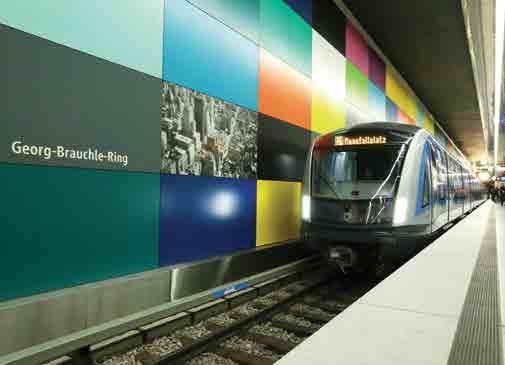
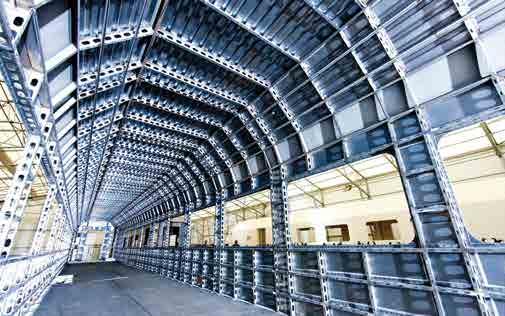
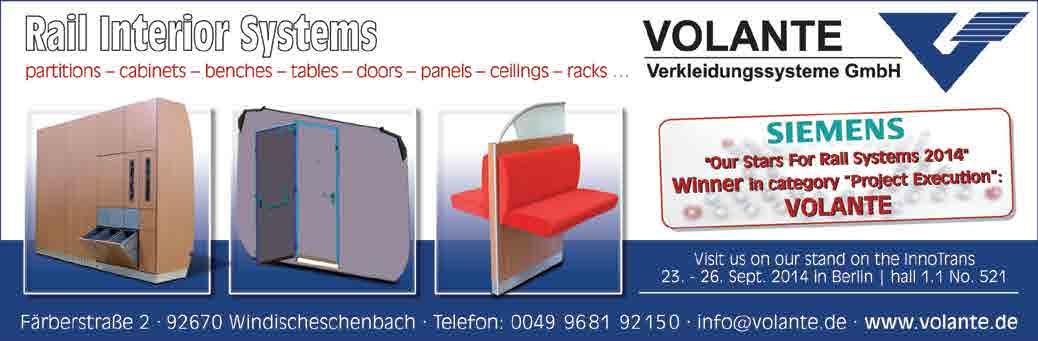

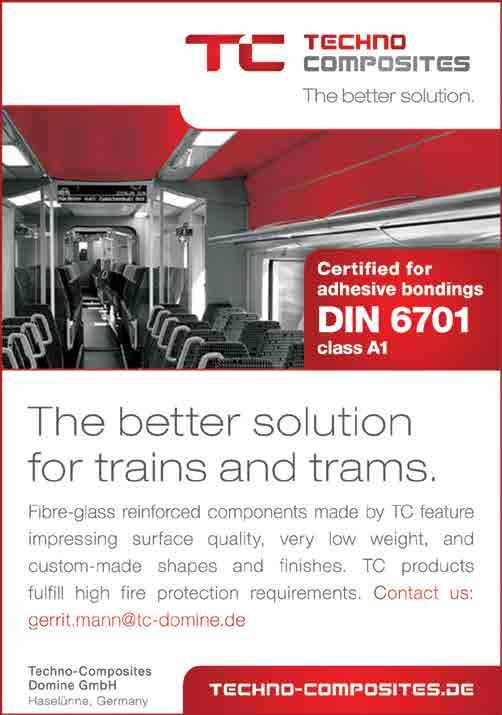
Glas Trösch AG Rail: Winner of the “STAR” in interior category from Siemens in 2014
Glas Trösch AG Rail has been nominated by Siemens Rail System Division as best supplier for the third time. After 2012 we were again awarded a “STAR” for the best supplier in the category “Interior”.
Besides outstanding quality and reliability, product innovation plays a significant role for our company. Thanks to our company-owned developmental team, motivated staff and state-of-the-art manufacturing facilities, Glas Trösch AG Rail counts as one of the most competent suppliers worldwide in the field of high-end windscreens and cabin glazing for the most important train manufacturers.

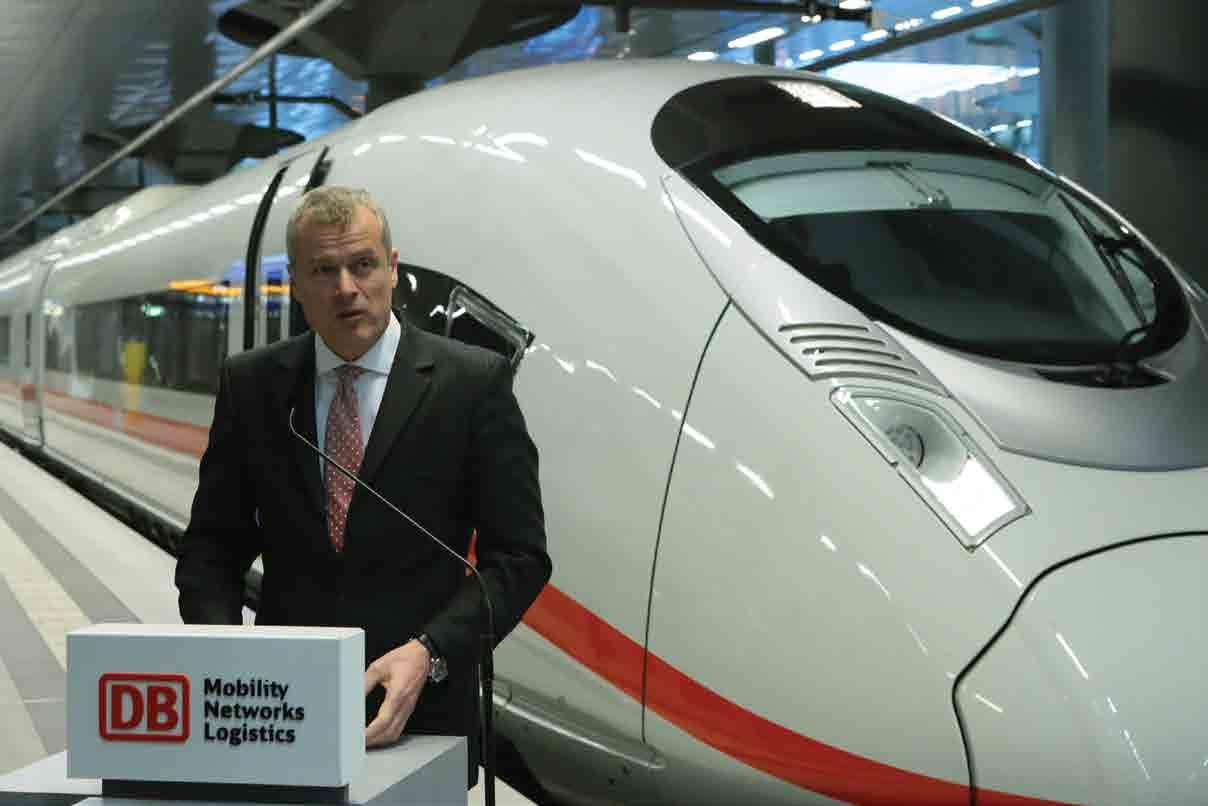

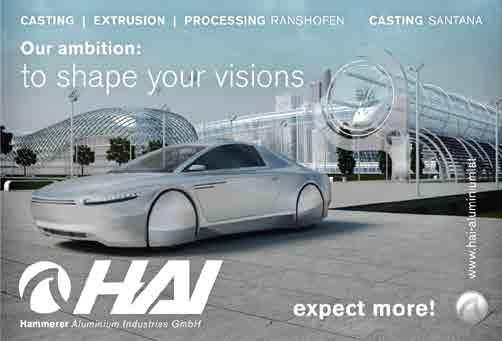
platform, have already been granted for Germany, Austria, Hungary, Poland, Romania and Sweden.
Latest simulation technology
The Siemens Vectron bogies are developed and manufactured in Graz, Austria. This is the world’s leading centre for bogie technology and one of the largest production facilities in the world for railway bogies. The units manufactured at Graz are installed in metros, trams, train-sets, high-speed trains and locomotives. The complete development expertise for bogies is concentrated at Graz where the latest simulation technology is used in product development. Among the
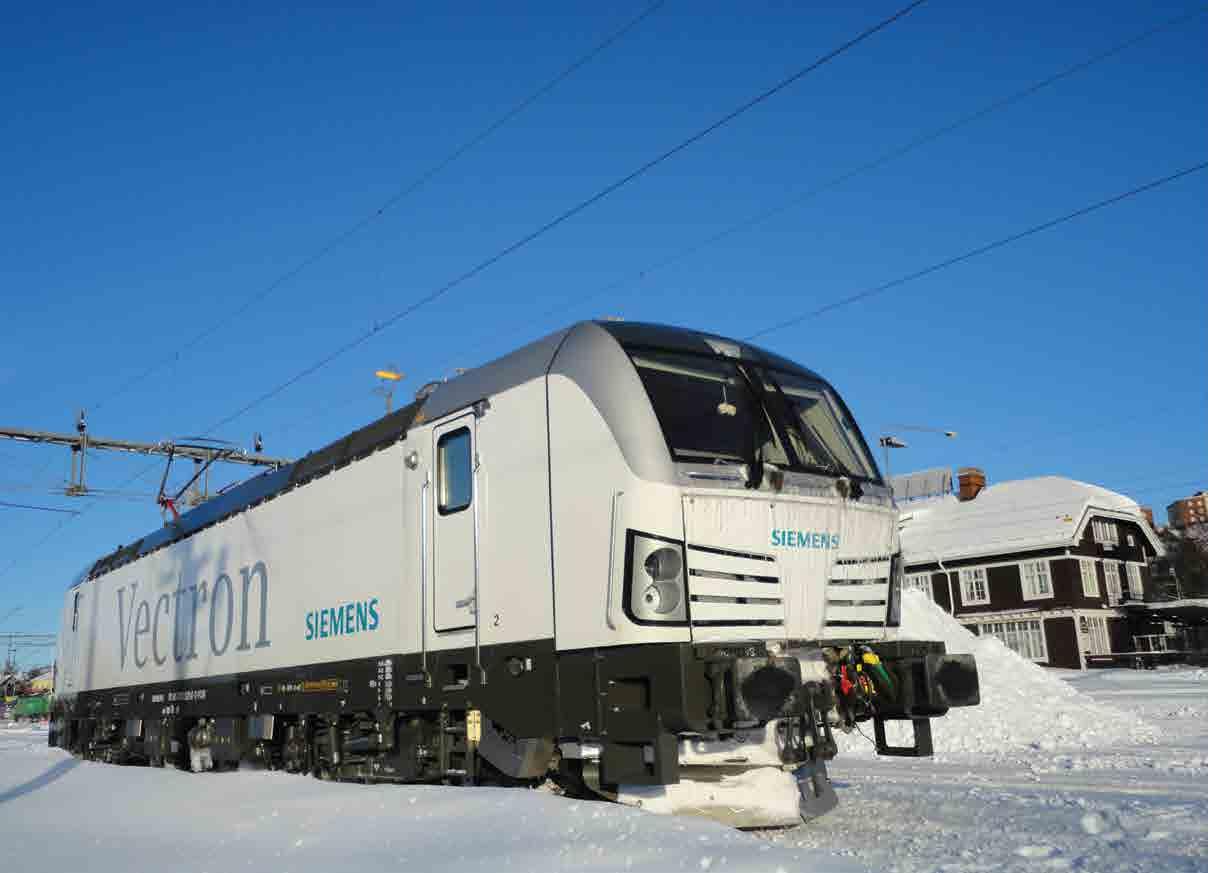
simulations performed are those for riding stability, safety against derailment, clearance requirements and wheel and rail loading. Strength calculations support the overall development process, and production and robotic systems are also simulated and optimised early in the construction phase.
The Graz plant covers a total area of 70,000m2 with production facilities and buildings occupying over 46,000m2. At Graz the emphasis is on car body construction, mechanical processing, painting and assembly.
Rising Stars
At Siemens, suppliers who provide consistent, dedicated and innovative services are recognised and rewarded when it comes to the placing of future orders and are entered into the company’s special competition: ‘Our Stars for Rail Systems’. The winners of this prized ‘seal of excellence’ are selected from seven different categories and are subsequently presented with an award at an exclusive prize giving event.
The seven categories are: carbody, interior, drive/brake, control and communication, services and project execution. On 25 March this year the following winners were announced: Jilin Midas Aluminium Industries Co for Carbody, Glas Trosch AG Rail, for interior, SKF Osterreich AG for drive/brakes, and Bachleitner & Heugel Elektronik OHG, for communications and control.
In addition, the following companies were also awarded stars: MTM Power Messtechnik Mellenbach GmbH for commodity parts, 1st in rail Ltd for service and Volante Verkleidungssysteme GmbH for Project Execution. Other nominees included K-Supra s.r.o., Hammerer Aluminium Industries GmbH, Techno-Composites Domine GmbH, Satek GmbH, Televic Rail NV, Lütze Transportation GmbH, PMA Deutschland GmbH, Sika Deutschland GmbH, PCS Power Converter Solutions GmbH, HOPPECKE Batterien GmbH & Co. KG, Zonegreen Ltd and Tiekra Service GmbH. The nominees are selected by a jury composed of representatives from Siemens Rail Systems management, strategic purchasing and the company’s other relevant business units.
Demand grows for Velaro high-speed trains
The Volaro high-speed train from Siemens is the most successful in the world, with more than 160 trains in operation globally. Not only does this advanced train minimise operating and maintenance costs, but emissions are also extremely low in relation to the high transport capacity. The Velaro D is aerodynamically optimised and a fully elevated roof section reduces the sonic boom in tunnels. Energy efficiency is also enhanced by the feeding of surplus braking energy back into the power grid.
The German Railway (Deutsche Bahn) has already taken delivery of 15 eight-car high-speed trains from Siemens. The company has been providing comprehensive expertise in project management for projects such as this for more than 160 years.
Predictive maintenance
Siemens trains are the most reliable in the United Kingdom thanks to the predictive maintenance carried out at the company’s facility at Kings Heath, Northampton. If train components are continuously monitored and sources of errors are eliminated at an early stage, then rolling stock can achieve close to 100 per cent reliability. The status of each of the 74 multipleunit trains serviced by more than 100 employees not only keep the 67 Desiro UK trains in good condition around the clock, but they also maintain seven 25-year-old English multiple train units. In the UK, predictive maintenance is a common method of achieving availability rates of approximately 99 per cent in spite of the complex structure of rail operators, leasing companies and repair shops.
The UK’s regional trains manufactured at the Krefeld-Eurdingen plant in Germany are serviced and repaired in ten British depots including the UK’s biggest depot at Kings Heath, Northampton. n
For further details of Siemens Rail Systems and services visit: www.siemens.com