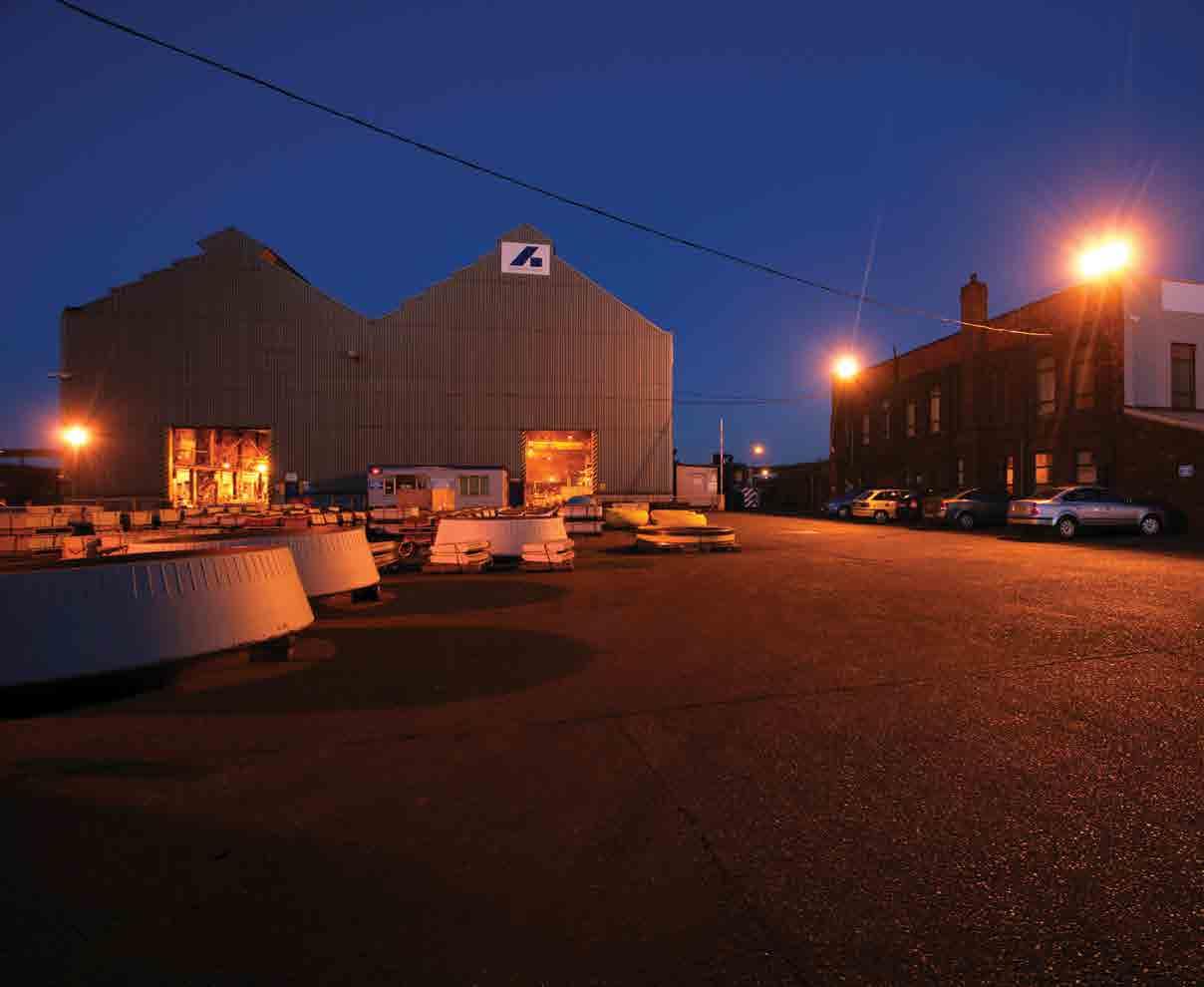
8 minute read
Consumables with a difference Bradken
CONSUMABLES WITH A DIFFERENCE
With a presence across five continents, Australia based heavy engineering company Bradken is a leading global manufacturer and supplier of a wide range of cast and fabricated steel products to the mining, transport and general industrial markets. The company’s European operations are based in the United Kingdom, where it operates two foundries. Victoria Hattersley met with the General Manager for Europe, Anthony Rowett, to find out more.
With around 5800 employees worldwide and an annual sales revenue of over AUD$1.31 billion (FY13), Bradken has a long-standing reputation as a global supplier of differentiated consumable products. The company has two core business focuses: a world class range of wear-resistant consumable and capital products designed for the mining and transport industries, and contract manufacturing services capable of producing the most complex engineered steel castings in the world from a weight of 1kg up to 25 tonnes.
But Bradken is more than ‘just’ a manufacturer, it is a solutions provider. The driving force behind the organisation is its firm commitment to innovation and continuous improvement, which ultimately provides customers with value through the creation of customised product solutions.
And it is this innovative ethos that allows Bradken to consistently work with some of the world’s most recognised names from Caterpillar, Rio Tinto and BHP Billiton to FL Smidth, Hitachi and AngloAmerican.
Evolution in the UK
Bradken has a long and proud history. The business, then Bradford Kendall Ltd, was founded in 1922 by two Australian entrepreneurs (Leslie Bradford and Jim Kendall), who used the proceeds of a winning streak at the races to establish their first steel foundry in Sydney.
In 2004, the Company, then under its present name, was listed on the Australian Stock Exchange. Since that time Bradken’s story has been one of continuous success. Its global footprint has expanded through both organic growth and complementary acquisitions (including the purchase of the Atchison/ St Joseph foundry and manufacturing facility in the United States and the Scunthorpe foundry in the UK) in a concentrated effort to globalise its range of products and services.
Today Bradken stands as one of the world’s largest combined foundry and heavy engineering groups with 59 manufacturing, sales and services facilities throughout Australia, New Zealand, China, the USA, Malaysia, South Africa, Indonesia, South America and the UK, giving it a truly international presence.
Bradken’s history of operation in the UK dates back 25 years. When Industry Europe

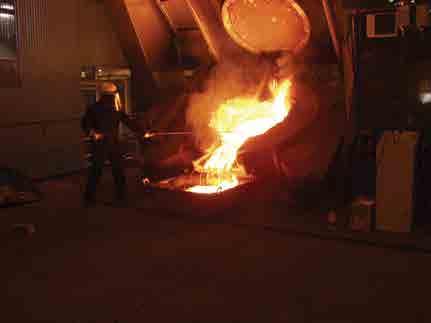


featured the company in its very first edition, the group’s presence in the UK looked very different. At this time it was known as ‘Bradken North British’ and was based in an entirely different foundry in Bathgate, Scotland. This site is now closed.
In 2006, Bradken acquired Firth Rixson Castings Limited with foundries in Scunthorpe and Darleston. These two foundries, in addition to the Bradken’s European Head Office facility in Rotherham (where its design department is also housed) form the core of the company’s current European manufacturing base, servicing clients from all over the continent and beyond.
Bradken’s Scunthorpe foundry, which Industry Europe recently visited, has a history of more than 90 years in casting production. The site operates a continuous improvement programme, as Bradken does at all its facilities, to drive improvement and efficiency. Last year (2013) for example, the company invested over €2 million in a new world-class heat treatment facility at the site resulting in improved safety, product flow and quality outcomes.
Core products and divisions
Two distinct brands operate under the Bradken banner: the Bradken branded company, structured into four discrete divisions (Mining Products, Mineral Processing, Rail and Engineered Products), and the Cast Metal Services business, a supplier of traded and differentiated foundry consumable products and technical expertise to the cast metal industry.
It would be very difficult, if not impossible, to list all the products that Bradken is capable of producing. But it would help to give a general overview of the kinds of solutions it can offer. The Mining Products Division specialises in the design and manufacture of ground-engaging tools, buckets, crawler systems and excavator undercarriage components, and a range of wear-resistant products for fixed and mobile plant.
In the Mineral Processing Division, Bradken is a leading designer, manufacturer and supplier of high-quality grinding mill, crusher and conveying products for the mining and quarrying industries. The Mineral Processing Division also manages and operates a metal recycling business that purchases and processes steel feed for Bradken’s
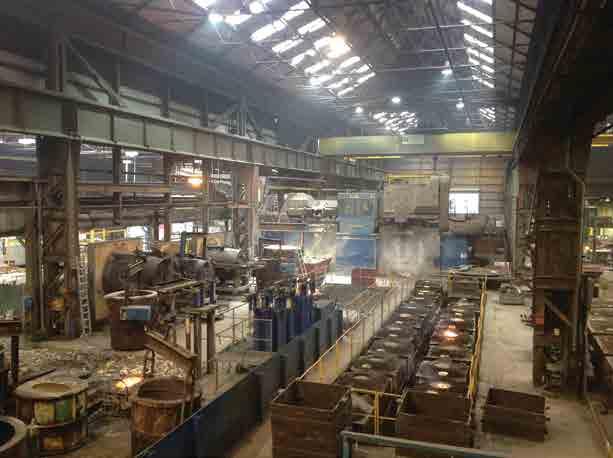
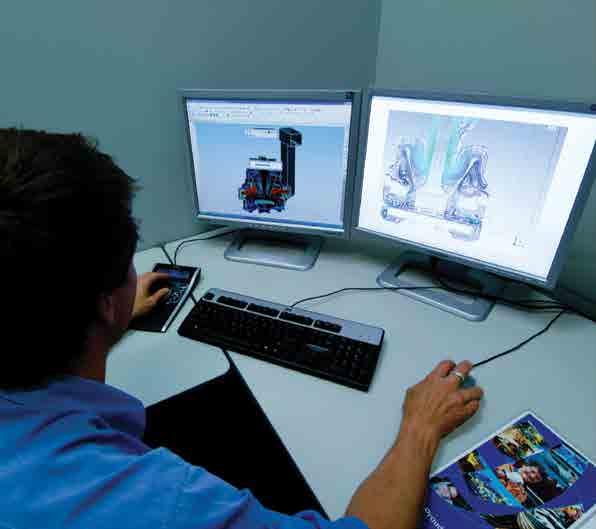
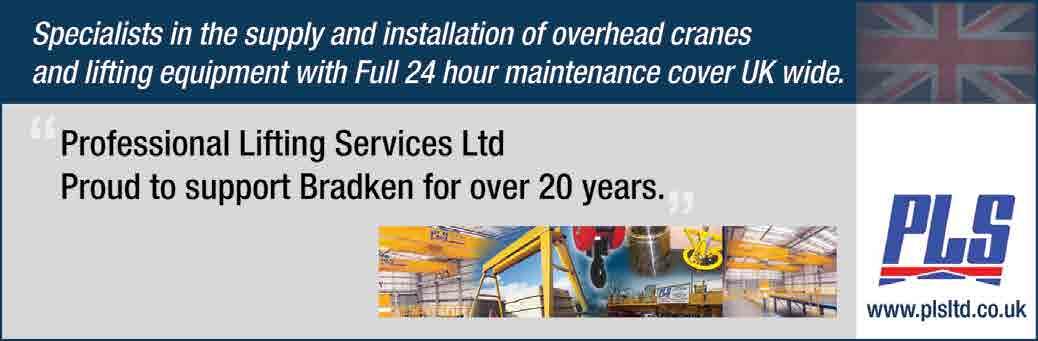
foundries globally, a growing segment, given the increased socio-political pressure for increased sustainability coupled with the high value of steel as a commodity.
Bradken is also highly successful in the transport sector offering both products and services to the bulk minerals and freight transportation markets, including high quality rollingstock equipment (bogies and drawgear componentry), complete wagons (iron ore, coal, bulk minerals and intermodal) and rail equipment spare parts (the Express Parts business) and equipment leasing options to a global network of customers.
Finally, the Engineered Products Division produces a wide range of highly engineered ferrous castings and machining services to the mining, resource, transportation and energy industries. This Division works with OEMs to manufacture highly specialised capital products that are ‘mission critical’ and require first-run production integrity. By drawing on its expertise in material selection, computer modelling and non-destructive testing, Bradken is able to offer customers turnkey solutions even under the most challenging and intense specifications.
Products can include rock crusher components such as jaw plates and feed chutes, valves and nuclear castings, rollers or buckets for heavy earth-moving equipment, gearboxes for large machines and even exposed structural castings for use in building design.
It is this Division for which the Scunthorpe foundry manufactures the bulk of its cast products. A look at the facilities and technologies at just this one site will give some indication of what Bradken is able to offer on a global scale. The foundry includes casting facilities, a machine shop, assembly and heat treatment. Its machining capabilities include vertical and horizontal boring, CNC vertical machining and rotary surface grinding.
Before the finished products can leave the foundry they go through stringent quality and process control. This includes hardness testing, magnetic particles, microstructure, chemical analysis, sand control, ultrasonic examination and mechanical testing, as well as the standard measurements to ensure that every component has been made to the correct dimensions.
Design capabilities
As mentioned above, the importance placed on product development to provide differentiated solutions for clients is what sets Bradken apart from its competitors. To this end, its designers work with state-of-theart casting simulation software in order to develop client-specific solutions quickly and efficiently. 3D CAD/CAM design and patternmaking and virtual prototyping mean that Bradken’s designers can take a few days to come up with a solution that might previously have taken weeks.
For instance, Bradken’s design department is often called upon by its OEM clients to develop consumable replacement components to be fitted onto their existing machines. A product can be modeled, modified and developed according to exact specification in terms of dimension, surface finish and so on. Innovation is an ongoing process and involves continuous improvement to develop products that are superior to the original.
As Mr Rowett says, “The key emphasis is on creating better value for the customer. When we say ‘differentiated’ products, we don’t mean different for the sake of it. We mean ‘better’. We can solve issues that perhaps only became apparent once the machines were in use. It’s a process of constant evolution.”
Moving forward
In Europe, Bradken has traditionally focused on the power and cement industries. How-
ever, Mr Rowett tells us that this is not likely to be the focus for future growth: “It’s simply down to the fact that a lot of the technologies or processes used for these sectors are gradually becoming obsolete. Instead, we will be developing in other areas. For example, at the moment, we are very strong in the European dredging industry and we see good prospects here for the future.”
It is also possible that the group may set up manufacturing in other European countries. At the moment, it either exports its castings from the Scunthorpe and Darlaston foundries, or hires third parties to manufacture in Europe to Bradken’s own designs. He concludes: “Whether or not Bradken sets up manufacturing elsewhere in Europe will depend upon both where the opportunities lie and how economically viable it is to do so. But this is certainly a possibility for the future.” n
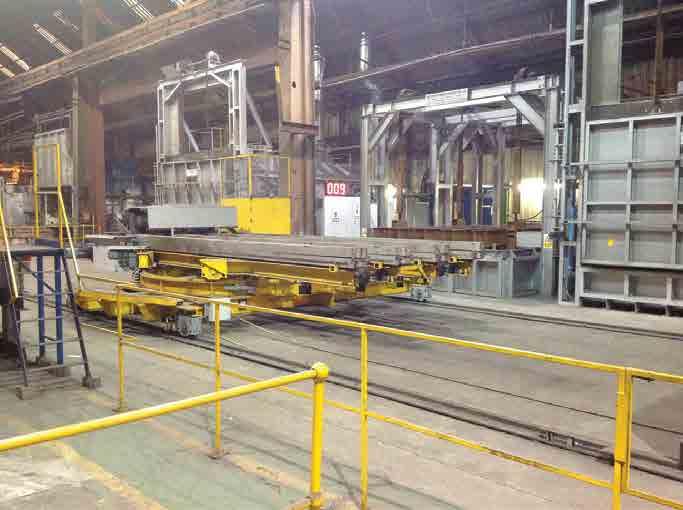
Capital Refractories specialises in the supply of refractory linings and associated products to the metal melting, foundry and cement industries around the world. The company manufactures a wide range of dry vibration rammable products for lining coreless induction furnaces, vacuum coreless induction furnaces and channel induction furnaces for the melting of steel and high temperature alloys, iron, copper, bronze, aluminium and masteralloys.
Capital Refractories is one of the largest independent refractory companies in the UK and operates on a global scale with clients in over 30 countries. Capital has been manufacturing, supplying and installing high quality refractory products to metal melters for almost 50 years.
Please visit www.capital-refractories.com for the contact details of our distributors worldwide.
Capital Refractories Limited Station Road, Clowne, Chesterfield, S43 4AB, UK Tel: +44 (0) 1246 811163 Fax: +44 (0) 1246 819573 Email: enquiries@capital-refractories.com
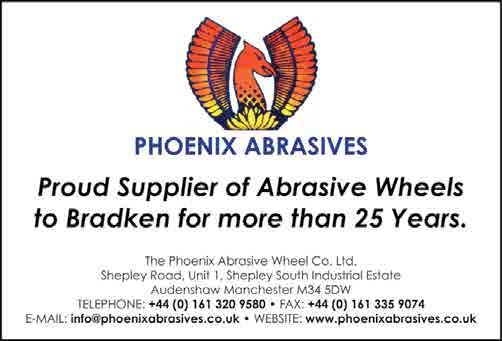
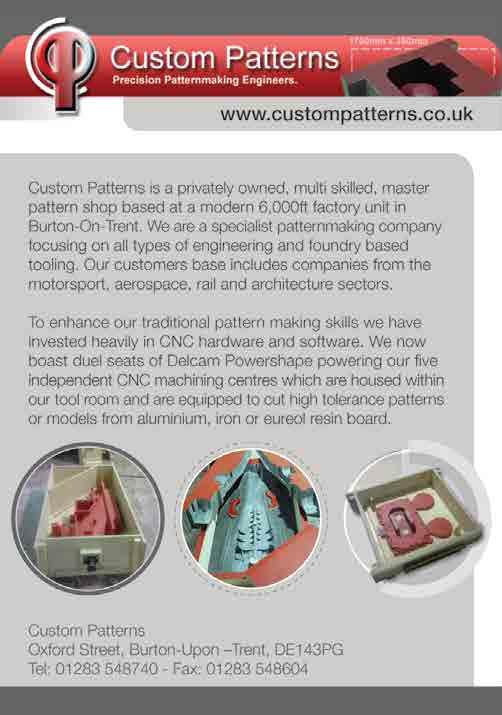