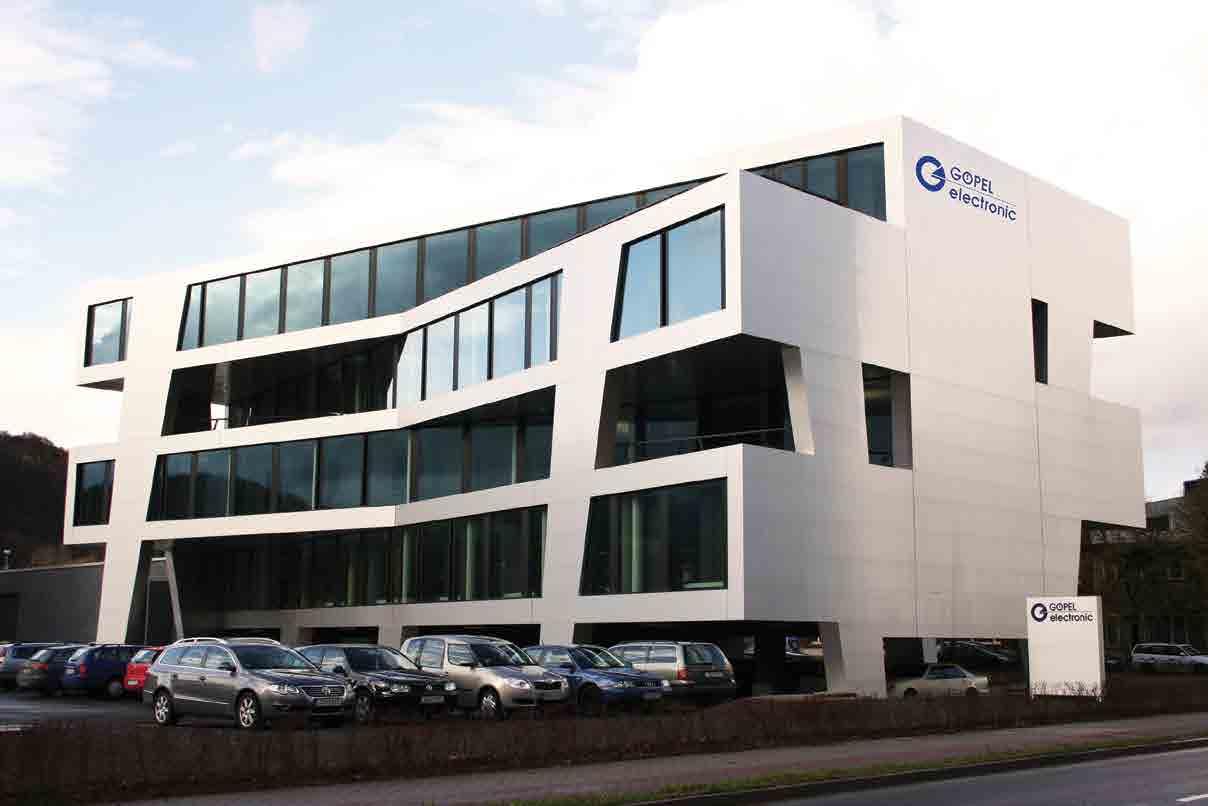
11 minute read
Safety, innovation and quality in everything we do
modern strategy for validation, test and debug as well as programming of complex boards and systems. They can be used throughout the entire product life cycle, enabling improved test coverage at reduced costs. A key part of ESA are chip-embedded instruments, permanently integrated or temporarily implemented test and measurement functions in an integrated circuit, that are the counterpart to external T&M instruments but don’t require invasive contacting by probes or nails.
To support its customers employing ESA, GOEPEL electronic has introduced the ESA Coach evaluation kit, which offers tutorials in ESA technologies such as Boundary Scan, Processor Emulation Test and Chip Embedded Instruments. “The advancing paradigm shift from intrusive test to Embedded System Access requires corresponding knowledge and technology transfer, which we are able to support through our ESA Coach,” says Jan Heiber, a GOEPEL electronic’s Application Support Manager. “Practical training in the newest test and programming strategies enables users to solve access problems caused by intrusive methods.”
Optical Inspection
GOEPEL electronic has been developing its Automated Optical Inspection (AOI) systems since 1996 when the first OptiCon system was launched. It has since been developed into one of the most commanding test technologies in electronic production and the first of the new company buildings was opened in 2003 specifically to support these systems. Last year, GOEPEL electronic upgraded its OptiCon TurboLine AOI system, which is widely used for both top and bottom PCB inspection in production for automotive products. An additional integrated camera module for PCB bottom side enables inspection of pin-in-paste solder joints together with the SMD inspection – all in one system.
Of course, however sophisticated an optical inspection system is it can see only what is actually visible. GOEPEL electronic has therefore taken its inspection systems a step further with the development of automated X-ray (AXI) systems which can inspect complex and double-sided assembled PCBs including all solder joints. At present only a minority of 3D AXI systems are fast enough to enable a complete PCB inspection within a production cycle because the magnitude of image capturing required and the large amount of data dramatically limits possible inspection speeds. But the revolutionary GigaPixel image capturing concept of GOEPEL electronic’s OptiCon X-Line 3D AXI system enables a complete 3D inspection of the entire PCB at speeds of up to 40cm2/s.
Solutions for the auto industry
The development and production of Intelligent Test Systems for the functional testing of electronic assemblies and devices for the automotive industry has been a major part of GOEPEL electronic’s business for many years. Functional tests are carried out at the end of the production line, typically at the final assembly point of complex boards where multiple electronic and mechanical components ‘meet’ for the first time. At this stage it is possible that the wrong electronic components get into the housing or electronic components may even be destroyed during the final assembly. It is to recognise these and other faults that functional testing of manufactured products is carried out at the end of the line.
A major order in this business area was carried out in 2013 when GOEPEL electronic’s OsCAR G3 functional test systems were put into operation at the production facilities of the worldwide Lear Corporation in Germany, USA, South Africa, China and India. The OsCar systems were installed for the functional testing of Lear’s BR205 series of car seats which are supplied for the new Daimler C Class. The OsCAR system executes ECU tests and checks additional electronic components inside the car seats; it is a versatile functional car seat test system that can be configured for specific test requirements and ‘unit under test’ with minimal modification and reprogramming effort. Because of the systems’ automatic seat identification system it can be used to test each car seat of each automobile manufacturer. GOEPEL electronic’s solutions for the automotive industry include bus communication and ECU testing up to functional test systems for vehicle control units.
GOEPEL electronic also offers solutions for acoustics analysis in vehicle manufacturing to enable noises such as squeaking or rattling to be detected and analysed through end-of-line testing. These include the SoundChecker mobile structure-borne sound analysis system and CARoLINE, an impact sound analysis tool that evaluates the acoustic quality of rotating, motor-driven components in the vehicle.
“The automotive industry is a very important market for GOEPEL electronic but our testing systems are applicable in just about all industries that use PCBs or other electronic assemblies,” says Thomas Wenzel. “Telecoms, medical devices and the rapid development of the Internet of Things are increasingly important markets for us and will be major drivers of future growth. We are a very dynamic company and we put just as much work into strategic marketing – understanding changing market demands and global logistics flows – as into developing new technologies for ever-more-complex boards. We see a lot of opportunities for the applications of embedded systems and we are always alert to new testing technologies just over the horizon.
“So I am confident that GOEPEL electronic can continue to grow, as it has for the last 22 years, step by step and year on year.” n
Teradyne
Some in-circuit test systems are moving to support both invasive and non-invasive test techniques. A good example is Teradyne’s TestStation family of test systems which have an open architecture that supports augmentation of traditional invasive in-circuit tests with native and partner boundary scan, functional, and embedded system access solutions.
Goepel has collaborated with Teradyne to design a specific SCANFLEX JTAG/Boundary Scan System card that plugs directly into the backplane of Teradyne’s TestStation test systems, which enables manufacturers to combine Goepel’s non-invasive boundary scan and ESA techniques with Teradyne’s comprehensive suite of traditional in-circuit tests. Teradyne’s multi-protocol support concept gives manufacturers maximum flexibility to select from a portfolio of invasive and non-invasive test techniques – to construct a test solution that best matches the fault coverage, test access and test throughput requirements of the product under test.
“The benefits of using an open architecture manufacturing test system that is capable of supporting multiple test techniques”, reports Alan Albee, Product Manager for Teradyne’s Production Board Test Division, “ includes lower development costs (because tests can be re-used), reduced equipment footprint, handling and operator costs (because there are fewer test stages), and improved diagnostic accuracy /faster repair time (because faults can be detected sooner in the manufacturing process)”.
STEMMER IMAGING
STEMMER IMAGING is Europe’s largest imaging technology provider with headquarters in Germany (Puchheim near Munich) and subsidiaries in many European countries. Our mission is to provide the users and developers of imaging technology with competitive advantage by adding value in the supply of quality components, expertise and support.
Imaging or machine vision is used in many different application areas such as industrial automation, production technologies, the automotive industry, medical imaging and traffic technology but also increasingly in many other industries - as a powerful and cost effective way of implementing automatic quality assurance. Even at high speeds and with stringent accuracy requirements, machine vision allows 100% monitoring and thus strengthens the competitive edge of those companies using it.
STEMMER IMAGING customers have access to a wide variety of imaging products from the world’s leading manufacturers and to a comprehensive support service, based on 40 years of imaging experience. STEMMER IMAGING are the developers of the independent, modular programming library for imaging applications, Common Vision Blox, and also manufacture application-specific products to enable complex solutions. Our unique service covers everything needed to solve your imaging task.
STEMMER IMAGING – Imaging is our passion!

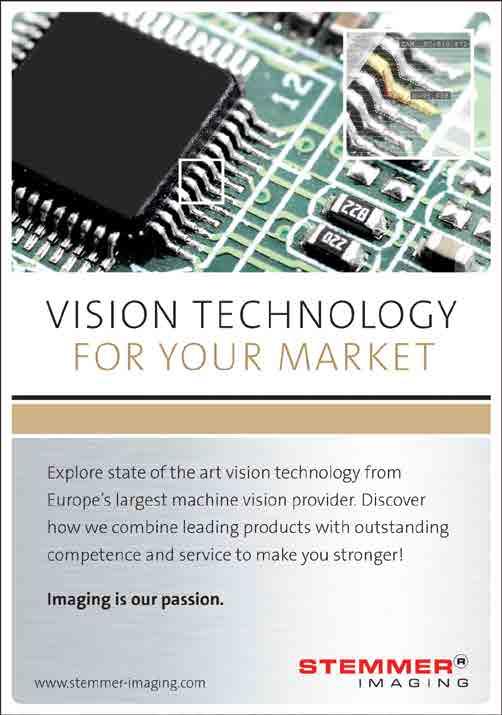
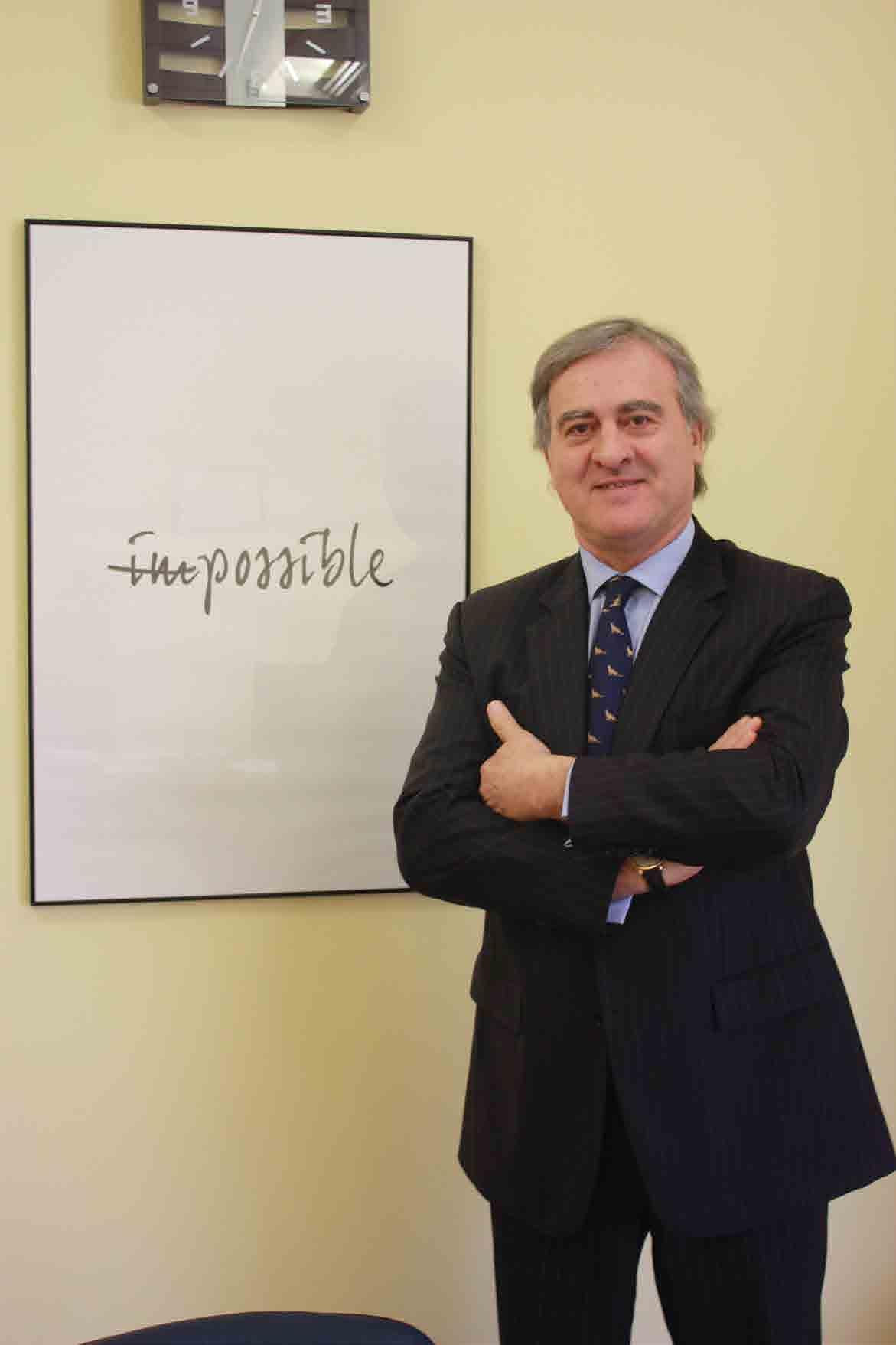
SAFETY, INNOVATION AND
QUALITY IN EVERYTHING WE DO
High quality, sophisticated electronics and innovative technology are the pillars of the success of Bitron Poland Sp. z o.o. and of the group to which it belongs. What is even more important is the human element behind this, as the CEO of Bitron Poland, Silvio Brignone, explains to Barbara Rossi.
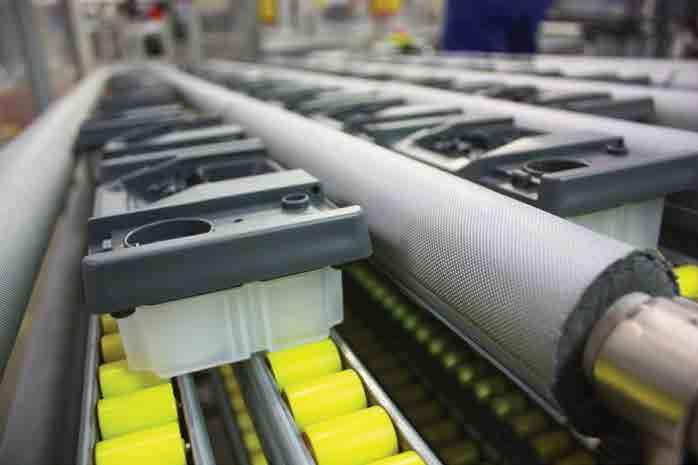
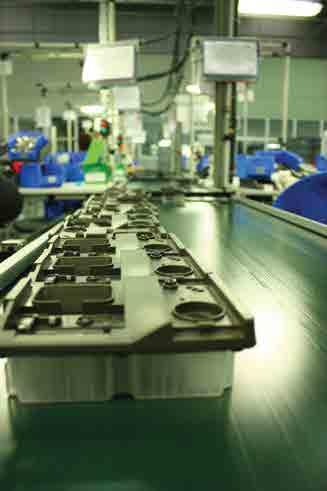

Silesia-based (Sosnowiec) Bitron Poland is part of the privately owned multinational Bitron Group, whose headquarters are in the Turin area of northern Italy. The group is specialises in the research, development and manufacturing of mechatronics devices and systems for the automotive, household appliance, HVAC and renewable energy sectors, as well as in producing electronic components for other industries.
The group, which was founded in 1955 as a manufacturer of household appliance components by three brothers – Enrico, Giovanni and Carlo Bianco – has a truly global presence, with thirteen manufacturing plants and development centres, nine sales and marketing facilities, one after-sales centre and one technical centre. In fact, over the years, the group has expanded both geographically and in terms of the market segments served. In 1968 it opened its first foreign site (in Spain) followed by its entrance into the electronics market the following year. Other milestones were reached in 1975, when Bitron started serving the automotive sector; in 1992 when its common corporate identity was created; in 1998 with the establishment of Bitron Poland; in 2002, with the birth of Bitron China; in 2008 with the launch of Bitron Turkey and in 2010, which saw the setting up of Bitron HVAC systems. A new addition to the Bitron family took place in 2013, with the inauguration of Bitron Mexico.
Today the group is led by Giovanni Bianco, employs more than five thousand people worldwide (with more than three hundred staff dedicated to R&D) and has a €650m turnover. Bitron Poland plays a particularly important role with its 1300 employees and €100 million turnover.
Furthermore, while most of the Group’s production plants produce only a part of the range offered by the group, Bitron Poland manufactures all the Bitron types of products. It is thus organised in five production areas: automotive, household appliances, HVAC, renewable energy and electronics. While the first four of these carry out the production of electromechanical components for their respective market segment, the last one is engaged in producing electronics components for the market segments served by its counterparts, as well as for other industrial sectors. Some of the main products manufactured, at group and Polish level, are car window control switches for the automotive sector, electric solenoid water valves for household appliances (for which Bitron is a world leader) and boiler components and systems. Bitron Poland also manufactures smart energy meters for the biggest Italian energy distributor and the group is also developing products for, the renewable energy sector, such as solar and photovoltaic panels.
Mr Brignone explains, “We have a very vertical activity. We take care of the whole production process, starting with design, thanks to our technical department, followed

The ITIB Group was established in the 70’s and since then it has been owned by the Italian shareholders from the Brescia – Paderno Franciacorta region.
We would like to invite you to have a closer look at the ITIB POLAND SP ZOO wide offer.
Międzyrzecze Górne 403 43-392 Międzyrzecze Górne / Region Bielsko-Biała Phone: +48 33 488 88 44 | www.itib.com
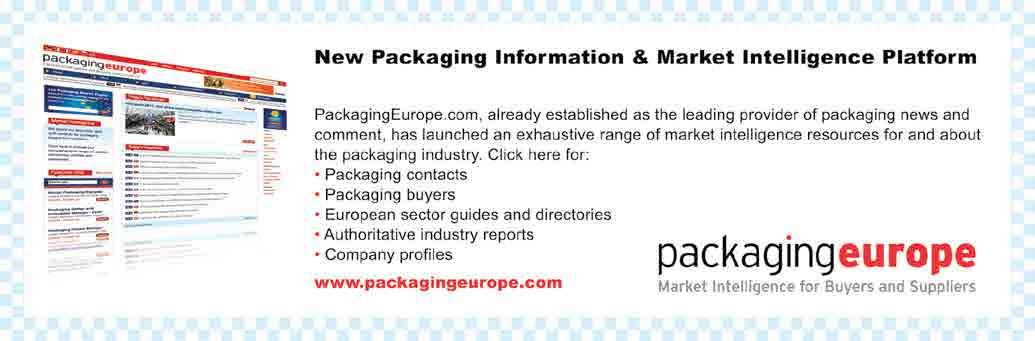
ITIB Poland
ITIB Poland is a company that started its activities in 2001 in Bielsko - Biała. In June 2009, ITIB Poland moved its production to a newly built facility on the outskirts of Bielsko -Biała, where it increases its production further and strives to meet the needs of the most demanding customers in Poland and abroad. BITRON POLAND SP Z O.O. is one of such customers, with whom ITIB closely cooperates.
The ITIB Group’s profile is divided on: The machinery sector - construction of complete lines (extruders) for the produce of corrugated pipes. Plastic product sector based on two technologies: 1 Blow moulding - various types of air distribution ducts, tanks, etc . used mainly by the automotive industry. 2.Extrusion - corrugated pipes for automotive, appliances and other industries.
TECHPLAST
TECHPLAST Andrzej Szczeblewski has been supplying BITRON with a variety of injection moulded plastic parts for several years. It was in 2007 that we first demonstrated our reliability to BITRON after it relocated production for the first of its moulds to our company. At this time we even produced parts during Christmas and the New Year in order to ensure the company was able to keep to its production schedule.
In addition to supplying the moulds, we gave BITRON a number of suggestions regarding their functionality, which allowed it to make several modifications. These resulted in improved production efficiency and quality. This collaboration has been so successful that as of 29 January 2014 BITRON has relocated production of 65 of its moulds to our site, and plans to relocate another later this year.
At TECHPLAST we have always completed our orders for BITRON on schedule. We also look after packaging and delivery, which ensures the parts are in perfect condition when they reach the company’s stockroom. To this end, we maintain a close relationship with BITRON’s logistics team in order to remain flexible and offer the fastest possible delivery times. Furthermore, we cooperate closely with BITRON’s quality control team throughout all stages of production.
Through this partnership and others, TECHPLAST has built a reputation as a trustworthy, solid and reliable supplier that always honours its commitments.