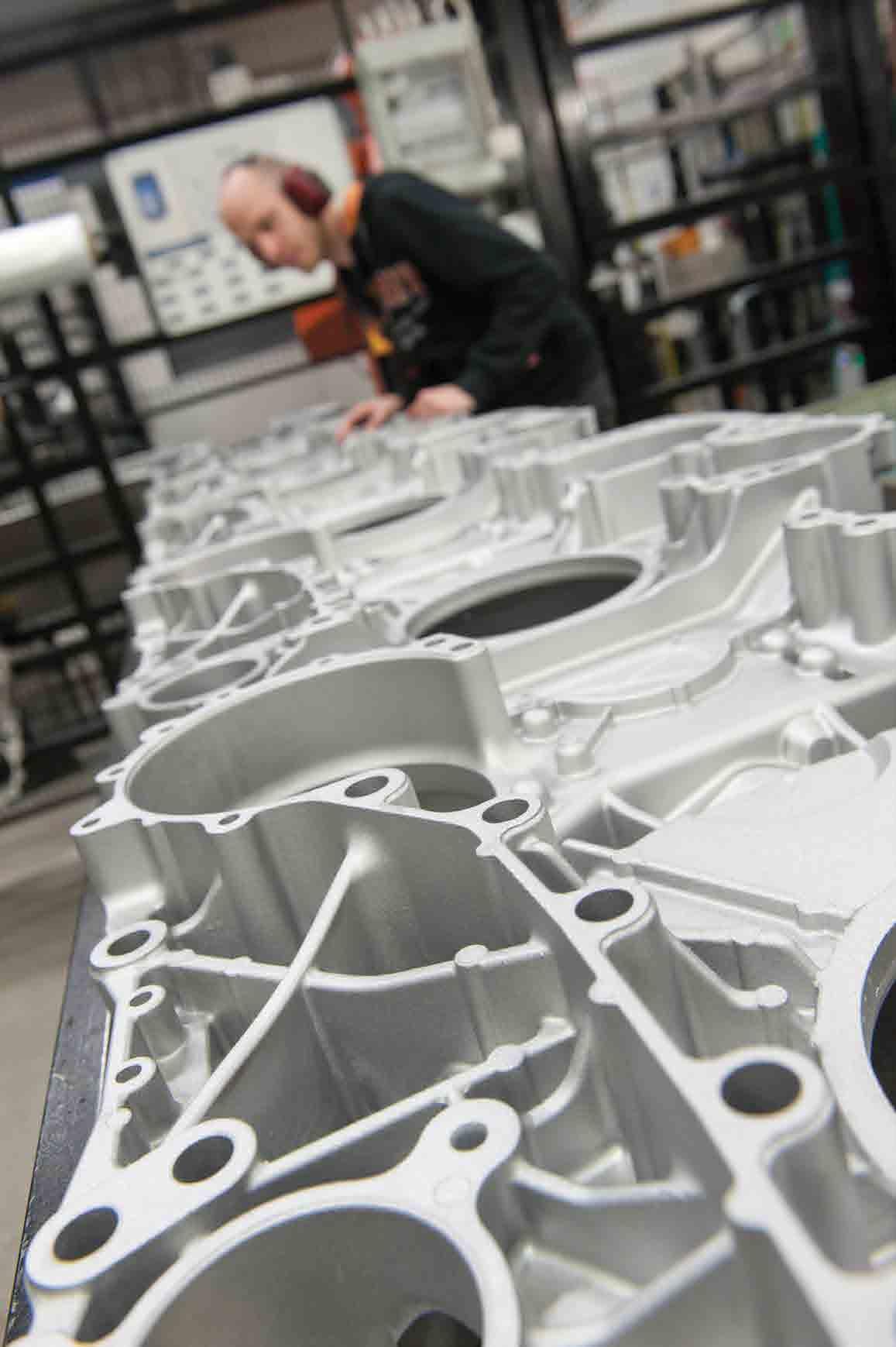
4 minute read
High pressure die casting Ljunghäll
HIGH PRESSURE DIE CASTING
The Swedish company Ljunghäll AB specialises in high pressure die casting and supplies car parts to major motor manufacturers like Volvo and Ford. Industry Europe reports on a company that uses its design skills to reduce costs for its customers.
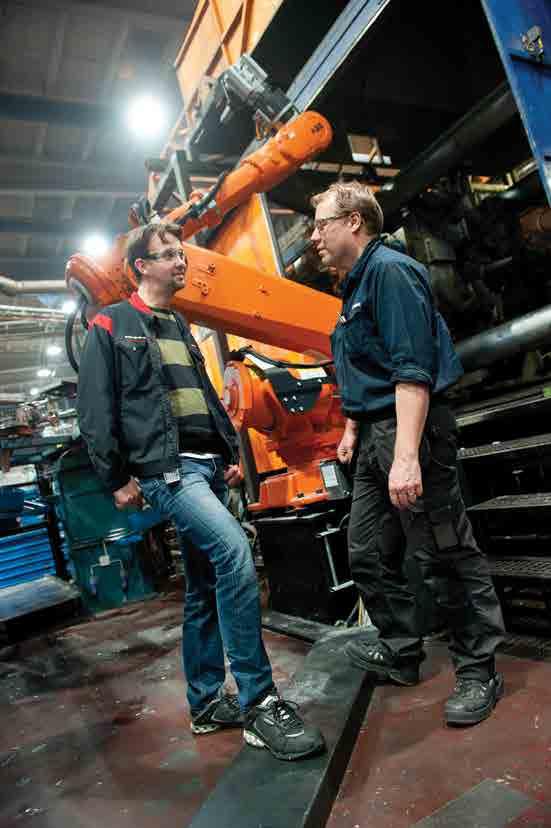
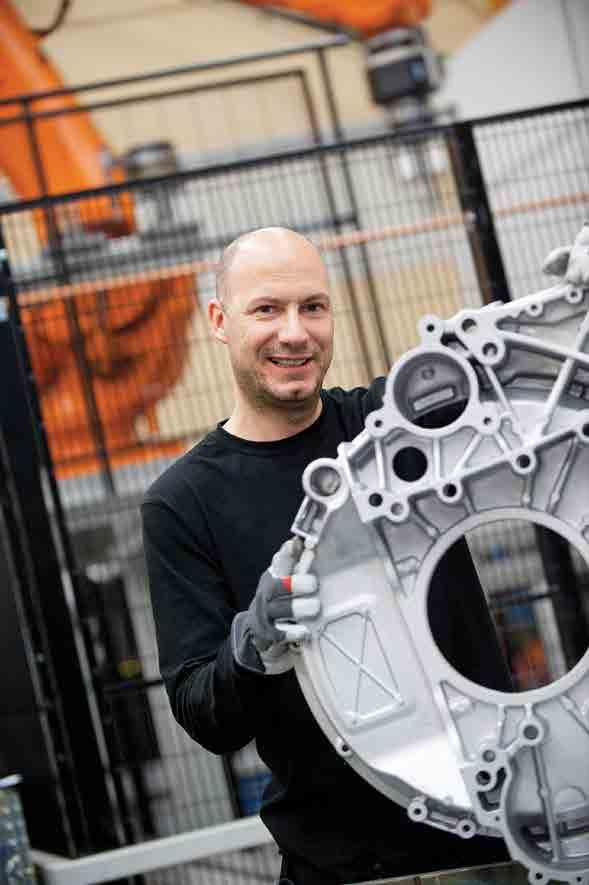
Ljunghäll began life in 1917 as a rural blacksmiths that made ironwork and shoed horses. Later the company moved into sand and chill casting. In 1963, it settled in its current location of Södra Vi, a village in the province of Småland. Today Ljunghäll is one of the world’s top manufacturers of car parts using high pressure die casting. The company aims to design parts that are strong, lightweight and competitively priced and that will also cause as little noise or friction as possible.
Ljunghäll presents itself as an ‘external engineering partner’. It works closely with clients at the early stage of development to design a new part for a vehicle. If a car company is looking to make improvements, it can come to Ljunghäll and the company’s engineers will create a better component to replace the old design. Ljunghäll’s advanced thin wall die casting parts enable carmakers to achieve savings on weight. At the same time, because its part designs require a smaller amount of raw material to produce, they can also be made at lower cost. When a new product is being developed, Ljunghäll can even station one of its own skilled engineers with the customer’s design team, ensuring that the project is fully aligned to the customer’s needs.
Ljunghäll makes aluminium components for heavy vehicles as well as for passenger cars and the company’s clients include the Swedish truck manufacturer, Scania. Its expertise is also employed in the telecoms industry for important customers such as Ericsson.
Quality and precision
Ljunghäll relies on the best production equipment to bring its designs to life. Production is highly automated, thanks to stateof-the-art industrial robots, and standards of quality and precision are high. Ljunghäll maintains a quality management system that is certified to ISO 9001:2009. The company has around 50 high pressure die casting machines together with around 80 CNC (computer numerical control) machines. Ljunghäll also offers a complete range of after-treatment methods such as machining, washing, assembling and leakage testing. For manual assemblage, it has for many years followed the Japanese ‘poka-yoke’ system, designed to prevent errors from occurring in the manufacturing process.
This year (2014) the company increased its production capacity still further with a 16 MSEK investment in a new 1650-ton high pressure die casting machine and related equipment. It is a fully automatic production line and has enabled Ljunghäll to increase capacity for parts up to 15kg.
Operating as a ‘strategic production partner’ to major players in the automotive sector, Ljunghäll combines a reliable service with the ability to be flexible. It believes in meeting its customers face-to-face, listening to their concerns and cooperating successfully with them to create a better part. With decades of experience of this type of work, Ljunghäll is often involved in several different early stage development projects at any one time. It prefers to solve problems for its clients rather than just blindly carrying out their instructions. It strives to think ahead and to devise innovative solutions that will exceed customer expectations.
Expansion in Europe
Ljunghäll is well aware that its customers are always on the lookout for ways to keep costs low. The superior design skills of Ljunghäll’s engineers certainly help customers to achieve this objective. However, the company has also taken steps to reduce the labour costs of its own manufacturing operations. In 2007, Ljunghäll expanded its production by taking control of Drop Press, a company in the historic Czech town of Čáslav. The acquisition of Drop Press (now renamed Ljunghall s.r.o.) provides Ljunghäll with a valuable base in central Europe from which to serve the flourishing Czech motor industry.
The company claims that its Čáslav site can deliver the standards of quality and reliability for which Ljunghäll is traditionally
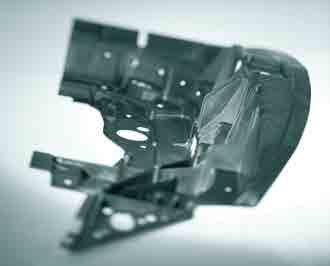
known, but at a lower cost for its customers. One option Ljunghäll offers is for a new part to be made initially in Sweden with a view to transferring the production to the Czech Republic at a later stage.
As a maker of high tech components, Ljunghäll is meeting the needs of the 21st century. The emerging economies are now demanding a larger share of the world’s energy resources, meaning that oil prices are likely to remain high. Ljunghäll’s lightweight components support the efforts of the motor industry to produce lighter vehicles that consume less fuel.
While attuned to the needs of the times, Ljunghäll is still proud of its rural origins as a village smithy. The company also takes its environmental responsibilities seriously and maintains an environmental management system in accordance with ISO 14001:2009. In addition, Ljunghäll is careful to ensure that its suppliers are aware of their obligations under the European legislation on the Registration, Evaluation and Authorisation of Chemicals (REACH). n

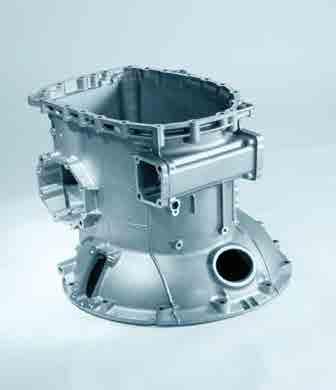
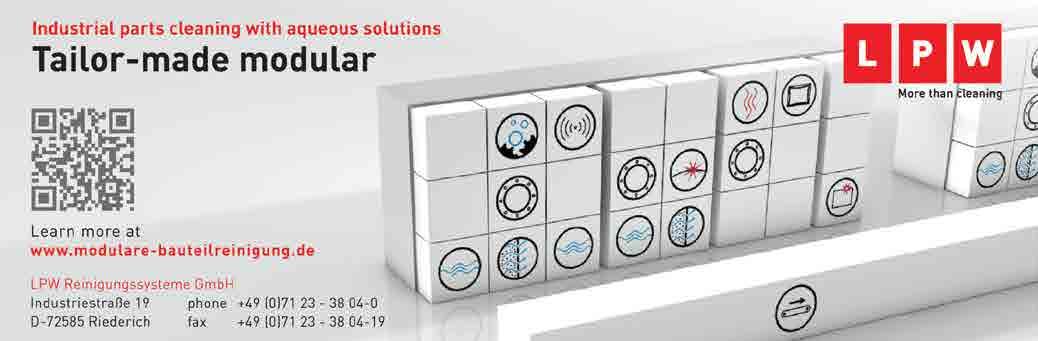
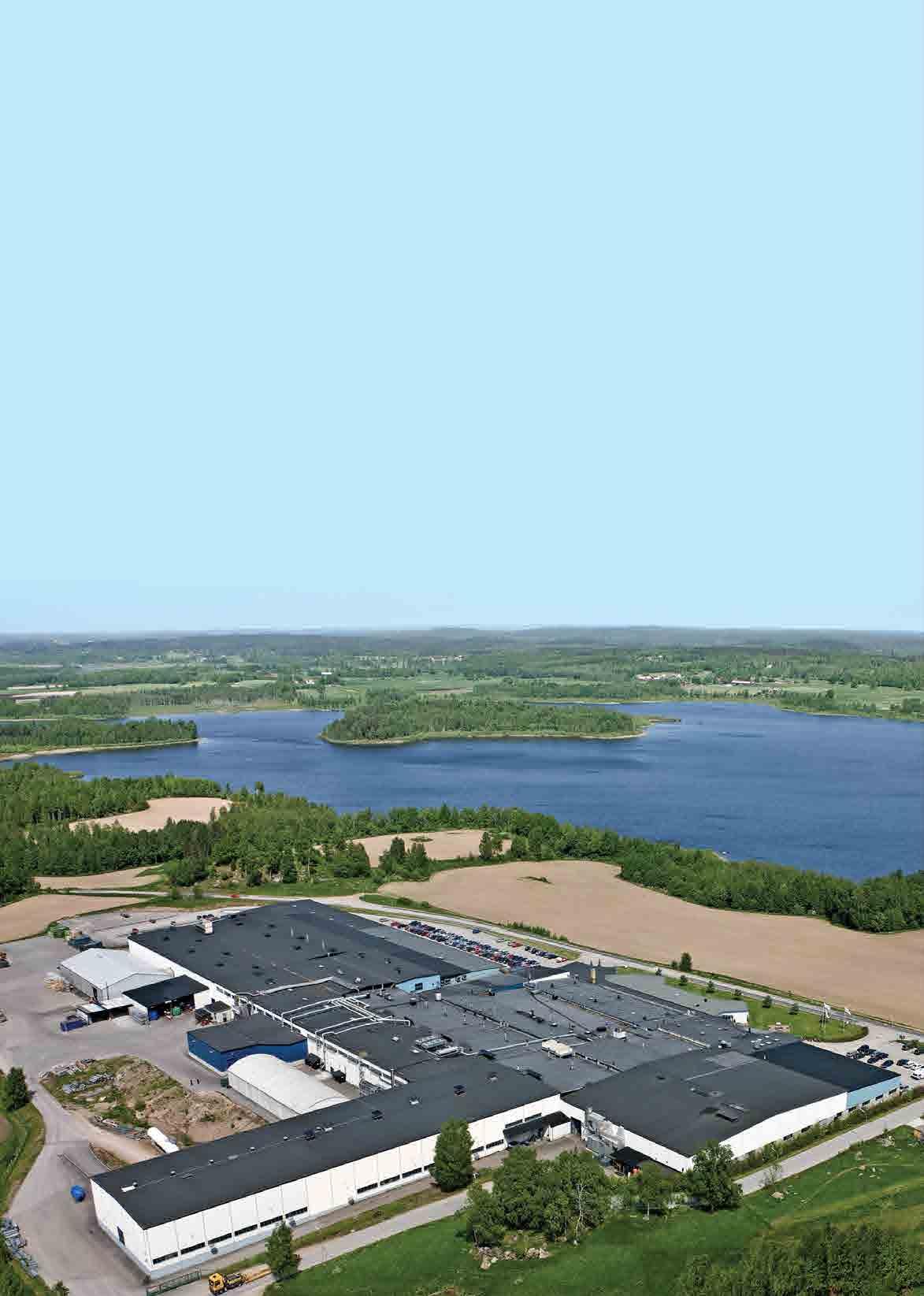