
11 minute read
The appliance of science Haldor Topsoe
THE APPLIANCE OF SCIENCE
Catalysts make chemical reactions much faster. Haldor Topsoe’s catalytic technology is accelerating change all over the modern world. Peter Mercer reports.
IN 1940 Dr Haldor Topsoe, a Danish engineer and research scientist who had worked with Niels Bohr, set up his own company to develop heterogeneous catalysts. From the beginning the idea that drove the company was to build a bridge between academic research in chemistry and the practical needs of industry and, indeed, of the people of the world.
Catalysis is a process that accelerates a chemical reaction that would otherwise be uselessly slow. It makes it possible to turn a wide range of resources into products that are useful, indeed often essential, to our lives. Ammonia, for example, is a key ingredient in chemical fertilisers and catalysts are indispensable to its production on a practicable scale. A typical ammonia plant will use catalysts to produce around 2,000 tons a day; without catalysts, it would take about a million days to produce the same amount.
Topsoe’s catalysts have played a central role not only in hugely expanding the global production of ammonia for fertilisers but also in driving the ‘green revolution’ in the 1960s, which made possible the tripling of crop production in many developing countries and enabled them to feed their growing populations. “Haldor Topsoe himself was a key player in establishing a modern fertiliser industry in India and Bangladesh, helping these countries to build their own ammonia plants rather than rely on expensive imports,” explains Mads Cordt Gyldenkaerne, Topsoe Communications and Marketing Manager. “It was in recognition of such pioneering work that Dr Topsoe was awarded the Hoover Medial in 1991 for ‘his technical abilities and entrepreneurship, and his involvement with leaders in third world countries, which have significantly contributed to an increase in world food production through technology transfer’.”
Today, of course, ammonia is used not only in fertilisers but to make everything from paper and plastic to vitamins and cosmetics. And catalysis itself is involved in the production of 90 per cent of commercial products. Catalysts are essential in reducing air pollution from industrial plants and road vehicles and in producing more efficient and cleaner fuels and the basic chemicals that are indispensable to modern industry. And in serving all of these needs Topsoe’s strategy remains that of marrying fundamental research to practical implementation, maintaining a synergy between R&D, process design, engineering, production and sales. That is why, for example, it acquired, in 1999, the world’s first specially manufactured electron microscope to perform in-situ catalyst studies – an unprecedented investment for a private business.
In 2014 Haldor Topsoe A/S is a DKK 5.3bn privately-held company with production plants in Frederikssund, 40km from Copenhagen, and in Houston, Texas. The Danish plant employs 650 people and its 20 production lines run 24/7. The US plant was built in 1971 and employs 150 people on four production lines. The company develops and manufactures its catalysts through three main business units: Environmental, Refinery and Chemical.
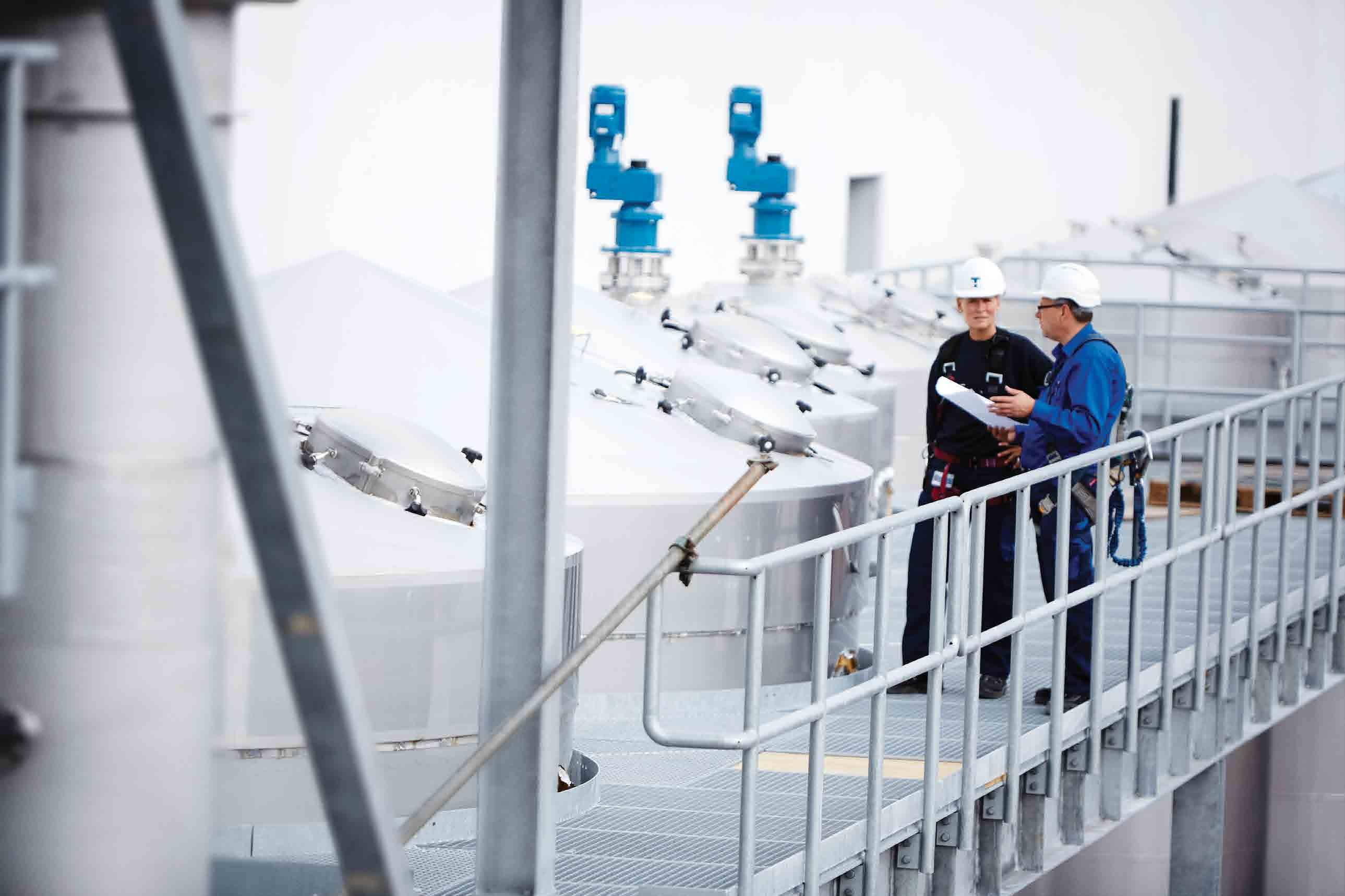
Environmental solutions
All over the world, Topsoe catalysts are making a major contribution to reducing air pollution. In fact the company’s first major product, the VK catalyst, which was marketed in 1944 to create sulphuric acid for use in fertilisers, is now playing a key role in solving the problem of industrial sulphur emissions. The VK catalyst portfolio has been expanded for use in a Topsoe process called Wet Gas Sulphuric Acid (WSA) which not only desulphurises toxic gases but also converts the sulphur waste into sulphuric acid, one of the most widely used bulk chemicals in the world. Topsoe’s WSA technology is today used in steel plants, in the mining industry and in processes where coal is gasified and converted into petrochemical products. Oil refineries too use WSA technology to create commercial quality sulphuric acid from the sulphur that is removed from transportation fuels.
In the automotive sector, the focus of Topsoe’s Environmental Business Unit is on treating the engine exhaust from heavy diesel vehicles. Devices using Topsoe’s SCR DeNOx catalysts are installed in the vehicle’s silencer to remove dangerous nitrogen oxides (NOx) as well as particulates and hydrocarbons. In fact, since these devices came on to the market in 2006, more than 250,000 heavy trucks and buses worldwide have been equipped with Topsoe’s SCR catalysts.
The SCR DeNOx catalysts were, in fact, originally developed to treat flue gas pollution from power plants and their wide use has helped to ensure that today most of the emissions from Western European and US power plant chimneys are not dangerous nitrogen oxides but water vapour and harmless elemental nitrogen. Topsoe is also the market leader in catalytic NOx removal for gas-fired power plants, which are becoming an increasingly popular alternative to coal fired plants, particularly in the US, where shale gas is transforming the energy market. Natural gas plants create no sulphur pollution but there is still the problem of NOx emissions, as there is with all types of combustion.
Peter Thoft Knudsen, Group Vice President of the Environmental Business Unit, says that growth in the emerging economies, coupled with tighter clean air legislation worldwide, will continue to fuel
Bjerne S. Clausen, President and CEO of Haldor Topsoe
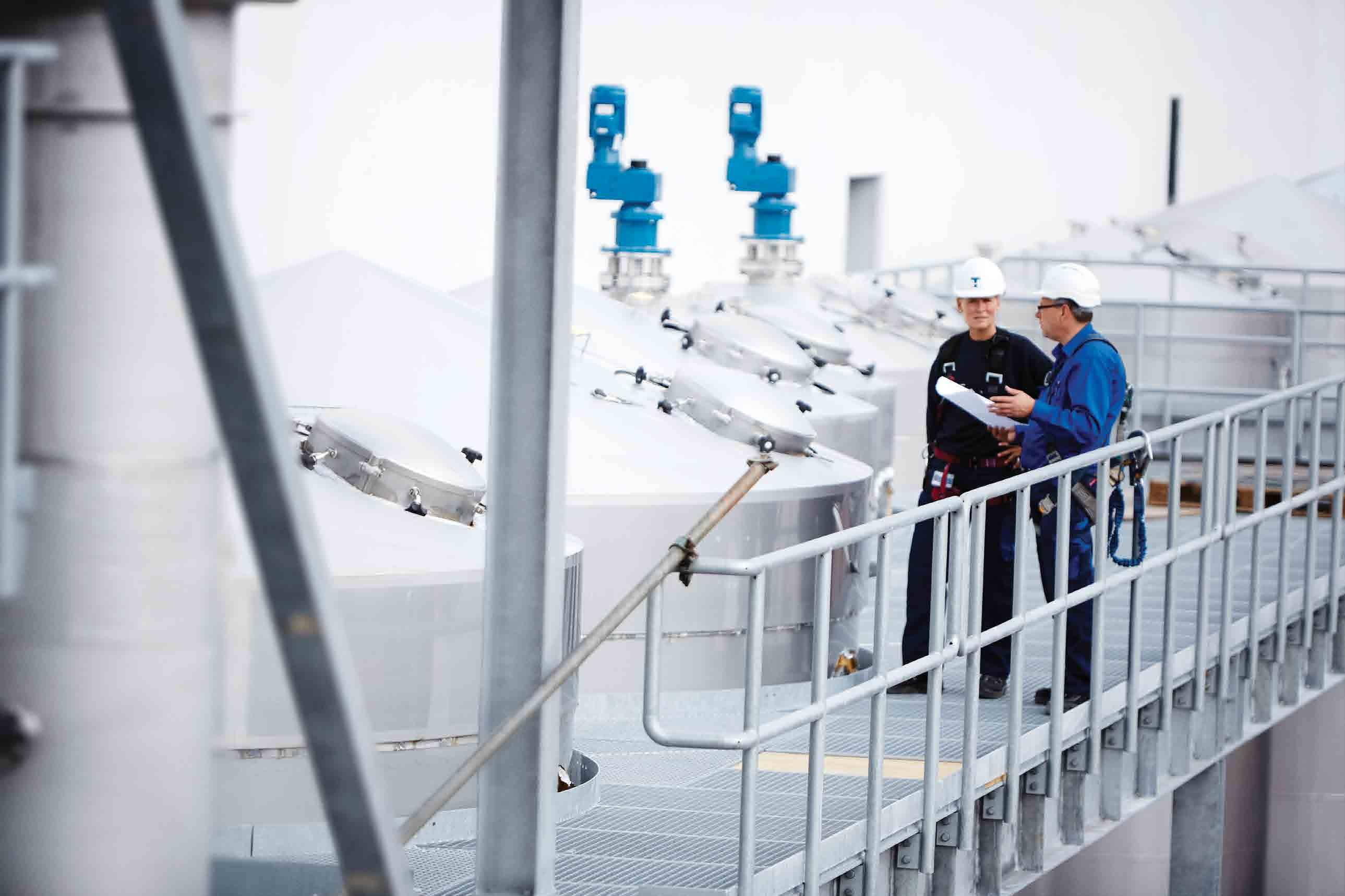
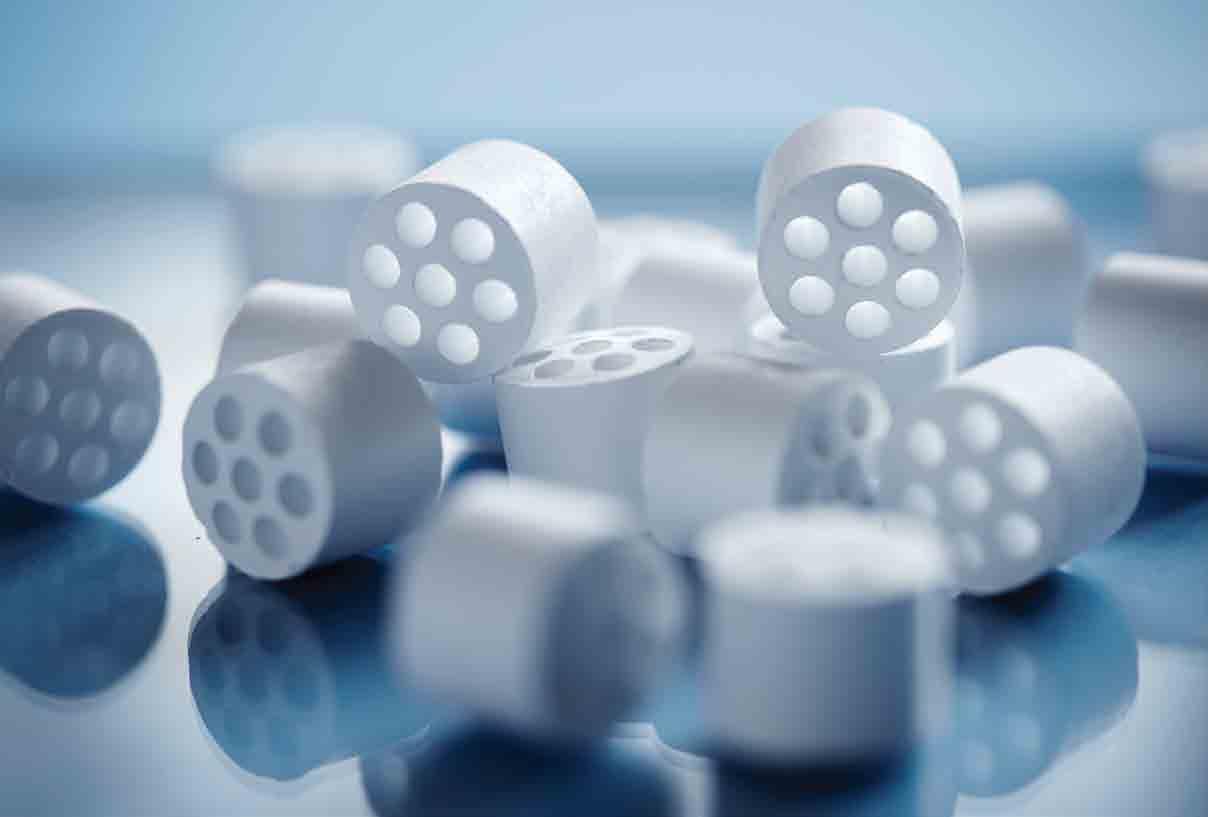
the growth of this area of Topsoe’s business. “In recent years, many countries with strong growth rates have become increasingly interested in pollution control,” he says. “In fact, more than 50 per cent of the WSA plants that we have sold around the world have gone to China and while Europe is currently our most important automotive market, China has by far the largest potential.”
Just how seriously Haldor Topsoe is taking this potential is evident in its on-going construction of an automotive catalyst plant in Tianjin. Capital investment in the plant will total DKK 900m and high-volume production for the Chinese market will begin in early 2015. The plant will manufacture catalysts for the removal of NOx from diesel engines used in light commercial vehicles, buses and trucks.
“Delivering efficient automotive catalysts is only part of our business in China,” says Bjerne S. Clausen, President and CEO of Haldor Topsoe. “We also offer larger, stationary catalytic solutions for cleaning off-gases from a wide range of industrial sources, including fossil-fuel and biomassfired utility boilers, gas turbines, oil refining and chemical plants. These technologies have proven their worth for years in Europe and North America and hold huge potential in terms of curbing air pollution in China.”

Making cleaner fuels
Topsoe’s Refinery Business Unit is focused on helping the worldwide oil refining industry to meet the ever-increasing demand for cleaner fuels. Most of its sales, which account for around a third of the company’s total revenue, are of hydro-processing catalysts involved in the production of diesel fuels, high-quality jet fuel, petrol and other products. The foundation of this business is the supply of catalysts and technology for the production of ultra-low sulphur diesel (ULSD), the fuel that has in recent years replaced conventional diesel throughout most of Europe and North America. Topsoe is the market leader in this technology – more than 40 per cent of all the ULSD produced in the world is processed using its catalysts, helping to make the fuel that goes into an engine as environmentally-friendly as the exhaust gases that come out. And, this year, Topsoe has invested more than DKK 300m in a new production unit at Frederikssund that will focus on the manufacture of catalysts for the production of ultra-low sulphur diesel.
However the increasing worldwide demand for cleaner fuels comes at a time
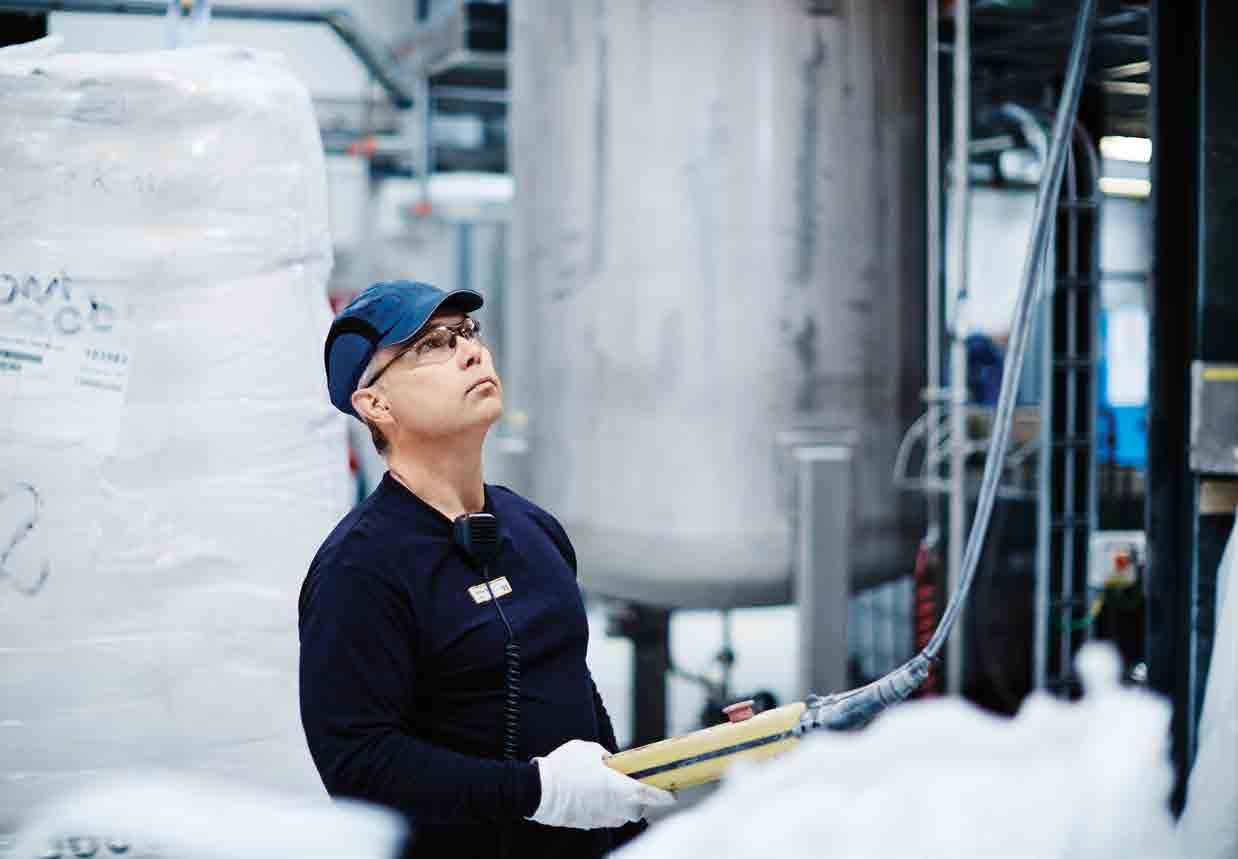
when the global supply of light and easilyrefined crude oil is diminishing; much of the crude that is pumped up today is heavy and contains increasing amounts of sulphur. To meet the need to upgrade this oil Topsoe has developed a catalytic process called hydrocracking, which breaks up the large hydrocarbon molecules of heavy oil into smaller ones, producing oil that can be more easily refined into light products such as diesel fuel. To complement this process Topsoe has also developed a catalyst series called HyBRIM which is used to reduce the sulphur and the nitrogen content of the heavy oil before it is hydrocracked. This pretreatment not only purifies the product but also enhances the effectiveness of the costly hydrocracking catalysts.
As in its Environmental business, Topsoe sees very important growth opportunities for its refinery solutions in emerging economies, where governments are increasingly recognising the seriousness of their pollution problems and are willing to adopt the more costly refining technologies that have become commonplace in Europe and North America.
Synthesis gas
The core activity of Topsoe’s Chemical Business Unit is the development and production of the catalysts and technologies needed to create four basic products: hydrogen, ammonia, chemicals such as methanol and formaldehyde and synthesis gas. It is in the last area, the creation of synthesis gas, that much of the CBU’s current development and growth is taking place.
Synthesis gas is an intermediate product that can be created from feedstocks such as natural gas, biomass, petcoke and coal and can then be used to make other basic products such as hydrogen, ammonia and methanol. But, crucially, it can also be used to make substitute natural gas (SNG) which can take the place of coal in factories, power plants and homes. In 2013 a Chinese SNG plant that Topsoe designed went on-stream in the north-west province of Xinjiang. This plant, the largest of its kind in the world, uses Topsoe catalysts and a Topsoe technology called TREMP to transform coal-derived synthesis gas into SNG. For a country like China, with huge coal reserves but also with huge pollution problems in its cities, the advantages of being able to transform coal into a clean fuel that can be easily transported thousands of miles by pipeline are obvious.

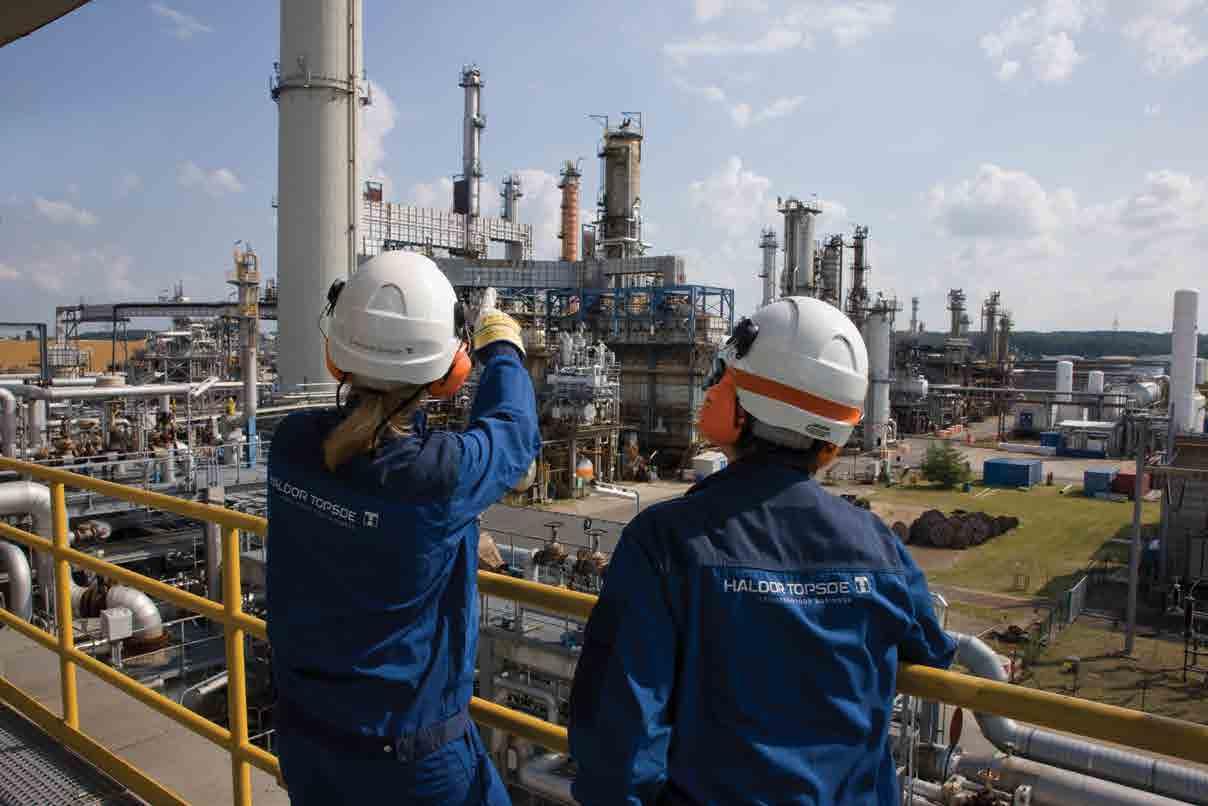
Another growth area for the Chemicals Business Unit is the use of synthesis gas for the production of gas to liquid (GTL) fuels. Since in this process the synthesis gas is derived from natural gas, it follows that this industry is emerging in parts of the world where natural gas is plentiful and relatively cheap, such as Qatar, Nigeria, Russia, Uzbekistan and, since the shale gas revolution, the US. As part of a global GTL partnership with the South African energy company Sasol, Topsoe’s Chemical Business Unit provides catalysts and proprietary synthesis gas technologies for the transformation of natural gas into a unique synthesis gas. Sasol then converts the synthesis gas into a sulphur-free fuel called GTL diesel.
New horizons
The mission of Topsoe’s New Business Unit is to explore and develop new ideas and new technologies that will drive the company’s future. In fact, Topsoe is looking to the Unit to play a major role in its corporate ’30 in 25’ strategy (that is, to increase revenue to DKK 30bn by 2015). At the moment some 40 projects and ideas are circulating within the company. One early phase project is called Battery Materials and is focused on developing new cathode materials that would enable lithiumion batteries in electric and hybrid vehicles to be recharged up to 80 per cent in ten minutes and give the vehicle a range of 500 km before recharging – a huge improvement on current performance. Topsoe has no doubt that the cathode market is going to be huge and that it is in a position to become a leading player.
In February of this year Topsoe also expanded its technology options in battery materials development by acquiring 18 per cent of UK-based Faradion Ltd, a company that is working on sodium-ion battery technology. Replacing the lithium in batteries with sodium is very promising since sodium is more commonly available, more sustainable and much less expensive.
Another new project is centred on a catalytic process, called TIGAS, to create synthetic petrol from just about any carbonbased material. This process in now ready for commercialisation and, in fact, Topsoe and three industrial partners have already executed a large-scale demonstration project near Chicago to produce synthetic petrol from wood chips. And, with the exploitation of massive reserves of shale gas in the US, there is now even greater potential in making synthetic petrol from natural gas. Topsoe believes that as oil prices continue to rise, TIGAS can make a very significant contribution to the realisation of the ’30 in 25’ strategy.
Looking even further to the future, Topsoe has set up a subsidiary, Topsoe Fuel Cell A/S, where 100 employees are working on the development of a type of fuel cell called a high-temperature solid oxide fuel cell (SOFC). R&D is focused on the core of SOFC technology – a series of very thin ceramic cells that make up the ‘stack’ where electricity is produced through the electrochemical reaction across the cell between hydrogen in the fuel and the oxygen in the atmosphere.
An interesting feature of SOFC technology is that it integrates well with wind and solar energy, as it can quickly ramp up and down to compensate for the inevitable output fluctuations of wind and solar systems. It is also reversible – electricity, from renewable generators producing excess power, can be combined with water to produce hydrogen fuel, effectively ‘storing’ the excess electricity for use when production is low.
As Lars Martiny, CEO of Topsoe Fuel Cell, says, “SOFC technology can build a bridge to a future in which renewable energy is a stable, practical alternative to the energy infrastructure we have today.” n
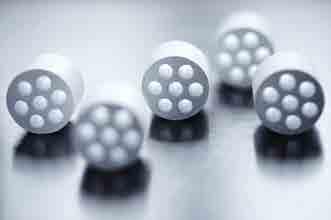