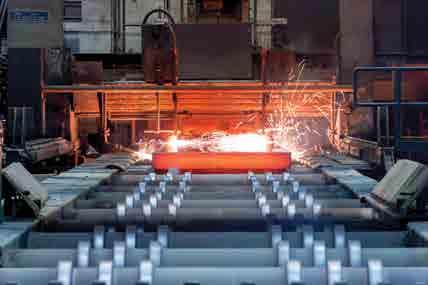
7 minute read
Vallourec tubes for Mont Saint-Michel
NEWS
New developments in the Metals industry
Ruukki Construction to focus on roofing business in Romania
IN conjunction with the combination of SSAB and Rautaruukki, operations serving the companies’ construction customers have been merged into a new division – Ruukki Construction. Ruukki is a well-known brand in the residential roofing business and sees growth potential in this business also in the Romanian market. However, market conditions in the steel structure and component businesses in Romania have remained weak, and Ruukki has been unable to turn the businesses back to profitability. As a consequence, Ruukki plans to discontinue these businesses and focus solely on the roofing business. There are plans to use the existing sandwich panel line and profiling lines in Romania in Ruukki’s other plants elsewhere. Visit: www.ruukki.com
Trimet acquires aluminum smelter in Voerde
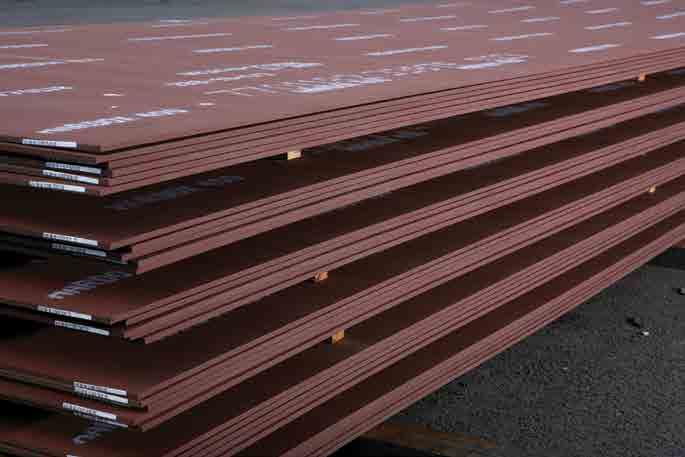
Trimet Aluminium SE has acquired Voerde Aluminium GmbH and all 280 of its employees. The company manufactures primary aluminum and carbon anodes used in electrolysis for metal extraction. Trimet will continue to run the aluminum smelter and anode factory at its location on the Lower Rhine and will take over the full staff.
With the Voerde location, the materials specialist has expanded its production capacity for primary aluminum, continuing the positive growth demonstrated over the past few years. “Key European industries have great demand for aluminum. With the Voerde location, we can meet the growing demand. The staff and the technical equipment are perfectly aligned with Trimet’s orientation as a provider of customised solutions,” says Dr Martin Iffert, CEO of Trimet Aluminium SE. Visit: www.trimet.de The current reline of blast furnace 2 in Duisburg-Schwelgern is being used as an opportunity to modernise a further key facility of ThyssenKrupp Steel Europe: Work has started on revamping one of the continuous casters in Duisburg-Beeckerwerth. The work is being carried out in parallel with the reline of blast furnace 2 in order to minimise production losses. The aim of the modernisation of continuous caster 1 is to improve slab quality and widen the product range.
The modernisation will involve costs of around 90 million euros. “This is further evidence that despite all the burdens being imposed on us, for example in terms of energy prices, we continue to put our faith in the Duisburg site and are investing in its sustainability,” says Dr Herbert Eichelkraut, chief operating officer at Thyssen-
ThyssenKrupp Steel Europe invests in modernising continuous caster in Duisburg-Beeckerwerth
Krupp Steel Europe. “This is an important signal for our employees, but also for our customers and suppliers.” Visit: www.thyssenkrupp-steel-europe.com
SSAB’s Hardox celebrates 40 years
SSAB’s aim was to develop a wear plate that was both harder and tougher than other steels on the market when the company produced Hardox 40 years ago. It needed to be hard to be able to withstand severe wear and tear over a long period of time and tough to be able to handle bending and intense use without cracking.
“When the material was launched in 1974 as the ‘bendable wear plate’, it was the first wear plate in the world to combine both hardness and toughness and also work well as construction steel,” says Christer Offerman, a wear plate specialist at SSAB. “The fact that Hardox is an excellent structural steel has been one of the keys to its success. This is of great importance to our customers. It means that they can produce effective solutions for thin and light dump bodies, containers and buckets, which can also handle high levels of wear and tear.” Visit: www.ssab.com
Outokumpu creates special surface with an 800-tonne stainless steel façade for Baosteel’s head offices
SKS, a joint venture between Outokumpu and Baosteel Group in China, is delivering over 800 tonnes of high-quality coldrolled stainless steel plate for the cladding of Baosteel’s landmark head offices in Shanghai and Guangzhou in China. Baosteel’s head office in Shanghai includes three buildings with a total façade area of some 48,000 square metres. In Guangzhou, the main building of Baosteel’s southern headquarters will be 140 metres tall. Both projects began last year and are expected to be completed in 2016.
Says Austin Lu, head of Outokumpu’s Asia-Pacific operations: “These buildings are a great opportunity not only for Baosteel to demonstrate its competence as a construction materials supplier, but also for Outokumpu to showcase its expertise in high-performance stainless steel. Both Baosteel and the architect are attaching great importance to the building materials used in these projects.” Visit: www.outokumpu.com
INDUSTRYNEWS
Sheffield Forgemasters to supply crucial castings for US Navy submarine fleet
The contract will see Sheffield Forgemasters International Ltd (SFIL) deliver 84 castings to General Dynamics Electric Boat Corporation, the company responsible for the design, construction and lifecycle support of submarines for the US Navy. SFIL won the order based on its strong working relationship with Electric Boat Corporation and its unparalleled history of supplying high specification steel castings for both the US and the UK Navy submarine programmes. SFIL are only one of a handful of companies around the globe qualified by the US Navy to produce these high integrity casting, having undergone an extensive qualification program involving both Electric Boat and the US Navy.
Dr Graham Honeyman, chief executive at Sheffield Forgemasters International Ltd, said: “This is a landmark order for Sheffield Forgemasters and for the UK and it cements our long-standing working partnership with Electric Boat Corporation.” Visit: www.sheffieldforgemasters.com
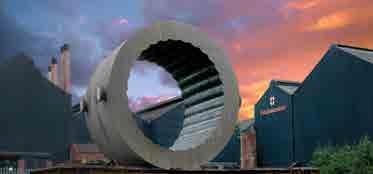
Hydro optimises production capacity in Sunndal
Hydro has decided to reduce remelt activities at its primary metal plant in Sunndal, Norway, and to replace volumes by ramping up production at its SU3 potline.
The SU3 potline consists of two production halls with a total production capacity of 100,000 tonnes per year. Owing to the economic downturn, Hydro curtailed SU3 in 2009. Hydro has now decided to restart parts of the remaining potline.
“We will start up one of the four remaining sections in November and December. Given that the startup goes according to plan, the rest of SU3 will be ramped up by mid-year next year,” says Hilde Merete Aasheim, head of Hydro’s Primary Metal business area. Visit: www.hydro.com
Tata Steel opens new automotive finishing line
Tata Steel has opened a new finishing line at its IJmuiden steelworks in the Netherlands. Tata Steel has invested €12 million in Finishing Line 32, which will process up to 400,000 tonnes of galvanised (corrosion resistant) steel coil a year.
Henrik Adam, Tata Steel’s chief commercial officer, said: “This investment will enable us to improve the supply of high-quality steels to customers while also improving delivery times. The new finishing line enables us to meet the most stringent quality standards for advanced steels, some of which are used by automotive manufacturers for vehicle body panels and safety-critical components. These steels are often stronger and thinner enabling our automotive customers to produce more fuel-efficient and lighter-weight vehicles.” Visit: www.tatasteeleurope.com
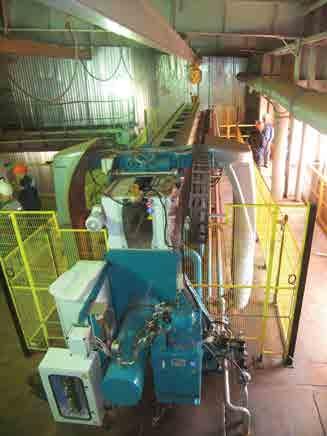
UC RUSAL launches pilot unit at Urals aluminium smelter
UC RUSAL, a leading global aluminium producer, has launched a pilot unit at the Urals aluminium smelter (ìUAZî) to produce primary scandium concentrate using red mud for the production of alloys. The new unit is capable of producing 2.5 tonnes per year of primary scandium oxide concentrate. Throughout 2014, investment in the project has totaled 74 million rubles.
The company expects to create a pilot plant, along with the necessary technology, for the processing of the primary scandium concentrate into a commercial product, where the content of scandium oxide will reach 99.0% by the end of 2014. The market price for such a product ranges from USD3000 – USD5000 per kg. The capacity of a pilot plant will be 500kg per year.
The scandium oxide produced will be used for the production of aluminium-scandium alloys at RUSAL’s smelters. The use of scandium greatly improves the consumer properties of aluminium alloys. Visit: www.rusal.ru
EVRAZ ZSMK adopts pulverised coal injection technology
EVRAZ ZSMK has launched a pulverised coal injection unit for two of its blast furnaces. The unit’s production capacity amounts to 160 tons of pulverised coal fuel per hour, or about 1.3 million tons annually. Investment for this project has exceeded 7 billion rubles.
“This change-over to PCI technology is in alignment with EVRAZ’s strategy to reduce costs and to improve production performance. EVRAZ NTMK – the first EVRAZ plant to adopt this technology – has already appreciated the cost advantage of PCI, so we expect that the application of this technology at EVRAZ ZSMK will also be a success,” commented Alexey Ivanov, EVRAZ’s vicepresident and head of the Steel division.
Pulverised coal injection ensures substantial cost savings on natural gas consumed for hot iron production, and results in the reduction of coke consumption by 15–20%. At the same time blast furnace productivity improves approximately by 5%. In addition, the new technology is good for the environment as it reduces emissions of greenhouse gases. Visit: www.evraz.com