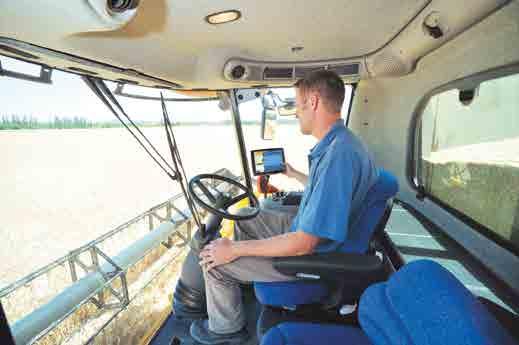
5 minute read
Simply the best Nitrogénművek
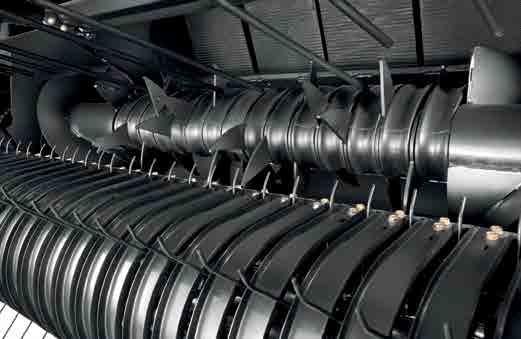
with more technology and low maintenance costs without breaking the bank,” stated Hedley Cooper.
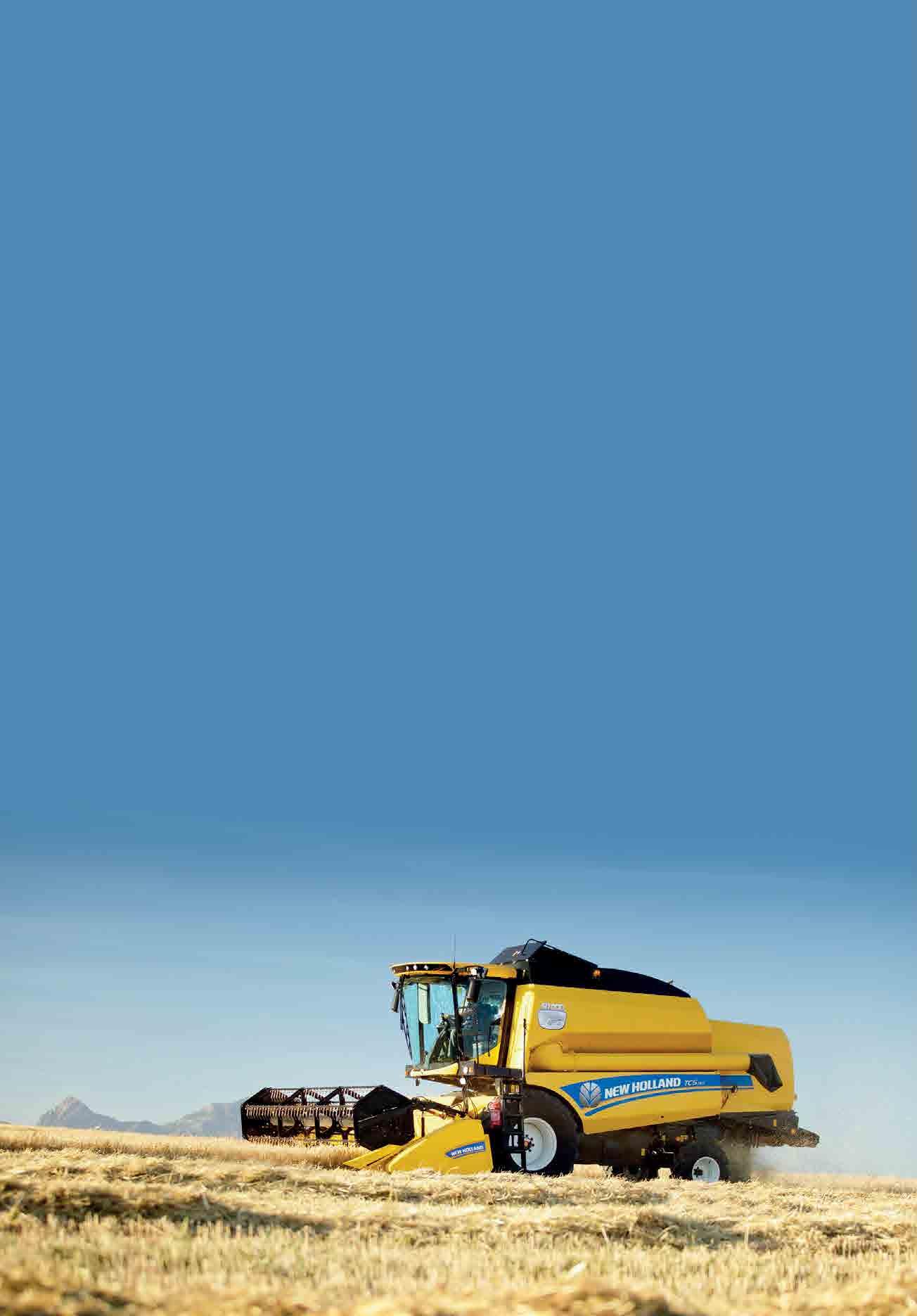
The new ActiveSweep
But it is not just in the area of combines that we have been seeing development and innovation. Over the past 40 years, New Holland has produced over 235,000 rollbelt balers. In celebration of this significant milestone, its all-new roll-belt models will feature a 40-year decal which will also market the success of these new models. The latest generation has redefined round baling with advanced roll belt technology that can improve capacity by up to 20 per cent and density by up to 5 per cent.
New Holland introduced the new RollBelt™ variable chamber baler series in 2013, featuring customised feeding systems like the SuperFeed™ and CropCutter™ rotor options. The new ActiveSweep™ crop processing solution offers a further choice to enable tailored baling.
Available on both Roll-Belt 150 and RollBelt 180 models, ActiveSweep has been purpose-developed by New Holland to transfer the crop directly from the pick-up to the bale chamber for gentle handling. Ideally suited to those wishing maintain long unbroken stems, ActiveSweep is perfect for baling hay and straw, minimising losses and producing a bale that can be unrolled for easy feeding or bedding.
Precision land management
Modern agricultural methods increasingly incorporate information technology to manage equipment in the field as efficiently as possible. The all-new New Holland PLM® Connect is a state-of-the-art communication system that can facilitate the control and supervision of equipment from a centralised office, allowing machine operation to be monitored and managed without the need
to spend time travelling between separate operations. It is a flexible system, needing just a 12volt supply to enable it to work with all brands of equipment.
A key PLM® Connect feature is connectivity between equipment. Machine utilisation is another key feature: Machines within a fleet can be quickly examined in order to decrease down time and increase performance, efficiency and in turn profitability. Although PLM® Connect is a full New Holland product, it is designed to offer compatibility with competitor products to include older machinery. This will enable the system to be added to any existing fleets.
Two levels of PLM® Connect, Essential and Professional, are available with core features including 360°, 24/7 machine access, optimised input management and detailed performance analysis and evaluation. PLM® Connect Essential ideally suits the needs of medium sized farms and can be fitted to tractors that are not equipped with CAN Bus technology.
PLM® Connect Professional offers indepth, real time information on equipment both locally and working at long distances from the main farm office. Fitted to vehicles with CAN Bus technology, PLM® Connect Professional relays detailed operating information to enable the remote monitoring of machine parameters and live communication with operators. Experienced operator input can be delivered to those less familiar with a given operation to instantaneously improve productivity and operating efficiency thanks to the real time connection.
“New Holland is aware of the reluctance some farmers and contractors have with modern connectivity systems,” adds Luca Mainardi, head of Tractor and Precision Land Management Product Management. “A key feature of PLM® Connect is its ability to evolve to meet the changing experience of the end user.” n
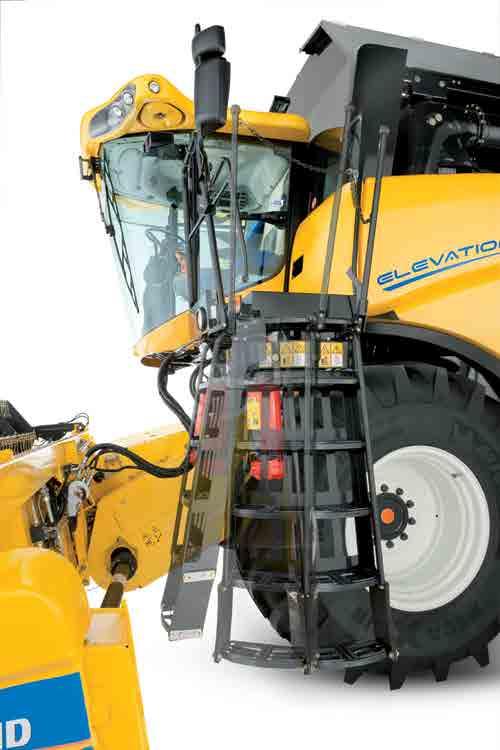
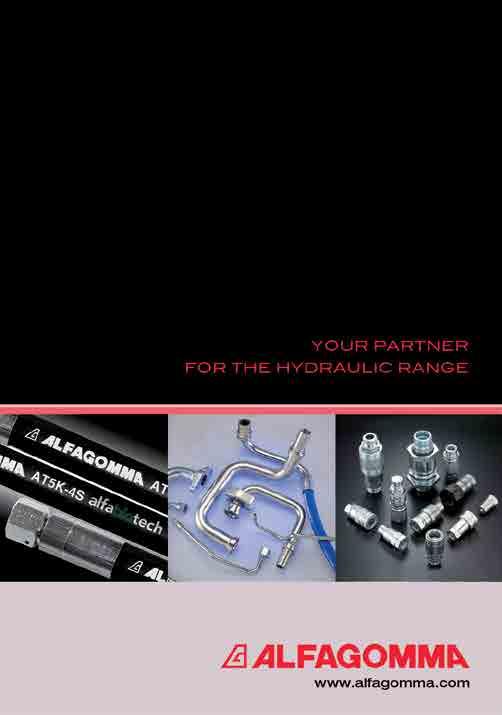
SIMPLY THE BEST
With 80 years of experience, how can a well established company improve efficiency, reduce its environmental impact, improve its capacity, improve customer relations and meet the challenges of chemical and fertilizer production in the 21st century? Nitrogénművek Zrt are meeting these challenges and more. Edina Beale investigates.
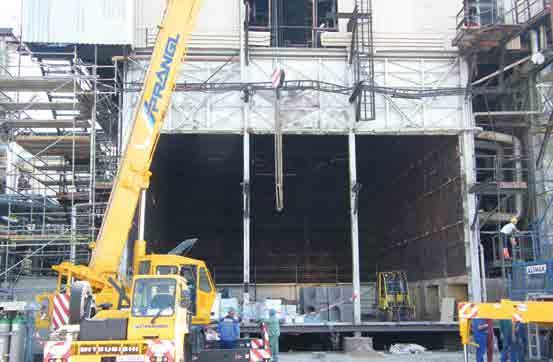
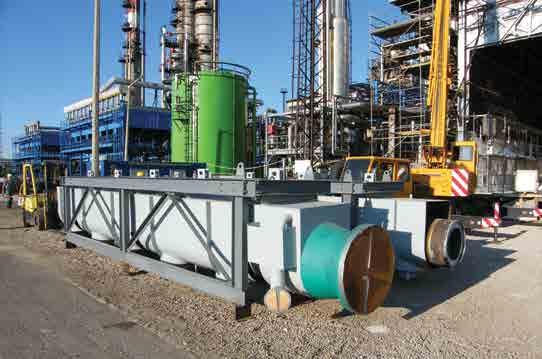
Nitrogénművek Zrt has been operating since 1931, making it one of the oldest chemical companies in Hungary. The company produces nitrogen based fertilisers, inorganic chemicals and industrial gases. In excess of 95 per cent of the products produced are nitrogen-based fertilisers including CAN (Calcium-ammonium nitrate), AN (Ammonium nitrates) Urea and liquid fertilisers. The present production rate is approximately 1,000,000 tons per year. The leading product in this range is CAN which accounts for approximately 50 per cent of production.
Growing capacities
Building capacity, improving efficiency and reducing environmental impact are important strategies at Nitrogénművek Zrt. In 2012, the company started an investment program to increase the capacity of the Ammonia plant. This project is due for completion in 2015. Once completed the plant will be able to produce 1300 tons per day ammonia and reduce the energy required to do this by 3 per cent.
Another area where capacity has been increased is in the production of nitric acid. In 2013 output increased to 1700 tons per day with plans to increase that figure to 1800 tons per day in 2014. Once complete the nitric acid plant will be extremely efficient in addition to being the highest capacity plant in the world, with the lowest environmental impact. The company is also investing in a new, high efficiency, 2000 ton per day AN/CAN fertiliser unit.
It is not only new equipment that improves efficiency. At the present time the company is reviewing its procedures in a number of key areas, including the Ammonia plant, to see where changing operating procedures and methods can increase efficiency and capacity. By adopting this approach the company is potentially able to gain maximum efficiency with minimum investment.
The company acknowledges that there are some areas where there is a need to build new plant, to replace ageing and inefficient systems, and areas are now being identified for this process. To power the actual equipment required for the manufacture of the products there is a need for energy, and Nitrogénművek Zrt has invested in a new electricity generating system that produces 3MW. Plans are already underway to introduce a new system that generates 10MW.
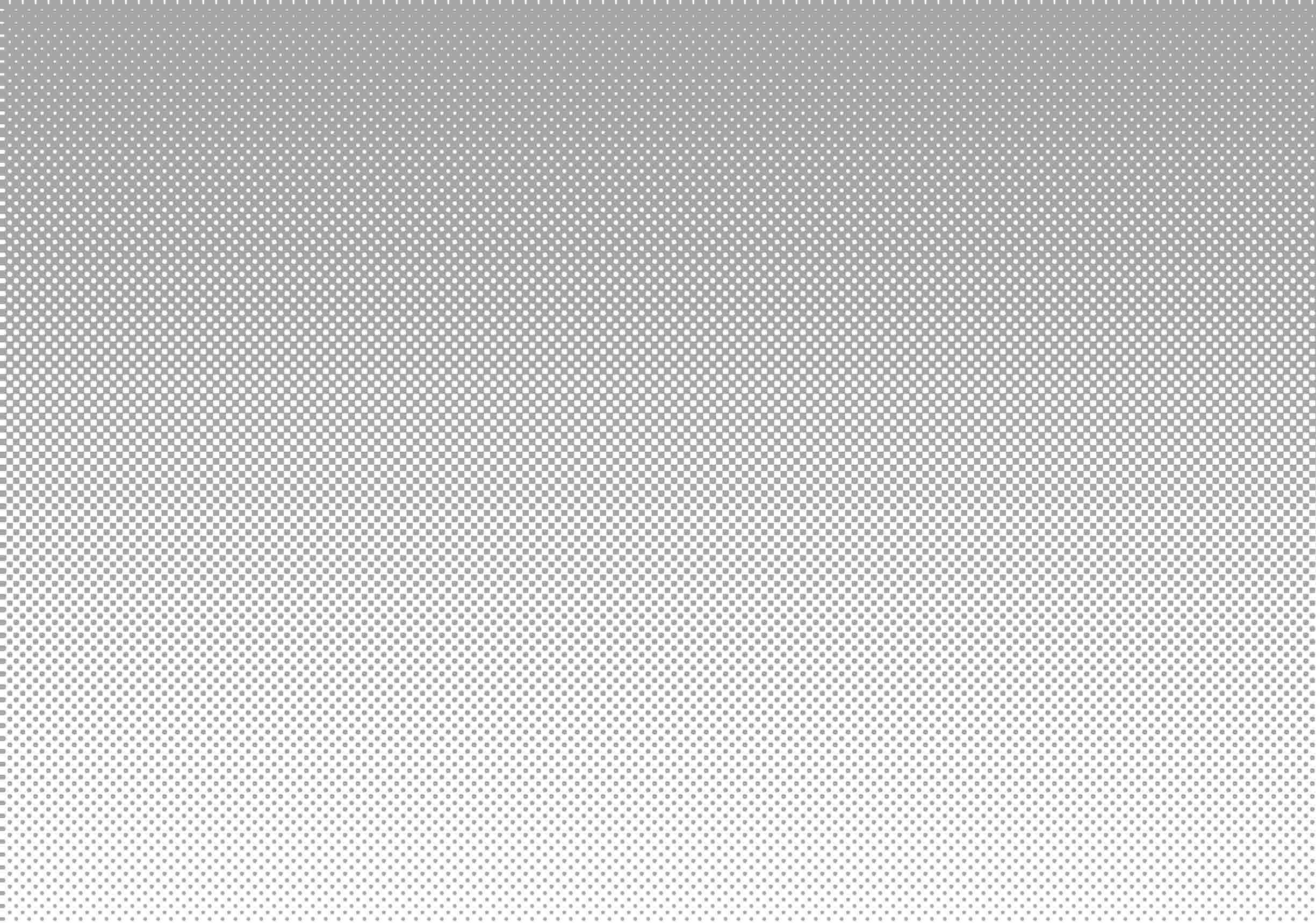
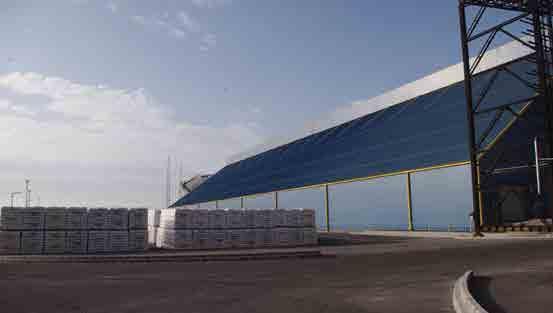
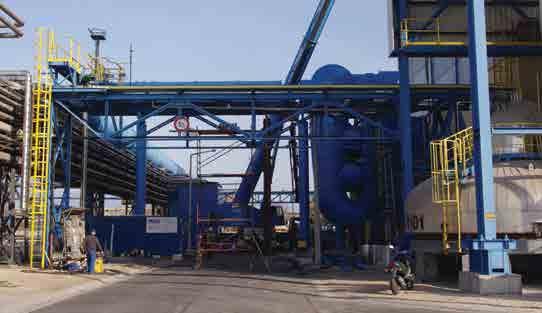
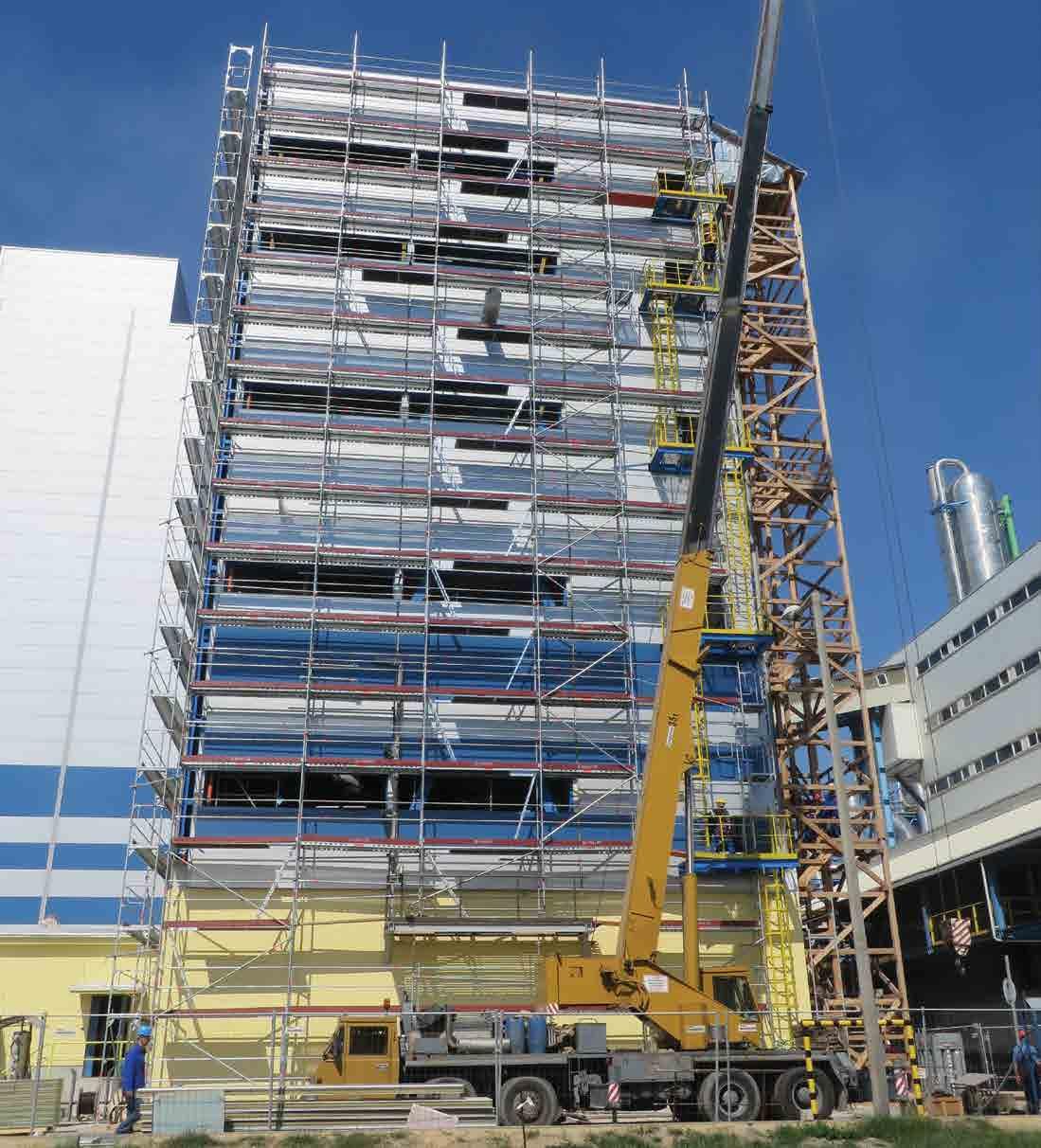
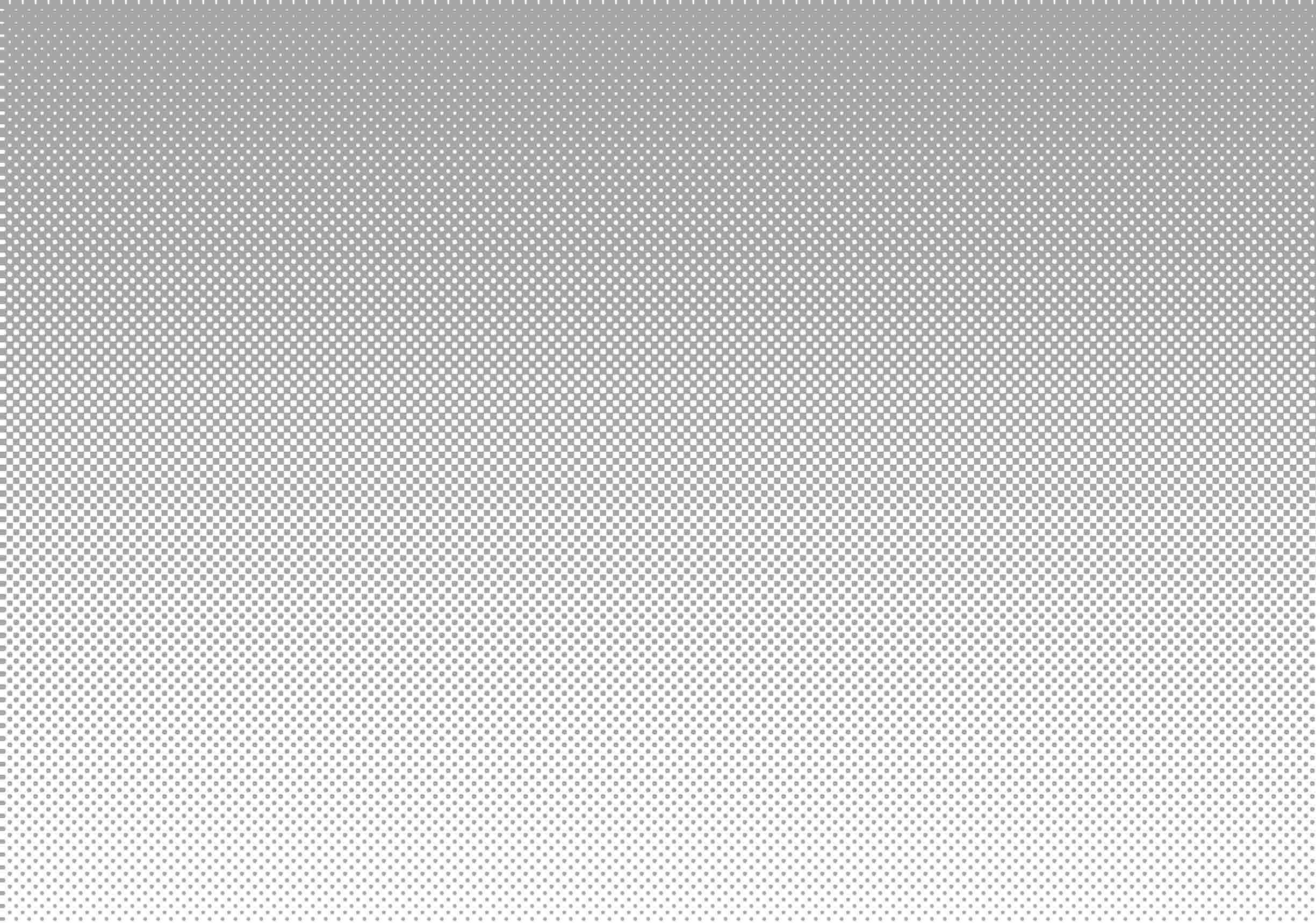
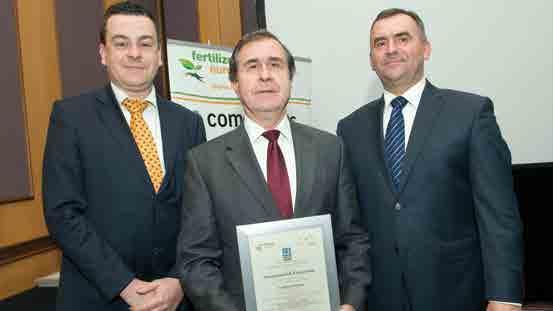
