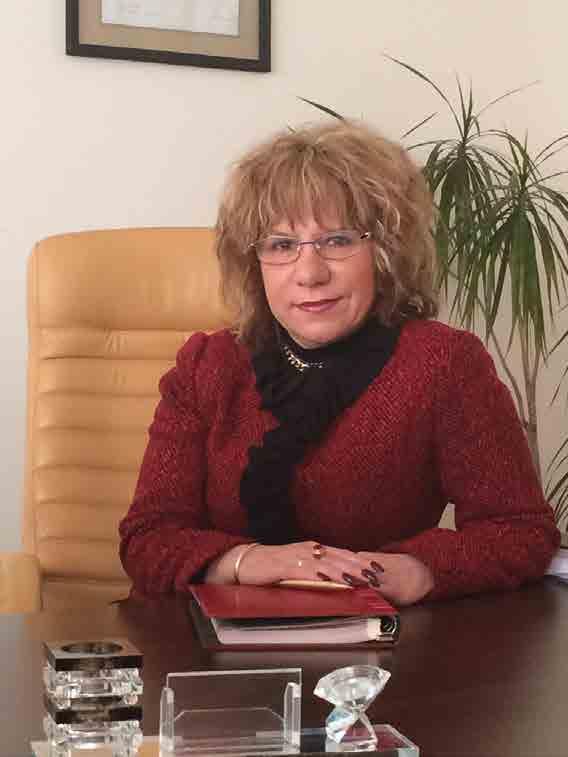
5 minute read
A strategic focus Alcomet
Alcomet AD, a leading Bulgarian manufacturer of rolled and extruded aluminium products, is leveraging its competitive advantages in an attempt to extend its footprint from the Balkans to the rest of the Europe. Vanja Švačko took the opportunity to speak with Mrs Neli Toncheva, Alcomet’s sales director, about the company’s main areas of investment and approach to portfolio management.
A STRATEGIC FOCUS
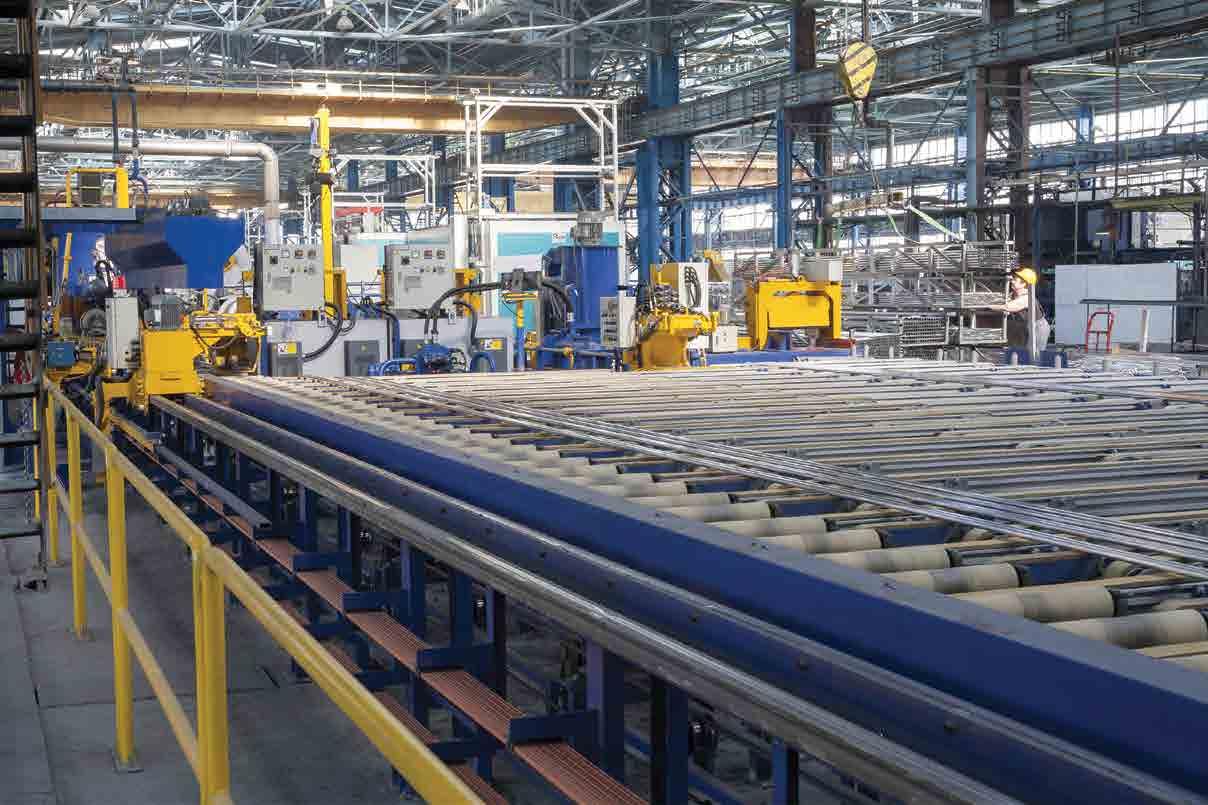
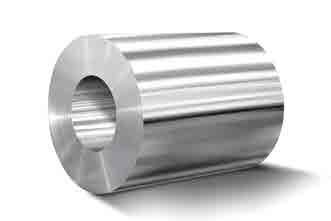
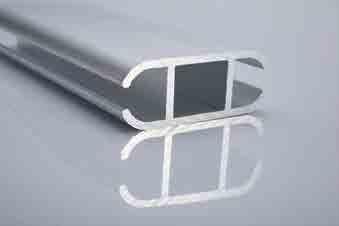
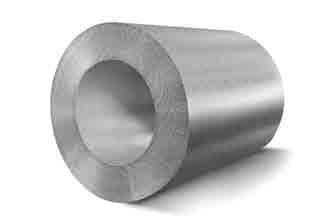
Although the project to build up an aluminium processing plant was initiated much earlier, Alcomet was inaugurated in 1981. Since that time the company has been producing foils (household, technical, container foil), profiles (anodised and powder coated profiles), sheets and strips that cover cast, rolled, extruded and packaging products with an annual capacity of 65,000 tonnes at the present moment. The company’s production site covers an area of 370,000m2 in the city of Shumen and has 890 employees. More than half of Alcomet’s products are exported to Germany, Poland, Italy and North Africa.
Over the past decade Alcomet has invested €75 million in production facilities that today consist of casting, rolling and extrusion shops. For its compliance with the highest quality management and environmental standards the company has been certified according to ISO 9001, ISO 14001, OHSAS 18001 and EN 15088:2005. A sustained investment cycle
Alcomet’s history is that of ongoing investments combined with portfolio expansion and a growing market presence. Mrs Toncheva explains, “The consumption of rolled aluminium products in Bulgaria is insufficient in comparison to how much we can offer. With only 8 per cent of production remaining here and 90 per cent sold to our European customer base, our investments and product development are designed to pursue value growth to meet the quality standards of markets worldwide.”
In 2012 Alcomet bought a new rolling mill from an Italian manufacturer, that has enabled it to increase its rolling capacity up to 30 per cent. Mrs Toncheva continues. Alcomet already has a strong presence on the foil market and we achieved 22 per cent of the European household foil market”. The new mill has given us an excellent opportunity to develop other products and to extend them to foil for heat exchangers (finstock), foil for the automotive industry, flexible pipes, yoghurt lids and other packaging materials used in the food industry such as foils for lamination, printing, extrusion etc.”
The next big investment, in 2014, was in a new 600-tonne press that has encouraged the company to look into a new market niche. Using this machine, it is now extruding small aluminium profiles weighing between 50 and 100 grammes per metre, where surface quality and surface treatment are of the utmost importance.
The opening of new market segments has allowed Alcomet to upgrade its portfolio because the new extrusion press, along with an automatic cutting line and CNC machine, has allowed it to focus intensely on complex value-added extruded products.
“We have invested in machines that can carry out additional processes, such as cutting, drilling, and so on,” says Mrs Toncheva. “We have also improved our anodising line,

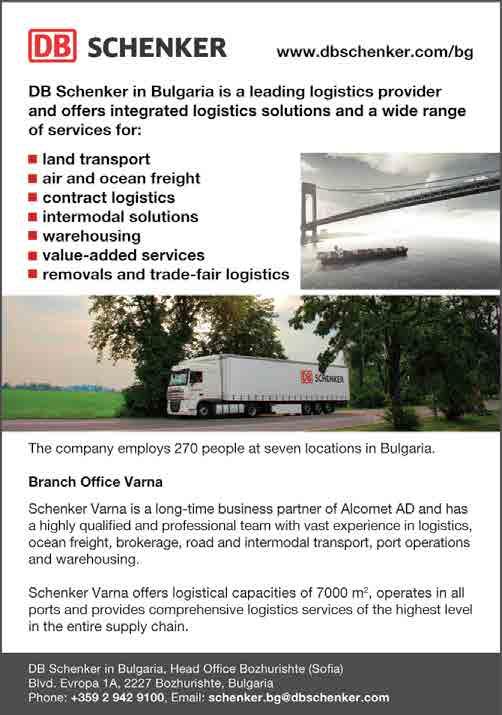
SIAD
SIAD is a leading Italian chemical group and supplies a full range of industrial, specialty, food and medical gases. SIAD is present in twelve European countries, with sales branches and production plants.
SIAD Bulgaria is a proud supplier of Alcomet AD of a wide range of gases used in the whole production process. Gaseous nitrogen is used as a protective atmosphere for the annealing of Aluminum coils, while liquid nitrogen is injected directly into the Aluminum extrusion presses to improve product quality and extrusion speed. Argon is injected in the molten Aluminum bath for enhancing final cast quality, acetylene is used as a lubricant in different processes and CO2 is an important fire extinguishing agent.
A whole number of compressed and packaged gases are also employed for different activities, from ordinary maintenance to extrusion dies nitriding.
for which the finishing operations and surface treatments are performed on the profiles for interior design. Special investment efforts in a powder coating line and anodising line will enable us to stand out from our competitors in the market and to move forward.”
Pursuing green solutions
Aware of the increased demand for aluminium foil in areas such as the packaging and heat exchanger markets, Alcomet is intensifying its presence in the food, automotive and construction industries. Indeed, that is one of the future goals for the company – more value-added and finished products for these sectors, as well as the distribution of profiles in larger volumes than ever before.
In addition, it should be remembered that the production of aluminium, a ‘green metal’, goes hand-in-hand with eco-awareness. Using aluminium helps companies to meet very strict environmental criteria and offer eco-responsible solutions.
In addition to improvements in waste management, recycling, the reuse of aluminium scrap (melting furnaces) and the utilisation of by-products, several investments have recently been made in the installation of modern purification facilities and upgrading the waste water purifying station in the extrusion shop.
“Creating a sustainable built environment is extremely important to us,” states Mrs Toncheva, “because of the direction we are trying to take in introducing ourselves as a viable partner abroad. It is not all about consumption and profit; it is also about offering eco friendly products that can be energy and cost efficient.”
Parallel to a successful business strategy, the company has implemented steps to ensure a sustainable social and economic environment. The company’s continuous initiatives are designed to support the educational, economic and cultural growth of Bulgarian society. Its ability to capitalise on its three decades of in-house expertise and growing market demands suggests that Alcomet is poised for significant growth in the years to come. n
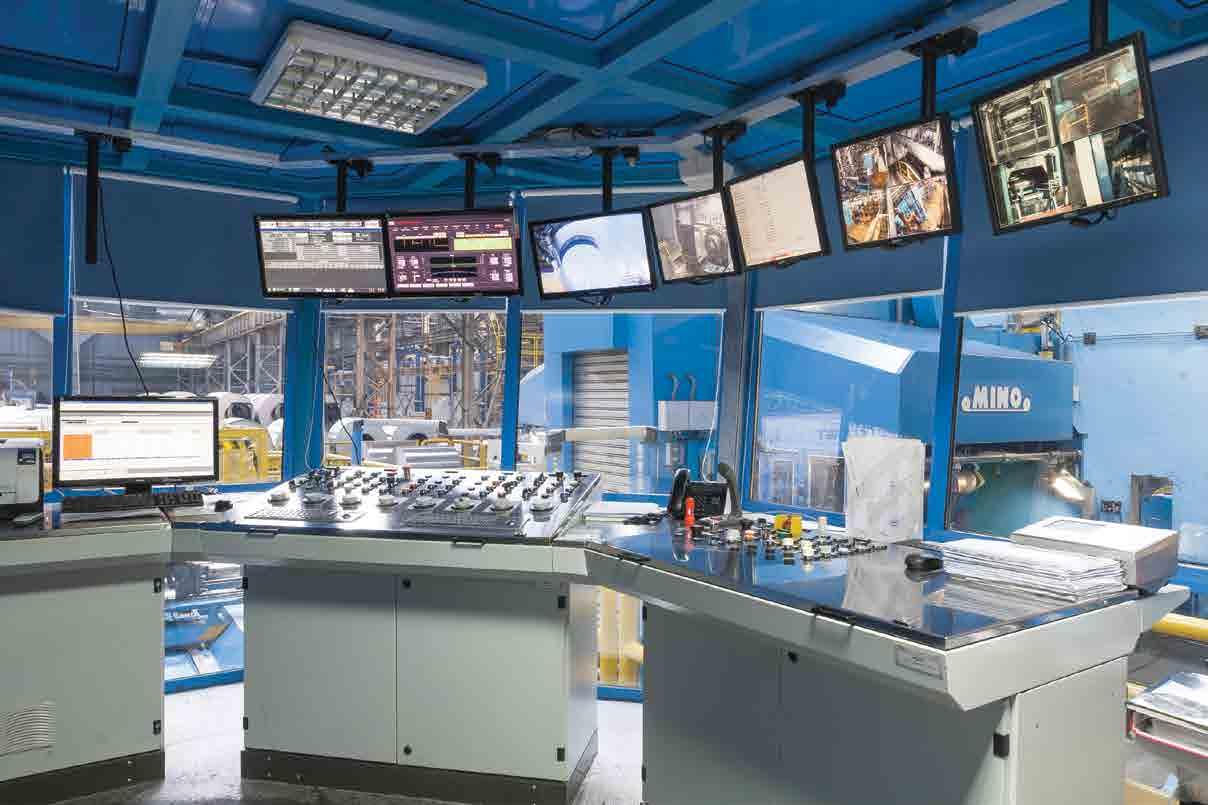
Visit: www.alcomet.eu
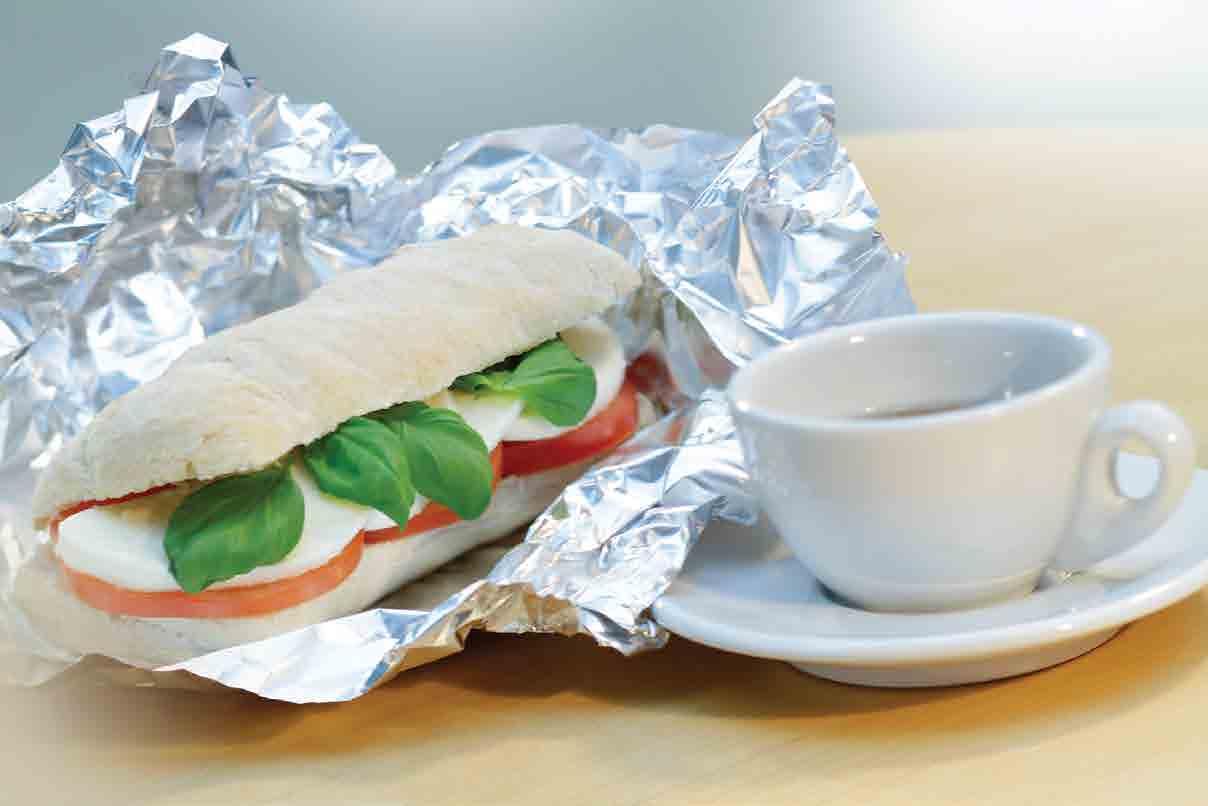
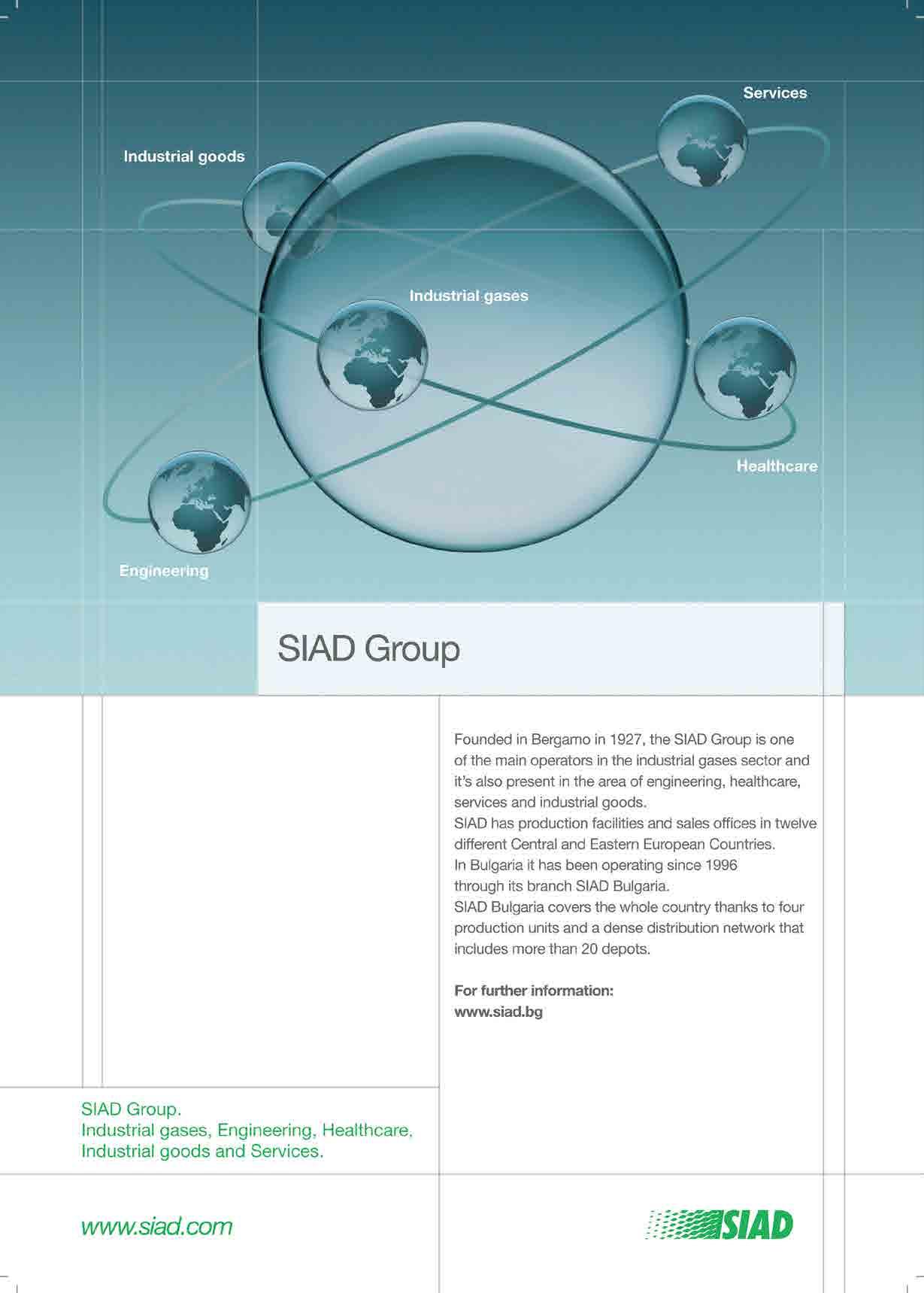