
6 minute read
Pioneers in abrasives technology Ekamant
PIONEERS IN ABRASIVES TECHNOLOGY
Ekamant AB is a market leader in the design and manufacture of advanced coated abrasives for the world’s wood industry. Philip Yorke looks at an innovative company that continues to set new standards and win market share in a highly competitive market.
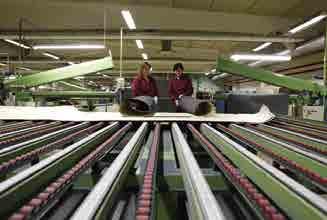
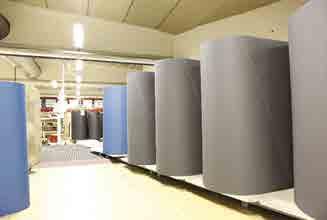

Ekamant is one of the world’s leading producers of coated abrasives for the wood industry. The company was founded in Markaryd, southern Sweden in 1928 and today its products are sold in more than 50 countries worldwide. Around 90 per cent of Ekamant’s sales come from global export sales. Today the company employs more than 500 people and has an unrivalled international network of dedicated local agents and distributors.
Diverse applications
Ekamant’s coated abrasive products are sold directly to distributors as well as to a diverse range of manufacturers in the wood industry. These include furniture makers, boat-builders, producers of kitchen cabinets and wood flooring manufacturers. Ekamant products can be found in large industrial manufacturing plants, as well as in small woodworking businesses from China to the USA.
The company’s product portfolio continues to expand to meet the changing needs of the market and it now produces abrasives for the preparation of car bodywork and for use with composite materials such as fibreglass. Ekamant’s products are designed to be used by the wood industry in the form of wide or narrow belts or discs. At its extensive manufacturing facility in southern Sweden, the company produces abrasives in ‘Jumbo’ reels, before sending them on to conversion plants throughout the world. Globally, Ekamant has subsidiaries in Indonesia, China, Poland, Estonia and South Africa as well as the USA. The company recently announced that it has established a new subsidiary in Moscow, Russia, which is a market destined to play an important role in Ekamant’s future sales.
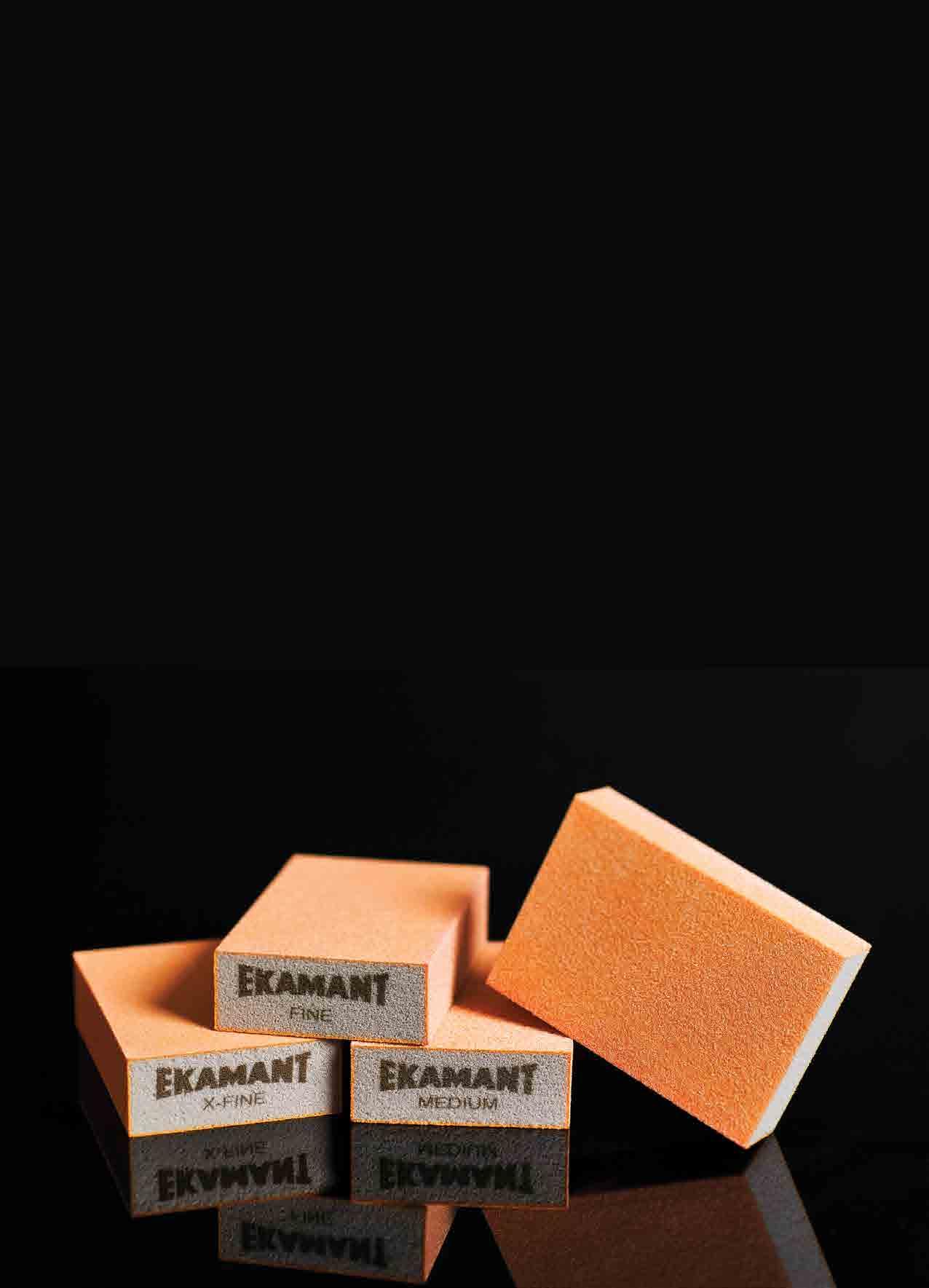
Increasing global reach
In addition to its existing distributors worldwide, Ekamant has appointed a new distributor in Morroco, which is a leading abrasives converter for the Morrocan market. Abraforme is based in Casablanca and will be the exclusive distributors of Eakamant products in the region. The company is a leading producer of abrasive belts, rolls and sectional belts that utilise a wide range of materials for use in the glass, wood, metal and stainless steel industries. Further a-field, Ekamant has entered into a new distribution agreement with S&G Abrasives of Aukland, New Zealand. This company was established in 1973 and has been appointed as Ekamant’s business partner in New Zealand. S&G has extensive expertise and experience concerning coated abrasives and has a major presence in the New Zealand market.
Furthermore, Ekamant has also increased its presence in the Middle East with the appointment of a new distributor in Bahrain. Modern Abrasives will act as distributors for the markets of Bahrain and Saudi Arabia. The company’s production facilities will cover the full conversion of all Ekamant’s abrasive materials.
One of the most important developments recently has been the merger between Ekament Production AB and Ekamant Scandinavien AB in 2014. This has already resulted in improved efficiency and therefore today Ekamant AB is the only legal entity.
Innovative new products
Ekamant has always placed a high priority on its commitment to produce innovative products that meet the individual needs of its customers. With the on-going growth in demand for polished wooden flooring, the company has developed a high-performance abrasive with an aluminium oxide grain coating. This is designed for sanding floors made of hardwood species such as oak, cherry, walnut and beech. As these parquet floors become more popular, the company developed its ‘Clearcut’ range to meet the new demands for hardwood flooring in Europe.
More recently, Ekamant launched its ‘EKA GOLD’ range, which is available in blocks, pads and super pads to meet a wide range of new industrial applications.
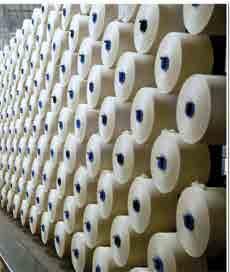
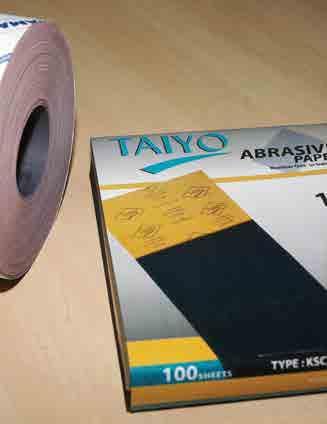
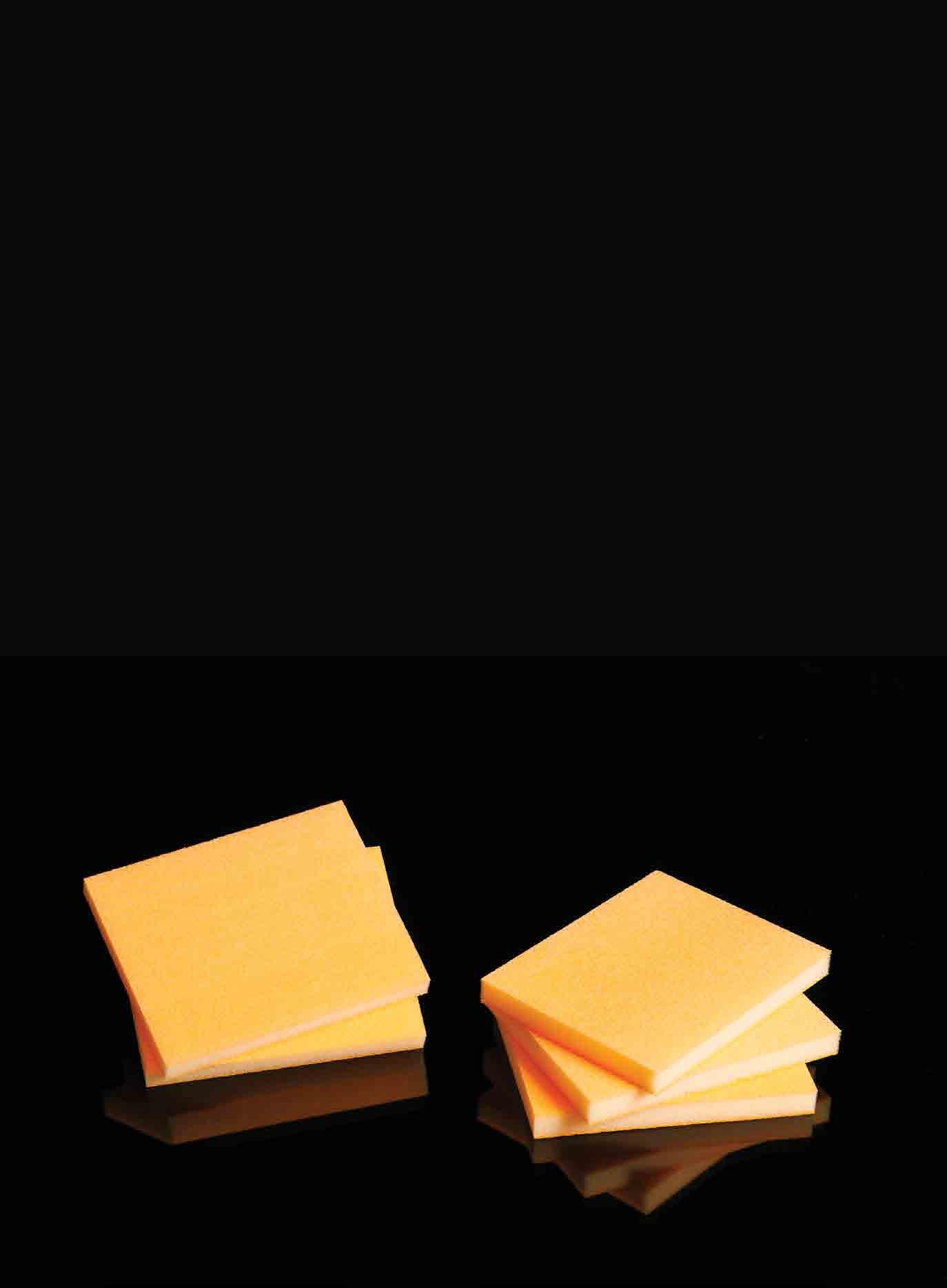

Investing in sustainability
Ekamant takes its responsibilities concerning sustainability and the environment very seriously. The company has been working in close cooperation with E.ON Energy on new initiatives to reduce energy consumption and waste products at its main production facility in Markaryd, Sweden.
The modernisation of its main plant is designed to increase efficiency and to significantly reduce energy consumption throughout its manufacturing processes. This new initiative will reduce Ekamant’s energy consumption at its primary production plant by 1000 Mwh/year. Furthermore, in another joint investment project with E.ON Energy, the company will harness the waste heat that leaves the company’s manufacturing processes and turn it into heating for local residents. Ekamant in cooperation with E.ON also plans to convert its whole heating system from oil to remote heating sources, which will reduce its energy requirements by a further 500 Mwh/year.
High quality materials
Quality control is at the heart of Ekamant’s value chain and it is therefore most careful in its selection of raw materials. In order to produce the highest quality abrasives the company relies only on the highest quality materials. This applies to all its components, which are divided into three key groups. The first group involves backing materials, which consists of special paper fabrics. The second group of raw materials are binding agents, the most common of which are urea or phenolic resins. The third group relates to the abrasive grain, which is the working part of the abrasive material. This is usually made of aluminium oxide, silicon, carbide and also other special products such as zircona. n
For further details of Ekamant’s innovative abrasive products and services visit: www.ekamant.com
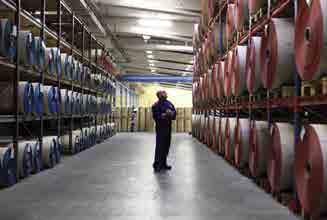

Know- how & automation are both major assets for the company FILATURES ET TISSAGES DE SAULXURES SUR MOSELLOTTE group Incopar France.
FTS runs 1 spinning and 1 weaving unit with high technical performance for the production of industrial fabrics. Our Cloths fi nd applications for abrasive coating supports, special textiles for cable lining, or any other industrial use.
Textile group Incopar means: • 3 Spinning • 4 Weaving • 2 Manufacturing
Our strength & technical performance: • Production of individual tailored coating supports. High quality criterias: • Raw cotton is chosen with greatest care coming from Central Asia & US. • Our internal lab carried out a large number of test continuously (regularity, resistance, metric counting…) • Our Label “Made in Vosges” is a guarantee of the highest standards. • Weight, resistance and thread count are closely analysed.
Our facilities include an 8000m² automated weaving unit specialising in Open End yarns of the textile group. The 3 spinning units produce around 1100 tonnes of yarn per month, amounting to 4 million lineas meters per month.
At a time when change is the only constant, FTS is looking forward to provide stable business and innovative solutions.
