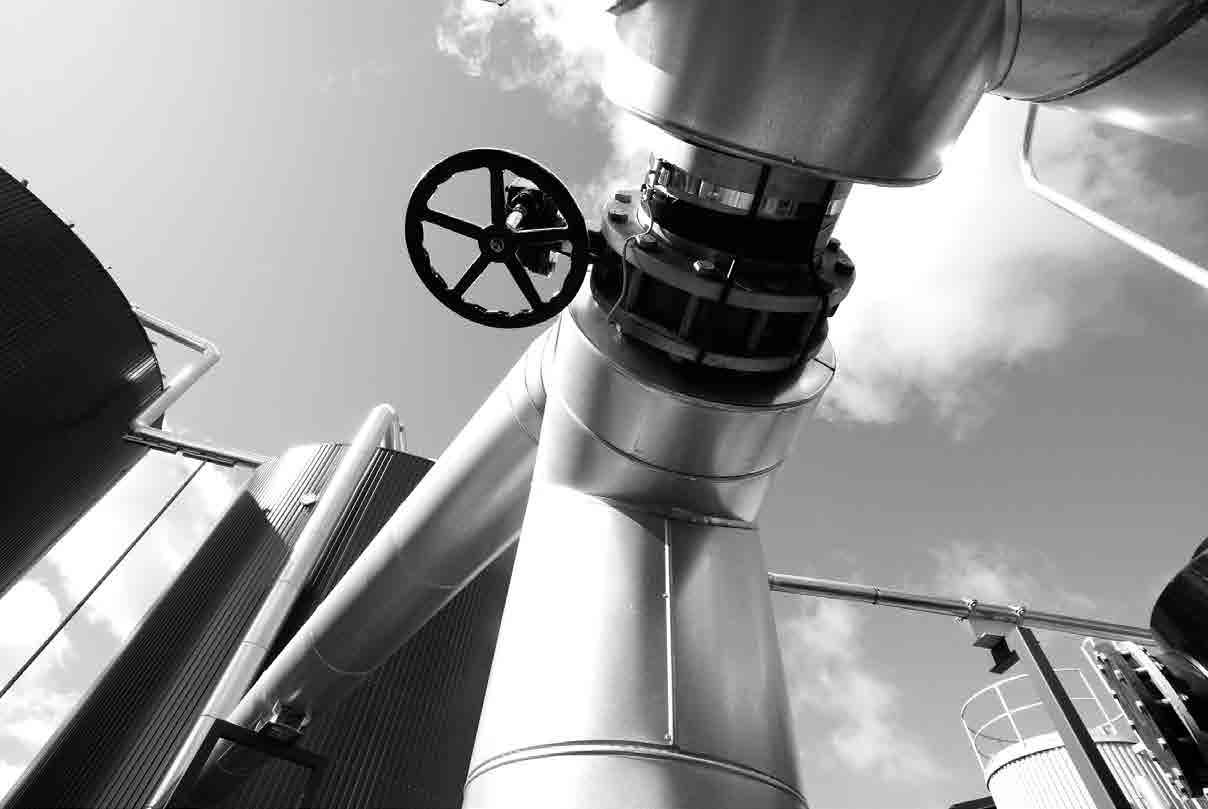
5 minute read
From shape to solution Calvi
FROM SHAPE TO SOLUTION
The Italian Calvi Group is a leader in the metallurgical and mechanical sectors. At this year’s Hannover Messe show it will be presenting some of its innovative processes for the manufacturing of customised steel profiles. Daniele Garavaglia reports.

The Calvi Holding is a group formed by 10 Italian and foreign companies, accounting for a total of 765 years of experience in the metallurgical and mechanical fields, with an aggregated turnover of €313 million (+8 per cent over last year), an estimated a gross operating margin of €27.2 million (€18.7 million in 2013) and 1400 employees. It was established in 2004 “to create value based on a network model, which develops synergies to provide its clients with products and solutions that are increasingly innovative and competitive,” explains Mr Riccardo Chini, president of this ‘pocket-sized multinational’ supplier.
From its headquarters in Agrate, near Milan, Calvi Holding leads two different networks: Calvi Network Special Steel Profiles (including Calvi, Falci, Fiav, Siderval, Sipa, Cefival, Hoesch Schwerter Profile, and Rathbone Precision Metals), and undisputed global leader in the design and manufacture of special steel profiles based on customer specifications; and Calvi Network for Material Handling (Lift-Tek Elecar and Lift Technologies), for the design, engineering and manufacturing of lifting units for forklifts.

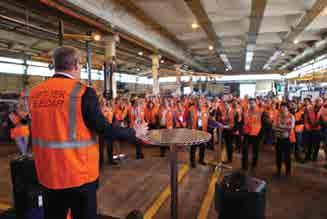
The networking model wins again
“Our subsidiaries located in Italy and abroad are the key to our entrepreneurial networkingbased model. This strategy enables each company to work independently but values their action and service, and allows for the sharing
of know-how and networking processes, technology and solutions. Instead of a hierarchical decision-making structure, our network model offers authoritative strategic coordination whilst leaving each company with the autonomy and independency to reach its own targets.”
According to Mr Chini, “The world manufacturing industry is experiencing a growing demand for the deformation of long steel products and other special materials in order to bestow precise mechanical characteristics upon them, whilst maintaining their stability and reducing dimensional tolerance.” This is exactly the direction Calvi Group has taken through the different stages of its development: from the merging of Calvi and Siderval, two small group of companies that engineer and manufacture long steel products, to create an established specialist on the European market, through to the incorporation of Hoesch Schwerter Profile, to widen the range of hot extruded products and acquire hot rolling capacity for large size profiles. Another important milestone was the strengthening of the group’s position in North America with the acquisition of Rathbone and the establishment of local production capacity, as well as the supply of vertical integrated solutions, from single profile to masts and complete front-end units for forklift trucks through the acquisition of Lift-Tek group.
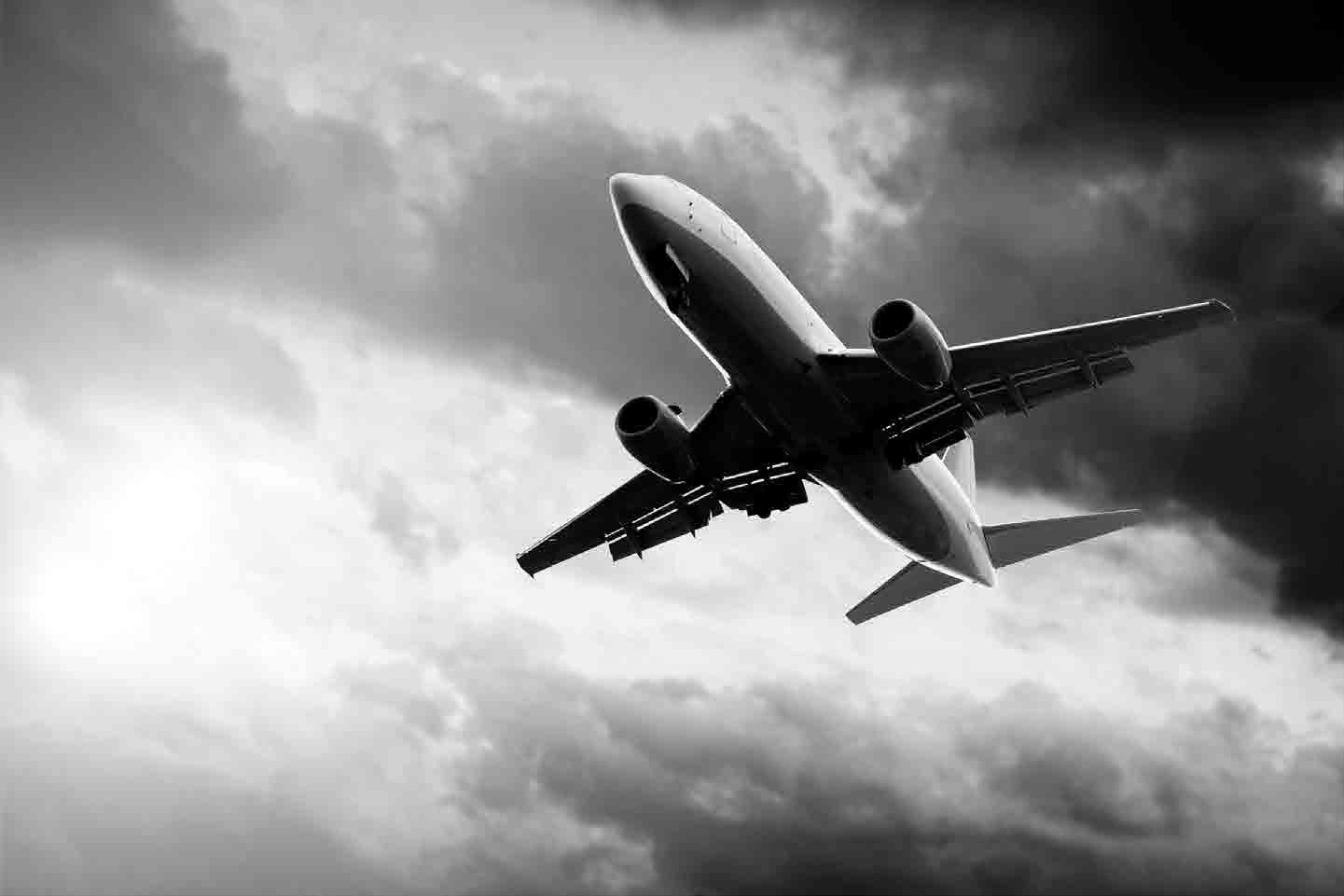
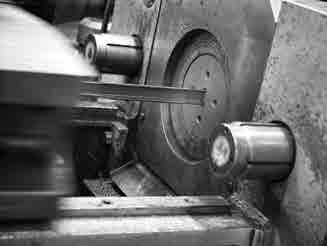
Manufacturing plants in four countries
The Calvi Group currently has manufacturing facilities in four countries (Italy, Germany, France and the USA), with marketing trends that depend on different process technologies (cold drawing, hot extrusion, hot rolling) and on the industries supplied. In Mr Chini’s words: “In 2014 cold drawing companies increased their activities by leveraging on recovered investments in sectors such as automation, special tooling machinery and systems for the automotive industry.” In these sectors, dimensional accuracy and close tolerances, smooth and scale-free surfaces, complex geometries and sharp edges, enhanced mechanical properties and metallurgical structure are important properties when it comes to choosing a profile. In fact, Calvi’s manufacturing capabilities and quality are based on the absolute reliability of its processing plants: a range of machinery that is perfectly calibrated in relation to the most complex manufacturing requirements.
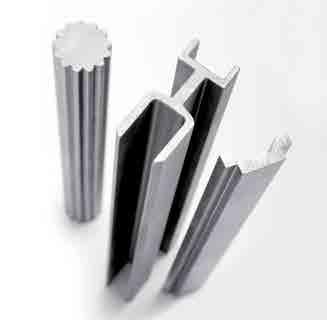
Oil, gas & logistics driving growth
“Companies manufacturing hot extruded profiles have enhanced their process flexibility

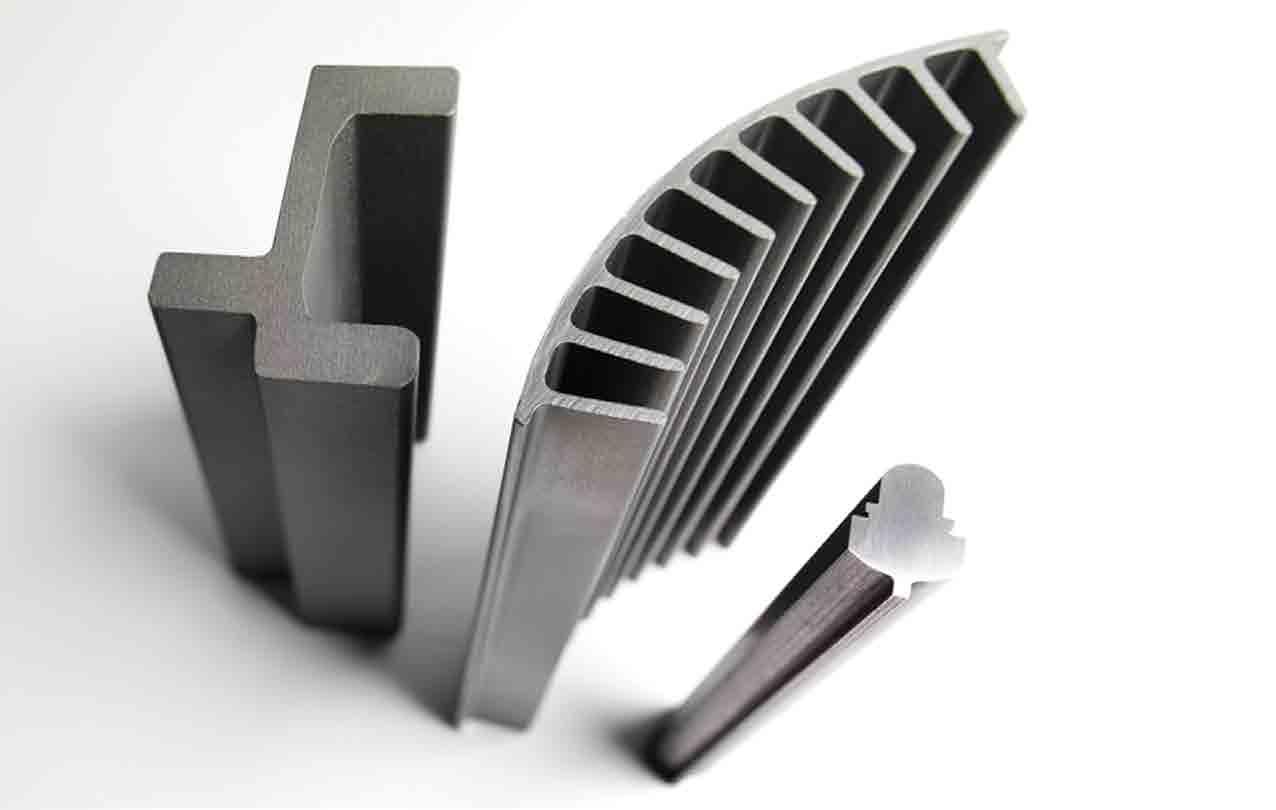
in order to meet irregular demand, generated mainly from retro-fitting projects for energy production plants and system building in the oil & gas industries,” Mr Chini continues. In this field, Calvi quality means guaranteeing complex seamless sections, solid or hollow, limited tooling and prototyping costs, flexibility on minimum volumes, and a wide range of materials for highly demanding applications.
“Our hot rolling facility in Germany has achieved positive growth thanks to the increased demand from the logistics sector. The same happened for our mechanical branch manufacturing customised lifting units for forklifts starting from hot rolled profiles.” Besides logistics, the railroad, agricultural machinery and automotive industries also rely on Calvi profiles for the superior mechanical properties of their components when submitted to particular stresses.
The optimum performance Calvi offers for the metallurgical industry goes hand-in-hand with the growth of its mechanical network, for which Lift-Tek designs and manufactures masts and integrated solutions for material handling. Its range includes masts, carriages, integral sideshifters, fork positioners, reach carriages and related components. Masts can lift weights of up to 15 metres with capacities up to 52 tonnes. Lift-Tek is a preferred supplier of all the most renowned OEMs.


Internationalisation and process innovation
Exploiting its consolidated know-how, the Calvi Group has always shown a strong tendency towards internationalisation. Its strategy relies on a wide international network including an in-house sales team of 50 people, about 90 agents in 25 markets, and 40 local agencies. This dedicated team of staff promotes the group presence during fairs and exhibitions, such as the upcoming Hannover Messe. “We consider this fair to be an unmissable event. It is not because of the new and many profiles that are being displayed, but for the appraisal of investments and process innovations that we keep introducing in our industrial system. All of the companies in our group are working in this direction. Among the most significant innovations, I’d like to mention specific plants for the stretching of titanium alloys and the start of hot-extruded bimetal tubes,” concludes Mr Chini. n