
4 minute read
Optimising air-core reactors Trench Group
OPTIMISING AIR-CORE REACTORS
The Trench Group is a global leader in the design and manufacture of high-voltage components including instrument transformers, bushings and coil products. The company continues to see strong growth and has been responsible for some of the world’s largest power installations. Philip Yorke reports.
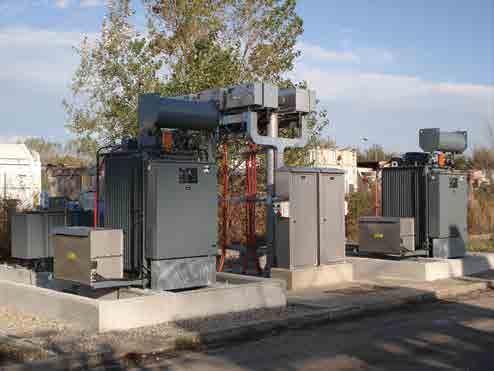
The Trench Group was founded in 1954 by an Austrian electrical engineer called Alois Esslinger and the company was named after him until 1990, when it merged with Trench Electric of Canada.
From the outset the focus of the company was on the development and production of reactors for electrical power systems. In the 1950s the company helped to pioneer the revolutionary use of glass fibre reinforced plastic as part of the insulation of reactors. Today the Trench Group is a member of the Siemens family and consists of 12 plants and sales offices in eight countries with more than 3000 employees worldwide.
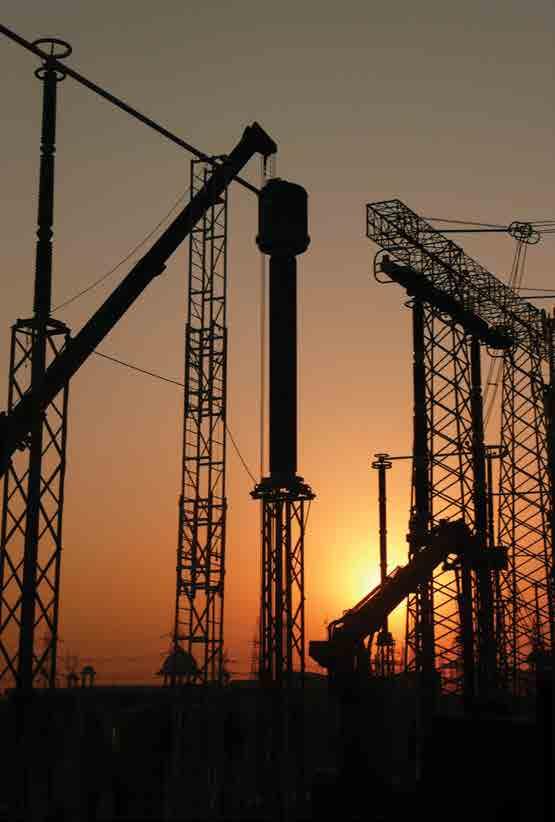
World’s largest air-core reactors
Recently Trench completed an order for the world’s largest high-voltage current-limiting reactors, which are also the biggest AC dry-type air-core reactors of their kind anywhere on the planet. The 500kV grid in the north-east area of Shanghai had encountered serious problems with the available short-circuit current. Trench provided the optimal solution for the State Grid Shanghai Municipal Electric Power Company and is now reflecting on six months of satisfactory operation.
An important node in the grid is the company’s Yanghang substation. It is the key 500kV station in the area with more than 500kV outgoing feeders, among which are two feeders connected to the huge Waigaoqiao fossil power plant in the north-east of Shanghai. Trench came up with the perfect solution, which was to deliver and install six phases of 500kV current-limiting reactors and related 500kV coupling capacitors for the substation.
Gu Enjie, head of domestic marketing for Trench China said, “This success is a success for the entire Trench project team. With several rounds of internal evaluation by customers and investigating electrical engineers concerning the manufacturing and site layout feasibility, the customer was convinced of our technical expertise and accepted our recommendations on the site configuration and its independent coupling capacitors.”
With this project once again Trench was able to demonstrate its technical leadership resulting from more than 60 years of experience, exceptional R&D and a clear commitment to meet the increasing challenges within today’s power industry.
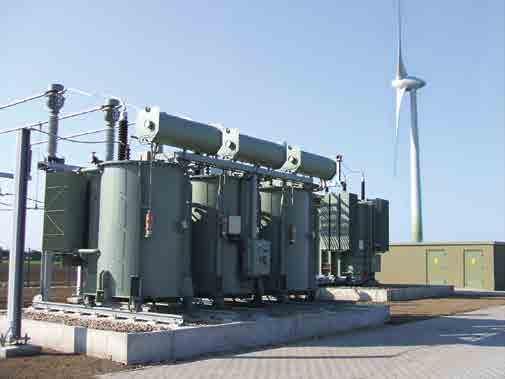
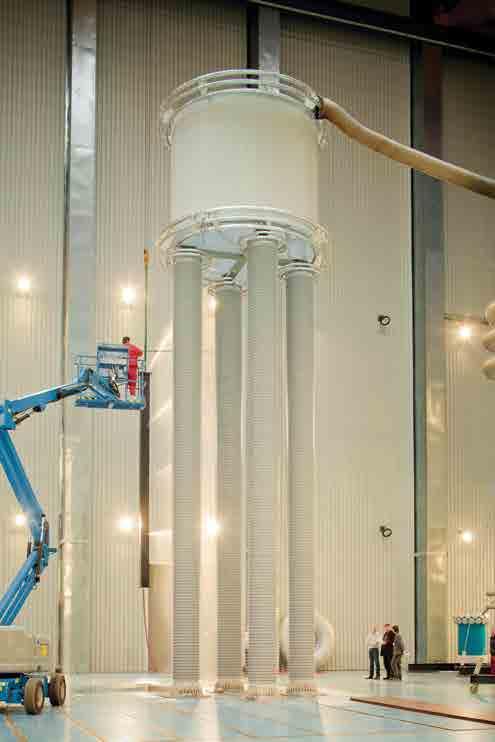

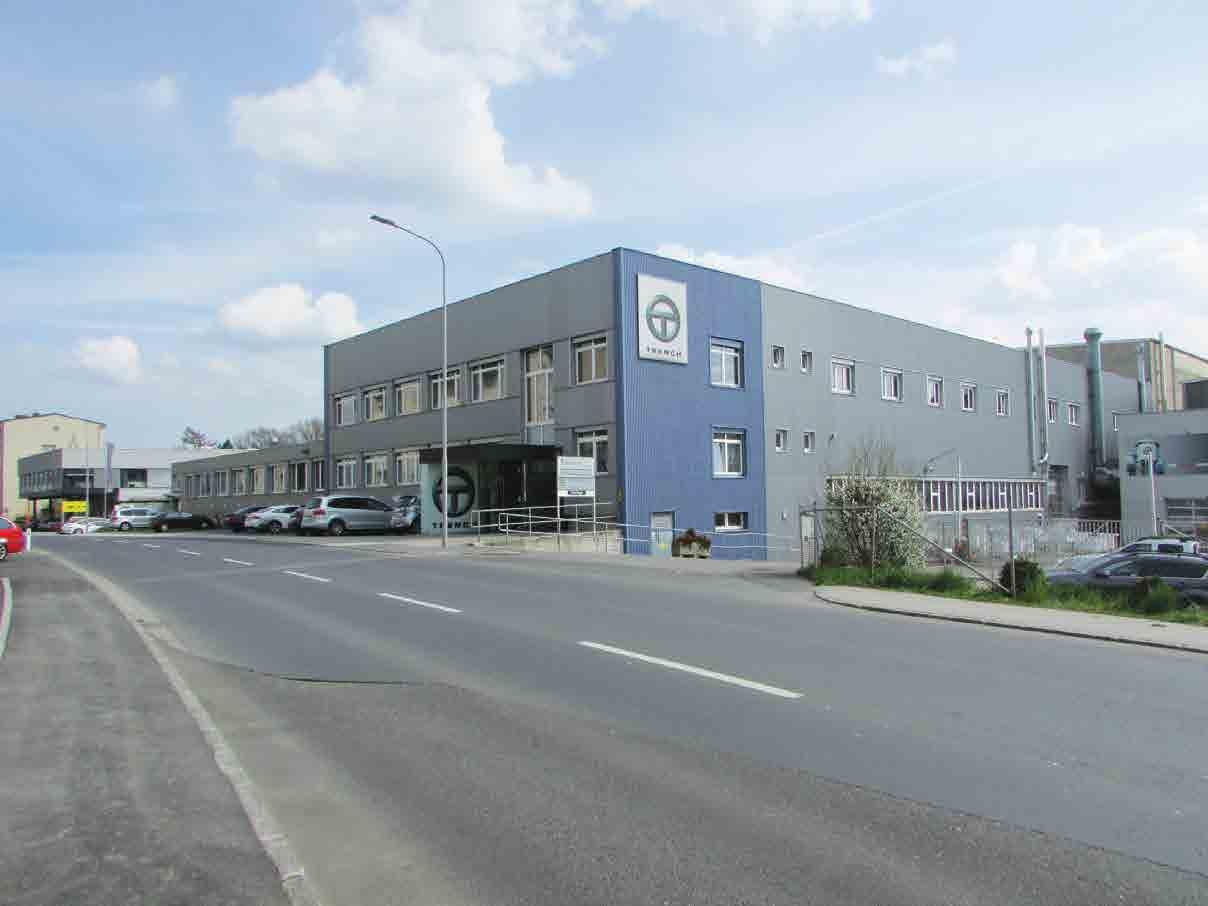
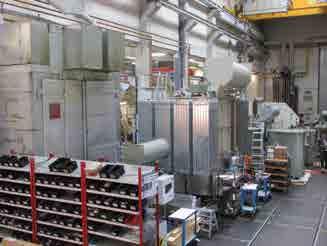
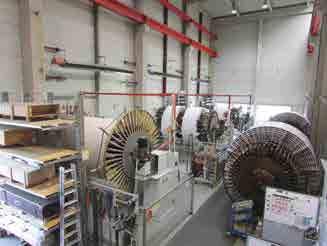
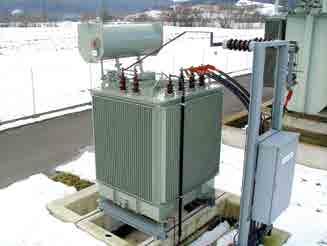
Superior reinforced windings
A Trench air-core dry-type reactor consists of a number of parallelconnected and individually insulated aluminium conductors. These can be small wire or proprietary cables which are custom designed and custom manufactured. These windings are mechanically reinforced with epoxy resin-impregnated fibreglass, which after a carefully defined oven-cure cycle produces a superior encapsulated coil.
Exceptionally high levels of terminal pull, tensile strength, wind loading and seismic withstand can be accommodated with this type of Trench reactor. This unique design can be installed in all types of climates and environments and will still offer premium performance.
Trench air-core dry-type reactors are installed in numerous polluted and corrosive areas of the world and continue to supply trouble-free operation. In addition to the standard fixed reactance type of coil, units can be supplied with taps for various inductance. In addition, Trench utilises various other designs for reactors including iron-core and water cooled examples.
Proven power
Throughout its entire history, the company’s deep commitment to the power industry along with its extensive investments in engineering, manufacturing and test capabilities, has allowed Trench to provide its clients with peace of mind through the exceptionally high quality and reliability of its products.
The components supplied by Trench are individually designed to reflect the needs of their intended applications and are further supported by a dedicated team of engineers that are ‘hands-on’ to provide the best in customer service and advice. The company also differentiates itself as a dedicated solutions provider through its highly developed research and development programme. This constantly addresses new technologies and their potential applications in high-tech reactor products.
The combination of the company’s long history of industrial experience and know-how, coupled with its strong global manufacturing and distribution network has enabled Trench to serve some of the world’s leading ERPC companies. These include Siemens, ABB and GE Grid solutions, as well as well as countless utility companies throughout Europe and the rest of the world.
Over the coming months and years Trench will continue to seek to provide market-leading solutions and products of the highest quality to its clients across the globe. The company’s global network of manufacturing plants will enable Trench to ensure that it is present wherever customer needs or new market opportunities arise.
Within Europe for example the move to renewable energy is increasingly proving a unique opportunity within the power transmission sector. Within Germany for example, the implementation of the ‘Energiewende’ represents a vital change in focus that will spur the development of new, innovative technologies and infrastructure. As a market leader in power transmission solutions, Trench is well placed to play a major role in Europe’s energy transmission and that of other regions of the world. n
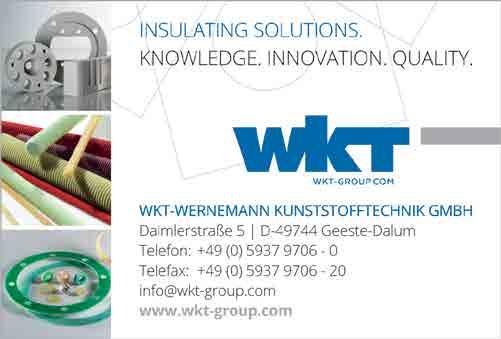