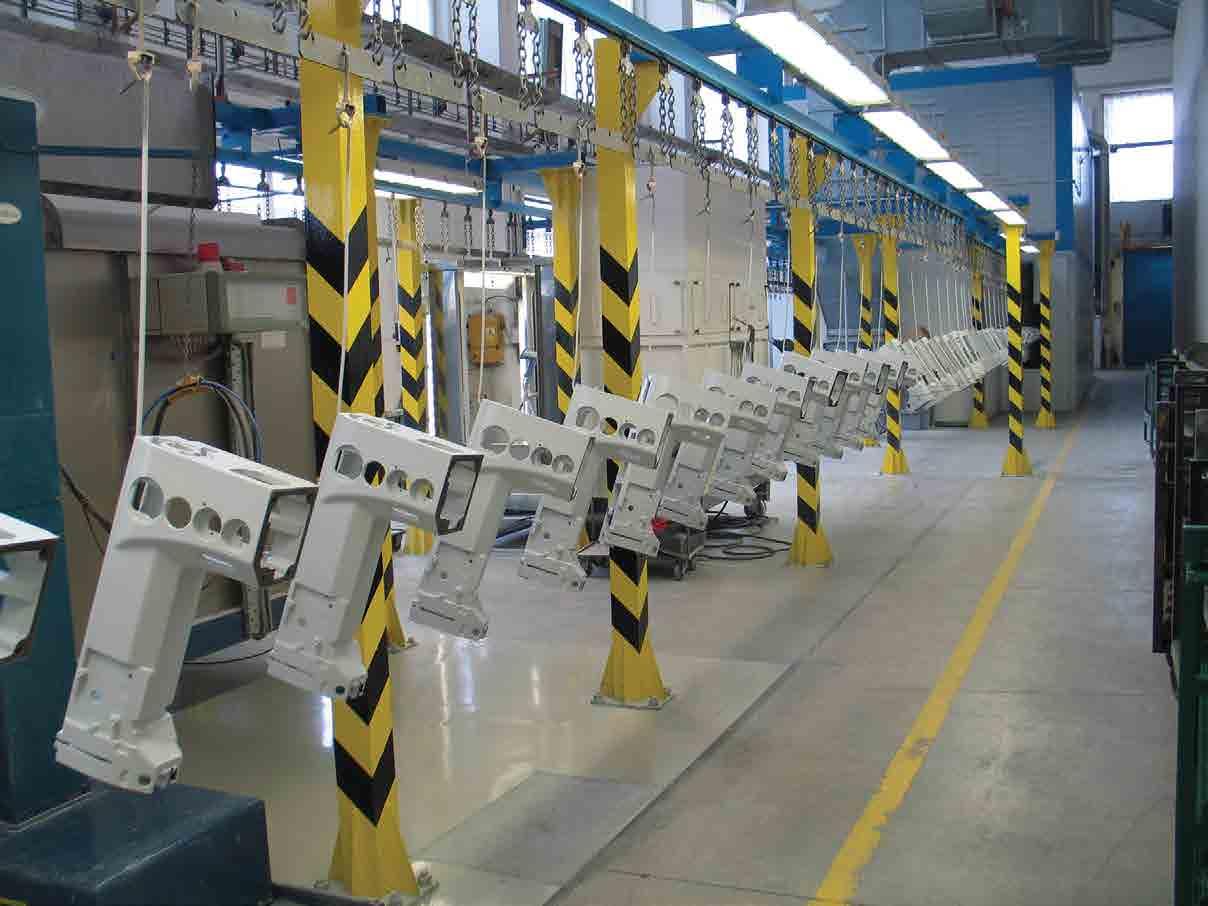
6 minute read
Synergy of tradition and innovation
Minerva Boskovice a.s., a traditional producer of sewing machines, achieved record-breaking sales last year, increasing its turnover by 17 per cent to over one billion Czech crowns. Romana Moares spoke to company managing director and chairman of the board, Mr František Hrda, about its recent successes and its plans for the future.
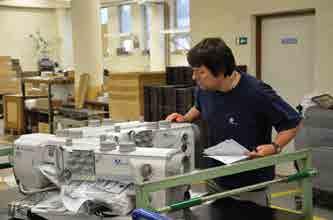
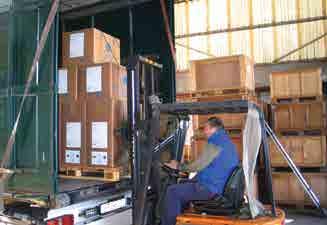
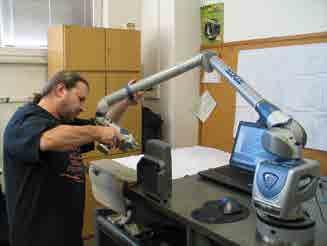
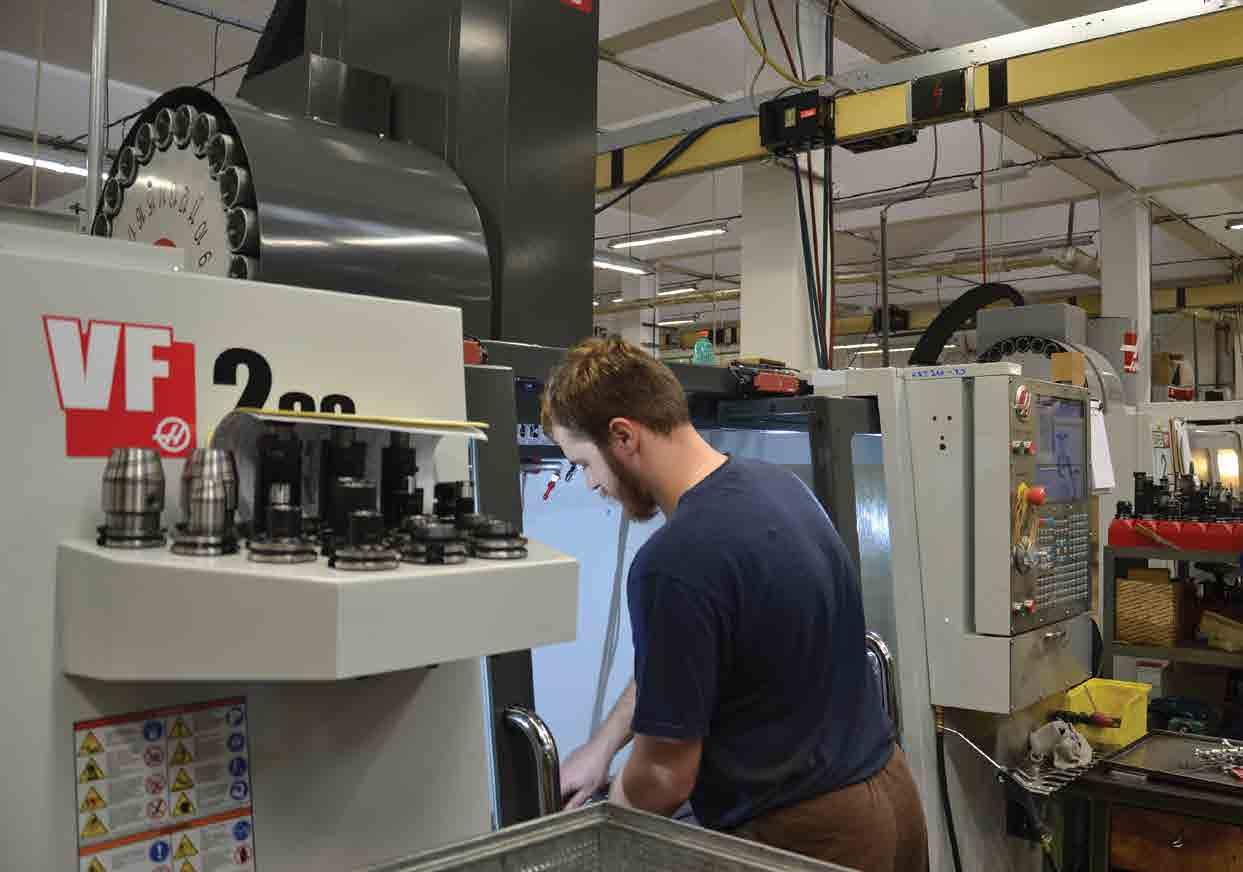
Minerva has been producing industrial sewing machines for sewing garments, leather goods, technical textiles, footwear and automotives for over 100 years. The company currently offers over 160 sub-classes of these machines, made in a wide range of shapes and worktops, with various feeding and sewing machine accessories. One of its key competitive advantages is its research and development capability, focused on technology and product innovation. With a workforce of 750, the company is one of the largest employers in the region.
This year, Minerva is celebrating its 135th anniversary. The company was founded in Vienna as a sewing machine producer, but in 1938 its production was transferred to Boskovice in Moravia. Minerva’s modern history started in 1990 when the business was privatised. Seven years later, the majority stake was acquired by German Dürkopp Adler. Since 2000, industrial sewing machines made by Minerva have been sold under the Dürkopp Adler trade mark. In 2005, as a member of the the Dürkopp Adler Group, Minerva became a member of the Chinese ShanGong Group.
Record breaking year
Minerva exports most of its output and develops long-term contracts. For example, the company delivers hundreds of machines to the Indian Footwear Design & Development Institute, and continues its important contract for Guoli Automotive in China, which sews for large car makers such as Volkswagen. Last year, Minerva increased
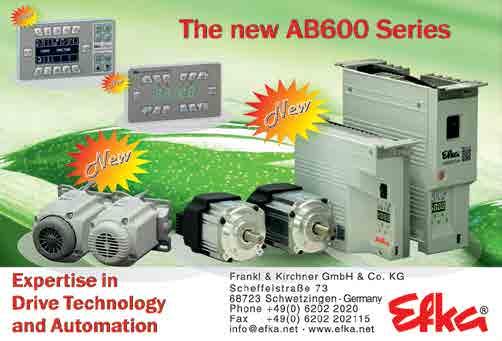
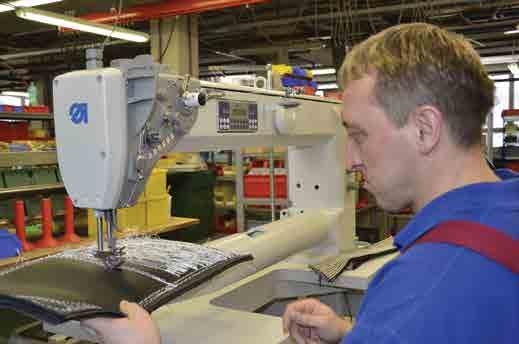
sales in its traditional markets such as Germany, Italy and India and won a significant market share in America and Africa. This was supported by generally favourable conditions in global markets and, in particular, the growth of the automotive sector worldwide.
“In the past two years, the company has recorded a significant increase in demand for its products which was, in 2015, reflected in increased output and sales and continuous extension of capacity,” says the managing director. “In line with this development, headcount also increased and greater emphasis was put on speedy installation and full utilisation of new investments.”
First class products
Industrial sewing machines account for 96 per cent of revenue. The main product groups are the medium-sized M-Type machines for automotive and technical textiles sewing. “Each year we introduce new types of products; the proportion of machines less than five years old is nearly 50 per cent,” says the managing director: “With regard to the lack of qualified human resources in the sewing sector, demand for sewing process automation is rising. This demand is fully met by the new Premium line sewing machines which we introduced onto the market in 2015.”
These modern machines are provided with a DAC Comfort control unit specifically developed by the Dürkopp Adler Group for the control of the drive as well as of the main machine functions, while simultaneously controlling the step motors. They enable quick, precise and pre-defined setting of base parameters for the sewing of a particular product. The Premium machines are fitted with a smart M2M monitoring system (modem and telephone line connection with online data transfer), enabling remote monitoring of the sewing process, simple and quick programme change, failure reporting as well as remote central parameter setting for a particular sewing operation.
Focus on innovation
“To remain competitive in the future, product development competence is not enough – this must be supported by modern production technology to enable fast and efficient implementation of newly developed products,” says Mr Hrda, explaining that production is concentrated in a single operational facility in Boskovice, which boasts all the required types of technology including conventional chip machining, heat treatment, galvanic treatment as well as coating. All of these technologies are modernised on an on-going basis.
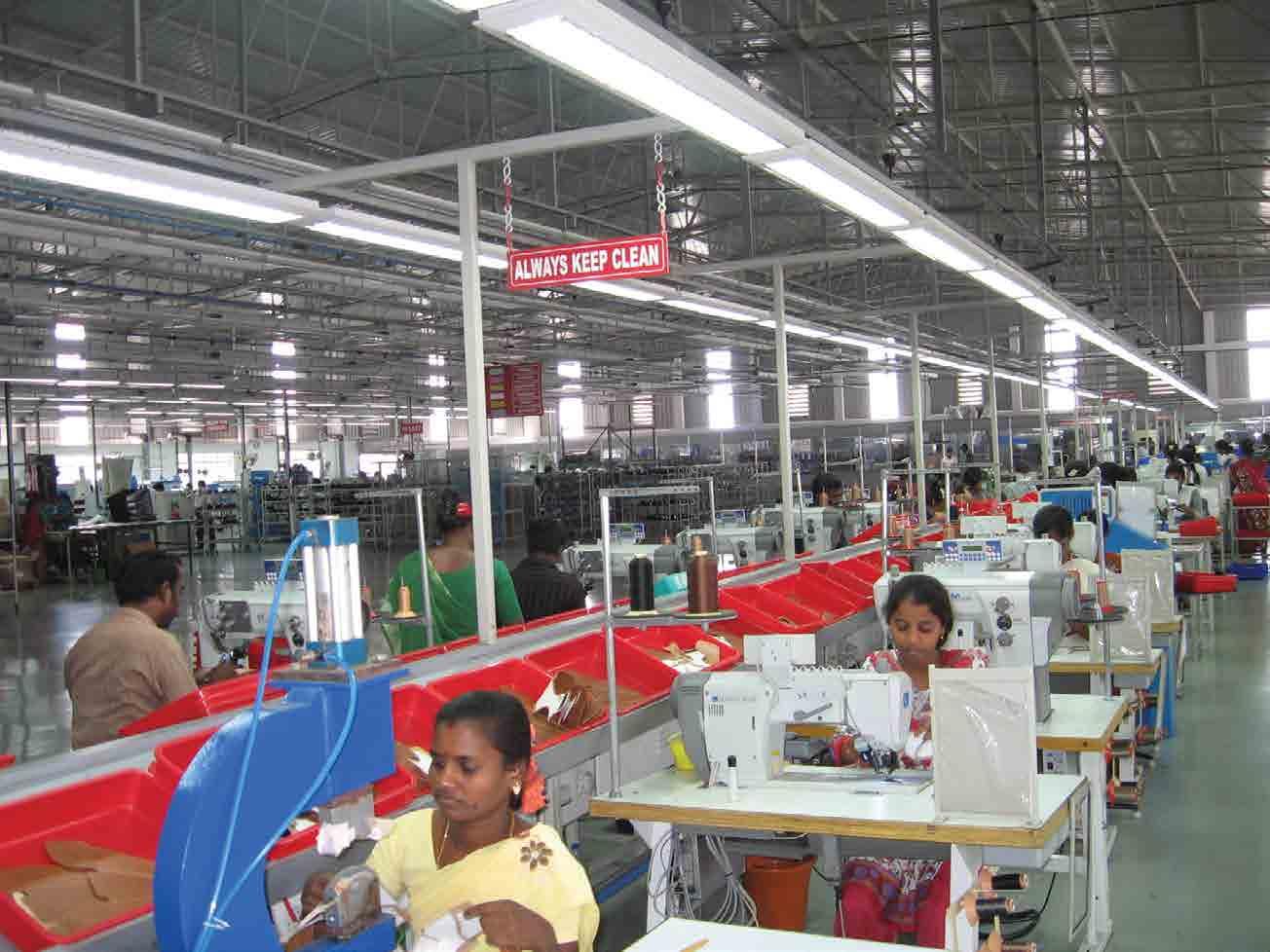
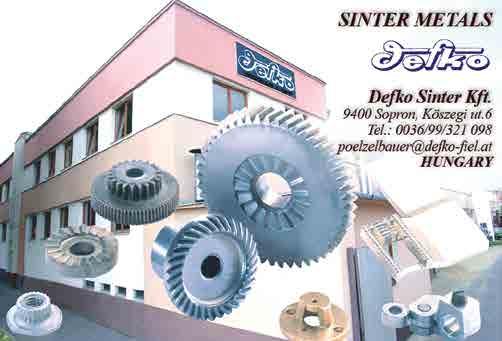
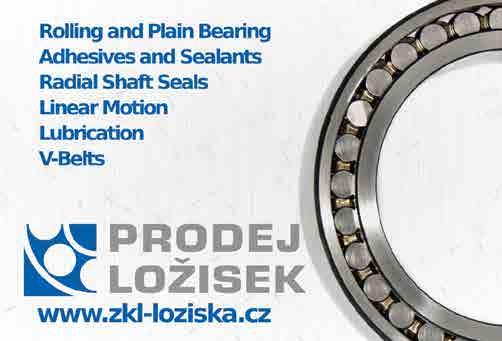
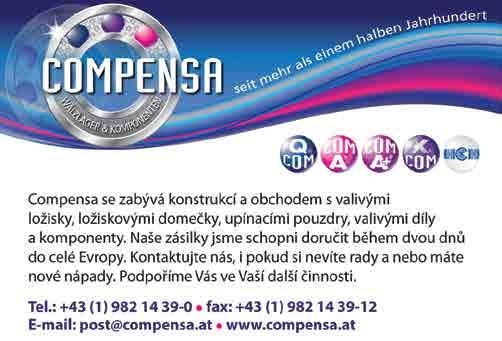
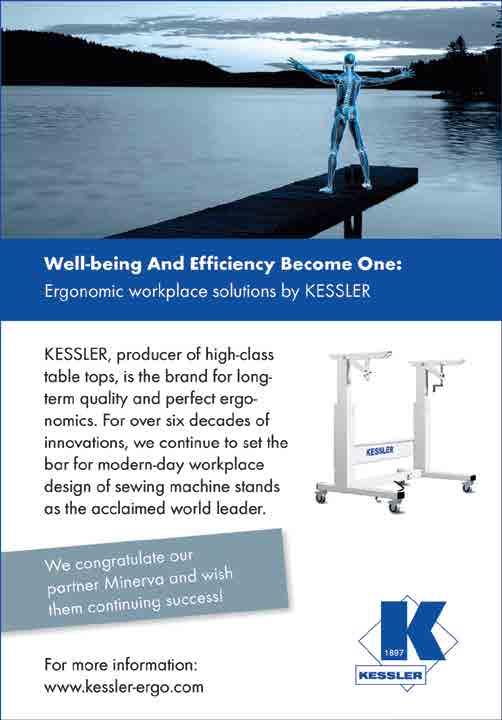
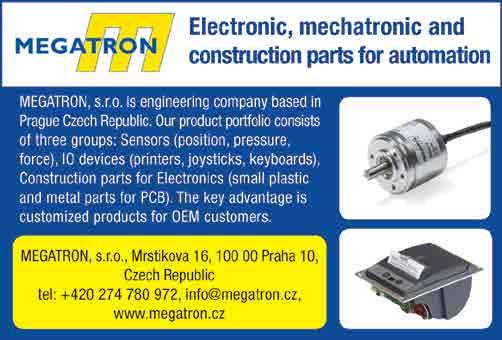
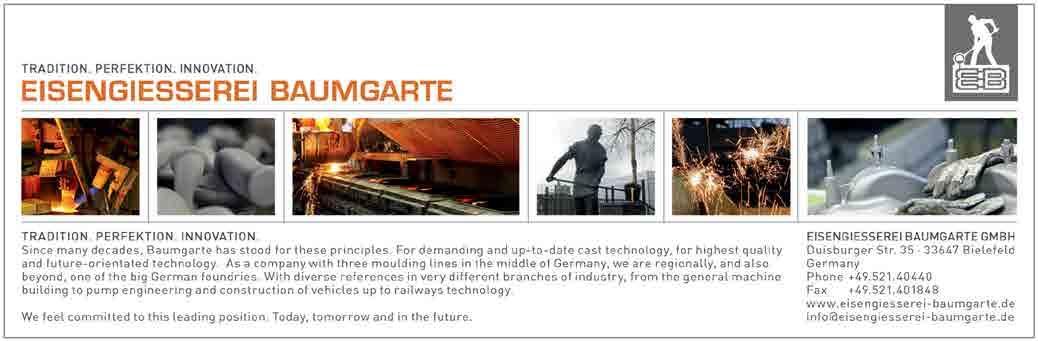
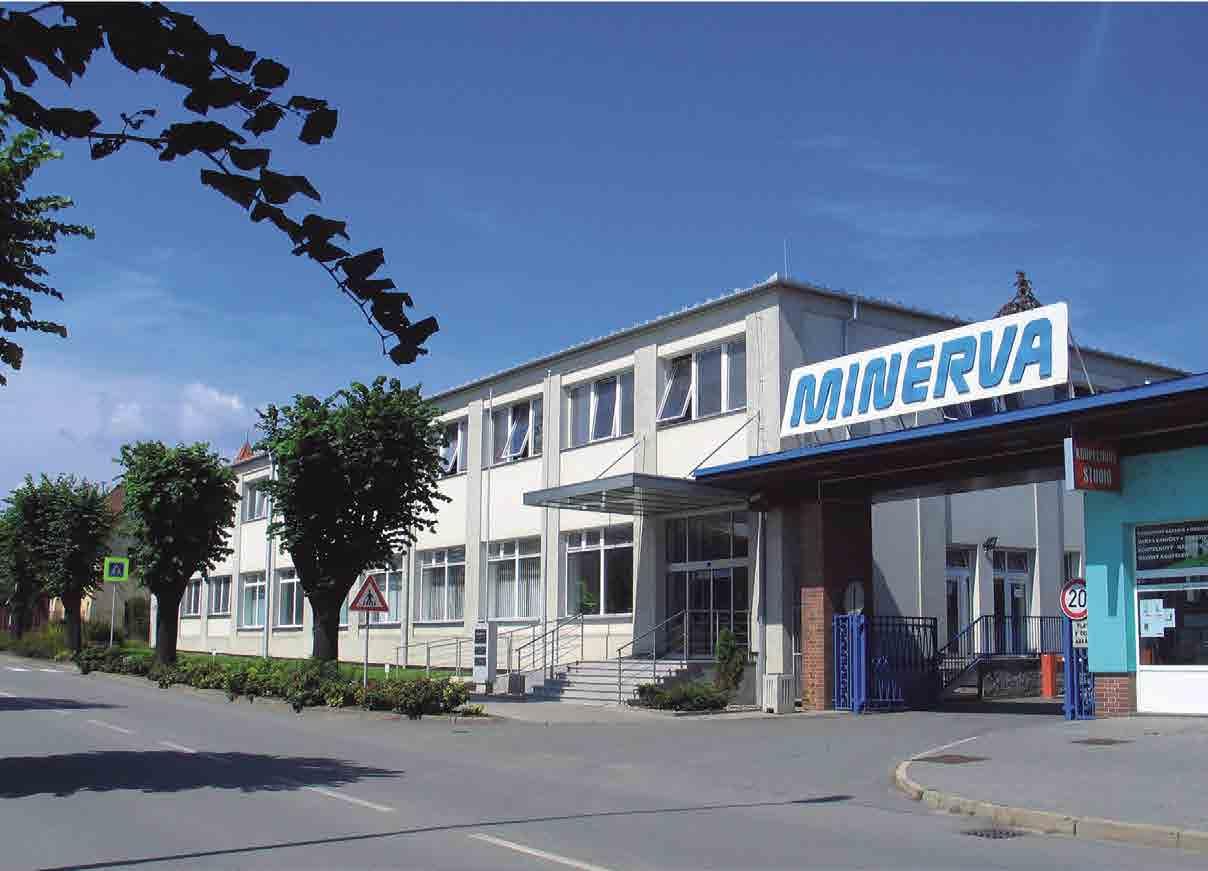
Every year Minerva invests some 50–70 million CZK in development. Mr Hrda explains that most of this amount is directed at progressive CNC machining. To this end, the company makes good use of EU programmes. In 2012–2015 Minerva implemented three EU funded projects worth CZK 92 million, of which most was spent on capital assets. Within the Potential Programme this was the ‘Product Development Extension’ project, within the Innovation Programme the ‘Introduction of Mass Production of Direct Drive Industrial Sewing Machines’ and the ‘Introduction of Mass Production of Heavy Industrial Sewing Machines’ projects. These programmes are part of OPPI and audited by the Ministry of Industry and Trade within the European Regional Development Fund.
Reliable partner
As in any sector, sewing machines are subject to severe competition, particularly from Japanese, Taiwanese and Chinese producers. “We can never compete with these on price, but only on quality, innovation and an individual customer approach, ensuring that our machines are the most reliable and productive. These are their key competitive advantages,” says Mr Hrda.
Minerva is fully export oriented: deliveries to the local market represent only about 2–3 per cent of overall sales. About 70 per cent of machines are sold to the parent company in Germany – these are primarily sewing machines for the automotive sector, used for sewing seats, headrests, internal upholstery, airbags and others. The remaining part of the output is sold to the shoe-making sector. After Germany, the most important markets are those of India and the Netherlands, followed by Italy, USA, China and Poland.
“Our objective for the future is to further develop and enhance our strengths. In addition to improving product development and the high technical competence of our employees, we want to further increase productivity in our key competences such as assembly and machining of basic cast iron castings,” says Mr Hrda, and continues: “In 2013 we set ourselves a target to achieve one billion in sales and 20,000 produced machines within five years. We met this target by last year, while increasing turnover by 40 per cent over two years. Our next target is not to continue to increase output but to maintain current employment levels, to ensure highly productive and efficient production and offer a flexible response to customer requirements,” Minerva’s managing director concludes. n
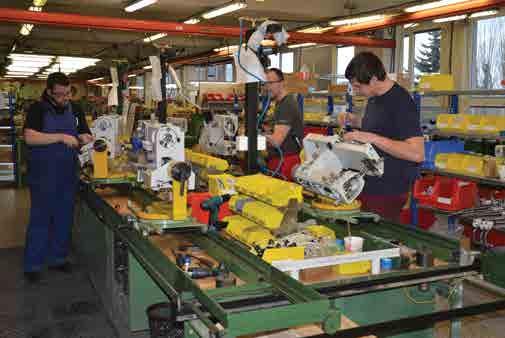