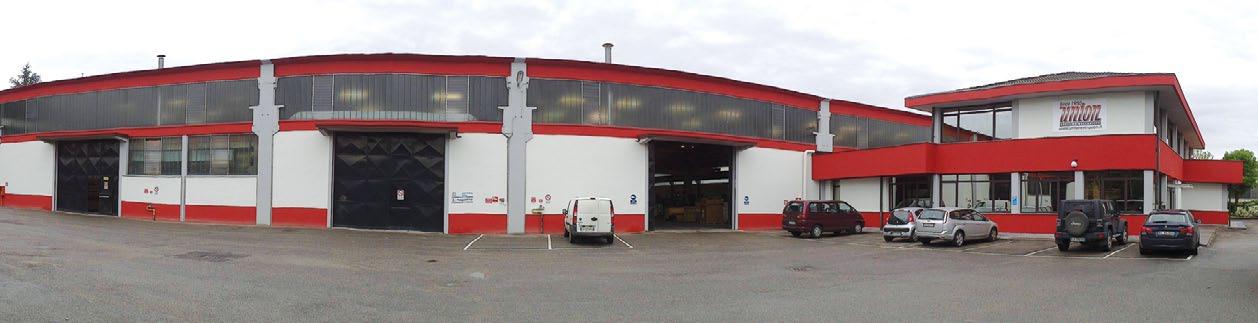
4 minute read
An established leader UNION
AN ESTABLISHED LEADER
Since its establishment in 1950 UNION, based in San Vittore Olona, Italy, has been developing and producing complete extrusion lines and components.
The quality standards it has achieved in its more than 65 years of continuous activity, its range of products and constant machinery updates have made UNION a leader in the field of extrusion. To many, its name is synonymous with reliability and productivity, providing technical services, hi-tech solutions and assistance to its customers throughout the world.
UNION’s range includes: extruders and complete extrusion lines for sheets, foils, profiles, hollow sheets at two and more walls, compounding and recycling equipment; special lines for composite panels of plastics and metal, and complete lines for undulated and greca sheets of PMMA, PC, PET; as well as advanced equipment for XPS, XPET, XPE foam boards, sheets and profiles.
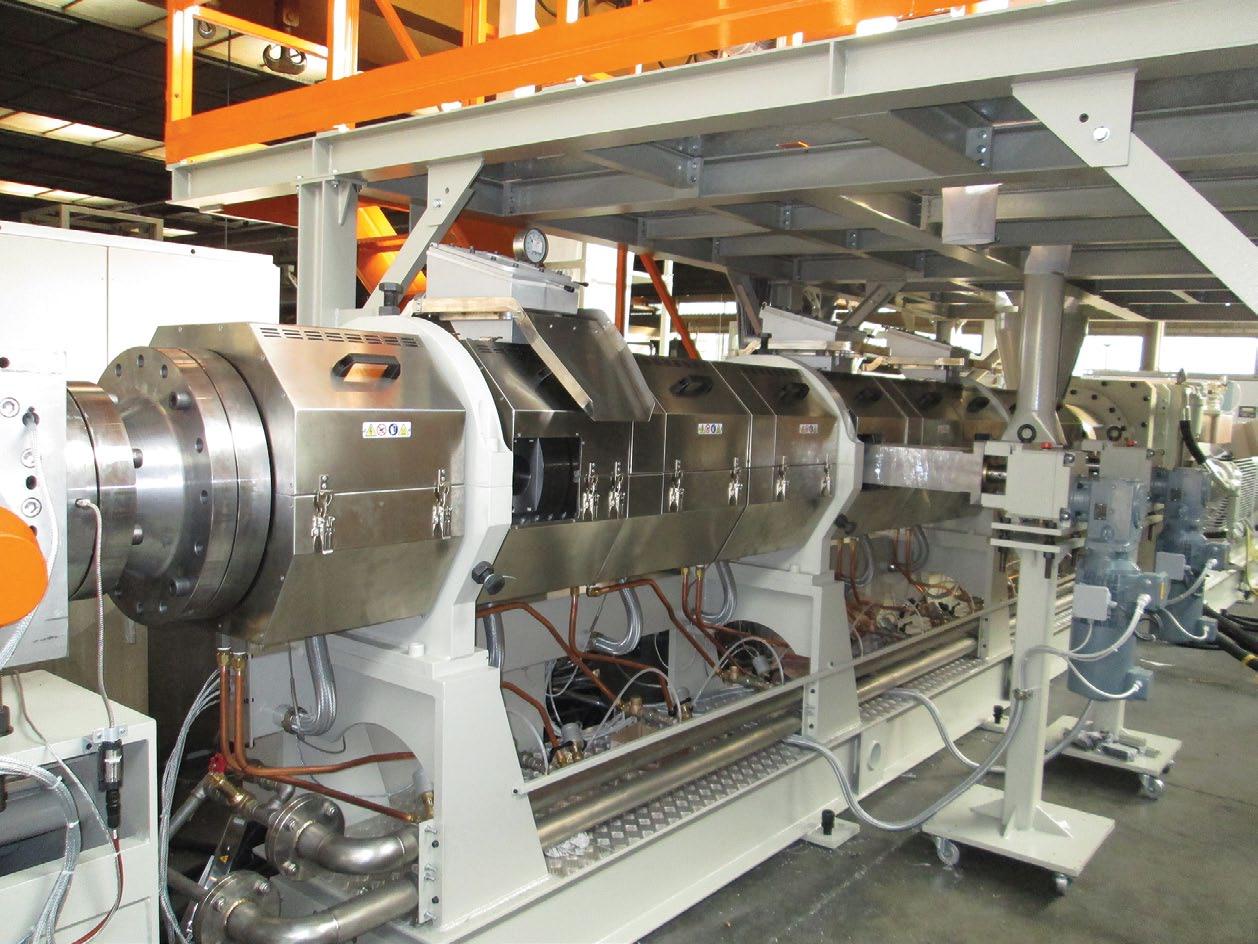
New experiences in compound and master-batch extrusion
“Union has intensified its activity in the compound extrusion industry,” begins Zanazza, the company’s sales director. “A few years ago we made a big line for the production of high-concentration polymers; while today we are focusing on the real compound and master-batch market, dedicated to the production of plastic materials with anti-flame, antiblocking and graphene additives.
“We have already made a series of machines, including a laboratory machine which has been newly installed at a compound transformation company, that will allow us to continue research in this field.
Our range already included slow and fast twin-screw co-rotating extruders, produced mainly for rigid sheets and foam production, but now we have developed machines which are totally dedicated to compounds and master-batches.”
In the 1970s Union achieved significant growth thanks to its granulation, colouring and compound machines: today it is able to transfer the experience gained in twin-screw co-rotating extrusion even to compound and master-batch lines. From February 2017 its laboratory has been made available to potential customers, and consists of two high-speed twin-screw extruders complete with dosing devices for powders and granules, mixers, side feeders and two different types of die cutters to perform compound tests and small-batch production.
“For less experienced customers, who are approaching the compound world with their first production facilities, we are able
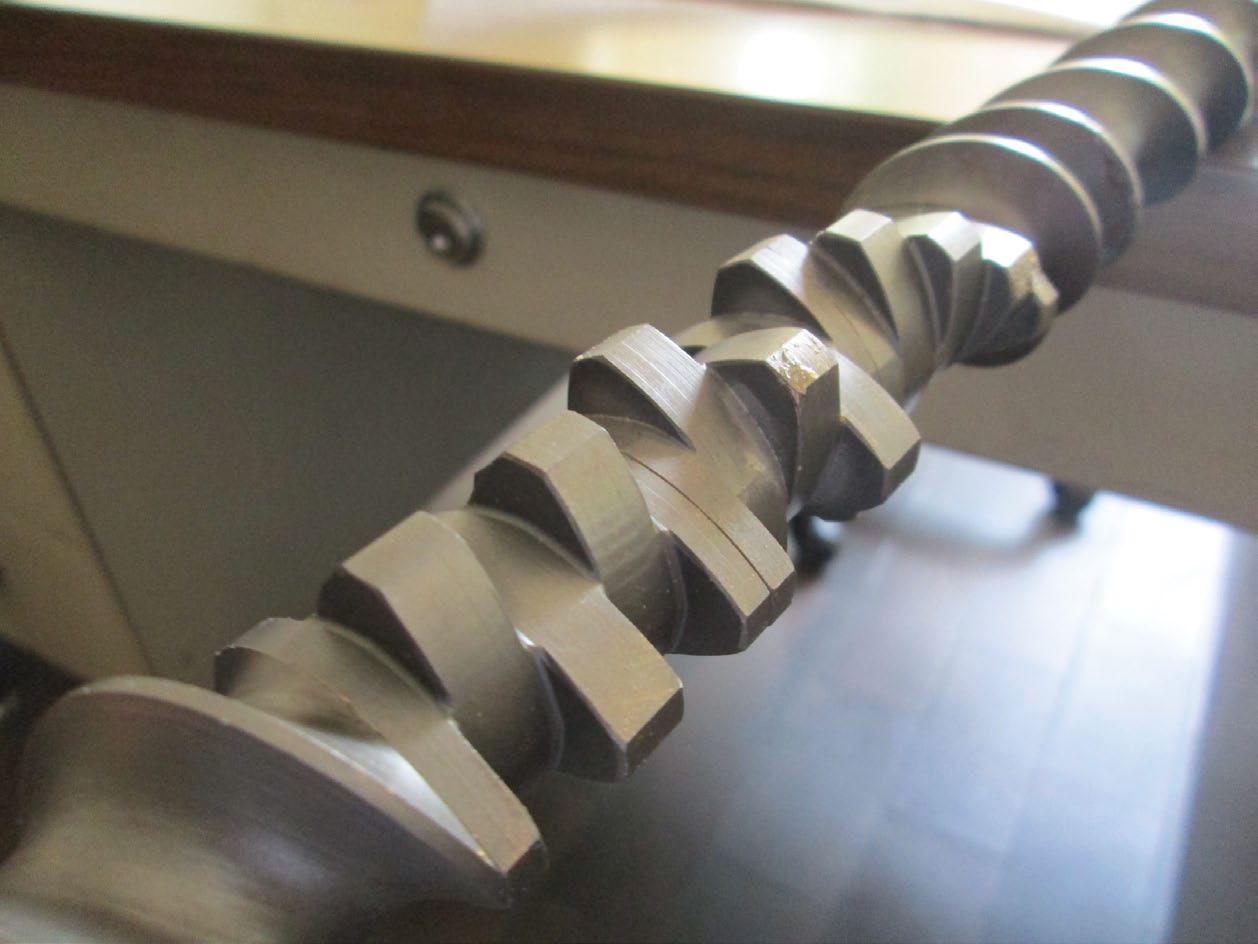
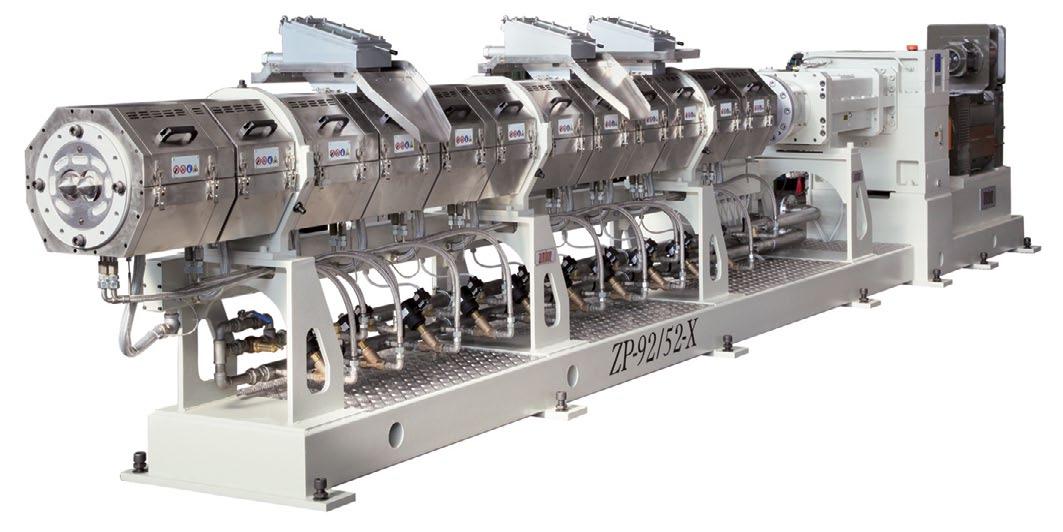
to provide our experience, if required, to improve the formulations proposed, using a consolidated partnership with an Italian company specialising in additives.
“In the granulation and recycling field we have also made great strides in the field of MICROGANULATION for foam materials, such as recycled EPS from post-consumer cases and recycling in foam microgranules from 0.8 to 1.2 mm which is used in the development of new products such as panels for acoustic thermal isolation – even those with high electromagnetic dispersion thanks to the use of graphene.
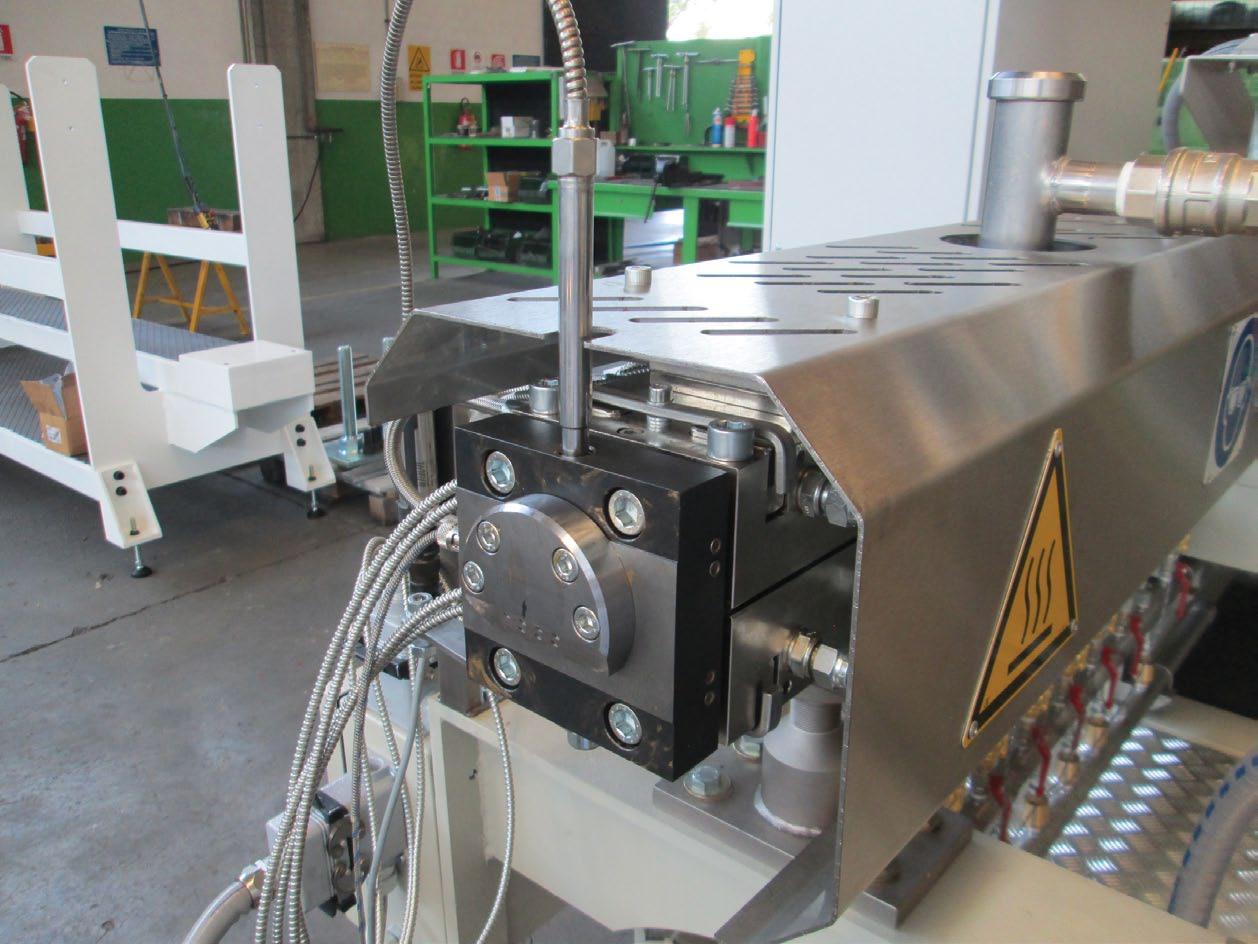
experience and know-how
“We do not stop here,” adds Zanazza. “Our intent is to further expand the range with machines that are still in development. I think it is important to keep in mind the positive experiences gained in the past: certain themes, in fact, cyclically re-emerge. The research in the compound field could also help to make new extruded flat dies capable of replacing other materials.
“I believe that the success of Union in recent years is derived mostly from the experiences gained during all the research and development phases, as well as those gained in the field from the 1950s up to now.
We have been pioneers among manufacturers of sheet singlescrew extruders in the construction of machines with more venting zones and sheet extrusion machines with an L/D ratio higher than those of competitors.
“When, in the early 1990s, machines with much greater lengths were proposed, our best competitors claimed that the extruder should have a length not exceeding 25–30D: today, however, these manufacturers have realised that a greater length, with equal screw diameter, ensures better mixing and energy saving.
“Today we believe very much in the realisation of new types of plastics: special materials, of which we talk so much, will be achieved when the polymers are modified with nanoparticles.
Our target for the future will be the use of compounds for the production of sheets with characteristics very similar to metals. The base will be a polymer made from those that are already known, but the structure will probably change: the addition of nanoparticles will give it higher mechanical characteristics.
“In the elastomers field, although it is in lower numbers than in thermoplastic materials, nanoparticles are already used. The intention is to participate with our technology in future developments in the field of thermoplastics.” n
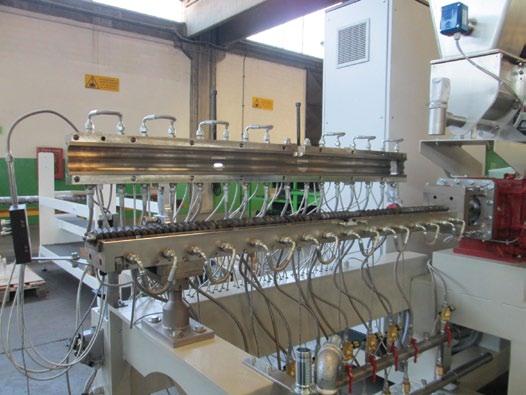
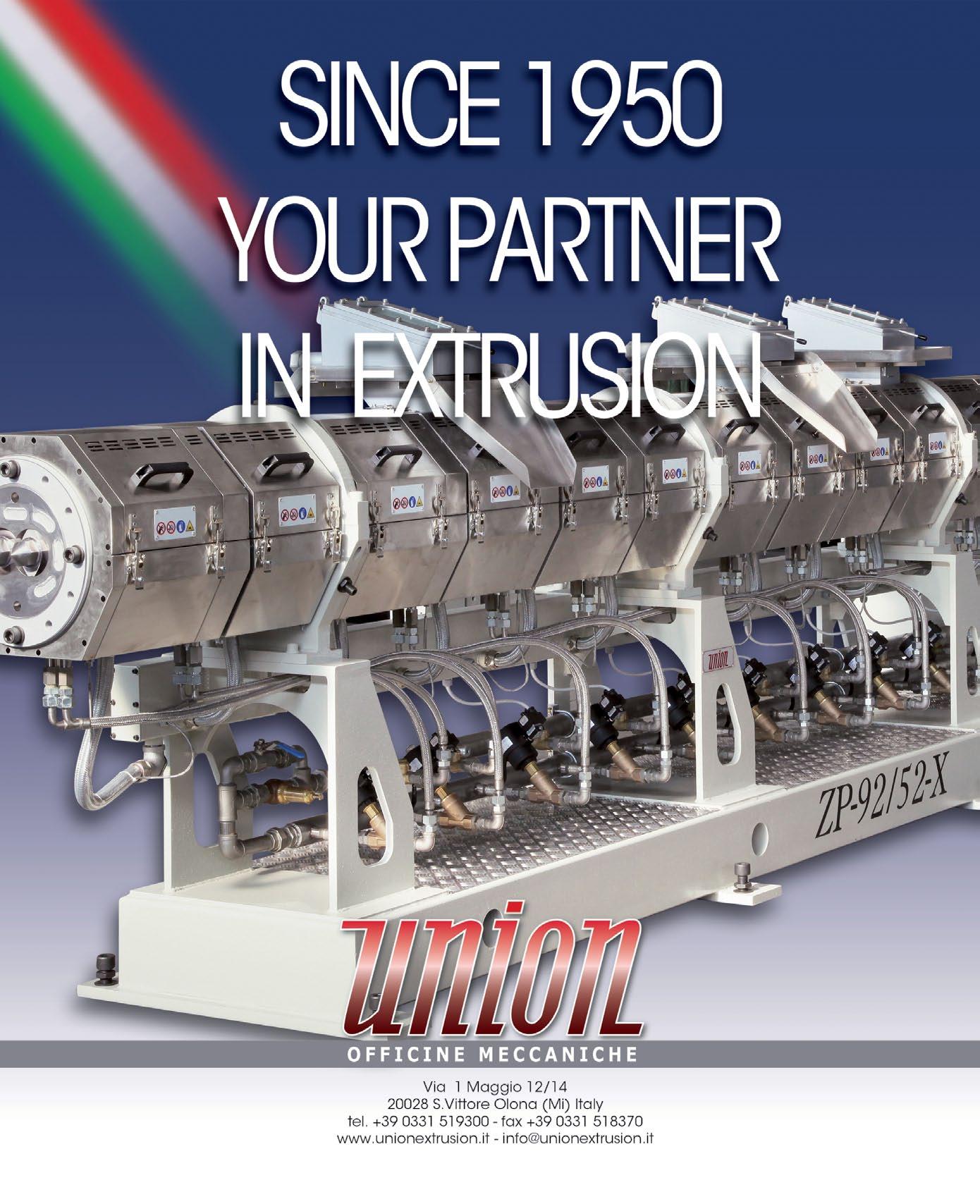