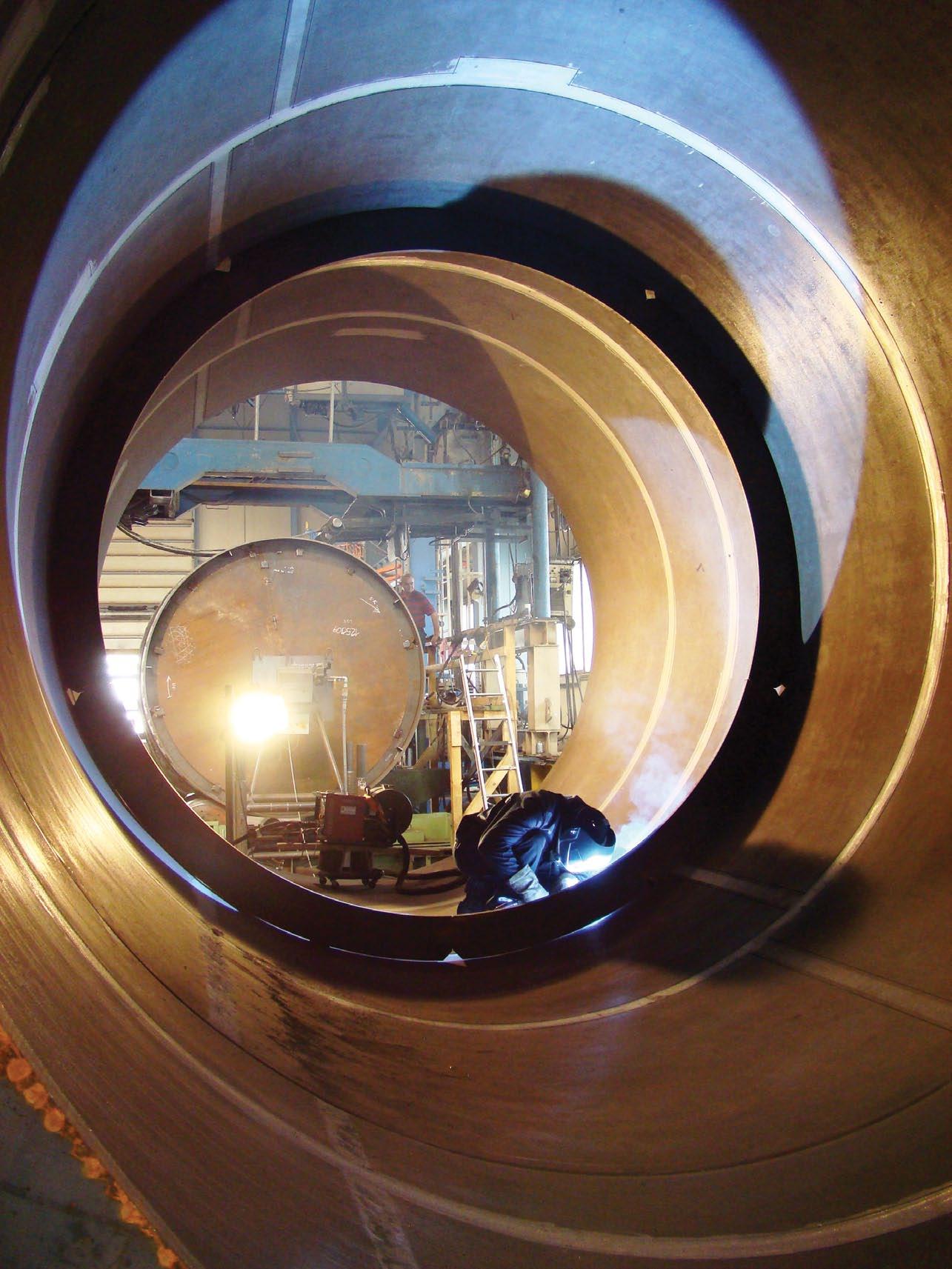
4 minute read
The high-pressure specialist
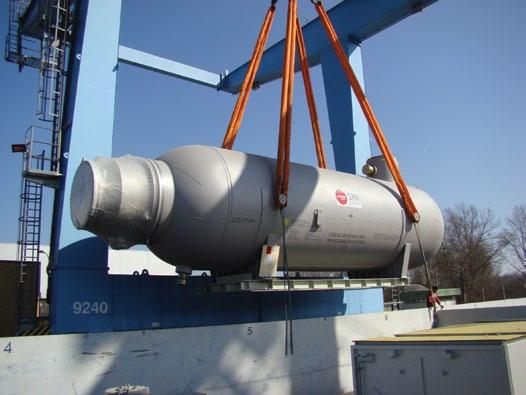
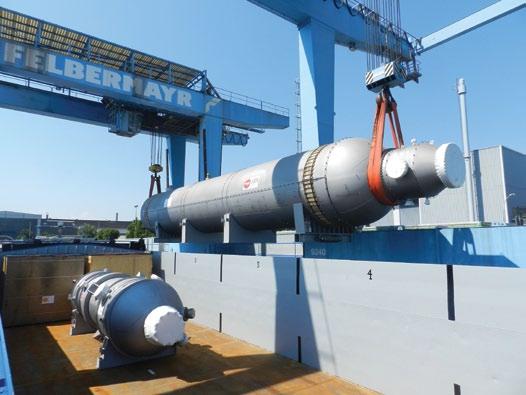
thE highprEssurE spEcialist
For decades, Schoeller-Bleckmann Nitec GmbH (SBN) has been one of the world’s leading manufacturers of high-pressure equipment for the chemical and petrochemical industry, in particular for the fertiliser sector. In 2008 the company became a member of the Christof Group, an international comprehensive engineering expert, cementing its position on global markets. Romana Moares reports.
Austria-based Schoeller-Bleckmann Nitec GmbH designs and manufactures customised high-pressure apparatuses for the fertiliser and petrochemical industries, in close cooperation with licensors and processors. The company, founded in 1862 in Ternitz, Austria – where it still resides today – was formerly known as Schoeller-Bleckmann Nooter GmbH. A major milestone came in 2008 when the business was acquired by Christof Holding AG, a global expert in complex plant engineering and industrial services with more than 100 years of market experience and an impressive international customer base.
State-of-the-art technology
Schoeller-Bleckmann Nitec GmbH is an expert in the field of urea and ammonia plants. For these complex facilities, the company produces high-pressure heat exchangers and high-pressure reactors, lined with highly corrosion-resistant materials, and all the fittings such as liquid distribution systems, sieve plates and others, made of heat-resistant, unalloyed steel grades and austenitic chromium nickel steel.
With its series of high-pressure vessels, SBN covers the entire process spectrum of ammonia plants: from primary and secondary reformers and various gas scrubbing stages with highpressure temperature and corrosive stress and high-pressure apparatuses for ammonia synthesis up to the connected pipelines. The most commonly used materials include temperature-resistant chromium nickel steels and nickel alloys as well as hydrogenresistant steels.
For many years now, Schoeller-Bleckmann Nitec GmbH has also been supplying high-pressure equipment and components to the chemical and petrochemical industry, both for the processing of crude oil and natural gas to various intermediate and end products, and as for the production of olefins and polyolefins.

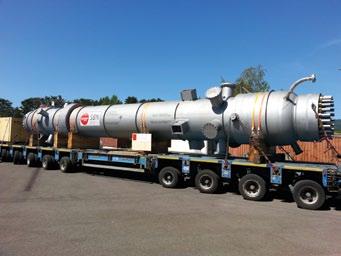
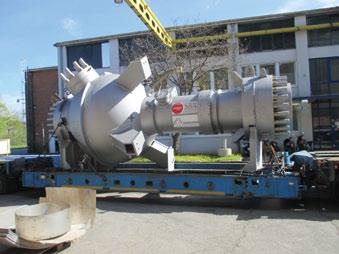
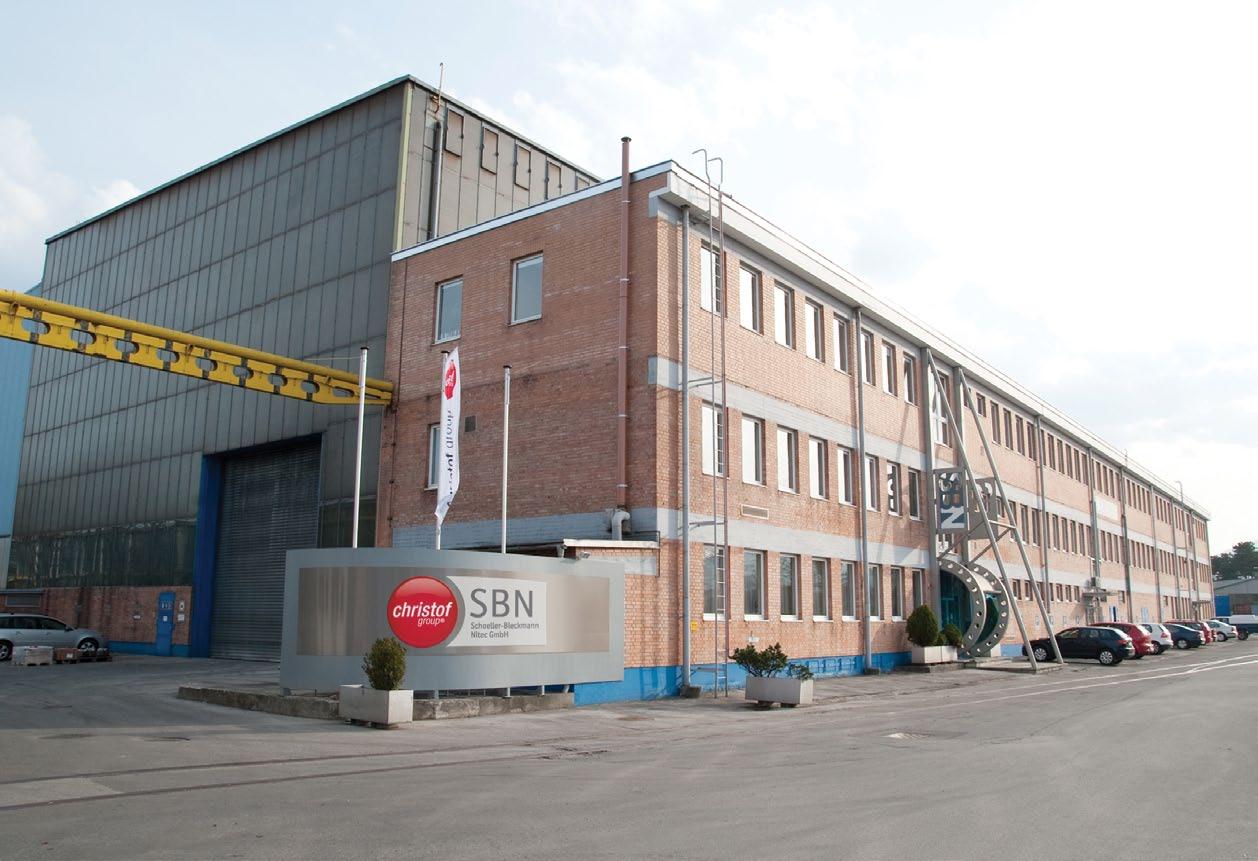
As a leading manufacturer of high-pressure equipment for the chemical industry, SBN offers its customers special on-site services such as welding of high pressure urea pipes, installation of sieve plates in urea reactors, repairs or exchange of linings in urea reactors, repairs of heat exchangers, complete piping exchange as well as engineering and logistics services.
modern production facility
Schoeller-Bleckmann Nitec GmbH has responded quickly to the trend towards increasingly larger and technically more demanding systems and therefore to heavier equipment – components weighing more than 200 tonnes are no longer a rarity today. The current requirements are fully reflected in production technology and manufacturing processes. In the last few years, the machine park has been brought up to date with a generous investment programme.
The factory in Ternitz consists of two production halls with a total area of 5270m². The prefabrication with the tailoring, the equipment for the sheet metal forming and the machines for the mechanical processing are housed in a new production hall with an area of 3000m². The modern technology includes a CNC BTA deep hole-drilling machine, a CNC carousel lathe and various welding manipulators with a load capacity of up to 100 t. Six
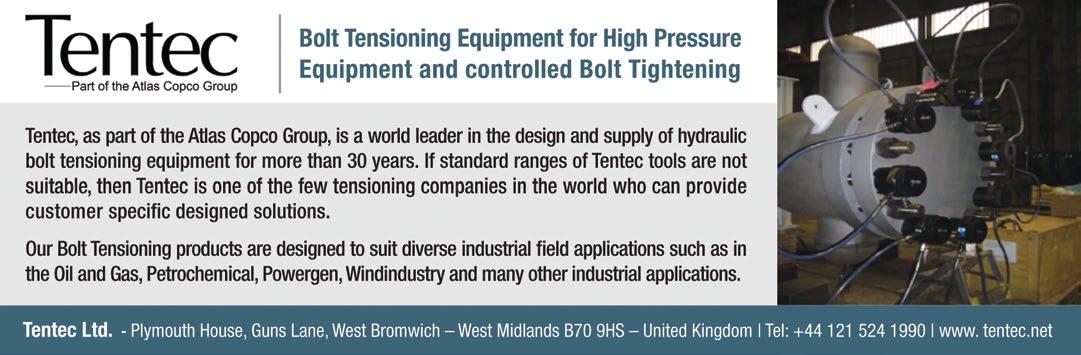
bridge cranes with a capacity of max. 240 t guarantee a smooth handling and loading of heavy components.
The basis of SBN’s manufacturing know-how rests on the mastery of highly complex welding processes. The company has a comprehensive range of welding equipment, from machines for TIG, MAG and electrode welding to machines for welding cladding (tape and wire cladding) and the computer-assisted systems for tube welding (conventional and background welding). In addition, a large number of container turning devices with a load capacity of up to 500 t are available.
To accommodate the increasingly large dimensions and weights of the equipment, the company has been running a second production facility in Linz for several years. The high-pressure equipment is prefabricated in parts in Ternitz, then transported to Linz where it is completed, inspected and approved by independent inspectors before being loaded directly onto the inland waterway vessel to be shipped to customers.
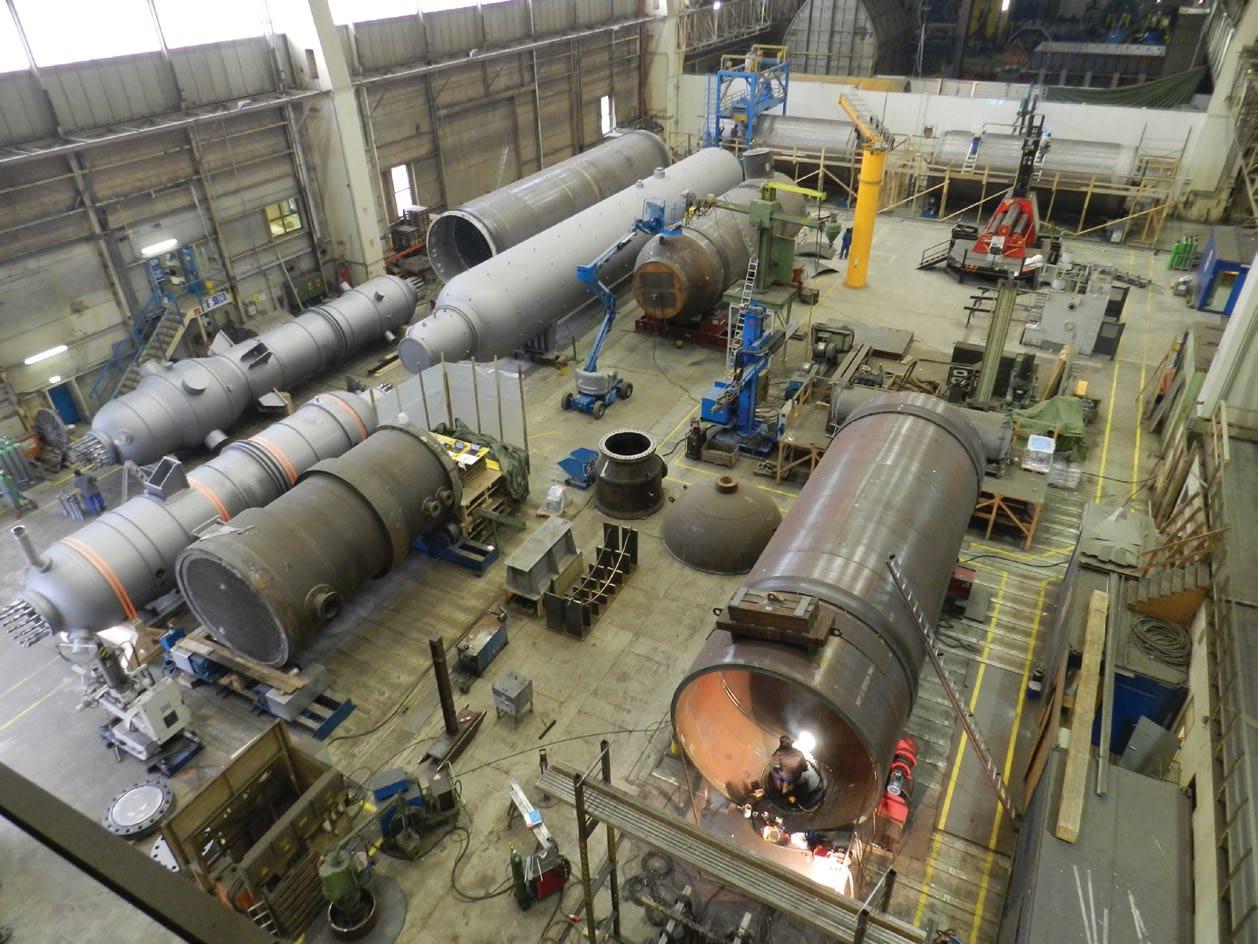
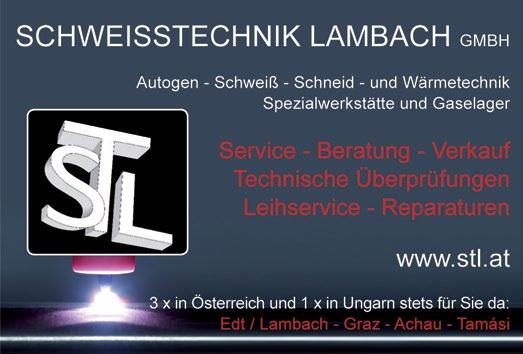
exceeding the expectation
In order to ensure that the high-pressure apparatuses manufactured fully meet the customers’ requirements the company has been working closely with licensors and material manufacturers for many years. SBN was a pioneer in the extensive use of Safurex® – a superduplex steel developed by the Swedish steel producer Sandvik AB and the Dutch lawmaker Stamicarbon BV. SBN is now producing a new generation of pool condensers and pool reactors according to the Urea 2000 process from Stamicarbon, which significantly increases productivity in urea plants.
The global trend towards ever-increasing plant capacities and the introduction of new technologies and materials present daily challenges for designers and engineers of companies such as SchoellerBleckmann Nitec. To keep pace with the latest market developments and to incorporate the latest requirements in its portfolio, SBN collaborates intensively with processors, inspection companies and technical universities.
The company’s philosophy focuses on customer satisfaction. On a continuous basis, a significant part of the company’s earnings is invested in research, development and innovation, whereby customers, suppliers and partners are often involved with the goal of offering optimal, cost-effective and future-oriented solutions. Solutions that not only meet but exceed customers’ expectations. n