
10 minute read
Steel giants join forces Consolidation in Europe’s
Steel Giants join forces
As 2017 draws to a close, the European metals sector can reflect on a year in which long-anticipated deals consolidating the Continent’s steel industry finally came to fruition. Ben Hargreaves reports.
The big news, finally announced in September after more than a year of negotiations, was the merger of German steelmaker thyssenkrupp and the European operations of India’s Tata Steel. The combined company – thyssenkrupp Tata Steel – will have shipments of about 21 million tonnes a year, and create Europe’s second largest steelmaker, with the new venture to be headquartered in Amsterdam.
Meanwhile Europe’s largest steelmaker has been busy doing deals of its own. ArcelorMittal announced a major acquisition to take over Italy’s Ilva works – Europe’s largest steel production site, whose plant at Taranto is equipped with five blast furnaces – in June, in a deal worth €1.8 billion. These moves mean that ArcelorMittal now has the capacity to produce about 60 million tonnes of steel a year.
Need for change
Combined, ArcelorMittal and thyssenkrupp Tata Steel will now account for approximately 50 per cent of Europe’s steel output. Why is large-scale change necessary in the EU steel sector? The answer is that the industry has struggled with dealing with its environmental responsibilities, global overcapacity, access to raw materials, and energy costs. Europe’s share of global steel production declined to 10 per cent in 2016, and in general the sector in Europe has suffered since the global financial crisis, with each tonne of steel worth around €215 in 2008, but just €46/tonne in the first quarter of 2016, recovering to approximately €83/ tonne in the first quarter of this year.
Producers in Europe have suffered from weakened demand since 2008, combined with a flood of low-cost imports from outside the EU. The impact of these fundamentals was keenly felt in the UK when Tata Steel announced a decision to pull out of its Port Talbot facility in Wales in the Spring of 2016, citing imports of Chinese steel, high energy costs, and weak demand as key factors. Although some of Tata Steel’s sites in Britain were sold off piecemeal, the Port Talbot facility, which employs 3500 people, survived thanks to a deal agreed to separate and reduce the company’s UK pension liabilities. That deal, thrashed out with unions and the Government, and approved by the British pensions regulator in September, removed one of the major barriers to the merger of thyssenkrupp and Tata Steel.
In a sign that the Port Talbot plant has a future as part of the new entity, Tata Steel announced a £30 million investment in the Port Talbot plant in November. Unions in the UK remain concerned about the impact of the merger on British jobs, but as prices have improved and the industry has moved to restructure, there have been signs of a tentative recovery in European steel production this year, with steelmakers on the Continent also returning to profitability.
Production of steel is also up on last year. Within the EU, Italy’s crude steel production for October 2017 was 2.3 million tonnes, up by 6.1 per cent on October 2016, according to the latest data from the World Steel Association. France produced 1.4 million tonnes of crude steel in October 2017, an increase of 1.6 per cent compared to the same period last year, and Spain produced 1.3 million tonnes, an increase of 11.9 per cent on October 2016. Turkey’s crude steel production for October 2017 was also at 3.3 million tonnes, up 11.1 per cent on October 2016.
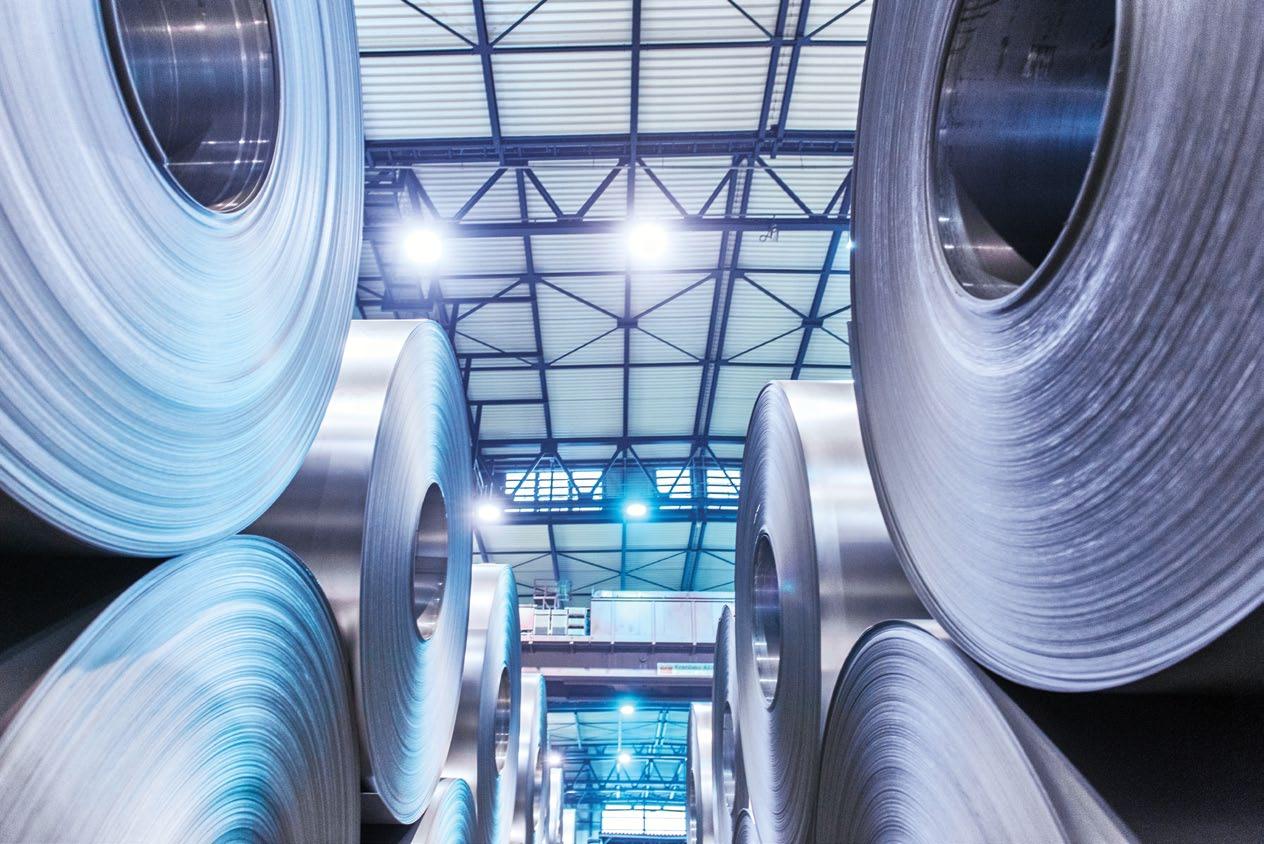
Global usage of capacity by the 66 countries that report to the World Steel Association was 3 per cent higher in October than in the same period in 2016, the association says.
Better environmental performance for steel
In terms of the environmental performance of steelmakers, in February, reforms to the European Emissions Trading System (ETS) were agreed after two years of talks. Under the new regime, energy-intensive users such as steelmakers that make efforts to be environmentally responsible should enjoy greater protection while greenhouse gas emissions across the EU continue to be cut. The reforms mean the highest performing 10 per cent of factories and other installations will receive all their ETS allowances for free, and a fund of up to €12 billion will be established to help industries innovate by investing in technology.
“The European steel industry wanted a scenario in which the best-performing plant in Europe do not incur undue costs,” says Charles de Lusignan, spokesperson for Eurofer, the European Steel Association. “If you are already at the forefront of environmental performance, you shouldn’t face other costs that are not borne by foreign producers.”
This has an important global effect. “If steel in Europe becomes uncompetitive due to environmental legislation, we find ourselves in a situation where we are importing steel from China. There, steel production can be up to 50 per cent more CO2-intensive. You find yourself exporting jobs – and importing steel and CO2. That is just making the CO2 someone else’s problem. The climate doesn’t work that way.
“We must be able to compete in the global market, while also being environmentally-friendly.”
Other reforms to the ETS hoped for by Eurofer, such as a better way of compensating indirect costs such as energy, did not take place. Under the reformed ETS, the costs of conforming to the scheme by electricity producers – who have to pay for all of their carbon allocations in an auctioning system – will continue to be passed on to the steel industry in Europe, affecting competitiveness. In some EU member states, there is compensation for this, but not in all, distorting the market, De Lusignan says. “One of the things we were hoping for under the reform of the ETS was that there would be a harmonised system for the compensation of indirect costs.”
Global competition
Europe has been faced with global overcapacity and the import of large volumes of steel from abroad – a problem that has continued throughout the year. The flood of Chinese steel onto the market has to some extent abated thanks to the successful introduction of antidumping measures. But around 400 million tonnes of a global steel industry overcapacity of about 650 million tonnes remains in China. This puts downward pressure on steel prices. A Global Forum on steel – run jointly by the G20 and the OECD – has been introduced to look at the problem.
“Dealing with overcapacity is key – and that has to be done jointly, not just by the EU, but by the other major steel-producing regions,” De Lusignan says. China is a key concern, but Iran and Russia are also important players in the global steel overcapacity debate. For example, Iran is looking at increasing its capacity for steel production by about 45 million tonnes between now and 2021. Eurofer would like to see a new, more responsive anti-dumping methodology introduced to address dumping of steel imports from China and other countries, and to take into account China’s desired WTO market economy status.
“Trade defences are the only mechanism we have to deal with overcapacity, until such a time as overcapacity is dealt with concretely,” he adds.
Innovation policy is also important in terms of the future competitiveness of steel. The EU, along with the Dutch Government, has contributed a third of the cost of the €25 million Hirsana test plant at Tata Steel Ijmuiden to develop a new technology for producing molten iron. Hirsana could enable steel companies to use a wider range of raw materials, including recycled materials in blast furnace
steelmaking, while delivering a 20 per cent reduction in CO2 emissions. The project is expected to take 15 years to prove. The Hirsana plant and process have the potential to solve some of the environmental issues associated with steelmaking, and could revolutionise the industry – but such projects require support to succeed, De Lusignan says. This support could include the relaxation of EU state aid rules and competition policy. “We shouldn’t allow companies to form cartels – and the EU is very vigilant on this.
“But if we are trying to engage in innovation, we would like to be able to combine investment across several parties, without being accused of engaging in cartel-like behaviour.”
Challenges for aluminium
The aluminium industry in Europe is facing some of the same issues as the steel sector, including global overcapacity. In fact, European Aluminium, the trade body for the sector in the EU, is calling for a forum to be established addressing overcapacity in the global aluminium industry, just as there is for steel. Compensation for indirect costs – which can be seven times higher than direct costs because aluminium production is so energy-intensive – should also be agreed to secure a ‘competitive and sustainable’ aluminium industry in the EU, the body says.
As with steel, the alumimium industry in Europe is coping with an increased level of imports onto the market from China. Chinese exports of aluminium to the EU increased by 39 per cent in 2016, according to European Aluminium. “The good news is that recent changes to the EU’s anti-dumping and antisubsidy legislation will enable Europe to better deal with the impact of these overcapacities in international trade,” explains Maximo Miccinilli, spokesperson for European Aluminium.
The changes allow for a new method of calculating dumping margins for imports from third countries in case of significant market distortions, or where there is ‘highly pervasive state influence’ on the economy. This allows the EU to use the same anti-dumping methodology for all WTO members, and to target ‘significant market distortions’. The upcoming G20 summit in 2018 in Buenos Aries, Argentina, “offers another opportunity to address this issue, which is global, and requires a global solution,” Miccinilli says.
Global overcapacity issues aside, primary production of aluminium in Europe is forecast to have grown by 1.6 per cent for 2017, and to grow by 2.3 per cent in 2018. Consumption in Europe was up by 3.6 per cent this year and will grow by 2.8 per cent in 2018, according to European Aluminium. For rolled aluminium, growth is being driven by the automotive – where aluminium will only find increasing use because of its light weight – and packaging markets.
“The building and construction markets are also picking up after several years of crisis,” Miccinilli points out. “We see a robust growth in the use of aluminium in automotive and transport, particularly for body sheets and heat exchangers for cooling applications. We expect this trend to continue. In addition, the electric vehicles hitting the market over the next few years could be aluminium-intensive.
“The most likely trend, however, will be multi-material design, in which aluminium plays a key role alongside other materials.”
That is good news for Europe’s steel sector, which continues to count automotive as a key market, as it undergoes further consolidation. Greater consolidation in the industry is welcomed by Eurofer. “On the whole consolidation that leads to a more coherently-sized and structured steel industry is positive. It allows us to compete on a global basis, while gaining economies of scale,” says De Lusignan. But authorities will continue to monitor individual deals closely to ensure they increase, rather than stifle, competition. For instance, EU antitrust investigators announced in November that they will investigate whether ArcelorMittal’s proposed purchase of the giant Italian steel plant Ilva will lead to price hikes.
Global competition will continue to remain fierce in 2018, and the threat of steel being dumped on the European market ever-present. Against this backdrop, European steelmakers will look to regulators to ensure they can operate on a level playing field.
De Lusignan says: “Dealing with overcapacity, environmental policy and investment in innovation are the areas that will secure the future of the steel industry long-term – if we get them right.” n
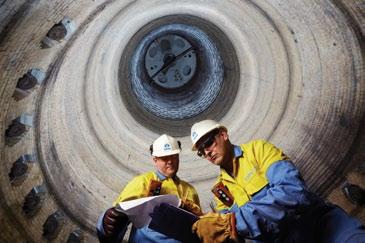
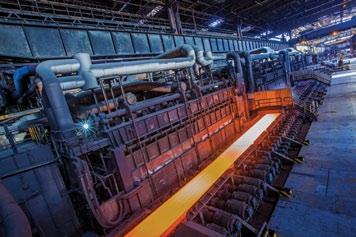
