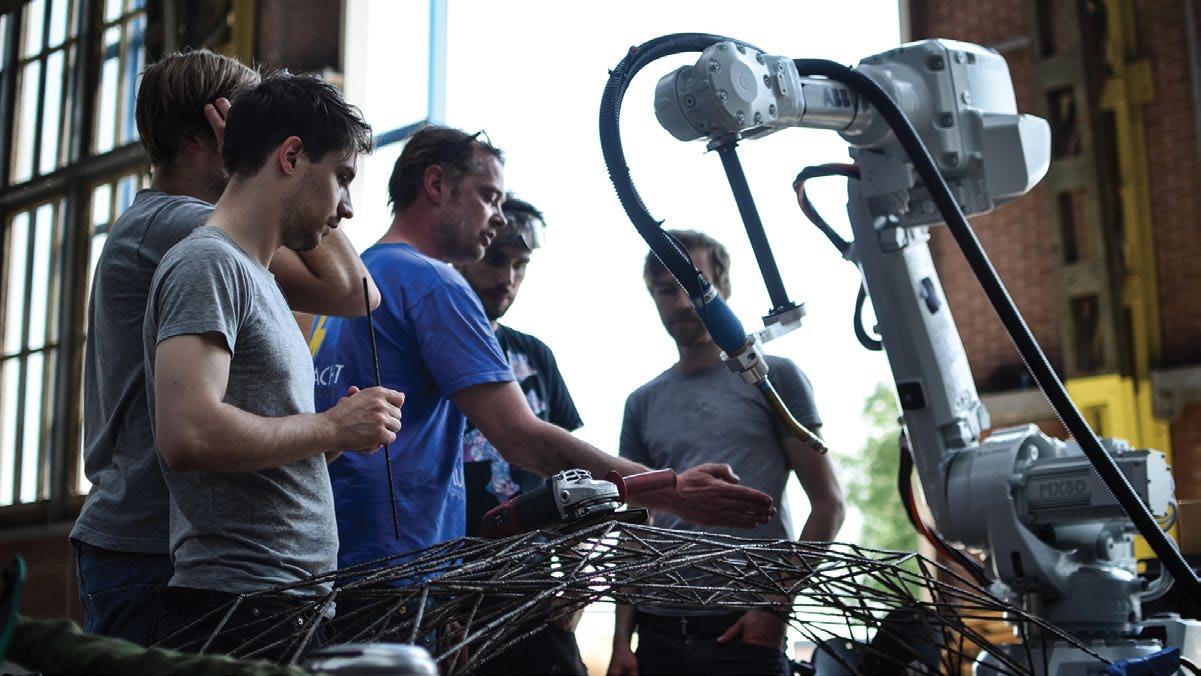
4 minute read
A bridge further with 3D technology
a bridgE furthEr
with 3d tEchnology
The Netherlands-based company MX3D is a pioneer in the field of robotics additive manufacturing technology. Victoria Hattersley looks at one its most ambitious projects to date – a 3D printed stainless steel bridge to be installed over one of Amsterdam’s oldest canals.
It’s the first project of its kind – a 12 metrelong stainless steel pedestrian bridge printed entirely using 3D technology. Due to be completed in 2018, the bridge will sit across Amsterdam’s famous Oudezijds Achterburgwal Canal in the old city centre, and will represent a major step forward in the use of additive manufacturing technologies.
Engineers from Imperial College London worked with MX3D to test the novel material properties of the 3D printed steel and perform finite element modeling of the entire structure. This helped to anticipate the impact of pedestrian or cycling traffic over the bridge and inform its design.
However, 3D printing in steel is still a relatively new field and the bridge has not been without its set-backs. Originally planned to be supported by a lattice of struts, further research suggested that this would have placed too much stress on the canal walls so an updated design was necessary. Although it will retain some of its original bends and twists, it now resembles a more ‘conventional’ pedestrian bridge.
Pioneering technology
But what makes this project stand out compared to other 3D steel structures is not so much its aesthetic appearance as its pioneering use of robotics. MX3D is a company that equips multi-axis robots with 3D tools and develops the software to control them.
According to Tim Geurtjens, the company’s CTO: “What distinguishes our technology from traditional 3D printing methods is that we work according to the ‘Printing Outside the Box’ principle. By printing with six-axis industrial robots, we are no longer limited to a square box in which everything happens. Printing a functional, life-size bridge is of course the ideal way to demonstrate the endless possibilities of this technique.”
Adam Hicks, group leader for additive manufacturing technology development at the University of Dayton Research Institute, had this to say about the importance of the project: “The methods they are using are unique, in that the process is entirely automated. MX3D has robotic arms laying down rows of welds, which the robots use to create structural shapes.
“Secondly, these robots can, in principle, crawl out onto the structure they’ve just created, extending the bridge out onto free space. With two systems, one working from either side of the gap, meeting in the middle,
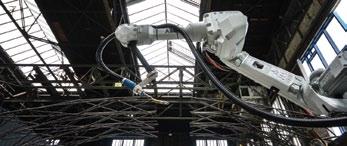
you can 3D print the entire bridge structure without any human involvement (aside from setting up the robots and hitting ‘go’).”
Digital twinning
There is yet another reason this construction is interesting: one of the partners joining the MX3D project, the UK-based Alan Turing Institute, is responsible for installing a sensor network on the bridge itself in order to monitor its ‘health’ in real time.
Once installed on the completed bridge, the sensors developed by the Alan Turing Institute – along with the University of Cambridge’s Centre for Smart Infrastructure and Construction – will collect structural measurements such as strain, displacement and vibration, as well as measuring environmental factors such as air quality and temperature.
The data is input into the bridge’s ‘digital twin’. For those unfamiliar with this term, digital twinning has emerged in recent years as a major new approach to design and maintenance in the fourth industrial revolution. In simple terms, it is the mapping, or ‘twinning’, of a physical asset to a digital platform. Sensors on the digital asset, such as those developed by the Alan Turing Institute to be used on the bridge, collect data to, among other things, predict breakages before they happen. For the MX3D project, this will enable engineers to monitor how the bridge changes over its lifespan. It will also allow for the bridge to be modified in the future to suit any required change in use.
Autodesk, a UK-based software developer, will be working alongside the Alan Turing researchers to power the bridge’s collection and processing. It is also helping develop machine learning algorithms that will enable the bridge to interpret and react intelligently to its environment.
All of this can help to overcome some of the traditional challenges associated with metal 3D printing – unlike SLS polymer 3D printing, for example, metal 3D printing requires forethought to design and anticipate what traditional post-processing steps will be required. Digital twinning is one way of getting around this issue. opening new doors

Such techniques, of course, create great possibilities for the 3D construction sector moving forward. 3D printing for infrastructure, such as houses and bridges, could be used in the future to rebuild places affected by natural disasters, build homes in undeveloped places or even – and we’re almost veering into sci-fi territory here – building homes and bridges on the moon or Mars before we get there ourselves.
According to Gijs van der Velden, MX3D co-founder: “The MX3D technique offers engineers the freedom of working with metals in an entirely new way. The digital twin of the bridge will help with the creation of a new design language. We hope that this data-centric engineering method will speed up the introduction of this exciting new technique into the construction market.”
An open call for ideas on how the data collected by the sensors can be used has been launched by MX3D and closes in February 2018. For more information, visit: http://mx3d.com/projects/bridge/
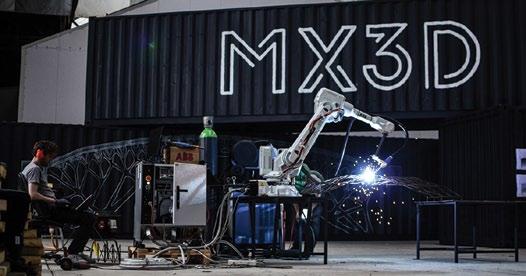
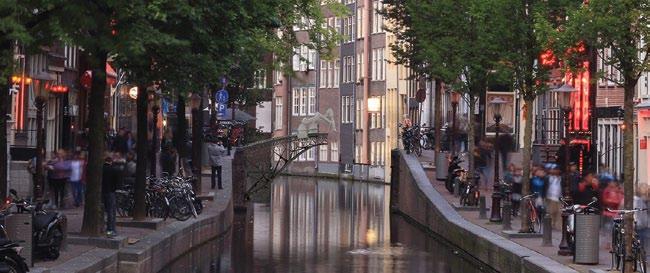