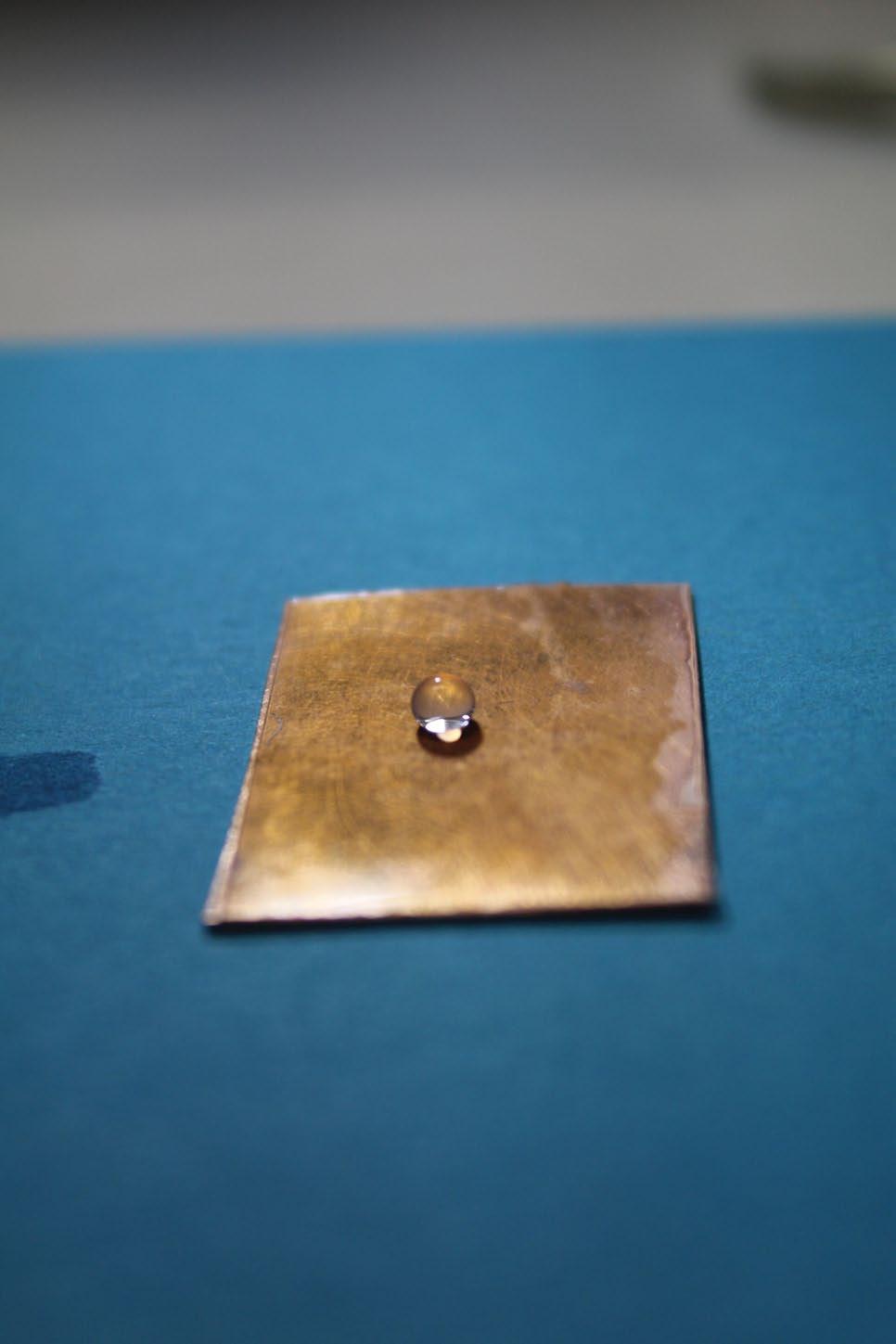
3 minute read
Technology spotlight Advances in technology
NeWS
TEChNOLOgYSPoTLIGHT
Advances in technology across industry
flexible electricity generation from areva
AREVA NP has installed a system to automatically adjust Goesgen Swiss nuclear power plant’s electricity generation to the needs of the grid operator. The successfully implemented solution varies the plant’s output between 50 and 100% of its installed capacity, without interaction of the operator. The output adaptation can be performed with power ramps of up to 30 megawatts per minute.
AREVA NP’s Advanced Load Following Control (ALFC) technology features a software upgrade of the reactor control system, adapts the relevant interfaces in the plant and comprises a comprehensive test series as well as operator training to ensure safe and proper operation.
“The intermittent electricity generation of renewable energy sources like wind and solar increases the need for balancing power. The ALFC system enhances the capabilities of nuclear power plants to deliver such services and to perform a stabilising role in the power grid,” said Carsten Dueweke, responsible for instrumentation & control projects at AREVA NP.
AREVA NP has already delivered its ALFC technology to four German nuclear power plants (Philippsburg 2, Isar 2, Brokdorf and Grohnde). Visit: www.areva.com
Transparent coatings for everyday applications
Dassault Systèmes helps to develop the first aircraft to be made in the United arab Emirates
Dassault Systèmes’ 3DEXPERIENCE platform has been used by Calidus, an Abu Dhabi-based advanced technology company recently incorporated, to develop its military light attack aircraft with multirole capabilities, the first such aircraft developed 100% in the United Arab Emirates.
The 3DEXPERIENCE platform enabled Calidus’s teams to virtually design, develop and optimise two prototypes within a two-year timeframe in order to unveil the aircraft at the Dubai Air Show 2017. Its single source of data and integrated applications accelerated Calidus’s design process and streamlined the company’s project collaboration both internally and externally with its suppliers.
“In 2015, Calidus set out to create a highly complex technological product and achieved its ambition on time by relying on a holistic digital approach to innovation,” said Philippe Forestier, executive vice-president, Global Affairs and Communities, Dassault Systèmes. “This achievement reinforces the 3DEXPERIENCE platform’s role in connecting people, ideas and data throughout a company’s value chain and across all disciplines, as well as Dassault Systèmes’ position as the technology partner of reference to the aerospace and defence industry.” Visit: www.3ds.com/industries/aerospace-defense Water- and dirt-repellent sportswear and outdoor clothing, or anti-fog windshields – there are many everyday products that can profit from highly hydrophobic coatings. For such coatings, researchers led by Dr Bastian E. Rapp at Karlsruhe Institute of Technology (KIT) have created Fluoropor, a material that is both transparent and abrasionresistant and that consists of a fluorinated polymer foam with continuous nano/micro-structure.
Water droplets run off the leaf surface: In nature, this phenomenon is mainly known from lotus plants. Researchers imitate this lotus effect by means of superhydrophobic, i.e. highly water-repellent, surfaces. Superhydrophobic properties develop due to structuring on the nano/microscale. Such extremely fine structures (one nanometre is a billionth of a metre) make surfaces highly sensitive to abrasion and account for the fact that they are not sufficiently robust for everyday applications.
In the case of Fluoropor, in contrast, the nano-/ microstructure is not limited to the surface but occurs throughout the material, thus giving the material a high long-term abrasion resistance and suitability for daily use. The foam seems optically transparent due to its tiny pores whose diameter is below the wavelength of visible light. Fluoropor, therefore, is ideally suited as a coating for transparent substrates such as glass. The material, can, however, also be applied to e.g., metal, polymers, or textiles.
Fluoropor can be efficiently manufactured in one step in different thicknesses by so-called photo-induced radical polymerisation. Visit: www.kit.edu
