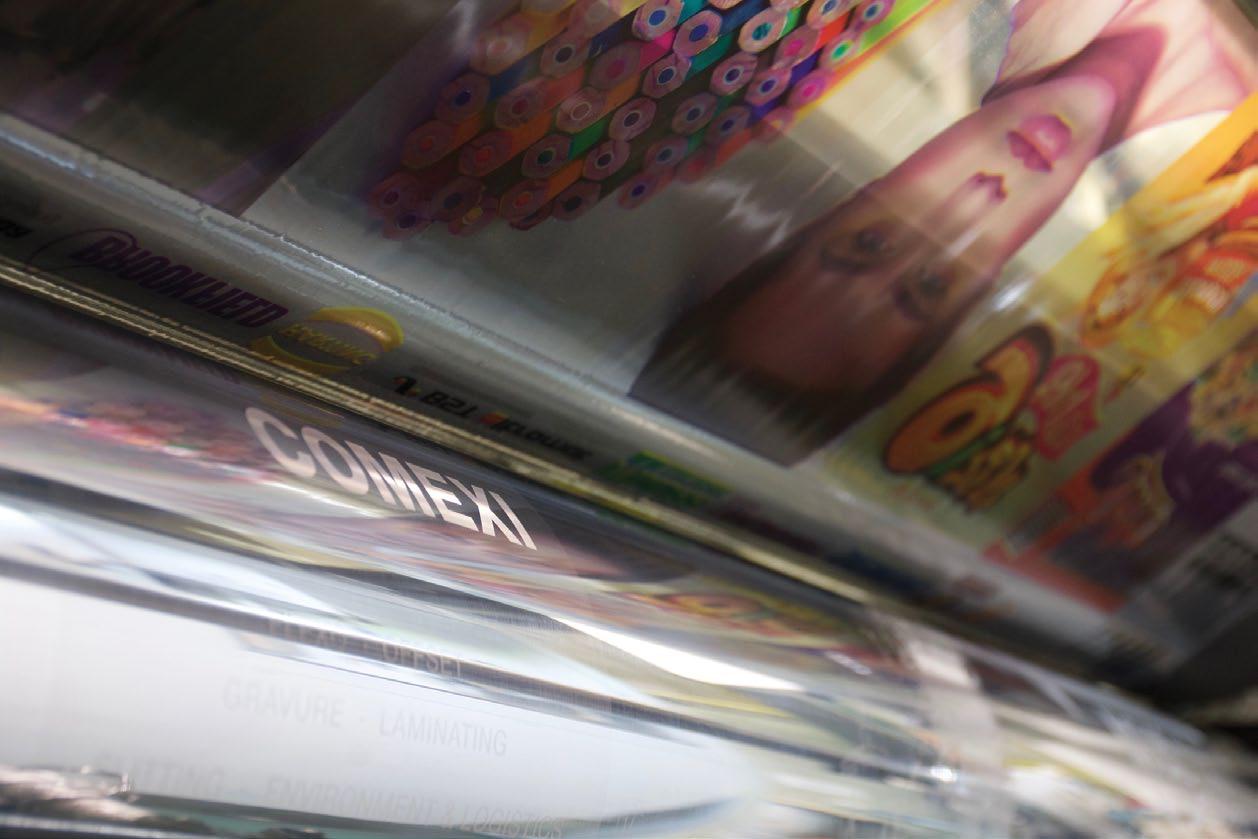
6 minute read
leader in packaging machinery solutions Comexi
LEaDER In PackaGInG MacHInERy SoLUTIonS
With over 60 years of experience in the field, Comexi has become one of the world’s leading manufacturers of flexographic presses to suit the market’s most demanding requirements. As a global supplier, offering cutting-edge solutions in gravure printing, laminating and slitting, the company has developed the most revolutionary solution for the most demanding clients: offset printing with central drum.


Comexi, founded in 1954 by the Xifra family, has a wide experience in manufacturing capital goods for the flexible packaging printing and converting industry. Comexi is made up of five product lines, each one specialised in a different conversion process: flexographic printing, offset printing, gravure printing, laminating, slitting and rewinding, as well as Industry 4.0. Each line provides global solutions to the demands of the constantly evolving market, with competitive and personalised equipment including the latest solutions in innovation, technology and sustainability – the three characteristics that define Comexi’s spirit and have made the company a leader in machinery solutions for the whole flexible packaging conversion sector.
Following its strategy of being the main global supplier for the flexible packaging industry, Comexi has also positioned itself as one of the leading and most cutting-edge companies in the development of solutions for laminating and coating, as well as slitting and rewinding. Its solutions for laminating and coating reduce the environmental impact with solvent-free and water-based tape applications as well as the usual solvent-based laminating. The company also offers the most sophisticated slitting and rewinding machines, researching and innovating constantly to satisfy the most demanding needs of the clients and end consumers, such as laser technology, labeling, robotisation and automation.
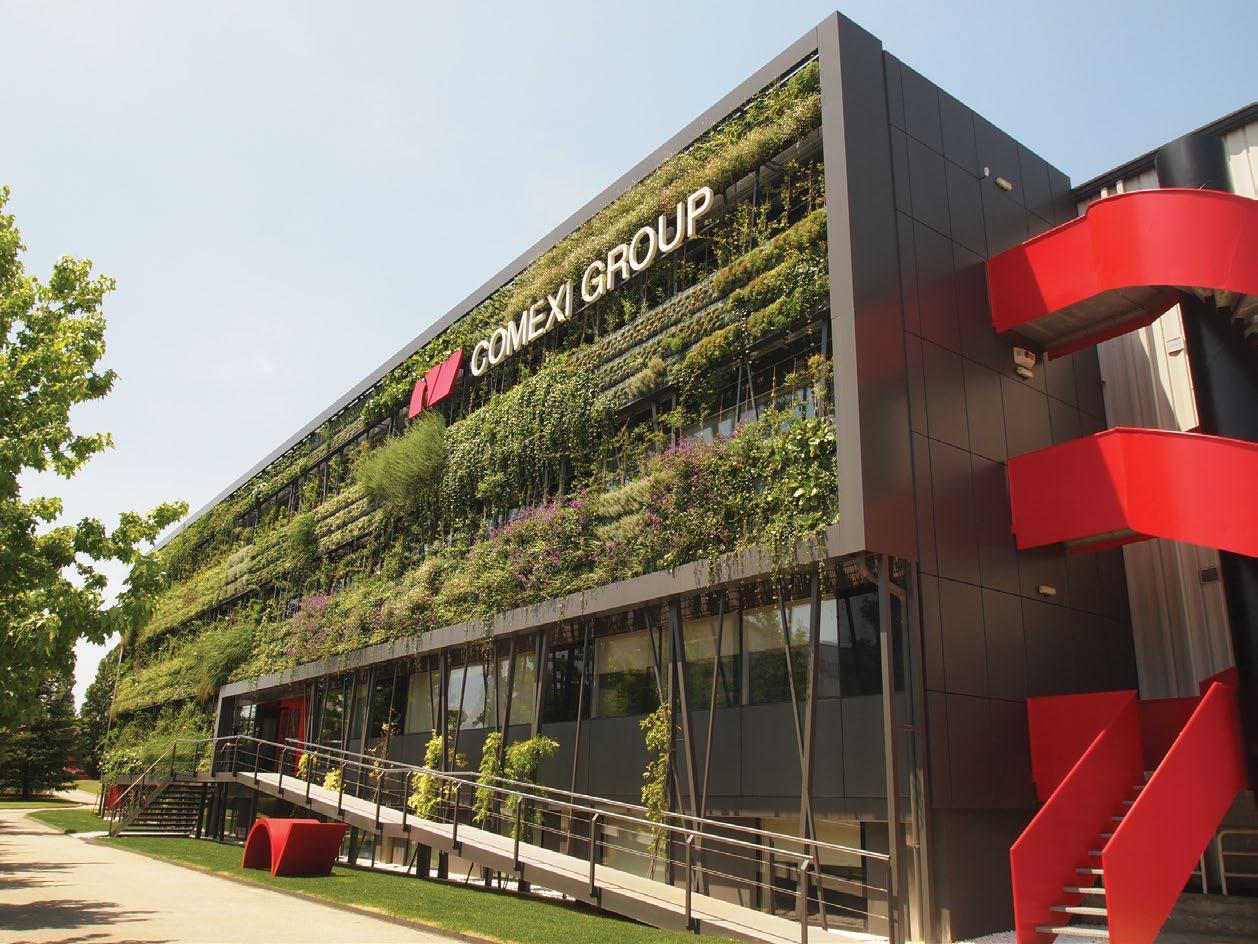
At the forefront
In 2016 and 2017, Comexi introduced new solutions including the Comexi F1 flexo press and Comexi F2 ML flexo press. It also created the Comexi S1 MS slitter. Moreover, in the coming weeks the group is launching a new laminator machine, the Comexi ML2, which offers total versatility to cover all kind of applications in the flexible packaging market.
The new Comexi F1 flexo press with robot technology offers a fully automatic changeover system for all the decks: sleeves, adapters and anilox. This innovation significantly reduces the changeover time and increases performance, improving the ergonomics and safety for the operator. The highly efficient press increases production output by at least 25 per cent, while allowing for the printing of 30 per cent more customised work. On the other hand, the Comexi F2 ML flexo press is an excellent machine from the point of view of profitability, designed to get the best quality at high speeds with large repeats. This flexographic press stands out for its high degree of versatility, while maintaining the ergonomics and usability features of all the Comexi F2 range.
Also, Comexi developed a revolutionary solution that adapts to the demanding time to market concept: offset printing with Central Impression Cylinder, which offers reduced costs per print and lessens the environmental impact thanks to the solvent-free EB offset inks. In this sense, over the past few months the group has completed new innovations and improvements and, currently, this machine offers maximum quality and is more competitive in terms of time-to-market. It can also achieve better production flexibility because its offset plates can be imaged on the site within minutes. The Comexi CI8 also stands out from the point of view of sustainability, aligning perfectly with Comexi’s environmental commitment. This technology has received two EMAS Awards for its sustainability credentials.
In response to the latest market demands, Comexi has developed its Cloud tool in order to make the jump to Industry 4.0. This tool provides the customer with real time and online data about production speeds, production output, productivity, set-up times, number of reels produced and downtime for preventive maintenance and repairs. It goes even further with job costing analytics, based on production time, film, inks and energy consumption. With this tool, factories and brand owners can see and understand quickly and easily all their data and processes to facilitate optimum decision-making.
A complete package
Comexi’s production facilities cover more than 36,000m2, divided into three production centres in Riudellots de la Selva (Girona, Spain), Montenegro (Rio Grande do Sul, Brazil) and Piacenza (Italy). All three production centers are working at its maximum production capacity. In addition, the company operates a commercial network in over 100 countries and has recently expanded its Service and Technical Assistance Department (SAT) in USA, Canada and South-East Asia

to offer a faster response to customers. At present, Comexi offers 24/7 technical service and assistance worldwide.
Comexi’s key sector is flexible packaging. Its effective organisation with business units for each product line, together with in-house R&D and product marketing teams, enable them to develop the necessary products required by customers and converters, and meet the latest trends and market demands. Apart from that, Comexi has the Manel Xifra Boada Technological Centre, Comexi CTec, a knowledge driver in the flexible packaging industry. Comexi CTec services cover several processes within the flexible packaging field and are divided into four areas: Consultancy, Innovation services, Demo Centre and Industrial Laboratory and Training and Academic activities. In 2017, Comexi CTec had more than 15,000 attendees to its 20 specialised courses.
Securing market leadership
Comexi’s key sales markets are Europe and America. All figures indicate that the company will experience significant growth worldwide during the coming years. Therefore, the group expects further consolidation of flexible packaging converters, which will result in a


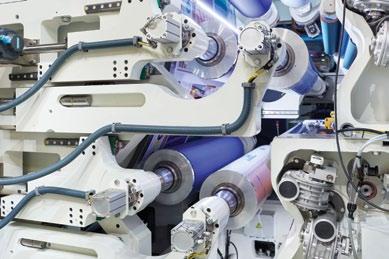
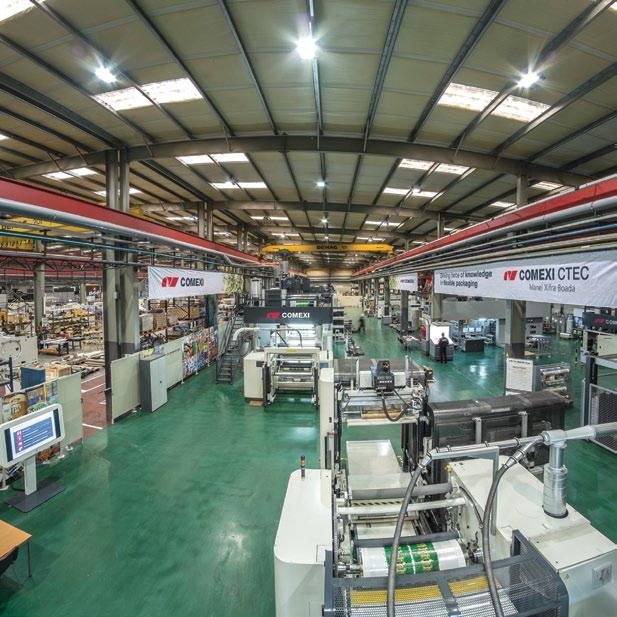
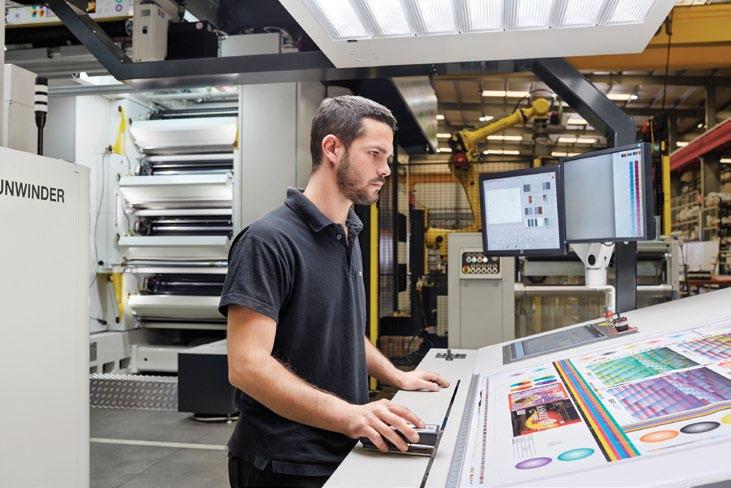
consolidation of factories and strategic investment plans in printing and converting equipment. In its turn, the market for manufacturers will also be consolidated and Comexi will be active in developing its manufacturing and service footprint on a global scale.
On a global scale, although the largest flexible packaging market in terms of value is North America, followed by Europe, the biggest flexible packaging growth market is undoubtedly Asia. This creates very interesting opportunities as demand for printing presses and converting equipment is anticipated to increase here and Comexi will ready to satisfy that demand.
The group has achieved significant growth over the past few years, owing mainly to the success of its flexographic, laminating, slitting and gravure technologies. At the same time, the company has been investing in research and developing successful innovative solutions, such as the Comexi CI8 offset printer. Furthermore, thanks to its Comexi CTec technological centre, the group has been able to position itself as a technological frontrunner, which has a deep and extensive knowledge of the flexible packaging industry. Looking forward, the group plans to grow through strategic partnerships, securing its market leadership by developing new technologies in the flexible packaging industry. n
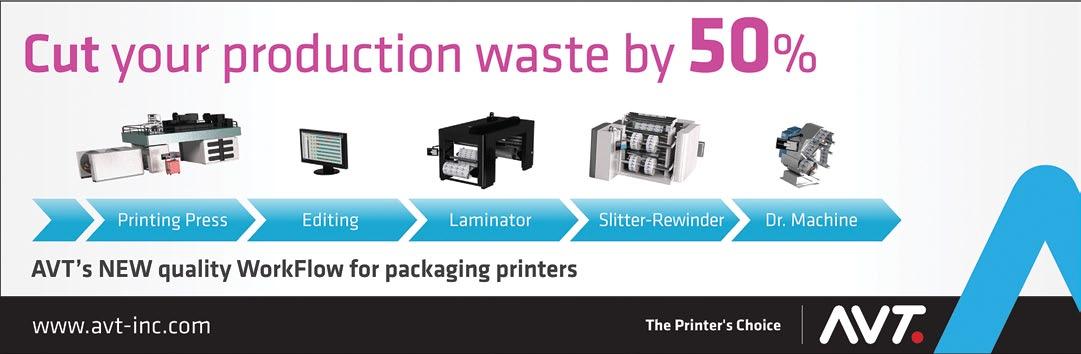
AVT
AVT’s WorkFlow link Solutions provide the essential connection between Printing and Finishing, for efficient removal of defective material Based on best in class 100% automatic inspection, it enables the best of both worlds – superior process control and waste savings, as well as 100% quality assurance, ensuring that your customers receive defect-free material.
WorkFlow link maximizes your entire operation with increased efficiency by eliminating the need for manual inspection – so you can run your converting machinery at maximum speed stopping automatically only at the relevant defective sections to be removed.
From printing through lamination, to rewinding, slitting or doctoring process, AVT’s Workflow link is both efficient and cost-effective. once deployed, it carefully tracks and controls the removal of defective material to help you deliver only quality products.