
4 minute read
Fast-forwarding efficiency Eton Systems
faST-foRWaRDInG EfficiEncy
Eton Systems is a global leader in the design and manufacture of advanced material handling systems. These systems are designed to eliminate manual involvement in the world’s production lines and to optimise handling efficiency. The company continues to set new standards for a broad range of manufacturing industries, from textiles to automotive products and furniture. Philip Yorke reports.
Eton Systems was founded in Sweden in 1967 by the Eton Fashion house, a company that has specialised in making shirts since 1928. However, Eton’s need to minimise downtime and streamline its production processes subsequently resulted in one of its founders, Inge Davidson, being inspired to develop new conveying technologies and the world’s first UPS (Unit Production System). Today Eton systems are employed in more than 60 countries worldwide, increasing productivity for companies across a broad range of manufacturing industries.
Flexible productivity
Eton’s unique Flexible Productivity Concept (FPS) is based upon two distinct production platforms that provide a wide variety of flexible system tools that significantly improve efficiency and customer profitability. The unique systems provide highly efficient solutions, which can be perfectly tailored to suit each individual customer’s needs. This involves removing the need for the handling of pallets, pallet racks, forklifts and all heavy manual lifting operations.
By reducing handling processes and the equipment involved, Eton can increase manufacturing production levels by between 60 and 100 per cent. Furthermore, through its latest patented systems the company can buffer both large and small items without any parts coming into contact with each other or getting soiled, thus allowing the handling of products with sensitive surfaces that are produced in both clean rooms and other challenging environments. Virtually all Eton system components are manufactured in Europe in order to meet the high engineering standards it demands and to deliver the best possible quality and operational reliability for its customers.
Today the company’s main focus is on vehicles, plastic filters, painting, assembly and furniture. Taking furniture as an example, Eton’s conveyer systems offer a big advantage as they are able to handle both hard and soft materials in a company’s supply chain.
This is especially important when it comes to the emerging economies of China, India and Brazil, where the company is clearly focused on system optimisation and the adoption of the latest high end technologies in order to achieve optimal productivity levels.
Strengthening uS presence
This year Eton will expand its presence significantly in the US with its automotive, textile, apparel, furniture and plastics industry system applications. High labour costs and a growing demand for stringent quality controls and faster delivery to markets means that Eton’s state-of-the-art technology has gained a lot of ground in the major growth markets of the world. Over recent years, Eton Systems has achieved high levels of sales in a variety of industry sectors, especially in the textile market, which is why the company believes that it is now time to leverage its success by making a greater investment in the US market.
Until recently, Eton Systems has relied upon its network of independent sales agents for its business in the North American market. However since the first quarter of this year, all sales related activities in the US are being handled directly through its headquarters in that market, in order to increase its presence and to ensure even better customer service.
The investment plan is both ambitious and comprehensive and is timed to coincide with the launch of the next generation of Eton technology, which is just around the corner. Therefore Eton is currently looking to recruit the best people for the job, including a new sales team, aftersales support staff, as well as new educational and training staff.
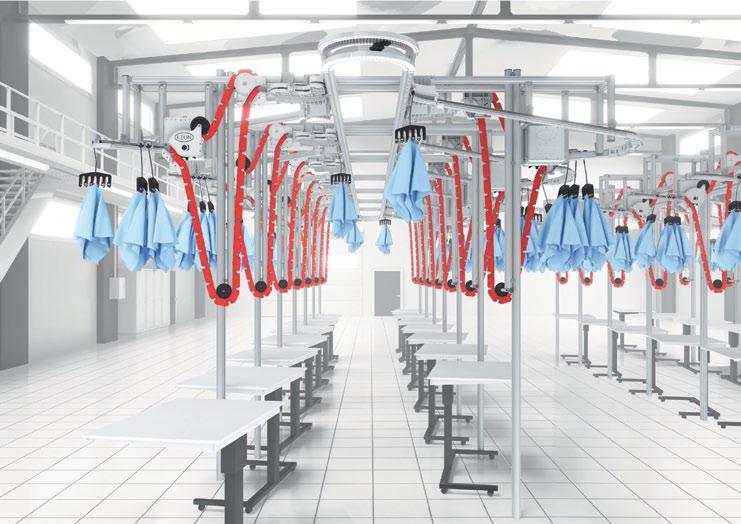
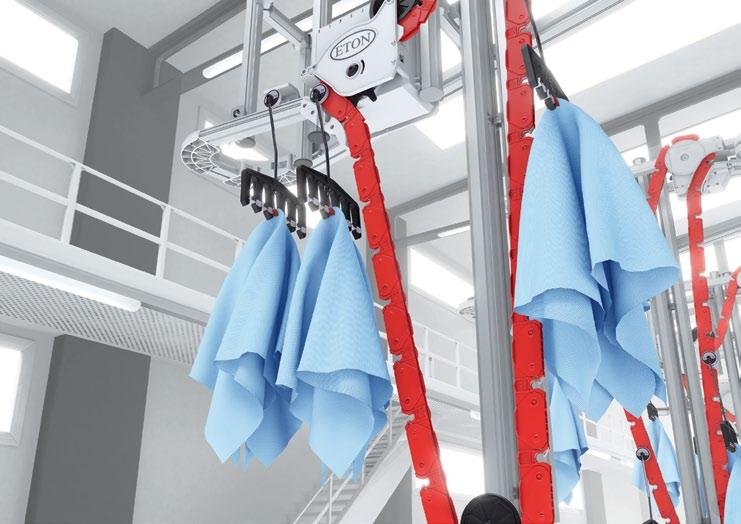
Alex Vega is responsible for realising the new venture and has broad international experience of initiating and successfully managing new branches for global enterprises. Most recently this was as MD and International Sales Director for Eastern-Bell Sports Europe. “Of course we see many advantages of being closer to our customers and having a direct overview of operations,” said Vega. “It allows us to be more flexible and to optimise delivery precision, thus providing a whole new service level to our current and new customers,” he added.
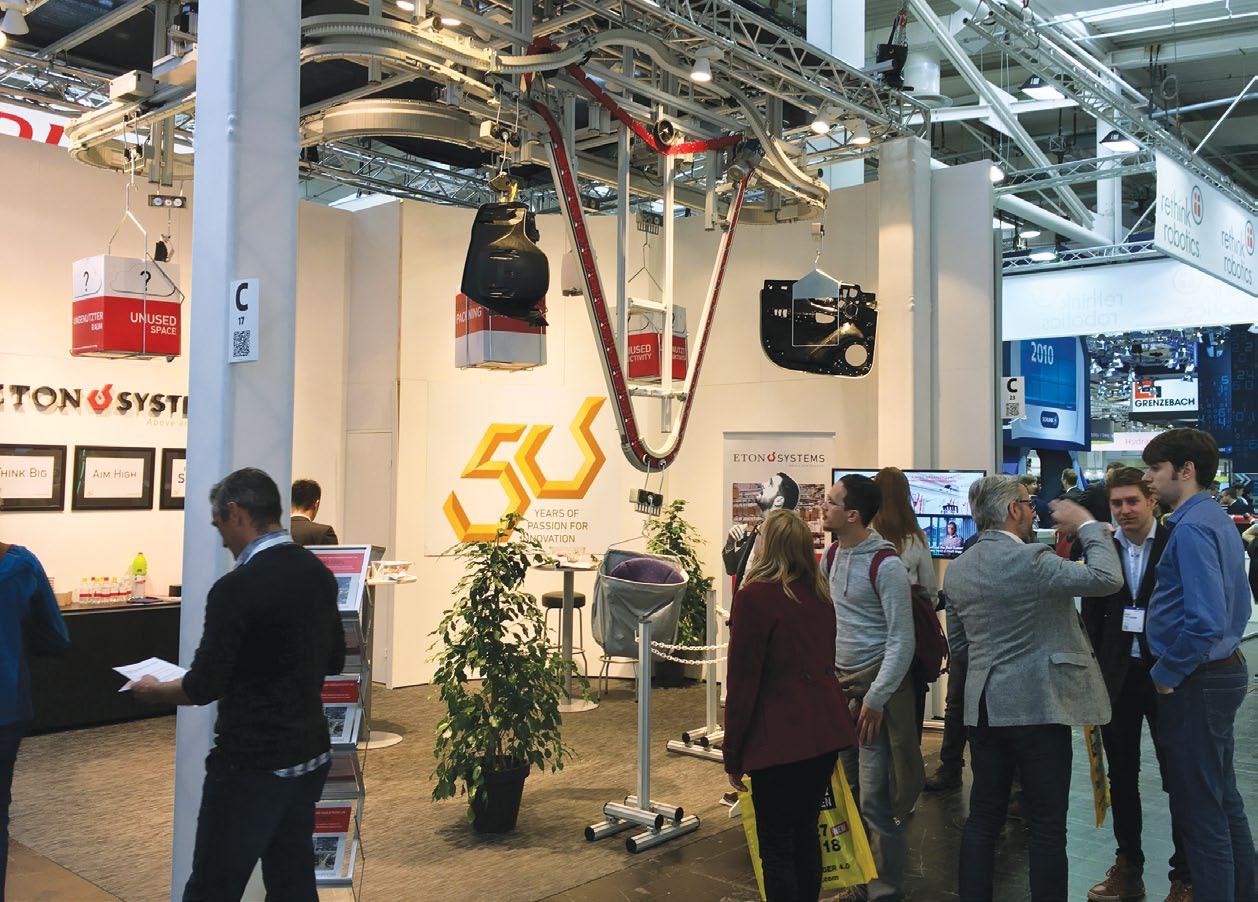
mascot for success
Mascot is a leading Danish apparel company and one of Europe’s largest manufacturers of workwear. This ambitious company continues to expand its global footprint with a clear goal to increase the number of production facilities under its own management. Mascot Vietnam has over 1000 employees and currently is producing over 6000 items of workwear every day. This represents around 30 per cent of Mascot’s total production output. In order to meet growing global demand, Mascot has recently inserted a new mezzanine floor at its present sewing facility in Vietnam which will support a further 300 employees.
To ensure the highest, most efficient production lines, the company installed the latest Eton Systems, which offer fully automatic conveyancing systems and transports products from one seamstress to the next. The company’s Danish production manager, Morgan Dietrich has no doubt that this represents a most valuable acquisition. “Eton is an excellent management tool, which can measure the efficiency of the individual sub-operation in the sewing line. It means that you can react quickly if any sub operators are not functioning optimally. You can even follow each order through the production line in Vietnam, simply sitting at your desk in Denmark,” he said.
For further details of Eton’s unique high-performance systems and services visit www.etonsystems.com
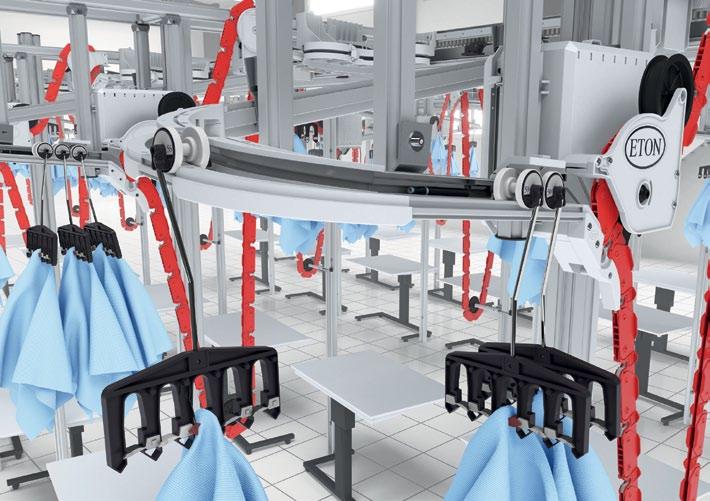
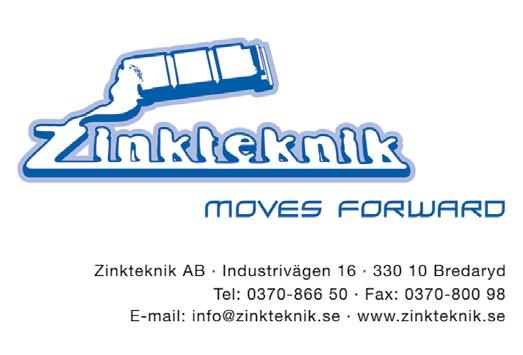