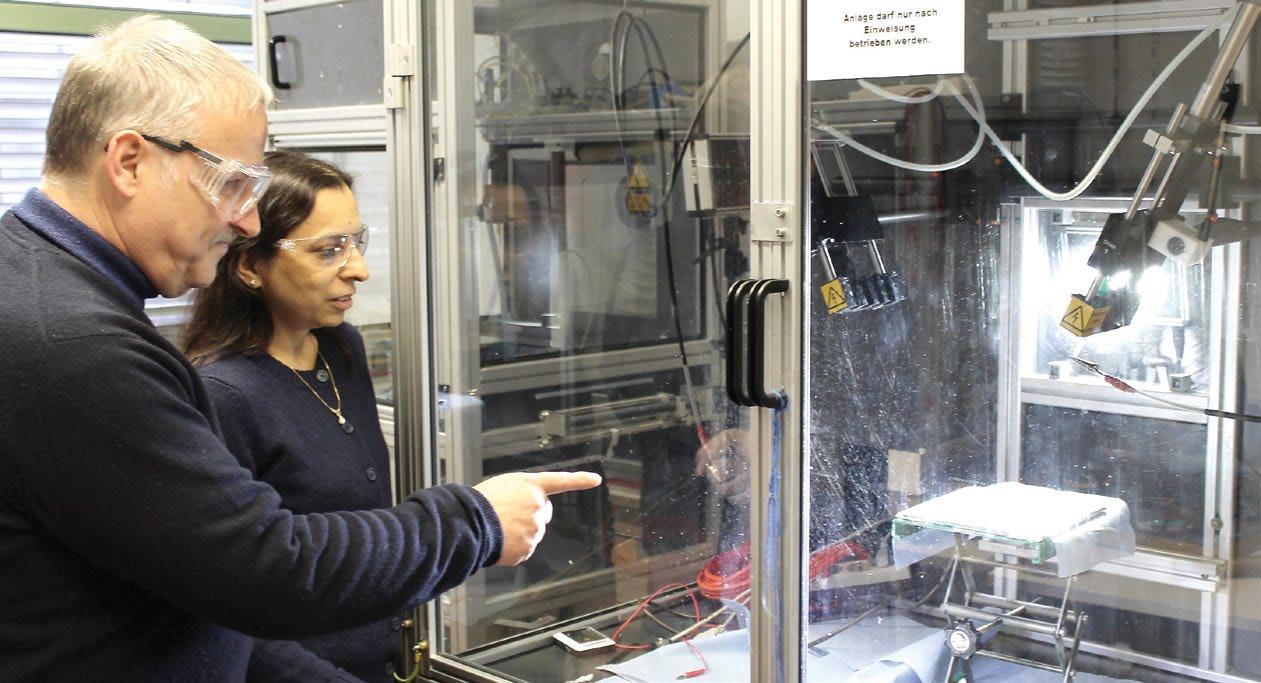
5 minute read
Smart dress The future of wearable tech
Prof. Dr. Andreas Greiner (left) and Prof. Dr. Seema Agarwal (right) with equipment for electrospinning at the university of Bayreuth. Credit- Christian Wißler
smart dress
We’ve been hearing a lot about smart textiles recently. From fabrics to regulate body temperature to those that can release medication into the skin, in the future the clothes we wear will no longer be just an aesthetic statement. Industry Europe looks at just some of the innovations in this field over the past year.
IN the Internet of Things, everything is connected – and this includes what we wear. According to a 2016 report by the technology consultancy Cientifica, the smart textiles industry – dubbed ‘Fashion’s Fourth Industrial Revolution’ – will be worth more than $130 billion by 2025.
Recognising that tomorrow’s consumer will expect more from their clothes, textile manufacturers and research institutions are investing in the latest technologies to develop fabrics combining technological components that can monitor external stimiuli, translate this into data and respond accordingly.
Special functions of the most recent ‘ultrasmart’ textiles can include regulating body temperature, releasing medication into the skin or even controlling the vibration of muscles during exercise. In addition, there are also more aesthetic applications for smart textiles, such as those that can change colour, light up or even display pictures or video.
To give some idea of the areas researchers and manufacturers are focusing on, here are just some of the more interesting stories from the world of technical textile technology over the past year.

Heated clothing technology
At this year’s ISPO Munich trade show, DuPont Advanced Materials announced the launch of Intexar Heat, a powered smart clothing technology for on-body heating.
“Intexar Heat is a revolutionary stretchable ink and film that when powered, creates a comfortable warmth,” said Michael Burrows, Global Business Manager, DuPont Advanced Materials. “Our team has worked hard to develop a heater that feels like fabric, doesn’t rely on cables, thick wires or big batteries, and can stand up to very cold environments. From outdoor enthusiasts to industrial workers, Intexar Heat can help conquer the elements in comfort, increasing focus and improving performance.”
Formosa Taffeta Company was the first textiles manufacturer to incorporate the Intexar Heat technology as part of its Permawarm line. Permawarm delivers clothing brands a complete garment heater system including the Intexar heater, connectors and control software.
Comfortable conductors
Up to now, textiles that are capable of conducting electricity have tended to be rigid, uncomfortable and generally impractical for everyday use. However, researchers at the University of Bayreuth, Donghua University in Shanghai and Nanjing Forestry University think they may have come up with a solution to this with the development of new, more wearable conductive nonwoven materials.
The materials developed by Prof. Dr Andreas Greiner’s team from the University of Bayreuth and their Chinese partners are flexible, and can thus adapt to movements and changes in posture. Furthermore, they are air-permeable, meaning they allow the skin to ‘breathe’ normally. These properties have been achieved through a unique production process: rather than inserting metal wires into finished textiles, the scientists modified the
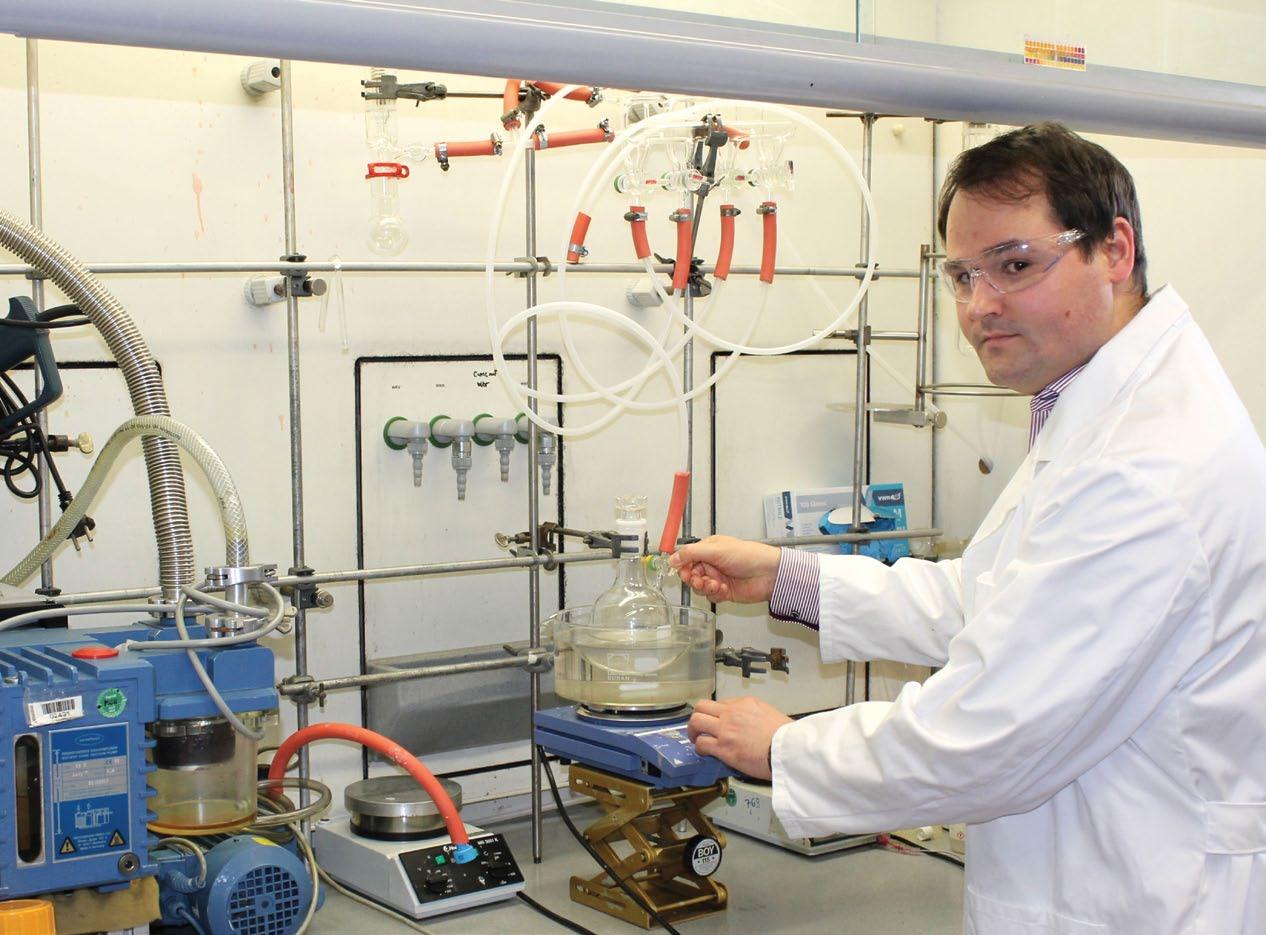
Steffen Reich m.Sc, doctoral student at the university of Bayreuth, producing a dispersion with tiny silver wires. Photo- Christian Wißler.
classic method of electro-spinning – used in nonwovens production for years. They found the resulting nonwoven material exhibits a very high degree of electrical conductivity.
This research, they say, could pave the way for comfortable garments with many technological functions. They could, for example, convert sunlight to warmth or contain sensors for fitness training.
Elsewhere, engineers at the University of Exeter in the UK are also threading circuitry into clothes to create comfortable devices that could make electronic fashion the future of the textiles industry.
Dr Ana Neves, a researcher at the university who specialises in wearable electronics, thinks bulky design is partly to blame for the lack of comfort in current wearable tech.
“The user needs to feel comfortable,” she said. “Most smart textiles still rely on integrating conventional electronics onto fabrics, attaching them to the surface and removing them when the textile needs to be washed.”
As part of the E-TEX project, Dr Neves and her colleagues are building devices directly into the fibres of textiles using flexible and lightweight components. A t-shirt, for example, could be designed to monitor the wearer’s heartbeat without the need for embedded electronics.
The idea for the project came about in 2014 when Dr Neves developed a technique to make textile fibres conduct electricity by coating them with graphene. She then decided to apply the method to incorporate electronics into clothing.
The properties of graphene are ideal for use in textiles. The semi-metal is just a few atoms thick, making it extremely lightweight, and it can be bent and even stretched while remaining robust. It is also transparent, which makes it suitable for light-emitting displays.
Furthermore, applying a coating to fabrics should be easy to integrate into existing clothing production. “If we simply add a step or two, the chances of this type of technology being adopted will be significantly higher than if we tell a manufacturer that they need to completely reformulate their production lines,” said Dr Neves.
medical applications
There have also been great advances in recent years in the area of smart textiles for healthcare. For example, the US company TissueGen is the developer of ELUTE fibre, a groundbreaking biodegradable fibre format for drug delivery, nerve regeneration and tissue engineering.
ELUTE can directly replace standard fibres used in standard biodegradable textiles and deliver medication directly at the site of the implanted fibre. For device developers, this means they can use the sophisticated drug delivery capabilities of absorbable fibres.
In future, the wider incorporation of such drug-loaded fibres into new or existing medical devices can result in faster healing, improved patient compliance and lower negative outcomes. The fibres can be used in regenerative medicine and medical devices such as cardiac stents, orthopedic sutures, peripheral vascular stents and many more besides. n
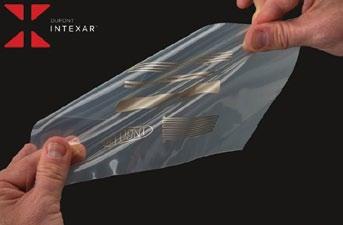