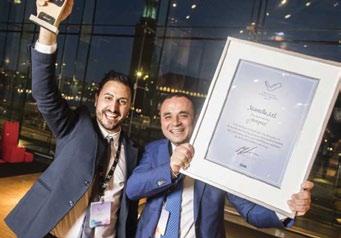
7 minute read
metals news The latest from the industry
NeWS
New developments in the Metals industry
ArcelorMittal breaks ground on pioneering carbon capture installation
ArcelorMittal has begun construction of new premises at its site in Ghent, Belgium, to house a pioneering new installation which will convert carbon-containing gas from its blast furnaces into bioethanol. If successful, the new concept has the potential to revolutionise blast furnace carbon emissions capture and support the decarbonisation of the transport sector.
The technology in the gas conversion process was pioneered by Chicago-based company LanzaTech, with whom ArcelorMittal has entered a long-term partnership. The technology licensed by LanzaTech uses microbes that feed on carbon monoxide to produce bioethanol. The bioethanol will be used as transport fuel or potentially in the production of plastics.
This is the first installation of its kind on an industrial scale in Europe and once complete, annual production of bioethanol at Ghent is expected to reach around 80 million litres, which will yield an annual CO2 saving equivalent to putting 100,000 electric cars on the road. The new installation will create up to 500 construction jobs over the next two years and 20 to 30 new permanent direct jobs. Commissioning and first production is expected by mid-2020. Visit: www.arcelormittal.com
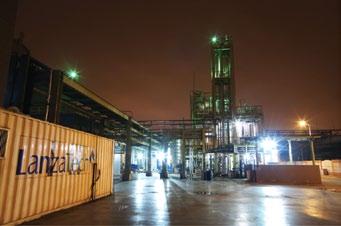
Construction begins on HYBRIT fossil-free steel plant
The HYBRIT initiative, a joint venture company owned by SSAB, LKAB and Vattenfall, has started construction on the first pilot plant for creating fossil-free steel in Luleå, Sweden. SSAB, LKAB, and Vattenfall have, alongside the Swedish Energy Agency, invested SEK 1,4 billion in the pilot plant. This means that the HYBRIT initiative has now entered its second phase. The goal is fossil-free, ore-based steel production, on an industrial scale.
The plant is expected to be ready by 2020 and its completion opens the possibility for fullscale testing and development of the technique to produce steel by using hydrogen instead of coal and coke. This could lead to a historical shift in production techniques, with water as a by-product instead of carbon dioxide emissions.
“By testing in pilot scale, we can leave the small-scale laboratory environment and instead mimic the coming industrial process, and prepare for efficient production. We are very happy to be able to enter the next phase and get one step closer to our target of fossil-free steel production, with all its environmental benefits,” says Mårten Görnerup, CEO of HYBRIT. Visit: www.hybritdevelopment.com

mantella announced as swedish steel prize winner 2018
The winner of the prestigious International Swedish Steel Prize has been announced, and this year the honour goes to Italy-based Mantella Srl for its innovative Stratosphere 3.0 rear-tipping semi-trailer.
The Stratosphere 3.0 has a chassis with the same weight as an aluminium frame, but with superior mechanical properties. It has outstanding wear resistance, greater fatigue life and offers weight reduction of around 30% compared to previous trailer chassis on the market.
“Mantella has come up with a unique design that represents an entirely new generation in tipper and body solutions. Skilled design work, smart production methods and fully utilising the advantages of high-strength and wear-resistant steel made it possible,” says Eva Petursson, Chair of the Swedish Steel Prize jury and Head of SSAB’s Strategic R&D.
The chassis is made entirely of high-strength steel with formed Z-beams instead of the classic welded I profile. Eliminating the welded beams gives vital improvements in fatigue resistance as well as production efficiency. It also provides an increase in load capacity, while maintaining a low weight. Additionally, the body of the Stratosphere 3.0 is made from wear-resistant steel, guaranteeing excellent durability over time. Visit: www.steelprize.com
Outotec to supply Boliden’s sulphuric acid plant in Sweden
outotec has agreed with the Swedenbased mining company Boliden on the design and delivery of an absorption section to be built for the sulphuric acid plant at the Rönnskär smelter. The order has been booked in outotec’s 2018 secondquarter order intake. Typically orders of this size and scope are valued at over €10 million. The Boliden Rönnskär plant is one of the world’s most efficient copper smelters. The new absorption section designed by outotec will be able to process the future gas volume from the upstream smelting process with high energy recovery. outotec’s deliveries will take place in the second half of 2019.
“We are extremely pleased that our longterm partner Boliden awarded us this order. outotec’s advanced absorption solution will safeguard the future capacity of the sulphuric acid plant and meet all of the current and planned european environmental requirements,” says Kalle Härkki, head of outotec’s metals, energy & Water business unit. Visit: www.outotec.com
INDUSTRYNEWS
Rio Tinto to begin work on Koodaideri iron ore mine in 2019
Mining giant Rio Tinto has announced it will begin developing its Koodaideri iron ore mine in Western Australia’s Pilbara region next year, highlighting parallel plans to de-bottleneck rail capacity, which should increase it to 360 million tonnes per annum (mtpa) in 2019.
The company expects to mine its first iron ore from the project, which it says is one of the world’s most technologically advanced, in 2021.
“The Koodaideri orebody is 50km long and 5km wide. It will be a new production hub which will be a key feature for the Pilbara for many years to come,” said Rio Tinto iron ore chief executive Chris Salisbury.
He also noted the mine would be the first one to take full advantage of automation in trucking and drilling. Visit: www.riotinto.com
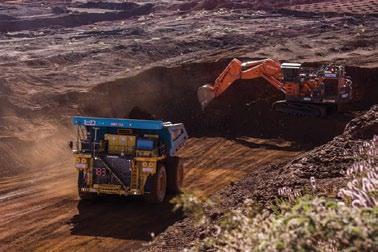
With the steel framed structure and load-bearing sheets designed and manufactured by Ruukki, the installation of the world’s largest indoor ski centre in Norway has commenced in Lørenskog near Oslo. The steel structure used to complete the architectural creation is based entirely on Ruukki’s own design.
“Over the past two years we have worked closely with the customer and taken the project forward. The design, manufacture and installation of the structures have all progressed to schedule. This is real testimony to what can be achieved with close, well-functioning collaboration at an early stage,” explains Petri Nieminen, SVP, Ruukki Building Systems.
The ski centre is spread over six storeys and houses a snow-covered area of around 40,000m2 – the same size as five football pitches. The downhill ski slope is 505 metres long and 100 metres wide at its widest point. The height difference is 90 metres. The slope will be equipped with three ski lifts with a combined capacity of 5000 skiers and hour. The ski track will comprise 120 components and weigh about 400 tonnes. Visit: www.ruukki.com
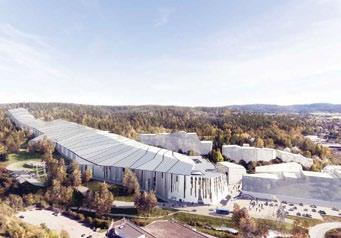
tata steel europe and posco sign auto steel partnership

Tata Steel Europe and South Korean steelmaker POSCO have signed an agreement to develop a new generation of steel products for automakers and other manufacturers to access.
The deal will allow Tata Steel Europe to access Physical Vapour Deposition (PVD) technology, an innovative process that allow steels to be given anticorrosion coatings without the current requirement to heat them during the hot-dip galvanising process. This has the potential to allow for an increase in the number of steel products on which specific anticorrosion coatings can be used. In exchange the agreement means POSCO will be able to produce Tata Steel Europe’s patented MagiZinc.
MagiZinc is an innovative hot-dip galvanised coating providing enhanced corrosion protection even in harsh environments. Its formulation allows it to outperform conventional galvanised steel, which is why the coating has been widely adopted by the EU automotive and construction industry since its market introduction in 2009.
Collaboration with POSCO represents the next phase in Tata Steel Europe’s ambition to support customers by making the MagiZinc® product available globally. Visit: www.tatasteeleurope.com
Polymetal International announces start-up of Kyzyl mine
Polymetal International plc has announced the start-up of the new Kyzyl mine in Kazakhstan, ahead of schedule and below budget. Following the completion of all construction and commissioning activities, Kyzyl successfully produced its first gold concentrate on 25 June. Polymetal has achieved the start-up of the concentrator one quarter ahead of the original schedule announced in 2014, and one month earlier compared with the January 2018 updated plan. mining activities have reached full design capacity with 315 kt of ore stockpiled ahead of start-up. The grade control programme demonstrated robust reconciliation with the reserve model with both ore grade and gold contained tracking slightly above plan. First concentrate deliveries to off-takers are scheduled for the end of July.
“Polymetal is delighted and proud to successfully complete the largest development project in the company’s history ahead of time and below budget,” said Vitaly Nesis, Group Ceo of Polymetal. Visit: www.polymetalinternational.com