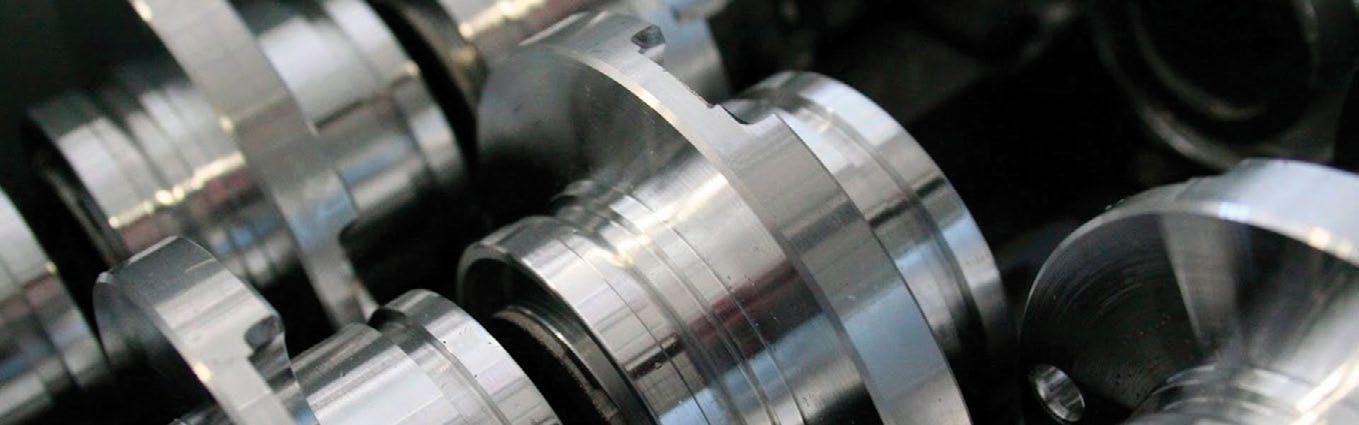
4 minute read
Integrated precision Brovedani Group
INTEGRATED PRECISION
Brovedani is a global leader in the development and manufacture of precision components for the automotive industry. The company continues to see strong growth due to its commitment to innovation and its renowned high precision engineering. Philip Yorke reports on a company that is spearheading the move into the digital age and the latest integrated production technologies.
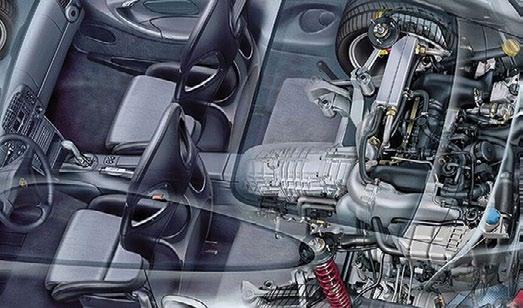
The Brovedani Group was founded in Tagliamento, Italy in 1947 and consists of three companies and six state-of-the-art plants, two of which are located in Italy, with others based in Mexico and Slovakia. The group currently employs more than 1,100 people and in 2017 recorded sales of around €120 million. This multinational company primarily focuses on components for the automotive industry, offering specialised solutions for fuel injection pumps, as well as for petrol direct injection systems and diesel common rail systems. In addition, it designs and manufactures components for air conditioning systems, starter motors and vehicle chassis.
The group benefits from its integrated organisational structure and innovative culture. As a result, it has become the component supplier of choice for global brands such as Bosch, Continental, Denso, Delphi and Eaton, among many others. Innovative solutions

The Brovedani Group has invested consistently in advanced manufacturing and control system technology for its mass production of sophisticated, high precision mechanical components. The company’s cutting edge engineering departments develop dedicated products that involve the design and construction of custom-built machines with integrated, multi-functional technologies. It also designs complete production lines for outsourced products, which further endorses Brovedani as a valued world-class partner dedicated to meeting – and exceeding – its customers’ needs.
Solid progress
The Brovedani Group took another strategic step forward when it implemented new Solid Edge Software in collaboration with its
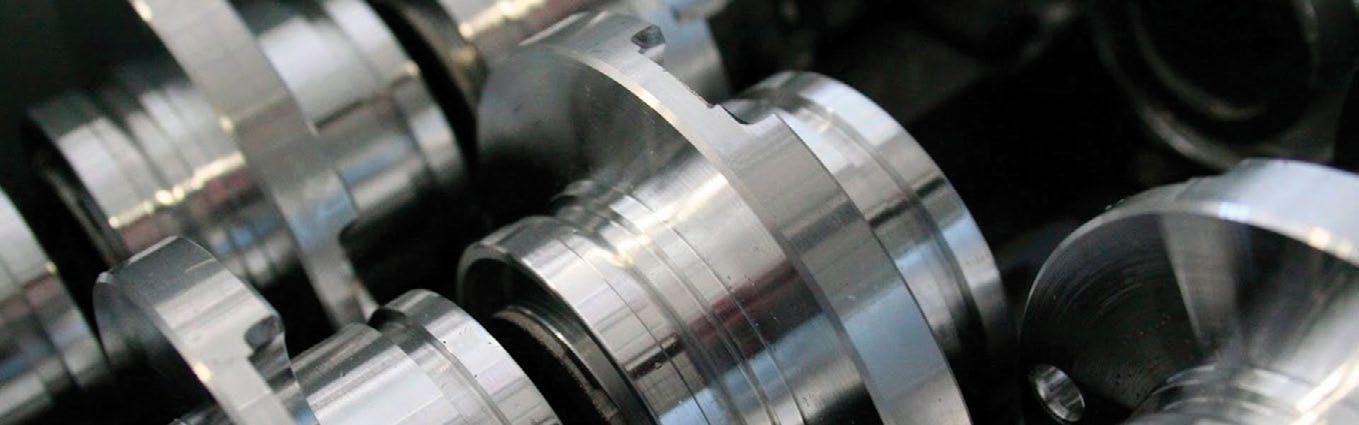
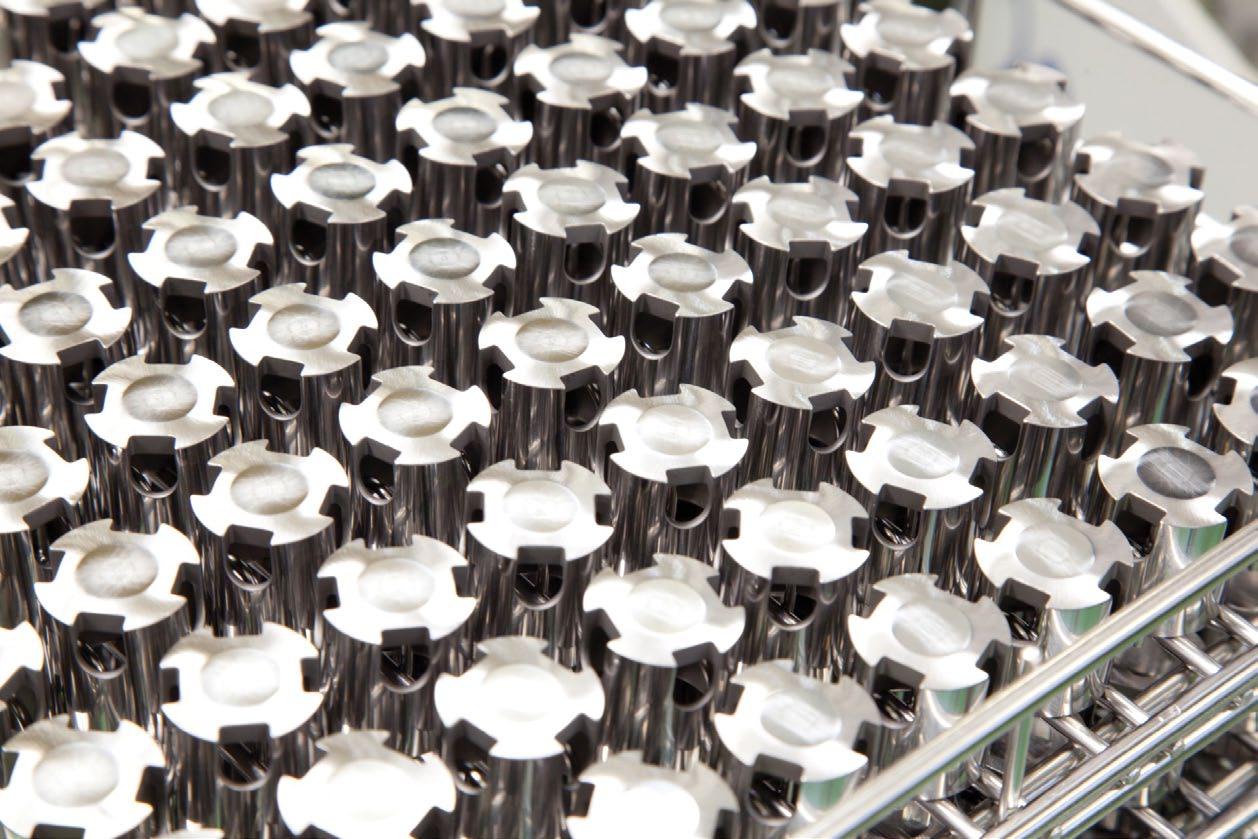
Siemens PLM Software partner, CCS, which has been supporting Brovedani from the start of the data exchange project.
Following this move, the company acquired additional licenses for the use of Solid Edge technology, choosing different configurations according to its specific requirements. To design industrial equipment, Brovedani requires full manufacturing licenses, which are also required for sheet metal, cabling and other functional items. However, design and drafting licenses are both very useful for handling small drawings and for machine design. As a result, Solid Edge technology will become a corporate standard and will now be extended to enhance the company’s plants in Italy, Slovakia and Mexico.
The benefits realised by Brovedani using Solid Edge technology are tangible and measurable. There are around 3000–4000 components and around 800 2D drawings required for each machine, making each one a unique creation. The level of customisation is therefore very high at Brovedani. “Our decision to apply 3D to the design and development of standalone machines was pioneering,” the company told Industry Europe.
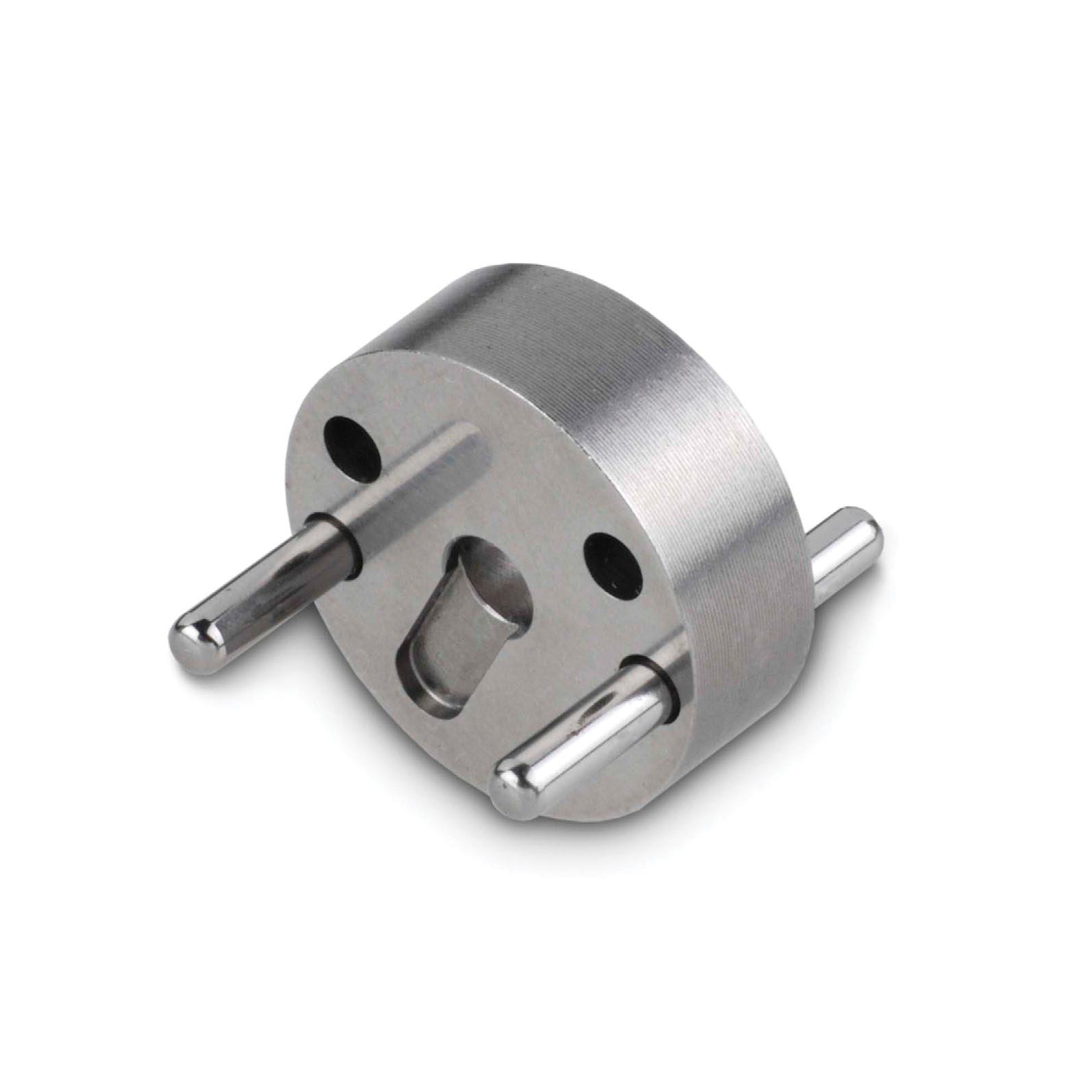
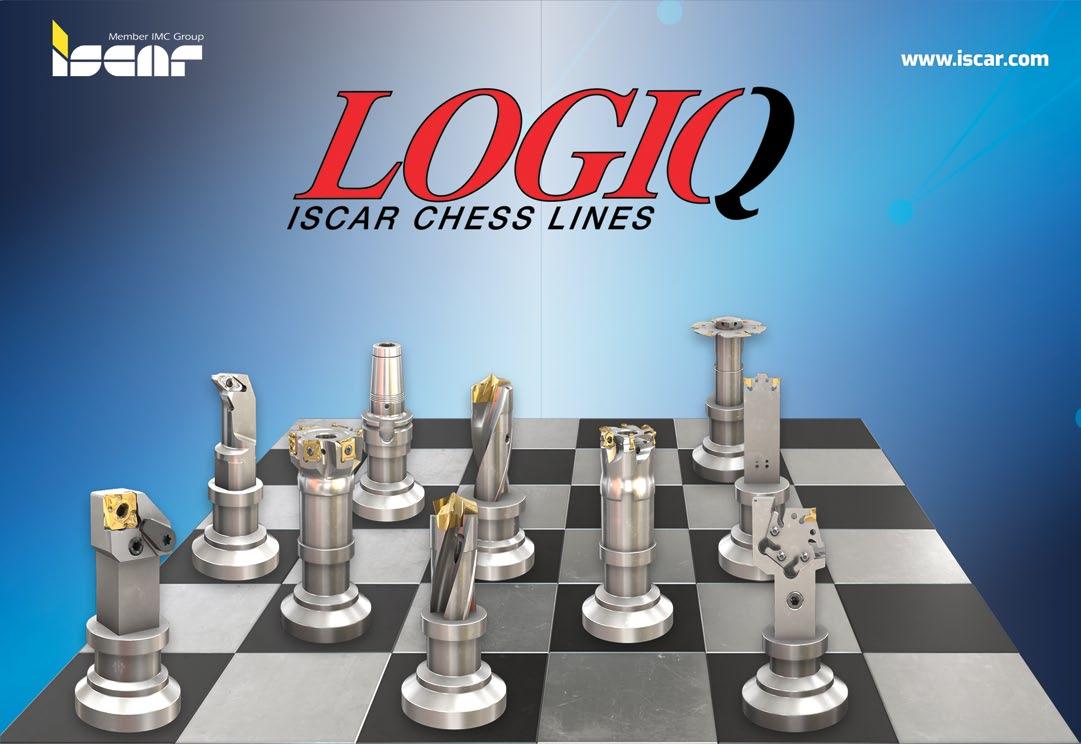
“However, there are few standard components that are common to all machines and here, the use of Solid Edge technology makes it much easier to re-use our data.” The company added that it now achieves savings of around 30 per cent as part of its overall productivity costs.
Digital crossroads
At the dawn of the third millennium the digital revolution is in full flood and is manifested in the industry’s acceptance of its 4.0 business principles. This new business tool is particularly relevant to the Brovedani Group as it stands with other global players at the digital crossroads. Today the sharing of data via cloud and the increasing availability of ‘open data’ streamlines communications and enhances efficiency.
Calculating the capacity of machines that are capable of analysing data, coupled with the ability to modify presses autonomously, is also a major advantage. This is encapsulated in the industry phrase, ‘Machine learning’. Furthermore, interaction between man and machines with touch-screen interfaces and augmented reality is also a valuable tool in the constant challenge to achieve a more efficient and more sustainable business.
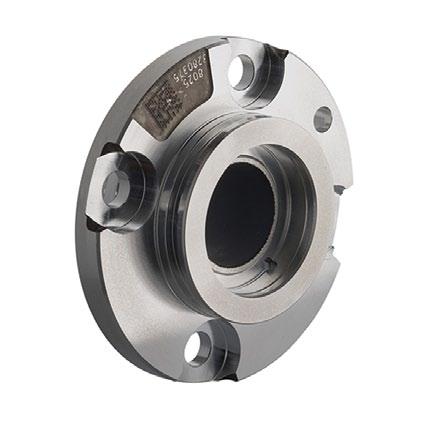
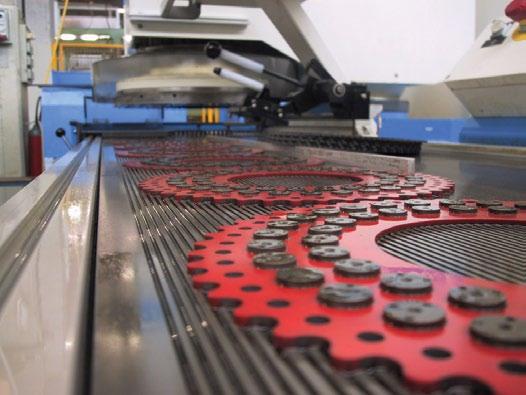
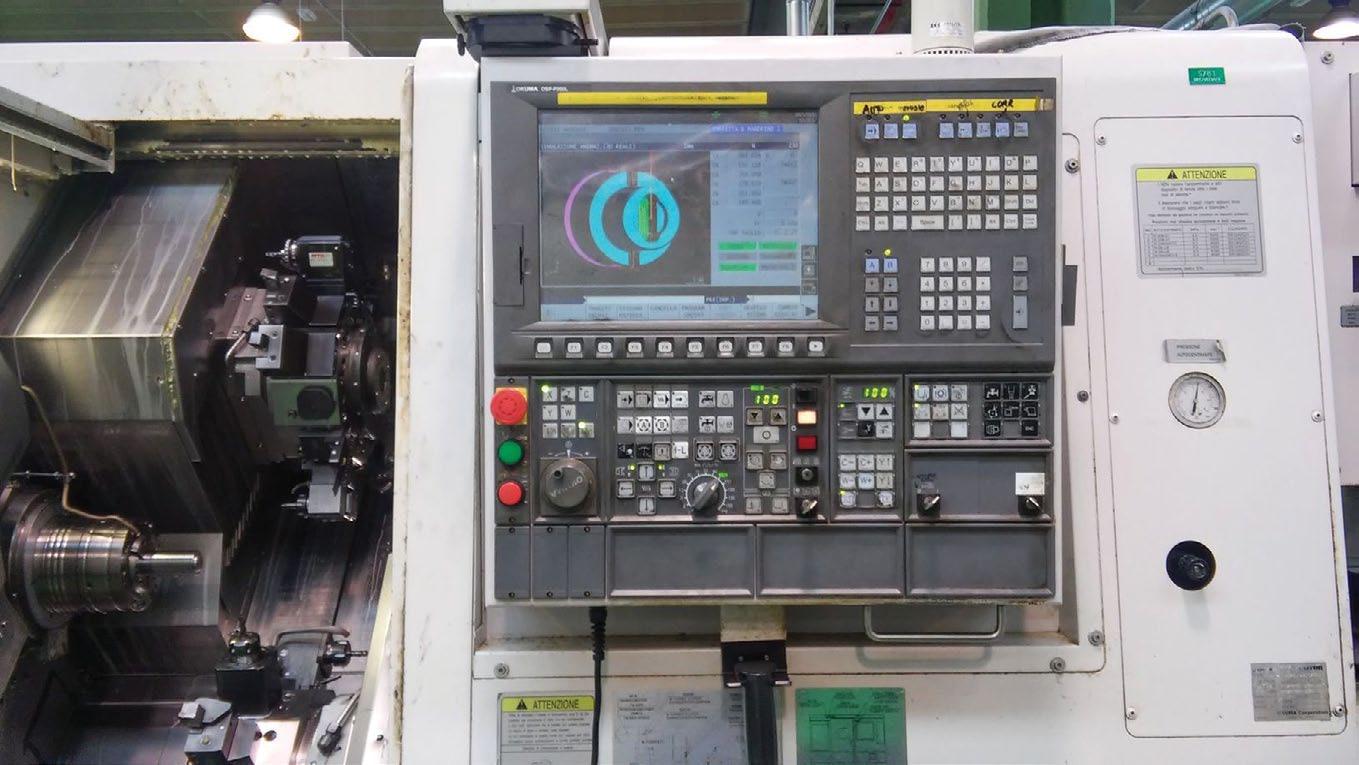
optimising industrial automation
Recently the Brovedani Group announced the merger between the Italian Company, FreTor Srl and the ‘Brovedani Technology Centre’ division. The company sees this as an important move, creating a major player in the sector of industrial automation and digitalisation.
It has also been announced that this synergistic corporate integration with FreTor will be managed by the parent company, the Brovedani Group. However, FreTor’s existing management team will continue to maintain their active role within the new corporate structure. The purpose of the merger is to grow the business operations of FreTor by extending its already considerable know-how in other industrial sectors and geographical markets, whilst drawing on the managerial skills and the international dimension of the Brovedani Group.
This significant merger between these two state-of-the-art companies was handled in association with the Milan-based company Special Affairs Srl, which acted as an exclusive advisor in relation to industrial governance matters and the financial aspects of the merger. n
For further details of the Brovedani Group’s innovative products and services visit: www.bovadanigroup.com
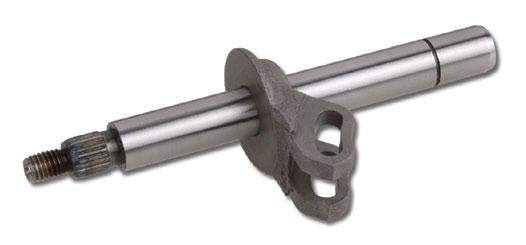
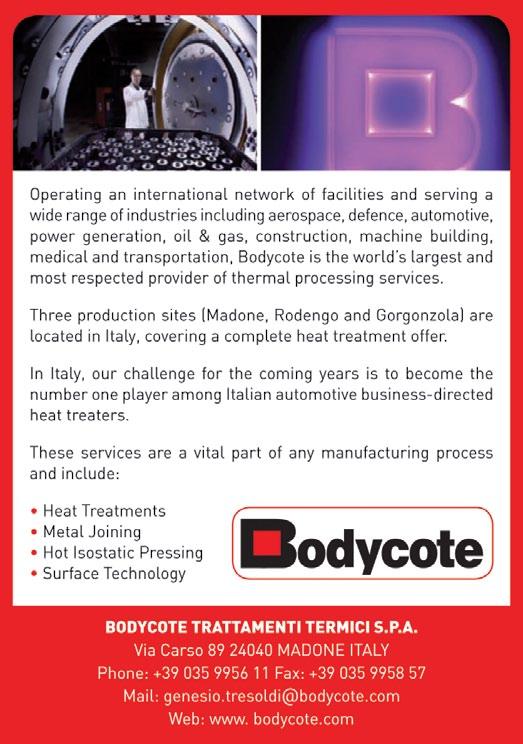