
4 minute read
At full speed EXEDY Corporation
at full speed
The Japanese DYNAX Corporation completed a major investment in Hungary in 2016 to expand its European manufacturing base in response to increasing customer demands. Two years on, the company is doing better than ever before and further capacity extension is under consideration. Romana Moares reports.
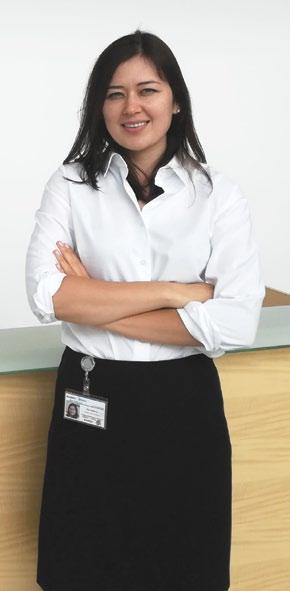
Founded in Japan by Kazuma Adachi more than 60 years ago, EXEDY Corporation, formerly known as DAIKIN Manufacturing, is one of the world’s largest original equipment manual transmission and automatic transmission component manufacturers, supplying the leading passenger, light commercial, truck and motorbike makers. The company has two business segments. The portfolio of its manual transmission related segment includes clutch discs, clutch covers and two-mass flywheels, while the automatic transmission related segment provides torque converters and automatic transmission parts. The company supplies all Japanese, some European and some North American passenger and commercial vehicle manufacturers, and has developed a reputation for unrivalled quality and reliability.
DYNAX Corporation, a fully-owned subsidiary of EXEDY, is the world’s largest wet friction material manufacturer. DYNAX produces and sells friction plates and other parts like reaction plates for passenger cars, trucks and heavy-duty vehicles. Its products support a wide range of worldwide OEM customers, including European customers, in automotive power train, construction and agricultural vehicles. DYNAX is continuously engaged in the advancement of state-of-the-art wet friction technology for material development, process optimisation, and functional testing.

modern manufacturing base
EXEDY DYNAX Europe (EDE) based in Tatabanya in north-west Hungary, is the only European manufacturing base of the two Japanese companies. Executive vice-president Elza Saitova reported: “The Hungarian company was founded in 1993 by EXEDY as a small factory for manual clutch production to supply local OEM makers, employing less than 20 people. Since then, we have increased staff numbers ten times and substantially expanded our product portfolio and production capacity.”
A major milestone came in 2015 when the company’s management announced its plans to expand production of DYNAX’s paper-based friction plates. The investment, worth HUF 7.3 billion, included the purchase of approximately 37,000 m2 of the surround-
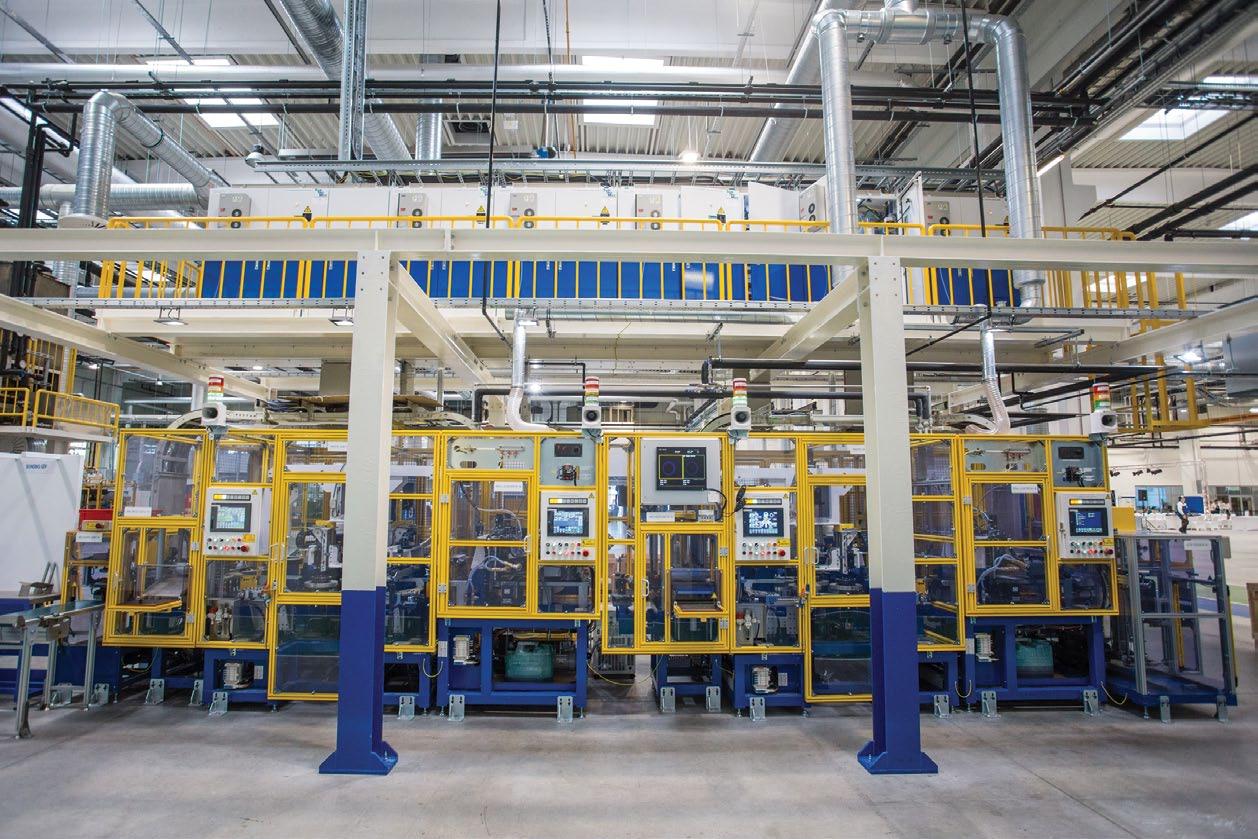
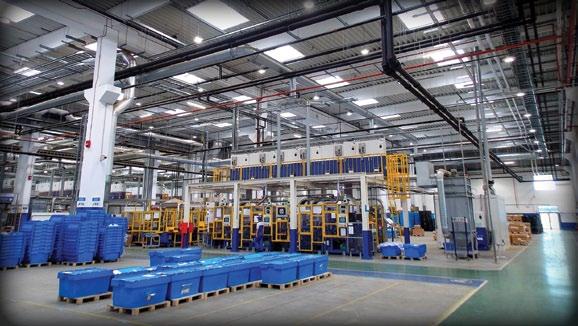
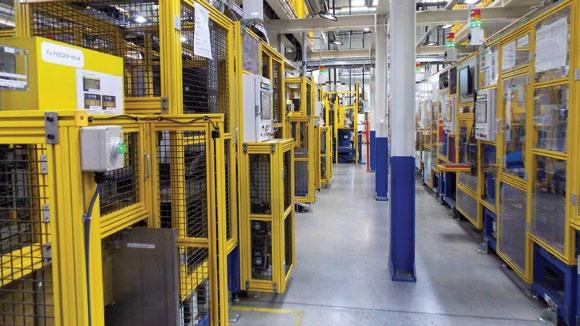

ing land, making the total area of the land 57,000m2, with sufficient space available for further expansion. The total area of the plant was extended to more than 12,000m2. The number of production lines increased to nine, boosting EDE’s friction plate manufacturing capabilities to 41 million units per year. The extended plant was commissioned in 2016, creating 150 new jobs.
Wet friction torque transfer
Products from the Hungarian factory are mainly shipped to European manufacturers. The key product is the friction plate, which has different specifications to suit customers’ needs for torque transfer and fuel economy.
Friction plates are used as torque transfer and braking devices in several applications including automatic transmissions, torque converters, AWD and 4-wheel drive couplings, and wet brakes.
Reaction plates are used in conjunction with friction plates as the reactionary element. In addition to transmitting the reaction torque, they assist with absorbing heat as a result of speed change. DYNAX uses specially made high quality steel to ensure durability, and has several processes in place that control surface finish to maintain friction requirements.
“The R&D facility is located in Japan and product innovation is one of the company’s priorities. The emphasis is always on supplying products that fully meet or exceed the customers’ requirements and needs. At the moment, the automotive market is still growing and is expected to do so for some time, which of course will boost our development,” Ms Saitova reflects.
New potential
She further pointed out that although the company uses international suppliers that are approved for the whole group, localisation is also a big topic. Each year contracts are awarded to local suppliers, as long as they meet the requirements for quality, reliability and cost-effectiveness.
However, as with most European manufacturers, the Hungarian plant does have to face the challenge of a lack of technically skilled people. “Attracting and retaining the right type of human resources is a critical aspect of any successful operation and admittedly an issue that we are dealing with on a daily basis. Particularly in the Tatabanya region with a lot of industrial manufacturers, it is the recruits who can afford to be selective, not the employers,” says Ms Saitova.
Still, in terms of the plant’s development potential, prospects look good. “We are in negotiations with different customers about increasing the volumes, or potentially introducing new products, so another factory extension looks fairly likely. There is enough space here on our current premises and we believe that we will be able support this development,” she concludes. n
