
5 minute read
Finishing first Steinemann Technology
fiNishiNg first
Steinemann Technology is a global leader in the development and manufacture of high quality sanding machines and abrasives. Renowned for its innovative and groundbreaking finishing technologies, the company continues to lead the field in its chosen disciplines. In February this year Steinemann announced the expansion of its US headquarters in Charlotte, North Carolina. Philip Yorke reports.
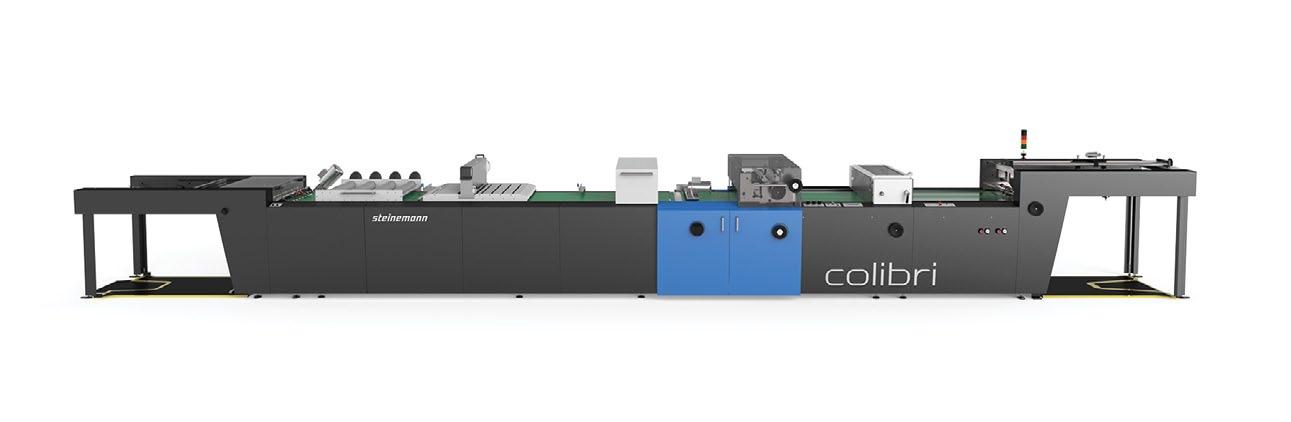
Steinmann Technology finishes first when it comes to the art of producing innovative sanders, high quality abrasives and quality control systems. Founded in Switzerland in 1917, it is a global leader in the manufacture of sanding machinery for the panel industry and UV varnishing systems for the graphics industry. The company offers optimal finishing backed by its unrivalled experience and legendary Swiss Precision engineering.
The Steinemann Group is headquartered in St. Gallen Switzerland and has major overseas operations in Asia, (Malaysia), China (Shanghai), South America (Brazil) and the USA (North Carolina). In addition, Steinemann operates regional offices in a further 42 countries worldwide.
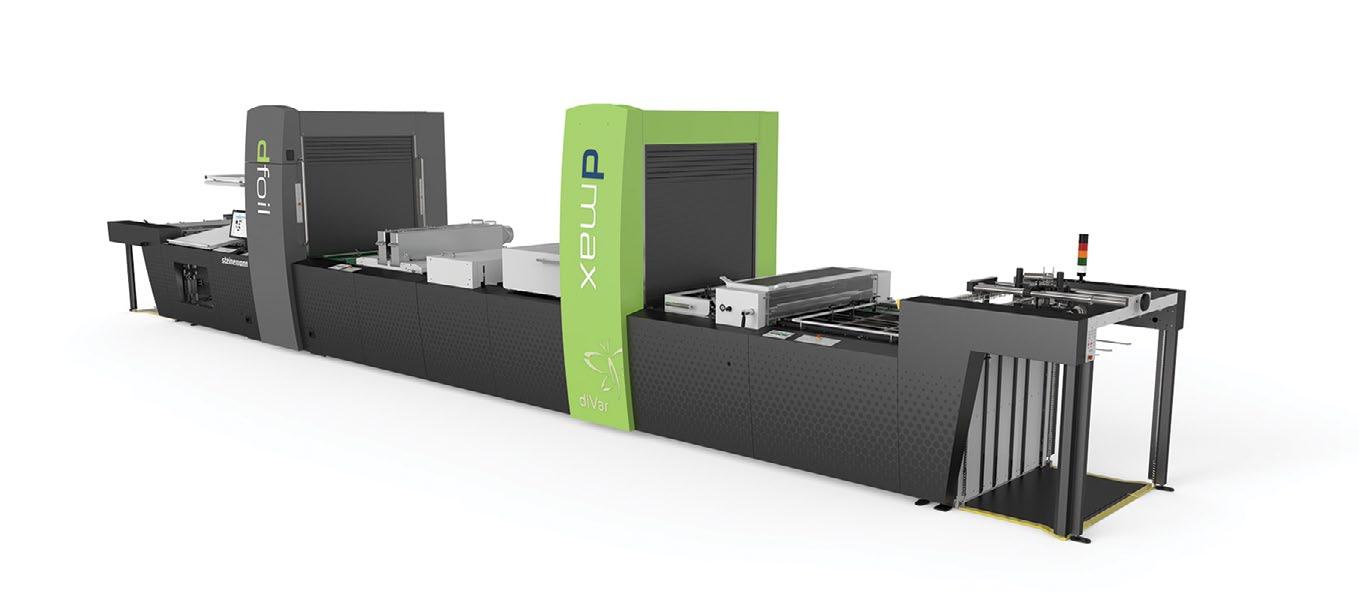
Innovative varnishing systems
Steinemann’s innovative varnishing systems and print enhancement equipment have captured the imagination of the printing and graphics industries. Whether it is for spot, full flood, varnish or foil finishing the company leads the field. This is also true when it comes to the manufacture of labels, brochures, posters, packages or any other printed materials. The company’s varnishing systems guarantee the highest quality, performance and efficiency. Its two different models cover a very broad spectrum of performance and applications.
For example, the company’s dmax systems are advanced digital inkjet solutions for spot and relief varnishing and represent a milestone in the development of digital finishing, thus setting new standards in productivity and versatility. Capable of handling 10,000 sheets per hour, the dmax systems offer the ideal complement to professional printers in all fields including web2print and book printing. Steinemann has over 40 years’ experience as a global leader in high-end finishing systems and has an enviable reputation for its innovation, consistent high quality and low maintenance products. These unique machines are the products of choice for printers worldwide. Even the compact entry-level model, the dmax 76c, is faster and more productive than any other system on the market.
Steinemann’s state-of-the-art coating machine is the Colibri, which offers full-flood varnishing systems with a roller coater for high quality UV varnishing and is the result of decades of continuous development. This advanced system is capable of handling up to 12,000 sheets per hour for a wide range of applications including packaging and commercial printing. Due to their unique sheet cleaning unit, Colibri systems deliver constant, high quality and high gloss results, even with minimum varnish applications.
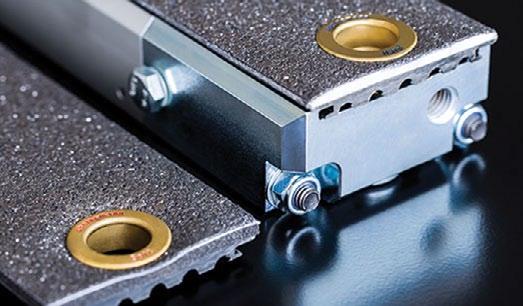
Global growth markets
The global demand for composite panels continues to rise unabated and this is particularly true of the North American market. With several new generation mills due to open later this year, Steinemann has taken the opportunity to expand its US headquarters and warehousing in order to continue offering the most dedicated support for its customers in all aspects of their sanding operations.
“We are unique in the industry, as we are the only sander manufacturer which can supply and support both the sander the abrasive consumables used in the process of manufacturing composite panels.
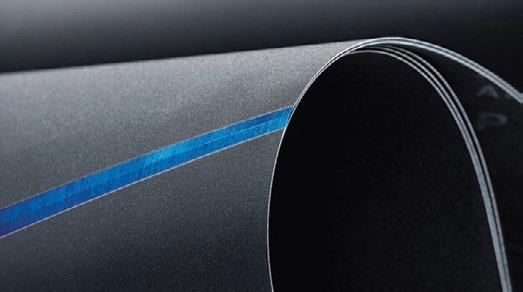
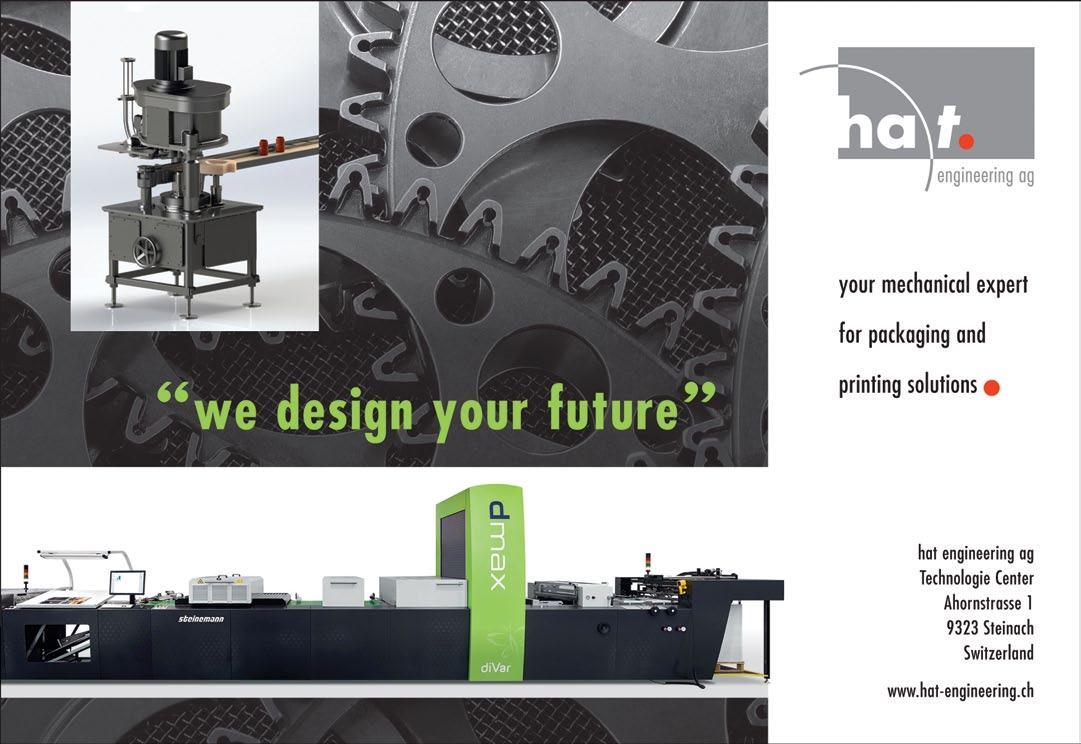
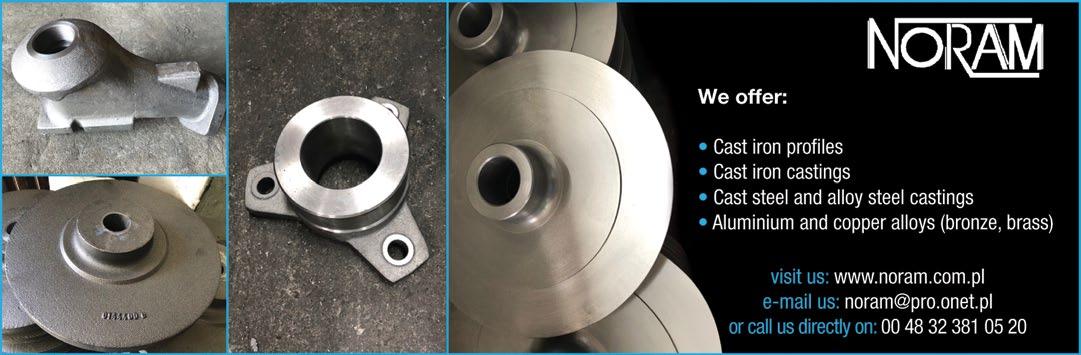
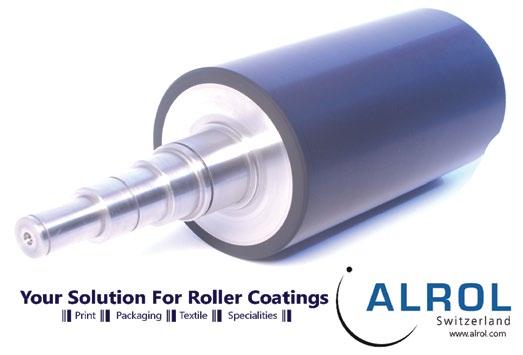
GMO NORAM
Gmo NoRAm Sp. z o.o is a family company, which was founded in 1994 and operates on the Polish and european foundry markets. We offer our clients a full range of services in the field of castings production from ferrous alloys and non-ferrous metals, starting from the development of foundry technology, to modelling and casting. We offer raw (unworked) castings as well as machined castings supplied as ready-made parts for assembly. Castings are made both manually and using machine-forming technologies. We specialise in making single castings, both small and medium series. our cooperation with Steinemann began in 2004 and continues to this day. We mainly supply them with large grey cast iron brake discs and coupling halves made from spheroidal cast iron. All products for Steinemann are delivered fully machined, varnished and ready for assembly. our cooperation with Steinemann is developing dynamically and we are currently their main casting supplier when it comes to the above products.


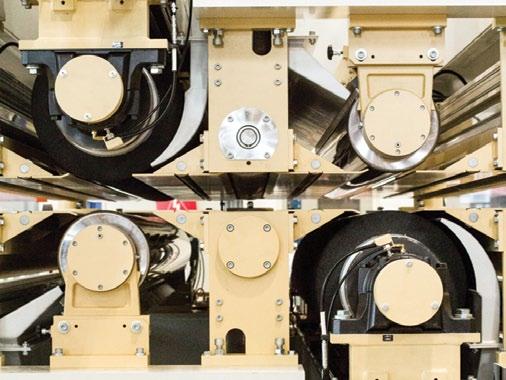
We are very pleased to announce the expansion of our North American headquarters and warehouse facilities. Our abrasive belt business has doubled in the past year, so the expansion of our warehouse will provide us with the opportunity to maintain a larger stock on-hand and to ensure that we continue to meet the needs of our many customers,” said Dan Murphy, President of Steinemann USA.
Partners in performance
Over the years Steinemann has built up strong partnerships with other leading European companies, including SwissMEM, Schmid Rhyner AG, Kurz, and Sturm-sfs, among many others. Recently it announced a new addition to its carefully selected partners with Repserve S.A.S of Columbia, South America, as exclusive partners of Steinemann Technology sanders and abrasive consumables.
“The timing in bringing an agent such as Repserve on is perfect. Our customer base continues to grow in South and Central America and being close to our customers is a key priority for Steinemann. Repserve is well respected in the panel industry and brings many years of customer knowledge and relationships,” commented Murphy.
It was announced that Repserve will cover the countries of Guatemala, Honduras, Costa Rica, Panama, Ecuador, Peru, Venezuela and Columbia.

unmatched surface quality
Steinemann has always strived to achieve the highest possible standards when it comes to surface quality. The company’s contact drums in the calibration process are at the heart of its wide-belt sander. Even minor deviations in the rotational accuracy or balance of the drums can result in a critical impairment of surface quality. Therefore high quality precision engineering and sensitive balancing are essential.
With speeds of up to 1500rpm, working widths of up to 3.3 metres and an output of up to 200kW per unit, the drums have to withstand very demanding parameters. This must be achieved without any vibration and at an accuracy level in the region of hundredths of a millimetre. One of the key quality features of Steinemann drums is their special ultra-hard coating. The harder the coating, the lower the wear – and the longer its service life. n
For further details of Steinemann’s innovative sanders and varnishing systems visit: www.steinemann.com