
5 minute read
long tradition in casting innovation Drawski

loNg traditioN iN castiNg iNNovatioN
Drawski S.A. is a cast iron foundry from Drawski Młyn, Poland. It specialises in casting grey, ductile and white cast iron. The company prides itself on its continuous activity going back to the middle of the 19th century.
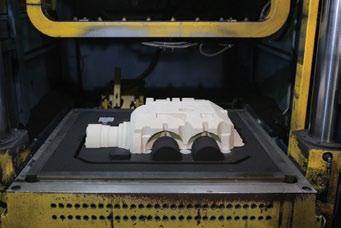


Founded by Ferdinand Sattler in the 1854 in Drawski Młyn, in the north-west part of the Wielkopolska Province, the foundry was developed from the local primitive steel mill and blacksmith workshop. In 1923, the foundry was acquired by Ludwik Kemblinski, a specialist in the casting industry, who invested in the production of iron castings made from malleable black cast iron, at that time a little-known process in Europe. Thus, he became the first and only manufacturer of this type of casting in Poland.
After the Second World War the company was nationalised and in 1951 the production of castings made from malleable cast iron was resumed. In 1967 the company’s biggest investment – the construction of JATŻEL-3000 induction furnaces – was completed. This allowed the foundry to establish the production of ductile cast iron class ZcC 3510 and pearlite ductile cast iron, not made in Poland up to that point. The 1970s was the decade when the company broke its record for castings production that exceeded 9000 tonnes.
In 1996, the foundry was transformed into the sole-shareholder company of the State Treasury. In the second half of the 1990s it invested in a modern foundry moulding machine from HWS, a leading German manufacturer of moulding machines. In the years 2004–2016 the machines and equipment for the production of high-grade spheroidal cast iron were purchased. The automatic moulding line Disamatic, supplied by the Danish company Disa, was another major investment for Drawski, and the DISA MATCH line concluded the modernisation of the moulding plant. The horizontal DISA MATCH line was a successful and very valuable investment.
According to Ryszard Kielczyk, Drawski’s chairman of the board, “Drawski was the third foundry in the world and the first in Europe to use the latest fully automated moulding machine and mould handling line. This was followed by a new shot-blasting machine and automatic painting line. In total, we have invested PLN 26 million (€6.2 million) in new technologies.”
21st century foundry
In 2003, Drawski became a joint stock company with a majority participation (96.5 per cent of total shares) of DrawInvest, one of whose shareholders is Mr Kielczyk. Since that time the company has grown rapidly, in large part due to the continuous investments in new machines and technologies. It also cooperates with the industry’s leading suppliers, which contributes to the ongoing strengthening of the company and translates into successes for all partners taking part in the cooperation.
“Our modern technologies and quality management systems enable us to produce a reliable product and the Environment Management System supports our efforts to run the environmental programmes,” says Mr Kielczyk. “We are currently implementing an innovative project to develop an inoculation method for spheroidal castings on a vertical line. The project includes the construction of the new production hall and purchase of new electric furnaces. The cost of this investment is PLN 11 million (€2.6 million).”
Drawski holds the Integrated Quality and Environment Management System PN-EN ISO 9001:2008, and PN-EN ISO 14001:2004 approved by TÜV Management Service GmbH Münich. Furthermore, the company has been awarded by the Polish Foundrymen Association and the Polish Chamber of Commerce for its achievements in production, economy and ecology.
“In terms of the production volume, we are a medium-sized foundry with annual production estimated at 10,000 tonnes of castings, including 2500 tonnes sold abroad. The castings are predominantly used
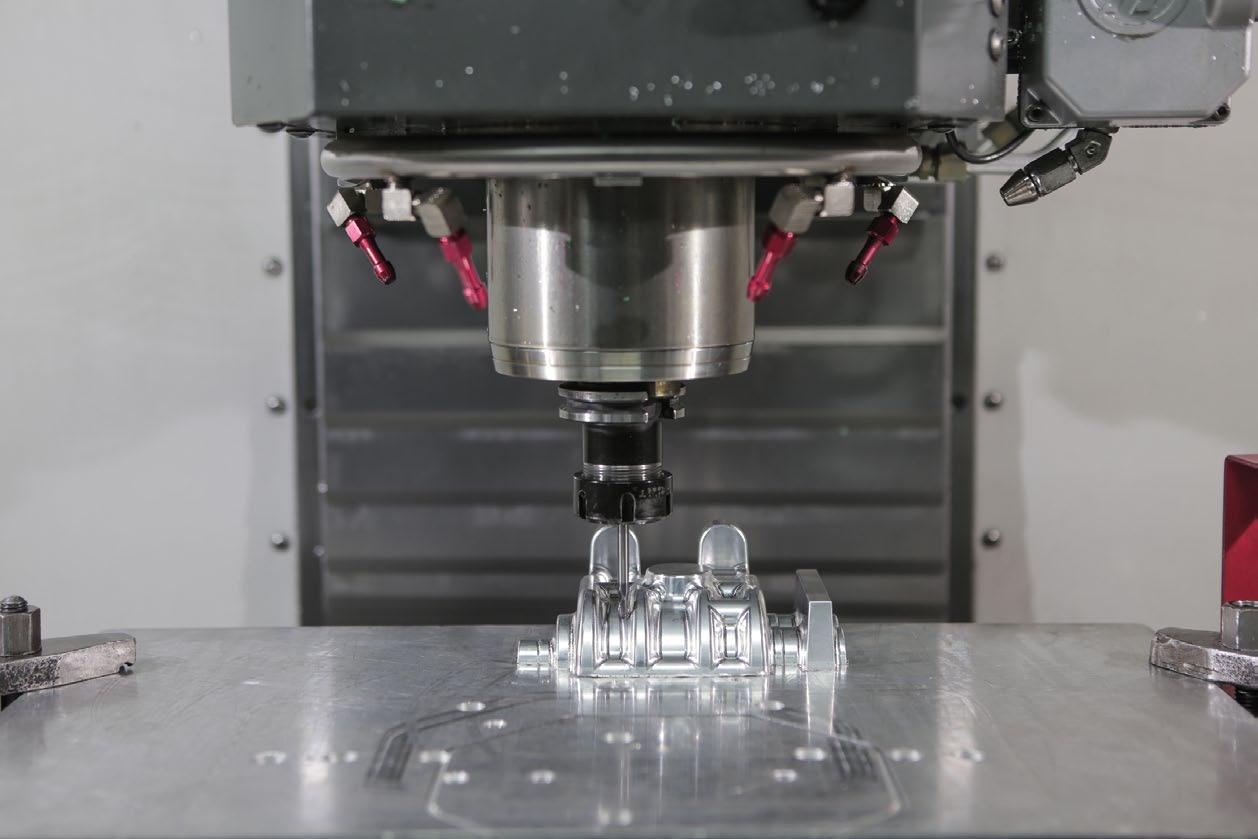
in the machinery and agriculture industries, also some are used in the water-supply-and-sewage, railway and mining sectors. The foundry can cast both small and big batches,” adds Mr Kielczyk. “Our annual net profit is PLN 1.5 million. About 28–30 per cent of our castings are sold abroad, mainly to Finland, Denmark, Sweden, Norway, Great Britain, Ireland, Germany, Belgium, Netherlands, France and Spain.”
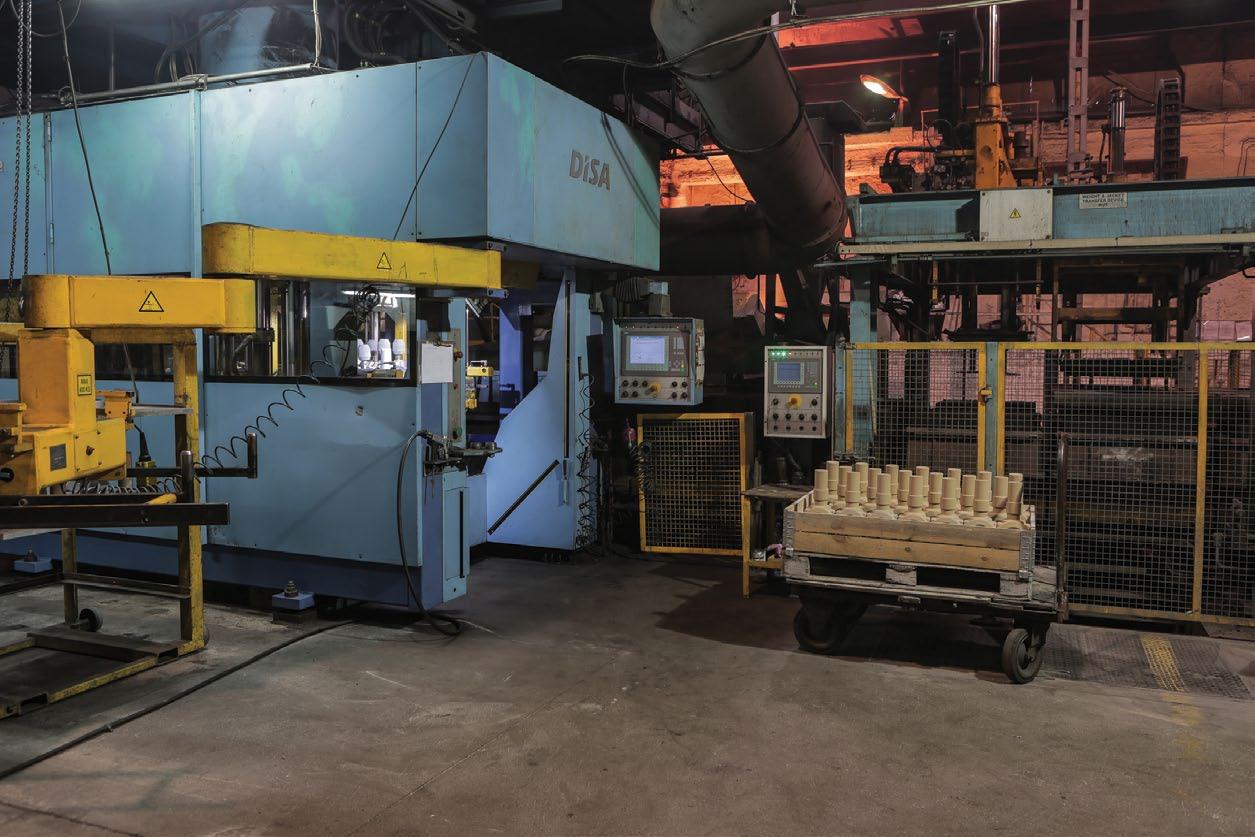
Following the trends
Drawski has always followed the latest trends in the world of castings. The company participates in all industry-relevant meetings and congresses where it can learn new technologies, exchange knowledge and opinions and meet new customers or partners. On 8 December 2017 it took part in an International Conference, ‘3D Printing for casting engineering’, during the Polish Foundry Day.
“3D printing is increasingly used in the foundry industry. This technology not only speeds up the formation of foundry moulds, but also provides the opportunity to create more complex shapes. It accelerates the entire production process, because prototyping using 3D printing is much faster,” explains Mr Kielczyk.
On 23–27 September 2018, Drawski will be present at the most important and spectacular event within the international foundry industry, the 73rd World Foundry Congress (WFC), held in Krakow, Poland, with the motto: ‘Creative Foundry’. The themes of the conference will include: materials, technologies, digitalisation, management and ecology. The WFC sessions will take place in a modern convention centre with a view of the Royal Castle in Krakow. The congress will be accompanied by a special exhibition dedicated to creative and innovative solutions in: foundry engineering technologies, castings, materials, casting production, instrumentation, machines and foundry devices, as well as management solutions. The 22nd International Fair of Technologies for Foundry METAL will be another accompanying event, presenting the most important companies from the foundry sector, including suppliers of raw materials, machines and components from more than 20 countries.
“It is a great honour for the Polish foundry industry to be the organiser of this event. It’s been a quarter of a century since we last had the privilege of hosting members of the World Foundry Organisation in Poland. It is no surprise then, that we are extremely excited to once again have the pleasure of greeting in Krakow about a thousand professionals from around the world,” says Mr Kielczyk who is himself, as the vice-president of the STOP Board, one of the organisers of the congress. n
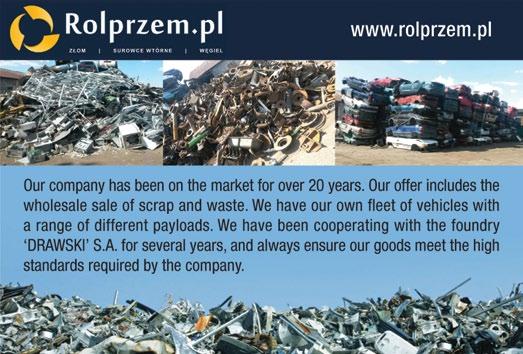
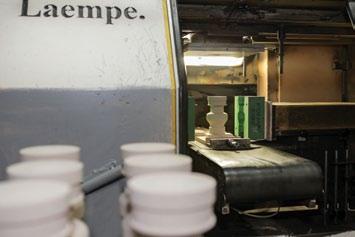
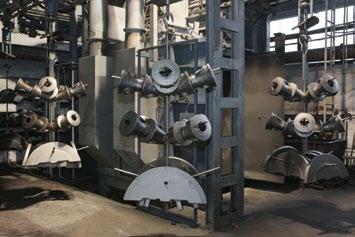
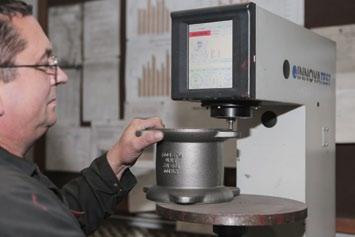