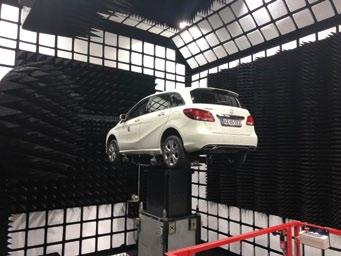
4 minute read
Technology spotlight Advances in technology
NeWS
TECHNOLOGYsPoTLIGhT
Advances in technology across industry
unique Lab in denmark to be Global Research mecca
The Aalborg University (AAU) laboratory is the first of its kind in the world and will be used by AAU’s Department of Electronic Systems, a decades-long world leader in antenna research.
The new antenna laboratory is the first anechoic chamber that can slide open the roof and a wall. These features combine the potential of an enclosed anechoic antenna lab and an outdoor measurement station, explains Gert Frølund, Professor and head of the antenna section in AAU’s Department of Electronic Systems.
“With the wall and roof of the new lab open, researchers can measure huge objects and signals over vast distances without the ground reflection and other influences that usually plague outdoor measurements. In practice, the lab simulates an infinitely large space that is shielded and radio anechoic, something that hasn’t been seen before,” says Gert Frølund.
“We have no idea what the new lab will be used for in the future, and that is exactly the point. We are taking into account that the future will bring rapid development that is impossible to predict, and have built the laboratory in as flexible and ambitious a way as possible so that it’s future-proof,” says Gert Frølund.
The lab contains an elevator and a measurement platform that can lift and rotate large objects like cars and satellites of up to 3500kg inside the laboratory. And by removing the roof, even larger objects such as wind turbine blades or fighter planes can be partially or completely lowered down into the laboratory. Visit: www.aau.dk
Plans for a 385-metre fish farm facility in the open sea
AN entirely new fish farm design, which looks more like an elongated offshore oil platform than a traditional aquaculture facility, may soon be installed in Norwegian waters.
A model of the ‘Ocean Farm’ concept is now being tested at SINTEF Ocean’s Ocean Basin Laboratory, which in recent decades has been the test site for many floating oil installations. The aquaculture sector is now looking to install facilities further out at sea in order to have access to more space and cleaner water, and reduce the risks of salmon lice and disease infection.
“Our aim is to advance the aquaculture sector in a sustainable manner,” says Bjarne Johansen, who is a project manager at the aquaculture company Nordlaks, which is behind the project. “We believe that the key to achieving this is to exploit new and more exposed areas of the ocean,” he says.
The main construction is made of steel and will contain six large nets, designed to house 10,000 tonnes of farmed salmon, amounting to up to 2 million individual fish. Out at sea, the facility will be as much as 385 metres long. The project was launched in response to the Directorate of Fisheries’ development licences scheme, which is a temporary arrangement involving the issue of special licences aimed at promoting innovative projects that require significant levels of investment. The Directorate had received 104 licence applications on deadline day in November 2017.
“Norway is a global leader in the development of large-scale salmon production facilities in exposed localities,” says Ivar Nygaard, who is a Senior Project Manager at SINTEF Ocean. “The Nordlaks project is the biggest aquaculture venture we have undertaken to date,” he says. Visit: www.sintef.com
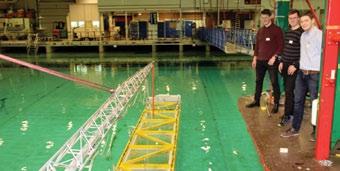
vtt developing a solution to marine plastic waste problem
VTT Technical Research Centre of Finland is helping to solve the global plastic waste problem. VTT is developing in a project called PlastBug a mobile container unit to remove plastic waste from ocean areas, in order to create a safe living environment.
“Our idea is to design a mobile container where microbes degrade plastic waste to valuable products like fuels or chemicals,” says Kari Koivuranta, Principal Scientist at VTT.
The aim is to develop a small, container-based factory that can be placed in an area where centralised plastic waste collecting or recycling is not possible or feasible. The container can be located on a beach or ship. The factory unit would get most its energy needed for the process from solar energy and wind power.
This year researchers in the PlastBug project have been searching microbes that are capable of degrading different kind of plastics (PE, PP, PS or PET) and have developed methods for the pretreatment of plastics. Researchers are currently using a three-stage screening method to screen microbes from different sources.
“Some microbes have already passed through the first two stages of the screening. In the third stage, we will confirm they are capable to consume and digest plastic. In the next step, if plastic degrading microbes are found, we will improve the ability of the most effective microbes to digest plastic, and we will develop plastic pretreatment methods further to ease the work of the microbes,” says Koivuranta. Visit: www.vtt.fi
