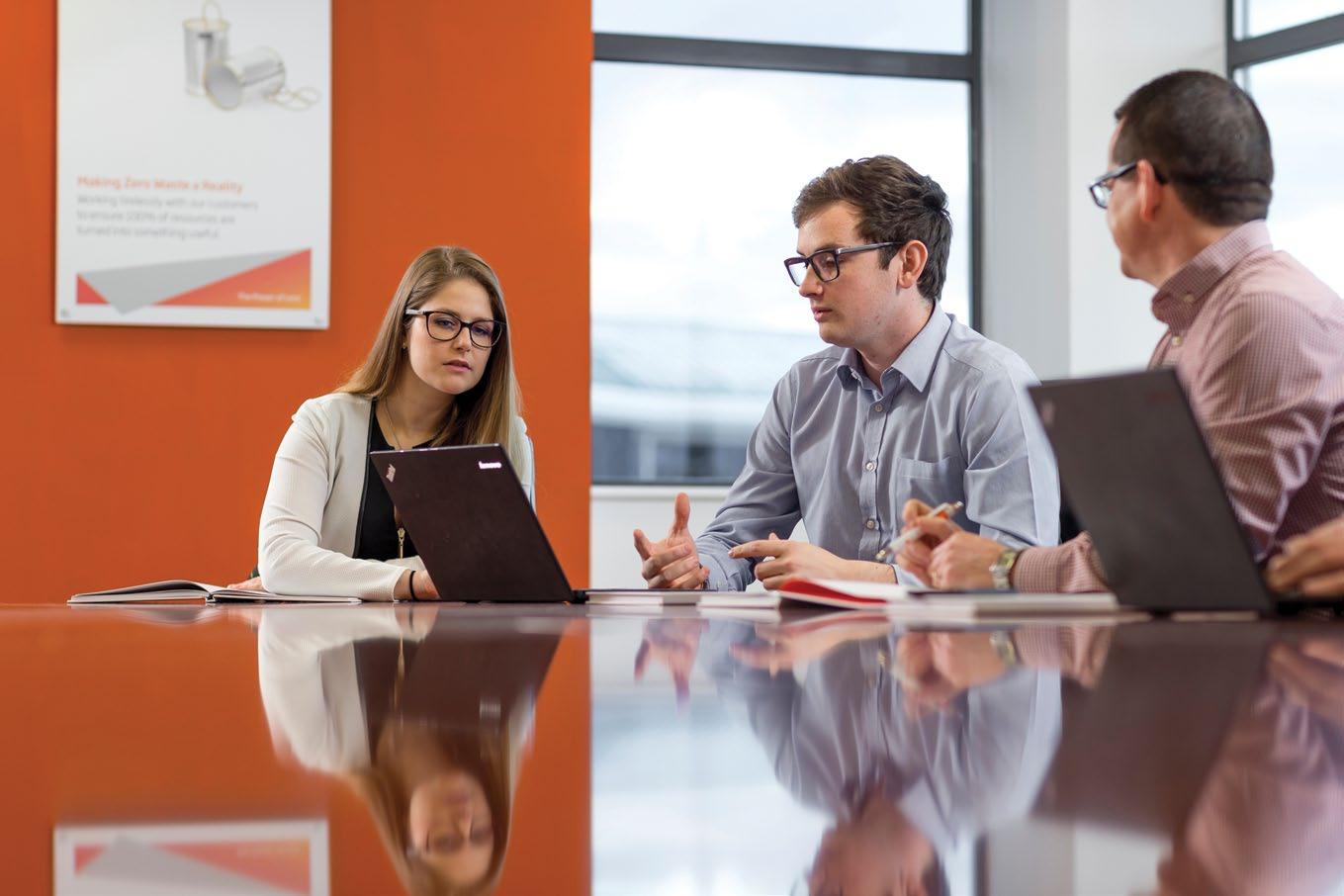
5 minute read
Stacking-up winning solutions DS Smith
sTaCKInG-uP WInnInG soLuTIons
DS Smith is a leading global provider of corrugated board packaging and specialised plastic packaging solutions. For many years the company has led the field in efficient product recycling and sustainable solutions. Recent ground-breaking innovative systems and products developed by DS Smith have combined to increase the gap yet further between the company and its competitors, as Philip Yorke reports.
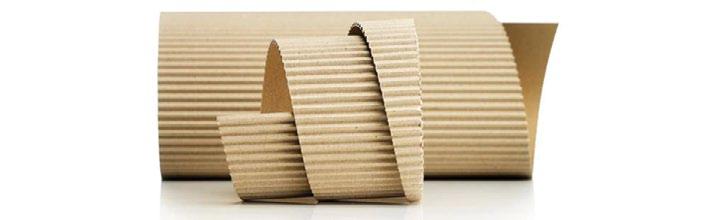
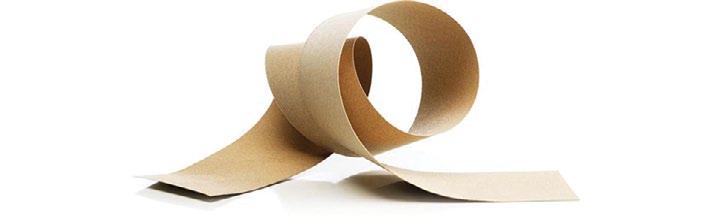
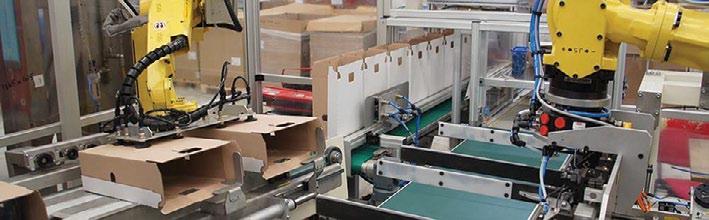
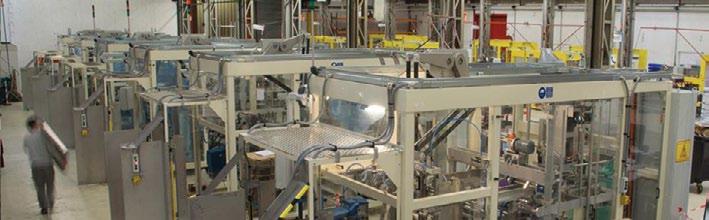

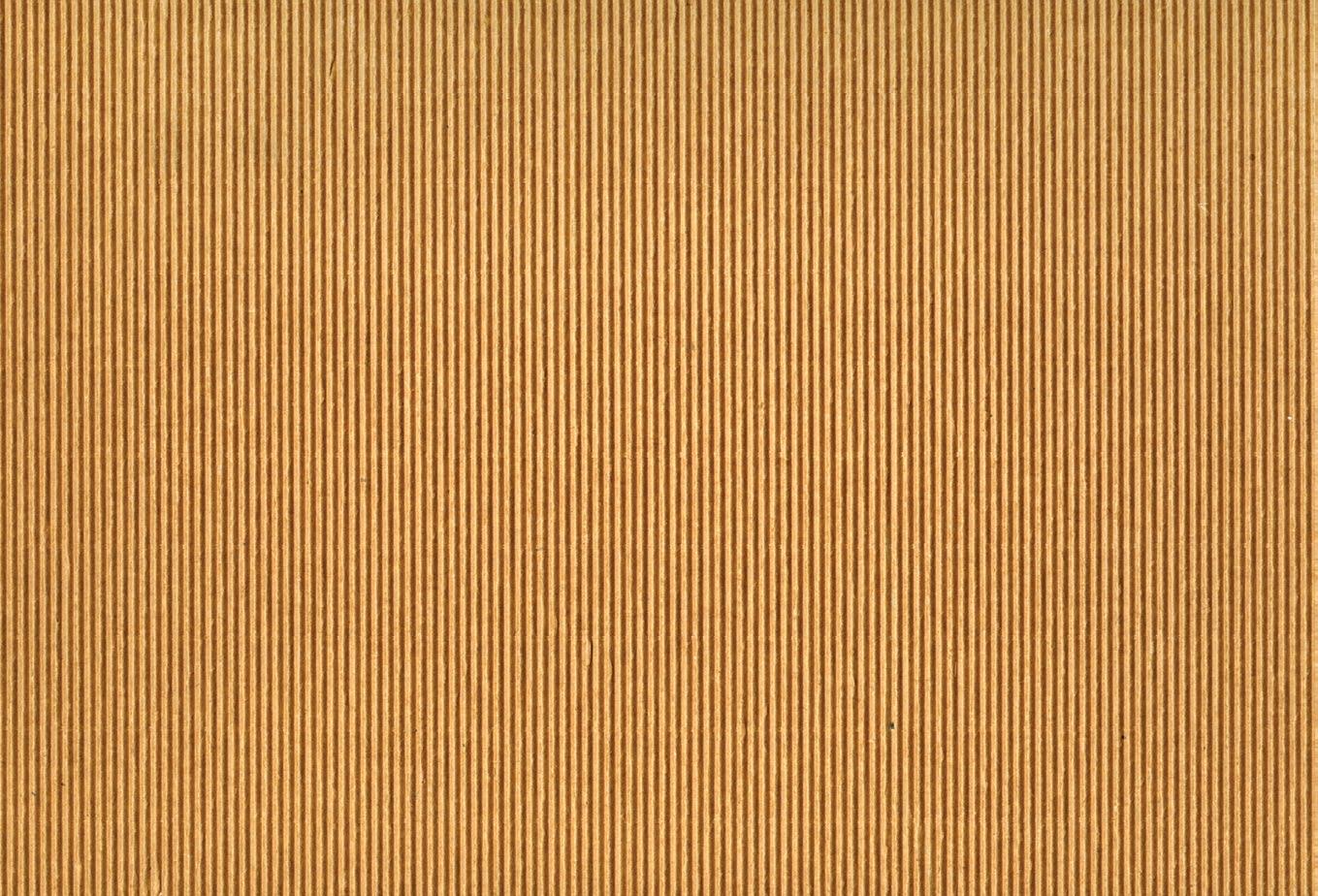
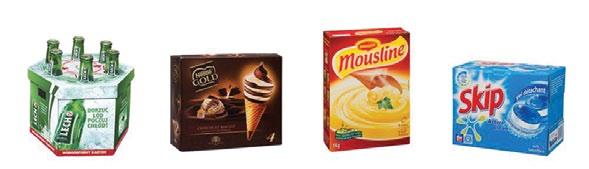
Founded in London in 1940 by the entrepreneurial Smith brothers, the DS Smith Group has grown to become one of the world’s most innovative and progressive packaging companies. Today its statistics are impressive by any standard. Currently the company employs more than 30,000 people worldwide, and its state-of-theart facilities are strategically located in almost 40 countries across all five continents. In the fiscal year 2017/18 DS Smith recorded revenues of more than six billion euros.
The company’s strategy for growth is based upon its dedicated understanding of its customers’ needs for far-reaching futuristic solutions. These systems must be designed to meet customers’ changing, and challenging future packaging needs. From the outset, DS Smith has been committed to delivering innovative products and processes that not only reduce waste, but also reduce production costs and eliminate complexity in their various supply chains.
By utilising its in-depth expertise, which ranges from design to production, and from supply to recycling, the company is able to offer the highest possible quality, as well as environmentally-friendly, innovative solutions and services. These solutions look at the big picture of its clients’ packaging needs and not just one element in isolation.
Boxing clever
DS Smith has always invested much of its bottom line in new product development and to improve recycling and sustainability. A recent result of this on-going investment programme is a breakthrough solution created for the soap and hand-cream dispenser sector. The company’s latest ‘Bag-in-Box’ solution provides the answer to many of the problems encountered in the refilling of dispensers from bulk containers, such as spillage and other packaging processing anomalies.
Today Bag-in-Box by DS Smith offers the ideal solution for soap and hand cream dispensers. This unique system comes in a contaminationfree sealed pouch with integrated dispensing options that make refilling easy, and products easy to store, as well as being and quick and simple to handle. With cleanliness being a top priority in any hospitality and healthcare facility, Bag-in-Box, is clearly the product of choice and one of the most popular solutions for wall-mounted hand soaps, sanitisers, moisturisers and other personal hygiene liquid preparations.
High-traffic rest rooms, schools and kitchens typically use between 800 to 1200ml ‘Bag-in-Box cartridges. These can be designed to suit virtually all wall-mounted dispensers in the global market place. For the hospitality industry, smaller sizes are more popular for products such as shampoos, body gels, hand creams and other personal care products. For high-volume industrial requirements the ideal solution is a three- or five-litre Bag-in-Box system for hand soaps and sanitisers
The many advantages of the new Bag-in-Box dispensing system include simple and quick refills without the risk of spillage, along with precise portion control and dosing. In addition, the new system offers full utilisation of the inner-dispenser space and involves significantly less plastic than competitive products. The special fully collapsible bag ensures less product waste and a sanitary-sealed bag benefits from a unique built-in nozzle device.
Dispensing perfection
One of the world’s most successful suppliers of caps and closures for the international food and beverage industry, Affaba & Ferrari, (A&F) decided it needed to replace its traditional type of packaging with more sustainable, durable and re-usable collapsible containers that would be perfect for base dispensing. The challenge revolved around that fact that sport caps are produced from two pieces. Once the first part is produced the caps need to be hygienically stored until the production of the second element is complete. To avoid the potential risk of the ingress of wood shavings from the storage pallets, A&F looked for a solution that would solve the problem without the need for employing wooden pallets.
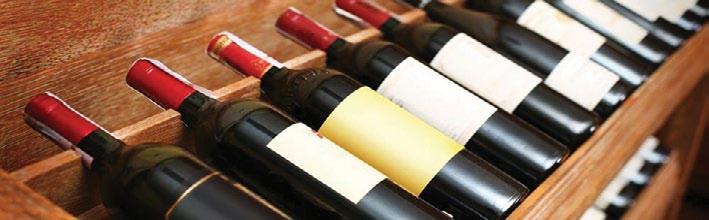
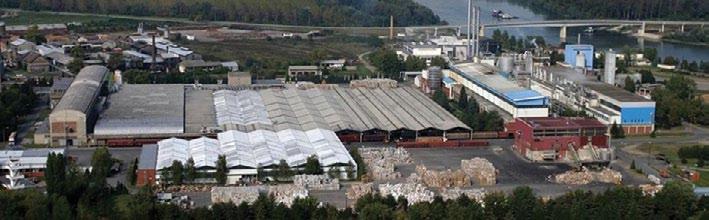

DS Smith Plastics’ ‘Stackabox’ system was designed especially for the handling of PET preforms, caps and closures. The re-usable and easily stored container makes it the perfect dispensing solution that can be utilised throughout the entire production process. What’s more, the base dispensing process significantly reduces the risk of any damage to the caps.
Following stringent testing at A&F’s manufacturing plants, it was confirmed that the highly efficient, flexible-fold ratios minimised warehouse storage costs. Furthermore, the product’s durable construction, with its smooth internal surfaces, ensures ease of cleaning, thus providing optimal hygiene for the safe storage of caps. Thanks to their long life span, A&F was able to drastically reduce its levels of packaging waste. In addition, DS Smith’s Stackaboxes are 100 per cent recyclable.
A taste of paradise
Rapak, part of DS Smith’s Plastics division, participated in the 48th APCC Cocotech conference and exhibition in Bangkok late in August 2018. Rapak exhibited its latest solutions for the production, processing and packaging of coconut-based products. Today Rapak is a key global player in Bag-in-Box packaging for coconut creams, offering a complete portfolio of Bag-in-Box filling equipment, flexible bags and fitments.
At this important international packaging event, Rapak showcased its renowned ‘Intasept Liquid Filling’ technology for Bag-in-Box packaging. This is comprised of a unique, double-membrane gland that offers superior security for heat-sealed enclosures, both before and after filling. The specially designed high-speed and economical filling machine, allows sterile products to transfer without the use of a chemical agent in the process.
Thanks to Rapak’s unique Intasept system and its airtight flexible bag, the Bag-in-Box is able to maintain the coconut cream in a fresh condition up to one year after production. n
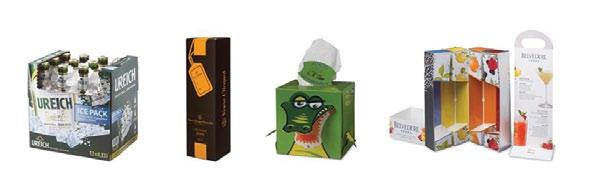
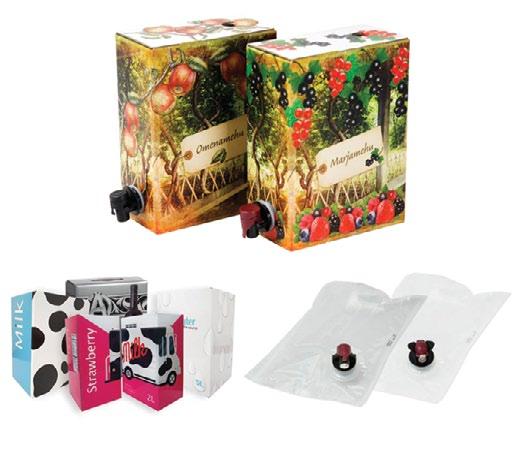
For further details of DS Smith’s innovative packaging solutions and services visit: www.dssmith.com

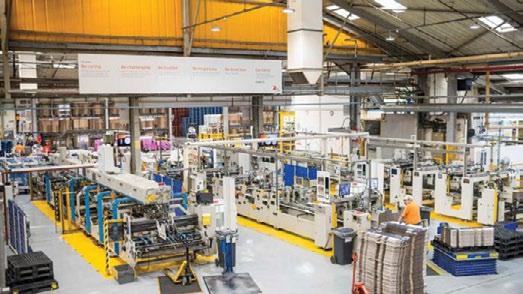
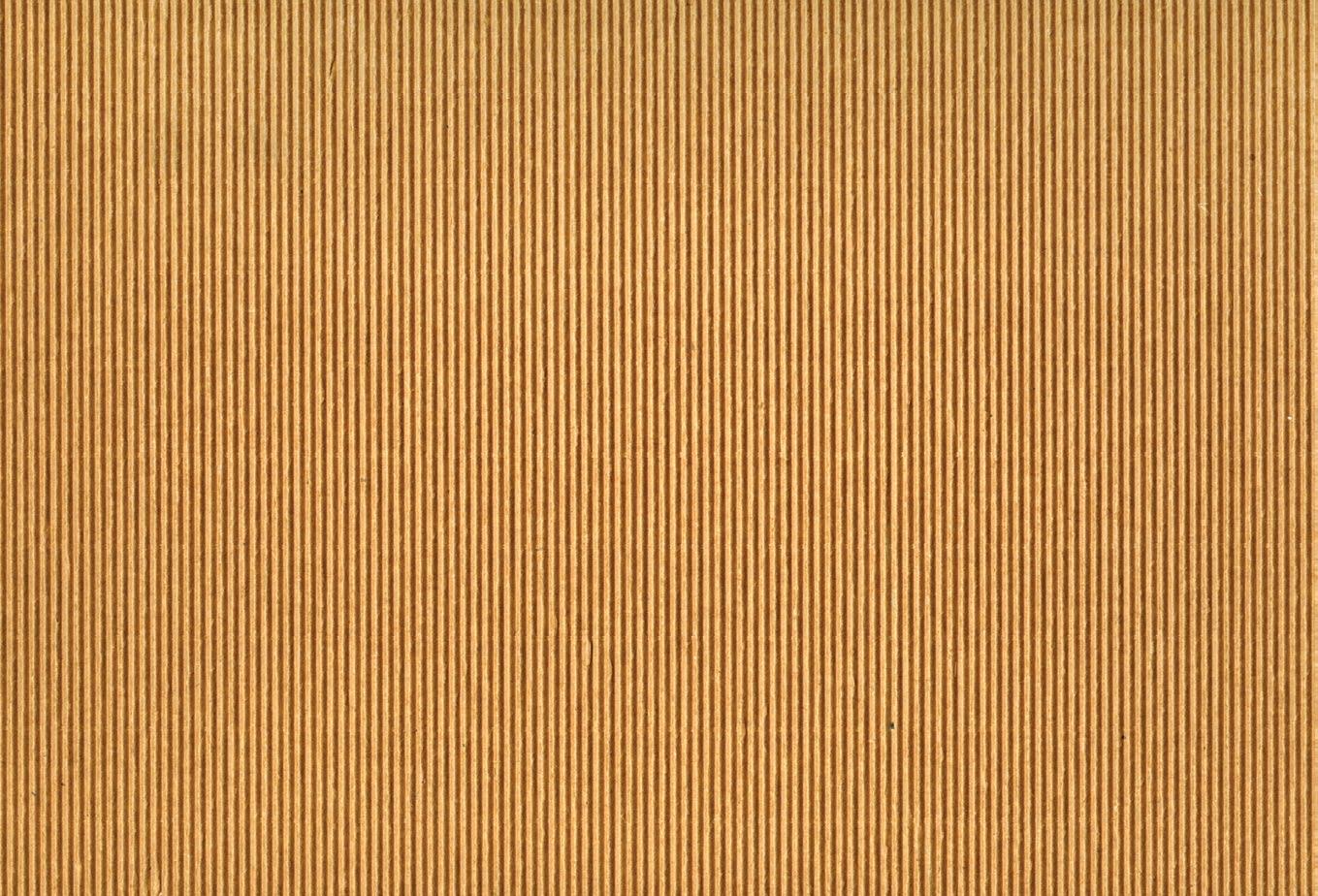