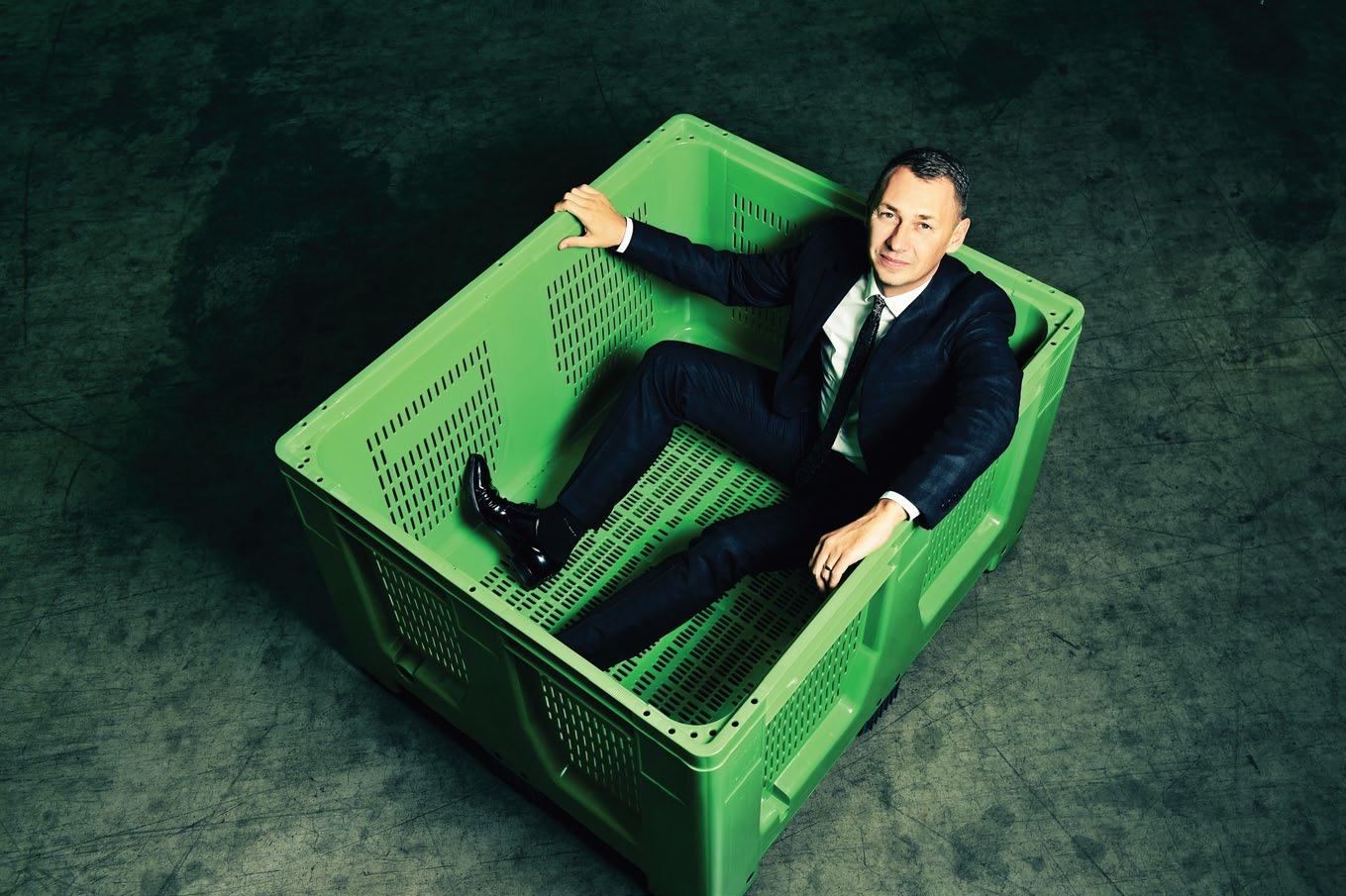
5 minute read
Green plastic packaging Schoeller Allibert
GREEn PLasTIC PaCKaGInG
Schoeller Allibert is one of the world’s largest manufacturers of returnable plastic packaging for material handling and a European market leader in its sector. In a world in which reducing the plastics impact is becoming an everyday imperative, Schoeller Allibert’s role will increase even further. Ludo Gielen, Chief Strategic Officer, spoke to Romana Moares about the new products the company is launching across its various markets and its ‘greener’ vision of future packaging industry.

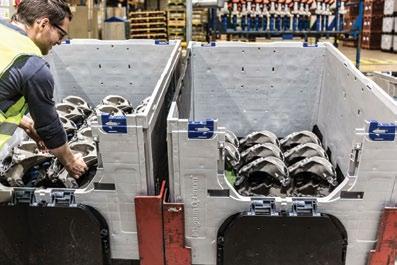
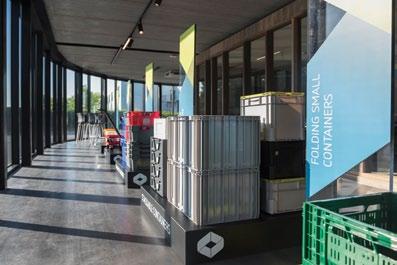
Schoeller Allibert has been inventing, developing, designing and manufacturing Returnable Transit Packaging (RTP) for more than 60 years. The company offers a comprehensive range of standard and tailor-made RTP packaging solutions across ten key product segments – foldable large containers, foldable small containers, rigid pallet containers, beverage crates and trays, stackable and stack /nest handheld boxes, UN pails, foldable IBCs, pallets and dollies. Continued focus on high quality, durability and sustainability helps the company’s customers to enhance supply chain efficiency and profitability, lower transport cost, reduce waste and enhance green branding.
The company controls about 10 per cent of the total returnable packaging market, and with 25 per cent of the European market share it is the number one in Europe. On the global level, Schoeller Allibert is one of the top three players.
“Schoeller Allibert offers its clients packaging knowledge and services including cradle to cradle recycling. We offer full support and
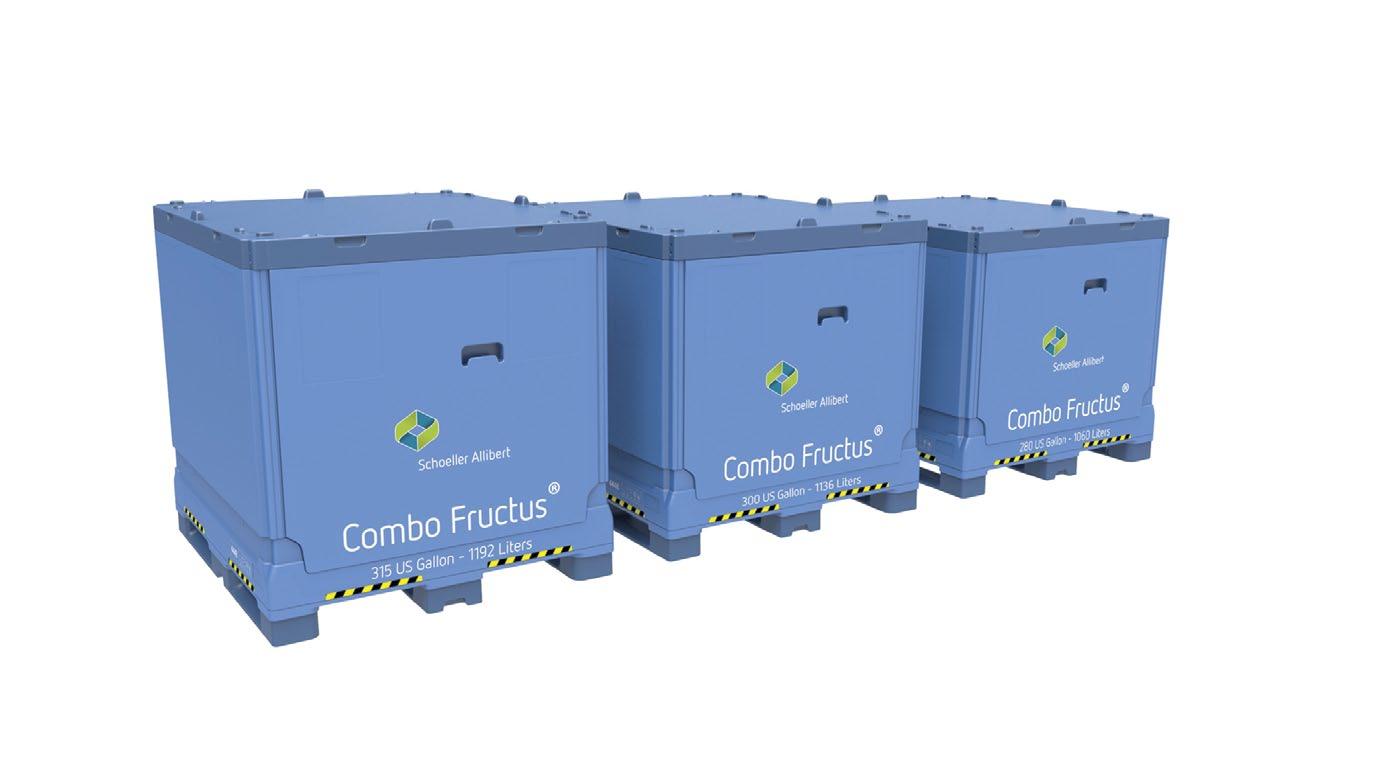
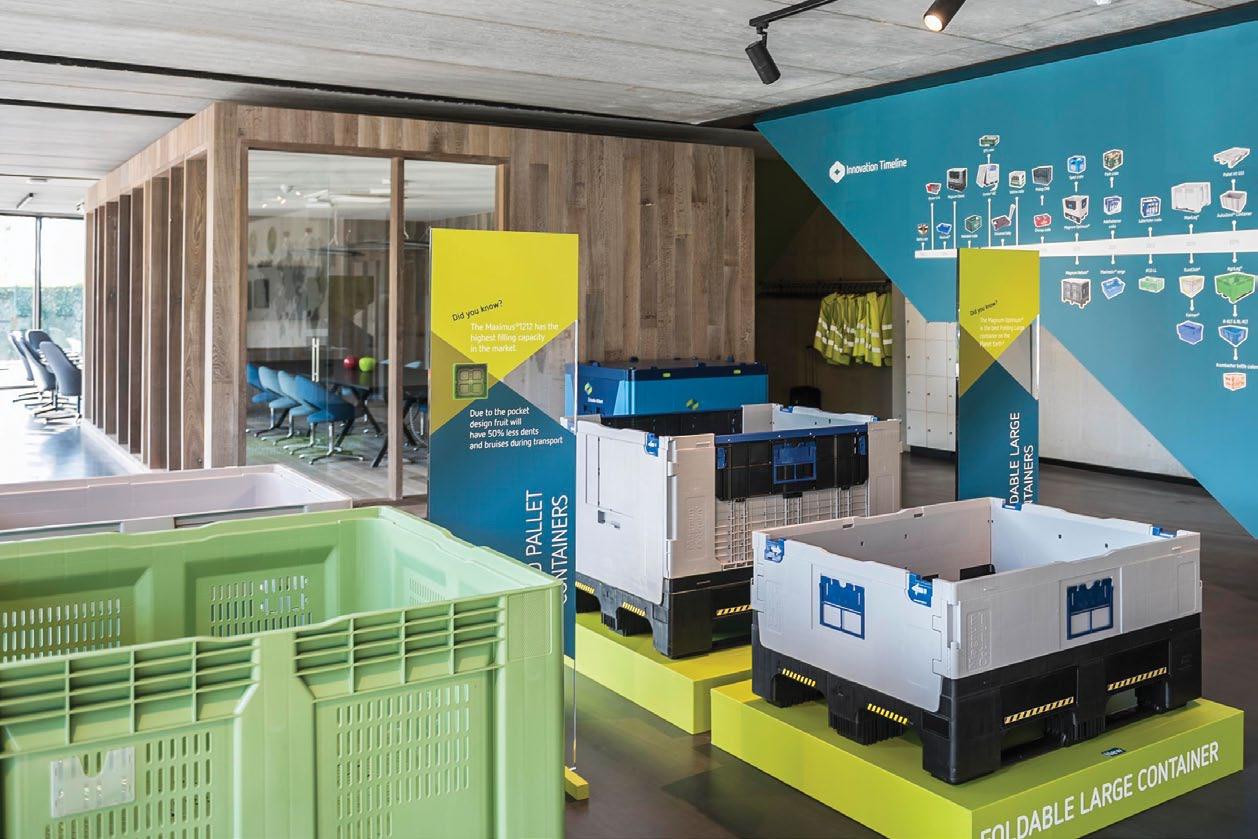
can take care of collecting, recycling and re-using returnable packaging materials that are ready for replacement,” says Ludo Gielen. “The products that are recycled at our facilities can even be safely used as food packaging. For this purpose, the EFSA (European Food Safety Authority) provided scientific advice and approval to our recycling process installed on three of our sites in the Netherlands, Germany and Spain.” Innovation programme
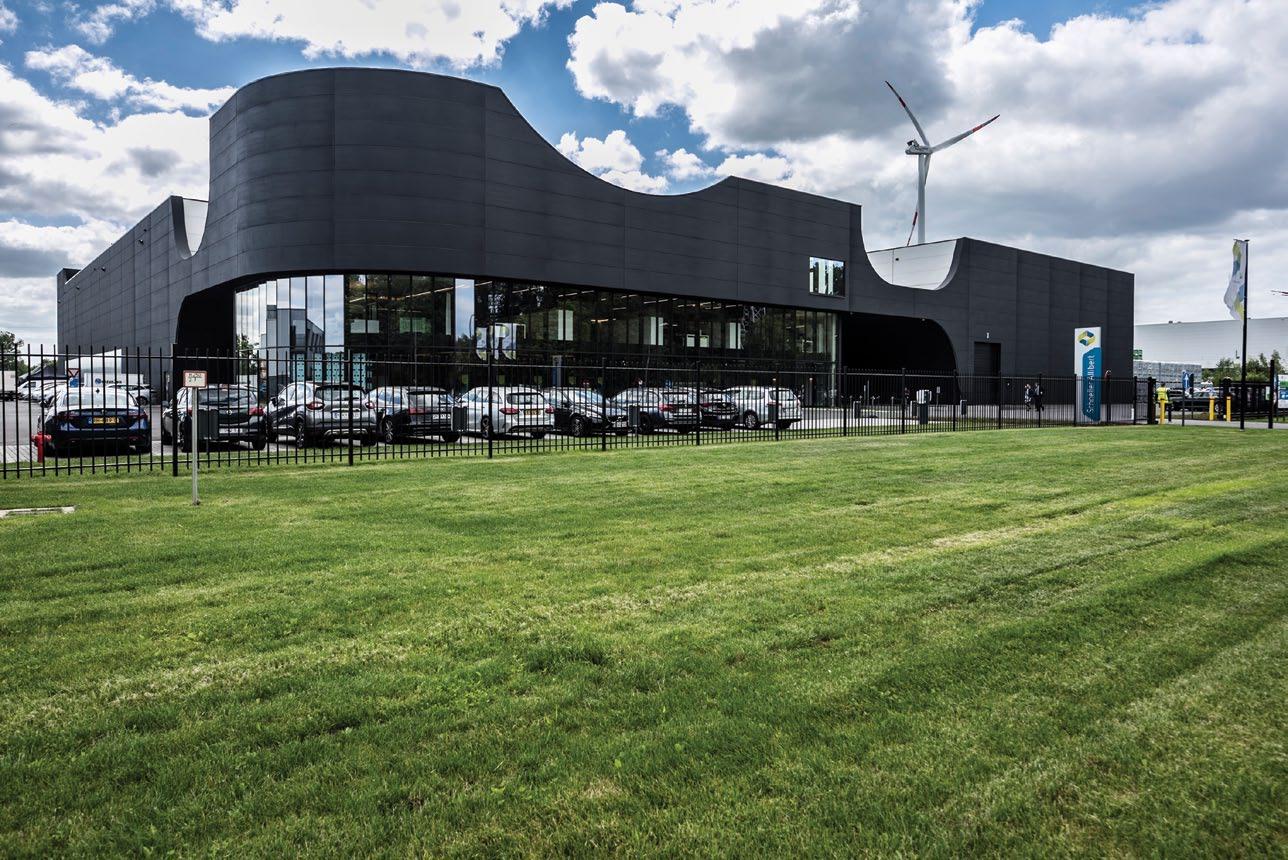

Following the integration of Linpac Allibert and Schoeller Arca Systems in 2013, each a leading player in their fields (reusable packaging and plastic pallet providers), joint efforts have been directed towards an innovation programme.
Many of the major innovations in plastic packaging systems were developed by Schoeller Allibert. The company invented products like smooth wall, foldable large containers and bottle crates with in-mould labels. The main focus has been on creating a sustainable packaging cycle.
“In the last five years, we have introduced more than 50 new products across all of the sectors we serve including automotive, food processing and agriculture, and we are continuing that process,” says Mr Gielen. “The products that we are bringing to the market are pretty unique. We try to make the product light and focus on creating more internal and a higher foldability, so that transfer and return may happen cheaper. The ultimate objective is to provide a better alternative to one-way plastics, thus responding to the world’s concerns regarding increasing plastic waste. “We pursue a very different strategy within the packaging industry and are proud to be in the reusable segment, a segment with a very high potential,” he goes on, emphasising that the strategic way forward is to keep bringing new ideas and new solutions to the market, where cardboard, wood and even metal gets replaced by easy-torecycle plastics. “That is our key message.”
The innovative focus covers all product groups across all markets the company serves. For example, later this year it plans to launch new foldable packaging that will replace the metal boxes used in the automotive industry, fully electrification-ready. Also this year, new products will be introduced for the food and beverage and agriculture sectors and, as Mr Gielen reveals, new packaging solutions for the e-commerce industry will be ready soon.
Close to customers
Major investment has gone into not just product development but also the production base. In the last two years, the company has opened two brand-new facilities to meet increasing market demand, strategically located close to customers.
In June the Schoeller Allibert Group inaugurated its 14th production plant – a state-of-the-art factory in Beringen, Belgium. As from 2019 this new facility, with a 6000m2 production hall, will be the first factory in which Schoeller Allibert will start to produce ‘circular plas-
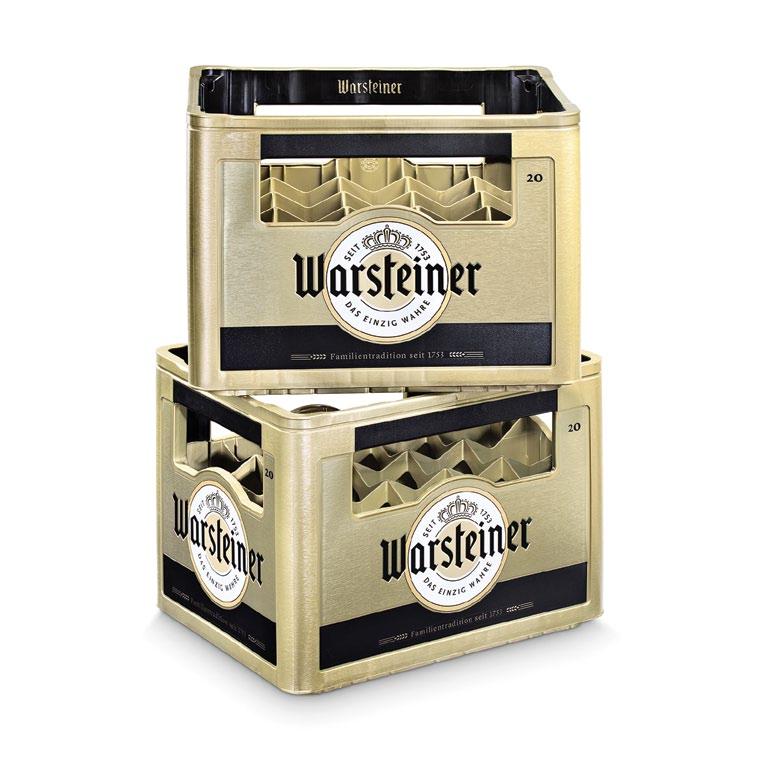
tic pallets’. The Beringen factory was opened just two years after the commissioning of another brand new plant in Poland, an investment worth €20 million. Located in the Katowice special economic zone, and with a total floorspace of about 6350m2, the plant produces a full portfolio of products for customers in the CEE region.
“We believe we need to produce close to the markets. If you want to be a sustainable company, you also need to avoid transport. That’s why the two locations in Belgium and Poland were chosen to cover both the western and eastern part of our European markets,” Mr Gielen points out.
With the latest manufacturing facility, Schoeller Allibert now operates 14 production plants worldwide – 12 in Europe, one in Phoenix, Arizona, and one in Shanghai. “In Europe, we have a very stable position and our business model has proven to be very successful. We will now attempt to apply it elsewhere, anticipating the industry’s needs and listening to consumers’ requirements. It is good to know that we are making a difference in the packaging industry,” he reflects. “We have ambitious plans for the future. Given the increasing environmental awareness worldwide and the general favourable market conditions we plan to grow by 50 per cent in the next five years.” n
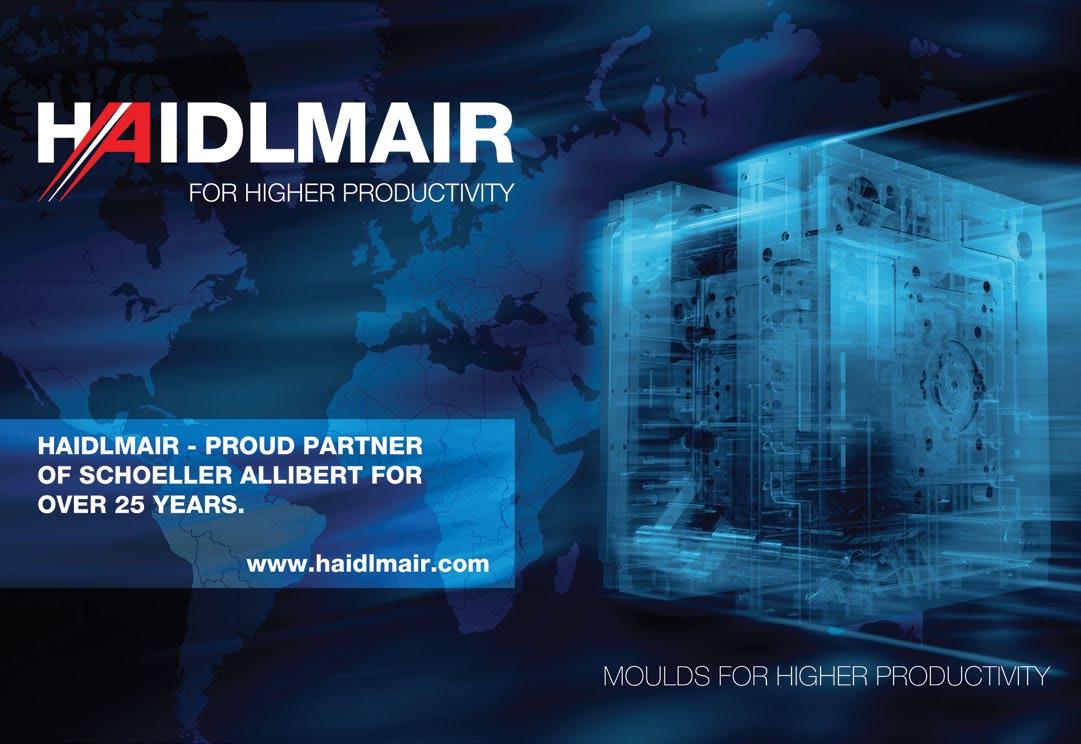