
3 minute read
Woven with Nature Kelheim Fibres
Plastic Free Solutions: VILOFT® short cut fibres are a leading material for producing fully flushable and biodegradable wipes.
WOVEN WITH NATURE
Kelheim Fibres is the world’s leading producer of viscose speciality fibres, combining innovative technology, technical expertise and outstanding customer service. Alexander Bachmann, the company’s Strategic Sales and Marketing Manager speaks about the latest developments.
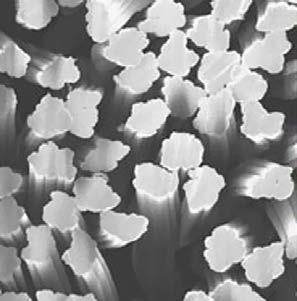
Bavaria-based Kelheim Fibres, established in 1936, is one of the oldest producers in its sector. Its speciality viscose fibres are used in widely diverse applications ranging from fashion, hygiene and medical products through to the nonwovens industry, and can be found worldwide. Today, around 80 per cent of the company’s output is sold in the export markets.
“We develop and produce high-value products. This has been our key strength and the reason we have survived the competition from low-cost manufacturers,” says Mr Bachmann. “Our products are 100 per cent bio-based and fully bio-degradable, making an important contribution towards the reduction of plastic waste and pollution by microplastics. With the growing preference for noplastic use, this is expected to be a growing business.”
He explains that innovation has always been a factor that has kept the company at the forefront, mentioning the recently launched Danufil® QR, the ‘fibre that sets quats free’, tailor-made for use in disinfectant wipes. The product has recently won the World of Wipes Innovation Award.
Danufil® QR is the only viscose fibre worldwide that – in contrast to standard viscose fibres – binds less than 10 per cent of “quats” (quarternary ammonium compounds), so that this common disinfectant can release its intended effect in the wipe.
Hidden Champion: Kelheim Fibres is the leading producer of tampon fibres and is planning to expand their position in the nonwoven hygiene market.


Danufil® QR fibres are made entirely of renewable cellulose and are therefore fully biodegradable. They can be easily processed with all nonwoven technologies.
State-of-the-art plant
The company suffered a major setback last year when most of the plant was destroyed by a large fire. Still, Kelheim Fibres has managed to turn this misfortune into an advantage, says Mr Bachmann. “The need to rebuild the technology gave us the opportunity to focus on modern state-of-the-art equipment and particularly on resource-saving and environmentally-friendly production technology.”
He pointed out that it is not just the technology that has been renewed but during the long shutdown the company also revised and implement changes in the whole process and production systems, significantly improving flexibility. “The ultimate outcome of this disaster is that we now operate a highly efficient, state-of-the-art highly environmentally-friendly production technology - we are now the fibre producer with the lowest CO2 and sulphur emissions in the world.”
This may further enhance the company’s competitive advantage as more and more producers, including the fast fashion brands, push for environmental-friendly products, and sustainability has become an important decision-making factor. “Just a few years ago, we couldn’t compete with the Asian manufacturers. Even then we were highly sustainable, but nobody cared. This has now changed, as sustainability has become a hot topic, and this development is of course very interesting for us.”
Natural from start to finish
Sustainability will stay at the core of Kelheim Fibre’s further development. This year the company has joined the CanopyStyle initiative, aiming to make sure that no wood from ancient and endangered forests is used for the production of viscose fibres, by seamlessly documenting the supply chain. Kelheim Fibres already meets the requirements of the strict EU Timber Regulation and exclusively uses wood pulp from sustainable forestry with either FSC® or PEFC™ certification. “Joining the CanopyStyle initiative is a logical next step which will deliver more transparency to customers and consumers,” says Mr Bachmann.
He affirmed that the company will continue to offer speciality fibres that can be tailor-made to the customer’s specifications and enable the production of future-oriented materials with integrated functionality. Examples include short-cut fibres that can be carbonised and integrated in compounds to create an electromagnetic shield or even electrical conductivity.
“We consider ourselves to be the world-leading nonwoven viscose fibre manufacturer and in the future, we plan to focus even more on the nonwoven industry, particularly the hygiene segment. The nonwoven business has been our key strength for many years and we would like to expand that knowledge further, to develop more groundbreaking products, meeting the requirements of the future.” n
Green Chemistry: Massive investments in environmental projects have made the cleanest viscose fibre in the world possible.
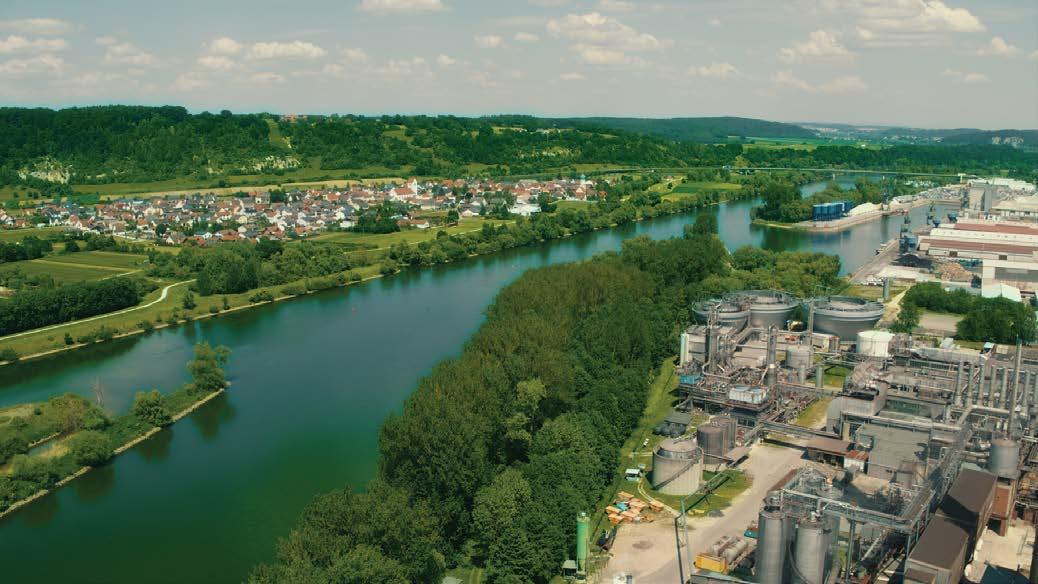