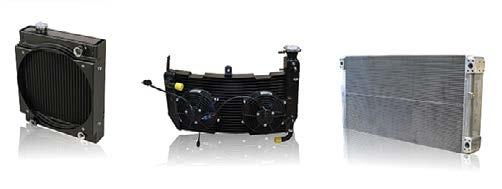
5 minute read
Condensed and integrated cooling solutions RAAL

RAAL is a European market leader in the design and manufacture of modular heat exchangers and cooling systems. With over 40 years’ experience in the field, the company provides custom cooling solutions for countless applications that range from automotive and industrial, to construction and mining, as Philip Yorke reports.
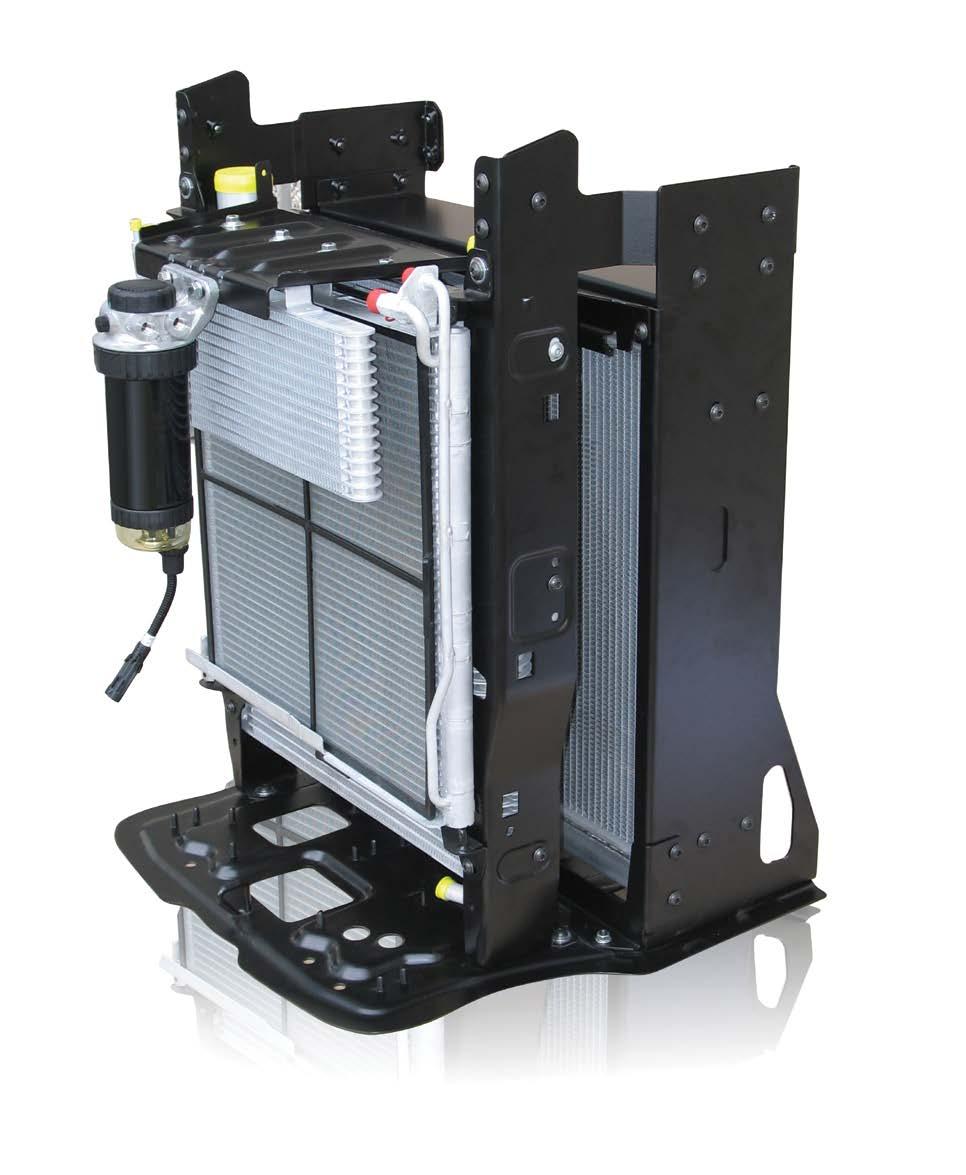
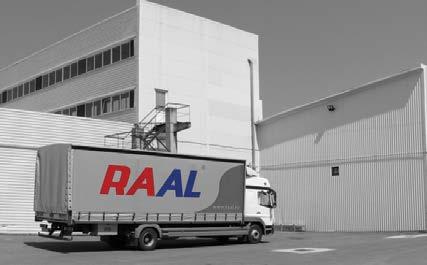
CONDENSED AND INTEGRATED COOLING SOLUTIONS
RAAL is a fully integrated engineering company based in Romania, that is active in all aspects of the manufacturing, design and testing of modular heat exchangers and cooling systems. The company is fully integrated, which means that every process and product is created in-house. This competitive advantage allows for very short development and assimilation cycles in the creation of new products as well as in the short-term production and supply of limited series production quotas.
The company utilises its own dimensioning software for heat exchangers, and its software is also developed in-house and based on theoretical studies that involve thousands of test procedures. The company uses FEA (Finite Element Analysis) to simulate the structural, flow and vibration stress conditions of each assignment.
Today RAAL can claim unrivalled experience in designing heat exchangers and cooling systems. Starting from the specifications, dimensions or CAD data of the application, RAAL designers are
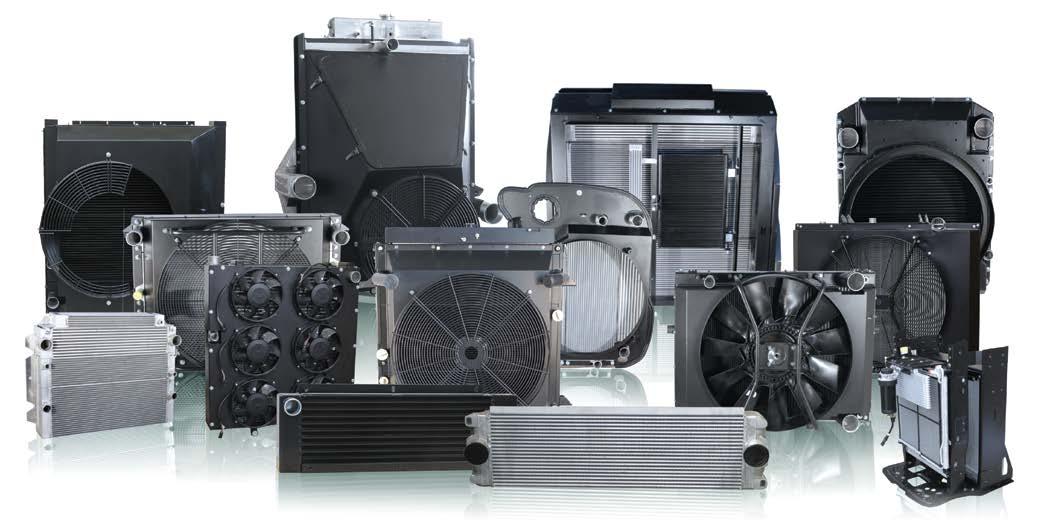
able to find the best solutions for the most efficient use of available space. The company’s designers also have the ability to continuously optimise its products, so as to fully meet the requirements of any application.
Advanced validation testing
The extensive RAAL Testing Centre is a state-of-the-art facility where the validation of new products is performed. Based on technical specifications or on the parameters obtained by means of DAQ carried out on a customer’s equipment, the heat exchangers are tested for performance and strength.
RAAL’s Testing Centre capabilities include thermal and fluiddynamic performance tests in its modern wind tunnel, durability tests, thermal cycle, pressure cycle, and burst-pressure. All of which are performed at ambient or at high temperatures in the dedicated climate chamber. The Centre also undertakes durability tests, shock and vibration testing, internal cleanliness tests and chemical and accelerated corrosion tests. This is in addition to conducting thorough and extensive metallographic studies.
RAAL engineers also have a vast experience in tool and die design, and in developing the specific equipment necessary for its manufacturing processes. The company places special emphasis on the design, manufacturing and optimisation of its new generation of fin-forming machines, which are capable of producing a wide range of fins and highly efficient turbulators.
As one would expect, all RAAL products are manufactured in full compliance of the latest international standards, such as ISO 9001:2008 and ISO/ TS 16949:2009 - Quality Management Systems. As well as EN ISO 14001:2004 - Environmental Management System and OHSAS 18001:2007 - Occupational Health and Safety Management Systems. Unique flexibility
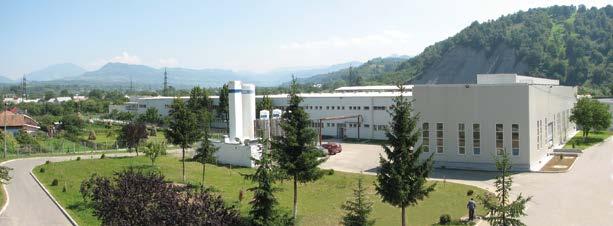
All RAAL’s advanced heat exchangers and cooling systems are adapted to precisely suit a customers’ needs and are developed together with them. The company is justly proud of its strong, creative research and development department that has been at the forefront of innovative thermal development for more than four decades. With over 150 specialist engineers and a well-equipped test centre, it has registered many patents for its fins & fin-forming machines and the latest design and technology solutions.
With its considerable on-going investment in R&D, and the latest equipment and cooling system technologies RAAL produces more than 50 prototypes every month, thus making it possible to achieve the development of a new product within 50 days, which is far less than many of its European competitors.
Each customer and every application are important to RAAL and, in this regard, it has trained and specialised its teams in different fields and applications. These include tool and die design, manufacturing, sales, logistics and marketing. RAAL is also unusual in that it is one of the few fully integrated companies in Europe that offers short-term product development and delivery at very competitive rates.
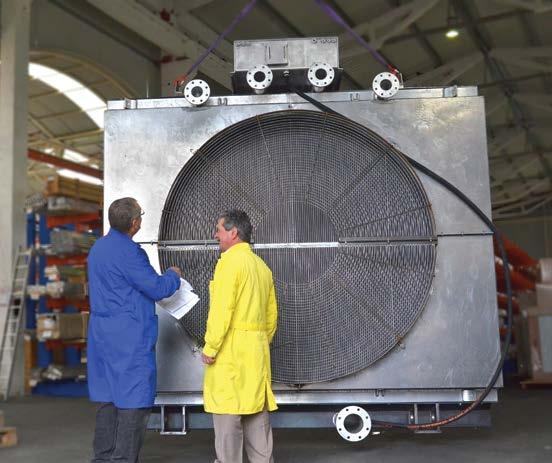

Focus on sustainability
For many years RAAL has offered compact and lightweight products that offer minimal impact on the environment. This is mainly due to the reduced consumption of materials and greater fuel efficiency. Its advanced cooling solutions comply with all the new environmental regulations on polluting emissions (Tier 4F, etc.).
What’s more, the company’s full range of modular customised products are all 100% recyclable and subscribe to the international Environmental Management System according to EN ISO 14001:2004. RAAL’s continuing focus on green issues and sustainability thus sets a positive example to other manufacturers in the field and makes an on-going contribution to combatting global warming.
Increasing thermal performance
With its strong commitment to increasing the efficiency of its products, RAAL’s Brazed Plates heat exchangers have been specifically designed to increase thermal performance in the fluid-to-fluid cooling applications. This type of heat exchanger is made entirely of aluminium alloys using advanced, controlled atmosphere brazing technology. Different working fluids can be used including water, oil, air and refrigerant. The latest Brazed Plates designs can be used for the various types of heat exchangers that the company manufactures which provide constructive solutions for all sectors from automotive and industrial, to ATV’s and avionics.
Furthermore, RAAL manufactures heat sinks, cold plates and battery coolers for hybrid and electric cars. In order to meet the increasing demand in this sector, the company has recently opened a new, state-of-the-art production hall dedicated exclusively to the manufacture of heat exchangers designed for the cooling of electronic circuits and batteries for hybrid and electric vehicle applications. n

For further details of RAAL’s innovative heat exchangers and cooling systems visit: www.RAAL.ro
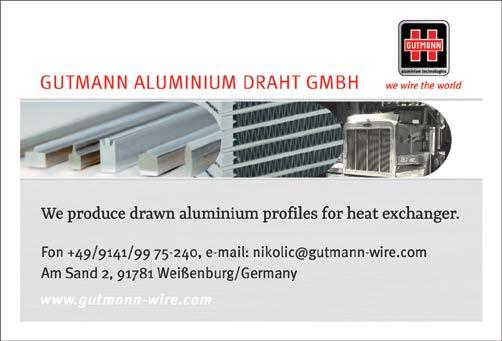