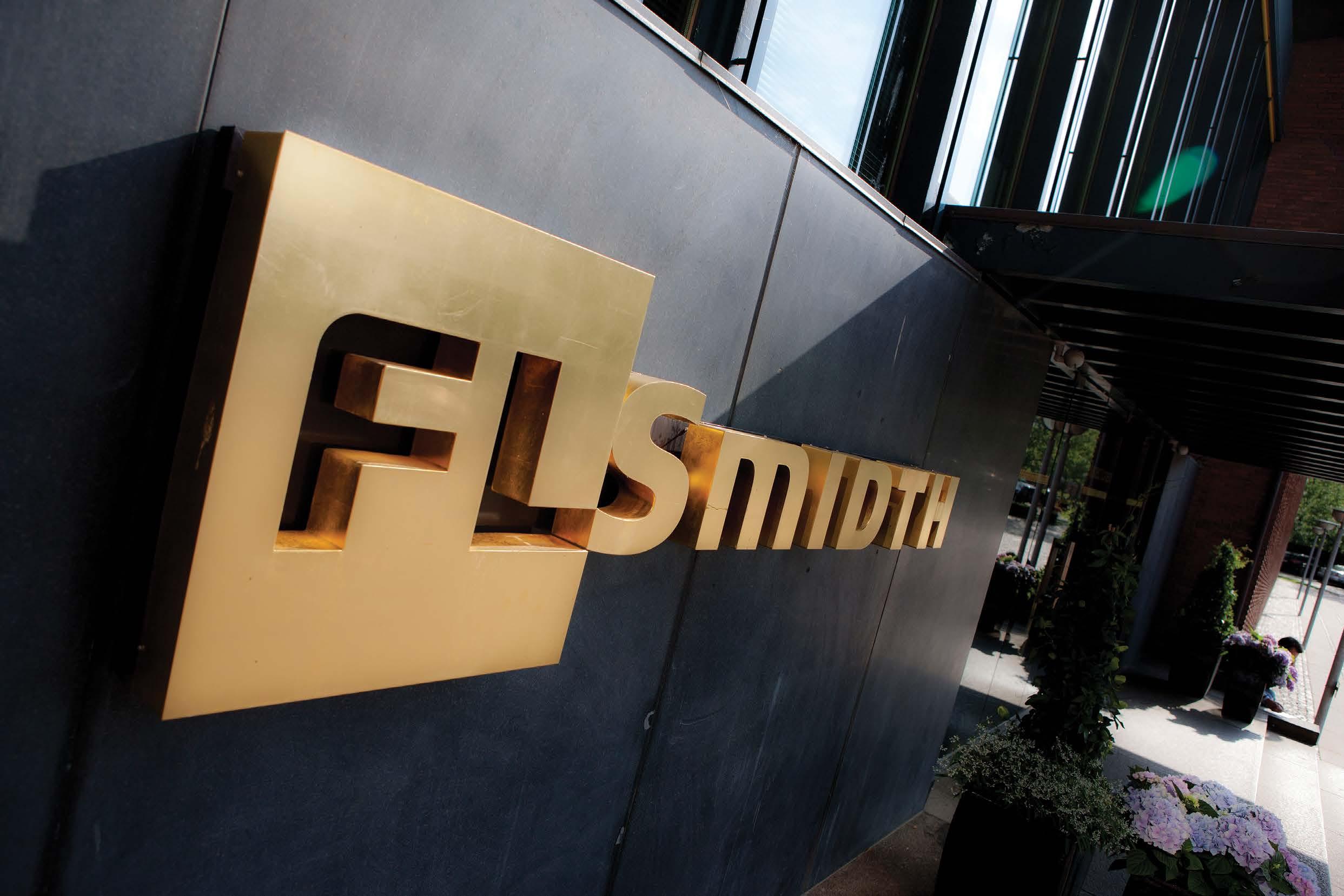
4 minute read
Testing times for lithium FLSmidth

TESTING TIMES FOR LITHIUM
In the race to supply the world with battery-grade lithium, FLSmidth stands out as the clear supplier of choice. Its new, best-in-class centres of excellence in Utah and Pennsylvania offer the most advanced testing capabilities for both brine and hard-rock lithium sources, as Philip Yorke reports.
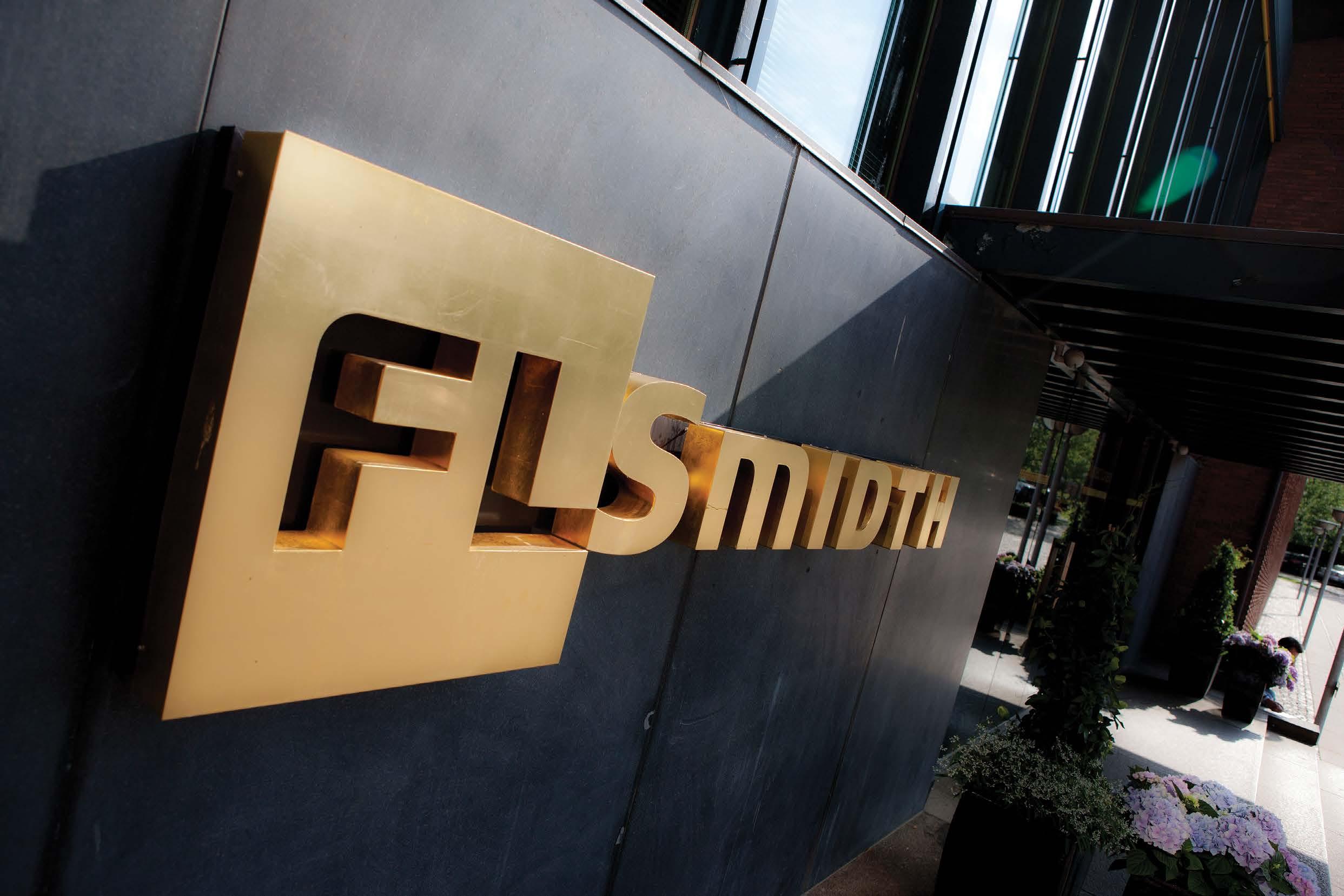
FL Smidth was founded in 1882 by Frederik Laessoe Smidth in Copenhagen, Denmark. From humble beginnings as an engineering consultancy it saw consistent growth and today is a global leader in the provision of machinery, systems and services for the cement and mineral industries.
Over the years the company expanded its non-core activities and in 1989, the entire FLSmidth Group consisted of more than 125 companies operating in areas such as cement, engineering, plastic, aerospace and cement building materials.
Throughout the 1990s leading international manufacturing companies such as Pfister, Ventomatic and MAAG Gear were acquired by the group. Today FLSmidth leads the field in its chosen disciplines and in 2018 employed over 13,000 people and generated revenues of more than DKK 20 billion.
Huge new markets
More than half of the world’s 250,000 tonnes of lithium carbonate equivalent (LCE) used in 2018, was accounted for by electric cars and by 2028 that figure is expected to be over 90% of 1,365,000 tonnes. Electric vehicles need large batteries and rising demand in this field is expected to create huge new markets for battery-grade lithium in the foreseeable future.
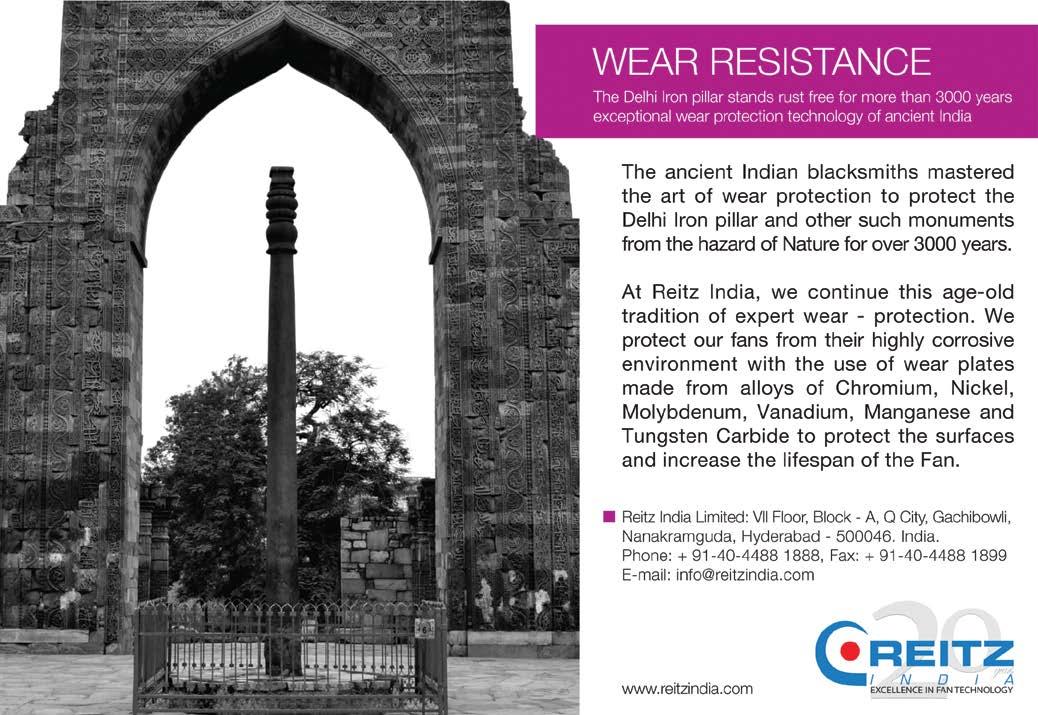
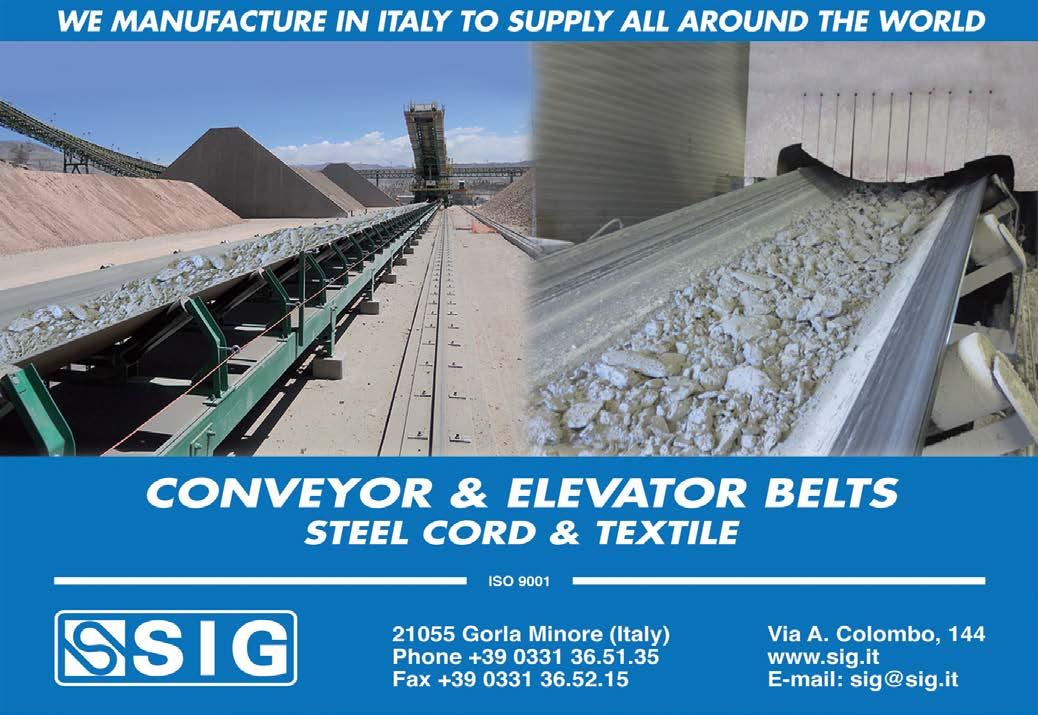
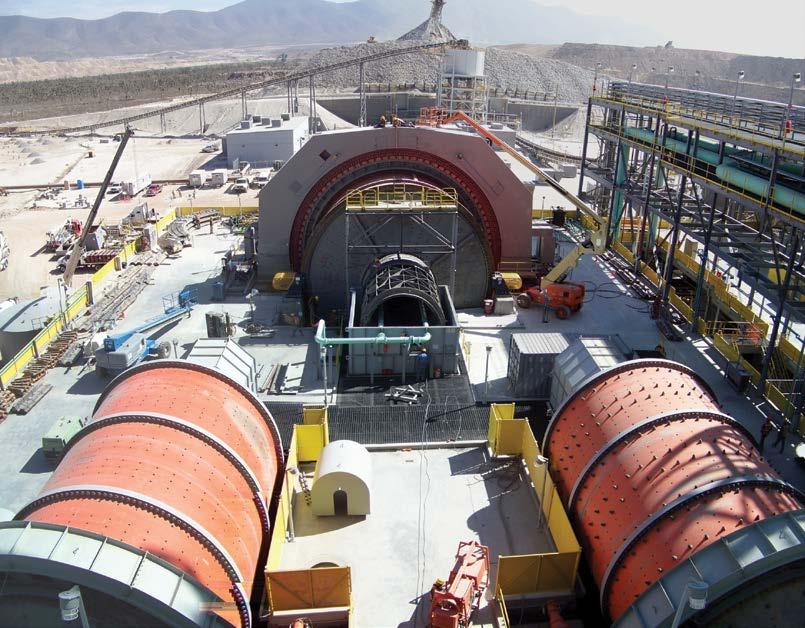
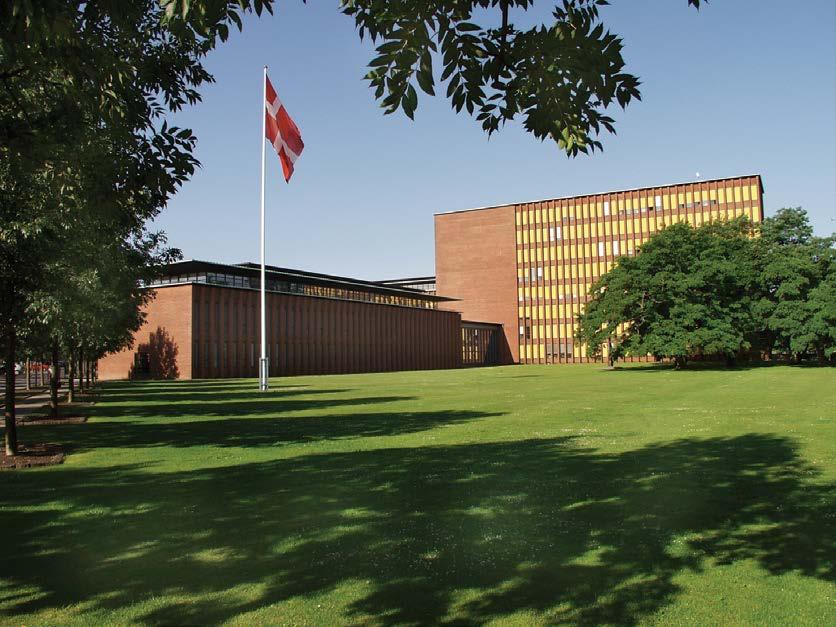
Today there is a global race to get these new projects off the ground, and time-to-market is overriding all other factors when customers consider the opening up of new production facilities. One way to speed up the process of designing and opening a new lithium facility is to ensure that the right testing is carried out of the source material. Some mining companies take a traditional approach and go to established commercial laboratories. However, those test procedures are not sufficient for the technology and equipment-design required to build today’s high-performance, more efficient facilities.
At its state-of-the-art testing centres in Salt Lake City, Utah and Bethlehem, Pennsylvania, FLSmidth has the world’s best-in-class testing capabilities for the testing of both brine and hard rock lithium sources. Testing at those facilities incudes mineral testing and pyroprocessing testing for the design of optimal manufacturing plant.
Based on these tests, the company can design the optimal process flowsheet, plant design and plant layout. This means it is able to offer exceptional value when customers approach FLSmidth early in the design process. The earlier that project discussions begin, the quicker the projects can move forward and the better the plant design will be. The early involvement of FLSmidth also results in lower capital expenditure and a significantly faster time to market.
Other processing solutions
Despite the young age of the industry, FLSmidth has more than 20 years of experience with specific hydro-processing in lithium facilities. For other processes, the company is able to replicate process equipment from other commodities and make modifications in order to meet other specific requirements.
KAO diamond mine in Lesotho, owned by Namakwa Diamonds, recently needed a significant pump conversion to be carried out in the field. This is an undertaking that can be both difficult and time consuming. In addition, it is also a ‘high-stakes’ operation as a cyclone feed is critical to the overall mining process and the ability to generate cost-effective returns. A wrong decision at this stage can result in a lot of lost revenue. It also takes trust to allow the changing out of a pump that a company is familiar with and to replace it with an entirely new and unknown pump, all based on a promise of significant cost-of-ownership rewards for the mining company.
It was the potential for greater cost-efficiency that convinced the KAO Diamond Mine to implement the latest KREBS MillMax™ Pump. After initial discussions, the first trial pump, a MillMax 8X6 centrifugal seal was installed in a cyclone feed application (DMS 2 Pump 1). After seven months of operation, results proved that the MillMax was performing exceptionally well, especially when it came to the area of reduced wear.
Brad Moralee, head of Product Unit Pumps, Cyclones and valves at FL Smidth said, “It is a high pressure situation for us, you are typically given a window of opportunity during a routine shutdown to complete a major change. After which, the new pump must run as expected when the plant is recommissioned. You need the combination of a great product, but more importantly great technical understanding of the process to be able to propose the correct, optimal solution. We also understand what is at stake from the customer’s perspective”.
For KAO the change produced ‘knock-out’ results when compared to the previous solution from a different supplier. The MillMax increased maximum operational life by an amazing nine times across the impeller, casing ad back-liner. This has seen KAO look again to FLSmidth, who suggested running a one month trial with the SlurryMAX®, which had recently just arrived on the South African market.
The new SlurryMAX trial was based purely on its sealing capabilities, as KAO were already confident of the hydraulic performance of the pump and had no concerns about wear either as they were confident that it would demonstrate predictable and even wear-life across all the wet-end parts. n
For further details of the FLSmidth Goup’s latest innovative products and services visit: www.fldsmidth.com