
5 minute read
The foundations of sustainable growth
HeidelbergCement, the German-headquartered multinational building materials company, is currently expanding its operations in the USA and taking a major step towards the realisation of a carbon neutral future for the cement industry
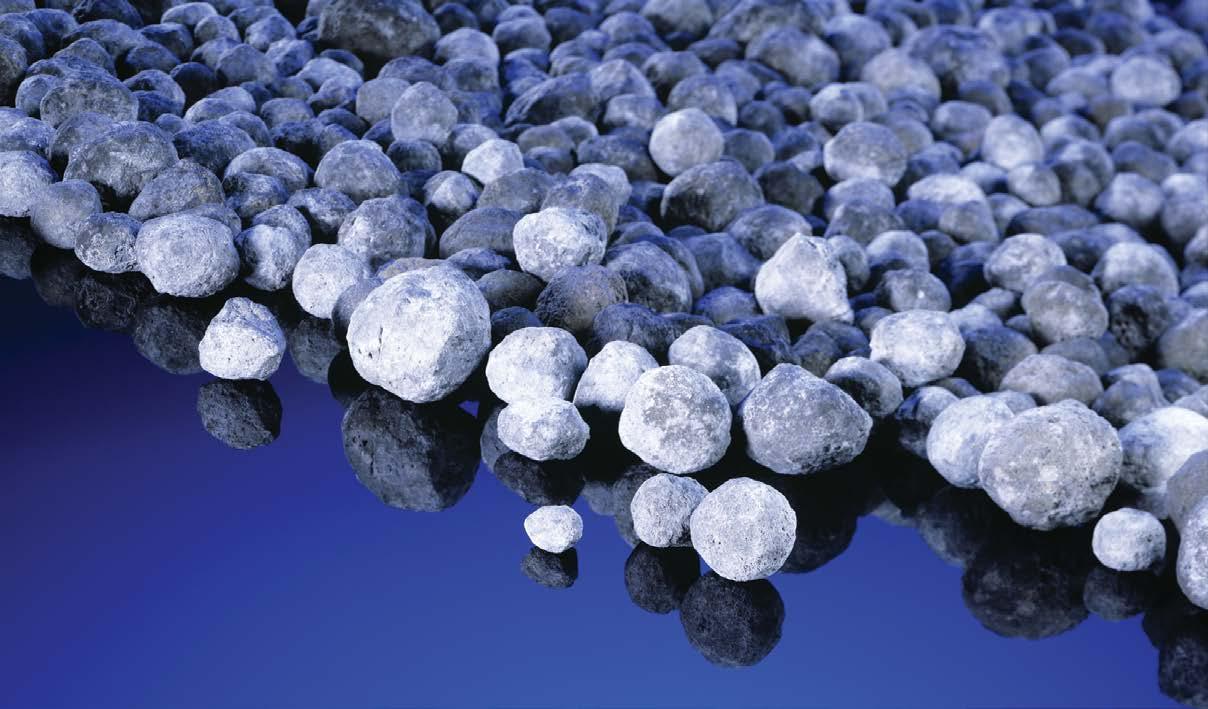
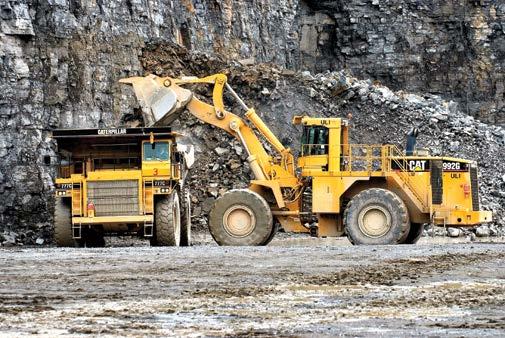

In September 2019 HeidelbergCement announced that its North American subsidiary, Lehigh Hanson, Inc., had entered into an agreement with Giant Cement, a subsidiary of Elementia S.A.B. de C.V., to acquire its Keystone cement plant in Bath, Pennsylvania.
The Keystone plant has been operating since 1928 and supplies the Pennsylvania, New Jersey and New York markets with bulk and bagged Portland cements. The plant operates with a kiln line which was modernised in 2009 and has a capacity of 1.1 million tonnes of cement per year.
“With its modernised kiln, healthy customer base and large limestone reserves, the Keystone cement plant is an excellent strategic fit for HeidelbergCement in North America and an important step in strengthening our cement footprint in this key market,” said Dr. Bernd Scheifele, Chairman of the Managing Board of HeidelbergCement. “The acquisition of one of the most modern and environmentally sustainable cement facilities in the United States will further help Lehigh Hanson reduce its carbon footprint by safely substituting alternative fuels for traditional fossil fuels such as coal. In addition, we anticipate a number of operational efficiencies as a result of this transaction.”
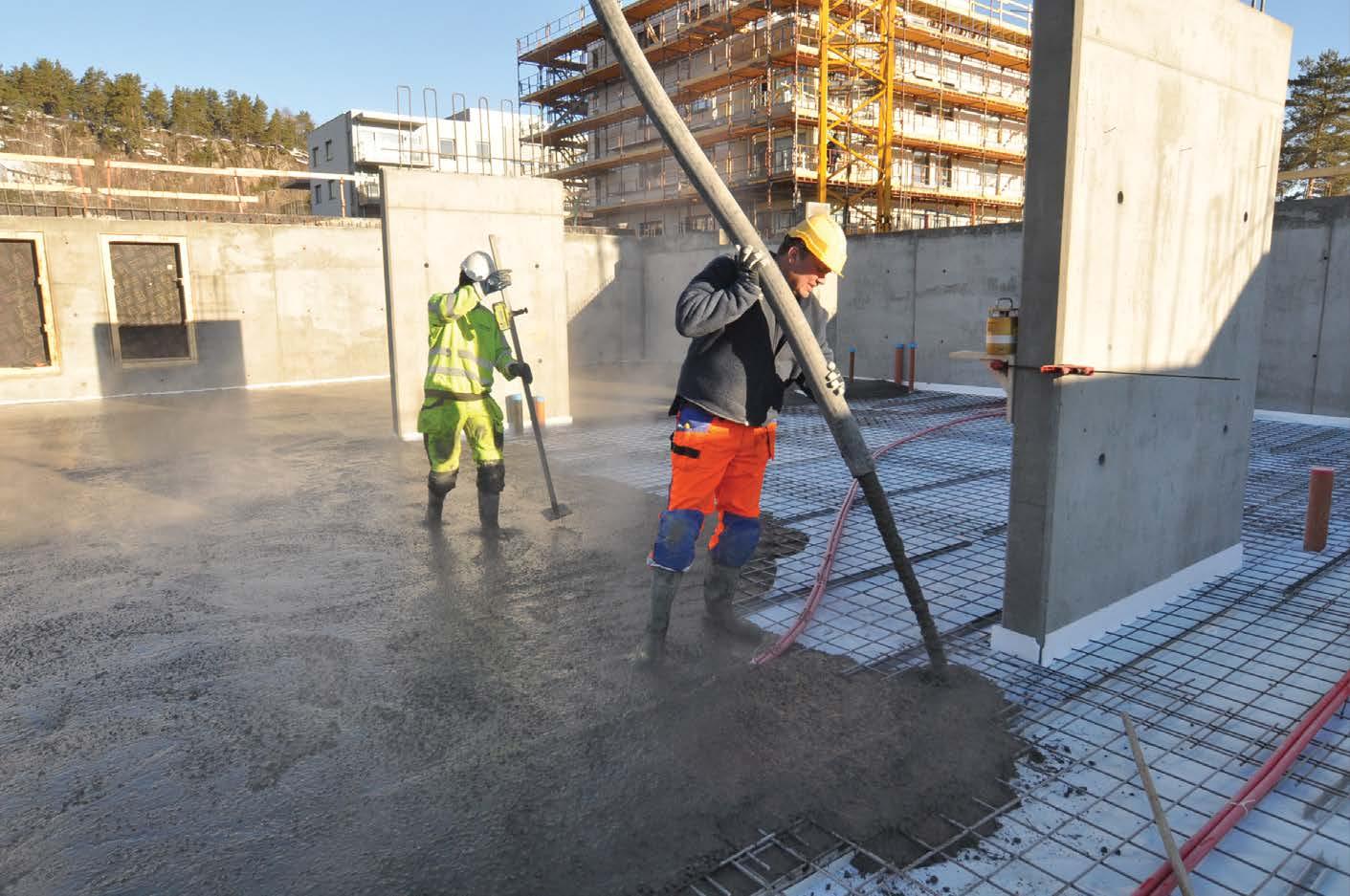
Global reach
HeidelbergCement is one of the world’s largest building materials companies. Its core activities include the production and distribution of cement and aggregates, the two essential raw materials for concrete. Its downstream activities include mainly the production of ready-mixed concrete, but also of asphalt and other building products in some countries.


With the takeover of the Italian cement producer Italcementi in 2016, HeidelbergCement became the world number one in aggregates production, number two in cement, and number three in ready-mixed concrete. Thanks to this acquisition, it also gained access to important new markets, including France, Italy, Egypt and Morocco as well as Thailand, Kazakhstan, India, the USA and Canada.
Today the Group has activities in around 60 countries with 63,000 employees working at more than 3,000 production sites. HeidelbergCement operates 156 cement plants with an annual capacity of 197 million tonnes, more than 1,700 ready-mixed concrete production sites and over 600 aggregates quarries.
In June 2019, HeidelbergCement further expanded its European operations with the acquisition of Cemex’s Centre region aggregates and ready-mixed concrete businesses in France. The acquisition includes seven aggregate quarries and 28 ready-mixed concrete plants. The acquired aggregates reserves and resources amount to about 25 million tonnes. HeidelbergCement France will fully integrate the operations into its own network.
“With this acquisition, we strengthen our vertically integrated market position in central France,” said Dr. Scheifele, “The operations fit very well into our existing network of aggregates and ready-mixed concrete plants in the Paris region, and we expect significant synergies. The acquisition is part of our strategy of disciplined growth and increasing shareholder returns.”
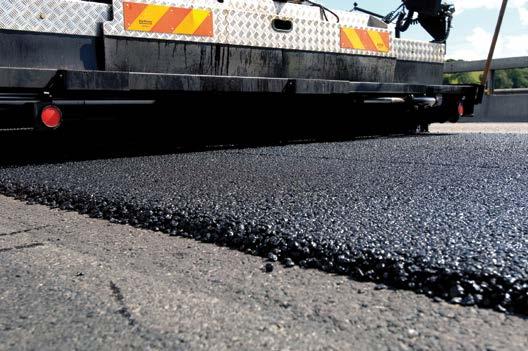

A Sustainable Future
Cement production is by nature raw material and energy intensive. Consequently HeidelbergCement has always built its long-term success on sustainable business practices. This includes securing access to raw materials reserves, efficient and innovative production processes, the development of new products and the use of alternative raw materials and fuels. HeidelbergCement is also active in the promotion of biodiversity at its extraction sites.
A major new step in advancing this sustainability agenda was taken in September of this year when the company signed an agreement to work with the state-owned Norwegian energy Group Equinor on the capture and storage (CCS) of CO2.
Since 2011, Heidelberg Cement’s Norwegian subsidiary Norcem has been running a project dedicated to CO2 storage in the cement industry at its Brevik cement plant. The CCS project “Northern Lights”, which includes the project at the Brevik cement plant, has been initiated by the Norwegian government in three different industry sectors. According to the plan, the captured CO2 emissions are to be transported to empty oil and gas fields beneath the North Sea beginning in 2023 and stored there permanently. The Norwegian government shortlisted Brevik for an industrial-scale CO2 capture trial at the start of 2018.
The Memorandum of Understanding signed with Equinor is a further step towards realising this CCS project. The agreement also includes the intention to examine the possibility of capturing CO2 at other HeidelbergCement plants for storage within the Norwegian continental shelf. Additionally, both companies will work on optimising the CO2 transport chain and strive to implement CCS as a panEuropean solution for CO2 disposal.
“At our Brevik cement plant, we have shown that we are able to capture carbon dioxide on an industrial scale,” says Dr. Bernd Scheifele. “Our CCS project is currently the most technically mature in the cement industry. We plan to capture around 400,000 tonnes of CO2 per year at Brevik, which corresponds to around 50 per cent of the plant’s total carbon emissions. For us, CCS – alongside our measures for reducing CO2 emissions – is another important element in our vision of CO2 neutral concrete production by 2050.”
HeidelbergCement is set to reduce its specific net CO2 emissions per tonne of cement by 30 per cent compared to 1990 levels by 2030. This target has been approved by the Science Based Target initiative (SBTi) and is in line with the goals of the Paris Agreement, making HeidelbergCement the first cement company worldwide to have approved science-based CO2 reduction targets. By 2018, the company had already achieved a reduction of 22 per cent. HeidelbergCement will realise its vision of carbon neutral concrete – at the latest – by 2050. n
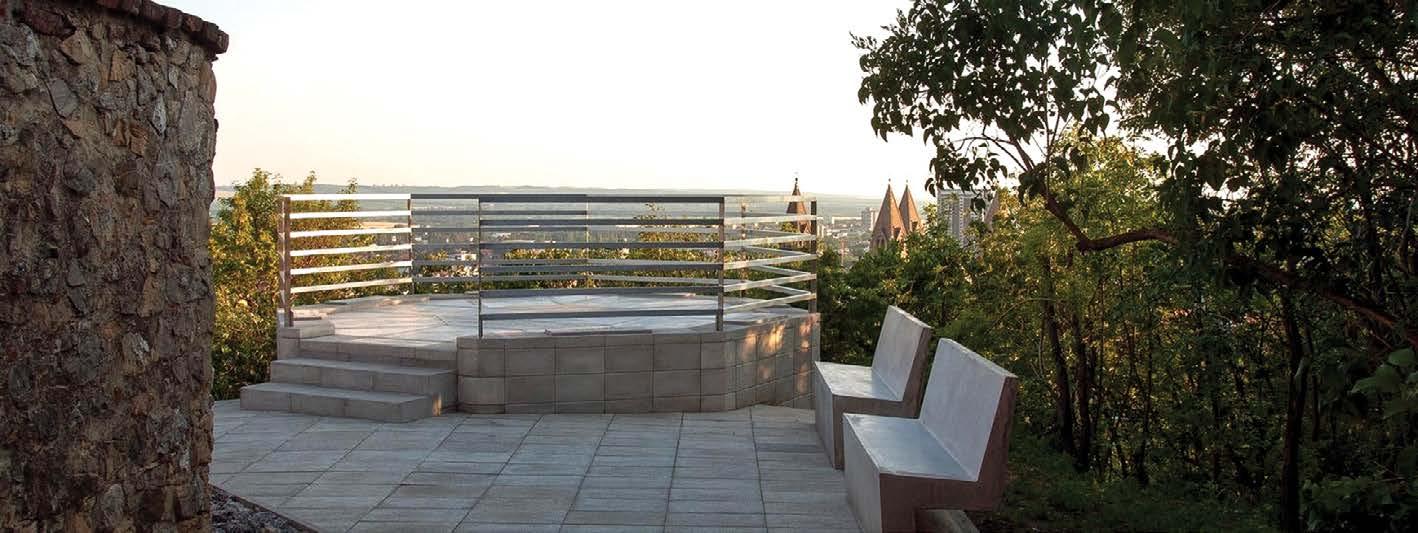