
4 minute read
Masterclass in mechatronics Bitron
MASTERCLASS IN MECHATRONICS
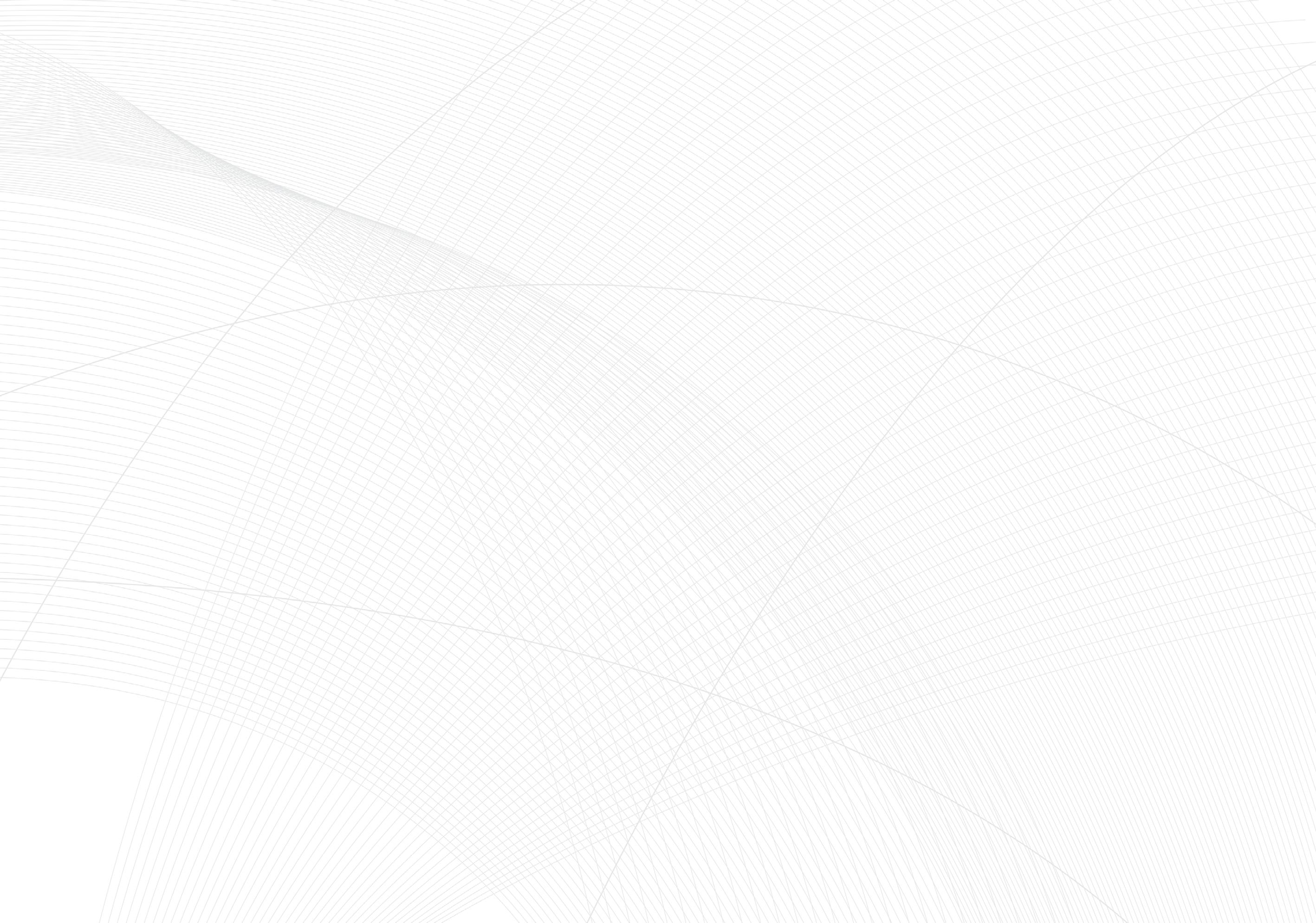
Bitron is an independent, high-tech Italian components manufacturing company with a broad product portfolio that ranges from household appliances and automotive products to HVAC and renewable energy systems. Philip Yorke reports on a market leader that continues to excel through innovation and sustainable manufacturing processes.

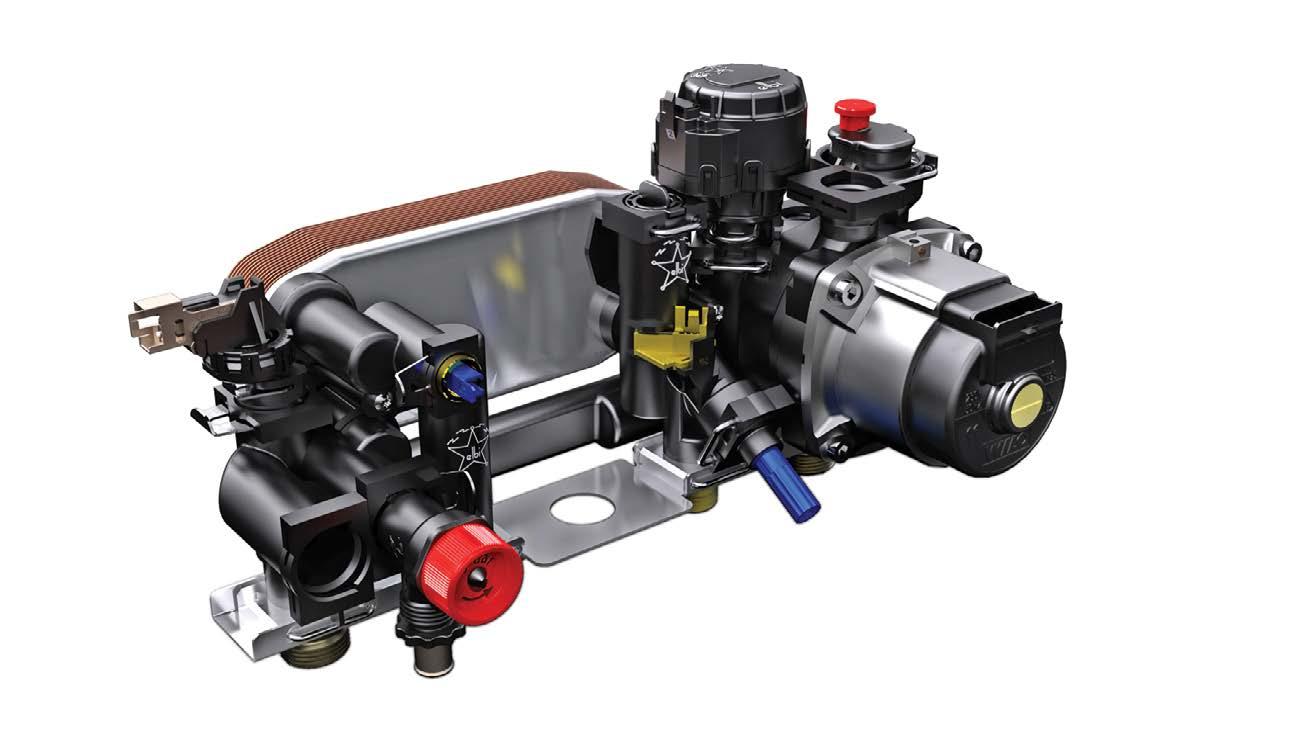
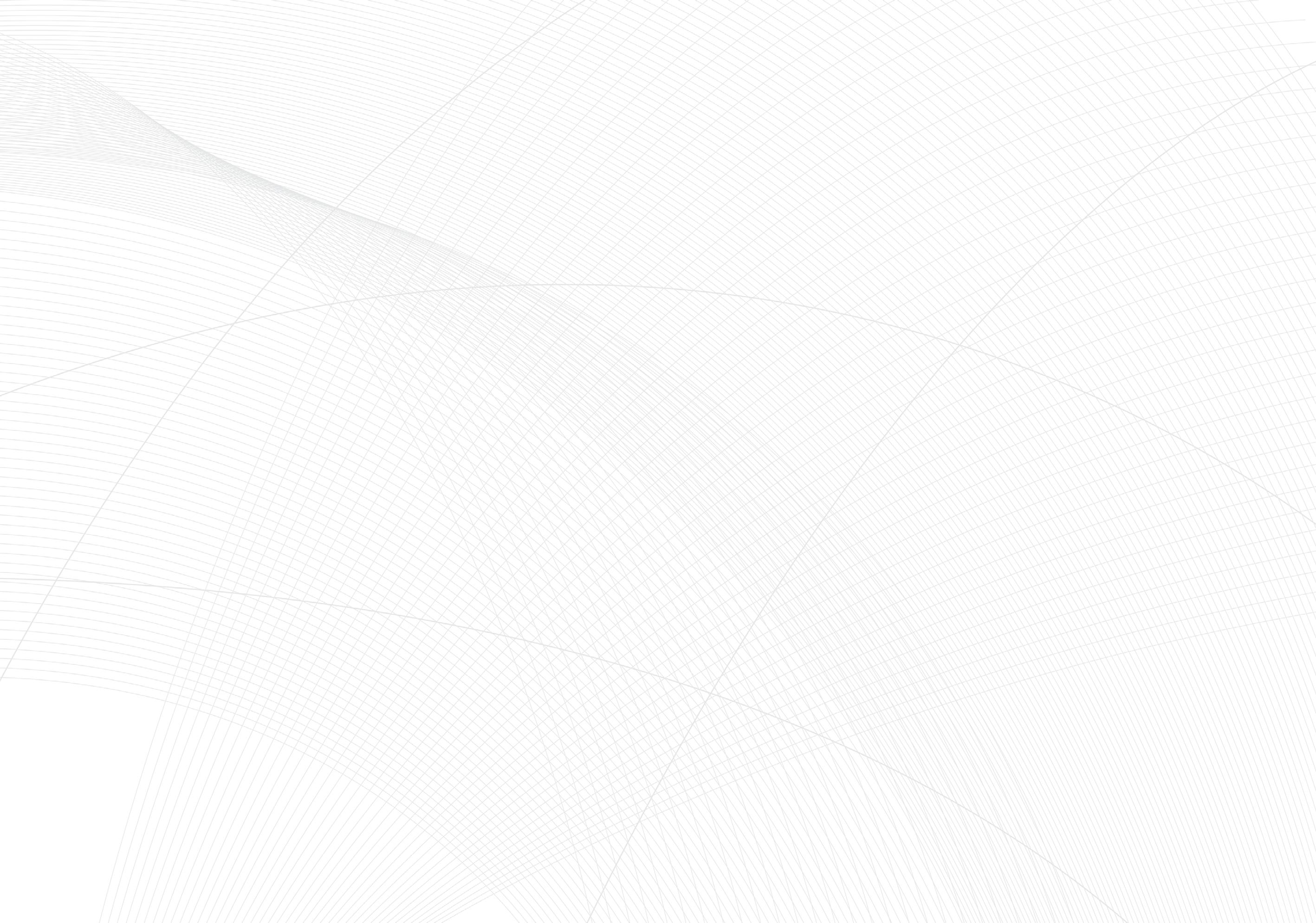
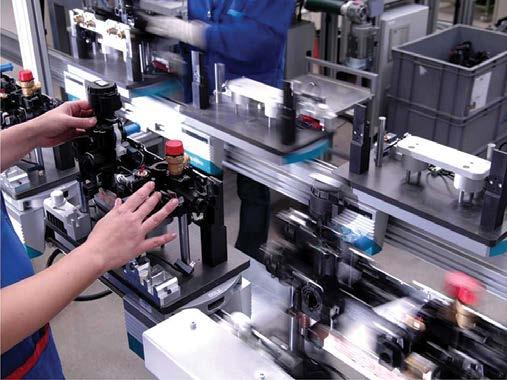
The origins of Bitron go back almost 65 years, more specifically to 1955 when three brothers; Enrico, Giovanni and Carlo Bianco, established a workshop in Italy to manufacturer household appliance components. Steady growth continued over the years, and the company expanded both in terms of geographical reach and market segments. These were further boosted by a series of strategic acquisitions. In 1992 there was the decision to create a new corporate identity, and thus all the companies of the group were renamed Bitron. Today the group is organised into four key business divisions: automotive, household appliances, HVAC (Heating, Ventilation and Air Conditioning) and renewable energy.
As with its other market sectors, Bitron is a leading global supplier of mechatronics products for automotive interiors. This includes pedals, switches, sensors, control-panels and displays. In addition, Bitron produces power-train components for commercial vehicles, motorcycles and scooters.
The company’s portfolio of HVAC components and systems is equally extensive and includes items for boilers, heat pumps, water heaters and other applications. The company’s range of hydraulic and electrical components and heat exchangers are comprehensive and unrivalled in the industry.
Diverse technologies
Bitron’s commitment to R&D has resulted in highly efficient, fully automated production lines with high process verticalisation, in order to allow the complete assembly of products inside its own plants. Some of the advanced manufacturing processes already integrated into its automatic lines are laser and hot blade welding for plastics, laser marking, coating, resin-dispensing and mechanical insertions.
The company has also developed a standard automatic, patented line called ‘the MAC line’ that can be configured and set up for multiple products and finishing processes, with the objective of achieving an automatic workflow that enables high mix, low volume production.
In addition, Bitron’s MES (manufacturing execution system) provides comprehensive solutions for traceability, production scheduling and quality KPI monitoring on a real time basis. Standard reports are also available, such as unique ID tracking or component batch utilisation. All its process monitoring systems work in real time, to help production operators and engineers to improve process quality and output.
Bitron’s product testing division manages in-circuit testing (ICT), functional verification testing (FVT) and special, customised tests. The company’s In-Circuit Test (ICT) is entirely designed and manufactured in-house including interface boards, test software and debugging.
In addition to classic in-circuit parameters, it also tests LED function and colour, as well as mechanical switches and potentiometers,
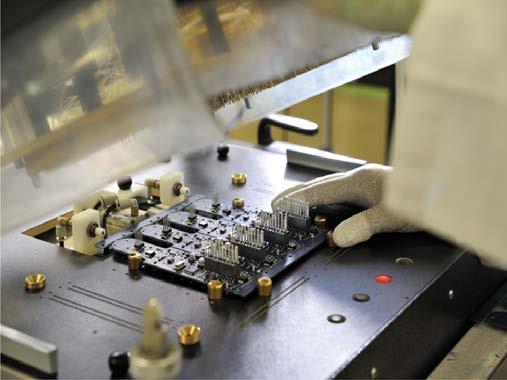
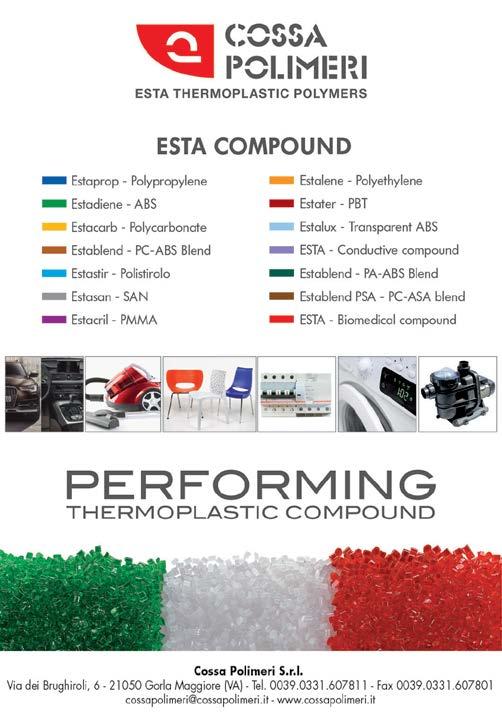


using mechanical actuators. Functional tests on energised boards are also carried out on these fixtures.
Devices such as microprocessors can be programmed during the ICT process. Furthermore, the equipment can easily be manually or automatically loaded and unloaded. The company also use the latest flying probe systems for fast prototyping.
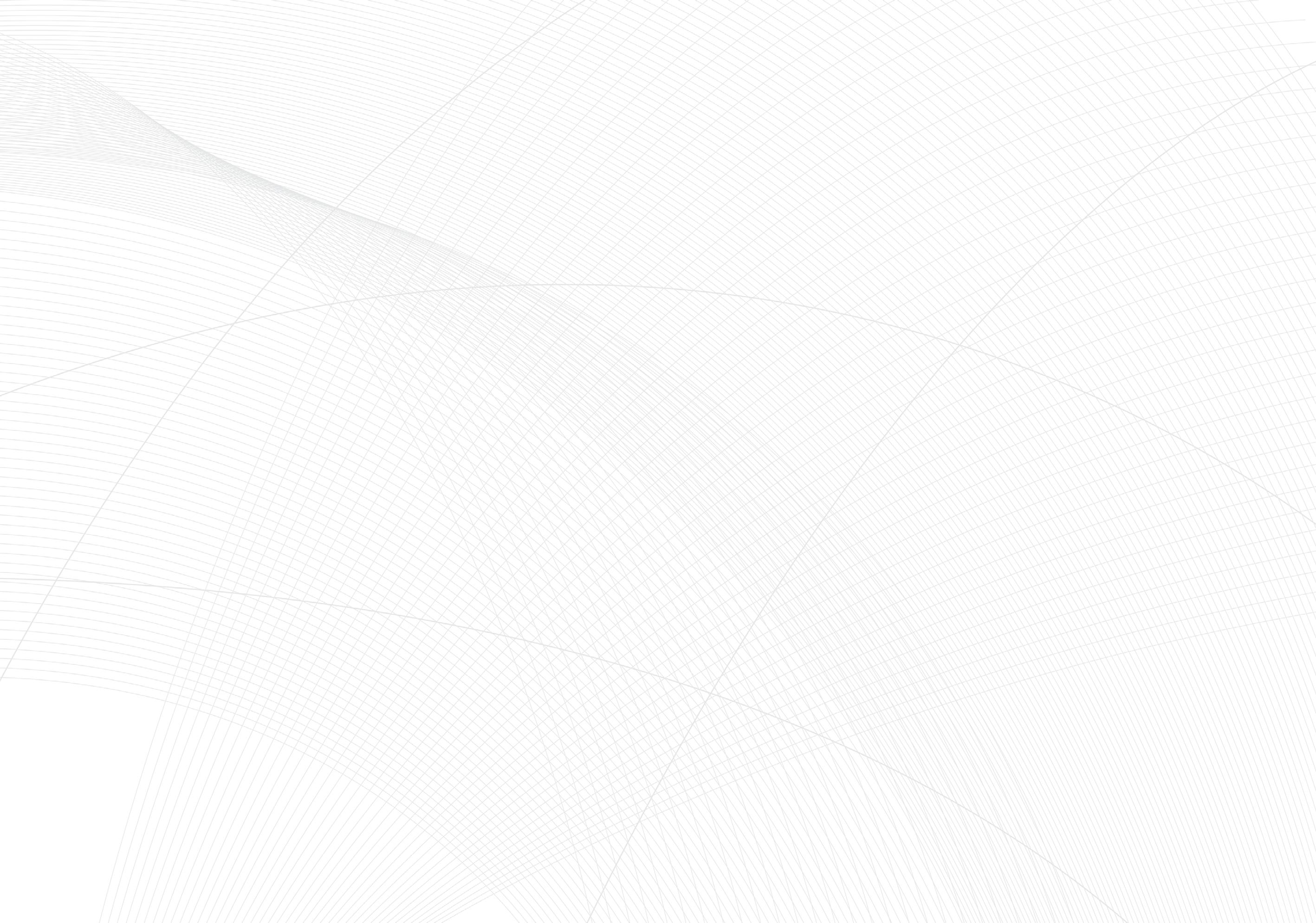
Customised functional verification
Bitron designs and develops standard functional verification test equipment as well as customised models for specific tasks, such as the testing of electricity meters, photovoltaic installation controls and tyre pressure sensors. Its advanced systems measure voltage, current, energy, power, pressure and torque. Loading and unloading can be carried out manually or fully automated. All test data is stored on centralised servers to respond to traceability requirements. As a global EMS provider, Bitron’s supply chain management system has dedicated modules for demand planning analysis, components procurement and delivery tracking. The ERP system can handle both manual order transmissions, and EDI implementations, according to its individual customer’s requests.
Optimised photovoltaics
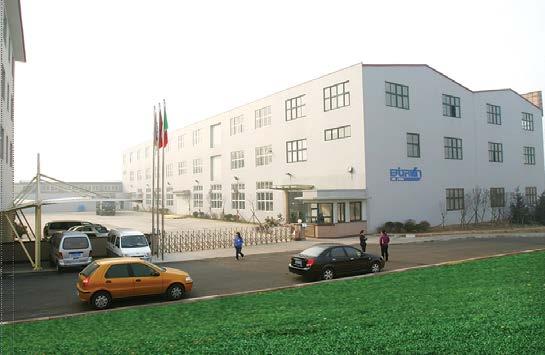
Components and systems are fully optimised for solar panels, boilers, heat pumps, water heaters and other applications. These include hydraulic groups, electronics components and heat exchangers, which are all produced by the company’s HVAC division. The Endana devices for the optimisation, monitoring and safety of photovoltaic panels and systems are also the specialisation of the renewable energy division.
Bitron employs over 6,000 staff worldwide, operating from 13 manufacturing plants and 10 marketing and sales offices. Its current turnover exceeds EUR 700 million, with a significant proportion being reinvested in R&D every year. This is an area to which the company dedicates about 9 per cent of its workforce.
Whilst most research is conducted in-house, partnerships are also in place with specialist universities for particular projects, such as those for renewable energy systems. Innovation & R&D have been priorities for Bitron since it was founded in 1955. The company is particularly skilled in designing systems and components for integrating several functions into one multifunctional system, thereby optimising design and reducing costs. Each year Bitron dedicates around 7 per cent of its turnover to R&D to enable it to stay ahead of its competitors and to ensure that its global OEM customers retain their competitive edge. n
For further details of Bitron’s innovative products and services visit: www.bitron.net