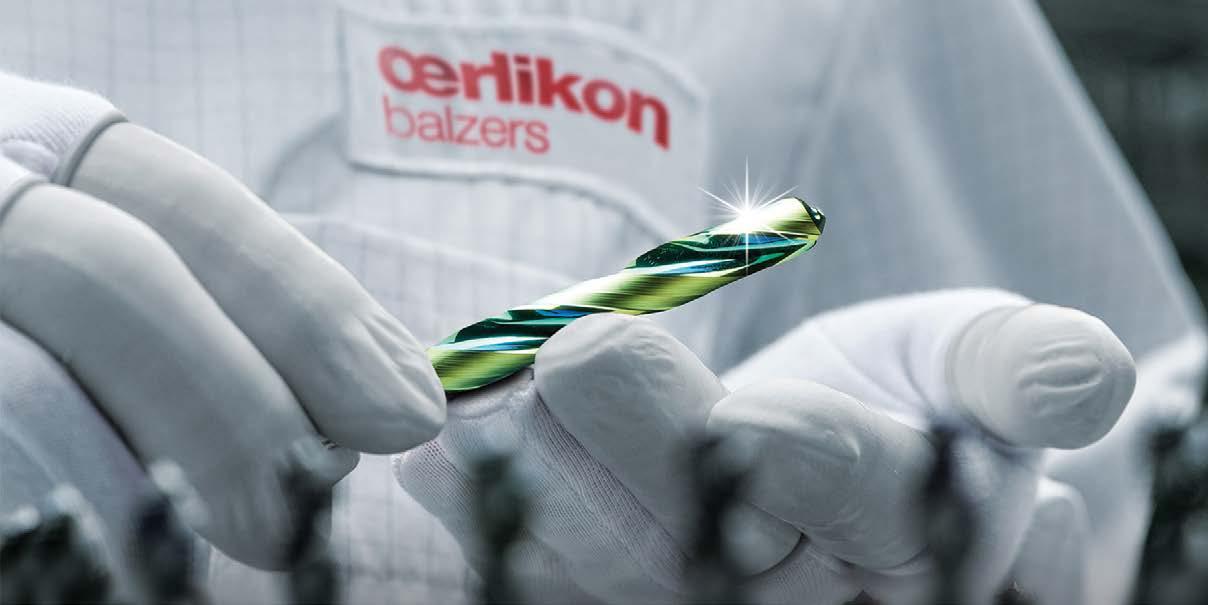
5 minute read
Supersonic surface solutions Oerlikon Balzers
SUPERSONIC SURFACE SOLUTIONS
Oerlikon Balzers is a leading global technology group with a mission to become the world’s number one provider of advanced surface solutions, as well as high-tech industrial materials and materials processing technologies. Philip Yorke reports on a remarkable company that is breaking down barriers and setting new standards in the industries that it serves.
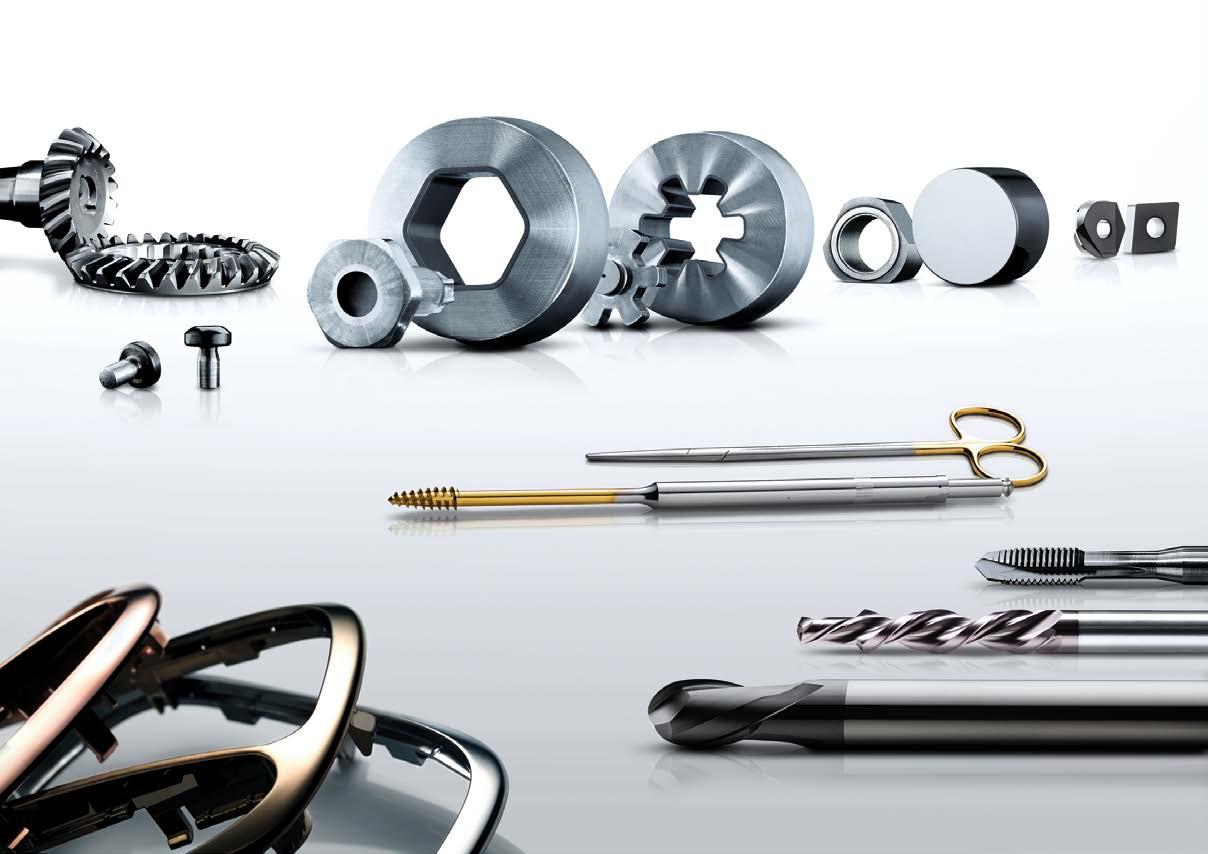
As a leading global technology and engineering Group, Oerlikon Balzers operates its business in two key segments: Surface Solutions and Manmade Fibers. The high technology group employs more than 10,500 specialists at 175 locations in 37 countries across the globe. In 2018, Oerlikon generated CHF 2.6 billion (EUR 2.39 billion) in sales and invested around CHF 120 million (EUR 110.3 billion) in R&D.
Oerlikon engineers materials, equipment and surfaces to high specification standards and provides a unique range of services in order to enable customers to obtain high-performance products and systems that offer them extended lifespans.
Drawing on its key technological competencies and strong financial foundations, the group is sustaining mid-term growth by executing three strategic drivers: addressing attractive new growth markets, securing structural growth and expanding through targeted mergers and acquisitions.
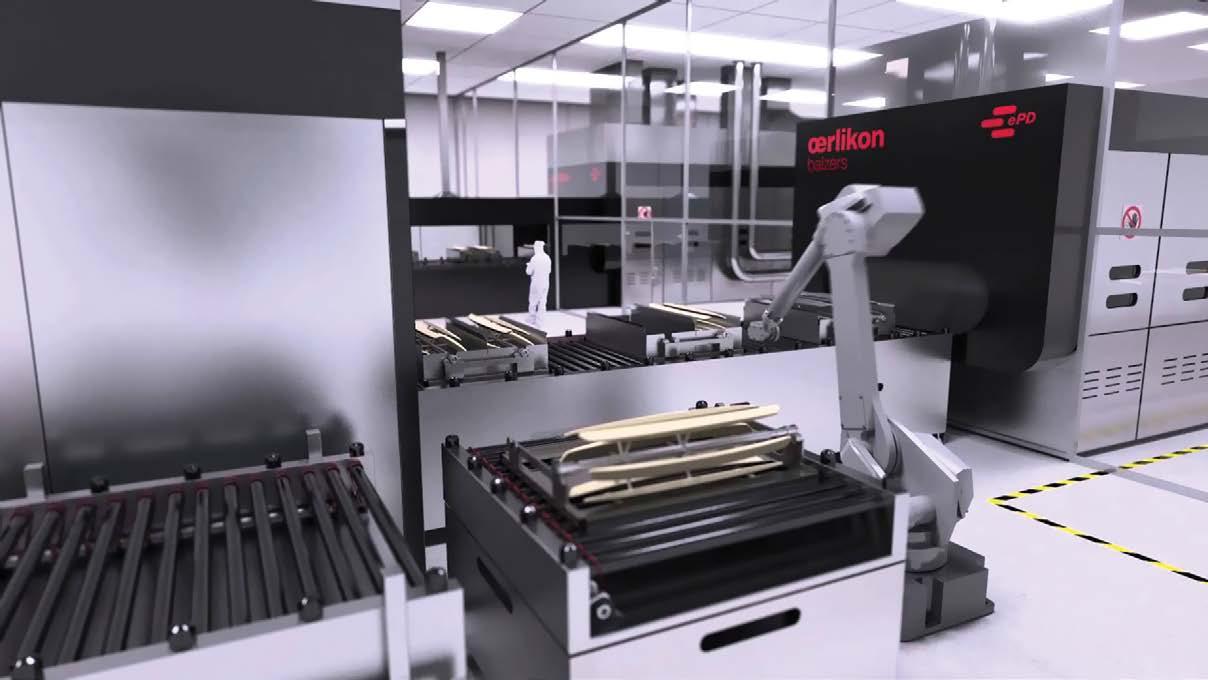
End-to-end aerospace solutions
On June 17th this year, Oerlikon AM and a leading aerospace company called MT Aerospace, created a strategic alliance to accelerate the use of additive parts in the aerospace and defence industries. The new partnership aims to bring greater efficiency and cost savings to the aerospace and defence markets by providing end-to-end solutions for their customers.
The two companies are important players in the aerospace market, and their combined expertise and sophisticated technical capabilities promise to help address the industry’s most difficult challenges, whilst improving efficiency and safety more economically.
The company’s “Additively Manufactured Components”, also known as 3D-printed or digitised components due to the precision with which they are made, are lighter and better designed than components made with traditional manufacturing techniques. Incorporating digital solutions in both air and space environments has already created new advances in the aerospace industry.
“With their bundled expertise, the two partner companies cover the entire value chain from component design and manufacturing to testing and qualification,” says Hans J. Steininger, Chief Executive Officer of MT Aerospace AG, a subsidiary of Bremen-based OHB SE aerospace company. “In this way, we can offer customers a ‘one-stop shop’ solution from product specification to the finished, qualified part.”
Driving the additive revolution
Additive manufacturing is seen as the next industrial revolution. Instead of using traditional techniques, casting, machining, joining and assembly, it allows complete freedom to create complex integrated shapes that are optimised for function, performance and cost.
“Through this partnership, we look forward to continuing to lead innovation and digitalisation trends in the aerospace industry by accelerating and scaling up the process from concept to operational delivery,” said Prof. Dr. Michael Süss, Chairman of the Board of Directors of Oerlikon.
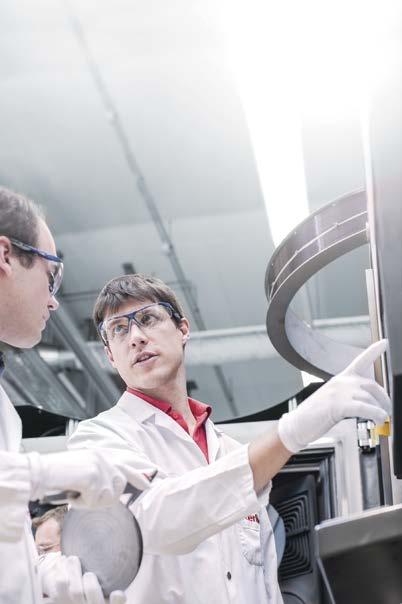
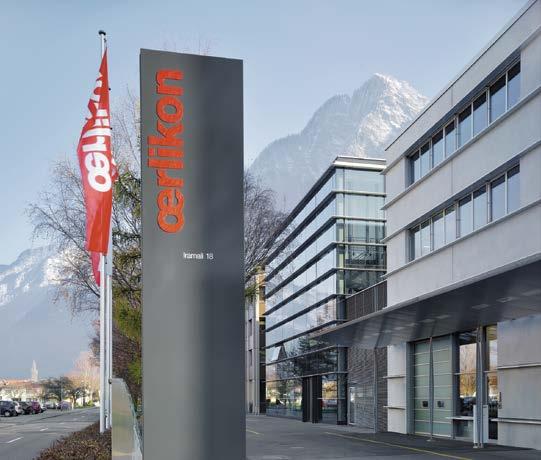
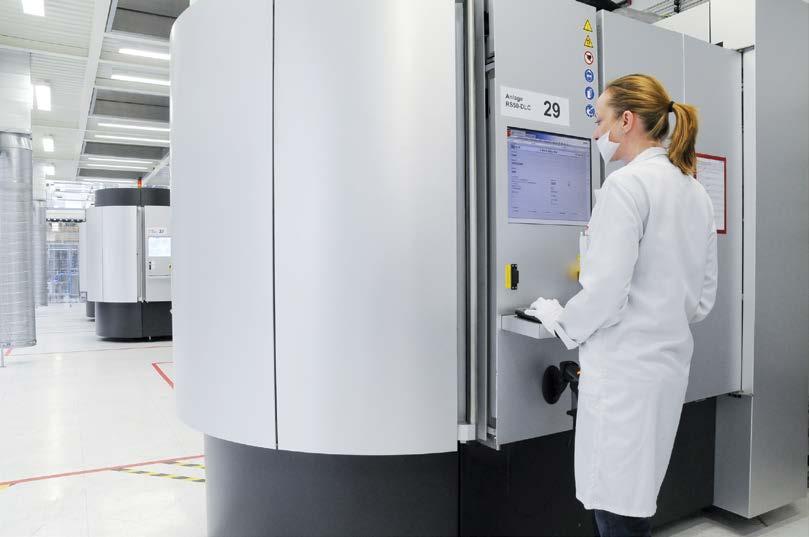
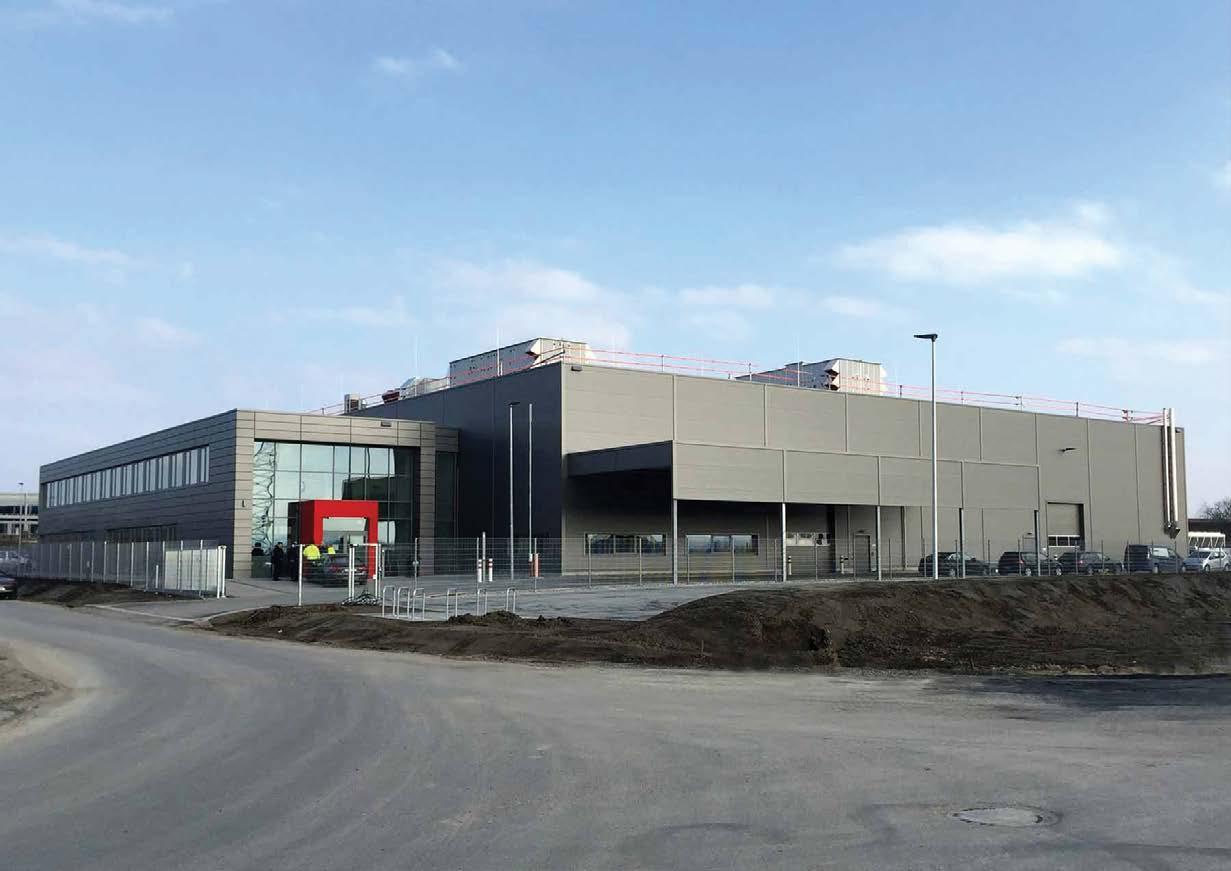
“To advance the application of additive manufacturing, collaboration with key players like MT Aerospace is essential. We are looking forward to bringing more additively manufactured parts to aerospace.”
By bundling their capabilities, Oerlikon AM and MT Aerospace are setting a path for their customers to unleash the full potential of additive manufacturing. The ability to optimally design specific parts or components provides obvious design and manufacturing benefits for all.
Focus on aerospace
Aerospace is one of Oerlikon’s most important, markets, where customers benefit from solutions that improve safety, aircraft power and efficiency. Oerlikon supports aerospace customers throughout the entire value chain with a portfolio ranging from coatings for cutting tools for the machining of aerospace components, wear protection for critical parts, abradable and thermal barrier coatings to powder and services for additive manufacturing processes.
Oerlikon’s advanced materials, functional coatings and process technologies boost performance and improve safety and fuel efficiency, while reducing emissions. These solutions not only meet customers’ precise technical requirements but are also super-efficient and cost-effective.
Unique innovation hub
Earlier this year, Oerlikon celebrated the inauguration of its all new USD 55 million (EUR 49.5 million) Innovation Hub & Advanced Component Production facility in Huntersville USA as part of its ongoing global growth strategy. The facility will serve as a cornerstone of Oerlikon’s Balzers’ additive manufacturing business in the US as well as acting as a springboard for its broader global activities.
The 125,000 square foot facility currently employs about 60 people and is fully operational. The additive manufacturing production facility is Oerlikon’s second location in North Carolina – the other site provides manmade fibers, in particular, carpet yarn systems.
Additive manufacturing uses high-tech tools, rapid prototyping and metal and plastic 3D printing to help customers create new components and transform production processes. With the help of Oerlikon’s additive manufacturing experts and the use of new technologies, companies can produce more complex and better performing components that are lighter and last longer, whilst also simplifying logistics and reducing the environmental impact.
This latest major investment is part of the USD 400 million (EUR 360 million), that the company has already invested in the US in the past five years. Oerlikon expects to invest another USD 200 million (EUR 180 million) in the next three years, adding some 400 new jobs. The Huntersville facility will continue to add jobs gradually and is poised for expansion as the business grows.
“This facility marks an important step in our investment strategy for growth,” said Prof. Dr. Michael Süss, Chairman of the Board of Directors, Oerlikon Group. “Additive manufacturing will play a decisive role in how industries and industrial processes will look in the future. We are committed to investing in this business and leading the industrialisation of this technology.”
“We are already working with customers in the aerospace, automotive, energy and medical industries worldwide, and we anticipate continued growth in those sectors, as well as in others,” said Dr. Sven Hicken, Head of Oerlikon’s Additive Manufacturing business. “We believe that additive manufacturing can transform production in many industries, and we are excited that our presence here allows us to better demonstrate those possibilities to our customers.” n
For more details of Oerlikon Balzer’s futuristic cutting-edge surface technologies and services visit: www.oerlikon.com
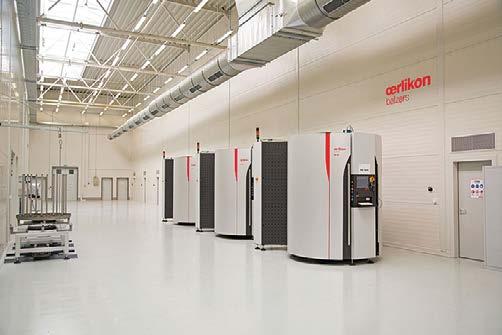
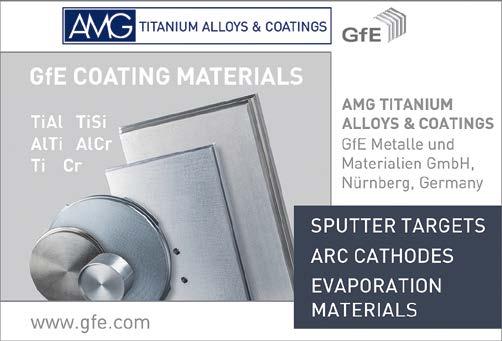