
7 minute read
3D printing - a breath of fresh air in a pandemic
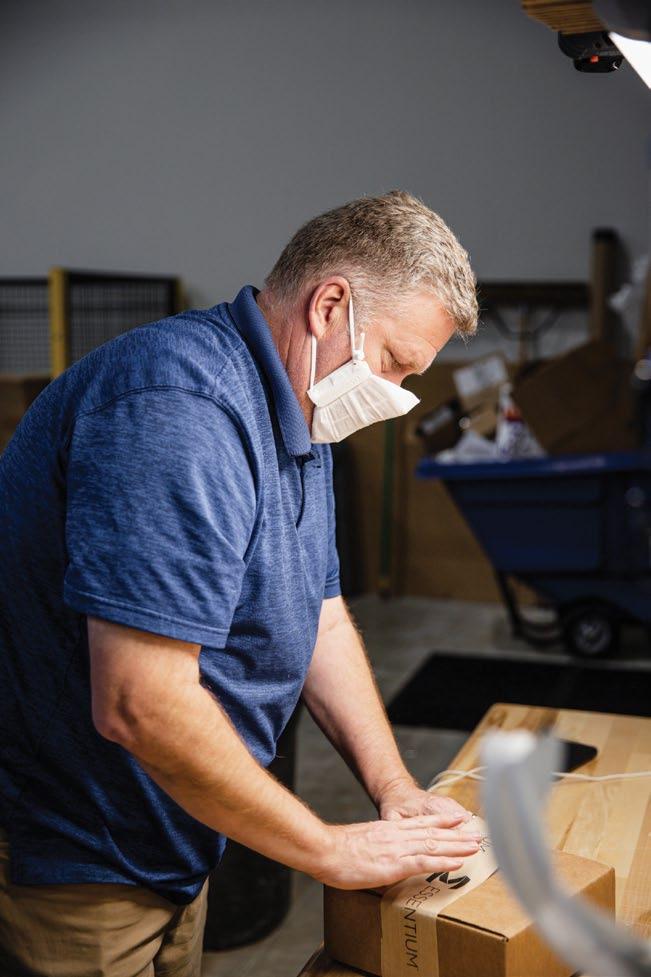
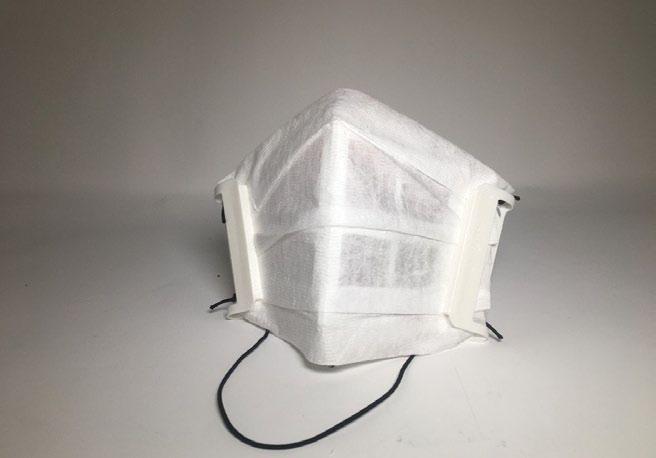
Industry Europe’s Ash Jones Spoke To The Boss Of The US 3D Printing Company About How The Coronavirus Outbreak Has Meant Shifting Production To Deal With The Pandemic.
With Covid-19 sweeping its way across the globe at an unprecedented scale, the effect it has unleashed on businesses is something nobody could have predicted. With this comes a particular danger to those on the frontlines, where the standard measures of social distancing cannot be met. 3D printing as an industry is still in its relative infancy; however, Covid-19 has provided unexpected room for innovation. Today we speak to Blake Teipel, the CEO of US 3D printing company, Essentium, on how they have shifted their production in the wake of a global catastrophe.
Industry Europe: Thank you for speaking to us, Blake. You’ve mentioned that Essentium’s manufacturing has shifted because of Covid-19. Could you possibly elaborate on that?
Blake Teipel: We have switched to a more abridged manufacturing role. We’ve been working with the FDA and others to test the design for community-use 3D printed PPE masks. There are a lot of these designs for M45-style masks, but really what we’re trying to focus on is something that is safe and effective, and they are printed using our classic TPU-74d. The main purpose of this is to preserve M45s solely for the medical profession and the folks on the frontline. Its design allows us to print it on a number of printers so we can get as many masks out there as possible.
Masks are a large part of this response effort, as seen in countries like Korea, Japan and China. There has been a large shift in public focus as to the efficacy of them in order to try and help contain the virus.
IE: In order to contain Covid-19, many countries have closed their borders which undoubtedly has an effect on businesses. How have these border closures affected Essentium?
BT: Border closures have affected production a lot. We have a global supply chain for many of our components, which has hindered us sourcing items such as printers. We may receive shipments of machines, but the logistic rates involved are often horrendous.
As far as manufacturing itself goes, companies will always be cautious for the first 6-8 weeks of the year. The early rise of Coronavirus didn’t help in this case, as we didn’t know whether or not it would blossom into anything problematic. When Covid-19 did strike, it proved to be a wake-
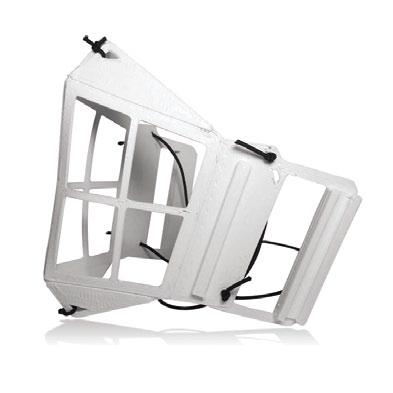

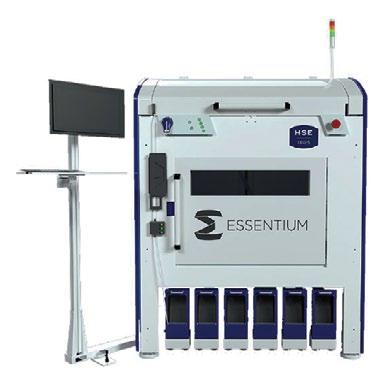
up call for many. Companies quickly realised that their supply chains needed to be more flexible and responsive – particularly in countries with high consumption.
The last few weeks especially have seen our business really take off, despite issues with sourcing, and the general perception of public health has changed also. For this reason, we’re trying to scale our business to meet these demands. All of these issues with supplies on top of then also having to adhere to social distancing policies – having half of our staff work from home – has had a profound effect on production.
IE: Have the issues of sourcing led to an increase in self-production on your end?
BT: Self-production in general has ramped up in the US. It’s difficult for us as a company to self-produce which still proves that we, and the US as a whole, don’t have a very robust supply chain for the manufacturing of capital equipment. Over the last 20 years, the US has outsourced 95% of that supply chain, which led to a loss of both the ability to craft the machines, but also the expertise to use them. This is where additive manufacturing could play a key role, as I see the general map of supply chains shifting following the Covid outbreak.
IE: Following from your point about maintaining social distancing and production issues, has Covid-19 had any effect on recruitment?
BT: Yes. We are cautiously growing our headcount with a priority on Essentium being a sustainable business. There has been a bit of a cash-crunch for our business and others, but we are seeing responses from every level of government with stimuli available to allow companies such as ours to lean forward. The question is: in the face of uncertainty, to do you rely on something safe, or do you try and innovate? Innovation is the best option provided you can afford to. We chose this route in an effort to help out those on the frontlines who have to work regardless of the situation.
IE: Could you elaborate on that?
BT: Yesterday, Essentium delivered our first small batch of PPE to the local police department. With the supply chains in turmoil they couldn’t get their hands on any masks, even for our local hospitals. There is an alarming rate of Covid-19 amongst police officers nationwide and so the equipment could help this number increasing exponentially. This also saves the M45s for hospitals as the police force do not come into contact with airborne versions of the disease to the same degree as healthcare workers. The last thing we need is a breakdown of social services because first responders are getting sick.
IE: Are you working with other companies to help increase the reach of your supplies?
BT: Yes, we are. I received three calls early on from companies in similar positions. For instance, one company in Indiana had pivoted their supply chain away from producing automotive parts to producing melt blown parts for use in the manufacturing of filtration devices. They requisitioned masks from us so they could integrate the filtration media with the masks. This has created this fantastic company-to-company relationship which allows us to work together to battle this pandemic.
Furthermore, the Governor of Texas has asked the National Guard to work with local businesses to help combat the mask shortage. To put it in perspective, in the state of Texas alone, there is a mask shortfall of 9 million, so the question is: what can we do to reduce this deficit?
The city government also put together a conference of local manufacturing companies, which put us in contact with a local injection moulding company who have access to six massive injection moulding machines here in town, with a branch containing 27 over in Long Beach, California. The company have had to lay people off because their response time is far too slow – 12 to 18 weeks to get tooling – so we’re working with them to help them with soft tooling to reduce their response time to about 10 days. That’s a significant turnaround.
There has also been a shift in fully moving to the digitalisation of the industry in response to Covid-19. We’ve set up a branch to allow people to 3D print themselves. This disease – although horrible – has stimulated a shift for many people into the digital age.
IE: What long-term effects do you think Covid-19 will have on the 3D printing industry as a whole?
BT: As mentioned, it almost forces people to fully embrace the digital age. There will be a tremendous amount of activity over the next few years for manufacturing supply chains to transition and prop up capabilities in areas where they didn’t exist before.
It will also help the 3D printing industry moving forward because we will see a massive emphasis on two things: network connectivity and improvements in QMS. I’m hoping Covid-19 will be a catalyst that will rapidly bring about a transition to Industry 4.0. Both supply chains and machines will need to be controlled remotely, machines will need to self-schedule and job queue and things like that. On the quality management front, the real challenge is if 3D printing will be a front for this type of manufacturing, the quality management system will have to allow for the production to take place quickly, effectively and cheaply.
The current situation is tough and the best thing to do is to always have a technologically progressive mood to increase the space for innovation. We have a strong focus on culture here at Essentium, and having a strong focus on the people in your company will give them the resilience needed to make it through situations such as this. n visit: https://essentium3d.com/