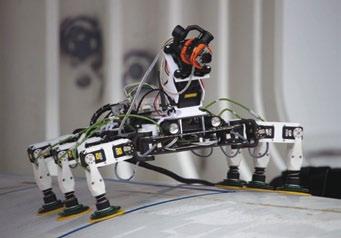
4 minute read
Technology spotlight Advances in technology
NeWS
TECHNOLOGYSpoTlIghT
Advances in technology across industry
bladebug 6-legged repair robot takes its First walk offshore
Last month, just off the Scottish coast near Fife, BladeBUG, a six-legged inspect-andrepair robot, took its first blade walk at ORE Catapult’s 7MW Levenmouth Demonstration offshore wind turbine.
BladeBUG is said to represent cost reductions of as much as 30% on lifetime blade maintenance undertaken by rope-access technicians. ORE Catapult has forecasted that for nextgeneration turbines, these savings could reach up to 50%.
Maintenance costs have long been an area of particular concern for offshore companies, with faster tip speeds and sea conditions combining to create significant damage to blades over time.
The BladeBUG robot is a £1 million (€1.12 million) collaborative project, funded in part by Innovate UK. The aim is to develop a robot capable of inspecting wind turbine blades for cracks and other damage, transmitting the data back to shore and resurfacing the blades, by the end of next year.
This was the first time BladeBUG was tested in real-world conditions, having previously been demonstrated on the vertical training tower at ORE Catapult’s National Renewable Energy Centre in Blyth. The walk has proven the six-legged robot’s ability to carry out lengthy deployments.
The demonstration saw the robot take a 50-metre walk on a vertically-positioned blade. The trial showed the BladeBUG’s ‘perfect’ vacuumpacked feet adherence to the turbine blades in offshore conditions, as well as its ability to navigate the curves of the blade, and transmit blade scans and a video feed to the technicians onshore.
ORE Catapult operational performance director, Chris Hill, hailed BladeBUG’s technology was a ‘potential game-changer’.
“I consider BladeBUG’s first walk at Levenmouth as offshore wind’s ‘moon walk’ – a historic milestone in the industry’s evolution. Robotics are here to stay, and they will be an essential ingredient to operating ever-expanding wind farms, deeper-water sites and faster, bigger turbines in the coming years,” said Hill.
BladeBUG CEO Chris Cieslak said: “In little over a year we have gone from designing and testing our first prototype, to taking our first tentative steps with our Mark I robot, to now seeing the BladeBUG robot walk along the blade of an actual offshore wind turbine. We cannot wait to perform further trials and demonstrate the capabilities further offshore.”
BladeBUG is a key part of the £4.2 million (€4.68 million) MIMRee project, the goal of which is to develop a fully autonomous inspect-and-repair system for offshore wind farms. The robot will work together with an autonomous vessel and a team of drones, using a robotic arm to clean and resurface damaged blades. The final MIMRee tech trials are scheduled to take place in mid-2021. Learn more at: www.bladebug.co.uk
KLM & TU Delft’s Flying-V Future Plane Takes First Test Flight
A rendering of Klm Royal Dutch Airlines’ Flying-V aircraft. Photo: edwin Wallet, Klm
Ascale model of the Flying-V, a new aircraft design that Dutch national carrier KLM hopes could revolutionise air travel, took its first successful test flight earlier this week in the skies above Germany.
Developed after two years of collaboration between engineers from the Delft University of Technology in the Netherlands and KLM, the Flying-V integrates several formerly separate parts of a traditional aircraft in its one piece fuselage and wing structure including the cargo hold, passenger cabin and fuel tanks, forming a V-shape.
The improved aerodynamic design enables it to use present infrastructure at airports, such as runways and cabins, whilst burning 20% less fuel than today’s most advanced aircraft, the Airbus A350 and Boeing 787 Dreamliner.
For the test flight, the team built a scale model of the Flying-V, three metres in width and weighing 22.5 kg, which required the pilot to take-off, perform a number of test manoeuvres until the battery was almost empty, and then land.
In a statement, project leader Dr. Roelof Vos said: “One of our worries was that the aircraft might have some difficulty lifting-off, since previous calculations had shown that ‘rotation’ could be an issue. The team optimised the scaled flight model to prevent the issue but the proof of the pudding is in the eating. You need to fly to know for sure.”
The statement also added that the model was able to take off easily after it reached 80 km per hour, but there was still more work to be done on the landing, which it described as “slightly rough”.
The Flying-V’s design requires it to land in a similar fashion to the Concorde, with its nose high, which means the landing gear needs to be extra long.
The team at Delft University aim to make air travel more sustainable and are also looking at ways in which fully electric and hybrid propulsion systems could be utilised to lower carbon emissions. Visit: www.klm.com
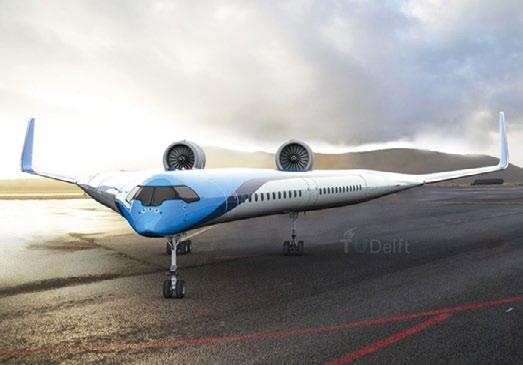