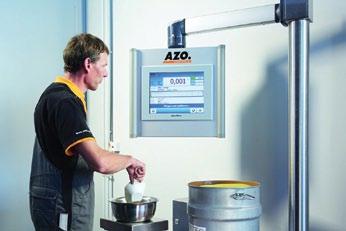
4 minute read
The experts in raw materials handling AZO
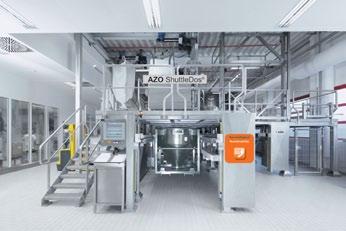

the expeRts in Raw MateRials handling
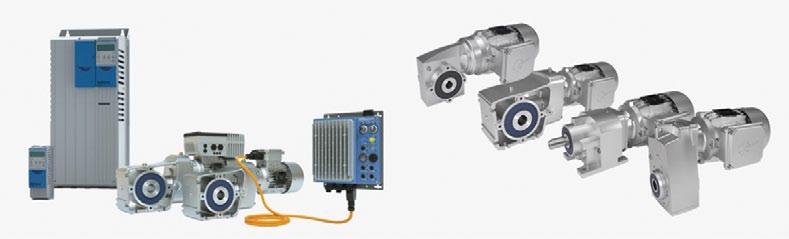
In 2019, Germany’s AZO Group celebrated 70 years of industry-leading innovation in the automated handling of solid and liquid raw materials. Now it is pioneering the digital transformation of its business
Last year, Germany’s AZO Group, the world leader in automated systems for handling of raw materials, announced the merger of its subsidiary company Azo Controls with Azo GmbH KG
“This is an important milestone for the AZO Group on the path to digital transformation,” the company explained. “With the benefit of leaner organisational structures, we will be able to improve the efficiency of work processes across all departments, including those in engineering. It will enable us to further boost productivity and the standard of service.
“We believe that this is the right time and the right way to broaden AZO’s scope to meet the needs of our customers and to face the challenges of the future. A mechatronic approach necessitates closer integration between process engineering and control systems in order to improve the efficiency and productivity of our plants even further. We welcome the challenge of digital transformation, with the goal of creating real added value for our customers.”
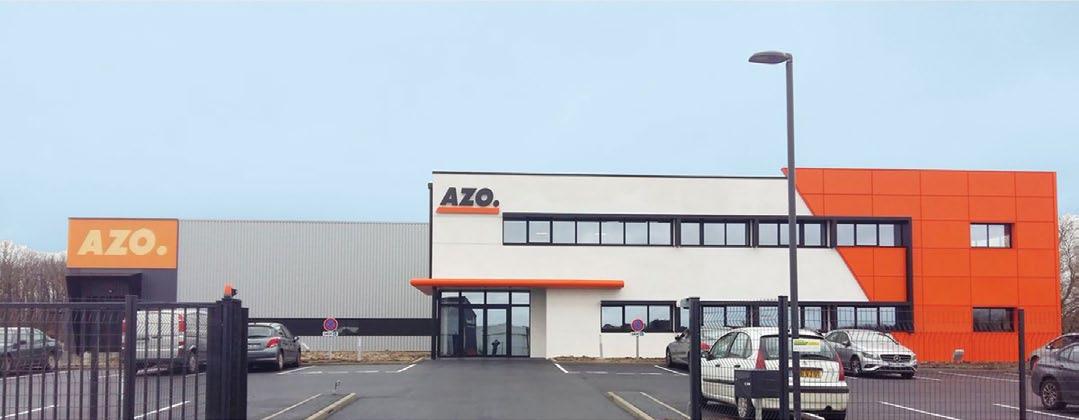
Anniversary celebrations
Later the same year AZO celebrated the 70th anniversary of its founding in 1949, when Adolf Zimmermann began building flour mills in a former sheep-pen in Osterburken. Since his development of the Pyramidal grain cleaning machine and the Triumph centrifugal flour sifting machines in the 1950s, AZO has assumed a pioneering role in the automation of raw materials and processes in the food, pharmaceuticals, plastics and chemicals sectors. It has initiated game-changing developments in the handling of bulk materials, in pneumatic conveying systems and in automatic mixer feeding.
The company’s Open House celebrations in September saw its premises transformed into a huge festival area where more than 7000 visitors filled the Osterburken facility, a space where forklifts and trucks usually operate. The electrical production, the customer centre, the bulk materials laboratory, the assembly hall, the sheet metal centre and the production centre were all open to visitors. Using the legendary AZO cyclone screener, a journey through time was presented from the founding of the company up until today. The control technology also looked back on the beginnings of automation with a time travel consisting of pictures and hardware. The comparison between a technical drawing on the drawing board and the digital 3D VR glasses, through which visitors could run through complete AZO systems in virtual reality, also showed the huge development in 70 years of company history.
All from a single source
Today the AZO Group is one of the world’s most experienced companies in the automated handling of raw materials. With more than 1000 employees, it delivers solutions for production processes in the food, pharmaceuticals, cosmetics, chemicals and plastics sectors. The company’s engineers are experts in the physical analysis of raw materials, engineering, process engineering, plant engineering, control engineering and automation, and digitalisation.
With four plants in Germany and operations in France, Belgium, Russia, USA, China and Thailand, AZO’s capabilities range from engineering and the supply of individual components to the construction of complete turnkey plants, automation, installation and comprehensive after-sales service
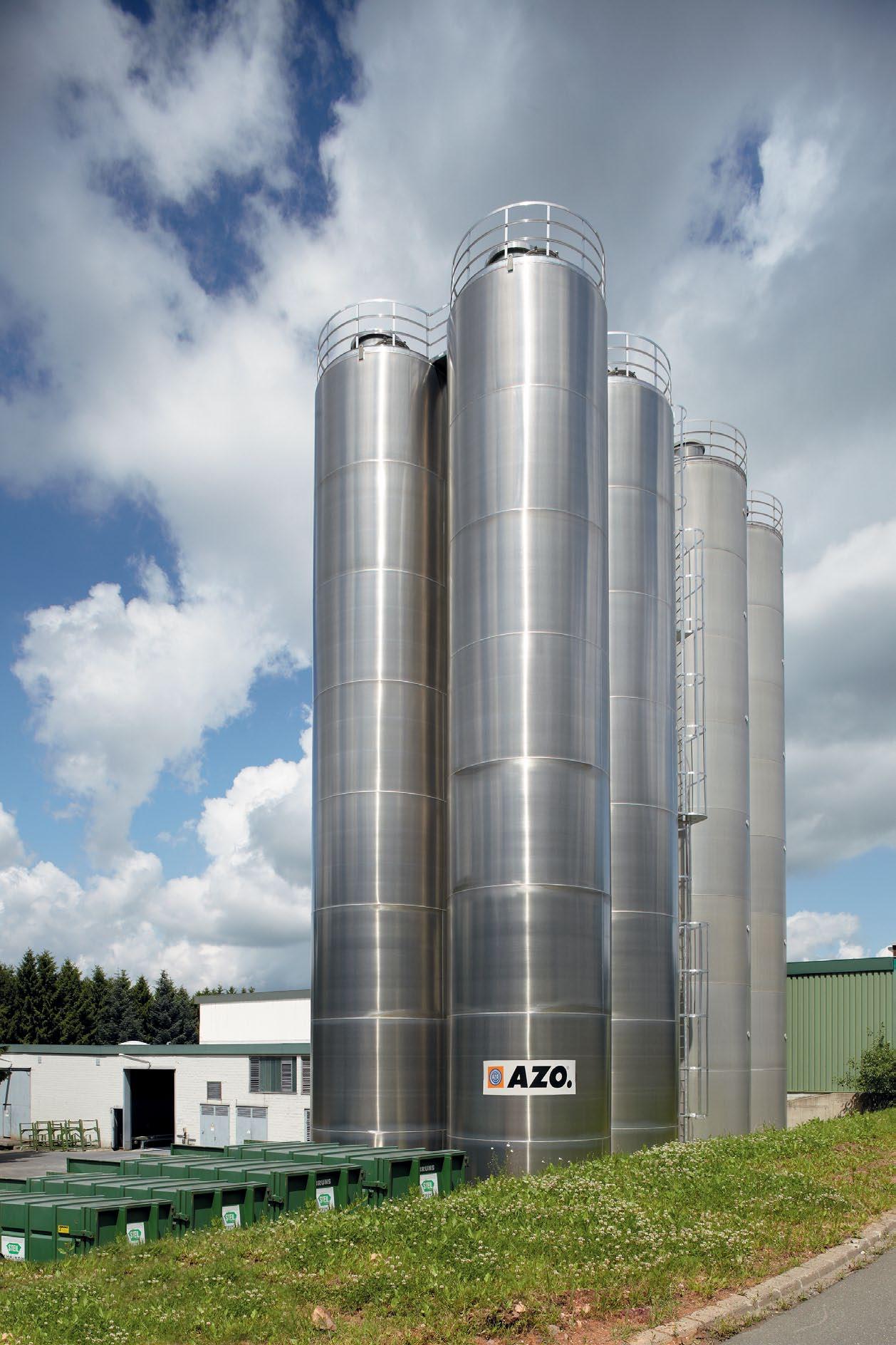
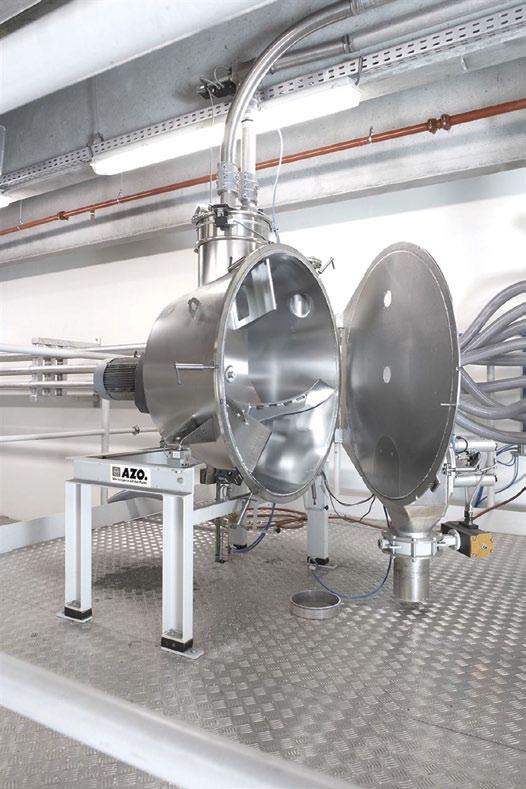
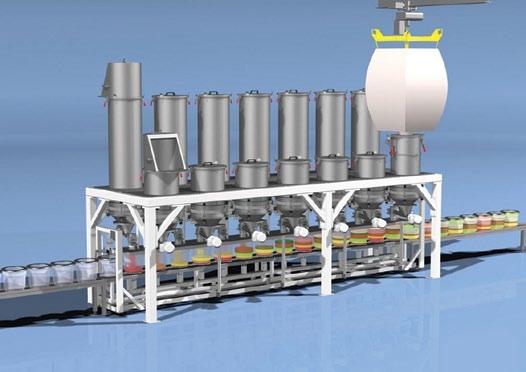

Its customers are thus able to get everything from a single source – from individual components for storage, discharge, screening, conveying, dosing and weighing of raw materials, through pneumatic conveying systems, screeners and bulk containers, to innovative systems for dispersion, mixing and homogenisation of liquid and semi-solid products, right through to turnkey solutions.
unmatched expertise
AZO’s expertise begins with the physical analysis of raw materials. Each raw material has its own unique properties. And even the same raw material can behave completely differently in different locations and under different circumstances. Solid knowledge about the properties of the products being processed and a wealth of experience in data evaluation and linkage are therefore much sought after when it comes to designing plants for the automation and logistics of raw materials. For decades, AZO has been analysing the different raw materials in its bulk solids laboratory and recording all the relevant data for automated handling in an extensive database.
Since no one project is the same as another, AZO offers customised solutions. It supports its customers in pre-engineering, planning new plants and in the expansion and refurbishment of existing plants. It conducts feasibility studies and works on viable proofs of concept to arrive at the optimum solution for any project.
Smart solutions
From consulting to implementation, from sensor technology to the commercial production planning phase, AZO’s plant engineering, process engineering and automation dovetail seamlessly to create reliable, comprehensive solutions with no interfaces and yet the utmost in connectivity. Starting with the creation of a digital twin via simulation and virtual reality, AZO can also build up a digital map of a customer’s plant that can be accessed virtually before the physical manufacturing begins. Thanks to data recording, visualisation and analysis, it also adds value to any production system during the operating phase. Smart data, a spare parts platform and augmented reality are integral components of the AZO offer. n
For more information, visit: www.azo.com
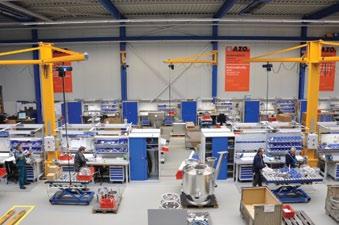
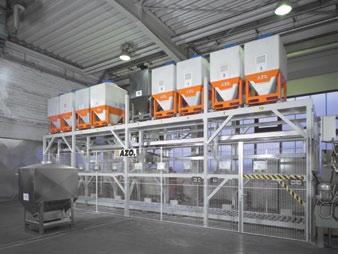
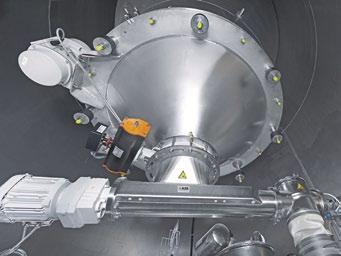