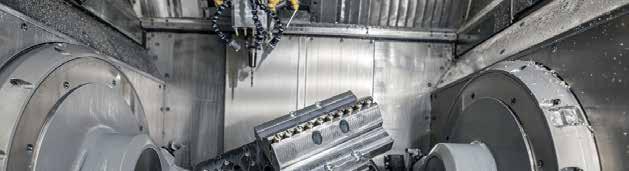
20 minute read
MACHINERY
FAMILY BUSINESS FINDS BENEFITS FROM SINGLE MACHINERY SUPPLIER
KNS Metals is one of Victoria’s fastest growing family owned and operated sheet-metal companies. The company was founded in 2014 by Kamal Singh, who had been working in the sheet-metal industry for over 30 years, together with his wife and two sons. Eldest son Amal is now General Manager of the company.
Advertisement
In 2014 Kamal Singh spotted an opportunity in the marketplace and with extensive experience believed that it was the right time to go it alone. The business has grown rapidly over the past several years and it now operates with around 10-15 staff.
KNS Metals specialises in custom programming and design fabrication for both commercial and residential customers. Commercial is the backbone of the company, which provides 95% of the business, while residential makes up the remainder. Their other services include CNC turret punching, laser cutting, pressbrake bending and welding. KNS operates Australia-wide but most of the clients with which it deals directly are based in Victoria.
Kamal and Amal believe that their business has been successful due to their knowledge of the industry and outstanding customer service. While working in the business, Amal has also been completing his electrical engineering degree. The and massively expanded the company’s cutting capabilities.

knowledge he has gained from this has been beneficial in enhancing the company’s overall expertise.
“Our past experience as well as our critical and logical thinking helped a lot; and with this knowledge we can give customers great lead times and great quality products,” says Kamal.
Most of the company’s work comes through word-of-mouth. As such KNS Metals has never had much need to advertise, however the company is now expanding into social media.
Kamal first encountered Applied Machinery when he purchased an Amada AE-2510 turret punch. When the company required another new machine, Applied Machinery was the first port of call. “We had dealt with Applied previously so it was only natural for us to do business with them again,” Kamal explains. “We were looking for the right machine and after discussion with Applied found that the Yawei pressbrake they offered was just what we were after.”
Applied Machinery helped KNS Metals to set up the machine when it was delivered and this vital help impressed the company. “When we moved to our new factory, Applied came in after-hours and helped us set up over just one weekend,” says Amal. ”We packed-up on Friday and
The Yawei fibre laser has a number of clear benefits: “We have found that the fibre laser is consistent and the speed and accuracy of cutting is brilliant,” says Amal. The advantages of the machine have already had a direct impact on the service provided by KNS. “Our lead times have greatly improved as a result of having the machine,” says Kamal. “We feel that we have taken back control of certain elements of our business,” he adds.
we were back working on Monday, that’s how much of a help they were,” Kamal explains.
Furthermore, the subsequent service and backup KNS received from Applied has cemented the relationship between the two companies. “We have a great working relationship with Applied and we are certain that will continue into the future,” says Amal.
The new pressbrake has had a big impact on the company. “We are very pleased with how the machine’s gone so far,” Kamal says. “We will likely get a second one as we anticipate further growth in part thanks to the effect the pressbrake has had,” he adds.
KNS had previously been outsourcing a number of jobs due to a limitation on laser-cutting resources. However, it soon became apparent that it needed its own in-house laser-cutter that would be able to perform high-quality precision cuts.
KNS went to Applied again and after reviewing Yawei’s extensive range of fibre lasers purchased an HLF15303kW model - Amal and Kamal were particularly impressed with the machine’s quality components, such as the Siemens controller. Importantly, this purchase allowed many of those previously outsourced jobs to come back in-house Staff have also found the machine easy to use: “We’ve had the machine for 3-4 months now and our staff are very happy with its ease of use and the way in which it operates,” says Amal.
The company is also reassured that Applied is always on hand to assist. “Occasionally, when we require additional assistance and technical guidance with the fibre laser, Applied has been available to help us right away; we are grateful for that support,” he adds.
“Laser cutting has become a big part of our business in recent times so the machine was a vital purchase. We are already booked out for the next 6 months because of the work we are now able to perform with the Yawei,” Kamal explains.
Much like the pressbrake, the success of the fibre laser has also meant that a second machine is likely to come at some point in the future.
Amal and Kamal would like to keep on growing and expanding the company’s customer base. “We are very happy with our growth over the past few years and in the short-term we will probably purchase another Yawei guillotine and turret punch press,” says Kamal.
Their growth and success in such a short time has meant KNS Metals will probably have to upscale yet again: “We will probably move to larger premises because we realise our current factory is not as big as what we wanted!” they conclude.
Applied Machinery 03 9706 8066 www.appliedmachinery. com.au
World class performance, without the price tag. That’s Applied thinking. NOW THAT’S APPLIED
With its extreme accuracy, speed and consistency of cut, combined with very low operating costs, the new Yawei HLF fiber laser is the perfect way to take your business to the next level. Dollar for dollar, the new HLF is in a league of its own, opening up possibilities for companies all across the laser cutting sector; from start-ups through to full production, 3-shift H I G H S P E E D P R O C E S S I N G S I M P L E T O U S E E X T R E M E A C C U R A C Y




With a quality German built Precitec auto-focus cutting head, IPG laser source, Siemens 840DSL controller and a fabricated, stress-relieved fully annealed frame it really is a cut above Precision sheetmetal processing solutions.
Fiber Lasers • Turret Punch Presses • Pressbrakes • Guillotines • Automation
DRILL BIT MAKER HAMMERS HOME THE IMPORTANCE OF SUPPORT

While the Western Australian mining industry has become synonymous with boom and bust cycles of investment, one multinational company serving the sector is increasing its local manufacturing output to satisfy WA miners' continuing demands for drill bits.
With its headquarters in Shannon, Ireland, Mincon Group manufactures on a truly global scale. This includes operations in South Africa, the USA, Canada and Australia.
The company’s growth over the past five years has been spectacular, with multiple acquisitions worldwide.
However, it maintains a philosophy of keeping full control over every crucial step of the manufacturing process, for each product in its range. This approach allows it to meet local demand and adapt to customer requirements.
The Mincon Rockdrills manufacturing facility in the Perth suburb of Welshpool is part of the global Mincon organisation that spans five continents, producing almost everything for drilling rock "from the drill rig downwards".
The Perth facility has specialised in hammer drill bits for the exploration market for some years, and is still the company's centre of excellence in that market.
More recently, though, it has expanded into the production of the physically larger production drill bits demanded by iron ore miners who are in full production. And in doing so, it has begun to manufacture products in Australia that have previously been imported from Mincon Rockdrills USA.

This expansion has coincided with a change to the makeup of the machine shop at Welshpool.
A reduction in the level of support provided by the company's previous preferred machine supplier led the Mincon team to investigate alternative suppliers. And with other manufacturing operations within the group favouring the Doosan brand of CNC machine tools, the decision was made to investigate the Korean machine maker’s range, available throughout Australia from Hare & Forbes Machineryhouse.
Mincon Australia Group Technical Manager Carl Blundell explains: “You can’t manufacture on this scale without proper back-up.
“Our Shannon headquarters machine shop gets great service from the local Doosan agent, and so do our colleagues at Mincon Rockdrills USA. is currently making. “But there’s more to come,” he says alluding to future product developments.
“Hare & Forbes supports our machines locally from its Perth office, so we don’t have to wait for support if something does go wrong. And that keeps our downtime to a minimum.”
The first arrival was a Doosan DNM6700 vertical machining centre with a rotary table. This was followed swiftly by a large horizontal machining centre. The Doosan NHM8000 has twin rotary tables on each pallet.
The latest additions to the machine shop have been: a Doosan Puma 5100LYC horizontal turning centre with extra-large 275mm spindle bore, a pneumatic chuck and a 1000psi coolant system; and Doosan Puma 3100XLY CNC lathe with programmable steady rest and a similar 1000psi coolant system.
Blundell admits that the extra-large bore on the Puma 5100LYC is something of an “overkill” for the bits that Mincon

The drill bits are manufactured from an alloy steel, perhaps surprisingly a material that originates from the aerospace sector. The barstock (and in some cases forgings) is pretty easy to mill in its raw state, but becomes considerably harder after heat treatment.
However, Carl Blundell confirms that the Doosan mills have more than enough power to deal with the semi-finished heattreated drill bits.
One feature of all the Doosan machines at all the Mincon facilities worldwide is the use of the same Fanuc CNC controller, which provides a uniform programming and control environment that makes it easy for operators to master multiple machines.
So does the company share programs between manufacturing operations? Unfortunately, the answer is no, even when a design like a production drill bit moves from the USA to Australia. “That would be an ideal situation,” says Carl Blundell ruefully, “but the products are not identical – the Americans are Imperial, but we of course are metric!”
Overall, the four Doosan machines have proved their worth at Mincon Australia. Carl Blundell describes them a “value for money and proven to do the job.”
But it is the support from Hare & Forbes that is the deal-clincher, and the true reason why, as Blundell says, “any future machine purchases are likely to come from the same source.”
Mincon Rockdrills www.mincon.com
A family-owned Australian manufacturer is thriving in outer Eastern Melbourne and doing so by embracing many of the concepts of advanced manufacturing within a traditional market.
W Granowski has been a pioneer in surface preparation and finishing technologies, and supplies abrasive blast cleaning and peening equipment, degreasing equipment and associated parts and consumables for a wide range of industrial applications.
For a company that is just about to celebrate its 92nd birthday, it certainly has a wealth of experience to fall back on. However, there is one part of the company’s reputation that is occasionally overlooked.
“People tend to forget that we are actually equipment designers and builders,” says Managing Director Caitlin Granowski. “Which is odd considering we’ve been designing and manufacturing our equipment here in Melbourne for more than 90 years.”
As a company, Granowski prides itself on creating robust innovative engineering solutions and today accomplishes this with the use of advanced engineering techniques such as digital manufacturing, robotics, optimisation analysis and design for manufacture. “It’s always an exciting time when a customer presents us with a challenging application,” says Caitlin Granowski. “It might be that they want to turn a 6m-high blast machine into a containerised ‘appliance’. Or they want to precision-blast an exotic material such as carbon fibre. We’re currently working on a delicate deburring application for lightweight satellite parts. As an engineering company, we thrive on these design challenges.”
The company works with its customers so that its equipment can be delivered interface-ready so to be easily integrated into the user’s production flow – whether the interfaces are for control, data acquisition, work handling or robotics.
Ultimately, though, it is experience that Caitlin Granowski considers to be the company’s greatest strength. “Over decades, we’ve designed and manufactured thousands of machines, across virtually every industry segment, for both the domestic and overseas markets,” she says, adding “and with 95% of our customers providing repeat business we pride ourselves on the quality of our equipment and the level of customer satisfaction and service.”
It helps that the company is technology agnostic, producing both wet and dry air blast cabinets, air and airless
MAGNETIC TOOLS BRING PLATES TOGETHER FOR WELDING
When butt-joining steel plate, getting the surfaces properly aligned for welding can be a problem. The traditional method involves temporarily welding a fulcrum arch to one of the plates and inserting a bar to lever the plate to a level position. After welding, the arch has to be broken or ground off and the surface refinished.
Mag-Mate Mag-Pry sheet aligning tools reduce this time-consuming procedure to a matter of seconds by holding the plates in perfect alignment at the flick of a switch (as shown in this video). (https://www.youtube.com/ watch?v=tGXpUrK90Rc)
Available in two different sizes, each Mag-Pry device combines a strong pry bar with a powerful on/off permanent magnet clamp and its own fulcrum point to enable effortless and time-saving alignment of butt-joined steel.
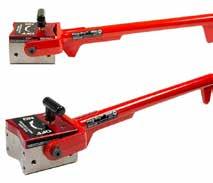
These alignment tools, available in Australia from Serpent & Dove, are suitable for all plate and seam work, including under foot, on vertical surfaces and even overhead.
Serpent & Dove - Applied Magnetics 02 9971 7577 www.serpent-dove.com

This airblast equipment for blasting the surface of carbon fibre wheels incorporates a robotic arm
(wheel) blast equipment and degreasing machines. This means that it can approach a customer’s surface preparation application without preconceptions and produce the most suitable integrated solution for each requirement.
These solutions evolve from the WG range of custom-built blast and degreasing systems, all of which are manufactured to
solve a specific problem, and encompass the full spectrum of surface preparations from fettling, deburring and descaling to polishing, etching, peening and degreasing.
W Granowski 03 9729 4333 www.granowski.com.au
REQUEST YOUR FREE STAMPINGS & WASHERS CATALOGUE & CALENDAR! Your Stamping & Washer Specialists
3D-Printed Prototypes Available

bokers.com +16127299365 sales@bokers.com
The JEKRAN XM series Waterjet is rich with technology but at the same time extremely user friendly, The X-MW series machines are equipped with many standard features such as built-in material databases, variable soft piercing function for brittle materials, auto garnet delivery system and laser light sheet positioning assistance to name a few.

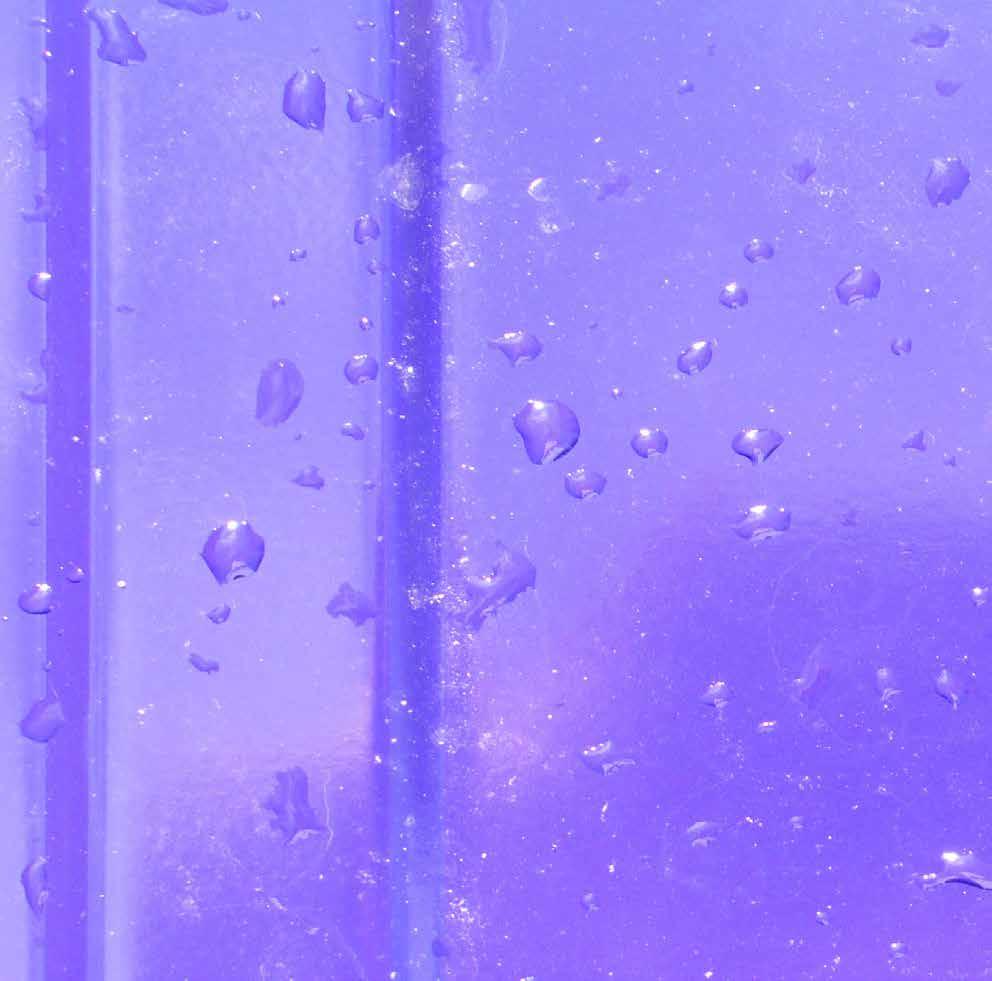

The powerhouse of the X-MW machine is the German built direct drive pump which outputs 3,800bar / 55,000psi at 100% duty cycle whilst maintaining unrivalled energy savings. These machines are manufactured in Europe and are unbelievably good value.

High Pressure Pump The heart of the system is the highly advanced German built variable speed direct drive pump, creating up to 3800bar / 55000psi pressure at 100% duty cycle using the standard 0.35mm orifice. The pump boasts a unique filtering system making it suitable for tap water quality saving you money on additional reverse osmosis equipment and maintenance costs.



Bulk Garnet Delivery System Equipped with a PLC controlled automatic bulk garnet feeding system the machine utilises unique technology which allows you to fill the bulk hopper without stopping the cutting process, combined with a garnet low-level sensor maximum production efficiency is achieved. The hopper capacity is 80L / 180kg.

CNC Control The CNC controller is a 15” Industrial Touch panel which has been ergonomically designed for users in both standing and sitting positions. Using large icon based intuitive CNC software, most operators can be well conversant in using the machine with a single day of training. The CNC and accompanying offline software accept DXF, SVG, HPGL, Vector files as well as G-Code files. Auto nesting of parts can be achieved for material sheet utilisation. Energy Efficiency The variable speed directly driven pumps on the X-MW series distinguish themselves in comparison to intensifier pumps with a much higher degree of power efficiency of up to 30% more efficient than intensifier pumps. CNC Control The CNC controller is a 15” Industrial Touch panel which has been ergonomically designed for users in both standing and sitting positions. Using large icon based intuitive CNC software, most operators can be well conversant in using the machine with a single day of training. The CNC and accompanying offline software accept DXF, SVG, HPGL, Vector files as well as G-Code files. Auto nesting of parts can be achieved for material sheet utilisation. Energy Efficiency The variable speed directly driven pumps on the X-MW series distinguish themselves in comparison to intensifier pumps with a much higher degree of power efficiency of up to 30% more efficient than intensifier pumps.
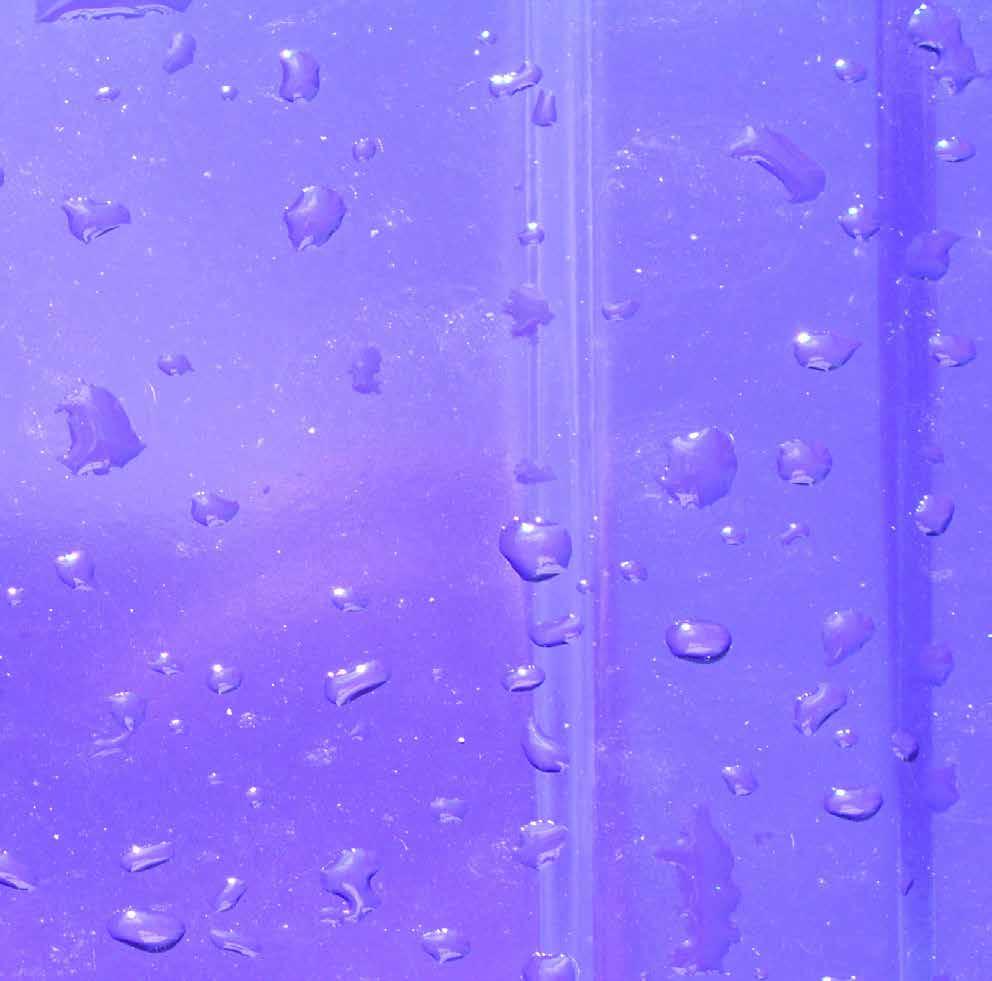

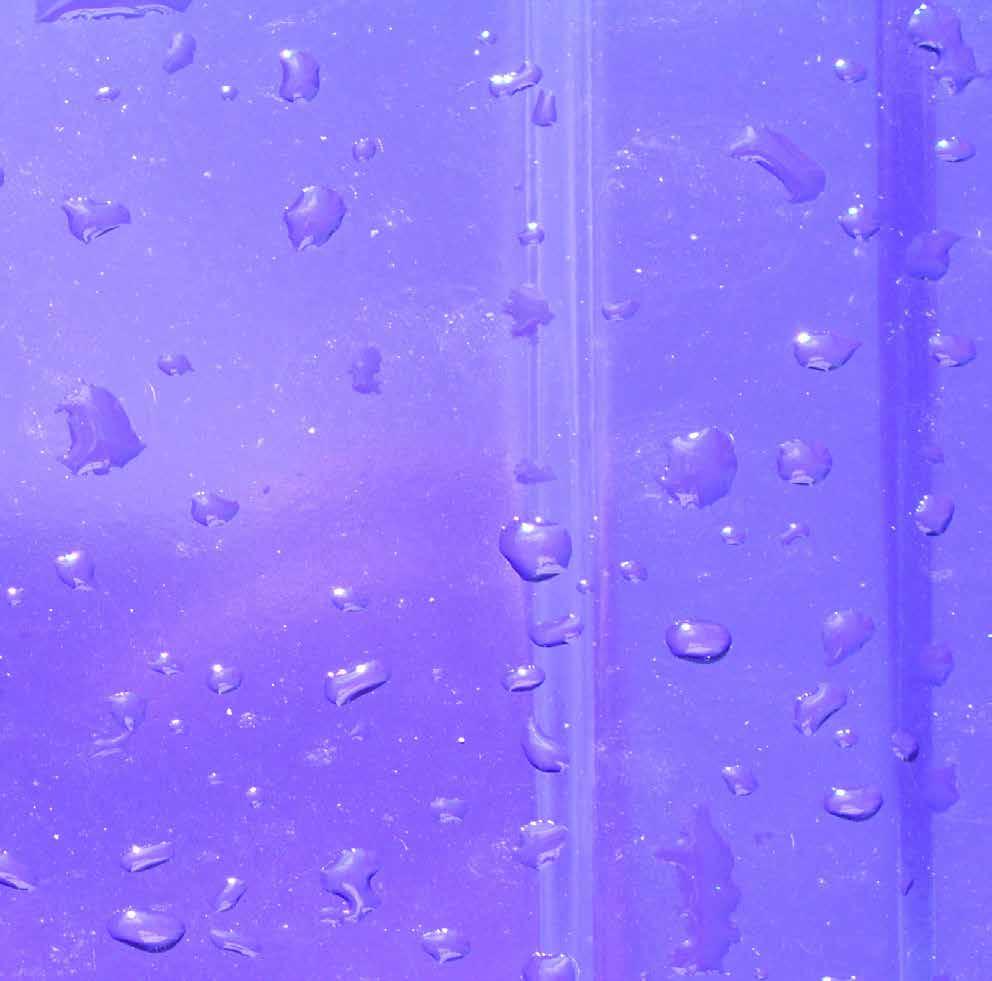

Material Database The material database makes the machine suitable for any user. Cutting parameters are all stored in the CNC and loaded accordingly. This means that correct parameters and cutting configuration is always set and an optimum cut is guaranteed. Material Database The material database makes the machine suitable for any user. Cutting parameters are all stored in the CNC and loaded accordingly. This means that correct parameters and cutting configuration is always set and an optimum cut is guaranteed.
Frame / Chassis The chassis is fully welded to improve strength and rigidity, making the whole composition robust. This is especially important after prolonged cutting times when heat can distort the construction. Frame / Chassis The chassis is fully welded to improve strength and rigidity, making the whole composition robust. This is especially important after prolonged cutting times when heat can distort the construction.


X-MW 44 1250 x 1250mm cutting capacity X-MW 84 2450 x 1250mm cutting capacity X-MW 105 3050 x 1550mm cutting capacity X-MW 107 3050 x 2150mm cutting capacity X-MW 125 3650 x 1550mm cutting capacity X-MW 44 1250 x 1250mm cutting capacity X-MW 84 2450 x 1250mm cutting capacity X-MW 105 3050 x 1550mm cutting capacity X-MW 107 3050 x 2150mm cutting capacity X-MW 125 3650 x 1550mm cutting capacity
$129,850 ex GST$129,850 ex GST
$135,000 ex GST$135,000 ex GST
$142,750 ex GST$142,750 ex GST
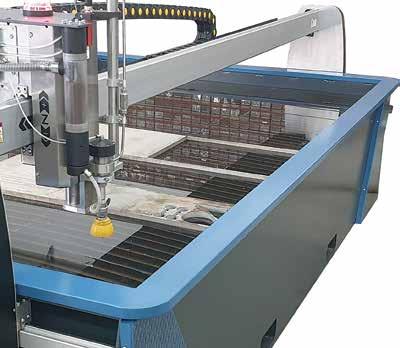
POAPOA

$153,000 ex GST$153,000 ex GST

MORE OF THE SAME AS FABRICATOR EXPANDS MANUFACTURING OPERATIONS

A Melbourne company founded almost 30 years ago by a fitter and turner working at Mistral Fans is developing an impressive reputation for its fabrication and manufacturing work.
Any Steel Fabrication specialises in custom work in both mild and stainless steel, delivering everything from one-off specials to larger-scale manufacturing jobs. Today, Any Steel Fabrication operates with a team of between 14 and 17 skilled operatives, boasting well over 50 years of experience between them.
Stan Vasilopoulos first struck out on his own in 1988, leaving Mistral Fans and purchasing a small lathe and a mill-drill from Hare & Forbes. He set up the machines in his father’s garage and set about manufacturing pulleys for gymnasium equipment.
Vasilopoulos is keen to make the point that he paid cash for those first two machines from Hare & Forbes; and also that the mill-drill is still in use to this day.
After seven years working out his father’s back yard, Vasilopoulos moved his operations into a small unit in Thomastown, which he still owns, and Any Steel Fabrication was born.
While Vasilopoulos has continued to source his machinery from Hare & Forbes, there has been another common factor over more recent years: a reliance on the Turkish made Baykal brand of machine tools.

that Stan Vasilopoulos sees his company’s future moving towards the mass production side of the business, producing higher volume runs to support other fabricators in the region. And with the addition of his engineering graduate son to the team, the company will have even more resources at its hands to take on ever more ambitious fabrication and manufacturing projects.
4-metre 160-tonne CNC press brake that is still in use today. And like all members of the Baykal press brake range, that machine is based on a rigid monoblock steel frame, which guarantees minimal deflection under load for repeatable accurate bending.
Today, the workshop at Any Steel Fabrication in Campbellfield features an array of Baykal CNC presses with capacities up to 300 tonnes (including that original unit with an upgraded CNC unit). There is also a Baykal guillotine, and – in pride of place – a Baykal BPS1503 X 170XPR CNC plasma machine.
That plasma machine combines a highly rigid table typical of the Baykal product line with the industry standard Hypertherm plasma unit. And it has allowed Any Steel to take control back over more of its production by removing the need to send cutting work out to subcontractors.
“When you buy any machine, you have to know that you have the backup to rely on, and buying Baykal equipment from Hare & Forbes I’m confident that I’ll get the support I need,” he says.
“All the Baykal machines have been very reliable. There’s been the odd minor issue, but these have all been sorted out very quickly. That’s why I’m comfortable in continuing to source Baykal machines from Hare & Forbes.”
The next arrival is likely to be a fourth Baykal CNC press brake, the largest of all, with a 6-metre bed and 400 tonne capacity.
With such a large investment in machinery, it is probably no surprise

Going forward, the biggest problem for Any Steel Fabrication appears to be lack of space. With the company’s ambitious expansion programme and the acquisition of still more Baykal machine tools, the premises in Campbellfield are starting to fill with equipment after only two years in occupation.
But that is just the sort of problem that most other companies would love to have. For Stan Vasilopoulos, it’s evidence of success.
Any Steel Fabrication anysteel.com.au
Hare & Forbes Machineryhouse www.machineryhouse.com.au