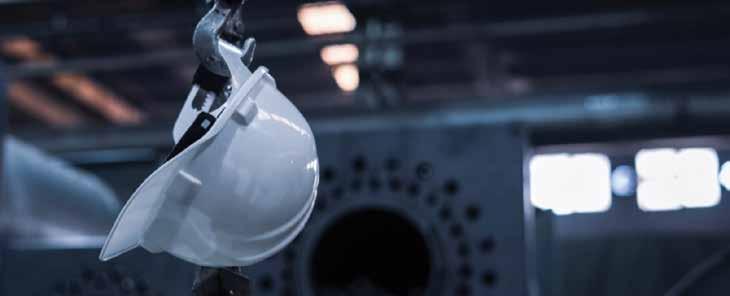
19 minute read
WORKPLACE HEALTH & SAFETY
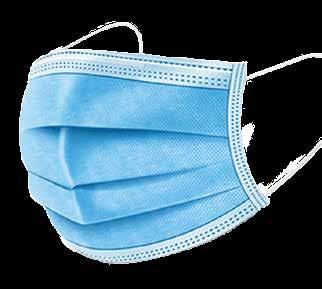
Canberra offers to help industry manufacture mRNA vaccines
Advertisement
The Australian Government is offering to partner with industry so that the country has the opportunity to produce mRNA vaccines and, potentially, other therapeutic products, using this technology.
In a joint announcement with Minister for Health Greg Hunt, newly appointed Minister for Industry, Science and Technology Christian Porter said the Government was inviting key commercial providers and potential providers to demonstrate their future capability and explain what government involvement, assistance or support could make that capacity a reality.
“We know that mRNA is an extremely promising branch of medical science and we know from work already undertaken that Australian businesses and researchers are developing mRNA capacity,” Minister Porter said.
“However our market analysis also shows there are gaps and challenges to scale-up, which mean it’s not currently possible to commercially manufacture mRNA treatments locally.”
He said the Government was taking a two-pronged approach to establishing this capability. “We are continuing negotiations with existing manufacturers while also approaching the market for others that can potentially provide viable solutions.
“This partnership approach will ultimately help us secure the best mRNA capability for Australians while delivering economic benefits, improving health outcomes for Australians and creating high paying jobs for the future.”
He said that while mRNA vaccines were already a key pillar of the Government’s vaccine strategy, mRNA technology had the potential to treat many other diseases including cancer, the flu, and cardiovascular disease.
“This approach to market builds on work already undertaken to understand Australia’s vaccine manufacturing capability, including a manufacturing audit undertaken last year and a business case.
“Both these will provide a strong evidence base on which to assess proposals as we work to build capability here at home.”
The Government is seeking proposals that will establish an end-to-end sustainable capability. Requirements that applicants will need to address include: • the submission of fully costed proposals to establish an end-to-end
onshore population scale mRNA capability; • demonstrated access to necessary intellectual property for manufacturing processes, technology transfer and production at scale; • capacity to make products available to the Australian Government as required and in priority over any other purchaser; • the ability to deliver secure supply of population scale mRNA vaccines, including to scale up production to respond to reasonably foreseeable health emergencies and issues; • the ability to deliver secure supply of other therapeutic mRNA based
treatments of a type and scale that may be needed to respond to the reasonably foreseeable health needs of the Australian community; • the sustainability of the facility over 10 years and an undertaking to maintain the capability onshore on an ongoing basis; • a commitment to collaborate and build and maintain working relationships with the Australian research community; and • opportunities for exporting vaccinations and treatments, both commercially and in support of our region, during any future health emergencies.
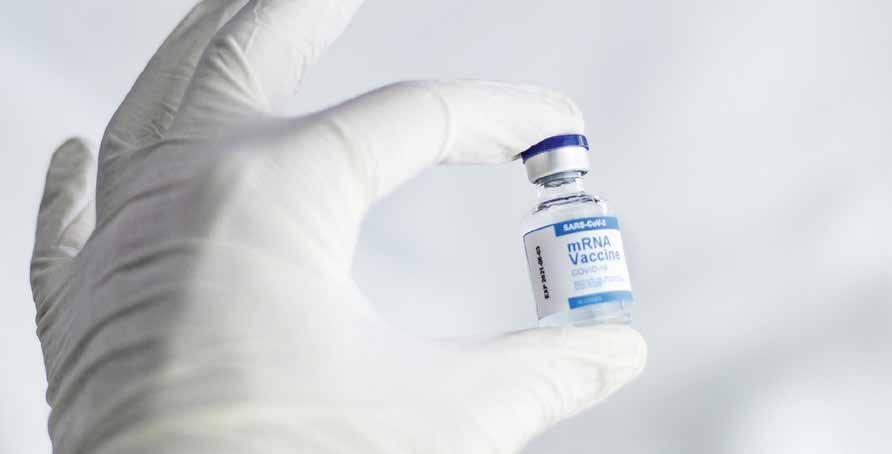
The Workplace Health & Safety Show will return to Sydney in September, bringing with it trusted industry pioneers and groundbreaking newcomers who will share news on current trends, research, progressive technology, processes and products that are redefining the world of safety. It will run from Tuesday 7 to Wednesday 8 at the Sydney Showground, Sydney Olympic Park, Homebush.
With the support of SafeWork NSW and the Australian Institute of Health and Safety, the Workplace Health & Safety Show is Australia’s paramount workplace health and safety event. The event guarantees a live, intuitive two-way learning experience with an expo including more than 100 companies, proactive discussions and forums, driven by the industry’s best, and providing insight into everything from workplace mental wellbeing to creative new technologies and the consistently changing universe of safety laws.
‘’With an eagerness for vendors to take part in face-to-face events again, I am delighted to announce the Workplace Health & Safety Show will return to Sydney on 7-8 September in 2021,” said Marie Kinsella, CEO, International Exhibition & Conference Group.
“We are delighted to have the presence of Australia’s leading suppliers in workplace health and safety exhibiting their new products releases at the Sydney event, including major exhibition sponsor Skytrust,” said Kinsella.
The opportunity to hear from industry leaders through a personalised and interactive environment has always been key to the Workplace Health & Safety Show’s success, and the 2021 event will be no different.
“We have made sure to expand on educational presentations in this year’s interactive forums and panel discussions to cover the topics on the national agenda, such as innovation, technology, significant hazards, mental wellbeing, and injury prevention, just to name a few,” said Kinsella.
“2020 was certainly an extremely tough year for all of us. As the ripple effects from Covid-19 move through the community, there has been a significant toll on mental health,” Kinsella continued. “Keeping the same in mind, mental health as a priority at workplace will be a crucial focal point of Workplace Health & Safety Show 2021.”
The Workplace Health & Safety Show is open for all safety managers and safety officers from various industries, including manufacturing, building/ construction, mining, councils/local government, hospitals, transport, and more.
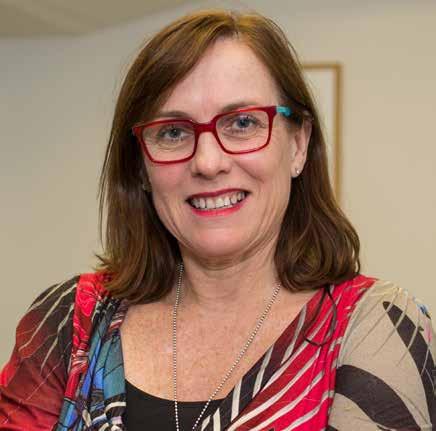
Marie Kinsella, CEO at IEC Group.
This year’s event will also see the launch of the Modern Manufacturing Expo, co-located at the Workplace Health & Safety Show. The Modern Manufacturing Expo will bring together a showcase of the latest advanced products and technologies for Australian manufacturers.
Registration to attend the Workplace Health & Safety Show is free. Register online at www.whss.com.au
Mental health to be tackled head on at Workplace Health & Safety Show
The issue of mental health and wellbeing is a major concern for Australian workplaces. Around 91% of all workers’ compensation claims involving mental health disorders between 2010–11 and 2014–15, were related to work and mental stress, according to Safe Work Australia. The World Health Organization found that depression and anxiety disorders cost the global economy US$1 trillion each year in lost productivity.
Mental health and wellbeing is misunderstood in today’s business world and employers are now searching for the best ways to respond and support employees’ mental health conditions.
The upcoming Workplace Health & Safety Show (7-8 September 2021) at the Sydney Showground, Sydney Olympic Park Homebush, promises to be more engaging than ever and aims to tackle the issue of mental health in the workplace head on.
The event will include an array of live, proactive discussions, seminars, Q&As and an interactive two-way educative experience with more than 100 companies. Those attending will discover new supplier resources and technology, increase their knowledge and insights, and develop new connections.
Particularly exciting will be a workshop on 'Practical approaches to managing psychosocial hazards in the workplace - a regulator's perspective', by Ian Firth, State Inspector, SafeWork NSW. During this workshop, Ian will delve into psychosocial hazards in the workplace, their challenges, and the practical approaches to managing risk. To give a more pragmatic outlook on the above concerns, Ian will also present a People at Work Case Study that can prove beneficial for employers and managers.
Samuel Eddy, Executive Wellness Coach, will lead an interactive seminar focusing on 'Powerful tools to improve workplace health, safety and productivity'. This seminar covers how employees can scale down their "stress temperature" to increase productivity alongside creating a safe and healthy workplace environment. The seminar not only focuses on theoretical beliefs, it provides a practical session for employers/managers to take away essential learnings for their organisation.
Another interesting discussion taking place this year is that by John Toomey, Wellness Thought Leader, on 'The care equation in preventing mental health challenges'. This seminar highlights the importance of why we should address mental health issues and break the stigma of its mythical theory on a chemical imbalance in the brain. The discussion aims to bring forward how one can use effective prevention to help the community. 'Driving action to improve mental health at work in NSW – Towards 2022 and beyond' is a seminar led by Jim Kelly, Director of Health and Safe Design at SafeWork NSW. Jim will drive the discussion by underlining the regulatory perspective on workplace mental health and the intrinsic role leaders play in driving safety culture, and the precautionary and proactive measures companies can take to manage psychological hazards in the workplace.
Attendees will get the opportunity to meet SafeWork NSW Inspectors: Kevin Murphy, Ian Firth and Genevieve Fleming, all three collectively experienced in Building & Construction, Psychological Health, and Manufacturing. This Q&A feature will allow an interactive discussion targeting employers’/managers' related concerns regarding workplace health & safety.
With the support of SafeWork NSW and the Australian Institute of Health and Safety, the Workplace Health & Safety Show is Australia’s paramount workplace health and safety event. The event guarantees a live, intuitive two-way learning experience with an expo including more than 100 companies, proactive discussions and forums, driven by the industry’s best, and providing insight into everything from workplace mental wellbeing to creative new technologies and the consistently changing universe of workplace safety laws.
Registration to attend the Workplace Health & Safety Show is free. Register online at www.whss.com.au
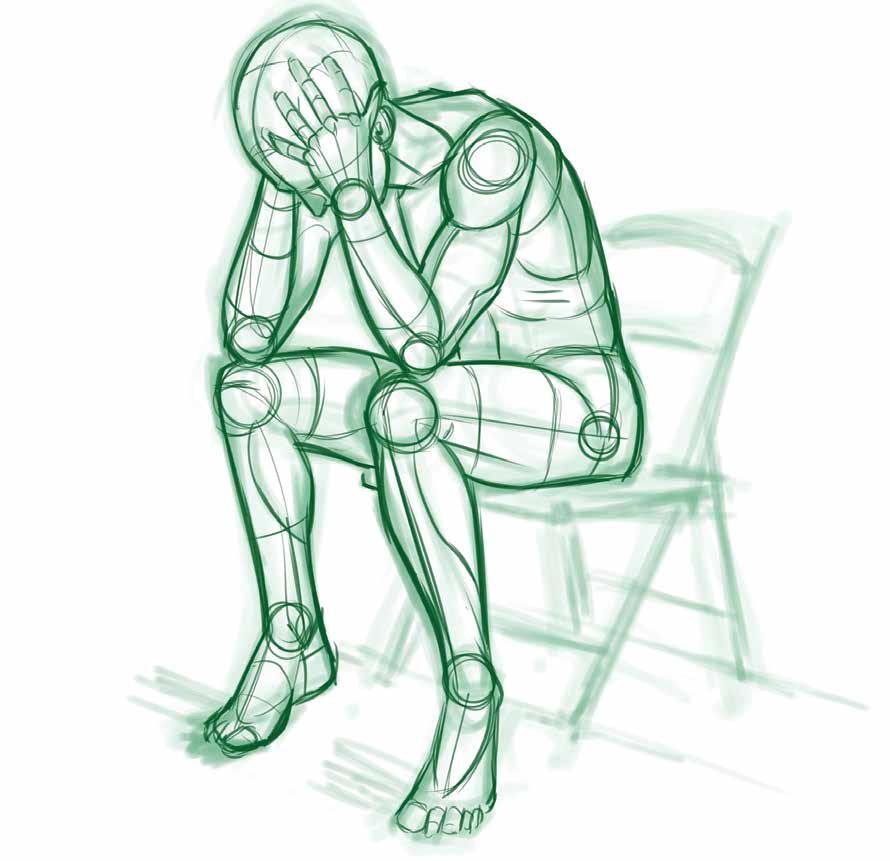
Compliance attains a new standard of speed and ease: ISO 37301
Compliance applies across the full expanse of a workplace – from machinery prestart routines to facility environmental standards. The breadth of compliance means that businesses must create a compliance culture from top to bottom – and in that order: compliance starts from the top.
It is tough to keep track of it all. That’s why businesses are turning to compliance management systems, in particular contemporary paperless ones.
These compliance systems line up with industry standards such as ISO 37301, “Compliance Management Systems – Requirements with Guidance for Use” from the International Organization for Standards. The standard is designed to cover all types of business, large and small.
With ISO 37301, compliance management should become quicker and easier, without sacrificing quality compliance.
Luckily for those wishing to modernise their compliance management systems, even those using the previous ISO 19600:2014 version of the standard, ISO 37301 is here to help. Paired with digital inspection solutions, the standard delivers a comprehensive package that sits along any other business inspection to transform performance and results.
Reducing waste is a significant goal with many organisations. It is important, therefore, that inspection and compliance be paperless. Key then is a digital platform upon which ISO 37301 can sit and work alongside. Inspection and compliance solutions have long helped businesses inspect safety in a facility, examine the asset lifecycle or conduct compliance checks. With dynamic checklists, corrective actions and simpler audit trails, paperless inspection solutions partner naturally with standards such as ISO 37301.
By utilising smartphone and tablet capability, compliance inspection and audit trail management can be greatly streamlined with high grade simple evidence. Compliance doesn’t have to be complicated ever again.
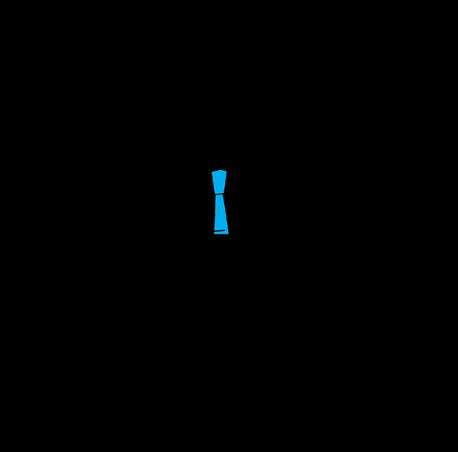
Pervidi 03 8862 6485 pervidi.com.au
We produce We produce PRODUCT VIDEOS, CASE STUDY VIDEOS,PRODUCT VIDEOS, CASE STUDY VIDEOS, We produce PRODUCT VIDEOS, CASE STUDY VIDEOS, MANUFACTURING CURRENT AFFAIRS VIDEOS and HOW TO VIDEOSMANUFACTURING CURRENT AFFAIRS VIDEOS and HOW TO VIDEOSMANUFACTURING CURRENT AFFAIRS VIDEOS and HOW TO VIDEOS
EXCLUSIVE! NOW PRODUCING 2 PART DOCUMENTARIESEXCLUSIVE! NOW PRODUCING 2 PART DOCUMENTARIESEXCLUSIVE! NOW PRODUCING 2 PART DOCUMENTARIES
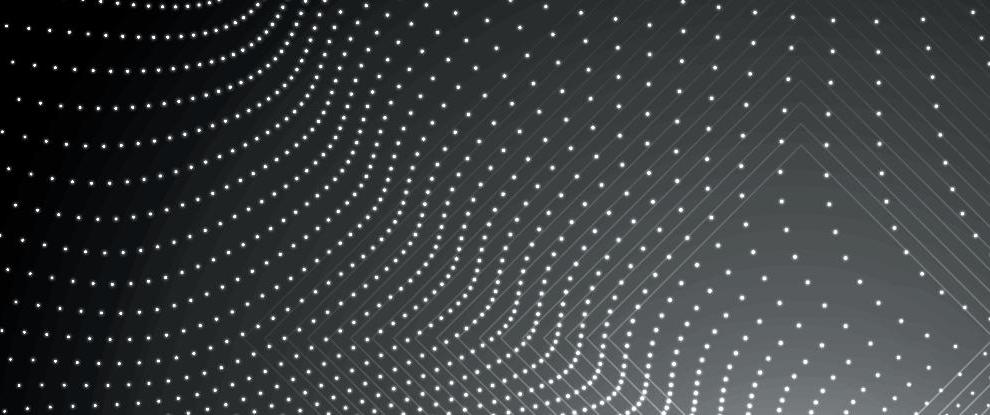
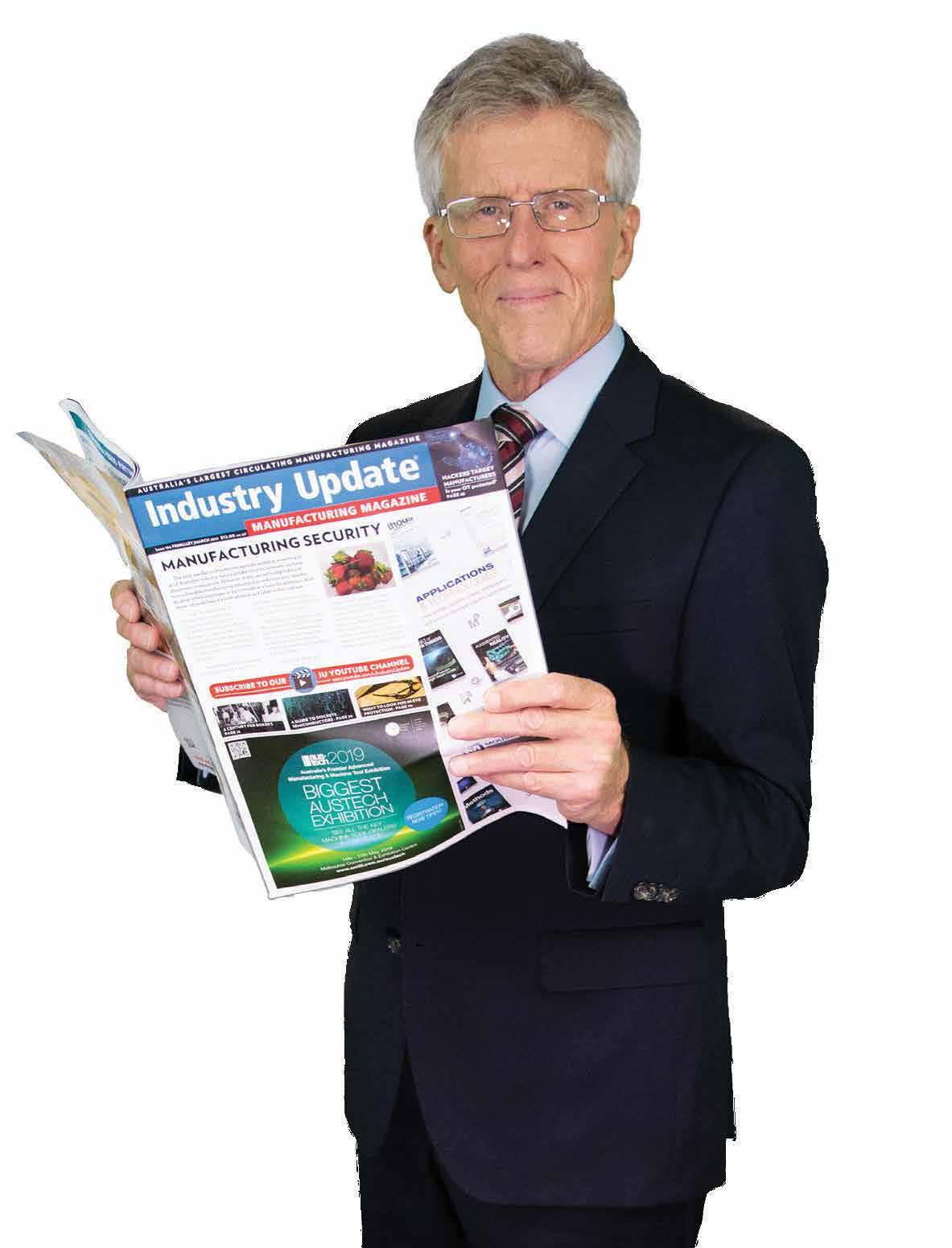
EXCLUSIVE! NOW PRODUCING 2 PART DOCUMENTARIES
Tim Webster Tim WebsterTim Webster
Australia’s National IconAustralia’s National IconAustralia’s National Icon and News Presenter and News Presenterand News Presenter
(Channel Ten, Foxtel, (Channel Ten, Foxtel,(Channel Ten, Foxtel, Sports Tonight, 2UE And 2CH)Sports Tonight, 2UE And 2CH)Sports Tonight, 2UE And 2CH)
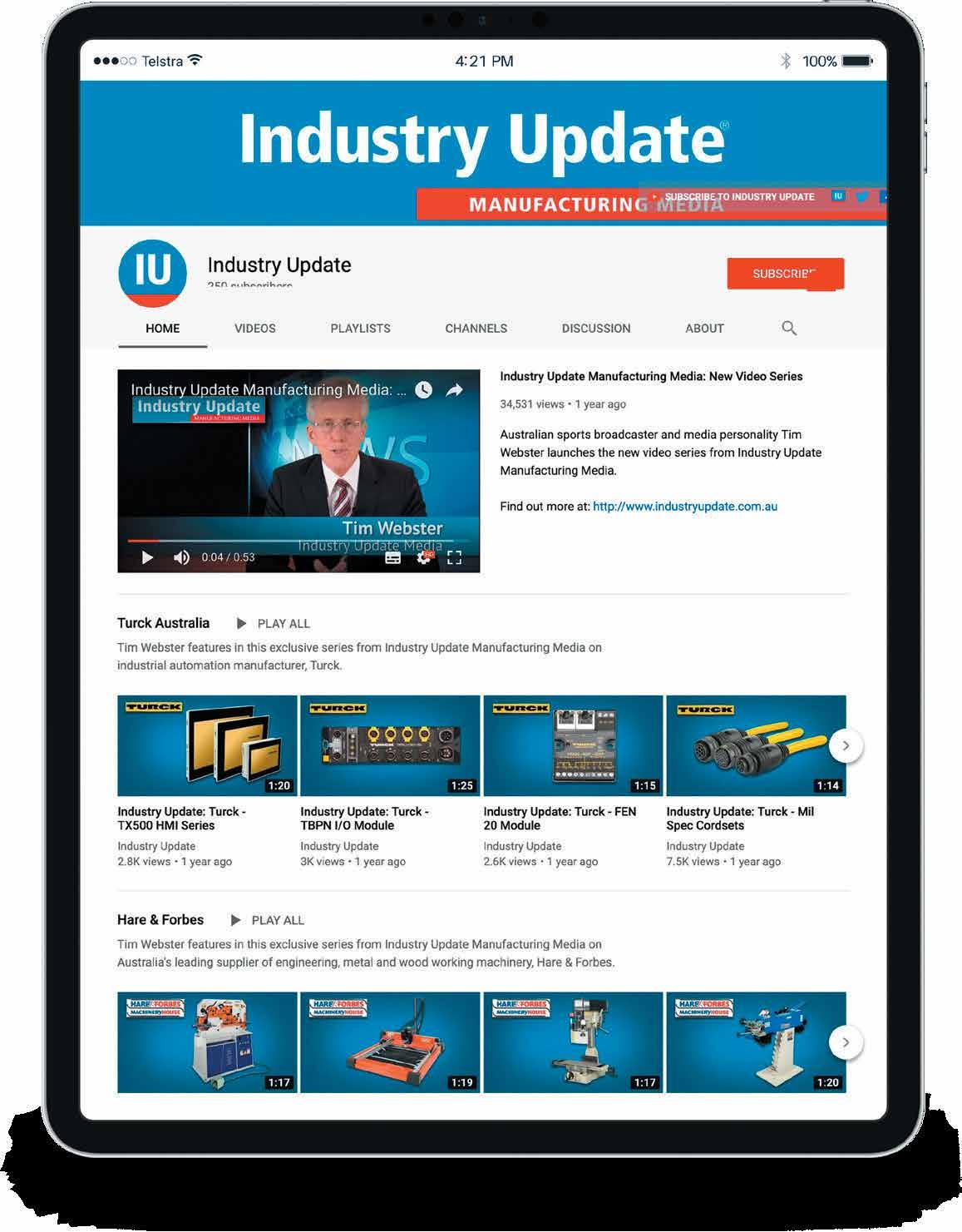
Tim Webster VIDEO PRODUCTION HIGHLIGHTSAustralia’s National Icon and News Presenter VIDEO PRODUCTION HIGHLIGHTSVIDEO PRODUCTION HIGHLIGHTS
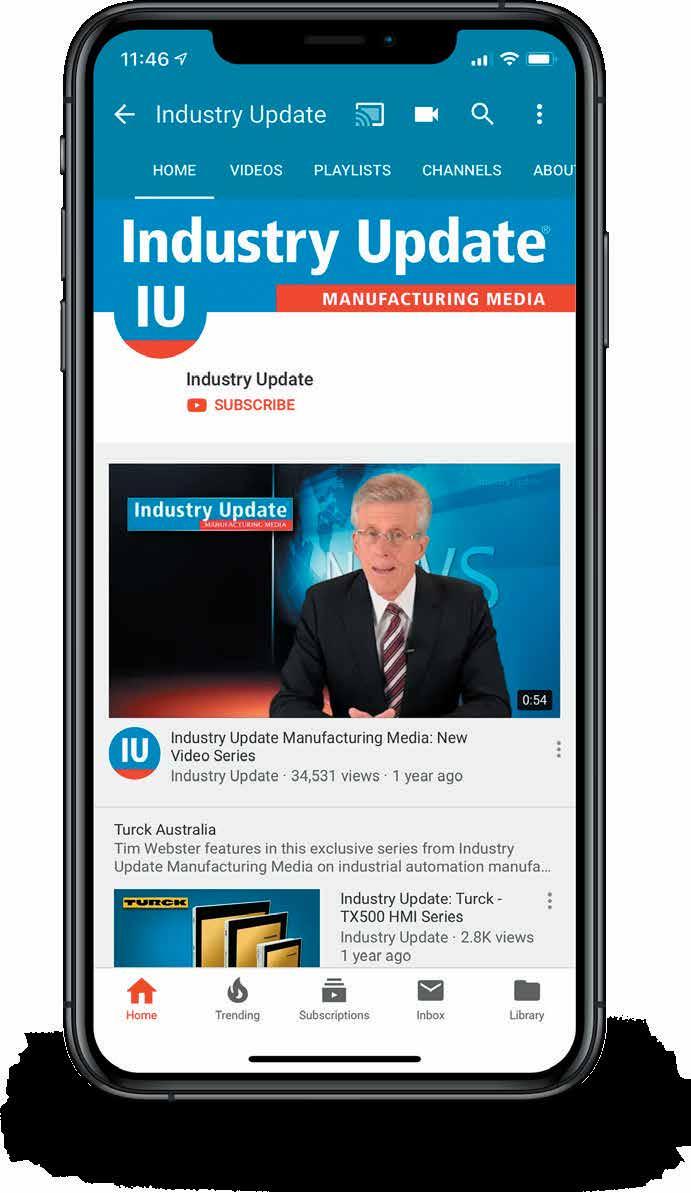
Industry Update Industry UpdateIndustry Update Youtube Channel StatisticsYoutube Channel StatisticsYoutube Channel Statistics
(Channel Ten, Foxtel, • • Hosted by national TV icon and news Sports Tonight, 2UE And 2CH) Hosted by national TV icon and news • Hosted by national TV icon and news
journalist Tim Websterjournalist Tim Websterjournalist Tim Webster • • Filmed in a 6pm nightly news broadcast style VIDEO PRODUCTION HIGHLIGHTSFilmed in a 6pm nightly news broadcast style • Filmed in a 6pm nightly news broadcast style • • Creating a high level of integrity for clients’ Creating a high level of integrity for clients’ • Creating a high level of integrity for clients’ products and services• Hosted by national TV icon and news products and servicesproducts and services • • Average video length of 1 to 2 minutes journalist Tim Webster Average video length of 1 to 2 minutes • Average video length of 1 to 2 minutes
1,250,000 impressions* 588,000 views* *Since service launch in 2017 Since its launch in 2017, Industry Update Video has been a phenomenal success, with content spanning the whole of manufacturing industry. • Individual client playlists, have all your videos in one place • Embed these videos on your website or any social platform (Facebook, LinkedIn etc) • All magazine advertising includes a QR code that links back to your website Industry Update Youtube Channel Statistics 1,250,000 impressions* 588,000 views* *Since service launch in 2017 • Filmed in a 6pm nightly news broadcast style • Creating a high level of integrity for clients’ products and services • Average video length of 1 to 2 minutes • Individual client playlists, have all your videos in one place • Embed these videos on your website or any social platform (Facebook, LinkedIn etc) • All magazine advertising includes a QR code 1,250,000 impressions* 588,000 views* *Since service launch in 2017 Since its launch in 2017, Industry Update Video has been a phenomenal success, with content spanning the whole of manufacturing industry. • Individual client playlists, have all your videos in one place • Embed these videos on your website or any social platform (Facebook, LinkedIn etc) • All magazine advertising includes a QR code that links back to your website 1,250,000 impressions* 588,000 views* *Since service launch in 2017 Since its launch in 2017, Industry Update Video has been a phenomenal success, with content spanning the whole of manufacturing industry. • Individual client playlists, have all your videos in one place • Embed these videos on your website or any social platform (Facebook, LinkedIn etc) • All magazine advertising includes a QR code that links back to your website 3.09 million impressions* 830,159 views*
that links back to your website
Product Video PacksSince its launch in 2017, Industry Update Video has been a phenomenal success, with content spanning the whole of manufacturing industry.Product Video PacksProduct Video Packs
More facts: More facts:More facts:
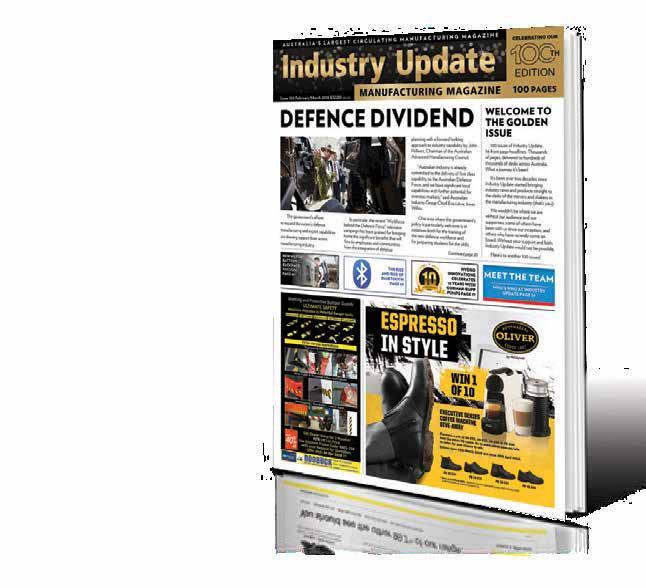
76% of businesses with product videos say their sales have increased, while the improved Companies must have good video content now - buyers expect it and will just go With over 1.5 million impressions and 600,000 views in less than 12 months, our videos are Product Video Packs More facts:76% of businesses with product videos say their sales have increased, while the improved Companies must have good video content now - buyers expect it and will just go With over 1.5 million impressions and 600,000 views in less than 12 months, our videos are 76% of businesses with product videos say their sales have increased, while the improved Companies must have good video content now - buyers expect it and will just go With over 1.5 million impressions and 600,000 views in less than 12 months, our videos are educational quality of the content reduced support elsewhere if they don’t have something getting great rates of engagement. 76% of businesses with product videos say Companies must have good video content With over 1.5 million impressions and 600,000 educational quality of the content reduced support elsewhere if they don’t have something getting great rates of engagement. educational quality of the content reduced support elsewhere if they don’t have something getting great rates of engagement. Some of our Industry Update Video clients One billion hours of video are watched on YouTube every day, with a user’s average viewing session lasting 40 minutes2 enquiries by 47%1 Source: 1) https://www.wyzowl.com/video-marketing-statistics-2018/ 2) https://www.youtube.com/yt/about/press/ interesting and informative to watch. More importantly it increases sales by 81% (see below). It is a no brainer. Plus, each video has an accompanying story published online, in e-news and in the magazine (with a QR code) to integrate all media options. Some of our Industry Update Video clients One billion hours of video are watched on YouTube every day, with a user’s average viewing session lasting 40 minutes2 their sales have increased, while the improved educational quality of the content reduced support enquiries by 47%1 Source: 1) https://www.wyzowl.com/video-marketing-statistics-2018/ 2) https://www.youtube.com/yt/about/press/ now - buyers expect it and will just go elsewhere if they don’t have something interesting and informative to watch. More importantly it increases sales by 81% (see below). It is a no brainer. views in less than 12 months, our videos are getting great rates of engagement. Plus, each video has an accompanying story published online, in e-news and in the magazine (with a QR code) to integrate all media options. Some of our Industry Update Video clients One billion hours of video are watched on YouTube every day, with a user’s average viewing session lasting 40 minutes2 enquiries by 47%1 Source: 1) https://www.wyzowl.com/video-marketing-statistics-2018/ 2) https://www.youtube.com/yt/about/press/ interesting and informative to watch. More importantly it increases sales by 81% (see below). It is a no brainer. Plus, each video has an accompanying story published online, in e-news and in the magazine (with a QR code) to integrate all media options. Some of our Industry Update Video clients One billion hours of video are watched on YouTube every day, with a user’s average viewing session lasting 40 minutes2 enquiries by 47%1 Source: 1) https://www.wyzowl.com/video-marketing-statistics-2018/ 2) https://www.youtube.com/yt/about/press/ interesting and informative to watch. More importantly it increases sales by 81% (see below). It is a no brainer. Plus, each video has an accompanying story published online, in e-news and in the magazine (with a QR code) to integrate all media options. VERSION JOB # / NAME STG 2550 BusinessCommbanking_Manufacturing_PRESS_245x340MM_v10 OPERATOR Dan OUTPUT NOTES/COMMENTS PERSONNEL CREATIVE DIRECTOR PRODUCTION 10 SETUP BLEED N/A GUTTER N/A SCALE 100% PLEASE NOTE: Image is only positional low res for now will need to update with the final high res for approval. ART DIRECTOR ACCOUNT MGMT TRIM 245x340mm SCALE 100% CURRENT DPI XXXDPI COPY WRITER CLIENT TYPE SAFE N/A COLOURS 4 Colour FINAL DPI XXXDPI DESIGN (Inc Spell Check) STUDIO (Inc Spell Check) TIME & DATE August 8, 2019 3:05 PM
Number one manufacturing Number one manufacturing publication in AustraliaNumber one manufacturing Number one manufacturing
publication in Australia Circulation of 19,233 and readership of 76,932publication in Australiapublication in Australia
Circulation of 19,233 Circulation of 19,233 and readership of 76,932Audited by and readership of 76,932Circulation of 19,233 and readership of 76,932
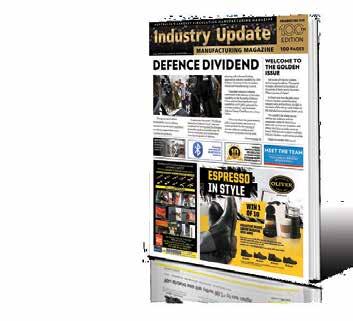
There has been extensive discussion of how office workers have adapted to the challenge of working from home (WFH), but the manufacturing sector has also embraced an increase in remote working, whether by design or necessity. Here, John Young, APAC sales director at automation parts supplier EU Automation, identifies the three major things the manufacturing sector has learned from a year of WFH. Having been forced to work remotely due to Covid-19 restrictions, many employees and companies are acknowledging that things will likely never return to the pre-pandemic status quo. In countries and sectors that have embraced high levels of automation, businesses can save money and employees can enjoy greater flexibility through hybrid models that mix working on site with more frequent and flexible remote working.
However, the debate so far has focused mostly on office working. Here’s three key things manufacturers in the APAC region have learned from a year of working remotely.
Accelerating automation?
For office jobs, there is little doubt that a year of remote working has accelerated the uptake of digital technologies and automation. According to Teo Lay Lim, South Asia Market unit lead for Accenture, the pandemic has effectively consolidated 10 years of digital transformation efforts into a mere six months.
In manufacturing, the picture is less clear, but the early evidence suggests more manufacturers turning to automation. At the very least, the crisis has shone a spotlight on automation technologies and the benefits they can offer. Automated guided vehicles (AGVs) are one of many examples of technologies that have enjoyed a period of growth throughout the pandemic and look set to enjoy a strong uptake in many sectors, particularly food and beverage.
Cyber gaps exposed
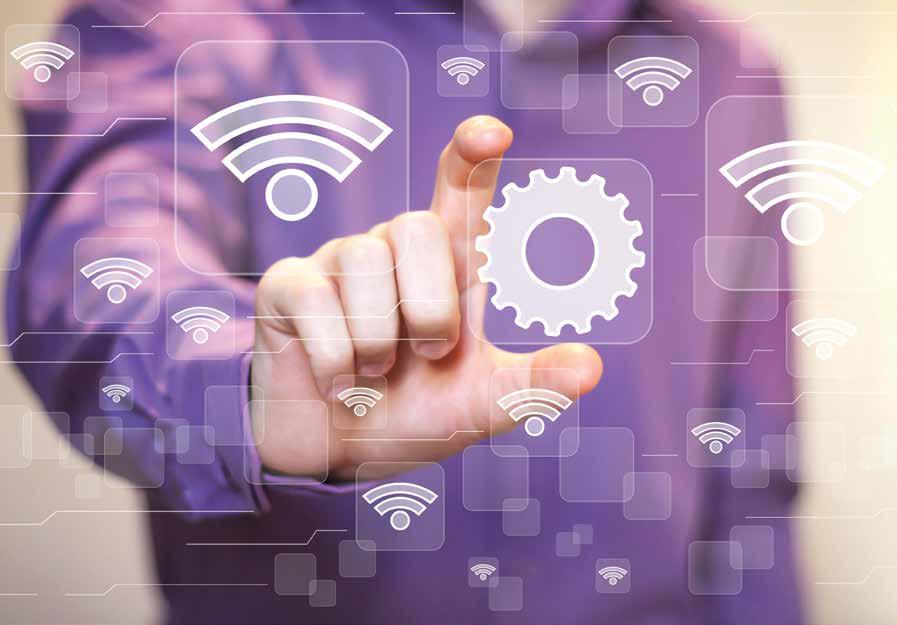
Although digital transformations have allowed greater levels of remote working, they have also exposed cyber vulnerabilities. The manufacturing sector is no different to others in this regard, but the stakes could potentially be greater. Just imagine the consequences of an industrial robot being hacked.
One problem is employees using vulnerable devices when working remotely. A recent study from LogMeIn, found that globally 31% of people are using ‘vulnerable devices’ when working remotely and for the APAC region specifically, the figure was 45%.
In another study from AT&T, which surveyed 500 IT decisionmakers in Singapore, Hong Kong and Australia, almost half the respondents said they anticipated the volume of cyber attacks to increase.
Remote condition monitoring
The possibility of remote working varies greatly in the manufacturing sector. One interesting area of development that has been given a fillip in the past year is technology that enables remote condition monitoring.
Remote condition monitoring is the ability to view the performance, status and behaviour of a machine from a distance in real time. This is achieved with a combination of Internet of Things (IoT) technology and cloud computing that allows an on-site machine to be tracked by maintenance engineers wherever they are.
Having automated sensors removes some of the need for human intervention. The data gathered via these sensors can be accessed remotely via cloud services and data visualization tools allow engineers to identify and diagnose a fault while working from home. Using these solutions, maintenance engineers can order components from parts suppliers such as EU Automation.
Many companies have learned a lot from WFH, and manufacturers are no exception. The challenge has encouraged the uptake of those technological solutions that reduce the need for human workers on site. However, manufacturers are also discovering that WFH is opening up greater cyber vulnerabilities and necessitating a more effective strategy to respond to this threat.
On-line sales: www.floorsafe.com.auOn-line sales: www.floorsafe.com.au Email: Email: sales@floorsafe.com.au sales@floorsafe.com.au AUSTRALIAAUSTRALIA Phone: Phone: 1300 717 769 1300 717 769