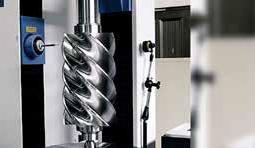
18 minute read
COMPRESSORS AND PNEUMATICS
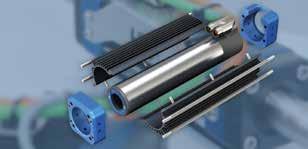
Food industry focus: To understand the challenges, you need to be on the factory floor
Advertisement
In Australia, the food and beverage sector accounts for 32% of the country’s total manufacturing turnover and is reported to be worth around $122 billion (Octet 2020). New Zealand, on the other hand, is a major food and beverage exporter, with the industry accounting for 46% of all goods and services exports (Mbie.govt.nz (2021).
On the global front, the food processing market is expected to grow by 6.04% (CAGR) between 2020 and 2027. This puts pressure on manufactures to fast-track productivity and improve their efficiencies year-on-year.
A recent report compiled by Diego Mirabelli, Industry Manager Food for SMC Corporation in Europe showcased the latest food industry trends and highlighted the challenges in light of the COVID-19 pandemic. It details SMC’s presence on the factory floor to identify the industry’s most pressing automation requirements.
What’s trending in food automation?
Surprisingly, the impact of the COVID-19 pandemic saw a positive uptick in automation. “Companies are changing the way they work. They’re focused on rapidly and continuously addressing challenges around productivity, downtime, energy savings, safety, hygiene and staying competitive in a tough climate.” explains Craig Sheppard, Sales and Marketing Director from SMC Corporation Australia New Zealand.
Food security remains an ongoing issue around the world, and Craig believes that automation will play a key role in addressing scarcity in the years to come.
“Other issues addressed by manufacturers is that of a reliable workforce, and workforce accessibility. Whilst labour is expensive, COVID-19 enforced lockdowns taught some harsh lessons with respect to staff accessing workplaces and the need for social distancing created its own set of challenges – especially in plants where productivity (both day and night) is crucial.”
And while workers will always be needed, many companies are now reassessing the workforce to ensure that they are adding value and making a difference to the company’s bottom line.
When analysing the shift (and embrace) of automation, the report by Diego Mirabelli detailed the following as key drivers:
1. Avoiding downtime
Most food plants operate 24/7, so a halt in food production can be costly and time consuming. Most areas are arranged in a continuous flow with one area being dependent on the activity of another - from primary material integration, to processing, and finally, packaging. The OEE (Overall Equipment Effectiveness) can be substantially improved by applying digital predictive maintenance solutions, training operators, and maximizing product reliability.
When analysing automation on the plant, Diego believes that the most critical component is the actuator. The procedure to replace an actuator is fast (usually 10 minutes) when its within reach and is easily accessible. In other cases, it can take up to four hours. Of course, the cost of proactively replacing an actuator will usually be a lot less than the cost of a stop in production.
However, to ensure real-time monitoring and pre-empt any issues before they occur, monitoring sensors need to be included as part of the automation control loop. SMC offers two types of sensors. “An induction sensor can calculate the speed of the rod while a pressure sensor can identify any leakages inside the actuators. Here, communication takes place via an IO-link in real-time.”
2. Productivity linked to automation
While this traditional, fast-paced industry has been lagging in automation penetration, robotics, and its stemmed technology (cobots) are key drivers for enhanced productivity and automation on the factory floor.
“Some of our team members are dedicated to understanding and developing solutions to complement robotic technologies. We offer gripping technologies and a wide range of plug and play gripper end-effectors for the majority of cobot suppliers.” comments Craig.
Answering to the call by industry, SMC offers wireless technology for robotics applications allowing for gripper communications via Wi-Fi, allowing for a reduction in weight and faster installation via reduced cabling requirements.
The next step is to introduce smart technologies combining flexible and quick format changes with high cycle rates and low life cycle costs.
3. Reducing costs by optimising energy efficiency
Food factories are energy demanding; they represent 19% of the whole manufacturing industry’s energy consumption. “SMC’s energy saving task force can analyse your plant and help you realise savings and efficiency gains.” says Craig.
Improvement costs may vary but the return on investment is often short. Whilst air leaks are still a common theme, there are other air usage areas of focus that can be can critically assessed, for which SMC provides a wide array of solutions: condition monitoring tools which provide information such as flow rate and pressure, Automatic Leak Detection System (ALDS) which provides near real time leakage monitoring and a VEX Stand-by Valve, which reduces air consumption during short stops or shuts it off during long ones.
Craig Sheppard, Sales and Marketing Director - SMC Corporation Australia & New Zealand
4. Machine Safety and Hygiene
“Safety and automation work hand-inhand, and safety valves form a fundamental part of our product range” he comments.
“Although hygiene has always been a central theme, COVID-19 has driven the message home. Both machine builders and food plants need solutions that are easy to clean and reduce opportunities for contamination.”
SMC Pneumatics 1800 763 862 www.smcanz.com
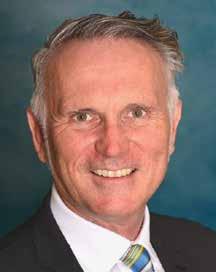
Expertise - Passion - Automation
Your production. Your way.
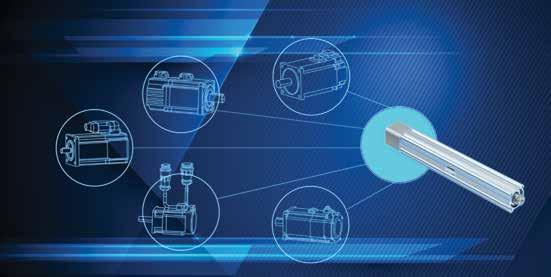
Choose the motor that is best for you!
Introducing the new motorless electric cylinder from SMC Discover the freedom of choice.
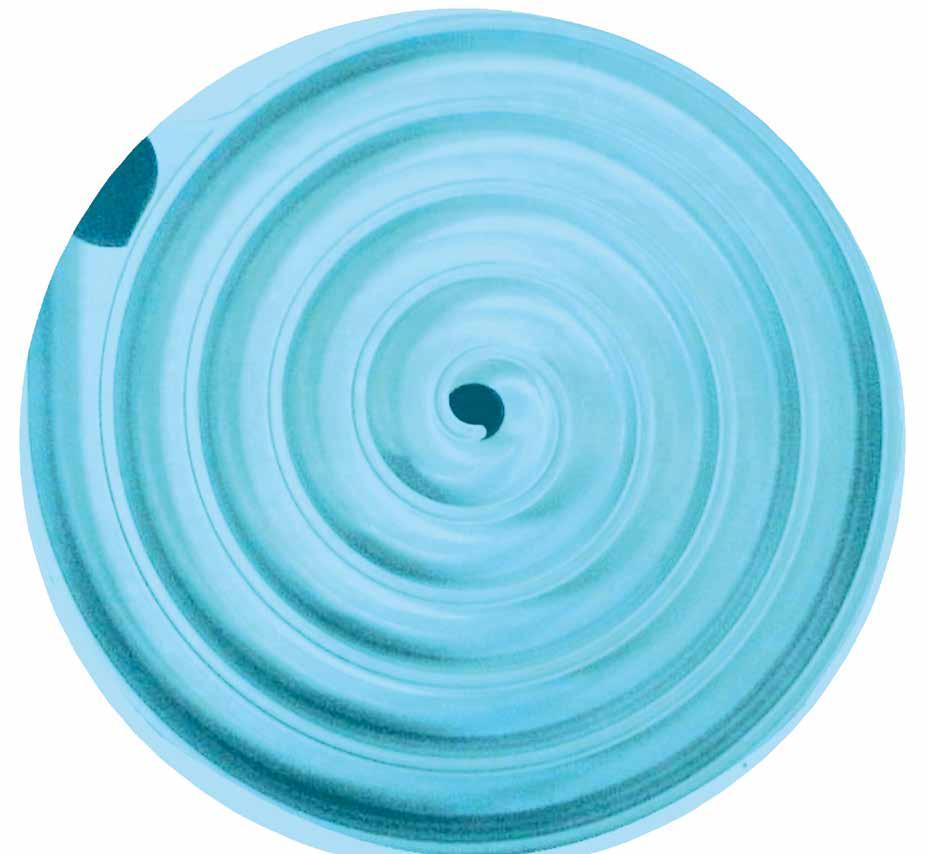
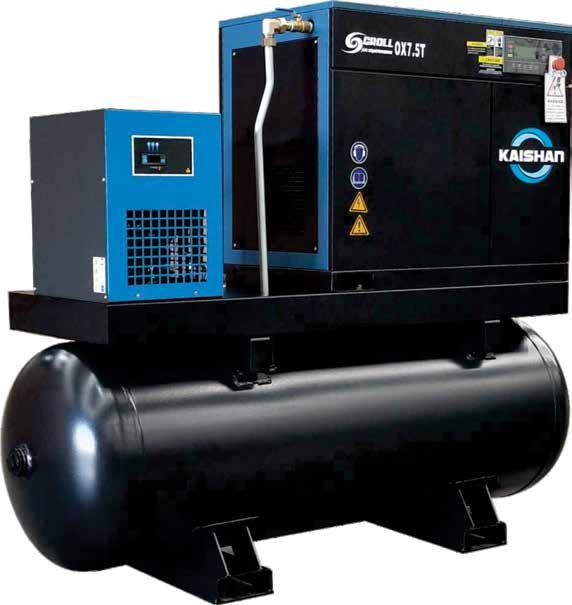
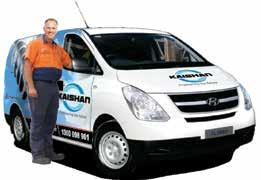
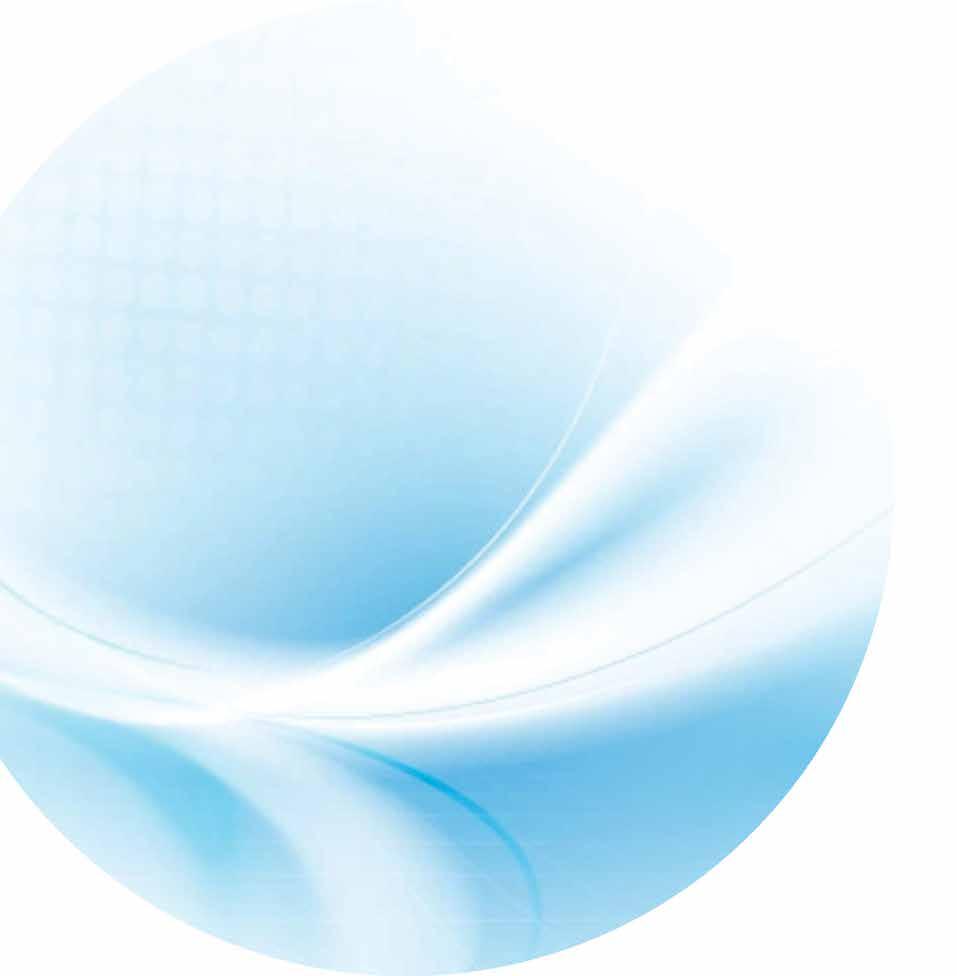
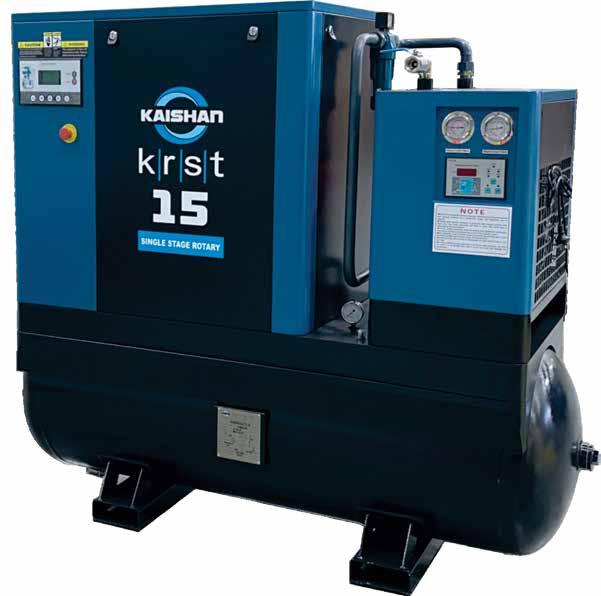
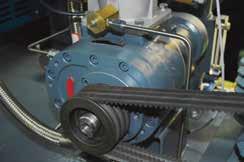
Essential components for efficient compressed air systems
Apart from the air compressor, which is the main power plant for the generation of compressed air, effective, efficient and reliable industrial systems depend on other components to ensure the delivery of sustainable, contaminantfree air to the end-use application. The ideal configuration and integration of the system components is vital for the enhancement of overall performance and low-maintenance, durable operation.
Air receivers
An air receiver, sometimes referred to as a compressed-air tank, is an integral and vitally important part of all compressed-air systems. The receiver acts as storage for excess air to accommodate the peaks of demand from your system and to optimise the running efficiency of your compressor. Short-term, high-demand periods are catered for while reducing pressure drop throughout the system and protecting the integrity of critical pressure applications at end use. Adding air storage capacity to your system decreases loading and unloading demands on the compressor, thereby reducing wear and tear, extending cycle times and cutting energy costs.
The most common example of compressed-air receivers is seen with the small, reciprocating, rotary-screw or scroll-type compressors, mounted on a “tank” or air receiver. The compressor operates on a start/stop, load/unload or vsd control system. Receiver-mounted air compressors are ideal for use in small-tomedium demand applications where space is at a premium.
In larger industrial applications (usually rotary screw-type compressors), receivers are usually separate vertical-standing units placed in the air supply line along with dryers, oil-water separators and filters. The compressors typically cycle utilising either a load/unload or variable-speed control system.
In some engineered circumstances, an air receiver can even continue to supply air while, if required, production plant and equipment is safely shut down.
Desiccant Air Dryers are particularly valuable when a very low-pressure dew point is required for sensitive applications. Vertical free-standing and tank-mounted Air Receivers store excess air to cater to peak demands and optimise system efficiency.

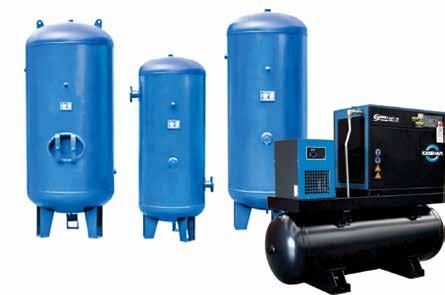
Air receivers make compressed-air systems more energy efficient by allowing the compressor to operate on longer cycle times and with tighter pressure bands. The bigger the air receiver, the more efficient the system.
Air dryers
Air dryers are essential for air compressors. Water present in the atmosphere, in the form of vapour and aerosol, is difficult to remove. When compressed, this vapour will condense, allowing liquid to form. Accumulation of this moisture over time can cause serious damage to the compressed-air system, such as corrosion, machine damage and product spoilage. Malfunctioning of control components, in turn, can bring the production processes to a halt, or impair tools, leading to additional maintenance and time costs. As such, air dryers need to be given due importance.
There are two types of air dryers – desiccant and refrigerated. Desiccant air dryers are particularly valuable when a very low-pressure dew point is required for sensitive applications. Refrigerated types are more common for industrial applications where dry air is needed, even in the hottest conditions.
Investing in a good air dryer will not only ensure your compressed air yields better returns for longer but also help increase your production levels by reducing equipment failure problems due to moisture, reduce loss incurred due to moisture-ruined equipment, and increase overall profits of your business. In short, air dryers are worth every penny spent. equipment, especially when the dirt and dust is combined with oil (which is often the case with compressors). Contaminant build-up can form inside valves, motors and other compressed-air equipment. Compressed-air filters integrated along the air lines between the compressor and end use offer a high degree of protection against wear and tear. Quality air filters have a lower pressure-drop than lowquality ones. This will save you energy. Every pressure drop in your system (from filters, dryers, long piping and so on) will require you to set your compressor on a higher setpoint, which will cost you extra electricity.
Particulate filters
Filters
Compressed-air coalescing filters protect end-use equipment from dust, dirt, pollen, oil, water and other contaminants. Contaminants can damage your
Particulate compressed-air filters remove dust and particles from the air. These particles are collected in the filtration material, where they stay until the filter is replaced every few months, depending on operation time and application. Clogged filters increase pressure drop and make filters less effective in removing contaminants.
Coalescing filters
Coalescing filters are used to capture oil and/or moisture that is suspended in the compressed air in very tiny droplets. Unlike particulate filters, the filter material collects the small droplets and transfers them to the bottom of the filter, where a condensate drain removes the liquid. Coalescing filters also need to be regularly replaced as contaminants slowly build up in the filtration material.
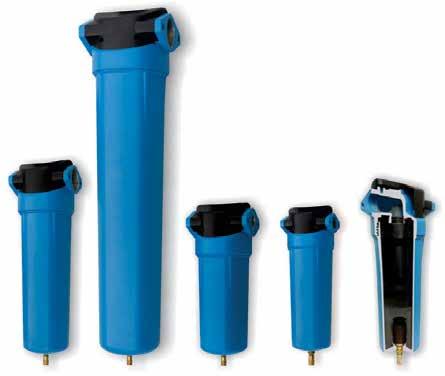
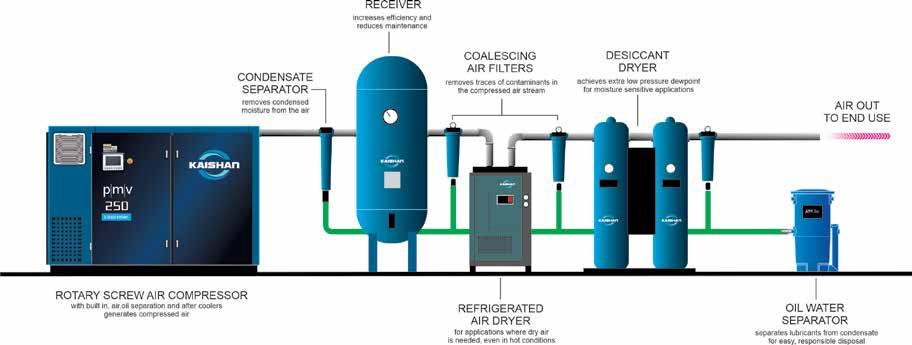
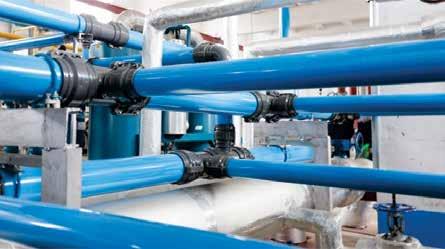
The type of Compressed Air Piping should be suited to the application and flow and have a bore that is large enough to handle the demand and system pressure.
Compressed air flows from your air compressor to the end-user equipment through your compressed-air pipeline. It is important that the type of piping is suited to the application and flow and that the pipe bore is large enough to handle the demand and system pressure. As all compressed-air systems will suffer some degree of pressure loss through the pipe system, the type, length, layout and installation of the piping are also very important. There are a few things to keep in mind when installing compressed-air piping, such as water, rust problems, the position of valves, the position of connections and filters, and many other factors. The most common pipe used includes:
Pvc: the use of pvc pipe is common but not generally recommended for use with compressed air. While readily available, inexpensive, and easy to install, pvc can sag over time and will require additional supports. The presence of air-compressor oils in the line from the compressed air can accelerate the degradation of pvc. recommended for clean air. While it works very well, it is expensive and more difficult to install, because the soldering of joints is time consuming and requires a high degree of skill.
Aluminium: with easy-to-install connections, aluminium piping systems are highly recommended for compressedair lines. Aluminium is lightweight, making it easy to handle, and it is highly recommended for most air applications. It is smooth bore, non-corrosive, and usually remains leak-free over the life of the system.
Oil-water separators
Quality oil-water separators remove lubricants from condensate for easy, responsible disposal. During normal function, air compressors produce small traces of oil-contaminated condensate. This moisture collects mainly in air receivers, coalescing filter bowls and moisture separators, making it easy to discard. This liquid cannot be discharged into storm water or onto the ground and must be specially collected in order to protect the environment. Because of this unavoidable by-product of using compressed air, an oil-water
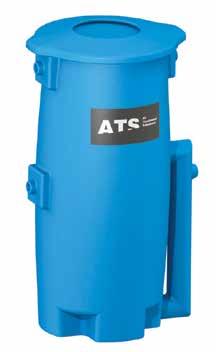
Oil-Water Separators remove lubricants from condensate for easy, responsible disposal.
separator is necessary and beneficial for environmentally responsible companies.
Auto drains
Auto-drain systems drain out the water that accumulates in air-receiver tanks, air dryers, coalescing filters and other low points in the air-reticulation system. If this condensate is not drained out it can enter the reticulation system, causing damage to pneumatic equipment, valves and actuators, and result in product spoilage.
To drain out the water, some systems use a timed drain. Other types use float switches or level sensors to drain out water after it reaches a certain level. Ask your kaishan specialist about which drain is the right one for you.
Condensate separators
Centrifugal condensate separators remove condensed moisture from the air. Since there is always moisture present in the air, condensate in compressed-air systems can’t be avoided. During the compression process, the air is heated then cools as it passes through the system. As it nears the ambient temperature (approach), vapour condenses to liquid and can be removed by mechanical separation utilising a condensate separator.
Servicing and maintaining system components is vital to operator productivity and cost saving
While thousands of businesses are dependent on compressed-air power, it is obvious that many do not fully understand the importance of maintaining the components to maximise reliability and performance. From the compressors to the delivery piping, it is vital to keep every component leakproof, contaminant free and operating at peak efficiency. Any air leak, degradation, blockage or failure at any point can cause major problems in the system itself and may impact the end application, product or process. System breakdown also means extended downtimes, production loss and costly repairs.
With input power costs increasing, the selection of quality components from energy-saving compressors right down the line is critical to ensure reliable, efficient and cost-effective operation.
System maintenance and repair services such as those offered by kaishan australia are a great investment in the sustainable, peak-performance operation of all types and makes of compressed-air equipment.
Kaishan Australia Pty Ltd 1300 098 901 www.kaishan.com.au
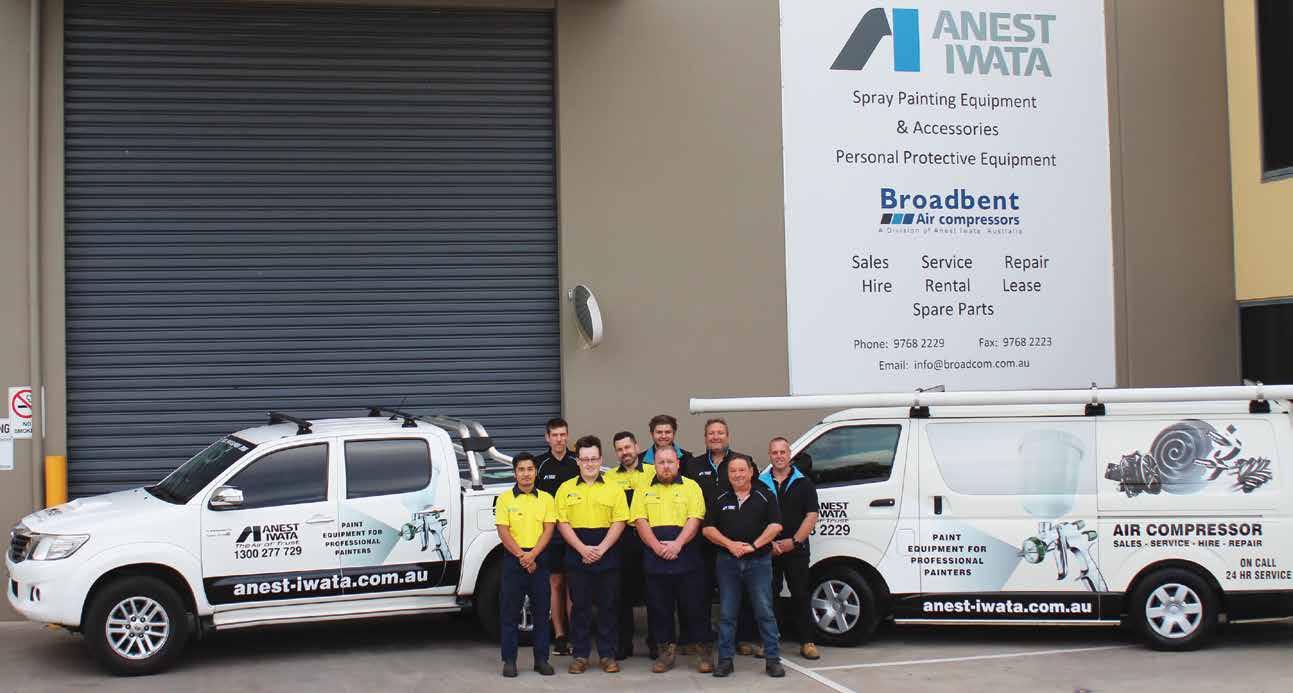
SMC helps Fletcher International Exports realise energy savings
From humble beginnings in 1967, Fletcher International Exports has evolved into what can best be described as one of Australia’s greatest agribusiness success stories.
Founder Roger Fletcher established the business by purchasing sheep from sale yards and selling them on auction. While much of this private, family-owned business still revolves around lamb and sheep farming and processing, Fletcher has since developed a range of high-quality co-products, ventured into grain exports, and has purchased a company-owned train to assist with logistics.
Fletcher operates from two facilities in Dubbo (New South Wales) and Albany (Western Australia); combined, these plants process up to 90 000 sheep per week. Speaking to the forces at play, Gabrielle Ryan, Project Manager at Fletcher, says the industry is privy to various interwoven and uncontrollable factors. “We face ongoing challenges around climate conditions, livestock supply fluctuations, international markets and currencies, competition, geo-political factors and increasing operating costs.”
In addition, the notable increase in the average weight of a sheep carcass meant that Fletcher had to evolve to accommodate changing processing demands. Explains Gabrielle: “The more kilograms per animal, the more meat needs to be processed, packaged and refrigerated which in turn requires investment in additional capacity. Adding to this is the rise in ‘quick serve’ restaurants and changes to portion sizes.”
To accommodate this, the company expanded and upgraded its facilities in terms of processing machinery, chilling, and refrigeration plants - all while keeping overheads front of mind.
Energy-efficient upgrades
Naturally, energy saving is a key driver for a progressive company like Fletcher and therefore working smart, mindfully and ethically remains top priority. “Our Dubbo plant is 32 years old, and we have spent the past few years identifying and analysing where we can improve on energy savings and enhance processes,” explains Gabrielle. “We had to renew our strategy and vision and invest to make a real change. Once we started seeing results, we wanted to find more ways to reduce our energy consumption.”
Fletcher turned to SMC Corporation Australia New Zealand (ANZ) to help them along their energy saving journey. SMC has spent years cultivating a customer-centric business where solutions are developed around customer needs – rather than the other way round.
Bill Blyth, SMC Energy Conservation Group Manager, heads up the energy-saving task team and explains that they work closely with customers to find sustainable solutions based on exact requirements. “More than ever, solutions need to be efficient. Efficiency keeps us competitive.”
Most of the work was focused around analysing and updating existing factories and processes.
In relation to the partnership, Bill says SMC has been collaborating closely with Fletcher’s for some time to help bring their energy saving vision to life. “From our early discussions, it was clear that Fletcher’s wanted to lead the way in terms of efficiency. We knew that we were in it for the long-haul and that our vision wouldn’t be achieved overnight.”
He adds that every change requires resources and funding. “SMC worked closely with the team on site to understand the most cost-effective approach and to establish a plan that would see improvements introduced in an efficient and costeffective way. In addition, SMC worked closely to support Fletcher’s with accessing Government funding for energy reduction projects.”
Realising savings
Mick Toovey, Maintenance Manager at Fletcher, worked closely with SMC throughout the two-year process. “Compressed air is costly,” he says. “SMC conducted a full audit on our air systems which gave us further insights into possible savings. In fact, our air compressor is now down from a 165kW compressor to a 110kW compressor following the improvements we have made.”
Mick says the savings have been substantial. “We have saved around $65 000 per annum on our energy bill!”
Best of all, Fletcher has continued to increase their production without compromising on their bottom line.
Bill says: “While the ultimate value lies in the bottom line, it really is about working smarter to support the maintenance and operation teams. Fletcher is committed to providing a cleaner and greener footprint both locally and globally, and to sustain this. This makes it an ongoing project of continuous improvement.”
“SMC energy saving components are embedded into the site processes at all levels, supported by a site maintenance team that is committed to retaining the efficiencies. We have also installed Air Management Systems (AMS) across the site to ensure energy efficient compressed air consumption as the plant grows.”
Components installed include: EX600 Ethernet manifolds and sensor interfaces, many standard ISO air cylinders and fit for purpose; MGPM, CG1, CG5 and CS1 air cylinders, including specially (Australian) designed guided rodless cylinders, air preparation, flow and pressure monitoring, vacuum components, rod lock cylinders for precision positioning, analogue cylinder position sensing, SY valve manifolds and proportional control valves and smart valve positioners. These are standard SMC products but when used in the right combination and when correctly selected and configured to each application, they become powerful energy saving tools within the business.
On project highlights, Gabrielle says: “A highlight was the installation of metering across the site. This was a huge job, but it now allows us to understand our plant’s inner-most workings in real-time. To give you an example, we installed over 30 water meters across site during the peak of the drought when our town’s water supply was sitting well below 1%. The metering enabled us to slash water use by 30% because we understood how and where it was being used. We now look at energy saving holistically and consider all aspects of the plant for potential savings.”
Gabrielle was pleasantly surprised about the scale of energy efficiency during this project. “I don't think we understood just how much we could improve coming into this. From fixing leaks, to installing air booster systems and introducing zoned pressure and flow control systems, our compressor load has been dramatically reduced. As the utility price continues to rise, and our production output follows suit, we have a responsibility to continue improving our energy footprint.”
The new approach has put Fletcher in a strong position to cope with rising costs and increasing global competition. The company exports over 95% of its produce to more than 90 countries and sees more developments on this front in future.
SMC Corporation Pty Ltd 9354 8222 smcworld.com
