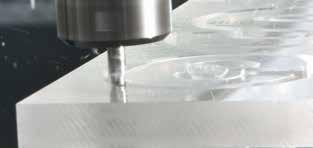
16 minute read
MACHINERY

Commissioning of Eilbeck’s new vertical lathe a smooth process with Applied’s expertise & support
Advertisement
If one was to nominate an Australian company that epitomises success in manufacturing, Eilbeck would have to be a lead contender.
With close to almost 115 years of experience in the manufacturing sector the family-owned company is today managed by Owner/Director Tom Eilbeck. Today the company’s staff numbers have increased to around 300.
It is now into its 4th generation and has grown through sheer hard work, capitalising on market opportunities and an overarching commitment to producing the highest quality equipment. This high level of quality has been reflected with repeat orders from many clients – both from the public and private sector.
Initially starting as a foundry on the Swan River in West Australia the company evolved into a machine shop and eventually into designing and building overhead cranes. Today Eilbeck Cranes has around 65% of the local overhead crane market, supplying to a diverse range of industries including civil and industrial developers. In the bespoke crane market, their share increases to around 75%.
The company has now come full circle, building a state-of-the-art CNC machining workshop in 2015 to complement its existing engineering, fabrication and welding skills gained from manufacturing components for the standard crane range. This bespoke new machining shop operates as a separate division under the banner of Eilbeck Heavy Machining and is managed by Tom Eilbeck’s son Charlie.
Up until 2015 all the components for their bespoke cranes had been contracted out to local machine shops; the new machine shop would allow Eilbeck to bring this work back inhouse and importantly provide the opportunity to tender for large-scale machining work.
“One of the key attractions for customers is that we can offer a full turn-key solution given our capabilities extend to design and engineering, fabrication, painting, welding and the mechanical side of any job. This capacity makes us an attractive proposition to the contract engineering and manufacturing sector,” Charlie Eilbeck said.
“We have purposely targeted large-scale work where there is less competition in the market; essentially big projects that were previously tendered out to overseas suppliers. We can handle work up to 200 tonnes and have some of the largest, most advanced CNC machines in Australia and we only ever purchase the very best brands,” Mr Eilbeck went on to say.
The mining industry, shiploader and rail mounted machines, rail equipment and other major projects are just some of the sectors that Eilbeck’s machining expertise is utilised.
Such has been the success of the CNC machine shop that the company has recently completed a second CNC heavy machining facility. This 6,000 sq metre block incorporates a 3,000 sq factory which houses some of the newest, largest and most precise CNC machine tools in Australia. This is complemented by dual 160 tonne overhead travelling cranes. Along with the existing facility, this has made Eilbeck one of the largest machining shops in Australia.
“We saw a big opportunity in the large vertical turning market and that’s where our hunt for a heavy-duty CNC vertical lathe started. Like many of our machine purchases we didn’t have worked lined up – we bought it anticipating we would secure work; that’s the way we do things, and it always works out well for us,” Mr Eilbeck said.
“Applied Machinery had tendered for some other machines, and we found they always presented well so we gave them the opportunity to quote on this large new lathe with the Hwacheon brand they represented.
“We already have a couple of conventional manual Hwacheon machines, so we knew the brand. They’re quite renowned for their vertical lathes and have a good reputation in the market which is why we ultimately ended up opting for the Hwacheon brand,” Mr Eilbeck went on to say.
The model selected was the heavy-duty VT-2000 model - a ram type vertical lathe with an 80″ chuck which provides optimum machining conditions and performance for large size heavy duty workpieces.
“I take my hat off to Applied Machinery – they did a really good job throughout, from managing the whole purchase process from machine selection, agreement on specifications through to training and commissioning. Their staff were always available to answer any question or fix any issue.
“Hwacheon were also very impressive. They sent a team of engineers and technicians overseas from Korea to do the entire installation and commissioning over a period of weeks. This was made even more challenging given the Covid 19 situation and the need for 14 days quarantine,” Mr Eilbeck said.
“As an OEM they excel in their support. I was very impressed with the fact that after the commissioning they kept one of the key engineers with us for three weeks to iron out any teething issues whilst we trialled different jobs through the machine. It’s actually been one of the smoothest commissioning of any machines we’ve had,” Mr Elibeck added.
The Hwacheon is being used to machine a variety of different parts including rope drums, mining equipment and brake discs for global OEMs.
“We’re very happy with the performance of the machine so far; it’s actually been one of the smoothest commissioning of any machine we’ve had. Given the quality of their advice and excellent service, I’ll certainly look at using Applied Machinery again for any future machine purchases,” Mr Elibeck concluded.
One of the outcomes of the Covid pandemic is the recognition of the importance of nurturing and assisting local manufacturing. This is reflected in the huge support that the Government is providing Australian manufacturers to encourage greater investment and the push to ensure major projects remain in the country – something that is benefitting Eilbeck.
A new block of land has been purchased in Wollongong which will house a factory that will be dedicated to heavy fabrication, painting and assembly. This will complement the existing eight factories around Australia.
With the extensive support the government is providing to Australian manufacturers, ongoing investment in new factories and machines and a can-do attitude to taking on all kinds of large projects, the future for Eilbeck Heavy Machining looks bright.
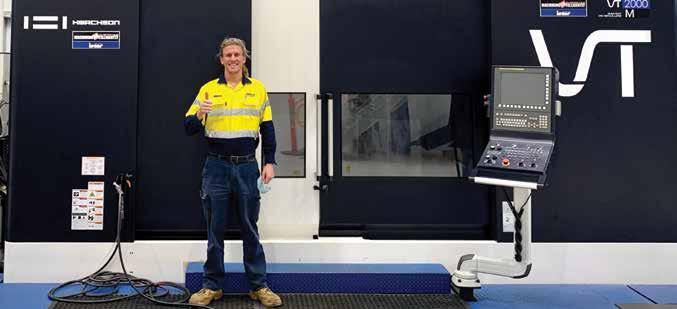
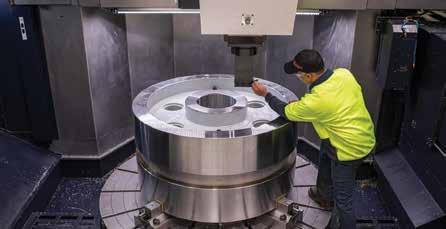
Applied Machinery 03 9706 8066 appliedmachinery.com.au
Tool presetters key to quality and productivity
Through their ability to precisely measure any tool off-line, with micron accuracy, tool presetters boost productivity and improve quality. Machine uptime is optimised and tool life is maximised, as a CNC machine is able to keep cutting.
Tool presetters provide three key features in the one machine: measuring, presetting, and inspecting tools. They save set-up time, improve accuracy and produce better quality parts while minimising scrap.
A state-of-the-art image processing system measures the cutting edges of tools in seconds, then saves and documents the measurement results so time-wasting fine adjustments are a thing of the past.
Adjustable boring bars can be easily set with micron precision in less than a minute, which in turn eradicates frustrating “trial and error” cutting. Tool run-out can also be checked and cutting inserts inspected using the on-board inspection camera.
“Presetting and measuring allows for shorter fitting times and greater productivity. While your machine works you can get the next tool ready. Thanks to correctly preset tools, the very first part will be of the highest quality. You can also be confident the tool will perform perfectly until the end of the tool life, thereby minimising the chance of rejects,” said Dimac Managing Director Paul Fowler.
Dimac is the sole distributor for Zoller; acknowledged as the premium manufacturer of tool presetters. Zoller is a German brand founded by Alfred Zoller; the company is still run by the Zoller family – now in its third generation. Since 1968, more than 28,000 presetting and measuring machines as well as tool measuring machines with worldwide unrivalled software solutions have been sold. Zoller also markets a range of EZset tool presetters.
Dimac has had a long, successful association with the company, which started when Mr Fowler met Christoph Zoller at Austech in 2007. Following a number of discussions, Mr Zoller was confident of Dimac’s ability to successfully market their brand in Australia and New Zealand and Dimac was duly appointed sole distributor for the EZset range.
EZset are assembled with high quality brand name components, such as Bosch pneumatic components, THK guides and Heidenhain Glass Scales to ensure a long, maintenance-free lifetime. Equipped with image processing based on the newest technology available, a precise tool mounting spindle and numerous measurement functions, EZset
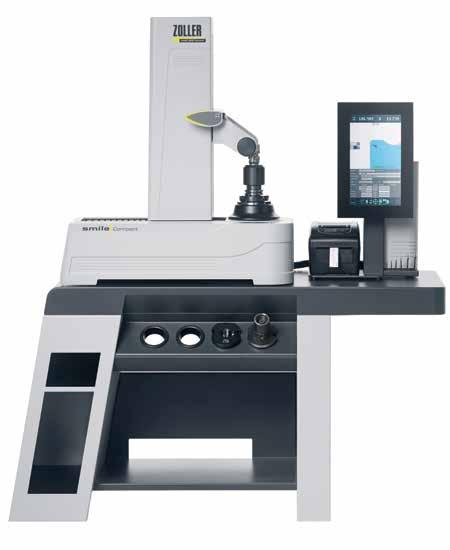
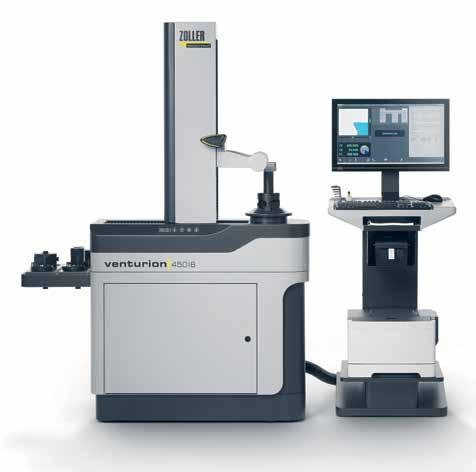
sets the benchmark in cost effective tool presetting outside of a CNC machine tool.
“Right from the start, the working dedication, eagerness to learn the product and focus on our brand gave me a very good impression of Mr Fowler and his business. Over the years we have met numerous times at trade shows where our relationship has strengthened. Having successfully marketed our EZset brand it made perfect sense to award distribution of our premium Zoller band to Dimac for both AUS and NZ markets,” Mr Zoller said.
Regardless of the model chosen, all Zoller presetters feature the highest quality components that include a high-precision freely accessible tool holder spindle, state-of-the-art optics, leading image processing technology and comfortable and easy to use ergonomic control units.
“We’ve been distributing German manufactured tool presetters for a number of years and these have enabled many CNC operators to improve their productivity and quality. Offering the choice of both the EZset and Zoller range ensures we can cater to all market segments; no matter what your requirements or budget, we are confident we will now have a presetter to suit your needs perfectly,” Mr Fowler went on to say.
In addition to offering an extensive range of models, both EZset and Zoller offer extensive hardware and software options to suit individual operators’ production needs.
Both brands have a range of optional features that includes a direct link via ethernet to various CNC machines. This facilitates the direct transfer of a measured tool’s library of results, thus eliminating the potential of damaging data entry errors.
“Precisely measured cutting tools deliver at least a 15% increase in productivity in your manufacturing processes. The initial investment in a tool presetting device is quickly returned through the increased productivity, higher quality and less waste. They are easy to operate and will save a company time and money,” Mr Fowler concluded.
Dimac Tooling (03) 9771 6121 www.dimac.com.au
Strong Representation With Heritage Connection
Australian-owned PBE-Roboplas has for more than two decades provided equipment, service and support for the nation’s plastics industry, helping processors increase efficiency and optimise productivity.
The Sydney-based company sells and services a broad range of plastics machinery and ancillary equipment, including injection, blow-moulding and extrusion machines, drying and dehumidifying, loading, dosing and mixing and robotic and automation equipment.
The range also includes temperature control systems sourced from noted European manufacturer Tool-Temp.
Headquartered in Switzerland, Tool-Temp designs and makes high-quality temperature control equipment for manufacturing industries.
PBE-Roboplas co-director and sales manager Gerald Frutschi said the Tool-Temp range comprises more than 60 standard models catering not just for plastics processing but a wide cross-section of Australian manufacturing industries, including the rubber industry, food production, pharmaceutical and chemical applications, die casting and print finishing.
Mr Frutschi said PBE-Roboplas’ range of ToolTemp industrial fluid thermal management equipment is critical for manufacturers seeking to achieve optimum results in terms of quality and economic efficiency and in turn maximise the full potential of production.
“Reliable temperature control is an important element in the manufacturing process and Tool-Temp is a world-class brand,” he said. “Anybody who has previously used one, knows it’s a quality machine.”
PBE-Roboplas can supply and service Tool-Temp cooling units with an operating range from -25°C to +40°C, water and universal temperature control units (up to 90°C), oil temperature control units (up to 360°C) and pressurised water temperature control units (up to 160°C).
Mr Frutschi, who heads up PBE-Roboplas with co-director Shaun Parker, who manages after sales and service, said the Tool-Temp equipment is designed to provide the best conditions for continuous use in diverse applications as well as ease of operation and maintenance.
“Reliability is the key with manufacturing equipment,” he said.

“The machines that we sell today, we won’t see them back for a service for a very long time. But when it does come time for servicing or changing components, they are very accessible and not difficult to disassemble.
“The equipment is manufactured in a way that is maintenance free but service friendly.”
Mr Frutschi said as well as supplying new ToolTemp units, PBE-Roboplas carries a comprehensive range of spare parts, ensuring a rapid response to any maintenance or repair issues.
PBE-Roboplas, founded in 1997 by Mr Frutschi’s father Francis and Paul Blunschi, has a long association with Tool-Temp, a relationship based in part on a shared Swiss heritage and similar commitment to customer focus.
“We have been representing them in Australia for more than 20 years,” Mr Frutschi said.
As well as the Tool-Temp range of temperature control machines, PBE-Roboplas also represents Yizumi injection moulding machinery, Wemo, Crizaf, Enmair, Sinco, Ferlin and Pure Oil.

PBE-Roboplas 02 9674 6511 pbe-roboplas.com.au
2/6 Taronga Place, Mona Vale, NSW 2103 www.serpent-dove.com.au
SLM Revolutionises 3D Metal Printing
How new ‘Free float’ software will be saving the space, aerospace and the energy sectors significant time and money
Laser melting leader, SLM Solutions GmbH, have just launched ground-breaking new software. A crucial development in 3D metal printing, it allows products to be built with reduced support structures.
Since the 1990’s a 3D metal part being built required support structures in a design as they provided support for overhanging sections as well as playing a vital role in the cooling process absorbing and distributing heat away from the component.
SLM’s advanced technology in 3D metal processing has now reduced support structures by setting ‘parameters’ at the design stage. The advantages are a reduction in metal powder, significant time saving on the build and reduced post processing time.
SLM Solutions released an industrial level 3D metal printer earlier this year, the NXG XII 600 that has
been quickly purchased by leading manufacturers in Europe.
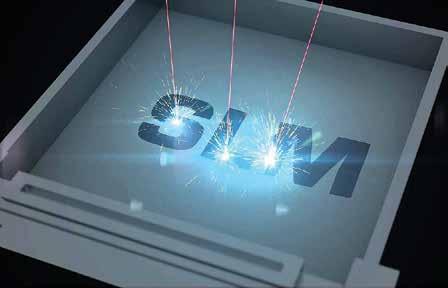
Now, the new Free float software provides industries such as space, aerospace and the energy sector - users of Inconel and Titanium, with cost effective solutions and reliability from a system with real technological advantages in part production.
“This new technology is another milestone, not only for us but for the entire industry. As a high-tech company, we are once again shaping the face of additive manufacturing with this product launch,” said Sam O’Leary, CEO of SLM Solutions announcing the launch.
Already installed across Australia, SLM Solutions machines are distributed, supported and serviced by Raymax Applications Pty Ltd located in Sydney.
Raymax Applications Pty Ltd 9979 7646 www.raymax.com.au
Washing Plants. Intelligent, cost effective plastic recycling solutions for Australian industry. That’s Applied Thinking.
Genox Washing Plants are high performance recycling systems for rigid or flexible plastics from various sources, including materials with high contamination levels. These modular systems are capable of processing general plastics including HDPE & PET bottles, PP woven bags and PE film (post-consumer or agricultural). • High speed washing system with corresponding speed according to material type • Under-water force-washing paddle maximises washing efficiency. • Minimises the recycling water flow rate and evaporation losses • Mechanical and thermal drying system minimises the moisture of the end product • System automation to ensure components actions are linked, system capacity is maximised and protected against interfering material • Repelletising system can be fully integrated into the plant to deliver high quality, high purity pellets that are ready for immediate sale into local and global markets.
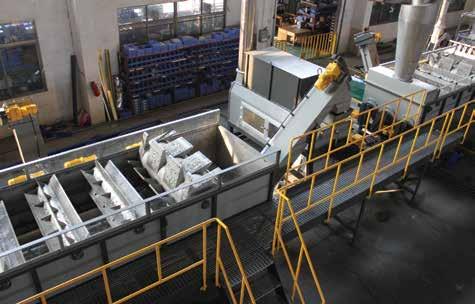
To find out more, call: 03 9706 8066, Email: sales@appliedmachinery.com.au, or visit: www.appliedmachinery.com.au
Effective Repair Using Laserline Cladding
Repairing worn or damaged parts instead of replacing them is common practice. Parts don’t last forever but it is possible with laser technology to repair a part exposed to corrosion, wear or damage and even give it a longer life. A reliable repair process is called ‘cladding.’ Cladding a damaged or worn part occurs where the laser beam directs metal powder to the identified site under highly controlled conditions. The process can reinforce damaged sections of very large parts and even to small parts that may otherwise have been difficult to repair.
Lasers are used for a range of purposes across different industry sectors. Leading this usage is Laserline GmbH, a German company with over 20 years of development expertise in designing high power diode lasers for applications in welding, heat treatment and cladding. Distributed here by Raymax Applications Pty Ltd in Sydney, Laserline has over 5,000 installations across the world for general welding, heat treatment, brazing and cladding. They are found in sectors such as the car industry in Korea where lasers are used in the manufacture of Audi Q3 vehicles, to the North Sea for removing biofouling on ships, and for the repair of defence aircraft in Melbourne. Engineering workshops across Australia use Laserline high power diode lasers especially for cladding repairs of large parts from oil rigs, vehicles and even turbine blades, to name a few areas where repair is cheaper than replacement.
Laser cladding occurs by using the laser to generates a heat source. This melts the surface of the workpiece in a very localised spot forming a molten pool, by applying short but intensive energy inputs that do not cause deformation yet are sufficient for melting. Management of the process during operation is possible as the energy input can be fine-tuned controlling the surface heat. A coating material, either as powder or wire, is added to the molten pool. This coating material is melted, fusing it with the original. Once cooled, a solid fusion compound of the two metals, or metallurgical alloy, remains securely bonded to the structure. Diode lasers offer the best results in the cladding process due to the ‘top-hat profile’ that generates a uniform energy input ensuring uniform surface treatment. The fusion between the base stratum and coating material provides a significant advantage as the metallurgical joins are very robust and add life to the repaired part.
The extent of laser cladding examples can be found in agriculture, cylinder repair in the mining industry, and even coating on heat exchangers. Agricultural field vehicles where traditional carbide layers that protect saw blades, disc harrows or counter blades from wear and corrosion can become damaged. Diode lasers can vary the coating thickness while reducing distortion of the part by forming a ‘quiet’ molten pool using minimal heat, still resulting in effective repair even extending the part working life. A growing market is seen in laser coating of hydraulic cylinders used in technical mining facilities such as coal extraction. The original coating on a cylinder corrodes very quickly exposed to the localised atmosphere and can lead to leaking. Until now chrome plating was the primary method used but this process is being replaced due to the durability of laser coating. Protection against highly corrosive gases or liquids that come into contact with metal heat exchangers during usage can affect the part life. It is possible to apply a thin repair coating to extend the product life. This same treatment can be used in incinerator plants where the metal structures has been attacked by chlorine. Cladding treatment of these items is a far more economical way to go.
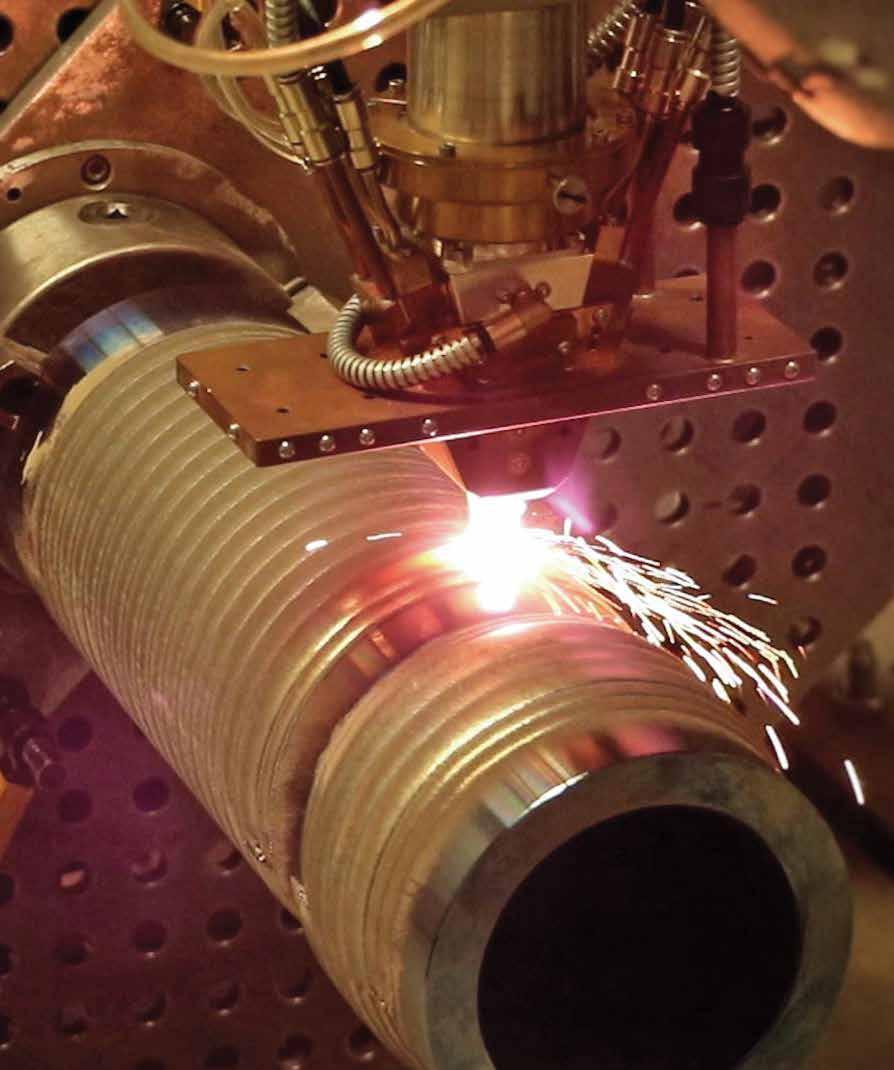
Raymax Applications Pty Ltd 9979 7646 www.raymax.com.au