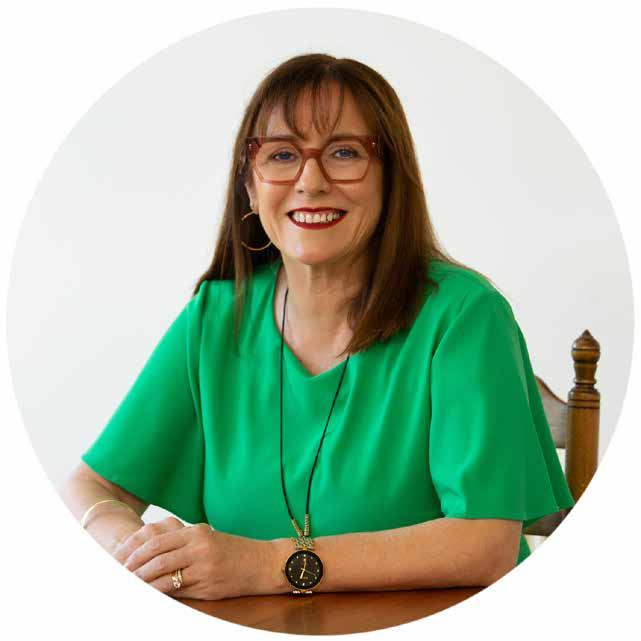
10 minute read
SAFETY
Improving workplace psychological health
By Marie Kinsella
Advertisement
Since the impact of Covid-19 there has been an increasing focus on people centric policies in workplaces across all industries.
Companies who demonstrate that they care about positive mental health and wellbeing of their employees, attract and keep the most talented staff.
Understanding the science A key focus of the dynamic Education Program in the upcoming Workplace Health and Safety Show, 25-26 May 2022 in Melbourne is promoting psychological health and wellbeing.
Appellon founder Sue Jaunsey is presenting at the collocated AIHS National Conference on psychological health. It is imperative that leaders and management teams understand the science behind what constitutes a happy workforce. Sue will provide a presentation highlighting the importance of understanding the body of evidence that exists within the discipline of behavioural and neuropsychology.
If we create a workforce environment based on achievement and connection, intrinsic self-worth is a natural outcome and stress and anxiety decreases. When stress and anxiety decrease, employees can access creativity and are more able to see the solutions and opportunities available to them.
Also featured in the co-located AIHS National Conference is Culture Smart CEO, Karen Walker presenting on employees co-creating their workplace wellbeing strategy. Recent research by Deloitte found that the highest return on investment in workplace mental health and wellbeing initiatives are those tailored to the needs of teams.
It’s people who collectively create healthy and safe cultures, and teams working together who can deliver such a high return on investment – average of $7 for every dollar spent – on their team’s mental health.
Wellbeing in the workplace is far more than an on-trend buzz word. The World Health Organization (2014) defines wellbeing as “a state in which the individual realises his or her own abilities, can cope with normal stresses of life, can work productively and fruitfully and is able to make a contribution to his or her own community.”
Presenting at the free Education Program held within the Workplace Health and Safety Show Melbourne is Mental Health First Aider, Carli Phillips. Her offering includes a simple, easy to follow corporate wellbeing checklist, tips to make your program super-efficient, and action plans with ideas for a wellbeing calendar to ensure a mentally healthy workplace.
Looking after each other’s health not only contributes to a better workplace and indeed a better society, it also returns better economic outcomes. Money spent in the area of improving mental health for employees should be treated as an investment not an expense. IU
International Exhibition & Conference CEO Marie Kinsella, has told Industry Update that wellbeing in the workplace is far more than an on-trend buzz word.
Weld Australia supports local electric bus investment
Weld Australia fully supports the award of a $70 million New South Wales Government contract for electric buses to a western Sydney manufacturer.Weld Australia is the peak body representing the local welding industry.
On Tuesday, NSW Premier Dominic Perrottet announced that another 79 electric buses would be ordered from Custom Denning, as part of its commitment for the state’s fleet of more than 8,000 buses to go green by 2030. This takes the Government’s total order to 100 vehicles.
Weld Australia has long urged all state governments to support local manufacturers, welders and fabricators in their procurement processes. Local procurement has the power to create thousands of jobs, a solid local supply chain, and an industry equipped to export world-class vehicles all over the world.
According to Weld Australia CEO Geoff Crittenden, “There is a real opportunity for the state governments to invest in creating a robust, resilient manufacturing industry that can compete on the world stage.”
“State government procurement practices that support local welders and fabricators will create thousands of jobs, supporting local economies in a post COVID-19 world. This contract with Custom Denning is expected to result in the employment of 40 new apprentices, plus many more skilled tradesmen.”
“With a long-term procurement commitment from the state governments, Australian manufacturers will have the confidence to reinvest in their own capabilities, strengthening the industry from within. This type of business innovation strengthens businesses and creates new and better jobs, which together support a move to higher living standards. Innovation investment by business is crucial to our ongoing prosperity.”
According to Crittenden, in recovering from the COVID-19 pandemic, this type of economic expansion is essential; both the Federal Government and the Reserve Bank of Australia have emphasised how important it is for state governments to spend money.
“And yet,” he said, “Our state governments consistently spend our money overseas.”
“For example, all of New South Wales’ trains are manufactured overseas; the $900 million Waratah 2 trains are being fabricated in China, the $2.3 billion Intercity fleet of trains is being fabricated and built in South Korea, and the inner west light rail trains were built in Spain.
Incredibly, services on the inner west light rail only just resumed over the weekend after they were suspended in November, because sizeable cracks were discovered in the fleet.”
“Worth well over $4 billion, had these three projects been awarded to local fabricators, they would have created thousands of jobs in New South Wales alone, and seen the development of cutting-edge new technology.”
“Offshoring manufacturing, welding and fabrication work to China, South Korea and Spain weakens Australia’s economy.”
“If all our state governments adopted a nationally consistent procurement process that considered whole of life costs and prioritised local content, not only would it create thousands of jobs, it would deliver better quality public transport. Locally fabricated trains would adhere to all relevant Australian and international Standards, reducing expensive rework and repair. Cheap imports from overseas often cost more in the long run,” Crittenden added. IU
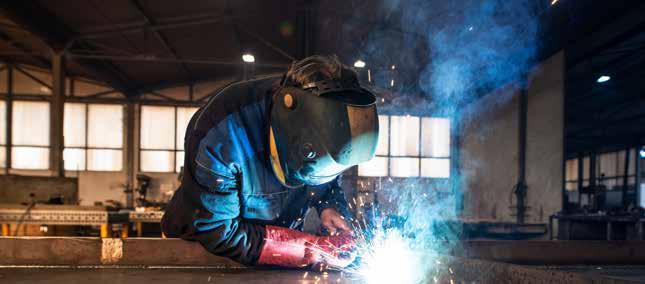
Weld Australia said a nationally consistent procurement process would create thousands of jobs.
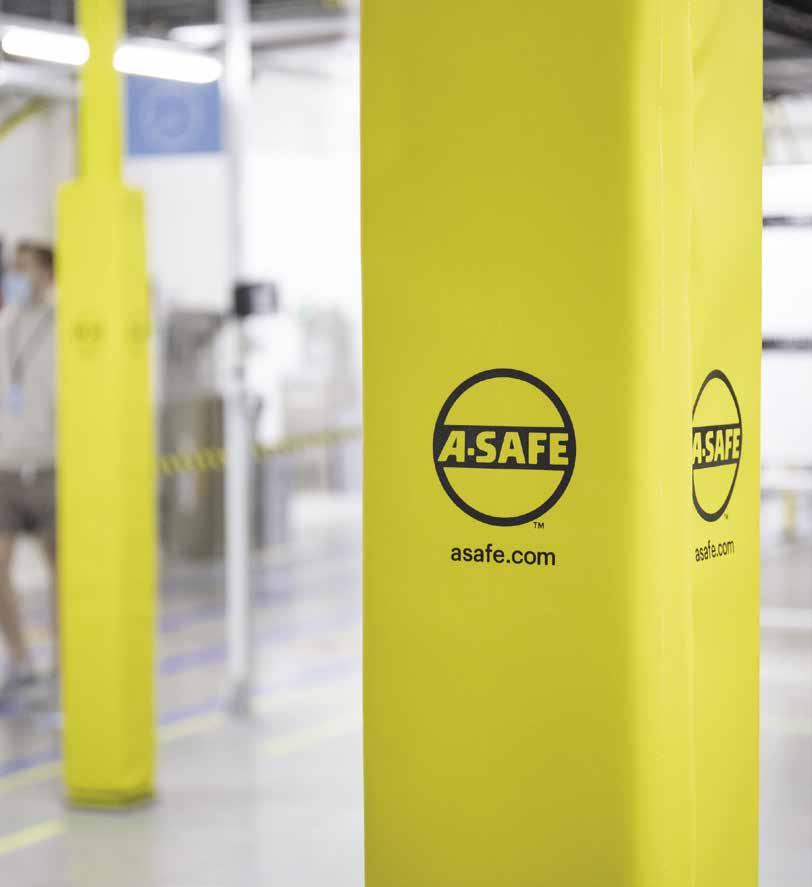
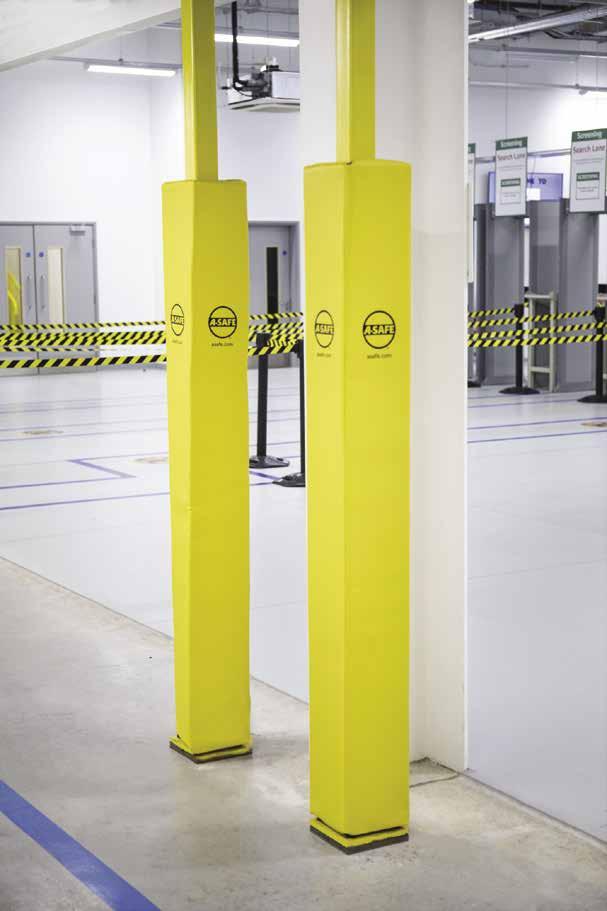
Preserve and protect your people Preserve and
The A-SAFE Padded Column Guard protects your employees from injuries caused by protect your people collisions with columns and other solid vertical structures. With a durable, high-visibility cover to provide a clear visual warning, while a soft foam core absorbs impact in the event of a collision. The A-SAFE Padded Column Guard protects your employees from injuries caused by collisions with columns and other solid vertical structures. With a durable, high-visibility Bespoke to suit any column width, the Padded Column Guard provides 360-degree cover to provide a clear visual warning, while a soft foam core absorbs impact in the protection from floor to head height. With a maintenance-free, event of a collision. hygienic cover material that is easy to clean, resistant to water and chemicals, as well as being UV-resistant to prevent fading. The Padded Column Guard is a perfect cost effective solution to any Bespoke to suit any column width, the Padded Column Guard provides 360-degree pedestrian area. protection from floor to head height. With a maintenance-free, hygienic cover material that is easy to clean, resistant to water and chemicals, as well as being UV-resistant to prevent fading. The Padded Column Guard is a perfect cost effective solution to any pedestrian area.

Manufacturing CEOs
UK factory workers want to upskill

aim for resilience R esearch has revealed that 80 percent of UK manufacturing employees desire to upskill in 2022, while the government hopes reskilling workers will create business growth. As a result, the UK government has opened the ‘Skills for Life’ campaign, for employers to increase their growth by reskilling their workforce. The campaign encourages employers to upskill their workforce, in preparation for post-pandemic economic recovery.
CEO’s within the global manufacturing sector will focus on resilient supply chains and tech transformation in response to continued uncertainty according to KPMG's Global Manufacturing Prospects 2022 report.
KMPG surveyed almost 150 CEOs in manufacturing companies in 11 countries in Europe, North America and Asia-Pacific. Three quarters are at companies with annual revenue of $1 billion or more.
More than two thirds of CEOs told KPMG that they aim to ensure their supply chain is resilient in the event of a major global disruption in the future. Their main operational priority is to invest in the digitization and connectivity of all functional areas in order to achieve growth objectives over the next three years.
Meanwhile, 67 percent responded that the overall objective of their organization is the long-term value for shareholders, almost five times more than the number focused on economic returns.n
It appears that the pandemic, climate change and geopolitics are driving manufacturing executives to focus even more than before on a twin transformation: smart digitization and a focus on environmental, social and governance (ESG) goals, according to KPMG.
It appears that CEOs at manufacturers have learned two important lessons from the pandemic: the vital importance of a resilient supply chain and the need to invest in new technologies to strengthen resilience, by both avoiding business disruptions—and taking advantage of them. If manufacturers take timely actions to ensure a healthy supply chain, it may enable manufacturers to withstand economic shocks in the future and improve competitiveness. Among the main findings of the survey: • Supply chain risk is seen as the greatest threat to the organization’s growth. More than two thirds (68 percent) of CEOs say they aim to ensure their supply chain is resilient in the event of a major global disruption at some point in the future. • The top way to mitigate stress on the supply chain is to extend their company's monitoring deeper into the supply chain to anticipate changes before they have a severe impact. • The main operational priority to achieve growth objectives over the next three years is to invest in the digitization and connectivity of all functional areas. • The pandemic caused CEOs to ponder deeper questions: 77 percent say they feel a stronger emotional connection to the purpose of their company since the pandemic began. • ESG goals, however, are not seen primarily as a tool for growth by the CEOs surveyed. A sizable minority (31 percent) said a focus on
ESG improves financial performance, but 54 percent said it has a neutral effect. Above all, 92 percent believe that conveying a sense of purpose will have the greatest impact on customer relationships. • Of environmental, social and governance issues,
CEOs are focusing more on the second of these, in response to the pandemic. But they are not ignoring environmental goals; 71 percent do see
“global challenges,” such as income equality and climate change, as the biggest threat to longterm growth. IU
In a Censuswide survey of 4,000 people, the results showed: • 69% of people wanted to increase their job satisfaction in 2022 • 67% said the key to achieving their work goals was through gaining new skills • 28%of workers said that ‘opportunities to learn’ were top goals
Manufacturing workers are most keen to explore: • IT (20%) • Finance (16%) • Business (16%)• Sustainability (11%)
According to Heineken UK managing director David Flochel, recent demands within the food and drink sector have been immense. “Having robust skills programmes in place has enabled our colleagues to adapt and thrive over the last two years, despite all the challenges of the pandemic. Skills opportunities can make a real difference for everyone, regardless of the stage of their career.”
David Flochel added that the Skills for Life campaign also provides a route for anyone to develop skills which can improve their life, through enhancing their career options. A focus on skills which are transferable across roles, employers and industries are a top priority for the development of everyone in Heineken.”
“Our Advanced (L4) and Higher (L6) apprenticeships continue to prove invaluable to develop workplace-ready talent in emerging technology disciplines. In addition to recruiting new apprentices, Ford is leaning into senior (L6-7) apprenticeships supporting a major programme of new-technology up-skilling of existing employees, as the automotive industry moves further into electrified and connected technologies,” Slatter said. IU
Ford Motor Company chair Tim Slatter also explained that the company has an established history of developing apprentices.
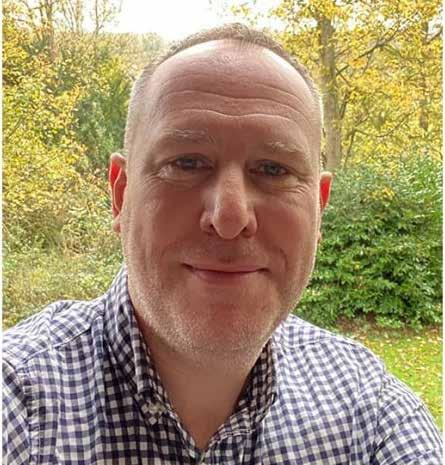