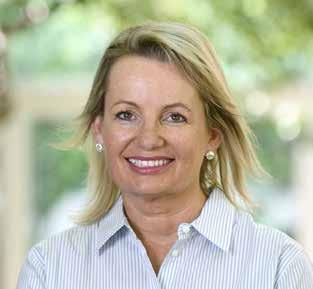
18 minute read
RECYCLING MANUFACTURING
The Government has elevated waste and recycling firmly to the national agenda and the micro economic reform that is now underway will be a game changer for business and the environment.
We simply can’t keep choking our landfills and waterways with waste, we can’t keep throwing aside valuable resources that could be re-manufactured into new products, and we shouldn’t ship our waste overseas to become another country’s problem.
Advertisement
These concepts are not new in themselves, they are things people have long been aware of, but that have been all too often put off until another ‘business day’, managed by states, local government and individual businesses with varying outcomes.
Co-investment
The Government has stepped in to create world first legislation to stop the export of the unprocessed plastic, glass, tyres, and cardboard, and signalled that we have arrived at that ‘business day’.
We have co-invested with state and territory governments, and with industry, to grow domestic recycling capacity to meet the 645,000 tonnes of waste that will need to be processed on shore as the export bans phase in. 86 Projects are already underway through our Commonwealth Recycling Modernisation Fund, a fund that was expected to generate $600 million in shared investment and which is now on track to exceed $800 million.
National waste and recycling targets are in place, we are funding national product stewardship schemes and we are driving public information campaigns promoting the value of products being “Remade in Australia.”
Recycling is no longer a ‘nice to have’, it is no longer something that we can stop thinking about once the ‘bins are put out’.
Recognising the opportunities that are created after that point is becoming an essential part of product design, manufacture, packaging, and management, and if that isn’t the case in your company, it is very likely to be in the near future.
Circular economy
The Government’s focus on what is so often described as the ‘circular economy’ is driven out of good public policy and good business.
By transforming Australia’s waste and recycling industry, we will support more than 10,000 new jobs–an increase of 32 percent in jobs in the waste and recycling industry–and divert over 10 million tonnes of waste from landfill every year. In addition, our economy will grow by more than $1.5 billion in Gross Domestic Product (GDP) over the next 20 years, and save 165 million tonnes of CO2 per year by 2040.
As we grow recycling in Australia, the challenge is to align the opportunities this sector presents with the way business and industry plan.
Product Stewardship provisions strengthened under the Recycling and Waste Reduction Act are about working with industry sectors to achieve that outcome and they include the provision to call out industries that don’t get on board. This is not the government telling industry what to do, we are investing over $25 million to help establish industry led stewardship schemes, which are about driving industry led solutions.
Already we have kick started schemes to recycle items that cannot be put in our kerbside recycling bins including batteries, clothing textiles, coffee cups, cosmetics, and soft plastic packaging. Improved long-term solutions
There is an urgent need to drive better long-term solutions for technologies and products that play a key role for our economy and our day-to-day lives, including solar panels, electric car batteries and the gamut of products used to make our homes and office buildings.
As an example, it is estimated that Australia will generate 288,000 tonnes of solar waste between 2020 – 2030. We need to prevent the valuable resources in these panels going to landfill and ensure they are used in new products.
This is not a pipe dream, we are already seeing recycling initiatives develop for products including farm plastics, sports equipment, sports shoes, food packaging, e-waste, tyres from the mining industry and used oil containers. Viable business solutions are out there, and it is in everyone’s interest to invest in this area now.
The Commonwealth’s ‘Remade in Australia’ campaign is an important reminder to look around and take note of the innovative recycling that is already part of our daily lives.
For industry it is also a compelling reminder to think seriously about the opportunities that lie ahead.
Recycling - the opportunity industry can’t afford to waste
Hon Sussan Ley MP, Minister for the Environment
Remanufacture NSW grants open until March
Round two of the Remanufacture NSW funding program is open until 5 pm Friday, 11 March. The program comprises two (2) streams - infrastructure and trials. This program provides co-funding for waste and recycling infrastructure to support industry to respond to Australia’s waste export ban. This program is co-funded by the Australian Government through the
Recycling Modernisation Fund and the
NSW Government through the Waste Less,
Recycle More initiative and is delivered by the NSW Environmental Trust in artnership with the NSW Environment Protection
Authority (EPA).
Program streams Remanufacture NSW has 2 streams: 1.Infrastructure 2. Trials
The purpose of Remanufacture NSW Round 2 is to offer funding up to $13.5 million to support the NSW resource recovery sector's response to changes brought about by the decision to ban the export of unbeneficiated waste plastic, paper and tyres. Remanufacture NSW ensures New South Wales leads by example and maximises recycling and reuse activities while keeping materials within the productive economy.
The program targets the following waste materials, which are subject to the export ban: • plastic• paper • cardboard • tyres
Under Stream 1 the establishment of new recycling infrastructure and equipment will be co-funded and includes, but is not limited to: • improving sorting technology and/or increased capacity for plastic, paper and cardboard products at materials recovery facilities (MRFs) • improving cleaning technology for plastic products at waste facilities increasing mixed plastics processing capacity • building capacity to process higher value single stream plastics such as PET (polyethylene terephthalate) and HDPE (high density polyethylene) • building capacity to process single stream plastics other than PET and
HDPE and compound materials • tyre recycling and reuse technology and infrastructure • increasing the use of recyclable and recycled materials in manufacturing and civil construction • mobile and stationary processing equipment.
Under Stream 2, innovative trials to address plastic, paper, cardboard and tyres will be co-funded, and include, but are not limited to: • trials that support the reuse of the waste export ban materials listed above • trials that aim to increase the capacity of manufacturers to use recycled material in their products and to provide secure markets for these recycled materials (examples include new/modified equipment to increase the use of
recycled • materials, such as post-consumer plastic, in the manufacture of goods or products) • trials that test new infrastructure/ equipment to sort, wash, dry, shred, flake, granulate or pelletise materials • trials that test equipment upgrades or process improvements to existing
MRFs to increase the quality of output materials, reduce contamination and/or increase capacity • trials that test upgrading plastic sorting, processing and manufacture technology to produce cleaner streams of plastic and have the potential to use larger amounts of recycled plastics • trials that test new methods of paper beneficiation so that local paper mills can accept higher volumes of paper and cardboard • trials that test new methodologies or technologies to process Liquid Paper Board • trials that test plastic processing, remanufacturing and new applications for recycled plastics • trials that test mobile processing equipment • trials that use new technologies or methods to reuse or recycle end-of-life tyres.
Funding available Grants of between $100,000 and $3 million are available to fund eligible Remanufacture NSW Stream 1 – Infrastructure projects, while Grants of between $50,000 and $1 million will fund eligible Remanufacture NSW Stream 2 – Trial projects.

Recycling transformation drives jobs in Victoria
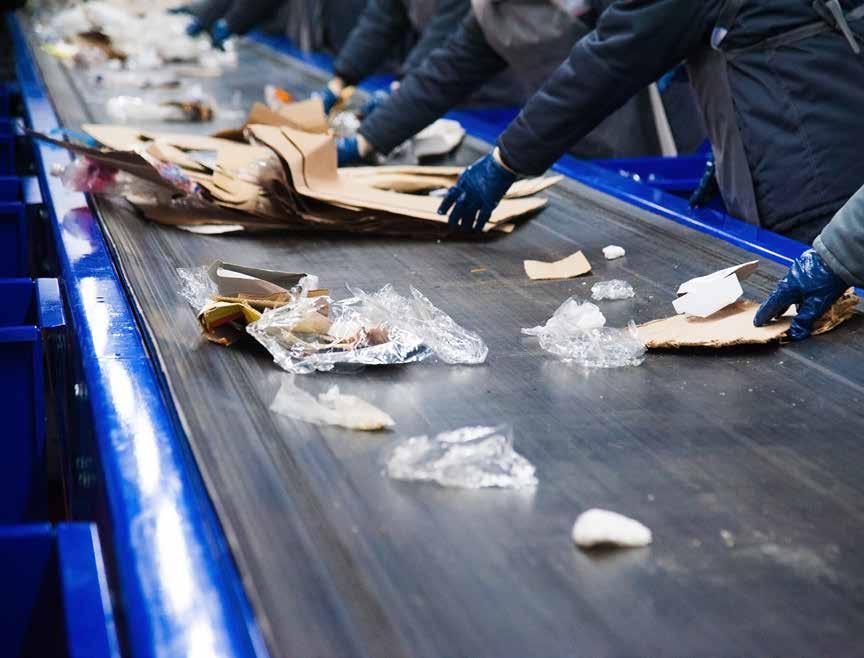
Recycling manufacturing will drive jobs in 2022.
The transformation of Australia’s recycling sector steps up another gear today with the Australian and Victorian Governments jointly announcing 13 new projects that will see 137,000 tonnes of plastics, paper, glass and tyres remade into new products while creating new jobs and new investment in the Victorian economy.
Federal Minister for the Environment Sussan Ley and Victorian Minister for Energy, Environment and Climate Change Lily D’Ambrosio announced $36.5 million in joint funding for projects under the Australian Government’s Recycling Modernisation Fund (RMF) and the Victorian Government’s Recycling Victoria Infrastructure Fund.
Minister Ley said the Morrison Government’s $190 million contribution to the RMF was facilitating unprecedented investment in recycling infrastructure, with the combined Commonwealth, state, territory and industry co-investment model on track to reach around $800 million.
“This latest round of projects includes a joint PET recycling venture that will process the raw plastic equivalent of one billion drink bottles each year to produce over 22,000 tonnes of recycled PET bottles and food packaging,” Minister Ley said.
“It also includes remanufacturing projects, new products that will re-make waste into garden pots, railway sleepers and corrugated pipe.
“The co-investment model is exceeding all expectations and showing that materials can be recycled and remanufactured to create new products and new jobs while helping our environment.”
The Victorian Minister for Energy, Environment and Climate Change, Lily D’Ambrosio said the new processing and remanufacturing technology would help create jobs, divert more recyclable material from landfill and tackle climate change.
“The thirteen funded projects announced today will enable Victoria to reuse over 137,000 tonnes of plastics, glass and tyres every year and have generated over $86 million in industry investment, giving a total value of $122 million,” Minister D’Ambrosio said.
“These projects will reduce waste to landfill and boost the local economy through the creation of 204 local jobs, in addition to other jobs generated indirectly through the construction and operation of these new facilities.”
The federal Assistant Minister for Waste Reduction and Environmental Management, Trevor Evans, said that the announced projects include two funded under the RMF’s regional and remote funding round.
“The Morrison Government is determined to overcome the city-country divide and ensure that regional communities can reap the same benefits of recycling their waste into valuable new products as their city counterparts,” Assistant Minister Evans said.
“These communities often have to send their waste long distances for recycling, making it harder to create opportunities for local recycling and remanufacturing.
“This means our RMF investments in new recycling infrastructure can make transformational differences to these communities – delivering local circular economies and creating and keeping jobs in the region.”
The Morrison Government is driving a $1 billion transformation of our waste and recycling industry to turbocharge domestic recycling so we can process in Australia materials that were previously sent overseas.
The $190 million Recycling Modernisation Fund investment, and measures to support Australia’s National Waste Policy Action Plan, will create approximately 10,000 new jobs all around Australia over the next 10 years.
The Recycling Victoria Infrastructure Fund is part of the Victorian Government’s $515 million investment to deliver the biggest ever transformation of the state’s waste and recycling industry. This includes $380 million to deliver Recycling Victoria: a new economy, the state’s 10-year plan to reduce waste, create jobs in new industries and drive more value from our resources.


ADVANTAGES:
Early leak detection Easy hose changes Pump thick sludge easily No corrosion issues Only one wearing part Very easy servicing
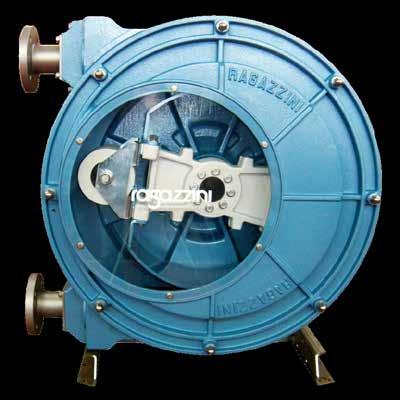
(02) 9898 1800
sales@HydroInnovations.com.au www.HydroInnovations.com.au
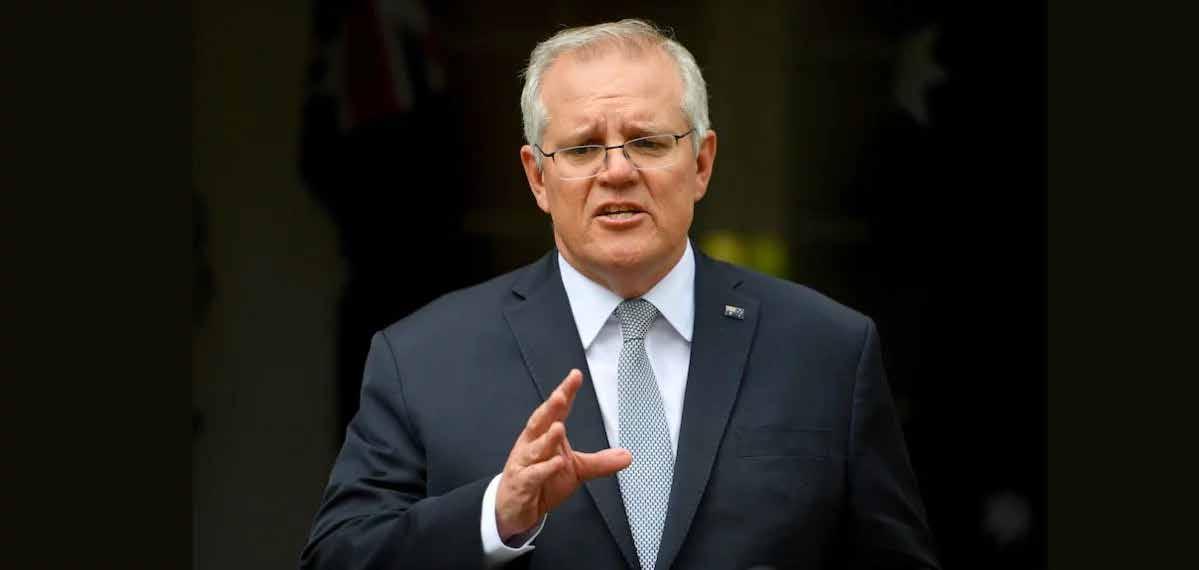
How the Government will accelerate growth and scale AJ Bush upgrades to an Echo-Storm
The Federal Government is taking its Modern Manufacturing Strategy to the next level, Prime Minister Scott Morrison told the National Press Club in Canberra in February.
He said that the pathway would be via greater investment in Australia’s worldclass university research capabilities.
“Our Modern Manufacturing Strategy has set out clear priorities to build new sources of growth and scale in six areas where Australia has significant comparative advantage, strategic interests and the capacity to harness new opportunities.
“In medical products, food and beverage, recycling and clean energy, resources technology and critical minerals processing, defence industry and space,” the Prime Minister said.
$312 million funding
To date, the Government has committed over $312 million in funding to boost manufacturing capability and supply chain resilience, leveraging $677 million more in private sector investment.
“We now need to better link and leverage our world class research sector to boost these efforts. 85 percent of Australian research is rated, officially, at or above world standard.
“Yet we continue to underperform, frustratingly, in achieving commercialisation outcomes. We need to shift the focus from citations to commercial success,” he said.
Accelerate linkages
The Prime Minister said that there was a need to “accelerate the forging of linkages between Australian industry and Australian university researchers”. Adding that we also need to develop a new breed of research entrepreneurs in Australia so they can create the new products and new companies and the new jobs.
He said that the Government’s University Research Commercialisation Plan would align these research priorities with the Modern Manufacturing Strategy. “We’re going to fuse them. It will focus research effort on the same six National Manufacturing Priorities.”
Trailblazer Universities programme
The first element of this plan, the Trailblazer Universities programme was announced in November. This will see eligible universities undertake reforms, including to intellectual property arrangements, and provide clear promotional pathways for academic researchers engaging in commercialisation activities.
Eight university proposals have been shortlisted to share in $243 million of investment, working closely with industry partners.
Funding of $30 million will also see participating universities partnering with CSIRO to access specialist equipment, enabling researchers to prototype and test technologies at scale.
Badging the $1.6 billion program, Australia’s Economic Accelerator as the “cornerstone” of the Government’s new approach to turning great Australian ideas into commercial success, the Prime Minister added that in driving commercialisation, the key policy challenge surrounds the socalled ‘valley of death’.
“This is where early-stage research is frequently not progressed to later stages of development because of the risk and uncertainty about commercial returns.
“We know this is not insurmountable. Other countries have made a better fist of solving this problem and the Government’s expert panel made a point of looking at this evidence,” he said.
He said that Australia’s Economic Accelerator is a stage-gated, competitive program designed to attract projects at proof of concept or proof of scale and their level of commercial readiness for both, but with high potential. It will allow Australian innovators to access funding opportunities for each stage of their project provided they can continue to prove project viability and importantly, commercial potential.
Industry engagement necessary
He said that at every stage, industry involvement and engagement was critical with the CSIRO’s Main Sequence Ventures engaged to catalyse venture capital investment in R&D in the final stage.
Meanwhile, because only 40 percent of Australia’s researchers work in private industry, well below the OECD average and the low mobility between industry and the university sectors has led to culture and capability gaps. The Government has identified these factors as reducing the ability of Australian businesses to innovate.
The Government will now invest in a new suite of industry PhD and research fellowship schemes to create Australia’s new generation of research entrepreneurs.
“We will invest in an additional 1,800 industry PhDs and more than 800 industry fellows over 10 years. This $296 million investment aims to fundamentally reshape the workforce of Australia’s universities and career options, encouraging mobility and collaboration between university researchers and industry.
“Our $2.2 billion University Research Commercialisation package will focus the considerable research power, the smartest minds of our universities, on Australia’s national economic priorities.
We are backing our best researchers and their ideas to ensure Australia’s economy roars back even stronger in the future, with leading edge manufacturing at its core,” he concluded. IU T he largest capacity rendering facility in Australia is located at the AJ Bush processing facility operation at Bromelton, Queensland where they manufacture nutrient-rich protein meals and tallows/oils. The factory effluent is rich in organic material, which is treated via anaerobic digestion and aerobic treatment processes with treated water used to irrigate pasture surrounding their facility.
Self-priming pump
When plant engineering manager, Byron Boyers wanted to upgrade the pond aeration system to a better and safer system, he contacted Hydro Innovations about its Echo-Storm venturi aerators from Gorman-Rupp. These aerators use a self-priming pump to draw water from the source to be treated. It is then pumped at pressure through the Echo-Storm which adds dissolved oxygen to the water and ‘conditions’ it while it accelerates at more than 16 metres per second through the unit.
Boyers said he wanted a unit with easier and safer access to the EchoStorm for maintenance, as all required equipment can be mounted on the pond bank. The existing self-priming Gorman-Rupp pump could also be utilised for the project. The effluent pond is 200m x 40m x 4m deep, with an inflow of 2 megalitres per day.
Boyers purchased a 4” VA4-550 Echo-Storm unit hooked it up to his Gorman-Rupp pump, designed a floating suction arrangement to keep the suction line off the bottom and pressed start.
Echo-Storm units are available in four sizes [2”, 3”, 4” and 6”] and can improve safety and reliability as well as reduce maintenance costs when compared with other aeration systems. IU
Echo-Storm can improve safety and reliability and reduce maintenance costs.
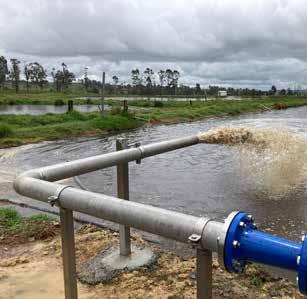
This solar panel ‘upcycling’ facility is a first for Victoria
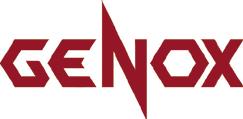

PV module recycling and upcycling has become a significant emerging market.
The University of Melbourne and RMIT University have partnered with the Melbourne-based company OJAS, to develop an ‘upcycling’ facility that will convert end-of-life photo-voltaic modules to ‘value-added’ materials.
The modules are used to make electricity from solar radiation in photovoltaic (PV) solar systems.
This will be the first facility of this type to rollout in Victoria with planned expansion across Australia. Research applications include using recycled glass fines in the manufacture of concrete, with bonus sustainability benefits of reduced carbon emissions
The upcycling plant is scheduled to be operational by the end of 2023.
Significant emerging market
PV module recycling and upcycling has become a significant emerging market, grabbing the attention of academia and industry, worldwide. The International Renewable Agency estimates the value of these materials to be worth approximately US$15 billion by the year 2050.
Researchers involved with the project are working to maximise resource recovery and reclaim the valuable constituent materials of PV modules: clean glass, silicon cells and polymers.
Project collaborators, the University of Melbourne and RMIT University, are seeking to find optimal applications of these recovered PV components.
Research to date has revealed that PV glass fines (small glass particles generated from grinding the glass) can be effectively used as a partial replacement for sand in concrete.
Conserving raw materials
Dr Massoud Sofi, the project's research lead from the University of Melbourne, says this application can conserve raw materials used for concrete production and reduce its carbon footprint. The production of concrete is one of the largest sources of carbon pollution, responsible for around eight percent of emissions globally. Depletion of sand in the streambed and along coastal areas also cause ecological issues.
The research team is now looking at developing specific applications of the PV glass-based concrete materials.
The team from RMIT University, led by Dr Ylias Sabri, is investigating refining the recycled materials for possible reuse in solar panel production or other value-added materials. They are also looking at the processing of ethylene vinyl acetate (EVA), a material that has good radiation transmission and low degradability to sunlight.
The University of Melbourne team in the Department of Infrastructure Engineering, led by Professor Priyan Mendis, has more than 25 years of experience in up-cycling industrial byproducts, including glass fines.
$3million grant
The project originally got under way in 2020 with a $3 million federal government cooperative research centres project grant to OJAS.
OJAS will employ an innovative physical separation technology from Europe to cost-effectively recover clean glass, silicon cells and polymer from PV panel waste.
OJAS CEO Neeraj Das said that a site lease in Victoria was secured in June 2021 for the ‘first of its kind’ PV module upcycling plan, and the separation technology equipment will soon be tested and commissioned.
“By the end of this CRC project in 2023, a PV module upcycling plant will be operating to process end-of-life PV modules collected Australia-wide and supply the recovered materials to downstream businesses for valueadded products.OJAS infrastructures is aiming to expand this solution across Australia,” he added.
A nation-wide collection network will be established to coordinate the stream of end-of-life PV modules, with the aim of minimising labour and transportation costs related to the collection process. The PV modules collected will undergo a series of processes to recover all their valuable materials. IU
vertical shredders. Built tough for the most demanding of shredding applications.
HEAVY DUTY VALUE FOR MONEY CIRCULAR ECONOMY
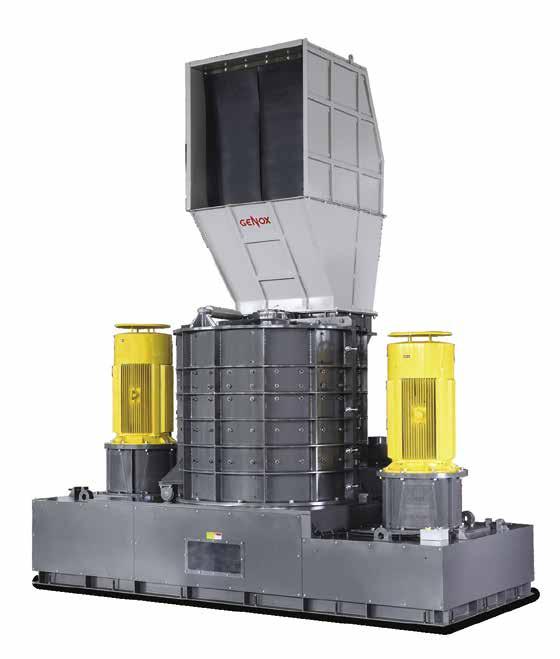
• Aggressive size reduction and densification of preshredded materials • Clean, high bulk density output for easy sorting and transportation • C&D waste, scrap metal and other heavy duty applications • Available with up to 440kW of power • Industry-proven and built tough for Australian conditions
To find out more, call: 03 9706 8066, Email: sales@appliedmachinery.com.au, or visit: www.appliedmachinery.com.au