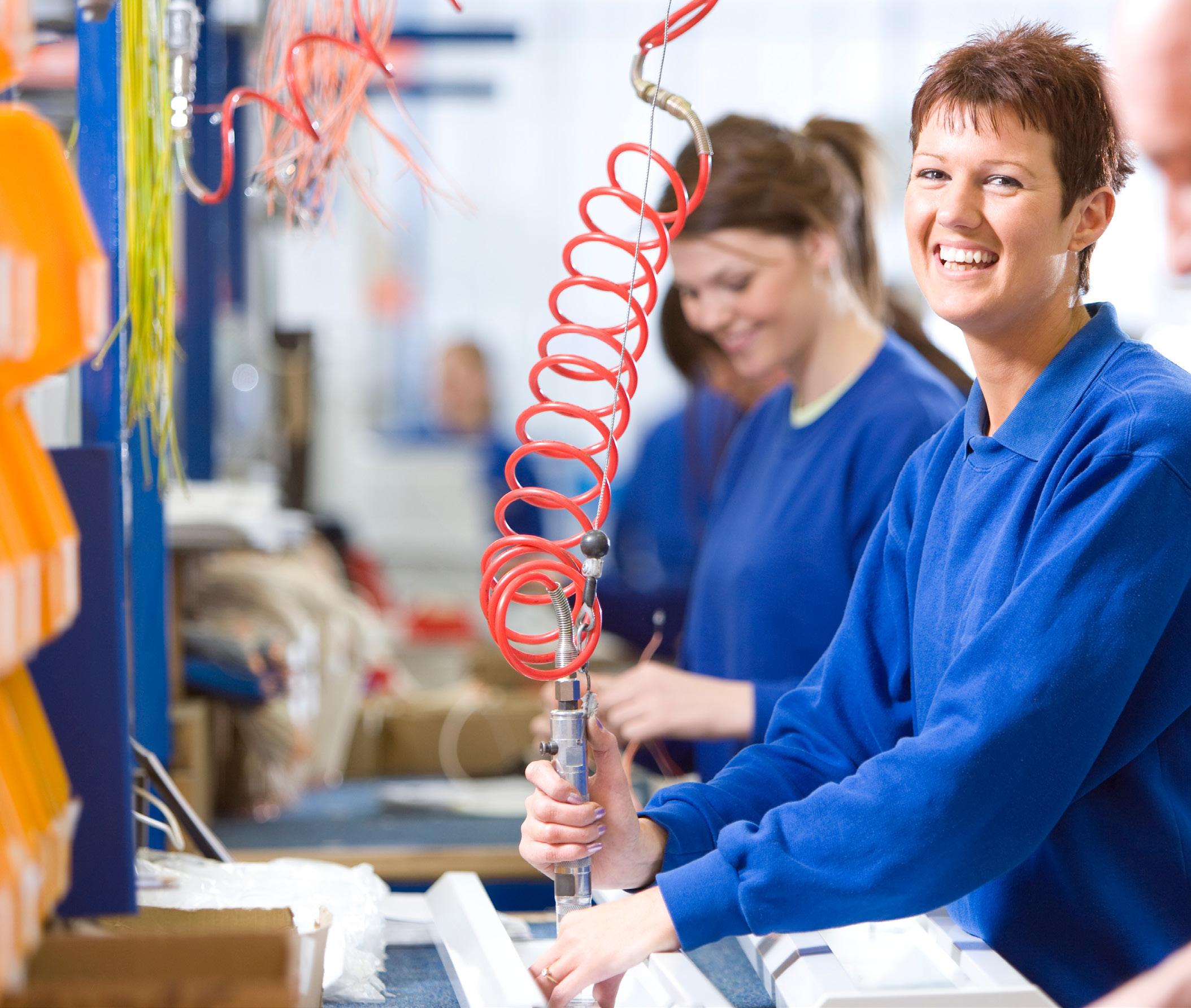
22 minute read
Women in Manufacturing
Tackling gender equity in manufacturing
120 Australian employers are now carrying the WGEA yellow tick to certify they are driving progress to make their workplaces equal.
Advertisement
Recognizing the contributions women are making to the manufacturing industry is important to underscore achievement, but is also essential to encourage more women to enter the field.
While women comprise almost 67.6 percent of the Australian labour force (according to ABS Gender Indicators 2020), a rate that is the highest during the past 10 years, they represent less than one-third of the manufacturing workforce.
For example, less than a quarter (24.1 per cent) of management positions in the energy industry are held by women, according to data from the Workplace Gender Equality Agency’s Gender Equity Scorecard (2020-21). And the current gender pay gap in the electricity and energy sector is 14.5 percent.
To provide a clear picture of the local corporate leaders who support the growth of women within industry, the Workplace Gender Equality Agency (WGEA) has named the latest list of Australia’s Employers of Choice for Gender Equality (EOCGE). 120 Australian employers are now carrying the WGEA yellow tick to certify they are driving progress to make their workplaces equal, including 12 new companies awarded the prestigious WGEA certification this year.
Together, these organisations employ approximately 320,000 Australians, offering benefits to those workers such as family-friendly workplaces through paid parental leave and flexible working policies.
Employees looking for a certified company to work for have the most options in the Professional Scientific and Technical Services group, with 47 Employers of Choice; followed by Financial and Insurance Services (21 Employers of Choice) and Wholesale Trade (13 Employers of Choice).
The WGEA citation is awarded following a rigorous application process with a range of stretch criteria, designed to measure the actions organisations are taking to advance gender equality outcomes for their employees. Compared to other organisations in the Agency’s dataset, the WGEA Employers of Choice for Gender Equality are set apart by a range of factors, as seen in their data: • Lower gender pay gaps: EOCGEs have an average gender pay gap of 18.9 percent compared to 23 percent for others. They conduct pay audits annually, and track and report gender equality metrics to their Boards. • Higher proportion of women on boards: 35 percent of EOCGE employers have women on their boards, compared to 28 percent in others. • Longer periods of parental leave: 14 weeks on average; compared to 10.7 weeks, with leave available to new employees as soon as they join an EOCGE organisation. • Superannuation on parental leave: 100 percent of EOCGEs pay super on employer-funded parental leave, including 18 percent who are also paying it on the Government scheme; compared to 81 percent and 7 percent respectively in non-EOCGE employers. • More male managers are taking parental leave: Nearly 29 percent of all managers taking primary carer’s leave in EOCGE organisations were men, compared to 15 percent in non-EOCGE organisations.
These organisations have a demonstrated commitment to advancing change not only in their organisation, but as leaders driving gender equality in their wider industries too.
Bar raises every year
Director of the Workplace Gender Equality Agency, Mary Wooldridge, says the bar for certification is raised each year to challenge companies to continue maintaining leading practice standards in workplace gender equality.
“Our WGEA Employers of Choice for Gender Equality emerge from an evidence-based assessment as Australia’s leading change-makers, who are driving and embedding gender equality in their workplaces and business practices.
“Critically, these organisations are delivering on a formula that sees better support structures in place for working families; stronger actions to address pay inequalities; and strategic recruitment and promotion practices that help to encourage the full participation of women at work.”
Kimberly-Clark Australia is one of the most recent companies to receive WGEA accreditation. Over the past two years it has held a specific focus at its Millicent Manufacturing site in lifting the applications received from females for Operations based rolls.
Wooldridge added that research into the cohort of Employers of Choice - produced in partnership with the University of Queensland – has analysed the actions they are taking compared to other organisations.
“It proved the outcomes of this approach are paying clear dividends: our WGEA Employers of Choice are closing their pay gaps faster, have a higher proportion of women in management, a stronger pipeline of women moving into senior management, a higher representation of women on their Boards and a higher proportion of female employees working full-time than other employers,” she said.
“We extend our congratulations to these leading employers and look forward to working with them closely to help accelerate positive change across all Australian workplaces.”
Employer of Choice citation
The Employer of Choice for Gender Equality citation is a voluntary, leading-practice recognition program. It is designed to encourage, recognise and promote organisations’ active commitment to achieving gender equality in Australian workplaces.
All employers in Australia with 100 or more employees report annually to WGEA to comply with the Commonwealth Workplace Gender Equality Act.
The citation holders are companies who then choose to go through an additional evaluation process, passing a range of evidence-based criteria under seven focus areas.
These criteria cover leadership, strategy and accountability, developing a gender-balanced workforce, gender pay equity, support for caring, mainstreaming flexible working, preventing gender-based harassment, discrimination and bullying and driving change beyond an employer’s workplace.
The assessment process examines the employees’ lived experience, along with the CEO’s commitment to driving and influencing equality outcomes not only within their businesses, but in their industries too.
Merilyn Glenn: from secretary to CEO
Merilyn Glenn is the founder and CEO of Liftco, a dedicated provider of safety devices to the Crane and Manufacturing industry, and which celebrated its 30th year in business. While it began in Ingleburn Western Sydney, its warehouse and showroom are now based in Wollongong.
Liftco was established to fill the market gap that existed in Australia and New Zealand for the provision of reliable safety and electrification products for Cranes and Hoists.
As founder of such a traditional male orientated business within a traditionally male orientated industry Glenn is unique, if not unusual in possessing the extraordinary qualities which have sustained her throughout her 30 plus year career.
Many Australian female leaders have built successful business careers that commenced as a secretary (now known as personal assistants (PA) and increasingly gender inclusive).
“My secretarial career started straight out of school in the late eighties, when I attended a secretarial college learning shorthand and dictaphone (which I don’t even think is used anymore).
“My first job was as a PA in a small company and my duties included running the office when my boss was away. This gave me a good grounding for my future career, she told Industry Update.
Leading since 1991
Glenn has been at the helm of Liftco from 1991 when, along with a business partner, they decided to seek an Australian agency for load limiting devices.
“Liftco was established in 1991 when we saw the need for improved safety across the Australian overhead crane and manufacturing industry. I started off with a business partner who later decided to pursue other avenues of business. I continued to lead Liftco, celebrating 30 years in business in 2021,” she explained.
Under this leadership, Glenn guided Liftco’s evolution into a small family business. “Everyone does a little bit of everything, I mainly look after marketing, advertising, stock control and the general running of the business. However, I am not afraid of getting my hands dirty in the factory when we are busy,” she added.
The last two years have been the most challenging for most Australian leaders of either gender and Glenn echoes this, “I think the last two years have been the biggest challenge of everyone’s career.
“Facing an uncertain business environment we have focused on staying positive. Our positive outlook and determination to succeed helped us through a very tough time,” she said.
Tenacity inspires
While Glenn doesn’t attribute her inspiration to any one particular female leader, she said that, “all women in business who are willing to put in hard work and make sacrifices inspire me. My female family members inspire me, I admire their tenacity.”
It is a commitment to continual improvement that has underwritten much of the success Liftco has experienced over three decades.
“The primary focus of our product range is to improve safety protocols on overhead cranes,” she said. But these protocols not only help save life and limb, they also “help reduce repair and maintenance costs”.
In the same way, Liftco has actively pursued inclusive employment practices. This pursuit has not only been ethically good, but it has also strengthened the business by enriching its workplace.
The company has been involved with various charity organisations, including Care Flight, Biggest Morning Tea, Relay for Life and Shave for a Cure, just to name a few.
Now that the pandemic years seem to be behind us, Glenn says that she sees the future as the biggest challenge.
“Remaining competitive in this difficult economic climate is an opportunity for Liftco to grow the business through innovation,” she said.
“After 30 years, I am also slowly moving towards retiring and handing over the reins to the younger members of the family who have taken on my work ethic and values. I’m confident that under their future management, Liftco will be supplying companies around Australia and New Zealand for a further 30 years.”
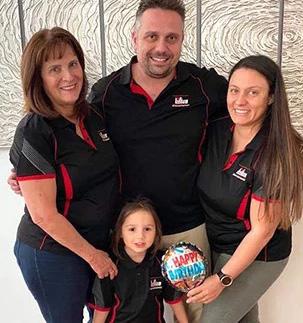
Merilyn Glenn (left)with Liftco team members Chris,Chantal and Aria Stojanovski.
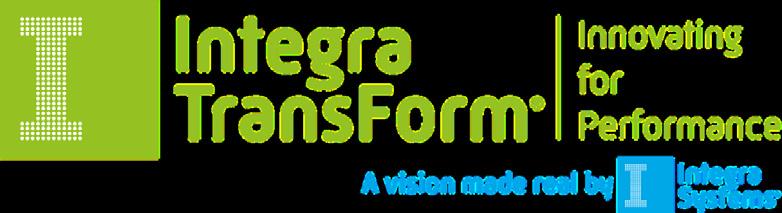
TRANSFORM YOUR WORKSPACE WITH THE BIOSMART PRO
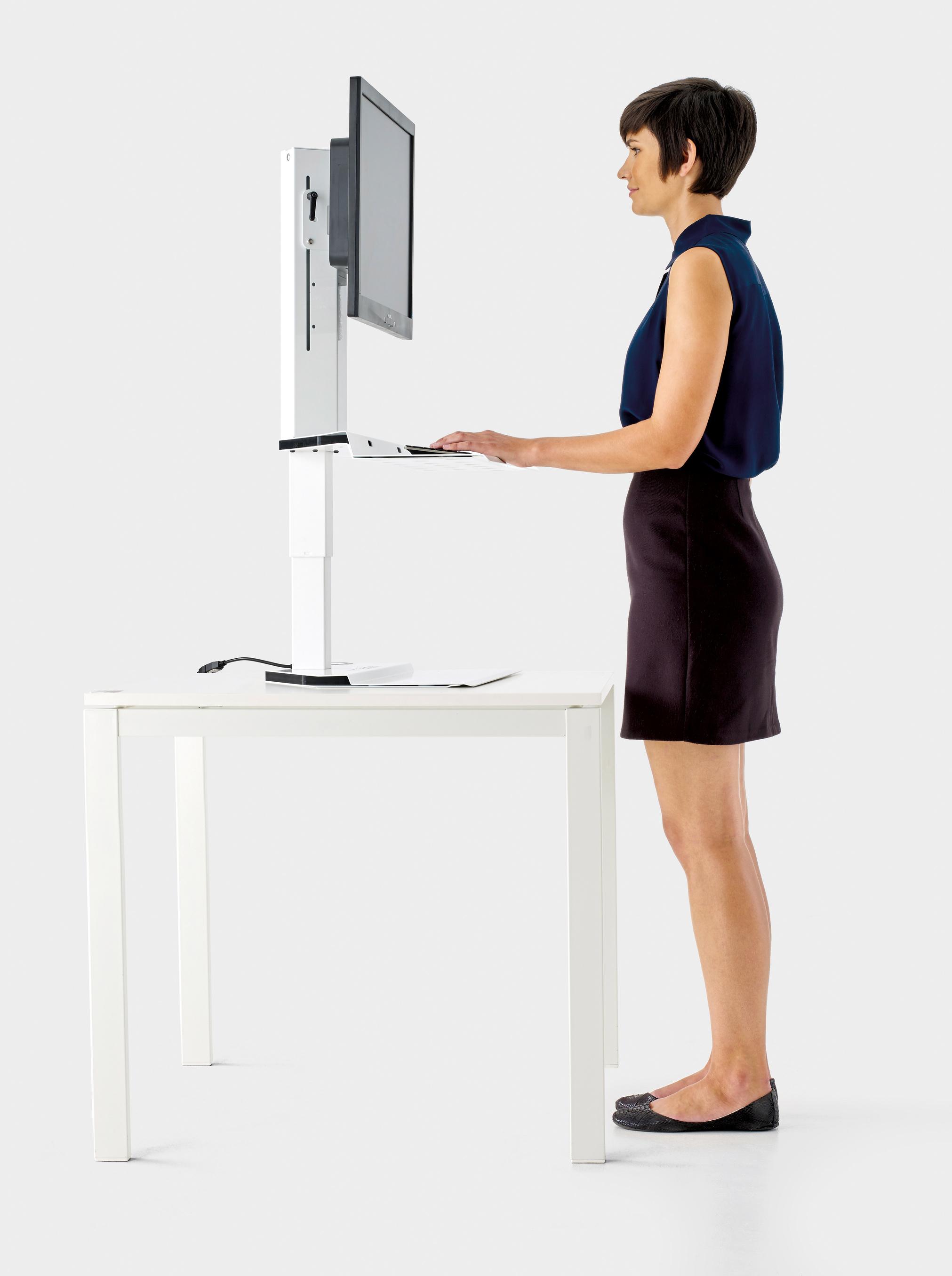
ELECTRONIC SIT-STAND DESK CONVERTER
AUSTRALIAN
MADE & OWNED
Why manufacturing needs women
For over 25 years Integra Systems commercial director Erika Hughes, has seen a lot of changes in Australian manufacturing. While the introduction of more women into the industry is definitely one of the changes on her list, she knows Australia has a long way to go before we achieve gender parity, and that may not even occur in her professional lifetime.
“It wasn’t long ago that I would go to manufacturing industry networks and find myself one of few women in the room, if not the only woman,” Hughes told Industry Update.
“I don’t feel quite as lonely anymore but it would be advantageous to the industry as a whole if there were more women involved. Research has shown that countries and specifically industry sectors flourish when there is a balance of genders and even strong female leadership.
“Men and women have different ways of going about things, which make for better decision-making and better business. Other industry sectors are doing it, and manufacturing still lags behind..”
Traditional roles
Erika believes the perception of traditional gender roles continues to play a strong part in keeping women out of the industry. For example, many women aren’t taught things that are hands-on, but there are women who love working with their hands in practical and mechanical ways that aren’t either art or craft-oriented.
Additionally, the misconception that you need to be an engineer or an industrial designer or even an assembly line assistant to work in manufacturing still prevails. “It doesn’t have to be blue-collar employment in manufacturing,” Hughes said. “It can be really fun, cool, funky, creative and you can make a difference. Manufacturing encompasses the full range of vocations – from the factory floor to design, administration and sales and marketing. These are all places where women can help usher manufacturing into the future,” she said.
Hughes enjoys seeing women of all types and all ages at Integra Systems, because diversity is about so much more than just fresh, young graduates.
“I think Integra’s team has been partly behind the supercharge of change in Australian manufacturing,” she adds. “It’s the way we’ve chosen our people, the way we work with the government, how we work with universities, and the way we handpick our people who match our values. We don’t see age or race or gender, we see values, and that just naturally brings more women into our company.”
When asked how to change perceptions and address the gender imbalance, Hughes suggested, “Passing on this knowledge and building up the confidence in young people, young women especially, by exposing them to what the possibilities are, that’s where you start to get the interest and stimulate new lines of thinking.
“But, at the moment, I don’t think enough women know that this is possible.”
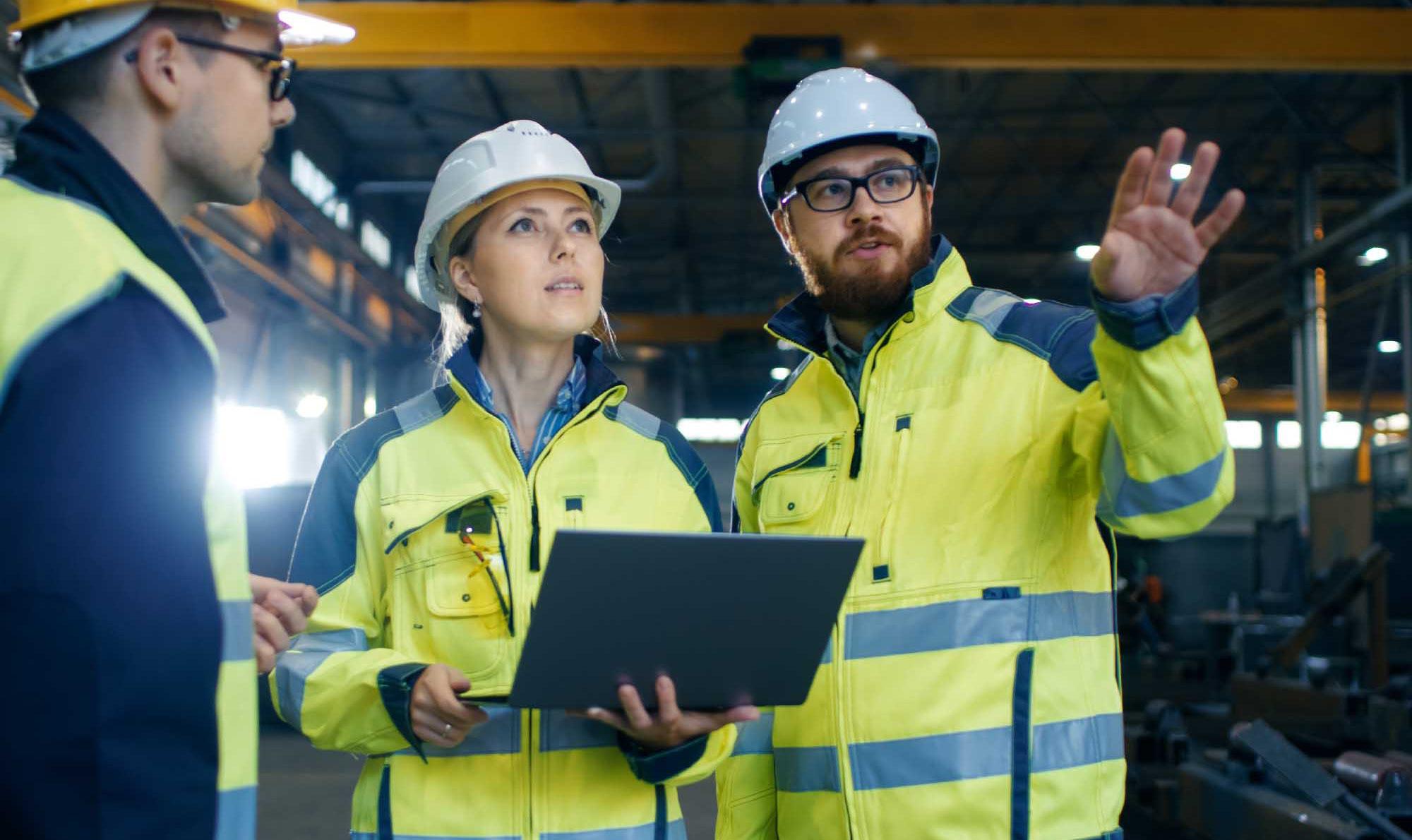
FWC appointment welcome but more needed
Australian Resources and Energy Group AMMA has appointed Paul Schneider to the Fair Work Commission. AMMA chief executive, Steve Knott said that Schneider is well known and widely respected within Western Australia’s industrial relations community.
“He brings significant experience from across the resources industry - the powerhouse of Western Australia’s economy - and in particular the offshore and maritime support sectors where industrial relations can be both complex and challenging.”
Schneider’s appointment as a Commissioner comes shortly after the news that deputy president Amanda Mansini will leave the FWC to assume her new role as Judge of the Federal Circuit and Family Court of Australia. Schneider is the Industrial Relations Manager of OSM Australia and has undertaken senior human resource roles with Seven West Media, Svitzer Australia, Upstream Production Solutions, Downer EDI Mining and McDermott Australia.
Schneider has a Bachelor of Business and a Masters of Business (Human Resource Management and Industrial Relations) from Victoria University.
However, AMMA has noted “with some concern” that the FWC will remain as having 43 statutorily appointed members - a historically low level of resourcing.
“The Morrison Government should very seriously consider additional appointments to the FWC prior to the 2022 Federal Election,” Knott advised.
“When the ALP left office in September 2013 there were 46 tribunal members and Australia’s labour force contained some 11.6 million people. “Today the FWC has 43 members and the labour force contains approximately 13.4 million people.
“Not only is the FWC administering an employment system with 1.7 million additional users than when the ALP was last in office, but matters are increasing in both volume and complexity. This includes a raft of COVID19 related workplace disputes that are swamping the commission currently and are only expected to grow.
Reid congratulated the AttorneyGeneral for making a high quality FWC appointment today.
“It is AMMA’s firm view that at least three more appointments would not only be well justified prior to the Election, but very necessary to maintain the functioning of the FWC,” he added.
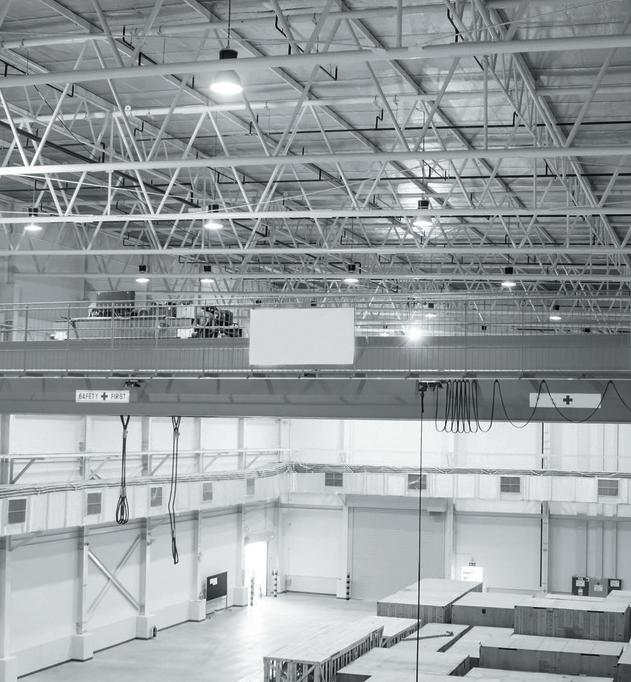
Steve Knott AM Chief Executive Australian Resources and Energy Group AMMA
REDUCE MAINTENANCE COSTS ON OVERHEAD CRANES
LOAD LIMITERS
ROPE AND CHAIN CRANES AND HOISTS
• Helps reduce the risk of accidents • Protects against overloading of Crane and supporting structures • Quick and easy installation and available for all capacity cranes • Available preset or easily calibrated on site • Helps reduce maintenance costs • Minimizes down time • Automatic reset by reducing the load
CONDUCTOR BAR
• Available in steel & copper • Quickly and easily installed • Supports required only every 1.5m • Also available in a compact cluster range SIDE PULL PREVENTERS / ROPE GUIDE PROTECTOR
Prevents side pulling and protects rope guides and drums on most multi-fall cranes & hoist • Prevent dragging of loads • Easily fitted to any crane/hoist • Helps reduce down time
Liftco Industrial Supplies Pty Ltd (02) 9829 4411
How Royal Apollo spearheaded Oceania growth
The Apollo Group is one of the world’s largest manufacturers. In this Q&A we asked chief commercial officer, Kevin Suphapvanich its growth within the Oceania region.
IU: Can you describe Apollo’s activity within the Oceania market. How has that grown in the past two years?
KS: The Royal Apollo Group established a production facility and sales/ service centre in Thailand five years ago to locally assemble, sell and service our Spiral Conveyors to the AsiaPacific vertical conveying market.
Initially, we were not very active in the Oceania market due to the pressing demand of East Asian and Southeast Asian markets. During that time, there were mostly indirect sales to Oceania through the European headquarters of some of our international system integrator customers.
They would purchase and ship the spiral conveyors from Europe to Oceania themselves to integrate into the complete conveying line onsite. Then from 2020, we significantly increased our focus and attention to the Oceania region.
Unfortunately, it was also the year that the COVID pandemic started. This prevented our Asia-Pacific team from physically travelling to the area.We approached the market through digital marketing and also via established channels like Industry Update. We made the best use of our AR sales and service tools to gain rapport to our customers despite the distance. It also helped that our modular designed Spiral Conveyors are relatively simple to transport and install, even without the presence of our installation technician, through the use of pictured guidelines and AR service app.
This resulted in significant brand exposure, customer base expansion, and sales growth within the last two years. But we are aware that we are just in the beginning stage and there is still much ground to cover in this region.
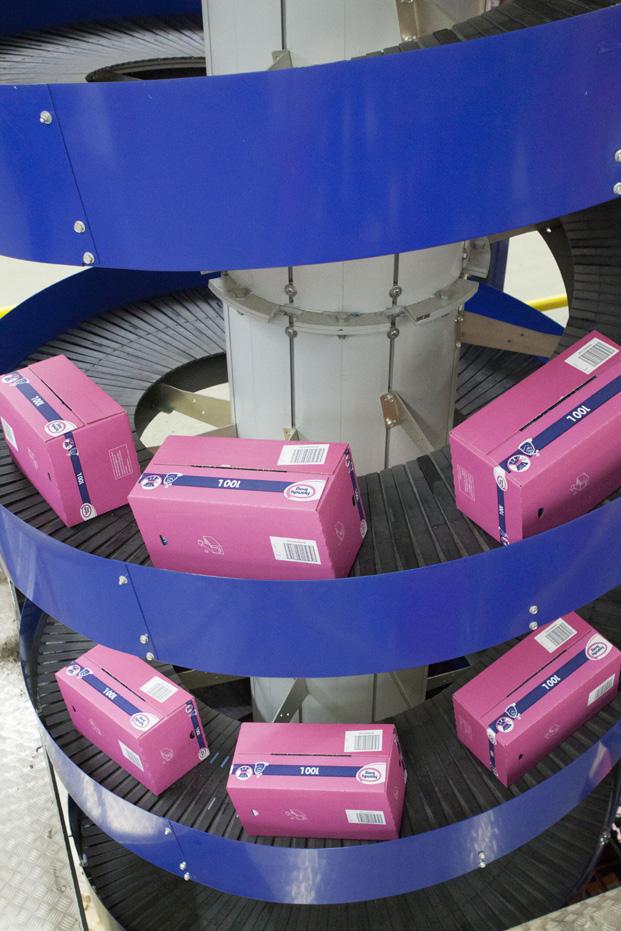
Apollo has expanded to locally assemble, sell and service its Spiral Conveyors to the Asia-Pacific vertical conveying market.
IU: What is your largest market in this region and what products are the most successful and why?
KS: Our Spiral Conveyors are used to transport packaged products in two main industries in this region.The first and largest industry is the food and beverage industry. Packaged food and beverages in bags, pouches, cans, jars, trays, cartons, and other primary and secondary containers sometimes need to be transported in large capacities and continuously up, down, or even over the production or filling lines.
This is where our Spiral Conveyors make the best use of the limited space to elevate products. For example, we are able to convey up to 120,000 bottles per hour continuously 24/7. We can proudly say that the biggest beverage manufacturers use our Spiral Conveyors in their production facilities around the world.
The other fast-growing industry is the warehousing sector. Here, cartons, totes, crates, and even irregularly shaped products such as car tyres and golf bags can be transported on our Spiral Conveyors. E-commerce and express delivery services, such as DHL and Amazon, require multi-feed spiral conveyors to move goods to and from the multiple floors of their storage rack.
IU: What benefits do customers in this region gain from your product and service?
KS: In 2022, our company, a family-owned 6th-generation business of Dutch origin, celebrates its 175th anniversary (as Industry Update readers may have found out from the previous issue). This year, we were also awarded the Royal title from the King of the Netherlands himself. This says something about who we are and what we stand for.
Our customers are actually receiving Spiral Conveyors from one of the pioneers in this niche vertical conveying market. On a glance, Spiral Conveyors may seem mechanically simple compared to the robotics of today, but there is actually a lot of know-how required to manufacture a robust and reliable solution.
For the Oceania region, our Spiral Conveyors are manufactured from Thailand. We have deliberately chosen this location, over other options such as China, to be our main production hub for the Asia Pacific region. We have made sure that the quality matches the machines assembled at our Dutch headquarters, less the European price tag and transportation difficulties.
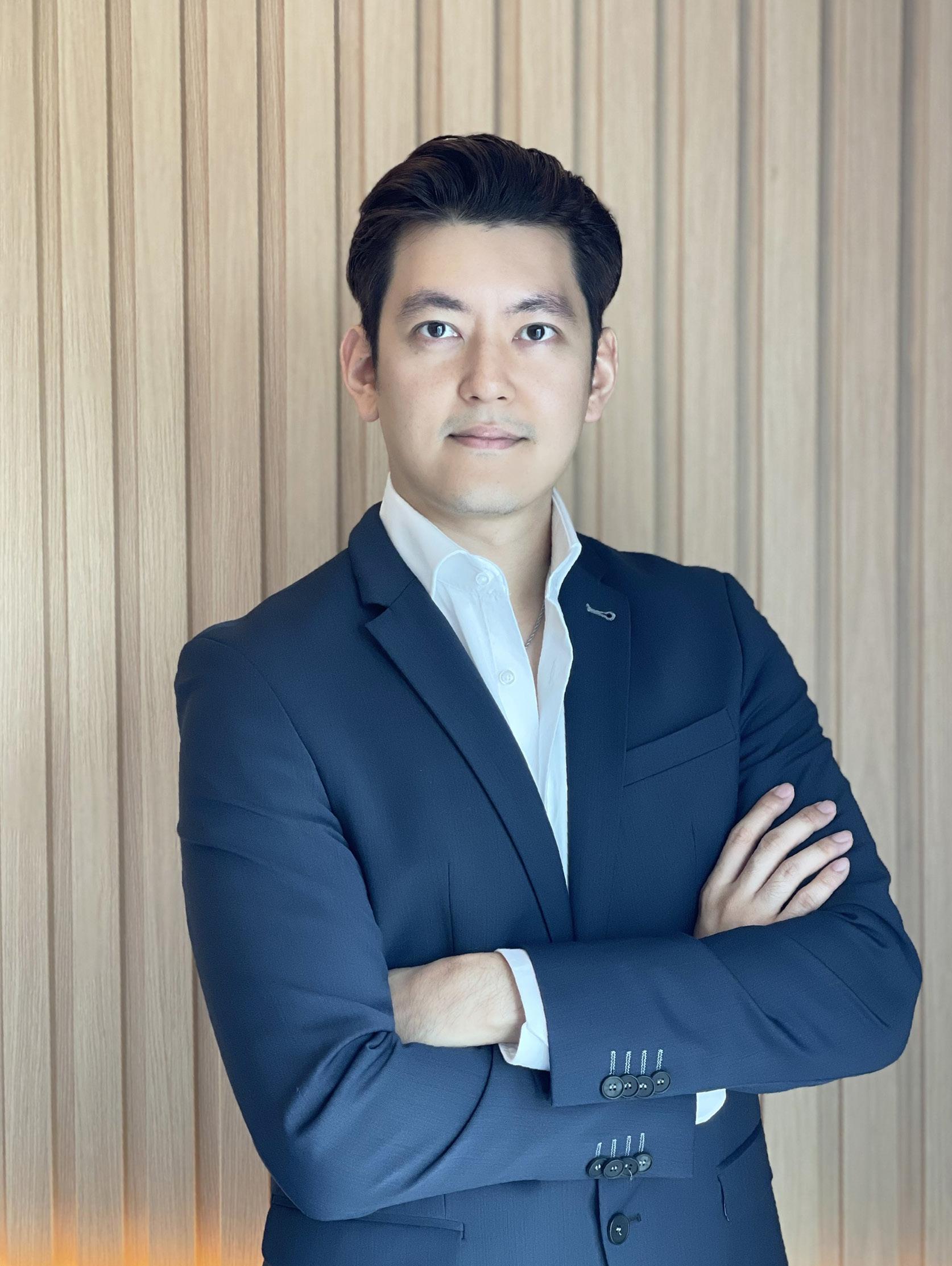
“From 2020, we significantly increased our focus and attention to the Oceania region.”- Kevin Suphapvanich
IU: Could you talk about your participation in Auspack next May and CemAT next July?
KS: With the opening of borders and reduction of travel restrictions, we took the first opportunity to join an overseas exhibition. That exhibition is Auspack in May, and we will be present with our own booth (D246). In July, we will return with another booth (B30) at CeMAT Australia.
We aim to convert our remote communication into physical meetings with existing customers and to meet new ones in person over the course of these two exhibitions. I hope Industry Update readers will be able to meet us at our booth as well!
IU: Given the current global disruptions could you comment on how you are managing with supply?
KS: The cost of materials and the availability and price of transportation has definitely been impacted greatly by the current global disruptions. We aim to increase the percentage of locally-sourced parts to maintain production lead times, without compromise to the standard of quality of course.
At the same time, we are establishing agreements with suppliers to maintain part prices where possible, so that our customers continue to receive the same prices. So far, we have been successful in maintaining our price and production lead time to customers.
• Proactive alerting and process control via a single point of control (SPC) • Digital work instructions • Digital check-sheets • Gauge and instrument management
Smooth transition
Plex QMS is part of the broad Rockwell Automation family of products designed to smoothly transition companies into the future of industrial automation and the Internet of Things (IoT).
Plex Systems’ suite of products for enterprise resource planning (ERP) applications were welcomed to the Rockwell Automation family in 2021. The platform deals with over eight billion transactions a day and has an A security rating. Plex Systems offers a single instance, multi-tenant Software as a Service (SaaS) platform for manufacturers that plugs into existing ERP applications, including manufacturing execution system (MES), QMS, supply chain planning (SCP), asset performance management (APM), production monitoring, process automation, and manufacturing analytics capabilities.
The Plex Smart Manufacturing Platform is designed for configurability, extensibility, and integration, enabling organisations to tailor the system to meet the unique needs of a production line and individual plants while maintaining enterprise-wide control and insight. “With platforms
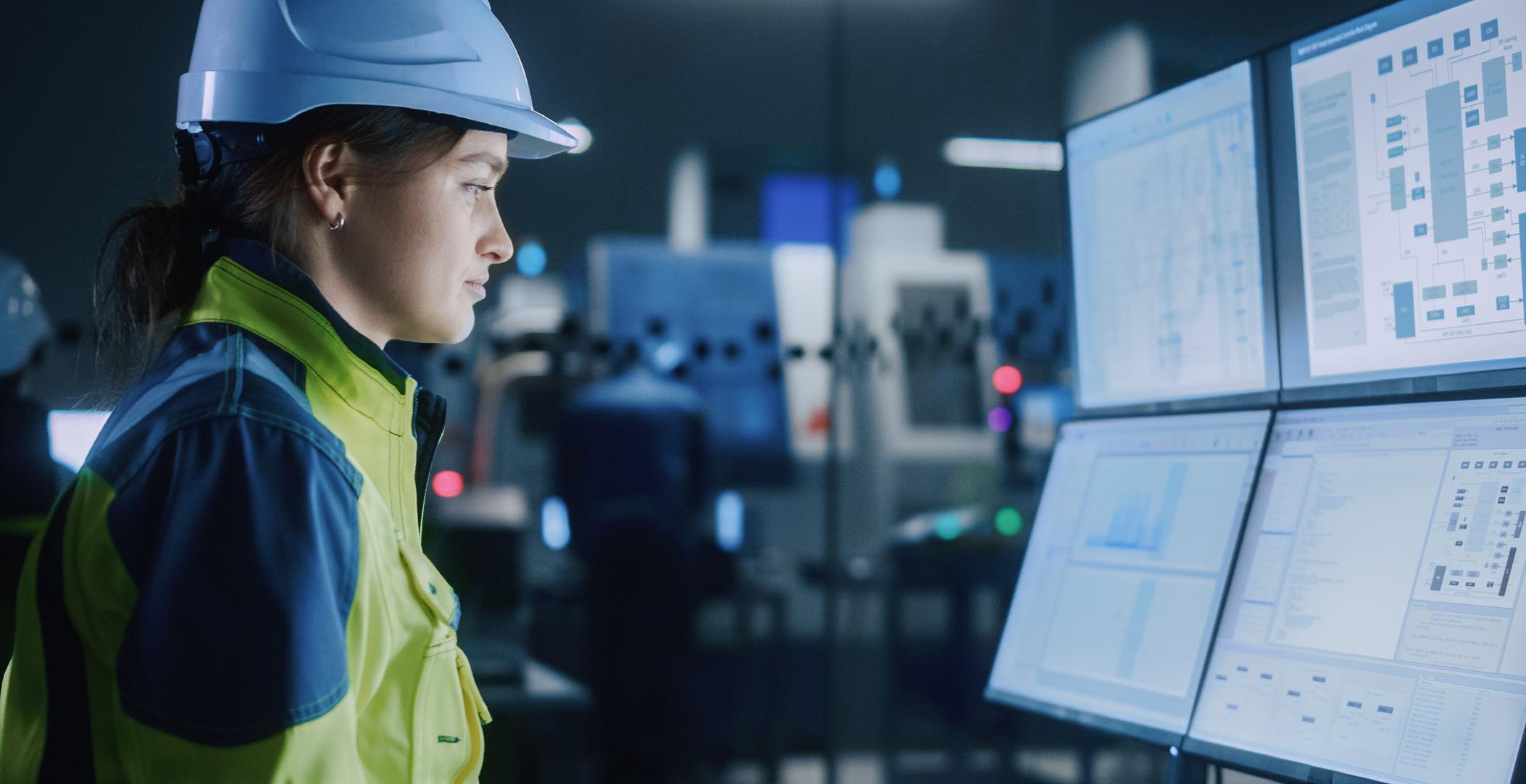
such as Plex – as well as Fiix ® customised plant maintenance software – Rockwell Automation offers SaaS solutions to customers, providing them with greater agility and closer alignment to where technology is heading, without large up-front investment costs,” Cahill continued.
“Previously, having sophisticated software and automation systems in place required data centres, infrastructure, large migration costs, and other up-front capital costs. Plex and Fiix level the playing field and allow companies of any size to capitalise on the latest technologies to enhance their manufacturing plant and processes, without needing to have a big budget,” he said.
Plex QMS is based on global and local experience in systematically reducing issues such as quality loss and risk of warranty issues.
Plex QMS ushers in digitally integrated quality and risk management
Rockwell Automation, is bringing its digitally integrated Plex ® Quality Management System (QMS) to Australasia and the South Pacific.
The cloud-delivered Plex QMS enables manufacturing enterprises to adopt industry best practices while helping them to reduce the cost of quality, maintain compliance, manage risks, and simultaneously scale up operations as required. The smart manufacturing system is deployed internationally in industries such as food and beverage, precision metalforming, high technology, electronic products, and automotive.
One sought-after capability provided by the technology’s cloud platform, for example, is the ability to
achieve a “single version of the truth”, enabling audits and mock recalls in minutes, hours, not days or weeks. Plex provides quality documentation and standards in real-time, digitally – across the enterprise. Plex QMS makes it possible to track production defects at the level of the container or individual part and determine products that need to be returned to the supplier. “Plex QMS is part of Plex’s practical, future-focussed suite of tools that responds to the needs of businesses seeking to build their local and export sales on the basis of outstanding quality, assured brand reputation, and enhanced customer relationships,” Rockwell Automation Information Solutions Sales Executive, Michael Cahill told Industry Update.
“As a versatile cloud platform, Plex QMS supports closed-loop quality control across individual enterprises or multiple operations to drive continuous improvement and business growth. It employs a Plan-Do-CheckAct perspective that installs quality management as an integral part of a company’s culture, shared across the whole business, by making it inherent to workflows and processes,” Cahill explained. “Plex QMS lifts quality assurance and compliance out of the “too-hard” or “too-costly” basket and transforms them into a cost-efficient, user-friendly process. By using Plex, companies can build their business and brand reputation through continuous quality governance and compliance with a broad range of statutory requirements and customer needs.”
Quality requirements and documentation can be shared in real time from top floor to plant floor, from supplier to customer, through the Plex QMS cloud platform.
The system generates digital process control plans with detailed inspection instructions and digital check sheets, all tightly integrated with product specifications.
Local and global experience
Plex QMS is based on global and local experience in systematically reducing issues such as quality loss and risk of warranty issues. Businesses can use it to manage and track documents such as engineering and material specifications, or recipes, while maintaining a detailed and constantly evolving list of compliance requirements, he added.
Integrated system and workflow for regulatory compliance – such as British Retail Consortium (BRC), Safe Quality Food (SQF), Hazard analysis and critical control points (HACCP), and Food Standards Agency (FSA) – are supported easily with best practice templates. This built-in digitised-assurance-of-excellence is a true generator of brand reputation and profits.
“The shared access and assurance delivered by Plex QMS is a welcome
change from piecemeal and disjointed quality control. It transforms diverse compliance from being seen as a necessary pain and expense, turning it into a strong positive process that provides a competitive advantage for the future.” Plex QMS is designed to provide immediate value for companies while preparing them for whatever the future brings. Built-in capabilities of Plex QMS include: • A single quality repository (rather than multiple places where data is siloed) plus drag-and-drop dashboards that require no setup, configuration, or special training • Integrated system and workflow for regulatory compliance (APQP, FSA, HACCP, HARPC, and more)
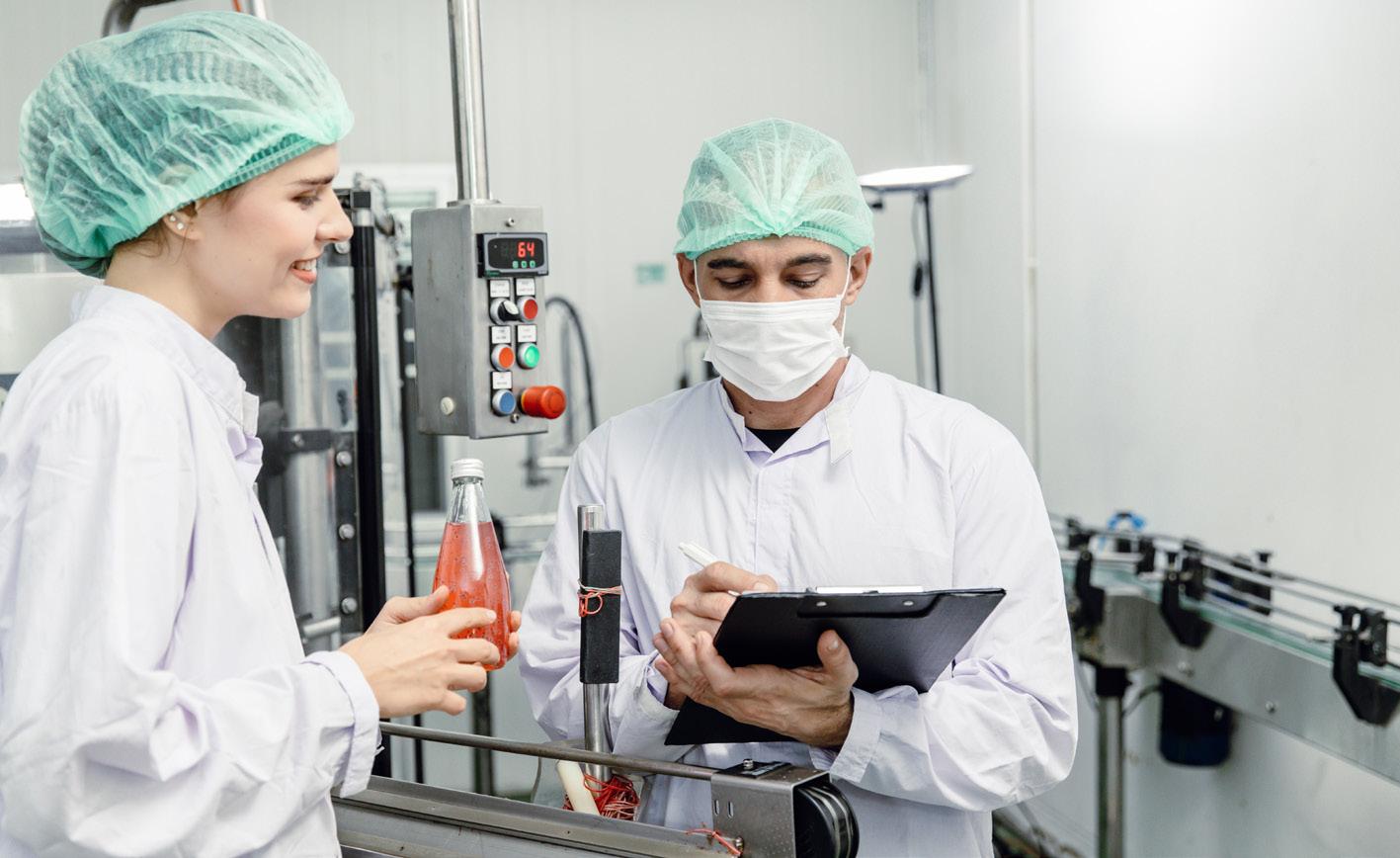
Rockwell Automation’s Plex QMS expertise is complemented by industry-specific managers in key markets, such as food and beverage, abovewarranty issues.