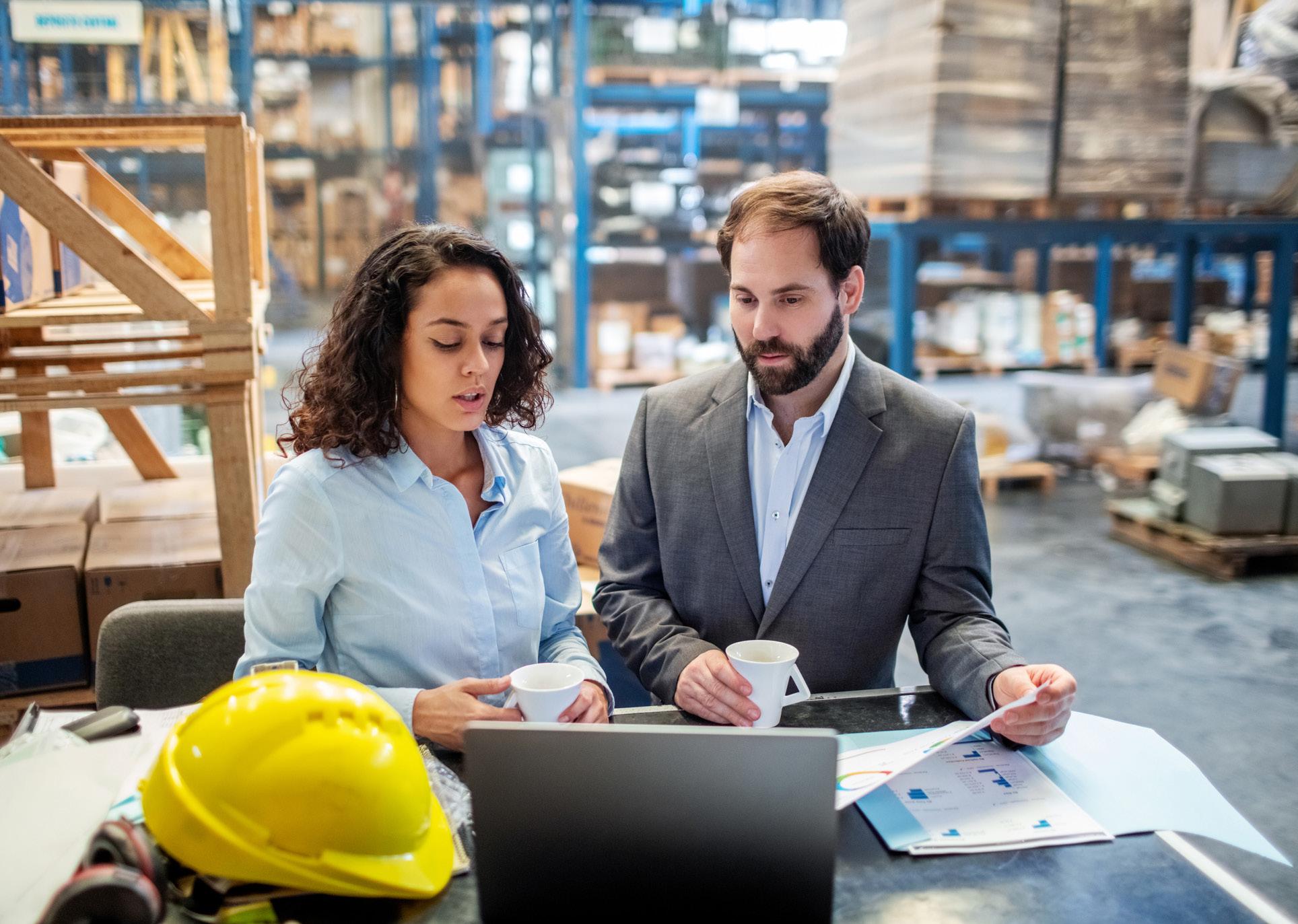
6 minute read
Employment
Ramp up recruitment as production stagnates
by Fuse Recruitment
Advertisement
Supply chain issues and labour shortages continue to impact Australian manufacturing. According to Ai Group’s Australian Performance Manufacturing Index (PMI), production levels fell in July 2022, but have rallied to be relatively stable in September, despite four out of six sectors contracting.However, most businesses reported labour shortages as a key issue constraining output.
In August 2022, Australia’s recruitment difficulty rate was 22% higher than the same time last year. Meanwhile, the percentage of Australian employers expecting to increase their staff levels went up by 13% over the same period.
Fuse Recruitment, a specialist in manufacturing recruitment across Australia, has partnered with many manufacturers over the past 12 months who have struggled to secure talent.
Jaquline Farag, Senior Recruitment Consultant at Fuse Recruitment, says “Clients will often contact me when their requirement is already overdue, which means they’re left to squeeze as much as they can out of their current workforce until they hire new talent”.
In September, the Australian PMI capacity utilisation index rose above the long-run average of 74.6% to reach 80.4% of available capacity. To increase production and prevent burnout in future, manufacturers will need to increase employment levels. Demand is not slowing down.
Demand continues to rise
According to Ai Group, sales and orders continued to grow in September. Additionally, the increasing number of Australian consumers post-pandemic now trying to source locally made products has highlighted the need for local manufacturing.
“Australian consumers have always had a preference for buying Australian products, this has been heightened in recent years,” says Ben Lazzaro, Australian Made’s Chief Executive.“During the pandemic, Australian Made experienced a fourfold increase in applications to use the logo, with consumers increasingly seeking authentic Aussie products produced in our clean, green environment and manufactured to our high standards.” advertised on SEEK grew consistently as businesses in Australia expanded and fought for candidates amidst labour shortages.
There were 15.5% more job ads posted in September than the same time last year in 2021.According to Ai Group’s research, average wages in Australia’s manufacturing industry have also reached a new high and have continued to increase for most of 2022.
Farag warns that while offering high wages is an easy way to bring on new talent, it is not a sustainable approach. She encourages businesses to pay attention to what their employees really want out of their employment, incentivising them to stay.
Value is key
Your employer value proposition (EVP) is the best tool for locking in talent when high salaries are not an option.
Your EVP is the benefits and work conditions you offer your employees, and influences how people feel and think about working for your company.Apart from a high salary, our consultants have found the biggest demands from job seekers are a better work culture, opportunity for career growth and the need to feel valued.
“Some of our clients get creative with what they offer, to align with their business’s needs,” says Aya Inazato, Recruitment Consultant at Fuse Recruitment and former manufacturing scientist.
“Some will offer RDOs where employees work nine-days per fortnight and one of my clients who is trying to attract more women into their workforce is offering paid maternity leave to their employees.”
“Offering benefits to attract and retain employees doesn’t have to be expensive and, if thought about carefully, it is possible to make employees happy at the same time as achieving organisational goals.”
Fuse Recruitment is a specialist in manufacturing recruitment. Many of our consultants have a background working in the industry and hands on experience, meaning they understand the intricacies and technicalities of the roles for which they recruit.
Fuse Recruitment fuserecruitment.com
Employees shouldn’t fear technology
In order to thrive in an increasingly competitive global market, the Australian manufacturing sector is embracing new technology.
Companies are investing in automation technologies, including robotics and artificial intelligence (AI), to achieve greater efficiencies and meet the demand for higher production - while keeping costs down.
The integration of new technologies does, at times, raise concerns from employees, who may fear they’ll be replaced by robots or automation.
“This is a common misconception,” says Hazel Stewart, Director of Innovate Learn, a Melbourne-based distributor of solutions from Wilson Learning Worldwide.
“The Harvard Business Review puts it best: ‘technology does not purge the need for human labour but rather changes the type of labour required. Autonomous does not mean humanless.’”
“The change to new technology actually brings a wide range of new employment opportunities” , says Stewart
She points to the findings of the World Economic Forum’s 2020 Future of Jobs Report, which estimate that by 2025, advanced technologies will lead to the creation of at least 12 million new jobs.
They predict increased demand for jobs such as Data and Machine Learning Specialists, but also very ‘human-driven’ professions, including Digital Marketing Specialists and Business Development Professionals.
While these findings are encouraging, they will do little to assuage the concerns of manufacturing employees who may not yet be equipped with these skills.
The question for manufacturers is, how to embrace advanced manufacturing without leaving employees feeling vulnerable or alienated?
Leading change
For the transition to advanced manufacturing to be successful, it is essential that employees are educated about the new technology, as well as its benefits and goals.
“It’s not that employees are resistant to change – but rather that they need clarity on how the change stands to benefit them on both an organisational and an individual level. It’s important that employees feel that their contributions are a valued part of the overall initiative,” says Stewart
Not a competition
A great point of departure in a change management initiative is to highlight the benefits afforded by automation and new technology.“Robots enhance the workplace for employees by taking on dull, dangerous and repetitive jobs,” says James McKew, Regional Director APAC for Universal Robots, the specialist developer of collaborative robots for industry (i.e. robots that can work safely alongside humans).
According to McKew, the argument that robots will take jobs from humans is an argument they regularly encounter.
Yet robotic automation, he explains, has many advantages for the workforce.
Collaborative robots are freeing up people to do more meaningful and fulfilling tasks, and Universal Robots has seen this repeatedly with their customers across the globe.
An unexpected but major benefit of automation is that it is reinvigorating the manufacturing sector by making it more attractive to young candidates, presenting an exciting pathway into a sector that may otherwise have limited appeal.
Broad skills
As well, more ‘abstract’ skills will be required by future-thinking manufacturing businesses that wish to thrive. Skills such as learning agility, collaboration, critical thinking, and problem solving.
“Change is inevitable, but once teams see new technologies for the opportunities and advantages they present, they can focus on strengthening their uniquely human capabilities.
“These capabilities will always be in demand in the fourth industrial revolution and beyond – no matter how many robots are working alongside us,” Stewart concludes.
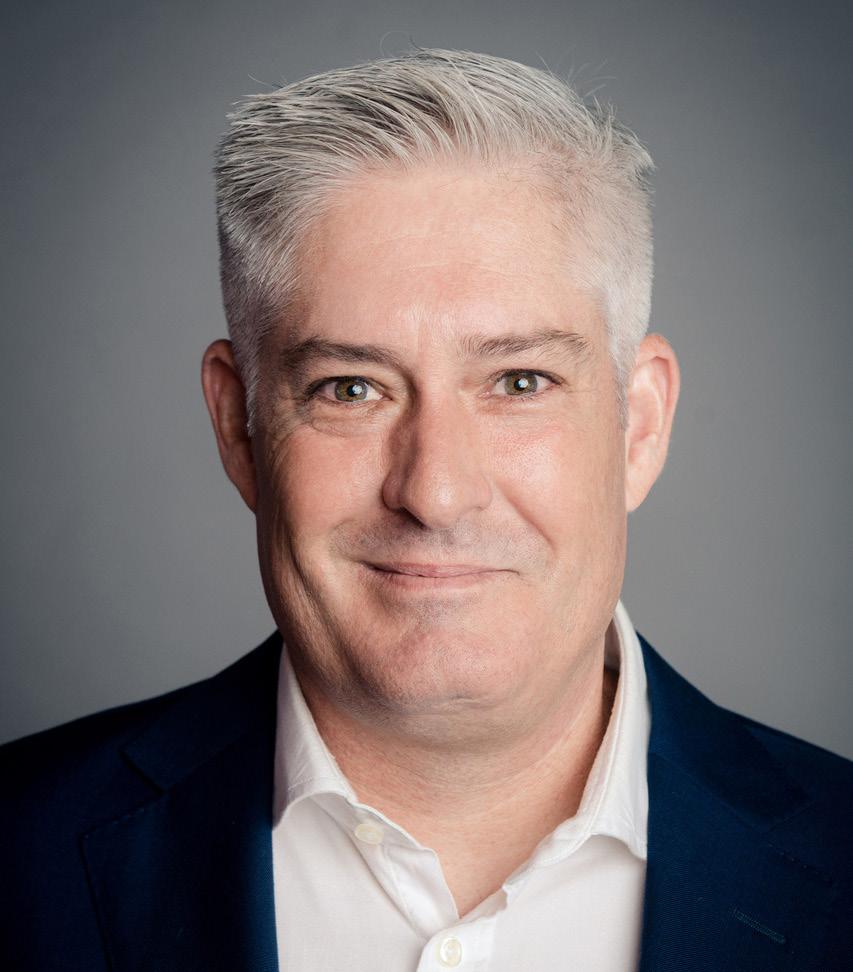
James McKew, Regional Director APAC for Universal Robots
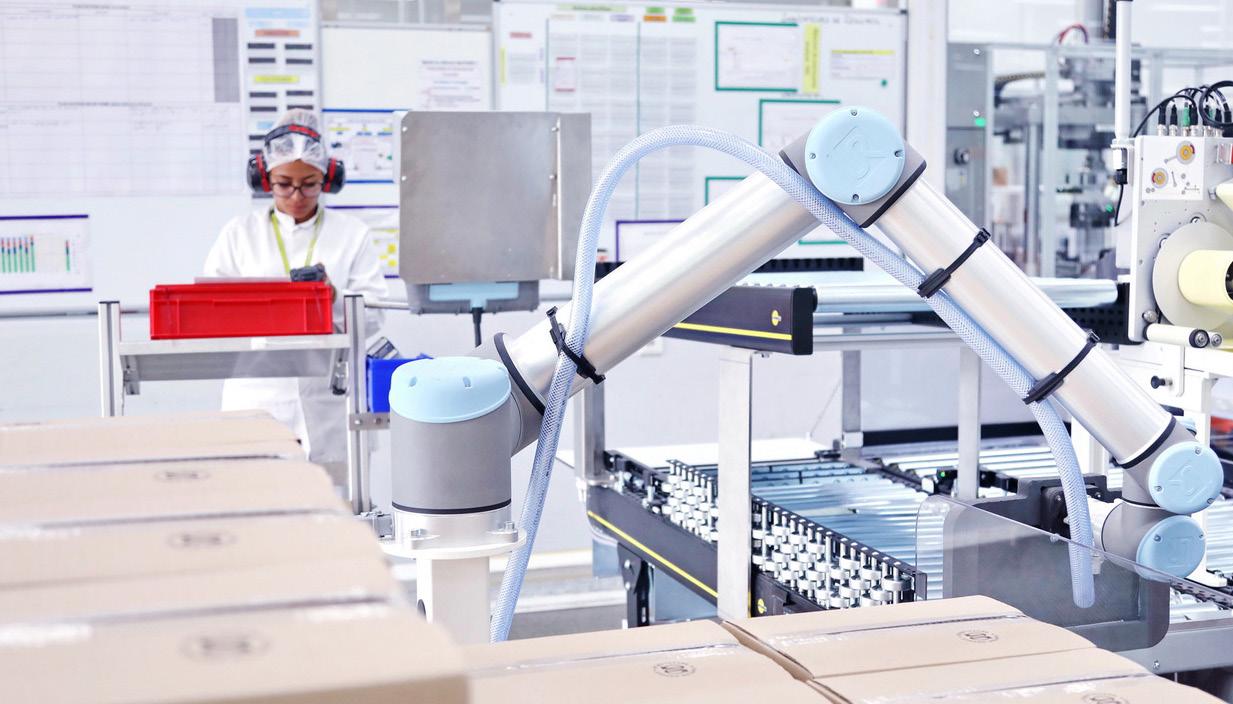
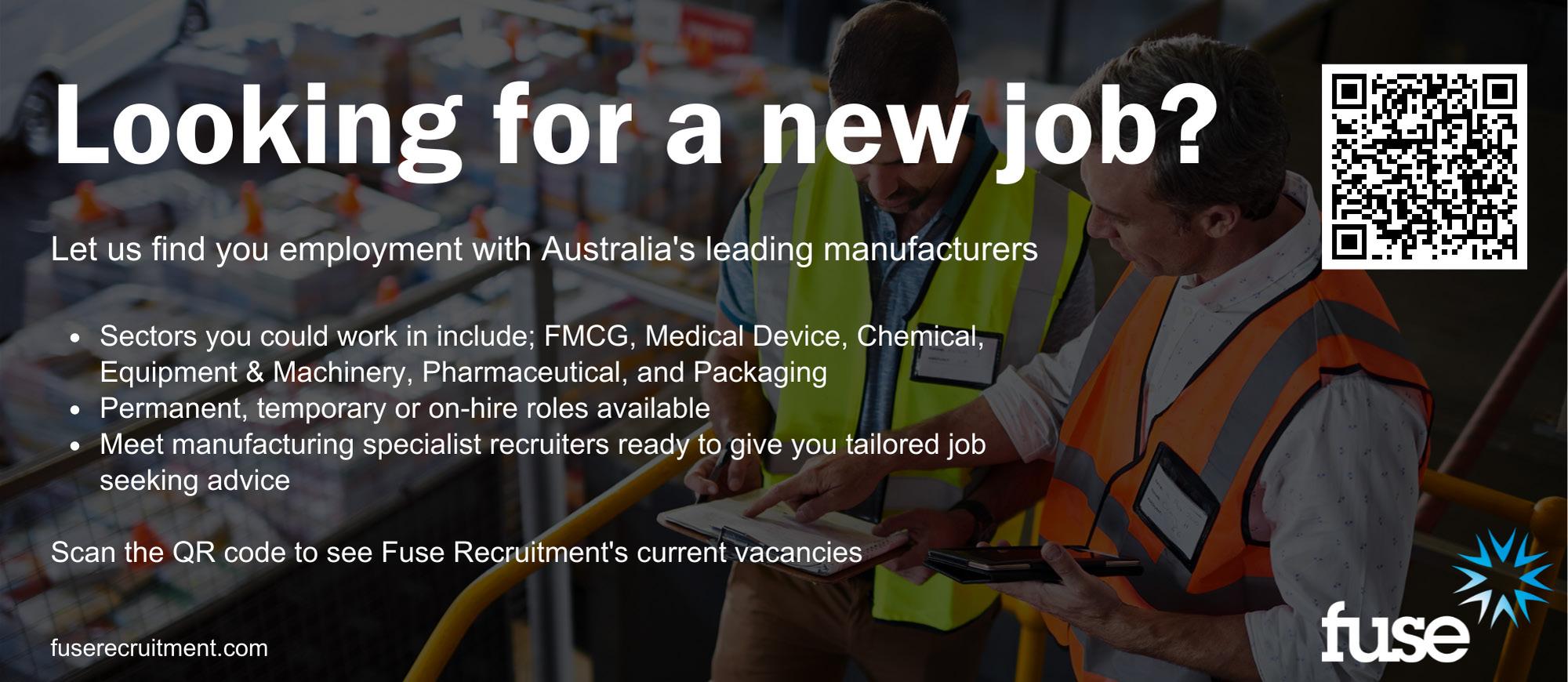