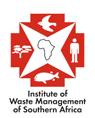
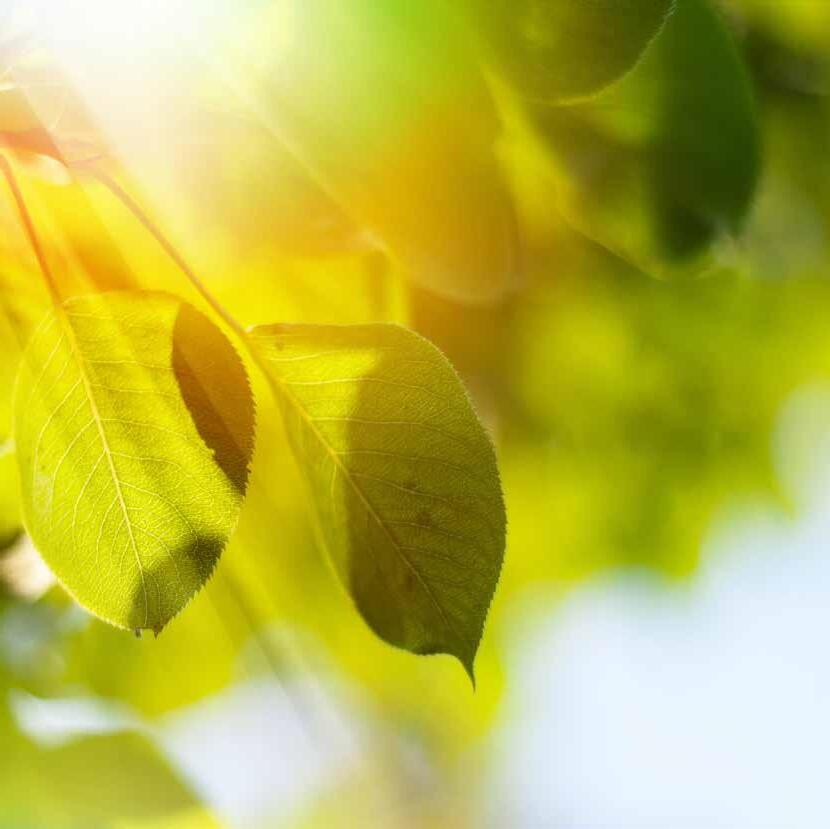
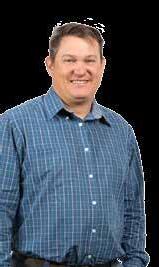
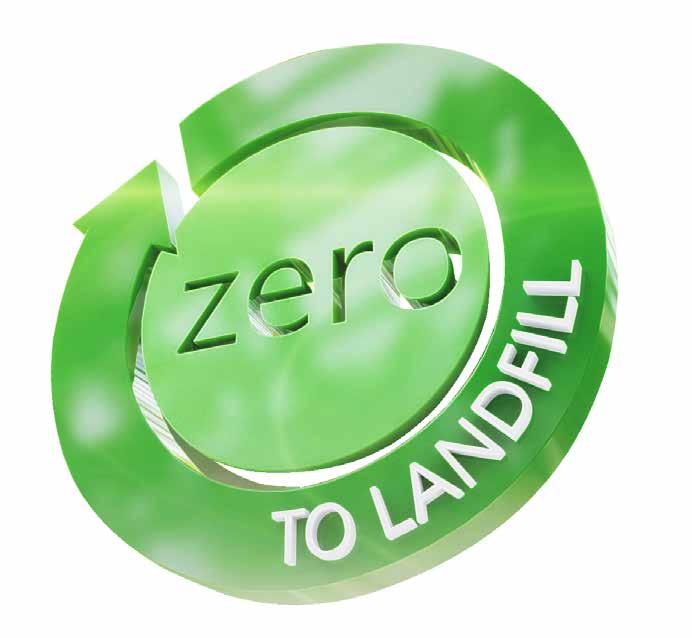
“We strive to be reflective of South Africa’s diversity, empowering our people, clients and other stakeholders through social investment and skills development.”
Hein Jansen van Vuren Marketing Executive, Engineered Linings
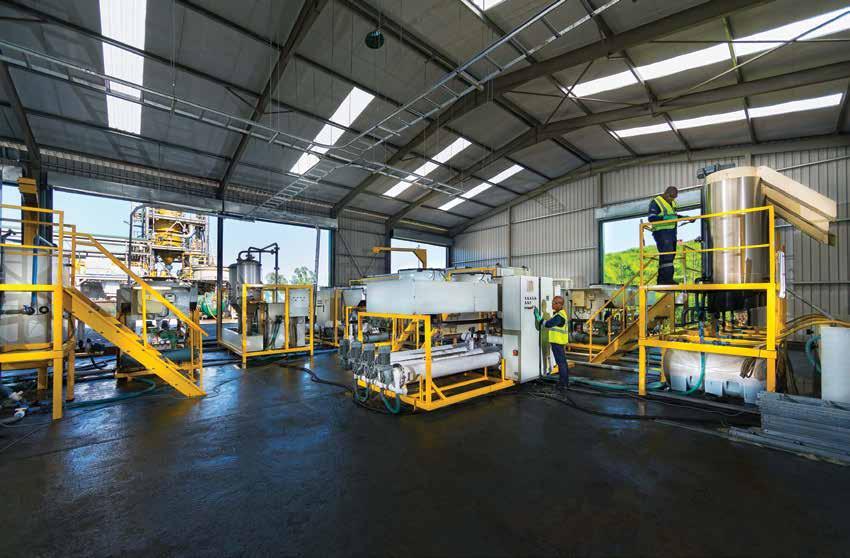
“We strive to be reflective of South Africa’s diversity, empowering our people, clients and other stakeholders through social investment and skills development.”
Hein Jansen van Vuren Marketing Executive, Engineered Linings
As a leading African waste management company, EnviroServ is proud to have achieved an industry-leading BroadBased Black Economic Empowerment (B-BBEE) Level 2 rating in terms of the revised Codes of Good Practice.
Our new B-BBEE status means that our customers get the benefit of enhanced procurement recognition from our new status, as well as from our status as a Black Women Owned entity.
This achievement signals the successful strides we are making in our company’s transformation and empowerment journey as committed to in our transformation charter.
We believe our BEE initiatives in the areas of supply chain management, skills development, employment equity enterprise and supplier development and CSI are truly transformative and changing lives.
In our first rating under the revised codes we achieved a Level 4 status. We set ourselves a goal to be a Level 2 this year and through robustly developed plans and focus we have achieved this. While we’re proud of our achievements, we remain cognisant that there is still much that needs to be done to achieve full true transformation and remain committed to continuing the process.
Customer Care - 0800 192 783 www.enviroserv.co.za
Retort Technologies’ managing director Nicolas Eleftheriades explains how his company’s unique thermal desorption plant is able to destroy “more than 99.9%” of hazardous waste, and is geared to achieve zero waste to landfill. P6
AQUATAN IS THE FIRST IAGI-APPROVED INSTALLATION CONTRACTOR IN AFRICA.
The fact that nearly 60% of our welders are certifi ed with the IAGI underscores our reputation for delivering geosynthetic installations professionally and reliably, every time.
Aquatan is ISO 9001/2008 certifi ed.
AQUATAN PROVIDES THE TOTAL SOLUTION!
In addition to our Geomembrane innovations, Aquatan’s HDPE, LLDPE, RFPP and EVA linings are used in applications ranging from hazardous liquid or solid waste to potable water reservoirs, linings of tanks, sewage ponds, anaerobic digesters, heap leach facilities, tunnels, canals, water features and underground water storage facilities. We also construct floating covers to Potable water, Molasses storage and Biogas containment reservoirs, small dams and tanks.
ENHANCED BARRIER SYSTEM®
Aquatan’s patented Enhanced Barrier System® (EBS) for waste sites is a new technology that has
gained international recognition for its dedicated and focused performance characteristics. The principle is to draw a fluid at a negative pressure through a barrier system to achieve:
1 Heat removal from Geosynthetic components
2 Post loading hydration of the Geosynthetic Clay Liner (GCL)
3 Removal of Volatile Organic Compounds (VOCs)
This innovative technology, for which Aquatan holds the worldwide patent, expands conventional containment barrier boundaries for protecting the environment far into the future.
The Landfill 2017 conference at Buffelsdraai Landfill in KwaZulu-Natal is done and dusted. Two and a half days were spent discussing and debating contemporary issues related to landfilling.
The common thread through most of the papers was that landfills are here to stay and will remain an integral part of the waste management hierarchy, but we need to design, construct and operate them properly in order to minimise their effects on the environment.
A reasonable assumption about a landfilling conference themed ‘Back to Basics’ is that it would likely champion a call to landfill all waste – in other words, to return to the habit of collecting waste
was meant by ‘basics’ was never defined, the presenters all introduced their own perception of the fundamentals, be it proper design, proper operation, or only disposing of waste that cannot be diverted. Perhaps the common definition of ‘basics’ coming out of this conference was that we should all accept responsibility for our waste, whether we collect, reduce, recycle, treat, dispose, design or enforce. It does not matter on which level of the waste hierarchy we operate individually; it is our waste problem and we should apply our minds to thre management thereof.
We should all accept responsibility for our waste, whether we collect, reduce, recycle, treat, dispose, design or enforce.”
true meaning of integrated waste management. One aspect that was mentioned a number of times at the conference is the generally poor quality of landfill operations. This is not a new topic. Perhaps the way forward is to include more operational guidelines and controls into waste management licences so that these can be included in external compliance audits.
The Institute of Waste Management of Southern Africa organises these events so that we – from all spheres of waste management – can learn from each other and, in so doing, develop an understanding of the benefits and limitations of all waste management activities. Waste management can never be only landfilling or only recycling or only alternative technologies. We need to share knowledge so that we can all understand the
Jan Palm
President: IWMSA
From one conference to the next: a call for papers for WasteCon 2018 has recently been released. The theme of this flagship conference and exhibition of the IWMSA to be held at Emperors Palace on 16 to 18 October 2018 is ‘Implementing the Waste Hierarchy’. Please submit your abstracts and show us how you are taking responsibility for your waste.
On a final note I would like to thank IWMSA vice-president Jonathan Shamrock for the effort he has put into the Institute over the years, and wish him and his family all the best with his new career in New Zealand. The waste management industry in South Africa will surely miss his valuable input.
Dispose of your used oil here... ...and you could end up here.
Up to 15 years imprisonment.
So for peace of mind, contact a NORA-SA approved collector or recycler to safely dispose of your used oil. Call 0860 NORA-SA (6672 72) for a collector in your area.
Publisher Elizabeth Shorten
Managing editor Alastair Currie
Editor Frances Ringwood
Head of design Beren Bauermeister
Chief sub-editor Tristan Snijders
Sub-editor Morgan Carter
Contributors Liz Anderson, Jan Palm,
Chemical and Allied Industries’ Association
Client services & production manager
Antois-Leigh Botma
Production coordinator Zenobia Daniels
Financial director Andrew Lobban
Distribution manager Nomsa Masina
Distribution coordinator Asha Pursotham
Printers United Litho Johannesburg
Advertising sales Tazz Porter
Tel +27 (0)11 465 5452
Cell +27 (0)82 318 3908 tazz@connect.co.za
Publisher No.9, 3rd Avenue
Rivonia, 2191
PO Box 92026, Norwood 2117
Tel +27 (0)11 233 2600
Fax +27 (0)11 234 7274/5 www.3smedia.co.za
Annual subscription subs@3smedia.co.za
R200.00 (incl VAT) South Africa ISSN 1680-4902
Institute of Waste Management of Southern Africa
Tel: +27 (0)11 675 3462
Email: gail@IWMSA.co.za
All material herein is copyright protected and may not be reproduced either in whole or in part without the prior written permission of the publisher. The views and opinions of authors expressed in the magazine do not necessarily reflect those of the publisher, editor or the Institute of Waste Management of Southern Africa.
Returning from Landfill 2017, hosted at the Buffelsdraai Landfill in October 2017, I was struck by the passion, commitment and technical brilliance of all the presenters, without exception. The theme of the event was ‘Back to Basics’ and, during the workshop on the same topic, it became apparent that one of the biggest challenges facing the industry is how to make landfilling more ‘sexy’ in order to get the necessary public (and consequent political) support and funding.
Chaired by Nick Mannie, the workshop kicked off with the question: “Are we investing in appropriate solutions and can we deliver on the high standards we set for ourselves?”
The gap between municipalities’ budget for their facilities versus what they need to spend in order to comply with current legislation is wide. With so little funding, it will be impossible to achieve what the ‘visionaries’ foresee as a future without landfills. Even if the funding were available, it would still be worth asking whether such a state of affairs would even be appropriate for South Africa.
“The fundamentals are known by the majority of landfill designers and managers. Collection, transportation and disposal are not rocket science,” Jonathan Shamrock pointed out, adding that funding is the major stumbling block.
By contrast, Lyndsey Strachan argued that many sites are poorly run dumps, yet they still require expensive capital equipment like bulldozers operating on-site. “We still need to concentrate on the basics by making sure that those who run our landfills are properly trained, from the technical engineer to the guy running the bulldozer.”
The truth is that both underfunding and a lack of capacity affect South African municipalities, albeit to different degrees at different sites.
To me, this indicates a more systemic problem: while there are many passionate, committed people in the South African waste management industry, there are still too many outside (and even inside) the industry who simply do not appreciate its importance and relevance to their lives.
For this reason, it’s important to educate the public about waste management and how it impacts their daily lives. Even more so, it is essential that those pillars of excellence within the industry learn how to tap into unconventional funding sources, from overseas environmental donors to global non-profits. This will ultimately result in sites that not only meet but exceed expectations.
With those words, I’d like to say “goodbye” to the many excellent colleagues and friends I have worked with in this sector over the past three years.
Although I have decided to go into education, I will never forget my time working with you all and the important lessons you have taught me. There are many among you who I will miss greatly.
Hazardous waste management leader A-Thermal Retort Technologies specialises in thermally treating and managing hazardous and toxic waste. Managing director Nicolas Eleftheriades explains how A-Thermal now offers two new services for their valued clients: a zero-to-landfill solution and thermal treatment for bulk flammable liquids, all while continuing to ensure a hazardous waste thermal destruction efficiency of “greater than 99.9%”.
A-Thermal has been a leader in the destruction of pharmaceutical and industrial chemical waste for more than 21 years. Our excellence in these fields has seen us maintain our ISO 14001 certification since 2009,” says Eleftheriades.
“In addition, the well-being of our staff, and maintaining high levels of customer satisfaction and service delivery resulted in A-Thermal achieving its coveted ISO 9001 and OHSAS 18001 certification in March 2016.”
A-Thermal is also a signatory of the Chemical and Allied Industries’ Association (CAIA) Responsible Care® initiative. This international voluntary programme raises standards for the transportation, management and handling of hazardous materials, winning greater trust from the public. A-Thermal is a processing facility that operates 24 hours a day. Process safety is of paramount importance to a successful operation. This drives A-Thermal’s subscription to and maintenance of CAIA’s high process safety standards.
“A-Thermal’s values align with CAIA’s in that both organisations seek to improve the quality of human life and the economy, without harm to people, property or the environment,” explains Eleftheriades.
Developed by Eleftheriades’ father, the late Dr Christos Eleftheriades, A-Thermal’s thermal desorption plant based at the company’s Olifantsfontein facility uses pyrolysis technology that is capable of achieving a 99.9999% destruction of all hazardous waste.
“Our company has completed an exciting project that will see us produce a carbonised residue by-product from the various and variable forms of hazardous waste processed at our facility, which we believe to be a world first. The carbonised
Nicolas Eleftheriades, MD, A-Thermal Retort Technologies
residue has similar properties to coal and can be used as an alternative form of fuel, essentially making A-Thermal a zero-landfill treatment and waste management facility,” says Eleftheriades.
“Secondly, a new addition to our product line we completed as a service to customers is the Aurora Calorific Converter. This new feeding system allows
• Correct storage of waste according to chemical compatibility and hazard nature
• An electronic waste-tracking system for easy reference and up-to-date stock control
• Zero-liquid discharge to the municipal wastewater system, including on-site water
• Treatment and recycling and recovery of products
• Control interlocks on equipment for correct operating conditions
• Residue analysis and reclassification by external, accredited laboratories
• A continuous emission monitoring system that operates 24/7 in monitoring our emissions
• Emergency response procedures, including drills
• Bi-annual environmental monitoring committee meetings
• External audits of the Environmental Management Plan
• Submission of a Quarterly Emission Report to the regulating authority
for the safe treatment of any and all flammable liquids. This is aimed at bringing relief to our customers who are now faced with more stringent landfill restrictions regarding liquid wastes with high calorific value.
“A-Thermal focuses on the safe disposal of toxic and hazardous wastes. Additionally, the business has been inspired by the Department of Environmental Affairs’ adoption of the European Union’s waste hierarchy, to incorporate other forms of waste diversion, like recycling, wherever possible. We focus less on minimisation and reuse, as this is extremely difficult to do when managing hazardous waste,” he adds.
Through technology partnerships with companies like Carbo Consult, Cecor, Coal and Waste, Energia and Waste Resource Management, A-Thermal is able to offer a complete solution for managing waste from all industries.
The company’s service offering includes: chemical waste destruction, pharmaceutical waste destruction, medical waste treatment, on-site waste management, land remediation, recycling and disposal of general waste, hazardous and general waste transportation, supply of waste packaging, waste management training, environmental consultancy services, and tyre waste management.
“We’ve come across some extremely tough waste streams over the years and we’ve never shied away from a challenge. When we are confronted with unusual waste to be disposed of, we partner with clients, working with them until their needs to dispose of waste in a legally compliant, environmentally friendly manner are met,” says Eleftheriades.
Managing the multiple challenges of hazardous waste to satisfy safety, environmental, and
regulatory directives requires an experienced partner with a proven track record in all relevant areas. From on-site pickup to final treatment or dis posal, it is important that the person or company responsi ble for creating that waste complies with the relevant norms and standards.
“As a hazardous waste treatment facility, caring for the environment is a key priority in all our operations,” says Eleftheriades.
A-Thermal saves its clients time and money by providing a solution that promotes business sus tainability through long-term risk management. “We remove and assume liability so that any company we partner with, or offer our waste treatment services to, can be assured that their waste is treated correctly and its destruction is verified by third-party-accredited laboratories. Further, because A-Thermal’s compliance meets global standards, clients will not need to continuously keep up with the latest legislation changes to be compliant. They can rest assured that we are continuously working to protect the environment and our future. All clients receive certificates of destruction, and A-Thermal can be audited by the client. In addition, our resident pharmacist gives clients expert technical support for medical and pharmaceutical waste products, and oversees the destruction of pharmaceutical waste,” says Eleftheriades.
www.athermal.co.za
“At A-Thermal, we permanently destroy toxic and hazardous waste, completely removing the danger that waste poses to human health and the environment,” he concludes.
The high risks associated with the transportation of dangerous goods on South Africa’s roads require the strictest observation of safety, health and environmental practices. Submitted by the Chemical and Allied Industries’ Association (CAIA)
Signatory members with CAIA are assisted in the transportation and related sectors to improve their safety, health and environmental performance for the storage, distribution and transportation of dangerous goods, says Deidré Penfold, executive director, CAIA.
As CAIA and its members often deal with transporting hazardous materials and the specific accompanying risks, it is essential for hauliers and logistics service providers to have management systems in place to identify and control these risks.
“Failure to do so can cause harm to people, animals, property and the environment in the event of an accident,” warns Penfold.
Dangerous goods professionals need to be well equipped with the latest information to make the best decision when they are faced with a dangerous goods incident. Dangerous goods incidents are most often caused by human error or mechanical/design failure in existing systems or infrastructure.
For this reason, CAIA hosted a successful Responsible Care® Transportation of Dangerous Goods Seminar in Johannesburg and Durban on 17 and 19 October 2017, respectively. The main objective of the seminars was to provide participants with hard-hitting and useful information, which they could apply directly in their workplaces.
In 1994, CAIA launched the Responsible Care® programme, the global chemical industry’s
unique initiative to improve health, safety and environmental performance, and to communicate with stakeholders about products and processes in South Africa.
All members voluntarily sign the CAIA Responsible Care® public commitment, pledging to conduct all operations, including the transport of hazardous materials, in a safe and environmentally sustainable manner and to incorporate the Responsible Care® ethics and requirements into their business strategy, management system and daily operations.
“CAIA is proud of the fact that the association oversaw the training of more than 50 new local Safety & Quality Assessment for Sustainability – Southern Africa (SQAS-SA) auditors in August 2017. These auditors assess the compliance of hauliers’ and logistics service providers’ SQASSA management programmes for the transport of hazardous and low-hazard materials every two years,” says Penfold.
“CAIA also produced a Dangerous Goods Segregation Wheel that indicates the load or storage compatibility of mixed cargoes at a glance, using the class warning diamonds in an easy-to-understand wheel. It assists in the segregation and storage of chemicals according to their hazard class. This prevents an undesirable chemical reaction from occurring should two or more chemicals accidentally interact when stored too close together,” she says.
Continuous efforts to improve safety during transportation and the associated handling of
Deidré Penfold, executive director, CAIA
chemicals are part of CAIA’s overall objective, in accordance with the guiding principles of Responsible Care®. CAIA achieves this objective by meeting legislative compliance, and by adopting cooperative and voluntary initiatives with government and other stakeholders.
“CAIA encourages operators of heavy commercial vehicles and road transportation companies to introduce a meaningful approach that focuses on crucial safe operating management practices. This includes, but is not limited to, driver health and wellness programmes, effective transport route risk assessment, behaviour-based safety for drivers, effective investigation of transport accidents and incidents, and the appropriate use of the learnings from such incidents,” explains Penfold.
Companies that are signatories to the Responsible Care® initiative are required to ensure that their transportation service providers comply with the requirements of SQAS-SA.
Liz Anderson , executive director, Responsible Packaging Management Association of Southern Africa
(RPMASA), unpacks the legal requirements for packaging, along with the penalties of non-compliance.
Packaging for all dangerous goods is regulated, as well as packaging for many foodstuffs.
Dangerous goods (DG) are chemicals and articles that have been classified at a global level and designated with a UN number, together with a hazard class, as they can pose a risk to people, property and the environment if not correctly packaged, handled, stored and transported.
They include industrial and retail products such as household chemicals and cleaning materials, aerosols, personal products, detergents, paints, solvents, pool chemicals, pesticides, fuels, batteries and many other everyday products.
In the 1950s, the UN – recognising increasing global trade through shipping, road and rail transport – initiated a Committee of Experts to compile technical regulations for safe packaging, documentation and transport to provide for common understanding and use for safe transport around the world. The aim was to enhance general safety and prevent accidents.
Through this committee, the UN Model Regulations for Transport of Dangerous Goods evolved, forming a global regulatory umbrella for all modes of transport. These cascade into
The essential rules for dangerous goods packaging are:
• Contents must be compatible
• Compliance with dangerous goods specifications
• Packaging must be UN tested and certified
• Each unit of packaging must be permanently marked with the correct UN packaging certification classification to confirm that it is safe for use with the product to be packed
• Correct labelling with product name and UN number, hazard type and pictogram, name of manufacturer and 24/7/365 emergency contact number
Modal Regulations, through the International Civil Aviation Office (for air), International Maritime Dangerous Goods (IMDG) Regulations (for sea), and regional and national regulations for road and rail transportation. South Africa is a member of the UN committee and has adopted its regulations as law through the National Standards.
All dangerous goods are classified into one of nine classes based on their physical and hazardous properties. These properties include whether the goods are explosive, gaseous, flammable, liquid, solid (including powders), oxidising chemicals and organic peroxides,
The UN Model Regulations for Transport of Dangerous Goods provides a regulatory umbrella for all of the different modes of transport across the globe
radioactive, corrosives or otherwise characterised as “class nine miscellaneous dangerous goods and articles including environmentally hazardous substances”. The nine classes are defined in the UN’s model regulations and in SANS 10228 and SANS 10229.
All goods are regulated for packaging, labelling, documentation and consignment procedures for transport. They are allocated a UN number, which must be marked on the label and accompanying documents in order to promote safe handling. This must be carried out in conjunction with the placement of the applicable ‘hazard’ warning diamond.
Key packaging principles
Safe packaging is the starting point for safe transport. Compatibility with the product to be packed is a fundamental requirement for all packaging. It is therefore essential for the packaging designer as well as the product manufacturer to understand the composition and properties of the products to be packed.
Safe, compliant packaging specifications apply to retail products, samples and industrial products for conveyance using any and all modes of transport.
Packaging regulations are regularly reviewed by the UN Committee of Experts in terms of new technologies and investigations into accidents and incidents around the world. These are clearly defined and any necessary improvements are included in regular biennial revisions of the model regulations, which are turn taken into the following revision of the modal and regional regulations.
Responsible packaging manufacturers will advise their customers on what specification of packaging is appropriate for their products, as long as the product is correctly classified. Product manufacturers are responsible for packing and labelling their products in accordance with UN regulations. This is the due diligence of product stewardship and producer
Receiving countries that deem dangerous goods packaging to be non-compliant can place goods under quarantine until the manufacturer has repacked their goods, at significant cost to themselves
responsibility, regulated under transport and environmental legislation, among others.
Packaging is the starting point for safe handling, storage and packaging. The use of non-compliant packaging could lead to failures that could have serious adverse effects on workers, the public, property, and the environment. Liability and the costs to rectify any harm done would fall to the manufacturer if they did not use compliant and properly marked and labelled packaging.
Compatibility with the product to be packed is a fundamental requirement for all packaging
Exporters could have their shipments denied under IMDG law. Additionally, receiving countries that find packaging to be non-compliant may quarantine shipments and require the manufacturer to repack and label goods in quarantine while bearing all costs and paying a hefty fine. European Union countries are
particularly strict and have further tightened their compliance monitoring since the Globally Harmonized System (GHS) requirements came into effect from 1 June 2015.
Companies’ insurance may refuse to cover such costs, as these packaging regulations have been in place globally for over 60 years. Moreover, the cost of harm to people and the environment is high, and any adverse publicity can be extremely
damaging to non-compliant manufacturers.
In 2003, an additional GHS classification scheme was introduced at the UN by a new Committee of Experts. This added human health and environmental risks to the existing regulatory policy that focused on physical risks posed by the transportation of dangerous goods.
For industry, this means that product manufacturers have to classify their products according to the new GHS classification and compile GHS-compliant safety data sheets. Also, labelling must be correct and the manufacturer must ensure that their packaging is still appropriate regarding any health and environmental hazards their product may pose.
(EL) is a division of PSV Industrial and has been servicing the industrial and mining sectors for 33 years. Marketing Executive Hein
describes how EL provides the best-quality product for specific applications in order to protect human health and the environment.
What does EL offer that other geomembrane suppliers do not?
HJvV EL has been working hard on finalising a B-BBEE equity partnership, which will be effective in the next few months. By becoming a fully B-BBEEcompliant linings company, EL will be able to expand our services to government and other statutory industries. We strive to be reflective of South Africa’s diversity, empowering our people, clients and other stakeholders through social investment and skills development.
What is the company’s stance on pollution dilution versus concentration and containment?
The global population is growing rapidly and open space is at a premium. We should, therefore, be reducing the quantity and type of waste sent for landfill disposal as far as possible. The dilution of hazardous or toxic substances by mixing with unpolluted wastes is not an acceptable substitute for the treatment of waste, its containment or disposal.
Even when diluted, these toxic contaminants (albeit at lower concentrations) remain a threat to the environment.
At EL, we believe that mankind has a responsibility to maintain and protect our natural resources. Future generations need to inherit a sustainable planet with the critical objective of perpetuating this legacy indefinitely.
How would concentration and containment assist?
Processes for the treatment of toxic waste produce a
concentrated mass of contaminants that need to be safely contained, utilising the best practices currently available. It is, therefore, critical that these concentrated contaminants be stored using the best practices available. Concentration has a much smaller disposal footprint than pollution dilution. It is critical all water resources be regularly monitored to uncover pollutants. Polluting companies/individuals must be held criminally accountable and forced to fund the clean-up.
environmental protection but always strive to remain competitive.”
What is the company’s full range of landfill lining products and services?
EL specialises in the supply and installation of geomembranes and other geosynthetic products for the containment of liquids and solid waste. Installations can range from potable water structures to large containment facilities.
The lining systems in these structures range from singlelayer systems to complex multilayer systems; depending on the material stored and the environmental protection level required. Our lining systems are supplied and installed to the highest available quality standards and material specifications.
EL supplies and installs ( inter alia ):
• geomembrane linings, in highand low-density polyethylene
• geotextiles – full range of weights
• geosynthetic clay linings
• drainage composites – Leakdrain
• reinforced flexible geomembranes.
What installation quality assurances do you offer?
The linings EL installs are manufactured by its suppliers in accordance with the international Geosynthetic Research Institute standards for geomembranes and barriers (GRI-GM). This specification defines minimum physical, chemical and mechanical properties that must be met, or exceeded, by the geomembrane. Liners that meet these standards are made from premium-grade, virgin polymers based on the best available technology. They have the necessary carbon black, heat stabilisers and antioxidants to provide the best possible ultraviolet protection.
EL is ISO 9001:2008 Quality Management System certified
and installations are done in accordance with SANS 10409:2005.
Our experience and track record are proof that EL will honour our commitments to our clients. Our vision is to provide clients with the best possible solutions available for the protection of the environment and scarce water resources.
What is EL’s business philosophy, mission and values?
We are committed to supplying and installing the best-quality geosynthetic materials available through continual improvement of our installation methods, quality management systems and training.
We do not compromise on quality and environmental protection but always strive to remain competitive.
In what applications has EL installed geosynthetic linings?
EL has installed geosynthetics in numerous structures, including:
• landfills
• heap leach pads
• tailings storage dams
• solution storage ponds
• water storage ponds
• oxidation ponds
• floating covers
• reservoirs
• aquaculture ponds
• irrigation dams
• water features.
In each and every case, the geosynthetic linings installed by EL have performed the function for which they were designed and specified. Whether as a lining for an irrigation dam or a base layer on a heap leach pad to contain pregnant gold solutions, these linings are all success stories.
Materials recovery facilities (MRFs) can be either ‘clean’ or ‘dirty’. While dirty MRFs have a bad reputation compared to their cleaner cousins, they still offer value if designed and operated correctly by motivated staff who share in the facilities’ profits. By Frances Ringwood
The two different types of MRFs have fundamental differences. One is ‘clean’, accepting pre-sorted recyclables from household kerbside collection, factories, retail centres and industry; the other is ‘dirty’, accepting unsorted household waste that inevitably contains perishable or rotten organic material.
Both types of facilities use many of the same machines, equipment and sorting arrangements for waste sorting. This might include steel skip bins, conveyors, screens and trommels. In South Africa, one of the main benefits of an MRF is that a single facility can create several dozen jobs, depending on the size and daily volumes of waste being processed. Globally, the value of MRFs is recognised in their considerable contribution towards improving national recycling rates, assisting to achieve Zero Waste to Landfill goals, fuelling a circular economy, and creating energy from biogas.
Processing volumes make the difference in how profitable either type of site will be. The type of waste will also affect the selection of certain machines for MRFs, as well as whether or not to include biogas tanks in the overall facility design. Since clean MRFs accept predominantly clean, pre-washed and pre-sorted recyclate streams like paper and cardboard, recovery rates are relatively high and should be around 90%. Recycling rates from dirty MRFs are much lower for a number of reasons.
These reasons include: grease-stained paper and boards cannot easily be recycled; adulterated plastics are difficult to sort; rotted material smells bad and can be maggot infested, which puts off waste sorters… the list goes on.
Even so, recycling rates at different dirty MRFs vary considerably, with some estimates being as low as 5% and others reaching 45%. Low recycling rates can strain profitability, causing
cash-flow issues and MRFs’ eventual failure. Understanding the reasons why MRFs fail and how to set them on the road to profitability and sustainability protects owners’ investments while also improving the overall investability of MRFs.
According to Ika Pietersen, national operations director, Waste Plan, MRF failures can normally be attributed to four main factors.
“The first is excessive fixed costs, such as the rental of a facility or the cost of capital equipment needed to operate the facility. These costs need to be considered very carefully during the planning phase of an MRF, as they are likely to be there throughout the lifespan of the operation.
“Second, MRFs fail due to poor layout and material flow. When the layout is not optimal, material cannot be processed fast and efficiently enough. This leads to congestion within the MRF, which reduces efficiencies even further, resulting in higher processing costs.
“Insufficient feedstock is another key reason behind MRF failure. Given the fixed and variable costs within an MRF, a minimum tonnage of material is required to cover these costs. It is, therefore, critical to make sure that the size of your MRF is in line with the expected tonnages it will receive.
“Finally, an MRF cannot be profitable if the workforce responsible for sorting is not both effective and efficient. Labour utilised in an MRF must translate to a quality product produced at a cost-effective rate. To achieve this, the correct management approach is needed in order to achieve desirable productivity while maintaining a high level of staff morale,” he explains.
South African waste management professionals tend to agree that finding the right approach to managing staff is the most critical factor in determining the success or failure of MRFs. It is also one of the most complex and difficult issues to navigate, especially given South Africa’s strict standards governing labour relations.
Waste pickers explain how they foresee labour being managed effectively at MRFs: “We urge government to develop MRFs in all municipalities. MRFs should be operated and managed by waste picker cooperatives with the support of government and technical support.
“Further, government must ensure that we are involved in waste management related projects as they are being planned and developed, and not only when implementation takes place,” The South African Waste Pickers Association said in a statement earlier this year.
When workers see that the work that they put in has a direct impact on the money they get out, this provides a powerful incentive to keep recycling rates high, raising the profitability of the business for all involved.
“MRFs fail due to poor layout and material flow. When the layout is not optimal, material cannot be processed fast and efficiently enough.”
“At the Malmesbury MRF, some years ago, staff were incentivised by being given a share of the facilities’ profits.”
Farms cover South Africa extensively and, as a result, the agricultural sector has the biggest impact on the country’s natural habitat. As automation and the use of vehicles and equipment increases in agriculture, more lubricant oil enters the environment from farms.
According to estimates, South Africa generates an average of 120 million litres of used lubricant oil a year, with about 10 million litres of this generated by the agricultural sector.
On average, a tractor can hold anywhere between 40 ℓ and 100 ℓ of oil and the average medium commercial farm can have anywhere between three and ten tractors. Considering that one litre of used oil has the capacity to contaminate a million litres of water, this is a potentially devastating amount of used oil, which could make its way into our environment if not collected and recycled responsibly.
Used motor oil contains numerous toxic substances, including polycyclic aromatic hydrocarbons, which are known to cause cancer. In addition, tiny pieces of metal from engine wear and tear – such as lead, zinc and arsenic – make their way into lubricants, further contributing to the polluting potential of used motor oil. Motor oil is exposed to heat and oxygen during engine combustion, which changes its chemical make-up.
Additionally, since spent motor oil is heavy and sticky, and contains an extensive concentrated
cocktail of toxic compounds, it can build up and persist in the environment for years.
Bubele Nyiba, CEO, Recycling Oil Saves the Environment (ROSE) Foundation – an organisation that champions the responsible management of used oil in South Africa – explains that once motor oil escapes the engine, it has the potential to travel long distances, with most of that used motor oil eventually making its way into waterways in the form of run-off.
We are comforted by the knowledge that farmers would never knowingly damage the environment.”
Bubele Nyiba, CEO , ROSE Foundation
“Once it reaches waterways, used motor oil is toxic to the plants and animals living there, and the oily film created on the surface of the water can impair natural processes, such as oxygen replenishment and photosynthesis. Used motor oil can also pollute soil and drinking water.
“With the frequent droughts we are experiencing, caring for our water resources has become a massive national priority,” says Nyiba. “The protection of visible water sources is as important as protecting underground water, especially
because farmers regularly use boreholes to tap into underground water.”
The farming community is known for its creativity and survival skills, hence the saying “‘n boer maak ‘n plan”. Unfortunately, in many farming communities in South Africa, cost-cutting methods and traditional practices that have been carried out on farms for generations are often not environmentally friendly and sustainable. Such practices include spraying used lubricant oil on the ground in order to limit dust damage to crops and also using the old oil on fence
posts as a preservative, as well as rubbing it on to livestock as a parasite deterrent.
“Conversion to more sustainable agricultural practice is necessary to both preserve South Africa’s biodiversity and ensure a future resource base,” says Nyiba.
“Many farmers do their own oil changes and minor services when their vehicles are out of maintenance plan and manufacturer’s warranty. The ROSE Foundation encourages these farmers to gather and store their oil in containers that can easily be transported to the nearest town and dropped off at a vehicle service workshop.”
Alternatively, there are some ROSE Foundationregistered collectors who operate in rural areas and will remove this oil for the farmers in an environmentally compliant and safe manner.
“We are comforted by the knowledge that farmers would never knowingly damage the environment.
“That is why it is important for us to reach out and create awareness about the potential harmful effects of used oil on the environment,” concludes Nyiba.
This year, National Recycling Day (15 September) saw the plastics recycling community gather at Ekurhuleni’s Emperors Palace at a glitzy event celebrating industry innovation. The SAPRO Awards honour those who make a difference by creating and purchasing recycled plastic products.
By Frances Ringwood
The biennial South African Plastics Recycling Organisation (SAPRO) awards recognise those South African men and women who design, manufacture, market and create markets for products either made entirely, or from a percentage, of recycled plastics.
Apart from recognising industry excellence, the awards serve an important function in that they create awareness among brand owners and product designers regarding the need to prioritise the use of recycled material in their plastic products including plastic packaging. Creating this demand stimulates creativity and innovation among plastics recyclers, converters and product designers, inspiring them to think of new ways to reuse plastic, diverting this waste from landfills and positively impacting South Africa’s ambitious national goal of zero waste.
The festivities were supported by platinum sponsors Erema Plastic Recycling Systems and Polyco, and gold sponsors Zerma and Plastics|SA, among others. These included a three-course gourmet dinner, a performance by musical group New Roots, and entertainment by MC Eugene Khoza (the voice of Nedbank’s
advertising campaign) and beloved South African comedian Evita Bezuidenhout.
The judging panel included the likes of Anton Hanekom, executive director, Plastics|SA; Don MacFarlane, packaging manager, Woolworths; Kobus Theron, quality control manager, Marley Pipe Systems; and Wendy Knowler, a well-known consumer journalist for the Sunday Times and East Coast Radio.
Entries were received from all over South Africa in five different categories. These were: products made from 100% post-consumer recyclate, products containing a percentage post-consumer recyclate, products made from mixed materials, novel and artistic products made from discarded plastic products, and a new category for concept ideas for new end markets.
“The criteria
RIGHT These sleeping bags for the homeless are made of PVC recycled from billboards
LEFT MyWaste Mouldings’ Waste Bin Separator recycles Tetra Pak packaging to assist municipalities with separation at source
SAPRO congratulated retailers who’d shown commitment to using shopping bags made from 100% recycled plastic
adjudicating each entry included the life expectancy of the product, the sustainability or longterm demand and market acceptance of the product, the measures taken to ensure product consistency and customer satisfaction despite
• Products made from 100% post-consumer recyclate – Cycliq for its Space Base bed base, which is lightweight, takes up a quarter of the storage space of alternatives and is ideal for export
• Products made from mixed materials – Greenlite Concrete for its Jumbo Building Blocks, which are made from recycled expanded polystyrene
• Products made from a percentage post-consumer recyclate –Usabco for its Addis 10 ℓ watering can
• Novel and artistic products – Street Sleeper for its waterproof sleeping bags for the homeless, which are made from recycled polyvinyl chloride banners
People’s choice – Infinite Industries for its manholes and covers made from mixed material for foot traffic up to 200 kg or for heavy-
Concept ideas – No winner was selected for the new concepts, as none of the three products nominated had been produced yet. Potential investors are sought to put these ideas into production.
Agriflow’s pipe cores, which would see recycled polypropylene being used to replaced cardboard cores used in industrial and consumer products like sandwich wrappers
Tereco and Plastic Trading in Atlantis’ roof tiles and cobblestones made by blending post-consumer mixed waste plastics with sand
Alan Lambert of Lambert Legal Consulting’s SuperSink, which is a small carry basin with a plug that can fit into a sink to reduce water use or in the shower to catch run-off – saving water
recycled material content, tonnage or potential tonnage of plastics that were converted and therefore diverted from landfill, technical achievements in manufacturing to overcome recycled material challenges, replacement of alternative materials, originality of design, and the care and pride with which the product was manufactured,” explained Khoza, ahead of the winners being announced.
The awards ceremony also featured a fun, new ‘people’s choice’ category, allowing those attending the event to view and then vote for their own favourite recycled plastic product.
First prize (Gold) for the overall winner of the Best Recycled Product of the Year was awarded to Graham Coleman and Gianni Nosenzo of Cycliq in Wadeville. Their product, the Space Base bed base, received the award owing to it being a product of high quality and market integrity, designed and marketed using recycled polypropylene from automotive parts, mainly bumpers.
Rudi Johannes, chairman, SAPRO, explained, “The judges were impressed by the product’s consumer acceptance, cost-effectiveness and the extent to which it reduces the amount of plastic ending up in landfills.
“Weighing just 19 kg, the double base folds up into a quarter of the space of a traditional
bed base, making it far easier to move, store, reassemble or export to growing markets in places like Australia and the Dominican Republic.
Locally, their plant produces about 3 500 of the black bases per month, but has the capacity to double that.”
Through this product, Cycliq has completely reinvented the bed base, creating a more user-friendly alternative to the more cumbersome wooden option.
“The past few years have not been easy for plastic recyclers. Virgin polymer prices are low and operating costs have increased as a result of higher fuel prices, and increased energy and labour costs.
“Moreover, traditional markets for recyclate have reached a point of saturation. Recyclers cannot be expected to take any plastic product at no charge and turn it into a perfect raw material that will solve the world’s energy crisis and change littering habits.” Rudi Johannes, chairman, SAPRO
LEFT Graham Coleman of Cycliq received the certificate for Best Recycled Product of the Year for the Space Base bed base from Rudi Johannes, chairman, SAPRO
ABOVE Twenty-three entries were selected as finalists, with certificates handed over to:
1. Agriflow for its low-density polyethylene irrigation pipe and the PP cores
2. Bosveld Gear for its rifle rest bag set
3. Cycliq for its Space Base bed base
4. Excellence in Engineering for its Wellfed feeding troughs
5. Greenlite Concrete for its Jumbo Building Blocks
6. Infinite Industries for all three of its entries, namely manholes and covers, heavy-duty sleeper ramps, and cable trench covers
7. Lambert Legal Consulting for its new SuperSink concept
8. MyWaste Mouldings for its Waste Bin Separator
9. Plastic Droppers for its Ridgedrop dropper for fences
10. Plastica Film Extrusions for its Smokey Wood bag
11. Roga Plastics for its Roof Undertile Membranes
12. Shik Shack Backpackers & Community Tours for its Eco Brick Backpackers Building system
13. Street Sleeper for its sleeping bags for the homeless
14. Tereco’s concept idea of Terra Pave or Terra Tile
15. Tuffy Brands for its two entries that have made it to the finals, namely its Checkers carrier bags and Tuffy refuse bags
16. Unilever and RPC Astrapak are finalists for their combined Organics shampoo bottle entry
17. Usabco Industries for its Addis 10 ℓ watering can
18. Verigreen from KZN for its Supa Mama swing bin liner
19. Wreaths International for its wreaths and baskets
On 25 July this year, Mpact Recycling opened its first liquid packaging recycling facility at its New Era mill in Springs. The second facility of its kind in South Africa, this R46 million plant is capable of recycling eight soccer fields of single-stacked baled material per year. By
The new plant will be able to handle up to 29 000 t of liquid packaging recycling per year, turning it into a range of useful products – from corrugated board for freight packaging to point-ofsale material. It will create six direct jobs and up to 500 indirect jobs, all of which will go towards feeding and supporting thousands of people living on or below the bread line.
Attending the event were heads of industry and government representing Mpact, packaging manufacturer Tetra Pak, the Paper
Frances Ringwood
Recycling Association of South Africa (Prasa), the Department of Trade and Industry (DTI) and the Department of Environmental Affairs (DEA).
Bruce Strong, CEO, Mpact Group, puts the achievement of getting this project off the ground into perspective: “It is important to highlight at the outset that paper recovery rates in South Africa are good by any standard. Of the 2 Mt (megatonnes) of paper available for recycling, about 1.4 Mt is already reprocessed.
“This puts our paper recovery rate across all grades at about 68%, which is comparable
with many developed nations. When it comes to paper packaging, it’s even more impressive, with a recovery rate well above 80% – which is world class,” Strong states.
He adds, “As a company, Mpact alone recovered 560 000 t during 2016 for reprocessing in our paper mills and those of our customers. The key to this level of recycling is to keep up the demand for recyclable products from paper and other manufacturers.”
Balancing the supply and demand equation requires there to be enough high-quality
recyclable material available to sustain the market for goods made using recycled card board and paper. Although South Africa already has more installed capacity for processing paper packaging then there is available, plants such as this fulfil a valuable function because they are specially engineered to handle unconventional bonded and mixed materials. This adds to the bulk of fibres used in paper recycling, adding to the sustainability of end markets and enabling an increase in demand.
Liquid packaging cartons, which are typically milk or juice cartons, are made up of about 75% paper board, lined with thin folds of polyethylene and aluminium, otherwise called poly-alu – which ensures the contents are kept safe without refrigeration.
This multilayer system means these products are difficult to recycle without substantial investment. Besides the paper fibre being used to make cardboard and paper, there’s also an opportunity for the beneficiation of poly-alu into products such as roof tiles or even energy. These are proven concepts elsewhere in the world but making them work requires support from regulators so that entrepreneurs are able to establish micro, small and medium businesses along the supply chain.
Godfrey Zwane, manager of the new plant, explains how it works, “Bales and water are automatically added to the pulper, to separate the poly-alu and the foil from the fibre into two streams. The main stream is for the fibre, which gets stored and screened. Screening removes any leftover plastic. Then the fibre gets blended with other recovered fibre.”
Tetra Pak fibres created through this milling process are short and need to be combined with other long fibres to increase the strength of the end product.
“From the mill, the recycled fibres are wound around massive reels, after which they are put through various processes and machines to make corrugated cartons and other corrugated products. We produce about 30 000 t of corrugated products for various end users, making use of predominantly recycled papers from our Mpact mills,” he adds.
This puts our paper recovery rate across all grades at about 68%, which is comparable with many developed countries.”
Bruce Strong,CEO, Mpact Group
The only other plant capable of recycling Tetra Pak packaging in South Africa is Gayatri Paper Mills in Germiston, which is capable of handling about 7 000 t per year.
Apart from new technologies making it possible to sustain higher recycling rates, paper is itself
a highly sustainable material, well on its way to meeting the industry-set recycling target of 70% by 2020.
As Samantha Choles, communications representative, Prasa, explains:
“In this country, paper is produced from farmed trees. Trees are planted and, once matured, after about 15-to-20-years, are harvested and new saplings are replanted in their place. This is what makes paper products renewable.”
She points out that 1.4 Mt of recyclable paper packaging was diverted from landfill in 2016.
“This could fill 1 680 Olympic-sized swimming pools. The 68.4% of recoverable paper that Bruce mentioned excludes books, archived
3 m3
of landfill space (and associated costs) is saved by recycling 1 t of paper
26 498 ℓ
of water can be save by recycling 1 t of paper
products, tissue and hygiene products and the likes of cigarette paper. Six years ago, the figure was 59%; in 2015, it was 66%. This is an exciting trajectory given that our target for the year 2020 is 70%.”
Rodney Reynders, sustainability director: Middle East and Africa, Tetra Pak, discusses how the international company he represents started out in Sweden in 1952 and has always been committed to consumer safety, extending to the protection of the environment.
“We first came to South Africa in 1957, just five years after the company started in Sweden. By 1979, we’d built a converting plant in KwaZulu-Natal. That facility employs 138 employees, supplying card and packaging products to customers in Southern Africa and at least 10 other African countries.
“As a responsible supplier of packaging, we’ve developed highly engineered solutions to take
1.4 Mt
of paper was recycled in South Africa in the last year
this product apart. We believe our empty cartons are a valuable source of material to recyclers – paper mills in particular. In fact, our cartons are being recycled at more than 150 recycling companies globally, most of which are paper mills,” he adds.
In this way, Tetra Pak supports the principles of a circular economy, through responsible sourcing and ensuring a way for its products to be recycled after use.
The keynote speaker at the event was the minister of the DEA, Dr Edna Molewa, who reminded attending guests that diverting paper waste from landfill also has positive carbon impacts.
“This plant will also be saving some 65 240 m2 of landfill space. What’s more is you’ll be cutting our carbon emissions by 11 400 t per annum. That’s huge. I think we can say with pride that, when we talk about South Africa’s commitment to reducing carbon
emissions, we are relying on good citizens like those gathered here today.”
The minister also acknowledged how municipalities and even metros struggle with waste management and recycling in general, adding that the Mpact plant is part of an initiative in conjunction with the DTI aimed to reduce the amount of waste going to South Africa’s landfills.
“While we are here today celebrating this important project, we are also implementing our National Development Plan (NDP). The NDP calls on government to commit to finding alternative and innovative ways to divert waste away from landfill sites and convert waste to valuable resources.
“Minister Davies and his department have, together with the DEA, put together a list of 40 bankable projects with this aim in mind. Here we are celebrating one of those put together in partnership with the DEA and DTI. We will now support it in every way to ensure it succeeds,” she concluded.
South African landfills are fast running out of airspace. Green waste from food waste, lawn clippings and other plant-based matter contributes massively to waste volumes. If this is diverted from landfills using on-site machinery, municipalities stand to save money while also creating more sustainable facilities.
“The TBU 3P allows users to heap their compost as high as 3.3 m, whereas smaller machines will usually only allow for heights up to 1.2 m.”
James Kamau, founder and principal , Mfangano Solutions
“The most effective way to reduce the amount of waste being sent to landfill is to take a ‘zero green waste goes to landfill’ stance. The biggest landfill-related problem we have in this is lack of airspace. Major sites at some of the biggest metros, including Johannesburg and eThekwini, have closed or are closing in the coming years,” says James Kamau, founder and principal of environmental management provider Mfangano Solutions.
Selecting the right site equipment to manage green waste not only saves on the cost of valuable land (which would need to be bought if a landfill filled up), but also has the potential to create jobs through both the green and circular economies.
Mfangano Solutions offers a range of green waste and other recycling equipment for the needs of industry, municipalities, building contractors and the domestic market. One of its most versatile ranges of machines, which is also ideally suited to South Africa, is TS Industrie’s mobile chipper-shredder Green Series. These multi-vegetation machines are the smallest wood chippers of their kind available locally and feature a unique cutting mechanism.
“The Green Series features a combination of blades and chippers. If the diameter of the wood is too large, the hammers move out of the way so the blades can do their work. Since the hammers are positioned for more input than the blades, the hammers work first, reducing blade wear. Additional blades mean the hammers also experience less wear,” explains Kamau.
Reducing green waste sixfold, the Green Series is specially designed to be able to handle moist leaves such as the dense palm leaves found
33% of the world’s food gets lost or wasted
US$990 billion is lost to the global economy through food waste
Food waste only makes up a small fraction of green waste compared to clippings and cleared brush
Increasing composting facilities is the most cost-effective way to improve available landfill airspace availability
frequently in the Western Cape and strelitzias most common in KwaZulu-Natal. “Nitrogen is an essential ingredient in compost and the Green Series is a really unique product in that it’s designed specifically for this purpose, adding value to green waste,” adds Kamau.
The Green Series is noise insulated, making it ideal for use by municipal and city authorities in urban environments. It also complies with all the latest health, safety and emissions standards. These products are ideally suited for creating mulching and cover material.
Mfangano’s Willibald Compost Turner TBU 3P aerates heaped rows of compost (windrows) so that windrows can be heaped higher, ultimately saving space and making composting facilities almost three times more productive.
“The TBU 3P allows users to heap their compost as high as 3.3 m, whereas smaller machines will usually only allow for heights up to 1.2 m. It’s important to aerate compost because this allows the bacteria inside it to work, kick-starting the composting process,” explains Kamau.
The machine is compact and easy to use, promising higher-quality compost yields.
Another new offering, made available to the local market through Mfangano is the Shark II EP5500 horizontal grinder, also from Willibald. This is a larger, mechanically fed machine. It can be mounted on the back of a truck for on-site chipping, lowering logistical costs.
“What makes this machine unique is its dual functionality – it boasts two grinding systems. The first is the traditional drum-and-screen configuration and the second involves side rakes, which allow the user to adjust the size of the wood chips produced using a remote control,” says Kamau.
An added advantage of the Shark II is that it features a MAN engine using AdBlue technology. It complies with the most stringent EU emissions standards, far in advance of what is required by local legislation.
“I believe that South Africa is on its way to becoming an environmental leader. That being the case, we focus on supplying machines with low emmissions so that our clients are confidently able to call themselves conscientious custodians of the environment,” he concludes.
Property investment giant Growthpoint recently launched an innovative pilot project that turns the large volumes of food waste generated by client businesses at its properties into compost.
The project, named G-Eco, short for Growthpoint Eco, is a partnership with Life & Earth and is currently being tested at Growthpoint Business Park in Midrand using waste produced at four of the company’s large multi-tenant properties in the area.
The initiative kicked off with the installation of a food waste composting machine at the company’s business park in Midrand. The plant turns food waste into 100% organic compost and can process up to 1 000 kg of food waste each day, with the capacity to make about 9 t of compost a month.
The company’s current waste contractors at Growthpoint Business Park, Woodlands Office Park, Woodmead Retail Park and Central Park received training that covered the process and how to separate wet waste at source. They also
worked with their clients at these properties, encouraging them to separate their food waste.
During the first four months of the trial, Growthpoint diverted 16 t of waste from landfill and produced 6 m3 of nutrient-rich soil, to be reapplied at the Midrand Business Park.
“The G-Eco waste-to-soil project is one component of Growthpoint’s bigger waste management strategy,” explains Werner van Antwerpen, head: Sustainability, Growthpoint.
It already reduces waste through recycling, and plans to ensure all its buildings have on-site recycling by the end of 2018.
Based on the success of the G-Eco pilot, the company plans to introduce more waste-to-soil plants in other areas of the country where it has clusters of property assets.
“We are excited to find out exactly how much waste-to-landfill we will be able to save with our different waste management programmes, but we are confident that it will be substantial,” says Van Antwerpen.
He also notes: “This innovative project contributes to Growthpoint’s environmentally responsible leadership and furthers our sustainable business journey.”
Every alternate year, the Institute of Waste Management of Southern Africa, in conjunction with Landfill & Waste Treatment Interest Group (LaWTIG), hosts a specialist Landfill conference. The Landfill 2017 ‘Back to Basics’ conference was remarkable not only for its excellent calibre of presentations but because it was held on an active landfill site and accredited nature conservancy. By
Frances Ringwood
From 18 to 20 October this year, landfilling experts gathered from around Southern Africa to attend the Landfill 2017 ‘Back to Basics’ conference.
Hosted by the IWMSA and LaWTIG’s KwaZulu-Natal branch, the event was highly anticipated due to the fact that it would be held on an active landfill site – something that has never been done in its 12 prior iterations.
Logan Moodley, Landfill 2017 chairperson and senior manager: Engineering at eThekwini Municipality’s Cleansing and Solid Waste Unit, kicked off the programme, saying, “Landfill 2017 is a first ever for the industry to host a conference pertaining to waste management on an active landfill; not only will you hear high-quality presentations from colleagues and
leaders in the industry but also maximise the opportunity to appreciate a one-stop waste management facility on best practices and innovative landfill engineering.”
In addition to guided walking and driving tours of the site, there were also two workshops. One was chaired by Nick Mannie, technical director: Waste, Aurecon, on ‘Back to Basics’ – the same topic as the conference theme.
The second was chaired by Karl Bester from the Department of Water and Sanitation (DWS) and waste specialist Geoff Purnell. Bester and Purnell’s workshop concentrated on capping, which is a way to isolate the waste body from the long-term effects of erosion and small burrowing animals, as well as managing water and gas safely post closure.
A conference goal was to address claims by so-called waste “experts” (salesmen) that landfills will no longer be necessary in the future. According to Moodley, the local market has seen “project developers” offering a one-stop treatment solution to most municipalities. These solutions claim to produce energy from waste, reduce environmental impacts such as greenhouse gases and guarantee “zero air pollution” and in some cases with no capital investment required. This, in fact, sounds too good to be true. New-age facilities like these do exist in other countries around the world but we need to ask whether it will be appropriate (or applicable) in the local environment.”
Another motivation for the conference was the need to see existing landfills as assets, and
“In South Africa, we are trying to drive waste management up the waste hierarchy by diverting waste from landfill but, in the end, all those activities have tailings and those by-products have to go to landfill.”
discuss how that concept might be packaged within a larger waste management plan.
Jan Palm, president of the IWMSA, also addressed attendees, thanking Moodley and LaWTIG KZN for organising the event and looking back at how far landfilling has come in the last two decades. “If you look back to 1996 when the Landfill Interest Group was formed, it marked two years after the first edition of the Minimum Requirements were published, and landfilling and waste management were synonyms back then. We had no waste hierarchy, and landfilling was the ‘sexy’ thing to do. “Today, landfilling has become undesirable, especially when compared with new waste management facilities and technologies. Landfilling is at the bottom of the waste management hierarchy, indicating that it is undesirable. If it is so undesirable, what are we going to do here for the next three days? I think the answer lies in the relationship between being undesirable and indispensable. In South Africa, we are trying to
drive waste management up the waste hierarchy by diverting waste from landfill, however, all those activities have tailings and by-products have to go to landfill. Additionally, in the event that a diversion activity fails, and there are many examples of this, or it needs to shut down for maintenance, the waste needs to be sent to landfill. In this way, landfills function as a safety net when all else fails.”
Since South Africa’s future landfills are set to function as a safety net, design engineers will need to ensure that these sites have minimal environmental impacts. “This is why the Norms and Standards have been set for base-liners and we have construction quality assurances on most sites. However, we are still a bit
thin when it comes to the operational side of landfills,” adds Palm. South Africa has spent millions on its landfilling facilities, but the unfortunate truth is that these state-of-the-art facilities are often staffed by under-capacitated people and operated like a hole in the ground; this is when things start to go wrong.
Raw truths, blatant lies
Kelvin Legge, chief engineer, DWS, then delivered his much-anticipated keynote address,‘Raw Truths and Blatant Lies’, sharing some of his vast
ABOVE LEFT Landfill 2017 was a fully booked event, demonstrating high industry interest
ABOVE AND LEFT Tour of Buffelsdraai Landfill’s operations, leachate management, landfill gas management, closed-loop engineering and bufferzone engineering practices
knowledge gained through being involved in more than 1 000 design reviews. “Since 2009, when the first draft regulations for Norms and Standards were floated, we’ve had just over 1 000 designs submitted and considered. We want to share with you some of our experiences over the last decade. These are some of the most valuable lessons for the benefit of the industry.”
These included: a consideration of some of the various criticisms levelled against government in its granting of landfill licences; the affordability of pollution control barrier systems; specific design aspects relating to the mechanisms, functioning and failure of waste management facilities; and the use of specification and construction quality assurance programmes.
Regarding the question of affordability, there’s a growing objection to the use of geomembranes for landfill lining coming from the private sector and members of the civil service.
“It has gone as far as the Presidency and is in discussion at that level, with inputs from various organs of state, but there’s also a big drive from the private sector to reduce costs and there’s a perception that geomembranes are the most expensive component of a waste containment facility,” added Legge. He then implored the assembled guests to think more broadly and strategically, showing a visual representation of the amount of drinkable water on earth compared to the planet’s size.
“If you took all the water in the world, and shaped it into a sphere, it would have a diameter of 1 380 km; if you remove the salt water, you’d have a sphere with a diameter of only 273 km. If you take into consideration only the freshwater that is available – in other words, relatively shallow groundwater and water in rivers and lakes – and put that into a sphere, it would have a diameter of only 56 km. That’s roughly the distance between Johannesburg and the middle of Pretoria. That’s all the water we have for the whole world. We also know that water availability is unevenly distributed over the surface of the globe: the majority of South Africa has less than 800 m3 per annum available per person. Looking at the cost of using that water, we have an estimated 40 000 to 60 000 dams in the country, of all sizes, many of which are not registered. We have 5 452 dams on our register, of which about 120 contain water that is polluted. Together, the registered dams contain 33.37 km3 of water storage. This needs to be compared with the 49 km3 of mean annual run-off when looking at the costs of supplying water to communities and industry. The cost of dams is enormous –typically, a large dam costs in the order of R3 billion. The conveyancing systems are then usually three to four times the cost of the reservoir itself. These are substantial costs.”
In the past, many of South Africa’s B+ and B- sites relied on diluting pollution and did not require geomembranes. However, given the
Landfilling (Class B site):
R430/t*
Composting:
Just under R600/t*
Recycling (after sale): R1 440/t*
*capex and opex
increasing need for water, due to population growth and growing uncertainty about water availability owing to climate change, there was a clear need to revise this pollution-dilution philosophy. As a result, in 1994, there was a substantial change in legislation.
“In particular, in 1998, pollution-dilution was outlawed through both the National Environmental Management Act Principles (No. 107 of 1998) and the National Water Act (No. 36 of 1998). However, it took many years for the NEMWA regulations to come into effect. The IWMSA was a key component in the public participation involved in creating this Regulation. Today, these laws are driven by the concentration and containment philosophy of waste. To sum up on the issue of affordability, I think it is important that we share with decision-makers that it’s not a matter of whether
Kelvin Legge, chief engineer, DWS
we can afford to implement today’s standards, but whether we can afford not to,” said Legge.
His further discussion was equally well reasoned, touching on expanding capacity for engineers granting landfill licences, the need for landfill operators to familiarise themselves with the minimum safety requirements, learning from the lessons of the past, and government’s policy for ensuring competitive practices in public procurement.
“Perhaps the most important recommendation I’d like to leave with you is the belief that applicants for landfill licences should give serious consideration to independent review of the design and construction processes. That should be a minor task, not necessarily regulated, but such a measure could reduce design costs substantially,” he concluded.
Site tours of the Buffelsdraai Landfill site also yielded unique insights into how a landfill might be managed in harmony with its natural surroundings for the benefit and education of the local community. Although the positive results yielded at Buffelsdraai may not be easy to replicate at every site, the principle of marrying waste management with nature conservation remains a useful concept.
“Buffelsdraai Landfill Site buffer zone is about 800 ha in extent. Historically, this site featured a mix of natural forests and grasslands. During the past 200 years, much of this was converted to sugar cane farms, and subsequent to the establishment of the landfill, the municipality leased some land back to local farmers to continue with this farming. In 2009, however, a decision was taken to replace the sugar cane with indigenous forest, as a means to offset carbon dioxide emmisions associated with the FIFA 2010 Soccer World Cup matches that were to be held in Durban. In addition, sugar cane farming does not mix easily with a landfill, as landfills produce highly flammable methane, and sugar cane farmers typically like
1
The official magazine of the
Trade and technical print magazines remain the most powerful method for getting your message across in the South African b2b market.
2
A 2016 report by Neilson found that for every one dollar spent on advertising in magazines, four times as much money came back to the advertiser, giving magazines “the highest ROI of all marketing media”.
3 A 2015 report from Neilson concluded that magazines yield the highest ROI of all media, using just 10% of ad expenditure.
4
The Entertainment and media outlook: 2016 - 2020, published by PwC South Africa, found that South Africa’s b2b market, including magazines, directories and online resources, made R9.5 billion in 2015 and is forecast to grow at a 4% CAGR to reach over R11.6 billion in 2020.
5
In a survey looking at consumers’ behaviour in the US, international research company Toluna found that 80% of respondents indicated a clear preference for reading print on paper.
6
Hubcast, a cloud print solutions company, published a recent research paper titled 10 reasons why print isn’t dead, why marketers need to print. The report explores the following reasons for a resurgence in print over the past year:
• Print is easier to read and navigate
• Print readers retain information better
• Digital reading fosters skimming
• Print is tactile
• Print is more credible
• Digital reading can have negative health implications
• Millennials love print
• Print is sustainable (more so than screen reading which requires electricity and fossil fuels)
• It is easier than ever to print globally
7
E-commerce giant Amazon, originally started as an internet-only retailer, has since begun building more and more physical bookstores and other retail outlets so that consumers can touch, feel and more fully experience their products.
• ReSource (quarterly) promotes integrated resources management, with a focus on waste management and cleaner production. It is the official magazine of the Institute of Waste Management of Southern Africa (IWMSA) and is endorsed by 12 industry associations.
• IMIESA (monthly) is the official magazine of the Institute of Municipal Engineering of Southern Africa (IMESA), focusing on infrastructure development, maintenance and service delivery.
• Water&Sanitation Africa (bi-monthly) is the official magazine of the Water Institute of Southern Africa (WISA), dealing with the preservation, treatment and provision of water.
• www.infrastructurene.ws is a leading news hub for infrastructure development and service delivery, linked to social media platforms.
We are market leaders in combining our print products with multimedia offerings to create content marketing campaigns across print and digital platforms.
Book a cross-platform package with print at its centre, and enjoy:
• greater credibility
• more reach and engagement
• extended brand awareness with your target market.
to burn their cane before the harvest. Methane coming off the site could significantly exacerbate the fires.
“With climate change becoming a more prominent issue and the Fédération Internationale de Football Association (FIFA) World Cup coming to Durban in 2010, there was an opportunity for us to offset some of the carbon emissions associated with hosting the event. The CO2 emissions associated with constructing our local stadium coupled with local transport for tourism were estimated to be more than 300 000 t (equivalent) of CO2. The municipality instituted a number of projects to offset that carbon footprint, of which Buffelsdraai was one,” explained Errol Douwes, manager: Restoration Ecology, eThekwini Municipality.
“Initial funding to the value of R2.5 million was secured through DANIDA, the Danish International Development Agency, which allowed us to kick-start the project. We appointed the Wildlands Conservation Trust (WCT) as a service provider to oversee planting of trees, through the use of their novel Indigenous Trees for Life initiative. We later got support from Treasury for a dedicated budget, and as a result, we now receive up to R7 million per year from the city’s budget for reforestation on this site. The amount allocated to tree planting here will decrease over the next 10 years as the focus in future shifts to management.
“On the back of this initiative, and together with the University of KwaZulu-Natal, we submitted an application to the Development Bank of Southern Africa (DBSA). The DBSA had received money from the National Department of Environmental Affairs for establishing the National Green Fund Grant, and we were successful in procuring more than R37 million from that fund over a five-year period for reforestation. That may sound like a lot, but a number of projects, over and above the tree planting, were established. These include community engagement, environmental education, and partnering with the university so students can do research on the site. The WCT’s approach to tree planting is to pay members of the community to grow seedlings through a credits system, with tree-growers including volunteers from local communities, called ‘treepreneurs’. Given the risk of transporting and paying out cash, such as cash heists targeting our truck drivers, the credits system was preferred. Treepreneurs can exchange their credits for foodstuffs at local stores. As a result, if you look at the broader deliverables of the project, it has not just been about forest restoration but also combatting poverty, creating employment, and providing education opportunities for local community members,” explained Douwes.
One of the key learnings emerging from the conference was that, although every site is different and no solution can be simply copied at various sites, there are elements of best practice that translate to all sites. Whether it’s simply the idea of introducing more trees to offset carbon costs, or introducing parts of a technologically advanced waste management facility, like a composting area, there are many ways for South Africa’s landfilling professionals to raise site standards. Most importantly, these interventions don’t have to cost the earth.
As coastal erosion becomes more prevalent due to rising sea levels and changes in global weather patterns, it has become increasingly important to have well-engineered, durable and easily manageable coastal protection structures in place,” says Gerard Dirks, technical manager, Fibertex SA. “Although using large sandbags as structural components of revetments is not new in environmental protection, Fibertex has made a substantial investment to design and manufacture a robust geosynthetic-sand-container (GSC) system, as an alternative to conventional revetment structures. These GSC bags are a lightweight, durable and workable geosynthetic substitute for traditional revetment systems utilising rock and even seawalls using concrete and reinforcing steel.
Fibertex’s GSC bags are used in the construction of efficient protection structures for erosion control, dune revetments and slope protection, as well as for emergency protection in floods.
“The function of a GSC bag is to allow for the free passage of water through the porous structure of the fabric and into the sand it carries, to absorb wave energy, while retaining the sand fill in the bag. This is unlike hard concrete structures, which predominantly protect by means of wave energy reflection, which could most likely have a negative long-term impact on adjacent structures,” adds Dirks.
GSC bags consist of a strong porous base fabric, which is mechanically needlepunched together with a coarse anti-abrasion and vandal-resistant (AVL) cover layer. This robust fabric combination offers a flexible structure that is able to retain a course fill medium – like sand – while allowing for the free passage of water.
Fibertex AVL geotextile sand containers, which are manufactured from UV-stabilised virgin polypropylene fibres, can withstand the effects of repeated wave attacks in harsh coastal environments and are the perfect soft solution to beach rehabilitation and coastal protection.
Geotextiles used in the manufacture of GSC bags are required to withstand the effects of different environmental conditions from the geotextiles used for conventional separation, filtration, drainage and protection.
The Fibertex team has given particular attention to critical factors in the development of this system, including abrasion, perforation, puncture and UV resistance, tensile strength and elongation, as well as permeability and drainage.
IBM’s South African research laboratory has been working on a project that uses a datadriven approach and machine learning – including artificial intelligence – to forecast future pollution trends, enabling preventative measures to be taken, which could save hundreds of thousands of lives.
By Frances Ringwood
Air pollution is the world’s single largest health risk, increasing the risk of respiratory and heart disease among almost all human life. Almost 7% of all deaths worldwide are caused by air pollution, mostly in low- and middle-income countries.
Major sources of air pollution include industrial production, motor vehicles, burning fossil fuels and urbanisation. The rate of urbanisation in Africa is the highest in the world and more than 700 000 deaths occurring annually on the continent are due to air pollution.
Tapiwa Chiwewe, research scientist at IBM’s South African laboratory, works with a team that collects data on meteorological conditions and air-pollutant levels to develop
a decision-making support system for airquality management.
“Our online portal uncovers trends and insights on air quality. Our multiscale computer model portfolio can forecast levels of air pollution between 12 hours and two weeks in advance,” he explains.
“The ultimate goal is to safeguard the health and well-being of people and the environment.”
Why air quality?
“My interest in air pollution started one day when I was driving into Johannesburg and there was a haze hanging over the city.
Something wasn’t right.
Almost 7%
of all deaths worldwide are caused by ambient and household air pollution, mostly in low- and middle-income countries
Major sources
I started investigating further, finding what sources of information I could on the status of air quality in the city and across the province. Then I started speaking with local authorities and various other partners, and began to discover more and more about how dire the situation really is and how we at IBM could intervene,” Chiwewe explains.
By using data from air-quality monitoring stations on the ground and combining it with meteorological data – such as rainfall, temperature, wind speed, wind direction and air pressure – the team uses artificial intelligence to create a dashboard that generates reports
of air pollution include industrial production, motor vehicles, burning fossil fuels and urbanisation
“This is useful for infrastructure planning – for example,
More than 700 000
deaths occur annually on the African continent due to air pollution
planning human settlements away from the most polluted areas. Even when it comes to mine reclamation, the technology can be useful for empowering communities. For example, when communities are located near mine dumps, they are highly at risk of adverse health effects caused by air pollution. If they have access to data determining when high pollution levels are likely to occur, they can take action; for example, an asthmatic might stay home from work or a family may choose to settle in a different area,” he adds.
“This type of decision-making tool can also be used for different types of policymaking, by, for instance, setting up different daily limits for pollutants produced by industrial factories. If the forecasting shows that air pollution will reach levels above the relevant safety limits, authorities can be sent in to tell plant owners to restrict their daily operations. An example of such a facility might be a coal-fired power station.”
By collecting data from 21 air-quality monitoring stations spread across Johannesburg, Tshwane and the Vaal Triangle, Chiwewe and his team have created a highly accurate air-pollution forecasting model.
Institutions supporting the initiative include the City of Johannesburg, the City of Tshwane, the CSIR and South Africa’s Department of Environmental Affairs.
“These fixed air-quality monitoring stations typically cost in excess of R1 million. So, if you consider just how large a city like Johannesburg is, installing a large number of these stations can be prohibitive in terms of cost.
Tapiwa Chiwewe, research scientist at IBM’s South African laboratory, leads the Next Generation Urban Ecosystems programme. The system harnesses historical and realtime data from environmental monitoring stations to assess air quality, as well as ground-level ozone to determine which pollution prevention methods are effective
“It’s useful to do in-situ sensing with this sort of monitoring station, because it provides accurate results but not that much spatial coverage,” Chiwewe explains.
“That’s when remote sensing and making use of satellite imagery are actually quite useful, as well as other remote sensing ways of measuring air pollution.”
Through crowd-sourcing, we may come to create a platform for situational awareness, which would inspire the co-creation of noble, innovative solutions aimed at managing air pollution.”
IBM research laboratories make use of artificial intelligence, machine learning and data-driven approaches to solve problems.
In the case of forecasting South Africa’s air pollution levels, the team used as much historical data on different levels of pollution as possible from the three selected areas.
This was then fed into a data-analytics pipeline and machine learning was applied.
“At this stage, we did not apply any knowledge of atmospheric chemistry, or some of the photochemical reactions involved in the formation of ground-level ozone. We decided to follow a strictly data-driven approach, making use of artificial intelligence, to see if we could actually predict the level of ground-level ozone – based on historical data as well as real-time data,” says Chiwewe. The team looked at parameters such as pollutant measures, including
carbon monoxide, ozone, particulate matter and sulfur dioxide, and complemented these with different meteorological measures, such as air pressure, relative humidity, and wind speed and direction. “We also added certain derived features to capture some of the cyclical variations, such as whether it’s a weekend or weekday, the hour of the day, and the season, among others,” he adds.
Comparing predictions with the actual data revealed a 77% correlation.
The next step was to incorporate knowledge of atmospheric chemistry to create a coupled climate chemistry model, capable of air-quality forecasting. Coupled climate chemistry models require an emissions inventory that sets up the initial conditions of the forecasting.
“Normally, there has to be a number of ground-based studies that are used to create
these inventories; the CSIR recently created an up-to-date emissions inventory for the City of Johannesburg. We wanted to do air-quality forecasting across the whole of South Africa. Doing ground-based studies was going to be an extremely time-consuming process. So, instead, we made use of satellite imagery and created an emissions inventory for different types of pollution across the whole country,” explains Chiwewe. The result was a pilot project on air-quality forecasting over a period of about 120 days, which focused on priority pollutants known to be most harmful to human health, this
included particulate matter of 10 µm or less (coarse inhalable particles) and 2.5 µm or less (fine particles), and other major pollutants that included sulfur dioxide, nitrogen dioxide, carbon monoxide and ground-level ozone.
“The pilot revealed a tight correlation between the forecasting data and the data we were getting on the ground – considerably reliable results,” he says.
Because of the high cost of air-quality monitoring stations, combined with the usefulness of the
information generated by the study, Chiwewe predicts cities will soon be installing internet connected air-pollution monitoring sensors on fixed infrastructure, like street and traffic lights, for measuring a limited set of air-quality parameters.
“Such sensors could also be installed on the properties of individual home owners wanting to contribute towards gathering this data,” he says.
“Ultimately, through crowd-sourcing, we may come to create a platform for situational awareness that would inspire the co-creation of noble, innovative solutions aimed at managing air pollution,” Chiwewe concludes.
The National Cleaner Production Centre of South Africa (NCPC-SA) held its third biennial Industrial Efficiency Conference in Cape Town, from 14 to 15 September, under the theme: ‘Transition to a low carbon economy’.
The event was aimed at equipping industry, including small, medium and large manufacturers, retailers and businesses, with an awareness of how to benefit from the implementation of resource-efficient and cleaner production (RECP) in their processes, in their journey to becoming cleaner, more sustainable businesses.
Covering themes of water efficiency, energy efficiency and sustainable energy, waste and industrial symbiosis, life-cycle management and the implementation of RECP, the event also sought to align businesses with the UN’s Sustainable Development Goals. It also supported cross-cutting issues such as green finance and productivity.
Feedback from delegates and partners was very positive. Guy Cunliffe of the Energy Research Centre at the University of Cape Town – one of over 350 attendees – described the event as “wonderful”. “We found the conference highly informative, and were very grateful for the opportunity to network with key people sharing our space in the field,” he stated.
Lawton Johnson, business unit manager at the SABS, said, “Thank you so much for a wellplanned and professionally executed conference. The presentations were relevant and up to date, and the specialist speakers were well prepared and experts in their fields. Well done.”
Kicking off with a word from Ndivhuho Raphulu, director, NCPC-SA, other presenters included Eustace Mashimbye, CEO, Proudly South African, with a presentation focused on buying local in support of a “more effective implementation of
LEFT Eustace Mashimbye (far left), CEO of Proudly South African, and Ndivhuho Raphulu (second from right), director of NCPCSA, were among the speakers kicking off the conference
BELOW Participants engaging on RECP implementation
All presentations delivered at the Industrial Efficiency Conference were recorded on video and are available on www.ncpc.co.za
a higher impact Industrial Policy Action Plan”, and Rabelani Tshikalanke of the Department of Environmental Affairs, who outlined the legislative environment in which companies need to operate.
After the morning plenary, the conference split off into five breakaway workshops (or sessions), each with its own theme. Themes covered waste, energy efficiency, water efficiency, industrial symbiosis and implementing RECP.
Among the speakers was Professor Linda Godfrey from the CSIR, who spoke about the importance of a circular economy.
Helen Davies from the Western Cape Government focused on the water crisis currently facing the province. She also shared case studies from companies who have benefited from the NCPC-SA becoming more water and energy efficient.
To be found in the foyer of the conference venue were different exhibitors displaying various technologies and engaging in interactive sessions with the delegates. Among the exhibitors were Proudly South African, the Department of Trade and Industry, the CSIR and the City of Ekurhuleni.
After her workshop in Breakaway 5, speaking about SMMEs’ participation in the green economy, Petro de Wet said, “We had a good audience; we had a good number, but we also had the right people. It was a targeted audience for the conference as a whole and it worked very well for us.”
De Wet, who is from the Global Clean Technology Innovation Programme of South Africa, said there was good participation during their workshop.
Lee-Hendor Ruiters, regional manager: Cape Town, NCPC-SA, said that planning a conference of this magnitude takes at least six months of hard work, planning and coordination.
The conference lasted one and a half days, ending at lunch on the 15th, with a significant amount of networking going on well after the close.
Many companies’ main expenses are raw materials, labour and energy. Labour costs are largely fixed and raw materials depend on the market. This is why energy-efficiency experts call energy management the “last frontier of cost management” – especially for plastic injection moulding.
By Frances Ringwood
Plastics injection moulding companies, whether small and new, or established market leaders, can save up to 30% of their electricity costs by taking a few simple steps, according to Dr Robin Kent, energy-efficiency expert at Tangram Technology.
Kent has authored the comprehensive ‘An Energy Saving Guide for Injection Moulders’, sponsored by oil and lubricant giant ExxonMobil in conjunction with leading global research consultancy Applied Market Information (AMI).
The launch of the guide was accompanied by an interactive webinar in which managers of plastics injection moulding companies from around the world were invited to actively participate in a panel discussion that included Kent; Chris Smith of AMI; and Mohammed Mourad, marketing advisor at ExxonMobil.
Feedstock prices and process costs keep going up, yet customers demand reduced costs. It may be possible for some large companies to reduce their cost per kilowatt (kW) of electricity but, as
Kent pointed out, “The cheapest kW is the one you don’t pay for.”
Using less electricity can save a lot of money for injection moulding plants as it is frequently among the three highest operating costs associated with these facilities – depending on whether they are sited in countries with high or low labour costs.
“Not only does managing energy improve the bottom line, it also enhances a company’s competitiveness and benefits the planet,” points out Smith.
“Another argument in favour of better energy management is that supplies are no longer guaranteed. For example, in Europe, a lot of energy comes from external supply,” points out Kent. African countries, even South Africa, experience similar periodic supply insecurities. This, again, supports the argument in favour of better energy management.
“However, unlike cars, which use more energy the faster they move, plastic injection moulding plants are more energy efficient at higher production speeds. This is because their baseload is amortised over a larger production output,” Kent explains.
Therefore, it is necessary to put systems in place so that the greatest amount of effort is spent on the areas with the highest return. For instance, replacing old incandescent lightbulbs with CFLs is a positive step but it will only reduce electricity costs by a fraction compared
with training staff to switch off unnecessary machinery, making regular investments in capital equipment, and paying attention to the operational optimisations of key machines.
To start, Kent recommends that plant managers map their energy usage by plotting their output production in kilograms versus their kWh used per month on a scatter graph. “This should enable you to work out where your fixed costs are – for example, lights and computers – and allow you to benchmark against other factories with similar energy-saving objectives,” he says.
Smith points out that, if clients aren’t asking for plastic injection moulders’ environmental performance information, they soon will be. Companies that measure and audit their energy-saving success, and the resultant lowering of carbon emissions, are the ones that are preparing to be tomorrow’s industry leaders.
“You might have already started this journey by getting your ISO 9001 or ISO 4001 certifications – which basically say that a policy needs to be in place for monitoring energy use. But you also need to audit, because people react as you audit and not as you plaudit.” He adds that there is now an ISO 50001 standard aimed especially at energy systems and emphasises that the road to energy efficiency is a journey and not a once-off event.
Figure 2 The performance characteristics line holds the key to understanding plant energy use
“A machine that’s about 20 years old may be ticking along, but it’s costing you money,” says Kent. “If you think about a refrigerator – the cost of electricity for running the machine will eventually exceed the cost of the purchase price.”
He adds that today’s modern electric and hybrid polymer processing machines are much more energy efficient than older hydraulic ones. Nonetheless, in either case, it’s important that these machines are optimised in terms of their barrel-heating, screw-back speed and other operations.
“Energy savings can also be achieved using drive technology, although the many options can cause confusion. We get variable-speed and variable-volume drives, and are now moving to electric-screw drives – which are the best,” he explains.
“In terms of peripherals, 50% of the energy used in barrel heating can be reduced simply by using insulation. This also makes machines faster and more stable. We need to learn to start thinking this way in terms of the downstream equipment too,” he adds.
Things to look out for include whether barrel heaters, re-blowers, conveyers and air compressors are on or off.
ExxonMobil’s Mourad points out that not all plastic injection moulders can afford to replace their
hydraulic polymer processors with electric ones right away. In certain cases, it might be more environmentally friendly to maintain an older machine for longer. In these cases, he recommends using a high-performance hydraulic oil for saving energy.
“Hydraulic oils are often overlooked. They represent 1% of a factory’s spend but can increase productivity and pump efficiency by up to 6%. Making this change can be as simple as purchasing the optimum product to reduce baseload, which will have an effect on the bottom line,” he explains.
Some of the challenges hydraulic oil faces are exposure to high pressure, shear stresses, compression and a high temperature differential range. These can cause oil to lose lubricity, damaging machinery.
“For this reason, we recommend using a high-performance oil with excellent shear stability and high viscosity index. It’s also worth performing a regular used-oil analysis, as prevention is better than cure,” he adds.
In two studies in Russia and Germany, ExxonMobil was able to lower plants’ electricity usage by 4.3% and 3.7%, respectively, by recommending its Mobil DTE 10 Excel high-performance lubricant.
“These examples highlight what our flagship hydraulic oils can do. We have a full range of multipurpose grease, gear and bearing oils,” he adds.
Ultimately, the fastest and easiest way to reduce energy consumption for any facility is to remember that it’s all about people. “Technical changes are not going to happen unless you’ve got people who are trained and enthusiastic about implementing energy-efficiency measures,” explains Kent.
“Simply training and empowering your staff can result in as much as 20% energy savings. People often don’t feel empowered to establish a new process, or even turn off a machine that shouldn’t be running. Appointing a leader to drive these changes can have an effect, but it’s important to keep training people on an ongoing basis (from the CEO to the maintenance staff) and celebrate successes as they are achieved,” he concludes.
Kent has audited energy management strategies at more than 500 companies.
When the powers that be forget to put people first, their loftier plans for the economic benefit of the country and its citizens fail. It is only when the human factor becomes a core focus that appropriate and beneficial policy and technological innovation can follow.
Plastics are a prominent material in modern manufacturing, given their light weight, malleability and relatively low costs. In the past 50 years, their use has increased exponentially across all markets.
But petroleum-based plastics can have significant economic and environmental drawbacks when they end up in ocean garbage patches, washed up on sea shores, or even as they accumulate in landfills.
The Ellen MacArthur Foundation has released a report, titled ‘The New Plastics Economy: Catalysing Action (2017)’, about how dialogue, harmonisation, innovation, analysis and outreach are needed in order for the plastics industry to have a prominent role in reshaping the manufacturing and use of goods throughout the world.
President Jacob Zuma has urged African heads of state to work closely together to ensure that the implementation of the Paris Agreement is a success.
“Climate change is a global challenge that requires no one to be left behind. The whole world affirmed this in Paris and Marrakech when the Paris Agreement entered into force on 4 November last year,” Zuma said.
He was speaking at the Meeting of the Committee of African Heads of State and Government on Climate Change at the UN Headquarters in New York in September this year.
He added that negotiations on the Paris rule book must remain on track and ensure that there is sufficient clarity on parties’ commitments under their nationally determined contributions to mitigation, adaptation and means of implementation.
“Developing countries should be provided with adequate support for their mitigation and adaptation actions, and progress should be made on a post-2020 finance goal that should be significantly more than the 2020 goal of US$100 billion per year in climate finance,” Zuma stated.
A 12-month pilot project in Ekurhuleni aims to bring waste pickers into the formalised waste management sector
Ekurhuleni’s Waste Recyclers Project is aimed at integrating informal recyclers through cooperatives into the mainstream waste economy, providing an income-earning opportunity for large numbers of poor people within our communities and pursuing alternatives for landfilling through encouraging recycling and reuse.
“The project will also help to save municipalities money by reducing the volume of waste that needs to be collected, transported and disposed of through promoting the recovery and reprocessing of recyclables,” the Gauteng Department of Economic Development, Environment, Agriculture and Rural Development said in a statement released in August this year.
The 12-month pilot project is being rolled out in the West Rand, Ekurhuleni, Johannesburg, Tshwane and Sedibeng.
As part of the project, the department is handing over 200 branded, motorised, three-wheeler vehicles to local waste cooperatives and SMMEs. A total of 200 drivers and 200 assistants will be employed to operate these vehicles.
Additionally, 2 000 receptacles are being provided to households for sorting at source and offering capacity building and skills transfer to these informal waste recyclers.
Four out of five African families depend on agriculture for their livelihoods, but only 4% use irrigation, while the rest rely on increasingly unreliable rainfall. According to World Economic Forum data published in 2015, switching to irrigated agriculture increases yields by up to 90% when compared to nearby rain-fed farms.
High diesel costs make irrigation an unaffordable expense for many smallholder farmers. With 620 million African people lacking a connection to the electricity grid, electric water pumps are also not a viable option.
In answer to the need for more reliable, resource-efficient irrigation in Africa, solar irrigation company SunCulture has released its new RainMaker system.
The internet-connected system is designed to help smallholder farmers in underserved communities improve agricultural productivity and profitability by providing a long-lasting, low-cost solution in low-rainfall areas. Its cutting-edge Climate Smart pump controller automatically optimises pump performance and battery charging based on cloud cover – extending pumping by up to six hours on cloudy days.
The International Congress for Battery Recycling’s ICBR 2017 – which took place in Lisbon, Portugal, from September 20 to 22 this year – saw more than 255 industry experts in attendance, 30 talks and presentations, workshops and a plant tour at Ambigroup Reciclagem in the Seixal Recycling Park.
In his keynote speech, Christophe Pillot, CEO of French market research institute Avicenne Energy, presented forecasts of market developments in the field of rechargeable batteries up to the year 2026. According to his estimation, for the first time, more lithium-ion batteries will be deployed in power applications in the automotive sector this year than in the IT and consumer fields.
Another keynote speaker was Professor Vera Susanne Rotter of the Technical University of Berlin, who provided an overview of the various materials that play a role in a circular economy.
One of the main focuses of this year’s ICBR was electric mobility and the treatment of end-oflife lithium-ion batteries, including closing the loop in e-mobility to recycling.
Venue: Emperors Palace
Date: 16 to 18 October 2018
Contact: Ann Oosthuizen at ann@iwmsa.co.za
The countdown to the next WasteCon has begun. Every alternate year, the Institute of Waste Management of Southern Africa (IWMSA) hosts the biggest waste management conference on the local industry calendar. With the last event in 2016 having been notable for the high quality of its technical papers and knowledgeable speakers from the local and international waste management industry, next year’s event promises the same high levels of input and engagement that have become a trademark of the event.
Venue: Emperors Palace
Date: 14 to 15 November 2017
Contact: Christine Dunbar on +27 (0)63 235 8031 or admin@saee.org.za
The Southern African Energy Efficiency Confederation is hosting the 12th Southern African Energy Efficiency Confederation Conference to serve the energy management, environmental, facilities building upgrade, energy engineering, cogeneration, power generation and efficiency improvement industries.
It is the one comprehensive forum where energy-efficiency professionals see exactly how economic and market forces, new technologies, regulatory developments, and industry trends merge to guide the critical decisions that shape industry’s energy and economic future.
Venue: Sandton Convention Centre
Date: 20 to 21 February 2018
Contact: Maria Dippenaar at maria@energyindaba.co.za
The Africa Energy Indaba conference seeks to provide an annual programme that shapes energy policy for the African continent. Key issues that impact the African energy sector will be discussed and debated at the event, based on discussions between leading global policy stakeholders, including African ministers. Delegates will have the opportunity to discuss, debate and seek solutions to enable adequate energy generation across the continent. Those attending and speaking at the event will include industry experts, project developers, financiers, energy users, government officials and manufacturers.
Venue: Sandton City Convention Centre
Date: 27 to 28 March 2018
Contact: Cecelia Braxton at cecilia.braxton@terrapinn.com
Power & Electricity World Africa is an annual conference aimed at Africa’s power and electricity industry. The conference brings together likeminded individuals who are committed to meeting the growing demand for energy on the African continent.
The conference serves as a platform where delegates can hear about the latest developments, innovations and investment opportunities that will help them succeed in the energy industry. It is collocated with Energy Efficiency World, Clean Technology World and a host of other associated events.