Waste Management
Halting the organic waste crisis
Legislation Driving diversion from landfill
Job creation
Recognising the real value of recycling
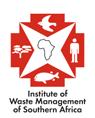
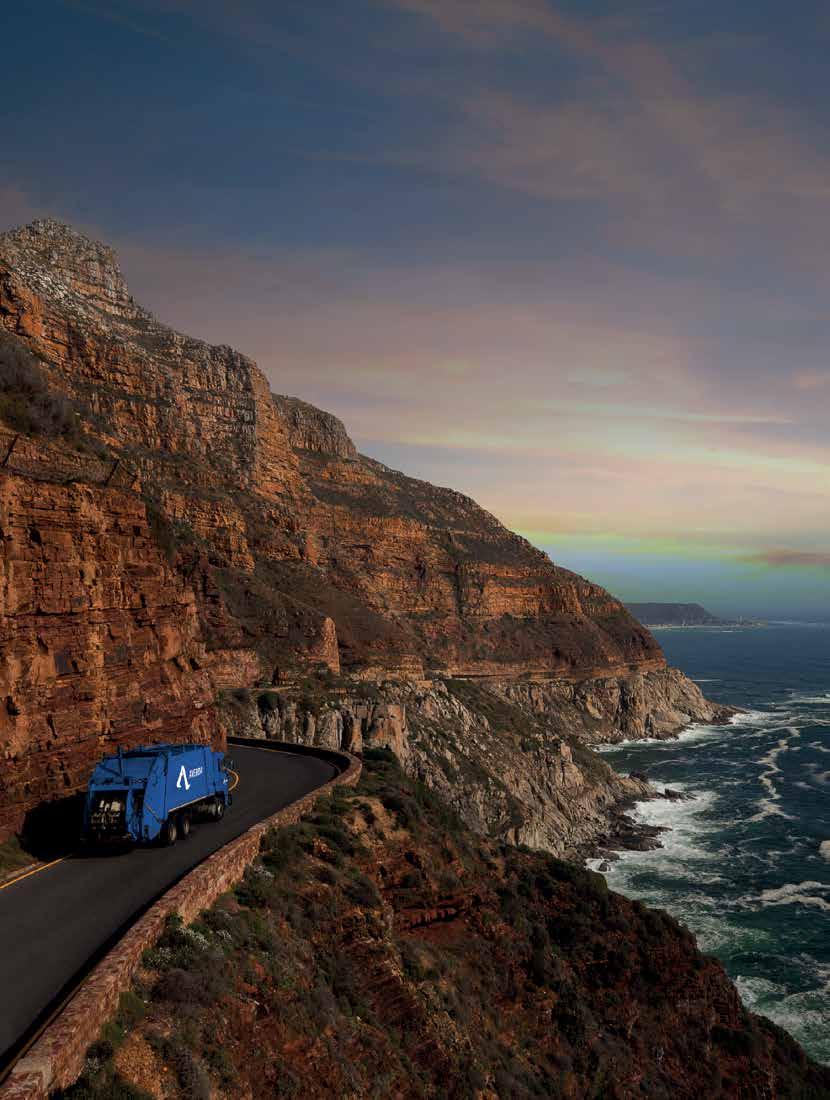
Waste Management
Halting the organic waste crisis
Legislation Driving diversion from landfill
Job creation
Recognising the real value of recycling
WasteCon 2018
Implementing the waste hierarchy
Heavy industry is a critical part of our economy. But disposing of the waste they produce in a way that’s safe for people and the environment takes years of expertise, scientific savvy and biochemistry knowledge.
Not just anyone can do it. That’s why EnviroServ employs qualified professionals for the job.
Like our Bookkeeper Lily, who is just as passionate about protecting the planet as you are. She’s an avid runner and has completed the Knysna Forest 21km and the Meiringspoort half marathon. Recent running achievements include the Strawberry trail run in George and participation in the relay train race 2018 from Port Elizabeth train station to Uitenhage train station. Lily also plans on running the Meiringspoort 21km again this year. Which means helping to protect the environment is in her best interest.
A loyal employee who has been with EnviroServ for 17 years, she takes pride in working for a compliant operation.
Because expertise is one thing, but employees who live the EnviroServ values of passion and integrity are dedicated to working towards delivering waste solutions that are environmentally responsible and effective.
1
Trade and technical print magazines remain the most powerful method for getting your message across in the South African b2b market.
2
A 2016 report by Neilson found that for every one dollar spent on advertising in magazines, four times as much money came back to the advertiser, giving magazines “the highest ROI of all marketing media”.
3 A 2015 report from Neilson concluded that magazines yield the highest ROI of all media, using just 10% of ad expenditure.
4
The Entertainment and media outlook: 2016 - 2020, published by PwC South Africa, found that South Africa’s b2b market, including magazines, directories and online resources, made R9.5 billion in 2015 and is forecast to grow at a 4% CAGR to reach over R11.6 billion in 2020.
5
In a survey looking at consumers’ behaviour in the US, international research company Toluna found that 80% of respondents indicated a clear preference for reading print on paper.
6
Hubcast, a cloud print solutions company, published a recent research paper titled 10 reasons why print isn’t dead, why marketers need to print. The report explores the following reasons for a resurgence in print over the past year:
• Print is easier to read and navigate
• Print readers retain information better
• Digital reading fosters skimming
• Print is tactile
• Print is more credible
• Digital reading can have negative health implications
• Millennials love print
• Print is sustainable (more so than screen reading which requires electricity and fossil fuels)
• It is easier than ever to print globally
7
E-commerce giant Amazon, originally started as an internet-only retailer, has since begun building more and more physical bookstores and other retail outlets so that consumers can touch, feel and more fully experience their products.
• ReSource (quarterly) promotes integrated resources management, with a focus on waste management and cleaner production. It is the official magazine of the Institute of Waste Management of Southern Africa (IWMSA) and is endorsed by 12 industry associations.
• IMIESA (monthly) is the official magazine of the Institute of Municipal Engineering of Southern Africa (IMESA), focusing on infrastructure development, maintenance and service delivery.
• Water&Sanitation Africa (bi-monthly) is the official magazine of the Water Institute of Southern Africa (WISA), dealing with the preservation, treatment and provision of water.
• www.infrastructurene.ws is a leading news hub for infrastructure development and service delivery, linked to social media platforms.
We are market leaders in combining our print products with multimedia offerings to create content marketing campaigns across print and digital platforms.
Book a cross-platform package with print at its centre, and enjoy:
• greater credibility
• more reach and engagement
• extended brand awareness with your target market.
WasteCon 2018 has come and gone. It never fails to exceed my expectations. The Conference, which was held at Emperors Palace in Kempton Park, was attended by approximately 471 delegates and exhibitors. It attracted 71 speakers from around the globe, who delivered high-quality papers and case studies.
The task of implementing the waste hierarchy is a mammoth one – and is a job not only for the waste industry but for every single South African citizen. We are still generating and disposing of millions of tonnes of municipal solid waste and hazardous waste at uncontrolled landfills across the globe. As a waste practitioner for the past 28 years, it is concerning that although we have some of the best legislation in the world, it is not enforced or properly regulated.
It is my opinion that the landfill and waste management standards in South Africa have deteriorated over the past 10 years.
One of our keynote speakers, Dr Ad Lansink, a Dutch politician and the father of Lansink’s Ladder (or, as we know it today, the waste hierarchy), launched his award-winning book Challenging Changes – Connecting Waste Hierarchy and Circular Economy at the conference.
It was encouraging to see how ordinary people, professionals and industry take on the challenge of implementing the waste hierarchy; however, the industry that manages the biggest
waste volumes in the country – our municipal sector – hardly participated in WasteCon 2018. What was very concerning was the lack of interest from the National Department of Environmental Affairs in finding workable solutions and taking hands with the Institute of Waste Management of Southern Africa. We should not be oblivious to the fact that South Africa is drowning in its own waste and ignore the fact that we have nowhere to go with our everincreasing waste volumes.
“As south Africans, we should be working around the clock trying to find workable, holistic solutions instead of fighting each other in court.”
is a total disconnection between regulatory authorities and the industry. As an institute, we are not only taking hands with our local partners but are also reaching out to international waste associations to assist us in making our regulatory authorities aware of the crisis in South Africa. We can no longer ignore our dire waste situation.
Still, it is encouraging to see the professional approach of the Western Cape governmental departments and neighbouring Namibia working towards implementing the waste hierarchy and taking the waste problem head-on. As South Africans, we should be working around the clock trying to find workable, holistic solutions instead of fighting each other in court. There
Patron members of the IWMSA
The IWMSA is dedicated, committed and ready for change! The time for taking hands in implementing Lansink’s Ladder and finding long-term, sustainable solutions is now. Thank you to our patron, members and all waste management practitioners for attending WasteCon 2018. We need you!
I would also like to make use of this opportunity to wish our patrons and members a merry festive season and a prosperous 2019. May 2019 really be the new dawn for the IWMSA we are all striving towards.
An
empty plastic bottle is worth money.
Recycling your empty plastic bottle has the potential to earn you money.
It’s made from a sophisticated material called PET, which, when recycled, is used in the production of many new and useful products – from textiles to automotive parts – and, most importantly, new bottles. Plastic bottles are not trash.
Please #Do1Thing and recycle.
Publisher Elizabeth Shorten
Editor Liesl Frankson
Managing editor Alastair Currie
Head of design Beren Bauermeister
Designer Ramon Chinian
Chief sub-editor Tristan Snijders
Sub-editor Morgan Carter
Contributors Kirsten Barnes, Leon Grobbelaar, Henry Nuwarinda, Bubele Nyiba, Natalie Skeepers, Kate Stubbs, Jürgen Tietz, Quinton Williams
Client services & production manager
Jayshree Maharaj
Production coordinator Jacqueline Modise
Financial director Andrew Lobban
Distribution manager Nomsa Masina
Distribution coordinator Asha Pursotham
Printers United Litho Johannesburg
Advertising sales Hanlie Fintelman
Tel +27(0)12 543 0480
Cell +27(0) 82 338 2266 h.fintelman@lantic.net
Publisher 150 Rivonia Road
Morningside 2196
PO Box 92026, Norwood 2117
Tel +27 (0)11 233 2600
Fax +27 (0)11 234 7274/5 www.3smedia.co.za
Annual subscription subs@3smedia.co.za
R200.00 (incl VAT) South Africa
ISSN 1680-4902
Institute of Waste Management of Southern Africa
Tel: +27 (0)11 675 3462
Email: gail@iwmsa.co.za
All material herein is copyright protected and may not be reproduced either in whole or in part without the prior written permission of the publisher. The views and opinions of authors expressed in the magazine do not necessarily reflect those of the publisher, editor or the Institute of Waste Management of Southern Africa.
© Copyright 2018. All rights reserved.
Despite a growing awareness around the importance of recycling, the Department of Environmental Affairs reports that less than 20% of waste is recycled annually. This means that most of the country’s recyclable materials continue to go to landfill.
Even with major cities implementing programmes to reduce the volume of waste going to landfill, two things remain clear: the participation rate of households, as far as recycling is concerned, is not nearly close to where it needs to be and the informal sector plays a vital role in diverting materials from landfill.
Household participation and attitudes are vital to the successful implementation of any programme aimed at diverting waste from landfill. Speaking at WasteCon 2018, Annabe Pretorius from the South African Plastics Recycling Organisation noted that there are currently too many steps in the recycling value chain and post-consumer recycling is expensive. All of these factors point to the growing need for separation at source.
This year, the City of Johannesburg introduced a mandatory separation at source programme (more on page 13) and while this is a step in the right direction, only time will tell if it will be successful in diverting waste from landfill – especially if we ignore why households were not participating in the programme before it became mandatory.
Taking the time to understand attitudes towards recycling and some of the factors preventing households from separating at source and recycling could go a long way towards entrenching this practice in our communities.
Earlier this year, I heard an audience member stand up at a CSIR event and note that while he knew that he needed to recycle, the truth was that he didn’t know how, or where to start. What’s sadder is that he was attending the event with someone from the waste industry.
While the waste industry is well aware of the fact that South Africa is fast running out of
landfill airspace and all the implications that come with this, more could be done to educate the man on the street on the true state of the South African waste industry.
Don’t hold back
Ordinary citizens need to know the status of our landfills, how legislation is changing the way we dispose of waste, and how diminishing landfill airspace affects the bottom line. More people need to know the good they are doing when they separate at source and recycle, not just for the environment but for job creation (we look at the real value of recycling on page 28).
As an industry driven by a passion to protect the environment and people, the onus is on us to educate those around us and shout a little louder. We need to work together to drive educational programmes and research around consumer behaviour and attitudes towards waste.
We need to learn from the water crisis and reach the masses with the right messaging and hard facts before it’s too late. We know just how important the waste management industry is, and it’s time everyone else does too!
editor
Liesl
Frankson
The landfill is located on a former brickmaking quarry and, according to Reg Gerber, national landfill manager, Averda South Africa, the site was specifically selected because of this history.
“During our environmental impact assessment, we looked at a range of things for the particular sites we were considering and this one came out tops in terms of the composition of the site itself. Because it was previously a brickmaking quarry for many years, the whole area is actually underlaid by significant layers of clay, which is what makes it ideal for a landfill site.”
In addition to the prime positioning, the landfill sits on top of a complex combination of layered materials aimed at ensuring that no waste seeps into the soil and contaminates the environment. This is something that Gerber is particularly proud of.
“Probably the most important part of this landfill site is the design of liners but because you can’t see it, its importance is hard to fully appreciate. The landfill is underlaid by a combination of materials that are 1.2 m deep. The materials include geotextiles, compacted clay, high-density polyethylene and gravel,” Gerber explains.
Neville Chetty, technical manager, Averda, adds: The liner system makes provision for the collection and drainage of leachate off the primary 2 mm liner and for leakage detection
As the first high-hazardous landfill to be constructed in Vereeniging, Gauteng, in 24 years, Averda’s Vlakfontein class A landfill has been built to the latest local and international standards. From planning through to operation, the Averda team is proving that the age of the environmental afterthought is long gone.
and collection between the primary 2 mm liner and secondary 1.5 mm geomembrane liners. Through the set-up of these layers and the choice of materials, we have made every effort to ensure that the waste and the leachate produced in our landfill will not come into contact with the environment.”
The leachate from the landfill’s Cell 1 site, which was commissioned in 2016, is fed into two tanks. Once the tanks are full, the leachate is pumped up to the leachate dam.
To manage the odours that come off the leachate dam, Averda has employed extensive air-quality monitoring protocols, which include high-tech gas probes and sentinels, as well as ongoing dust monitoring.
“In the event of a complaint, we have real-time data available to ascertain the nature of the complaint so that operational adjustments can be immediately undertaken,” Chetty says.
Being a Class A landfill site, Averda employs strict control measures for those looking to dispose of hazardous waste at Vlakfontein.
“We have a delay period for hazardous waste streams, and waste generators or waste management companies would need to give us anything from 24 to 72 hours’ notification or forewarning if they wanted to drop waste off at Vlakfontein,” Gerber explains. This forewarning allows landfill staff to plan for the load by sending
The Vlakfontein Landfill has a footprint size of 270 000 m² and a gross airspace of 6 500 000 m³
The landfill currently accepts more than 25 000 t of waste per month, with room for further growth
The landfill was constructed at a cost of R250 million.
According to Averda, the landfill has a lifespan of approximately 30 years
Once completed, Vlakfontein will feature six cells as well as a leachate and effluent treatment plant
“Our on-site laboratory is capable of handling most waste acceptance confirmatory procedures, but we do use accredited external laboratories for the waste classification analysis, as the independence of the results is an important aspect.”
“In the event of a complaint, we have real-time data available to ascertain the nature of the complaint so that operational adjustments can be immediately undertaken.”
a representative out to meet with the waste management company or generator to complete the appropriate paperwork. This includes documents such as a toxicity sheet, and the main aim of the exercise is to determine what is in the waste, how it was generated, and what constituents one would expect to see in it.
“We will also take a sample and send it for analysis. Once the results come back, we know what we’ve got to do with it because we’ve got to treat it in a certain way. Different types of hazardous waste require different treatments for them to be disposed of correctly, which is why we insist on notification ahead of time.
“Our on-site laboratory is capable of handling most waste acceptance confirmatory procedures, but we do use accredited external laboratories for the waste classification analysis, as the independence of the results is an important aspect,” he explains. Once the waste arrives on-site, it goes through further sampling and testing to determine if it is
indeed what the waste company says it is. If the on-site laboratory picks up on any discrepancies, the waste carrier will be turned away.
Chetty is particularly proud of the relationships Averda has built with the neighbouring community.
“We have been engaging the local community from the very beginning of the Vlakfontein site journey. Today, we have a constructive and positive working relationship, whereby issues or concerns raised by the community are addressed immediately.”
The company recently invited the community onto the landfill to see how it operates, as well as showcase the range of technologies and controls Averda has in place to ensure that both the community and the environment are protected.
Looking ahead, Gerber notes that this waste leader will continue to build on what they have created. “From the planning phase, the intention
was to create a one-stop waste park, which envisages separation of waste, recycling, wasteto-energy and treatment, with only a fraction of waste being disposed of,” Gerber explains.
In the next five years, Averda plans to construct two additional waste cells, as well as a liquid hazardous waste plant that will treat most liquid hazardous waste streams, including leachate and effluent.
Mozambique residents cause the least impact on the world’s climate. This is according to recent research from energy comparison expert MoneySuperMarket.
Its latest study shows that Mozambique residents use almost 100% green and sustainable energy, creating almost no waste, and producing almost no carbon dioxide.
The study notes that while they did exceptionally well in this regard, the country’s
failure to treat local wastewater would likely have adverse effects on the local environment and the health of residents.
Other African countries leading the charge in tackling climate issues include Ethiopia, Kenya and Zambia. According to the study, Ethiopia’s energy consumption is markedly lower than Mozambique’s – 1.75 Btu/capita/year, compared with 8.9 for Mozambique; however, Ethiopians’ waste production and exposure to pollutant PM 2.5 particles are both higher.
Unlike Mozambique and Ethiopia, Zambia treats a portion of its wastewater – 4.2% of it. However, pollutant particles and energy consumption are significantly higher, making this only the third greenest population.
Finally, Kenya ranks among the greenest countries in the world but when compared to the rest of the top five African countries, green energy usage is comparatively low and pollutant particles are high, as are CO2 and waste production.
Mozambique’s residents have the smallest per capita impact on the world’s climate
from green mango peel could be the key to remediating oil sludge in contaminated soil according to new research from the University of South Australia.
Dr Biruck Desalegn, lead researcher at UniSA, says that, without treatment, oil-contaminated
The waste part of the mango – the peel – is being used as an affordable, sustainable and environmentally friendly treatment solution for oil sludge
soil presents a massive risk to ecosystems and the environment. The new nanoparticles, synthesised from green mango peel extract and iron chloride, work by breaking down toxins in oil sludge through chemical oxidation, leaving behind only the decontaminated materials and dissolved iron.
“Last year, global oil production reached a new record of 92.6 million barrels per day, but despite improvements in control technologies, oil refineries unavoidably continue to generate large volumes of oil sludge,” Desalegn says.
Desalegn says this discovery presents a sustainable, green solution to address the significant pollution generated by the world’s oil production.
“Our research uses the waste part of the mango -- the peel -- to present an affordable, sustainable and environmentally friendly treatment solution for oil sludge.
“And while the world continues to be economically and politically reliant on oil industries as a source of energy working to remediate the impact of oil pollution will remain a serious and persistent issue.”
Rubber crumb produced from recycled truck tyres has become a highly successful addition to equestrian arenas, adding yet another innovative application to this locally manufactured material.
Locally, rubber crumb, which is produced from used truck tyres delivered to Mathe Group’s Hammarsdale plant, has been used to manufacture rubber flooring and paving and acoustic underlays for carpets, as well as for foundations for sports fields utilising artificial grass.
It wasn’t until the group received a phone call from Stephanie Ashley-Cooper, who manages Simbithi Stables, that company head Dr Mehran Zarrebini began researching the possible application of rubber crumb in equestrian arenas.
Ashley-Cooper contacted Mathe Group looking for a softer surface for the arena used by 16 horses stabled on the Simbithi Eco Estate near Ballito, KwaZulu-Natal.
The arena measures 30 m by 60 m, and the surface comprises one quarter rubber crumb to three quarters sand.
Ashley-Cooper says that the rubber crumb, which was mixed with the sand in the
Rubber crumb produced from recycled truck tyres has become a highly successful addition to equestrian arenas
A mixture of Mathe Group rubber crumb and sand has been used in the equestrian arena at Simbithi Stables. The mixture has proved to be a very effective working surface
arena, has performed better and better over time, as it has been repeatedly recombined with the existing substrate and is levelled and raked each day.
“The surface gets better and better as we use it. The horses working there seem to float over the surface as opposed to sinking into the sand,” she explains, adding that it has created a lighter surface that has a certain “bounciness”.
Zarrebini says that finding more and more applications for recycled rubber tyres is not only a commercial but also an ecological success story. Up until a few years ago, tonnes of used tyres were building up into a potential environmental disaster in South Africa, as there seemed to be very few uses for the products that would result from recycling them.
That has now changed, and Mathe Group expects to reduce approximately 200 000 used truck tyres into rubber crumb and other useful products by the end of 2018.
MetPac-SA recently hosted its first AGM and – according to Kishan Singh, CEO of Product Recovery Organisation (PRO) – its ultimate aim was to promote the responsible consumption of the planet’s finite resources, specifically in the manufacture of metal packaging.
“We need a new way of doing business, and government’s Section 28 call for an Industry Waste Management Plan, whereby all manufacturers and producers of packaging materials will be held accountable for the products they produce, is forcing all of us to embrace the concept of a circular economy as a way out,” said Singh.
MetPac-SA was formed approximately 18 months ago, with the aim of establishing the metals packaging industry as a valuable and recognised contributor to sustainability throughout the supply chain and beyond.
Today, the association has also become a repository of information and knowledge pertaining to the metal industry in South Africa. It represents the interests of the entire metal packaging value chain in South Africa, including steel, tin plate and aluminium packaging producers and the recyclers of these materials. “We are breaking new ground and entering uncharted territories,
Some of the MetPac-SA members who attended the association’s first AGM in Johannesburg recently (L–R): Alex Baisch, Charles Muller, Muhammed Darsot, Kishan Singh, Klaus Hass, Casper Durandt, Louis Wenzel and Philemon Sereme
and cannot succeed without the industry’s support,” Singh added.
“Time will soon tell what the future will hold and how funds will be administered, but we know it will demand a greater degree of collaboration between brand owners, retailers, municipalities and other stakeholders to ensure that the packaging industry as a whole creates better products, more jobs, sees greater transformation, and operates in a way that is overall more environmentally responsible,” he concluded.
The Tshwane Community Ecological Warriors Network programme is starting to bear fruit as groups within the network have already set up series of environmental activities in townships around the city. The network, which was started in December 2017, is
and
comprised of volunteering youth groups who engage in environmental projects that they have established in their respective townships. According to the City of Tshwane, the projects are meant to address various environmental issues within their respective areas.
“Since the inception of the network, the department has invested in it through sharing knowledge, celebrating days of environmental importance, undertaking environmental excursions, and having an open-door policy with the warriors for any support and assistance.
“Thus far, the programme has positively impacted the youth projects. Through various environmental awareness sessions conducted with eco-warriors; they are now more equipped with environmental literacy and are empowered to take informed environmental decisions,” notes Ntebo Mabokela, environmentalist at the City of Tshwane.
Under the theme ‘Implementing the Waste Hierarchy’, the IWMSA gathered 76 high-level speakers and hundreds of delegates at Emperors Place in Ekurhuleni, Gauteng.
The first day of the conference saw a wide variety of presentations from industry stakeholders, with a strong focus on recycling behaviour, beneficiation and the cost of implementing the waste hierarchy.
The presentations from the plenary session set the tone for the conference, with keynote speaker
Conference presentations were loaded on to a complimentary memory stick for each delegate, and sponsors and exhibitors were recognised in the conference’s unique mobile app instead of on printed paper
When it comes to waste management, South Africa faces a unique set of challenges. In an effort to address these challenges and move the country towards zero waste to landfill, the IWMSA recently hosted its 24th biennial WasteCon flagship conference and exhibition. By Liesl Frankson
Dr Ad Lansink – the Dutch founder of the Ladder of Lansink (now known as the waste hierarchy)
– discussing a variety of pertinent issues related to the waste hierarchy and the circular economy. Lansink noted that a fundamental requirement in the roadmap to a circular economy was to be averse to risk, given that we face so many environmental risks globally. He identified population growth, raw material scarcity, and political and economic stability as some of the key risks that have an impact on the environment and the global drive towards sustainability.
Lansink also identified some of the key challenges to implementing the waste hierarchy and transitioning to a circular economy, some of which include:
• closing loops in several sectors and on various levels of the waste management industry
• developing new technologies
• creating shared financial and behavioural values and principles
• establishing shared responsibility between producers, consumers and government
• creating extended (specifically global) support
• decoupling the economy from the environment
• a firm transition towards renewable energy.
Turning to recycling, Annabe Pretorius from the South African Plastics Recycling Organisation discussed the importance of changing behaviours and attitudes towards recycling in order to tackle the plastic pollution problem.
“We can’t ignore the fact that plastics are central to everyday life – many of us drove here
100% recycled paper was used for the conference programme
in cars made of plastic. Plastic is not the villain; however, it is blamed for the visible litter problem. And while calls from consumers to ban singleuse plastics and straws are valiant, that will unfortunately not change behaviour, which is where the real problem lies.” Pretorius urged the plastic and waste management industry to work together to deal with the challenge of plastic pollution because plastic recycling in South Africa was not practised enough.
“The plastic industry has committed to dealing with plastic pollution by signing the Global Declaration, leading recycling campaigns and undertaking cleanups to remove plastics from the environment and recycle them. The reality is that this is not enough. We need to address the visible litter and create a visible culture of recycling because, at the moment, all we see is the litter and the recycling happens around the corner – somewhere out of sight,” she explained. Pretorius noted that while recycling was the solution, demand was an important driver of the industry in South Africa and that we need such markets. She also added that for recycling to be even more effective, separation at source was absolutely necessary.
While unpacking her study on ‘The social dilemma of household recycling’, Wilma Strydom from the CSIR noted that the potential for social pressure to positively influence recycling behaviour in South
Africa was limited. “We found that people are driven to recycle by internal factors rather than the subjective norm or what others think.”
She added that for the subjective norm or social pressure to be more effective in driving recycling behaviour, government, private recycling companies and the media would have to make a concerted effort to collaborate and encourage households to recycle more, as well as provide the necessary infrastructure and services to enable this to happen.
Professor Linda Godfrey – manager of the Waste Research, Development and Innovation Roadmap’s Implementation Unit at the Department of Science and Technology – asked the critical question:
“How do we fast-track the change to a circular economy?” Godfrey was part of the research and development of the Africa Waste Management Outlook conducted under the auspices of the United Nations Environment Programme, the International Environmental Technology Centre, and the CSIR. “Some of our findings point to challenges such as the existence of inadequate measures to manage new and changing waste
e ach delegate was supplied with their own glass water bottle that they could refill at designated water stations around the venue
Relevant, sustainable waste management solutions will be key to realising the vision of an African circular economy
streams,” she explained. “In response to these challenges, we often see a knee-jerk reaction to ban products, rather than implementing measures to address the challenges. As an example, we see polyethylene terephthalate (PET) bottles and containers being banned, which, in the context of freshwater security across the African continent, can have detrimental impacts on communities,” she continued.
Godfrey further suggested that the sad reality is that “many African dumpsites are filled with reusable materials and no plan for diversion because of a lack of the will to do so.”
She reiterated that by no means is the African picture all doom and gloom, as she highlighted many wonderful examples from Africa and Southern Africa that showcase the inherent entrepreneurial and innovative spirit of our continent’s people.
“Ultimately, waste management solutions that are relevant and sustainable within the African context will be key to realising the vision of a circular economy on our continent,” she added.
The final day of the conference comprised three technical tours, which gave delegates the opportunity to experience waste management
Dr Ad Lansink, the Dutch founder of the Ladder of Lansink, discussed a variety of pertinent issues related to the waste hierarchy and circular economy (Photo: Etienne Smit)
practices in action. The tours took delegates to the Tufflex Plastic Products, Geocycle and Mpact operational sites. Commenting on the conference, Leon Grobbelaar, president of the IWMSA, noted that the presentations and workshops sparked numerous discussions on how we can find solutions for the waste management problems we collectively face, by focusing on waste avoidance and reduction, reuse, recycling, recovery and, ideally as the last port of call, the treatment and disposal of waste.
“We hope that the content and benchmarks shared at WasteCon 2018 will be carried forward by delegates to ensure that we win the war against waste, one day at a time, and secure a sustainable environment for generations to come,” he concluded.
A total of 64% of the food waste generated during the conference was preprocessed and thereafter removed for composting
With only six years of municipal landfill airspace left, Johannesburg is staring down the barrel of a wheelie bin. While the city implements programmes to reduce reuse and recycle, industry experts ask: Are we doing enough to curb the amount of organic waste going to landfill?
By Liesl Frankson
Gavin Heron, co-founder of Earth Probiotic, believes that more needs to be done. “In terms of the current status of household food waste disposal in South Africa, nothing is happening on a formal basis. There are those proactive individuals who see the benefit of composting their food waste, but the sad reality is that most organic waste ends up in landfills,” he notes. According to an
audit by the CSIR, 40% of all waste going to landfills nationally is organic.
Heron points out that promoting the diversion of food waste from landfill is important for a number of reasons, chief among them the fact that we are fast running out of landfill space.
“As landfill airspace dwindles and becomes a scarce commodity, we can expect the cost of waste disposal to increase significantly. Constructing new landfills is expensive and these will no doubt be built further away
from our expanding cities, which will further drive up the cost of waste disposal,” he says.
Not only is diverting organic waste away from landfill important to help delay Landfill Zero, it is essential to prevent adverse environmental effects.
“When organic waste is landfilled, it rots and produces methane. This methane is 22 times more damaging to the environment as a greenhouse gas than carbon dioxide. This makes
it difficult to meet our climate change obligations. It also attracts pathogens, and produces leachate that will eventually pollute our increasingly scarce water sources,” Heron adds.
To address these concerns, Heron believes a critical change is needed in the messaging around food waste and its diversion from landfill. “At the moment, food waste minimisation tends to focus on environmental or green issues. First, we need to focus on the costs of that waste, the hygiene issues, and the risks associated with food waste. Food waste is expensive to discard for any business.
“Research by Dr Suzan Oelofse at the CSIR has directly measured the cost of food waste to our economy at over R10 billion per annum.”
To cut the cost of food waste disposal in commercial kitchens,
The Earth Cycler easily handles up to 5 000 kg of organic waste per month
Heron suggests on-site composting. On-site composting solutions are an easy, malodour-free way of managing food waste with the benefit of producing a valuable useful output.
“Key to this is in-kitchen separation, which not only increases dry recycling volumes by upwards of 30% but also enables waste volume measurement and reduces contamination,” Heron explains. “We measured that food waste composting activities reduced food costs by 4.2% and kitchen consumables by 11.8%. So, looking at the messaging and motivation for composting and diversion of food waste from landfill, it makes business sense first and environmental sense
after that.” For commercial kitchens, composting food waste on-site can reduce their total waste bill, and give these kitchens financial predictability going forward, which is essential for budgeting purposes. In addition to this, legislation is on the way that will ban food waste from the general waste stream.
“Cape Town and Johannesburg are already focused on reducing organic waste to landfill by 50% by 2022, leaving commercial and household kitchens with only three years to solidify a plan to deal with their food waste. Composting organic waste is a strategy that will not only protect the environment, but ensure that you, or your company, are ahead of the coming tsunami of regulations that will turn your food waste to
At the moment, food waste minimisation tends to focus on environmental or green issues. First, we need to focus on the costs of that waste, the hygiene issues, and the risks associated with food waste
• Waste Collection Optimisation
• Waste Transfer Station design
• General Waste Landfill design
• Hazardous Waste Landfill design
• Landfill Rehabilitation
• Landfill Auditing and Monitoring
The mass of food thrown out by Johannesburg residents, per capita, per annum 8 –12 kg
As landfill airspace dwindles and becomes a scarce commodity, we can expect the cost of waste disposal to increase significantly
• Landfill Closure
• Leachate Treatment
• Regional Waste Studies
• PPP Involvement in Waste Management
• Alternative Technologies for Waste Reduction
• Integrated Waste Management Plans
Contact Numbers
Telephone:+27 (0)21 982 6570
Fax:+27 (0)21 981 0868
The Earth Cycler food composting machine is already proving popular. It is currently installed in Zambia, Mozambique, Botswana and South Africa. In Botswana, the Earth Cycler will manage food waste at a luxury safari lodge. As the unit is enclosed and does not emit odours, it will not attract animal scavengers. In Johannesburg, the Earth Cycler has been placed at the Standard Bank Office Park in Roodepoort. Here, it will process food waste from the canteen as well as paper hand towels from the lavatories – paper waste that is normally sent to landfill.
landfill practice into an almighty problem,” Heron insists.
A local solution
In a bid to help South Africa deal with its impending organic waste crisis, Heron’s company has developed a food waste composting machine, known as the Earth Cycler. According to Heron, the machine can process
up to 5 000 kg of waste per month, making it ideal for hotels, universities and office parks.
“Managing food waste with the Earth Cycler is simple. It has been specifically designed for ease of use and robustness. Operators are guided through a loading procedure that measures the amount of food waste added and then indicates the minimum carbon requirement for effective composting. Other than the loading procedure, all other processes are fully automated,” Heron explains.
The machine is also extremely energy efficient and can be solar powered. Energy efficiency is obtained by relying on natural aeration and bacterial action versus blowing heat and air through the machine. The system includes remote management and live data capability, with data dashboards that can display food waste volumes processed, CO2e saved, landfill airspace saved, and potential carbon tax exposure. “All of these elements are essential in
reporting the environmental return on investment of on-site food waste composting. An additional benefit is that the Cycler will also process waste paper and cardboard – a commodity that’s expensive to store and move to recycling facilities,” Heron adds.
“As city moves to implement programmes to reduce the volume
of waste going to municipal landfills, Johannesburg residents need to realise that the landfill airspace crisis is their problem and not something they should just push on to the municipality. If we can learn anything from Beirut’s crisis, when landfills close, waste builds up and residents riot – so we all need to play our part,” Heron concludes.
it’s no secret that south africa is running out of landfill airspace.
In a bid to delay landfill ‘day zero’, the City of Johannesburg has implemented a mandatory separation at source programme to reduce the volume of waste going to municipal landfills.
the city rolled out a separation at source programme on a voluntary basis. encourages residents to separate their waste at home using a threereceptacle model.
In an effort to increase participation and the extraction rate of recyclables, Pikitup’s separation at source programme became mandatory as of 1 July 2018.
in Fy 2014/15,
20 808 t of dry waste (paper, plastic, glass, cans) was successfully diverted away from landfill sites because of the programme.
The programme covers about 490 000 households.
Less than 20% of waste is recycled annually, meaning most of the country’s recyclable materials continue to go to landfill.
Through the programme, the city hopes to extract an average of 13 kg of dry recyclables per household per month by 2021.
More than 19.2 Mt of general waste and 1 Mt of hazardous waste went to South Africa’s 133 landfill sites in 2017.
Legislation (NEMA, 2008 and the National Waste Management Strategy, 2011) requires generators and collectors of waste to manage it in a manner that prioritises the preservation of natural resources and the environment by applying the principles of the waste hierarchy in their order of preference.
talbot & talbot has invested nearly r10 million over the last 18 months into developing its new state-of-the-art organics Laboratory. the Laboratory is set to open up new services and capabilities in the waste, contaminated land and water sectors. micole martens, operations manager: Laboratories, talbot & talbot, discusses the company’s new venture.
Could you give us an overview of how the organics laboratory came about?
MM Historically, Talbot Laboratories has had a reputation for providing quality inorganic and microbiological analyses in-house. All organics analyses were subcontracted to reputable peer laboratories. Over the years, the demand for highervalue organics analyses grew exponentially so the transition into the realm of organics analysis was inevitable. The initial idea of developing in-house organics capabilities started in 2010 but the realisation of the organics facility only came in 2017.
Prior to the launch, Talbot & Talbot mentioned that the facility would open new services and capabilities in the waste, contaminated land and water sectors. Could you elaborate on this?
The new organics facility extends the scope of Talbot Laboratories’ organics testing to include testing
for the legislative requirements for disposal of waste to landfill and contaminated land (NEMWA, No. 59 of 2008). The new capabilities include a unique service offering of advising clients and providing them with a waste assessment report, together with a safety data sheet and classification.
Why is a facility like this important to the South African waste sector and the country as a whole?
It allows testing that was previously outsourced to be done in-house at significantly reduced turnaround times and lower costs. Talbot Laboratories prides itself on quality and the ability to analyse samples regardless of the sample matrix. Laboratories with the capability of analysing waste streams in accordance with local norms and standards benefits the waste sector and country by supporting the timeous and legal disposal of hazardous wastes. Talbot & Talbot also offers treatment solutions for waste streams to help minimise or exclude disposal to landfill.
Which industries will benefit from the new organics laboratory, and how?
This facility will be beneficial to almost every sector requiring organics analyses – in particular the environmental, food and beverage, and agricultural sectors. Gas chromatography-mass spectrometry provides capabilities for testing pollution incident samples against a National Institute of Standards and Technology library of millions of organic compounds.
What is the one piece of advice or information about biomass or organic waste that you wish more people in the industry knew?
Biomass has a wide array of uses, including directly to generate heat or electricity with a steam turbine. Biomass can also be used to make methane gas, biodiesel and other biofuels. It is renewable, carbon-neutral, cost-effective and abundant, and its advantages outweigh its disadvantages.
As South Africa runs out of landfill airspace, what role will science and technology play in combating this problem?
The innovative technology and methods being researched and developed can only escalate the positive impact to reduce volumes to landfill. Facilities such as these and the ability to analyse diverse samples for various analytes can only assist this process.
In line
with increasingly stringent global standards, South African
of improving upon and changing its waste disposal practices.
industry is faced with a challenge
Arguably, one of the greatest obstacles within the waste economy is the current dependence on landfills. By Kate Stubbs
According to the 2018 Africa Waste Management Outlook Report (authored by the UN Environment and CSIR), more than 90% of waste generated in Africa is disposed of at uncontrolled dumpsites and landfills, often with associated open burning. Moreover, 19 of the world’s 50 biggest dumpsites are located in sub-Saharan Africa.
Over the past several years, new legislation has been developed to improve the disposal of waste to landfill and, more importantly, to encourage industry to seek alternative solutions. One of the most significant developments has been the prohibition of certain waste streams from landfill disposal as from 2013 – with additional waste streams falling into this prohibition on an annual basis. It is imperative that local industry stakeholders are aware of this legislation and take the necessary steps to comply. Critically, these prohibitions represent an opportunity to seek alternative and more sustainable waste management solutions, and create a more efficient waste economy in South Africa.
In August 2013, the promulgation of the National Norms and Standards for the Disposal of Waste to Landfill (GN R 636 of 23 August 2013), together with the Waste Classification and Management Regulations (GN R 634 of 23 August 2013; WCMR), inter alia, formalised a comprehensive new legal framework. The Standards for Disposal of Waste to Landfill included a list of wastes restricted or prohibited from disposal to landfill, which has been coming into effect systematically since 2013 as per prescribed time frames. These wastes include reactive wastes, recyclable waste oils, whole waste tyres, lamps, lead acid batteries, and waste with a certain calorific value, among others.
Kate Stubbs Director of Business Development and Marketing at Interwaste
The prohibitions reflect the need to ensure the safety of those involved in the physical disposal of waste to landfill, as well as the long-term protection of the environment. Importantly, the prohibitions are indicative of the Regulator’s intention to drive the sustainable diversion of waste from landfill in accordance with the guiding principles of the Waste Management Hierarchy and the Waste Management Act.
The phased implementation of certain landfill prohibitions post August 2013 is intended to allow industry and the waste sector sufficient time to prepare and to explore alternative waste management solutions for the subject waste(s). Overall, the local waste sector has been responsive to this call by the Regulator so far, evidenced by many of the subsequent investments made in respect of the management
of wastes already or imminently prohibited for landfill disposal. Examples of such initiatives already implemented include lamp/lighting recycling facilities; other WEEE waste recycling facilities; waste-derived fuel (WDF) preparation facilities; development of co-processing capacity within the South African cement industry; refusederived fuel (RDF) production facilities; used/spent solvent recovery facilities; as well as many other innovative waste recycling, recovery, treatment and composting facilities.
On 23 August 2018, the following, additional, waste streams were prohibited from landfill disposal under the new legal regime:
• Reusable, recoverable or recyclable used or spent solvents
• PCB-containing waste (>50 mg/kg or 50 ppm)
• 25% diversion from the baseline at a particular landfill of separated garden waste.
Arguably though, it is those prohibitions that are yet to come into effect that will require the most management and technology interventions. That said, it could also create opportunities for the sector as a whole. From a financial viewpoint, these recent prohibitions should not have a dramatic effect on industry. PCB-containing waste, as well as solvent wastes, are already largely managed through alternatives to landfill
disposal (e.g. recovery/rejuvenation, recycling or thermal destruction). The disposal of quartered tyres is already ostensibly prohibited (as is any tyre; whether whole, quartered or shredded) in terms of the Waste Tyre Regulations (GN R 1064 of 29 September 2017) under the Waste Act.
Importantly, 23 August 2018 also introduced prohibitions on the concurrent disposal of certain waste types to the same working cells of any operational landfill facility, as specified in Section 5(2)(a) of the Norms and Standards for the Disposal of Waste to Landfill, as follows:
Section 5 (2): “The following prohibitions and restrictions on activities related to the disposal of waste to landfill come into effect after the timeframes indicated for each activity from the date of the Regulations taking effect.” Notwithstanding the WCMR having divorced a waste’s classification
Prohibited or restricted waste disposal activities:
(A) Disposal of
(i.e. general vs hazardous) from its landfill disposal requirements, the above listed ‘disposal activities’ prohibitions move the sector, at least partially, back to the regulatory realm of having distinctly operated general (pre-classified general waste) and hazardous waste landfills or, more correctly, disposal cells.
Key transformation required Given the above, landfills intending or required to manage both pre-classified general waste, as well as Type 1 Waste that has been treated and/ or hazardous wastes, will need to essentially operate two distinct cells at any such landfill site, i.e. a cell/s for disposal of pre-classified general waste and other Type 2/3/4 general wastes, as well as another separate cell/s for disposal of Type 2/3/4 hazardous and pre-classified
i) Type 1 waste that has been treated, with pre-classified general waste under Annexure 1 to the Regulations (paraphrased)
ii) Any hazardous waste, with pre-classified general waste under Annexure 1 to the Regulations (paraphrased)
iii) Type 4 waste with any waste other than Type 4, unless part of treatment
Timeframes:
Five (5) years: 23 August 2018
Five (5) years: 23 August 2018
Five (5) years: 23 August 2018
ADVANTAGES OF THE PROCESS WITH FLAT DIE PAN GRINDER MILL:
� Reduced investment and operating costs
� Cutting granulators are not required
� Long service life of the granulation tools, about 5,000 t of waste tyre shreds
� Large surface of the crumbs
� High purity (rubber/steel)
� High proceeds from final products
AMANDUS KAHL GmbH & Co. KG
Dieselstrasse 5-9 21465 Reinbek Hamburg, Germany
+49 (0) 40 72 77 10 info@akahl.de akahl.de
General waste: Domestic waste
Business waste without hazardous waste/chemicals
Non-infectious animal carcasses
Garden waste/waste packaging/waste tyres
Hazardous waste: Asbestos waste
PCB waste (i.e. containing >50 ppm PCB)
Expired, spoilt or unusable hazardous products
General waste (excl. domestic waste), which contains hazardous waste or hazardous chemicals
Building and demolition waste not containing hazardous waste or hazardous chemicals
Excavated earth material not containing hazardous waste or hazardous chemicals
August 2019, the industry will see the disposal of liquid waste, as well as hazardous waste with a calorific value of more than 20 MJ/kg, prohibited
Mixed, hazardous chemical wastes from analytical laboratories, and laboratories from academic institutions in containers <100 ℓ
Healthcare risk waste (HCRW)
hazardous wastes. This requirement would also affect initial waste handling at generators’ sites – where such generators would now need to ensure that they appropriately segregate waste in a manner aligned, irrespective of whether or not such wastes are intended for disposal at the same landfill.
Looking ahead, in August 2019, the industry will see the disposal of liquid waste, as well as hazardous waste with a calorific value of more than 20 MJ/kg, prohibited.
These prohibitions could have major financial impacts on such generators, given that the costs for the treatment, recycling or recovery
of these wastes are typically higher than any conventional management thereof to landfill. This challenge will be amplified by a general lack of such ‘alternative capacity’ in areas outside of Gauteng, relative to the more ready access to landfill disposal elsewhere in South Africa for such wastes under the current legal regime.
Critically, while the intention of the landfill disposal prohibitions is being understood from a purely theoretical point of view, the continued implementation of further prohibitions is likely to have an ever increasing impact on the waste management costs of generators producing these wastes in the short to medium term. For
the prohibitions reflect the need to ensure the safety of those involved in the physical disposal of waste to landfill, as well as the long-term protection of the environment
waste generators and industry stakeholders alike, it is imperative to start planning for the 2019 prohibitions, and to seek relevant investment and technology development opportunities with regards to alternative waste disposal solutions.
The growing interest in and application of circular economic principles now defines all materials as either biological nutrients (organic material) or technical nutrients within an economic system. This raises the question: if waste material was considered a technical nutrient, what would this mean for landfill management? The simplest place to start is with those streams that represent the most ‘unreasonable resource flows’.
These are streams for which alternative treatments and uses are well known, and have low barriers in terms of cost and availability of material for a viable business model. In the major metropolitan centres, one of these streams is builders’ rubble.
Currently, about 85% of builders’ rubble generated in South Africa is disposed of at landfill (DEA, 2012). For many waste generators, a landfill is the most feasible ‘sink’ for builders’ rubble, which may be due to logistics costs to divert the material to a builders’ rubble processor, the lack of rubble crushing facilities, excessive contamination of the material, or a perception that builders’ rubble has no further use.
Some of the benefits of a secondary materials economy are presented in Figure 1. Virgin construction materials are generally extracted and processed at some distance from the point of sale and application. Secondary materials generated through wastage on construction sites
While landfill sites have traditionally been designed and operated as permanent waste sinks, the perception of waste has been changing to the point that we now speak of a ‘waste economy’, of markets through which previous waste materials are extracted, processed and resold. By Kirsten Barnes, Quinton Williams and Henry Nuwarinda*
and demolition are normally available far closer to construction activities than virgin materials. Logistics costs are the limiting factor in the builders’ rubble market, as well as the market for virgin construction material. This benefit may, therefore, achieve large cost savings and drive the business case for the use of secondary construction materials.
Therefore, landfills are well placed within the builders’ rubble value chain to act as processing and stockpiling sites for builders’ rubble, and ideally a point of sale as often waste disposers
may also be buyers of the secondary construction materials produced.
Three rubble crushing projects at landfills in the City of Cape Town, Ekurhuleni and Stellenbosch were to be assessed in terms of contract type/ tender structure, quality control processes, opportunities/challenges for the contractor, benefits or losses for the public sector, as well as market uptake of material processed. Unfortunately, the tender processes for both the
City of Cape Town and Stellenbosch have been delayed. Some insights can, however, still be derived from both processes.
The crushing project at Simmer and Jack landfill in EMM was initiated through a business opportunity workshop run by the Gauteng Industrial Symbiosis Programme, as delivered by the National Cleaner Production Centre South Africa (NCPC). The NCPC operates under the auspices of the CSIR, which has an ongoing relationship with EMM regarding research and innovation.
An opportunity was identified at the workshop to trial a crushing project on Simmer and Jack landfill, which at the time had less than five years of landfill airspace remaining.
The project is structured through MoUs between the CSIR and Eco-Match (the crushing contractor), as well as the CSIR and EMM. There is no contractual relationship between EMM and the crushing contractor. The CSIR oversees and reports on the project with a view to structuring successful crushing contracts inclusive of all five EMM landfills.
The MoU holds Eco-Match to supply all the cover and material for landfill roadbuilding at processing costs +25% to the municipality. However, these costs are only incurred if the material is processed. To date, this hasn’t been necessary with all cover material applied with limited handling, and roadbuilding material being larger blocks that are difficult to crush. The only processing for roadbuilding is the use of a bulldozer to crush the material applied to the road bed.
In terms of the contractor for landfill operations and maintenance, EMM incentivises the contractor with improved compaction ratios and landfill space saved. As a result, the crushing project is beneficial to the landfill contractors, which probably contributes to the success of the initiative.
Since initiation in June 2016, the crushing contract has diverted 18 000 m3 of builders’ rubble from
landfill, and produced approximately 6 000 m3 of G5/G6, with the remainder in stockpile. The project performance will be reviewed in November or December this year, and the way forward will be plotted to extend the crushing project in EMM, most likely through a tender process. As a result of this intervention, as well as raising the height of the landfill, the lifespan has been extended to more than seven years.
There are no landfill fees at Simmer and Jack for clean builders’ rubble less than 300 mm in diameter; however, clean rubble greater than 300 mm is charged at R232.14 to R249.55 per tonne (2016/17 and 2017/18 fees), while mixed rubble is charged at the general waste fee of R242.24 to R260.40 per tonne (2016/17 and 2017/18 fees).
Assuming the landfill fees are cost-reflective of landfill operations, the diverted material represents a saving of approximately R4.74 million to the municipality (taking the average of the general waste fees), with Eco-Match bearing the operational costs of crushing the diverted material.
The NCPC aims to stimulate resource efficiency and cleaner production approaches in boosting manufacturing in South Africa that are
Builder’s rubble is a valuable secondary construction material and landfills are well positioned as stockpiles for this resource
cost-effective and environmentally sustainable. The demonstration of a successful crushing project on a municipal landfill should stimulate the uptake of such practices at other municipal landfills in the country. Furthermore, the contractor’s goals were realised with a financially sustainable industrial operation, with Eco-Match being able to access both feedstock and supply a quality product that is stimulating a growing demand for rubble as a secondary construction material.
The tender for crushing at three landfill sites in Cape Town is still being adjudicated at the time of writing. With a history of failed crushing operations on Cape Town landfills related to products not meeting market demand, CoCT partnered with GreenCape to modify the crushing tender structure for project success. GreenCape is a not-for-profit company predominantly funded by the Western Cape government to facilitate growth in the green economy through investment and job creation. GreenCape was able to interface with the industry without jeopardising the tender process
and provided CoCT with information derived from a crushing industry survey.
Key findings were that the crushing process and products should not be specified within the tender document, such that the contractor can modify the process, and therefore the products, to suit market demand. Furthermore, the responsibility to move product should rest with the crusher, which incentivises the delivery of high-quality product that is in demand.
This was in response to two failed crushing contracts, where there were no requirements in the tender regarding crushing process or any requirements to move the product. The result was that the crusher could not move the product due to a lack of market demand, and the municipality was left with growing rubble stockpiles.
Crushers highlighted that experience in crushing is key to screen, crush and blend streams to achieve the required product performance. Inexperienced crushers will likely produce only poor-quality fill suitable for some fill applications, which does not extract maximum value from the material.
A key point raised was quality control at the landfill gate and stockpile area, with many crushers requiring a less than 1% contamination in the feedstock entering their site; for CoCT, less than 10% contamination is designated ‘clean’ builders’ rubble, which is disposed of free of charge, while rubble with greater than 10% contamination is charged at the general waste fee.
If at least 300 t per day is available, it might be possible to crush at no cost to the municipality, especially if the land is available rent-free. In such a scenario, diversion targets were also acceptable to the industry, with the proviso that product could be sold from site due to the high costs of transport. It remains to be seen whether industry tendered on this basis for the CoCT crushing contracts.
Stellenbosch Municipality requested that GreenCape coordinate a site meeting at Devon Valley landfill with the crushing industry of the area, for a site inspection and for the municipality to invite proposals for crushing of the material at landfill. These proposals were then used to
The main challenge from a crusher perspective is the nature of the builders’ rubble entering landfill. Loads entering landfill are generally far more contaminated, even when classified as clean
If materials currently being landfilled were to be recognised as having value in the economy, landfills would form key links in such materials’ value chains
determine whether a request for quote (RFQ) or tender process would be followed, and to inform the content of the call.
findings for rubble crushing at municipal landfill sites
• Partnership with an independent, not-for-profit company has been key to all three case studies highlighted. Municipalities are unlikely to have in-house crushing expertise, which makes tender or RFQ design very difficult without industry input. However, municipalities cannot engage with the industry during the drafting of the tender/RFQ, as this would be seen as favouritism in the procurement process.
Secondary materials generated through wastage on construction sites and demolition are normally available far closer to construction activities than virgin materials
The independent body may engage with the industry to garner industry views, which may be communicated to the municipality in the form of an anonymised report, as was the case for CoCT and Stellenbosch.
• The pilot project approach has been very successful in Ekurhuleni, where there was scepticism around the ability of the crushing industry to handle the higher levels of contamination experienced at landfill (rather than crushers’ own sites) and to move the resulting product. Given the lack of current successful crushing projects at landfill in South Africa, this is understandable, as well as due to the nascent market status of builders’ rubble in many areas.
Cape Town and Gauteng have rapidly growing markets, while markets in the rest of the country seem to be limited.
• In this uncertain landscape, pilot projects allow for testing the waters before engaging in the strictly governed public procurement processes.
• Highly experienced contractors are needed, with access to market for the products. In aiming for experienced crushers, landfill management need not specify processes or products, as such prescriptive tenders may not take market demands into account, and result in products that are not saleable. Requiring the contractor to sell the material allows the crusher to adapt to market demand and maximise processing of material on landfill for increased sales.
• There should be acknowledgment in the tender/contract that such crushing operations are beneficial to landfill operators in reducing handling costs for rubble, as well as saving landfill airspace.
The main challenge from a crusher perspective is the nature of the builders’ rubble entering landfill. If crushers operate their own site, very strict gate controls are the norm, with those crushing for high-quality products tolerating less than 1% contamination at the gate. Loads entering landfill are generally far more contaminated, even when classified as ‘clean’.
It is recommended that municipal and landfill operator staff be trained regarding builders’ rubble, its usefulness, quality requirements, as well as effective diversion and stockpiling operations. Ideally, crushers should station a full-time staff member at the landfill to oversee diversion and stockpiling for maximum feedstock integrity and, therefore, the highest possible quality products. Communication from both municipality and crushers is also vital as to the quality of material desired.
Landfills are situated as close as possible to industrial and residential hubs in order to costeffectively service the waste management needs
of both homes and businesses. As such, if materials currently being landfilled were to be recognised as having value in the economy, landfills would form key links in such materials’ value chains. Landfills also represent a site of aggregation, accepting distributed waste ‘resources’ from many sources into one area.
However, the change in perception regarding landfills – from being a simple containment of rubbish and pollution to a resource hub – will have some implications for landfill management, as well as the waste supply chain.
Clean builders’ rubble is non-hazardous material, with limited impacts due to leaching (leaching of cement is the main concern). Furthermore, this material has both demonstrated applications and available technology for processing and reuse.
The successful recycling and application of this material is dependent on a goodquality supply of feedstock through effective segregation of material at source, excluding all other materials such as plastic, organics, soil, etc. Furthermore, quality control from gate to feedstock, processing and product stockpiles is vital to extract maximum value from the material and ensure high performance in the correct applications.
The case studies presented here demonstrate the viability of crushing on landfill in contexts of sufficient feedstock, as well as adequate construction activity to create a demand. Many metropolitan areas and larger towns in South Africa should provide suitable conditions for such crushing operations on landfills. They derive considerable benefit for municipalities, and the crushing and construction industries.
*Kirsten Barnes is an analyst in the Waste Economy Project at GreenCape, Quinton Williams is a waste economy programme manager at GreenCape, and Henry Nuwarinda is a project manager at the National Cleaner Production Centre South Africa.
For a full list of references or more information, contact the authors at kirsten@ greencape.co.za, quinton@greencape.co.za, or hnuwarinda@csir.co.za.
Communities
throughout the world increasingly have disposal issues with materials perceived as waste or no longer useful. This
is a
complex matter and the most common solution is to turn a blind eye, passing the problem on to future generations by resorting to landfill.
There are, however, growing concerns regarding the impact on the environment, together with the awareness that win-win partnerships for waste disposal are not only desirable but can be viable. This approach has given momentum to trends such as the rejection of single-use plastic products; value-added recycling by adopting a circular-economy approach to manufacturing; and, importantly, to view the waste by-product of our consumerist civilisation as a potentially valuable energy source.
Geocycle, the global waste management business of LafargeHolcim, treated 14 million tonnes of waste in 2017 – almost twice the total annual household waste generation of a country such as Switzerland. Employing the high-temperature environment in cement plant kilns, the company co-processes a wide variety of waste including solid shredded municipal and industrial waste, spent solvents, used tyres, waste oils, contaminated soils, industrial and sewage sludges, as well as demolition waste.
Co-processing does not leave any ash residue requiring disposal solutions, as the incinerated ash is incorporated in the clinker that is the basis of cement. It means that processed waste products are used as direct substitutes for fossil fuels and other raw materials of traditional
cement production. In this way, the waste has made a valuable contribution to reducing CO2 and energy costs, while the high temperature and residence time in the kiln ensure cleaner combustion; the diversion of waste from landfill and uncontrolled dumping then reduces pollution and saves land. Co-processing can, therefore, be seen as playing a critical role in solving the problem of waste disposal for modern society and making an important contribution towards a sustainable circular economy.
In South Africa, the government has taken a pivotal regulatory step with the Waste Classification and Management Regulations, and the supporting Norms & Standards Disposal Requirements for waste prohibited or restricted in terms of disposal compliance for hazardous waste with a calorific value greater than 25 MJ/kg (23 August 2017).
This focuses everyone’s mind on realising the value of waste products by defining their place in the energy chain.
“It marks the beginning of a new era for private/public cooperation in the disposal of used materials and landfill diversion,” says Brent Mahoney, director, Geocycle South Africa. “In concept, it is an example of industrial ecology, where – instead of South Africa merely being another throwaway society – the used material from one application is considered a potential raw material for another, or an energy source.”
Lafarge South Africa, a member of the international LafargeHolcim group, and its
subsidiary, Geocycle South Africa, have the approval of the Department of Environmental Affairs to operate licensed facilities to produce alternative fuel resources (AFRs). Geocycle has been providing a processed supply of various recycled, high-calorific-value materials, such as industrial oil sludge and used tyres that are used as fuel in the cement kilns at Lafarge’s Lichtenburg Cement Works, in the North West. The international Geocycle company has evolved into a leading provider of municipal, industrial and agricultural environmental management services, with a presence in 61 countries and over 10 000 customers worldwide. Today, the company is renowned for its responsible management of more than 10 million tonnes of waste each year. It is playing a significant role in preserving natural resources, minimising the health hazards associated with waste, and reducing the carbon footprint of waste.
Globally, it is estimated that approximately 4 billion tonnes of waste is generated every year
“At Geocycle, a passion for health, safety, the environment and landfill diversion is at the heart of everything we do.”
Globally, it is estimated that approximately 4 billion tonnes of waste is generated every year and south Africa alone produces 108 million tonnes annually
and South Africa alone produces 108 million tonnes annually. It is a massive and rapidly escalating environmental problem, with 49% of waste currently disposed of in landfills and controlled dumping, while 30% is not collected and merely finds its way on to open dumps or is burnt. Only 13% is recycled and 8% is used for energy recovery or incineration.
The waste problem consumes 80 km2 of land for landfills every year. To help put this into perspective, Brazil has one of the biggest dumpsites in the world, at 136 hectares – this equates to almost 200 football pitches!
The co-processing that Geocycle has developed for hazardous waste is the careful introduction of AFRs into the cement kiln to replace natural fuel resources such as coal, oil and gas. There is great emphasis on being careful, as the waste has to be sorted, blended and pre-processed before introduction to the kiln, to ensure tight quality control.
Geocycle, the global waste management business of LafargeHolcim, treated 14 million tonnes of waste in 2017, almost twice the total annual household waste generation of a country such as s witzerland
Conditions in cement kilns are ideal for the safe and total destruction of the waste stream, as these kilns operate at a temperature above 1 400ºC. In addition, the material in the kilns spends at least five seconds at this high temperature, ensuring that any contamination is going to be completely destroyed. The kilns operate with tight quality control and are also continually subjected to close monitoring of emissions.
While co-processing as an AFR is a critical solution for diverting hazardous waste from landfill sites and dumps, it is only part of the extensive service offered by Geocycle, which incorporates a full needs assessment, waste collection and transportation, laboratory analysis and pretreatment. The waste is separated into material suitable for recycling such as certain plastics and glass, and AFRs, as well as alternative raw materials for cement manufacture.
Geocycle South Africa has a waste management licence issued by the Department of Environmental Affairs and is a member of the Institute of Waste Management of Southern Africa. “We have the international
experience to be a trusted partner in ensuring compliance on waste management and a leader for landfill diversion procedures in South Africa,” says Mahoney. “Health, safety, the environment and landfill diversion are at the heart of everything we do: we are committed to working towards a better, zero-waste future.”
ROSE-registered collectors and processors are compliant with all waste transportation legislation and are strictly managed and audited
South Africa generates an average of 120 million litres of used lubricant oil in a year. This is a large amount of used oil that, if not collected and recycled responsibly, could make its way into our environment, contaminating landfills and groundwater. By Bubele Nyiba, ROSE Foundation
Environmental legislation requires used oil generators to store their used oil safely and ensure it is collected and processed by licensed oil collectors and processors, who will ensure it is recycled in an environmentally compliant manner.
Bubele Nyiba, CEO of the ROSE (Recycling Used Oil Saves the Environment) Foundation, says it’s essential that used oil generators use registered oil collectors to remove their oil and take it to be recycled in an environmentally compliant and safe manner.
The ROSE Foundation, an NGO supported by the main lubricants manufacturers and distributors in South Africa, controls the licensing and compliance of used oil collectors and processors. According to Nyiba, the ROSE-registered collectors issue the generator with a safe disposal certificate on collection. “The transport of used oil, as a hazardous waste, is governed by regulations contained in the
National Waste Information Regulations, which state that every waste transporter of hazardous waste must be in possession of the safety data sheet prepared by the waste generator in accordance with SANS 10234, as well as the relevant waste manifest documentation,” explains Nyiba.
ROSE-registered collectors and processors are compliant with all waste transportation legislation and are strictly managed and audited, further ensuring the customer’s compliance as a waste generator, she adds.
All transporters of hazardous waste must complete a waste manifest document, which must contain the name of transporter, the address and telephone number of the transporter and the declaration acknowledging the receipt of the waste. This manifest must be provided to the waste manager at the time of delivery to the treatment facility and the transporters must retain copies or be able to access records of the waste manifest document for a period of at least five years. In addition, the waste
manifest documentation needs to be available upon request. “Good news for used oil generators is that the safe disposal certificate issued by ROSE-registered collectors also acts as a hazardous waste manifest, thereby fulfilling the requirements of reporting by law.
“This document will be filled in by the used oil collector and will contain information on the generator of the used oil, the collector as well as the processor. Included in this information is that of the waste itself – the volumes, origin, the date of collection, etc.
“Four copies of this documentation are generated. Customers receive the pro-forma invoice as well as their certificate of safe disposal. The collector keeps a copy in their book and a final copy goes to the ROSE Foundation,” Nyiba highlights.
He explains that as transporters of a hazardous waste, ROSE-licensed used oil collectors must
Here are the foundation’s top tips for the storage of used oil:
• Drain used oil into a clean container with a tight-fitting lid, such as a reusable combination drain pan/storage container. For small quantities, you can use a specially designed plastic ROSE ‘Sumpy’ container to collect and store your used oil. Large-scale generators will store the oil in drums or storage tanks. Contact the South African Industrial Container Association (SAICRA) for more information on used oil containers on 0860 72 42 72.
• Ensure that you store the oil in a container with a secure lid so that it cannot spill out. Empty oil containers and drums make effective makeshift storage vessels for used oil; however, do not use a container that previously held chemicals such as cleaners, solvents, fuels, paint or bleach.
• Always clearly label the containers ‘used motor oil.’
• Keep these containers in a place that can be accessed by used oil collectors and keep the surrounding area clear and clean. Ideally, store them under cover and away from heat or sources of ignition.
• Keep oil-change pans free of water and ensure your storage containers are tightly sealed and covered to protect them from rainwater. Oil that is contaminated with water is far more difficult to recycle – requiring several laborious and costly processes to separate the water from the oil before it can be recycled.
• Ensure that you do not mix used oil with other fluids such as antifreeze, transmission fluid, petrol, diesel, etc. Mixing them may make them non-recyclable as well as very hazardous and flammable.
• Build a bund wall around bulk used oil storage tanks so that, in the event of a spill or leak, the used oil will be contained. In the event of an oil spill, contact your used oil collector.
conform to SANS 10232 – legislation that governs the placarding and documentation of vehicles carrying dangerous goods. Licensed used oil collectors must also meet a number of general safety requirements on their vehicles.
Nyiba says all vehicles’ placarding and documentation must be an accurate reflection of the dangerous goods being transported. In addition, dangerous goods placards must be made out of a rigid material, such as painted metal plate, rigid plastics, plastics material or coated paper that can withstand bending and warping and must be 700 mm wide and 400 mm high in size with a 10 mm black border.
The word ‘waste’ must also appear above the UN number and phone number must appear as the operator number, provided it is available 24 hours a day.
“A used oil collector’s insurance provider’s number, a Hazcall or a control room number can be used for specialist advice – provided it is available 24 hours a day and the full placard, including the 10 mm black border, must be clearly visible from the roadside, whether directly fixed on the vehicle or supported on a permanently fixed frame. The placard must also be clean and legible,” she continues.
Three regular-size dangerous goods placards must be stuck on the vehicle, semi-trailer or trailer – one at the rear and one on either side of the vehicle. Vehicles with a GVM of less than
3 500 kg can be fitted with smaller placards (350 mm x 200 mm) where space does not allow the fitting of a regular-size placard.
A regular-size (250 mm x 250 mm) orange danger warning diamond must be attached to the front of a vehicle or a truck tractor so that it is clearly visible from the front. Again, vehicles with a GVM of less than 3 500 kg may be fitted with a reduced-size (100 mm x 100 mm) danger warning diamond where space does not allow the fitting of a regular-size one.
Furthermore, all National Oil Recycling Association of South Africa (NORA-SA) used oil collectors must also carry the following documents in the designated space within their vehicles: a transport emergency card, in the form of a Tremcard or TREC for each dangerous goods item; one or more dangerous goods declaration(s) to cover all the goods that comprise the load; and a confirmation of classified waste, if applicable.
Top tips for storing used oil
The safe disposal of hazardous waste has become a critical issue for business in South Africa and the ROSE Foundation endeavours to make things easier by helping companies get on board with the right way to store, transport and dispose of used oil.
For more information and to find out about registered collectors and processors, visit www.rosefoundation.org.za.
As transporters of hazardous waste, ROSE-licensed used oil collectors must conform to SANS 10232
Large-scale generators store used oil in drums or storage tanks
Whether it’s because they want to do their bit to help save the planet or they’re passionate about giving new life to old things, South Africans are recycling more than ever before. By Liesl Frankson
John Hunt, managing director, Mpact Recycling, says while the country’s citizens may have a general understanding of the benefits of recycling, they may not realise just how much good they are doing. Every item that is recycled is one less item going to the country’s strained landfill sites. Less waste to landfill means a reduction in greenhouse gas emissions but, according to Hunt, recycling also helps to address some of the country’s socia ills such as unemployment and poverty.
The Paper Recycling Association of South Africa notes that recycling has helped create work opportunities for more than 100 000 people. As a leading player in the paper and plastic packaging industry, Mpact continues to create important employment opportunities in the sector.
“The process of helping to develop recycling businesses has been part of Mpact Recycling’s business model for many years,” Hunt explains. “Over time, the focus has moved from businesses in
outlying towns and cities to looking to underserviced areas closer to our branches. In the last few years, we have helped set up over 40 buy-back centres in and around Johannesburg,” he adds, noting that the business of collecting recyclables lends itself to the development of small black-owned enterprises, as the capital investment required is low and the company has the expertise to transfer knowledge to these new business owners.
“Recycling is a very local business. You need to be on the ground to know where the recyclables are to be found. Enterprise development is thus an important part of our business and of growing recycling rates in South Africa.”
It was in this spirit that the company set out to develop collections in deep rural and township areas. One of the company’s recent recycling collection initiatives saw Mpact venturing into the Zululand area to establish a buy-back centre in Empangeni as well as a collections facility at a landfill site in Hluhluwe.
“Mpact has a mill in Felixton and a recycling branch in Richards Bay. The area north of Richards Bay is characterised by widely separated, small
“When a piece of plastic or paper is recycled, its value moves from being a cost to the city to being a tradeable commodity.”
John Hunt, managing director, Mpact Recycling
rural towns and villages. Collecting recyclables in this environment is challenging due to the small volumes in each town and the long distances to fetch the materials,” Hunt explains.
“We embarked on a project to provide consistent collection of recyclables throughout the area to encourage local collectors to persevere and grow their recycling efforts. Much work still remains to develop more efficient logistics processes, but the consistent collections have provided stable and consistent incomes to the people involved,” he says.
Through its buy-back centres, Mpact provides support to the waste collectors and sorters in these small towns and villages. In addition, the company has set up sorting and bailing facilities that provide further work opportunities.
“Projects like this enable recycling to happen. Without this effort, the materials we have recycled would have ended up in landfill sites and those involved in collecting recyclables would then have no income,” says Hunt.
Commenting on the short-term goals for the project, Hunt says he hopes to make the collection processes more efficient and encourage others to participate. “Next, we would like to develop similar projects in other areas, where possible,” he adds.
South Africans already recycle a large quantity of material. Now the next step in improving on our current recycling rates relies on new ways of collecting
According to the Paper Recycling Association of South Africa, the annual paper recovery rate has increased by 2% year-on-year since 2012 and is currently at 68.4%. PET Recycling Company (Petco) reports that plastic bottle recycled tonnage has grown by 822% since 2005.
While these efforts point to a growing awareness of recycling, Hunt notes that there is still more work to be done. The Department of Environmental Affairs reports that less than 20% of waste is recycled annually, meaning most of the country’s recyclable materials continue to go to landfill.
Through its buy-back centres, Mpact provides support to waste collectors and sorters in small towns and villages
recover the maximum amount of material from collected waste at a cost and scale that make it economically viable. Although many breakthroughs have been made in recent years, more research and development work needs to be done,” Hunt explains.
Less
20%
More
“South Africans already recycle a large quantity of material. Now, the next step in improving on our current recycling rates relies on new ways of collecting from homes and offices before this material ends up on landfill sites. This will require local authorities and recycling businesses working closer together,” he points out.
In addition to closer collaboration, Hunt notes that technology can play a critical role in increasing the amount and type of materials that can be recycled.
“The challenge in recycling many types of material is in developing technologies that can
Other industry bodies such as Petco are also working to equip small enterprises with the tools to participate more effectively in the circular economy
“The more South Africa invests in technology for recycling, the less waste there will be to go to landfill, which is why public-private partnerships are necessary to boost recycling activities in South Africa and ensure we find sustainable solutions to reducing waste, creating jobs and protecting our beautiful country,” he continues.
Commenting on the true impact of recycling, Hunt notes that when a piece of plastic or paper is recycled, its value moves from being a cost to the city to being a tradeable commodity.
“Economic value is created. This value is distributed to all the people in the recycling process, from the trolley pushers collecting on the streets all the way through to workers in recycling factories. By recycling, each of us can contribute to the creation of wealth, which South Africa so needs,” he concludes.
In
A proud Southern African distributor of MACFAB waste balers and agent for Enerpat recycling equipment
Through our relationships with world-leading waste equipment manufacturers, we ensure our clients’ needs are met with a diverse range of quality waste processing machinery – throughout Southern Africa.
Formed in June 2017, Optimum Recycling Solutions has set out on a quest to provide good-quality, affordable recycling equipment to a wide cross section of the Southern African recycling industry – from entry-level collectors on the streets to recycling buyback centres and retailers.
The company focuses on the importing and distribution of recycling equipment in Southern Africa and was recently granted ‘distributor agency’ status for Southern Africa by MACFAB recycling equipment. “This provided a unique opportunity, as MACFAB was not officially represented in Southern Africa,” notes Barry Stead, managing director, Optimum Recycling Solutions.
“MACFAB operates and owns state-of-the-art manufacturing facilities in Ireland and has been operating since 1971. It is an international leader in the manufacturing of waste balers and, as such, is represented in over 30 countries,” he adds.
An all-inclusive offering
Stead says the company aims to be a one-stop shop for its clients, with an in-house supply chain service providing further synergies.
“This enables us to offer a full management function, ensuring equipment is seamlessly managed from door to door, inclusive of installation and training.” Stead notes that the company values strategic partnerships in the industry with stakeholders, as they are vital to making a difference and creating a better environment for all.
“We’ve formulated innovative rental solutions together with Mercantile Bank, while our national servicing requirements and warranty support have been entrusted to Hyflo SA, among others.”
In its quest to service the recycling industry and grow its partnerships, Optimum Recycling recently attended WasteCon 2018. “We were pleasantly surprised by the interest shown in our equipment, among both delegates and
ABOVE Our 50 t galvanised balers are efficient, competitive and made for Africa
exhibitors. We found WasteCon to be of great value, with much potential for business and partnerships of value.
“Ultimately, Optimum Recycling’s value proposition is to build a team of entrepreneurially minded people across South Africa who: value and cherish our environment; understand the challenges our customers face; and exist to provide superior service and cost-effective, innovative solutions and equipment for the management and compaction of disposable and recyclable waste in Southern Africa,” Stead concludes.
“Ultimately, o ptimum Recycling’s value proposition is to build a team of entrepreneurially minded people across s outh Africa…”
The system, which was developed by Dutch start-up organisation The Ocean Cleanup, features a 600 m long floating construction that will form an artificial coastline to capture the plastic waste that accumulates in ocean garbage patches.
These garbage patches occur where different oceanic currents converge to form enormous vortices. In total, there are five of these major vortices (known as gyres) in the world’s oceans –the largest of which is in the North Pacific.
According to the latest findings, the Great Pacific Garbage Patch between California and Hawaii is as large as Mexico and contains 1.8 trillion pieces of plastic. “The ocean plastic problem is huge and continues to grow every day. Eight million metric tonnes of plastic waste ends up in our oceans every year, a trend which is rising exponentially.
“Due to their specific densities, some types of plastic can float near the surface for many years before the effect of UV light and wave impact
The world’s first system to combat maritime plastic waste was recently deployed 1 200 nautical miles west of California, USA, in the Great Pacific Garbage Patch. This innovative solution could soon form part of the globes largest clean-up in history.
breaks them down into microplastics in these formations known as garbage patches or trash vortices,” explains Boyan Slat, founder of The Ocean Cleanup.
To tackle this, the organisation has partnered AGRU Kunststofftechnik to develop the system. The backbone of the system is a 600 m long floater pipe made of fully pressure-resistant PE 100-RC XXL pipe.
Another key feature of the system is a 3 m deep skirt attached below the floater. Together with the floater, the skirt forms an artificial coastline in the ocean. The floater provides buoyancy to the whole system and prevents plastic from floating over it. It also prevents smaller particles from escaping underneath. This sophisticated solution sets out to retrieve and recycle 90% of the plastic from the Great Pacific Garbage Patch by 2040 – harnessing the power of the ocean to its advantage.
The system takes advantage of the three natural oceanic forces to ensure that it moves faster than
The 600 m long Ocean Cleanup system was towed from San Francisco to the site in the Great Pacific Garbage Patch on 8 September 2018 (Photo:
the plastic in the swirling mass of rubbish in the garbage patch. “Both the plastic and the system are being carried by the currents. However, winds and waves propel only the system.
“As the floater partly sticks out above the surface, and plastic is primarily just beneath it, the system thus moves faster than the plastic, allowing the plastic to be captured. The skirt extends deeper in the middle than on its edges of the system. As the current applies pressure on the skirt, the system naturally adopts a U-shape, which enables it to concentrate plastic in its centre, like a funnel. The drag generated by the skirt also acts as a stabilising force, allowing the system to reorient itself when the wind changes direction. And because the system – like the plastic – is free floating, it automatically drifts to the areas with the highest plastic concentration,” Slat explains.
Every six to eight weeks, a ship will collect the concentrated rubbish and deliver it to a wastecarrying mother ship, which will bring the plastic ashore for recycling. If the first Ocean Cleanup system is successful, a full fleet of 60 floating screens will gradually be launched in the Great Pacific Garbage Patch.
“The amount of plastic waste present in this vortex of refuse would then be halved every five years, removing 90% of the plastic waste from the Great Pacific Garbage Patch by 2040,” Slat concludes.
However, solar solutions projects required to power an organisation can be complex, with a number of ‘hidden’ costs and potential pitfalls that could jeopardise success. Kevin Norris, consulting solutions architect: Renewable Energy, Jasco Intelligent Technologies, discusses some of the challenges companies should be aware of before embarking on a solar project.
What is the most common error companies make when embarking on a solar project?
In planning a solar solution, one of the most common errors is the failure to properly calculate the true costs. Solar solutions consist of more
than just solar panels and inverters. The Solar Energy Industries Association estimates that over 60% of the total cost of solar solutions in the USA lies in the ‘soft’ costs, with the actual panels and inverters making up less than 40%, and the same parameters are very likely to hold true for South Africa and the rest of the globe.
In the wake of looming energy price hikes, many organisations are proactively considering solar solutions as an alternative. there has never been a better time to go solar.
Organisations should carefully scrutinise their solar provider quotes to ensure that all ancillary costs, which include labour, site surveys, engineering and design fees, are factored in. Also, peripheral components such as mounting structures and/or assemblies and wire management costs should
It’s not always possible to accurately calculate all costs until implementation is complete, as the scope may change or difficulties may be experienced throughout the course of the project. This is especially true when obtaining budget quotes where no site surveys or assessments have been done. In addition, it is critical to account for the storage, transport and security of all delivered equipment, bearing in mind that components may lie in storage for some time while the project is under way. Solar equipment is a hot target for theft. Therefore, 24-hour security is imperative for the
It takes a team for a successful solar installation. What personnel costs should businesses be aware of when implementing a solar solution?
A successful solar solution is the result of skills that extend beyond the installation phase of the project.
Depending on the scope, scale and conditions of the solar solution, different people will be needed to contribute their expertise and advice at various stages of the project.
Many professionals may be required, from electricians to environmental impact assessors. It takes a team for a solar solution to be implemented in a sustainable and successful manner, and organisations should ensure their solar solution provider includes these associated personnel costs in their quote.
Can you give us an example of some of the professional services that may be required on a solar installation that could add up?
Solutions architects are needed to design and engineer the solution based on a site survey, which yields information on the requirement and site conditions. This is a lengthy process and many companies fail to comprehend the amount of work that goes into planning and designing a solution before a proper quotation can even be raised. This is one of the reasons why budget quotes are so unreliable.
If the solution is mounted on high poles, car ports or at ground level, civil engineers will be needed to assess soil conditions and provide a solid, stable foundation. A weak or poorly factored foundation can result in the entire structure collapsing at the first sign of strong winds or excessive rainfall.
If the solar solution is going atop a roof, structural engineers will be required to assess the structural stability and strength of the building, and make structural enhancements if necessary.
The stringent regulations of the Occupational Health and Safety Act (No. 85 of 1993) must be
adhered to, as inspectors may investigate a solar solution at any time during implementation. Failure to comply can result in very costly fines, as well as a halt in production until compliance is met.
A formal health and safety officer will ensure that the project is registered with the Department of Labour, and that all standards are adhered to. Organisations should ensure that all of these associated personnel costs are factored into their quote.
What are some of the additional aspects businesses overlook when planning and implementing a solar solution?
There are several additional, yet important, aspects that aren’t always considered when planning and implementing a solar solution, resulting in exceeded budgets, poor installation or even risk of fines. These include:
• The impact of environmental factors such as wind, rain and proximity to the coast.
• Logistics requirements – forklift and utility vehicle hire, and storage space required for the duration of the project.
• Insurance – both during and after installation, to mitigate risk.
• Using reputable suppliers – poor-quality equipment or civil work will inevitably lead to having to do repairs and replacements before necessary.
• Applications – depending on the scale and location of the solution, organisations need to lodge applications with various governing and regulatory bodies such as the National Energy Regulator of South Africa, the Department of Energy, the local utility provider, the Department of Health & Safety, etc.
• Time – a sizeable project can take several months or longer to complete, factoring in travel, accommodation and subsistence allowances for installation staff for the estimated duration of the project, etc.
• Solution maintenance – solar solutions are fairly self-sufficient once up and running; however, they do need to be regularly maintained and monitored to ensure maximum efficiency and uptime. There are remote monitoring systems that proactively monitor for issues such as soiled solar PV modules, degradation, and wear and tear, sending an automatic alert when performance drops so that businesses respond accordingly and address the area of concern. This extends the longevity of the solution and can reduce the risk of downtime or system failure.
What should businesses look for in a solar solutions provider?
Before embarking on a solar solution, businesses should make sure they use a reputable solar solution specialist provider that fully understands
cost of solar solutions in the U s A lies in the ‘soft’ costs
the requirements before they begin. The service provider needs to be invested in software and hardware solar knowledge, and must be able to identify possible areas of risk or concern so that they can be addressed at the initial phase –possibly even from quote stage. Finally, a competent service provider should have a demonstrable track record of successful solar implementations to prove their experience.
Sustainability and eco-friendly innovation have become key focus areas for property developers and construction companies alike. Green building initiatives and environmental factors are being considered at every stage of a building’s life cycle. By
The ultimate goal of green building initiatives is to ensure that the processes that make up a building’s life cycle produce limited habitat loss, pollution and environmental degradation, while complementing the traditional aspects of classical building design such as economy, utility and ergonomics. Effectively, it attempts to integrate economic, social and environmental sustainability into a new paradigm for construction.
While the focus of green building and sustainability in construction has traditionally been on the end product, more developers and construction companies are looking at the construction process itself in their efforts to become more eco-conscious.
Conventional construction methods consume a lot of energy and emit large quantities of greenhouse gases (GHGs), which contribute to global warming and, ultimately, environmental degradation.
The primary sources of waste and environmental impacts in construction include the manufacturing and transportation of building materials, the energy consumption of construction equipment and processing resources, as well as the disposal of construction waste.
As such, Mark Fugard, managing director of Concor Western Cape, says a main principle of green building construction is the selection of materials and equipment that are environmentally conscious and energyefficient. “For example, the manufacturing of concrete and reinforced steel accounts for most of the GHG emissions of all building materials, but the use of recycled reinforced steel and other materials should
mitigate this effect. Similarly, recycling and reuse operations are integrated into construction wasteuse management, minimising landfill waste.”
For the construction industry to become a true advocate of sustainability, Fugard notes that the sector will need the conscious buy-in of all stakeholders as well as make a conscious effort to move away from traditional models and embrace environmentally friendly or green building practices.
“The construction industry plays an essential role in the socio-economic growth of a country through the continued provision of commercial, residential and public infrastructure, which is integral for the quality of life of citizens and society as a whole.”
For Fugard, sustainable construction involves committing to the attainment of economic, environmental and social sustainability.
“Economic sustainability involves making efficient use of resources including labour, materials, water and energy, while environmental sustainability means committing to preventing harmful effects on the environment, minimising waste and making efficient use of natural resources. Social
“the construction industry plays an integral role in the support of a sustainable environmental and economic future and, like many others, we believe green building practices are the way forward.”
sustainability entails responding to the needs of stakeholders including clients, suppliers, employees and local communities, at all stages of the project life cycle,” he explains.
Fugard notes that green building construction practices are not without their challenges. “The integrated approach requires procurement of contractors and specialists in a field for which there is not much expertise, in addition to the organisation of procedural change in construction and wastemanagement practices. However, while green building construction holds many challenges, the benefits should not be understated,” he highlights.
The sustainability, cost saving and lower dependence on fossil fuels means that green buildings are future-proof and more enticing to developers and rental parties. Due to all the carefully considered and incorporated energy-efficient technologies in the design of a green building, they cost less to maintain and are becoming cheaper to insure over time, as the risks are lower than those of a conventional building.
The Government Communication and Information Building in Pretoria was the Nedbank Sustainability winner in 2014
In general, the green building initiative represents a shift in thinking from the idea of ‘getting the job done’ to construction that fulfils the objective of the building, taking into account environmental considerations.
“The construction industry plays an integral role in the support of a sustainable environmental and economic future and, like many others, we believe green building practices are the way forward. The success and accreditation of our current products give support to the transition from classical business practices. We hope that, through our green building projects, we can create awareness in the public and industry of the value of sustainable initiatives and work towards the creation of not just green buildings but green complexes and green cities as well,” Fugard concludes.
The Portside Building in Cape Town was built by Concor and is a 5-star rated Green Star building
GREEN BUILDINGS INCORPORATE superior air quality, lots of natural light, access to views and noise control, which benefits building occupants, making these building better places to work or live in. The major considerations taken into account are energy and water efficiency, resource efficiency, indoor environmental quality, and the building’s overall impact on the environment.
“THE CONCEPT OF GREEN BUILDING has been well received by the South African public, with the GBCSA having certified approximately 400 green buildings in South Africa since 2007,” notes Sakena Parker, transformation manager at Concor.
“IN PRIVATE DWELLINGS, ALTERNATIVE energy like solar energy and reusing/ recycling water resources is increasingly being used and I see green building extending into residential precincts, where greening the landscapes and parks will create healthy, liveable, environmentally responsible areas. It’s important to note, however, that there is still a lot that needs to be done to create a greater awareness of respecting the environment, as well as highlighting and educating people on the benefits of minimising waste to landfill as business opportunities,” she adds.
THE QUALIFICATION OF GREEN BUILDINGS in South Africa is determined by the Green Building Council of South Africa (GBCSA). All green buildings are Green Star rated by the GBCSA, which validates the quality of the product to developers. To be Green Star rated, buildings must have the required documentation and credits relating to procedures monitored by green practitioners.
“THE MARKET FOR GREEN BUILDING has been slowly developing over the last 10 or so years. Demand for commercial green buildings generally started in the Western Cape but we see that this need has now been fully embraced in Gauteng. It is a market trend and a client requirement, and we accommodate it as best we can,” explains Parker.
THESE RANGE FROM DETAILS ON MATERIALS, such as types of paint used in the building, to confirmation of reuse and recycling policies utilised in production. A 4 Star Certified Rating rewards ‘Best Practice’ while a 6 Star Certified Rating recognises ‘World Leadership’ in green building.
WHILE THE FOCUS OF GREEN BUILDINGS has largely been in the commercial space, Parker says she foresees an uptake of green building in the residential arena.
The Sarchi Chair in Waste and Climate Change at UKZN has partnered with SANEDI and IWWG to o er an International Training Seminar and Summer School on the e ective “Management of Waste as a Resource”. This programme will provide advanced training for Practitioners, Scientists and postgraduate students on the most innovative practices in waste treatment, characterisation and valorisation.
The programme is a unique opportunity to engage with key national and international experts in waste management.
in partnership with
For industry to remain competitive in a challenging economy, it’s constantly in search of ways to enhance energy efficiency, energy savings and energy recovery, while reducing carbon emissions.
With energy consumption typically representing over 70% of a compressor’s life-cycle cost, industrial company Atlas Copco has introduced its fourth-generation VSD+ compressors in a bid to save energy and assist customers in curbing costs.
“Compressed air, much like electricity, is a utility that is critical to most production processes. So, the core business and not the source of the compressed air should be our customers’ primary focus,” explains Charl Ackerman, business line manager: Industrial Air, Atlas Copco. “Ensuring that our customers’ compressed air systems are seamless, efficient and cost-effective to help keep their electricity bills and production costs to a minimum is, therefore, our focus.
The compact, smart, efficient and reliable Atlas Copco GA75-110 VSD+ fulfils all these requirements perfectly for complete customer peace of mind.”
This gave rise to the development of groundbreaking, energy-efficient VSD+ technology, which combines the company’s expertise and
know-how on energy-efficient technology into one unmatched ultra-high-efficiency solution.
The boosting of the completely in-house developed GA VSD+ technology offers increased efficiencies that can cut energy bills by as much as 50% for lowest total life-cycle cost and sustainable productivity for end-users.
Pioneered by Atlas Copco in 1994, VSD technology is fundamental to the company’s solid efficiency drive. VSD matches the compressor’s speed to the compressed air demand, presenting an efficient option for operations where compressors are regularly run at below maximum capacity or where air demand profiles fluctuate.
According to Ackerman, motor speed regulation is the most efficient compressor control method where air demand varies “because the inefficient transition period between full and no load is eliminated, which avoids excessive off-load power consumption.
“Maintaining the net pressure band within 0.10 bar (15 psi), greatly reduces the overall average working pressure and energy costs.” Soft start will lend further flexibility as gradual motor ramp-up avoids electricity surges. Reduced carbon dioxide emissions are a further benefit offered by VSD technology.
Energy savings halved with fourth-generation Atlas Copco GA75-110VSD+ compressors
Ackerman, however, does point out that VSD is not a one-size-fits-all solution and recommends a fixed-speed compressor as the most efficient solution for applications that demand constant pressure or applications requiring air at maximum capacity 24/7.
“We have also improved the efficiency of our nitrogen generators,” states Ackerman. “In addition to the standard NGP, we are also able to offer the enhanced NGP+. Our nitrogen generators incorporate PSA (pressure swing adsorption) technology and can simply be plugged into an existing compressed air installation to delivers an independent, reliable, secure, flexible and cost-effective supply of nitrogen with purities of up to 99.999%.”
In closing, Ackerman points out the importance of regular and correct maintenance by trained technicians, which he says is fundamental to the efficient performance of a compressor.
“As part of our customers’ efficiency drive, we are seeing an unmistakable increase in demand for a total solution that includes said service and maintenance as well as the monitoring of compressed air installation. Atlas Copco offers to assist end-users in achieving the lowest possible operational costs and sustainable productivity.”
You can have the best systems and equipment in the world, but if your people don’t use them, you are wasting your time and money. As a country, we have to move people beyond compliance to ownership.
By Jürgen Tietz* & Dr Natalie Skeepers
The safety landscape is changing rapidly as people evolve and technology improves. Safety managers are paying more attention to methods of reducing injury and costs, while improving productivity, safety culture and the education of workers.
In an effort to move South African industries – including the waste industry – from a culture of compliance to one of ownership, Disruptive Safety has come up with an innovative and creative way to stimulate safety discussions in the workplace. Our goal is to empower clients with the knowledge, systems and processes so that they can self-manage going forward. In particular, we aim to educate and empower health and safety representatives to make a difference by giving them a micro-learning tool – a handbook – which is fun, interesting, educational and visual, thereby ensuring understanding, a high level of impact and retention.
We translate the legal requirements into simple, practical English so that the reps can understand the critical role of their functions. The feedback we have received has helped to confirm that this solution delivers results, by shifting the mindset from one of compliance – where the focus is on following the rules and “don’t break the egg” – to one of ownership – where choice is central, from reactive to proactive – and problem-solving.
Results that speak for themselves
We aim to re-energise and transform health and safety on-site by clarifying the functions, expectations and power of influence that health and safety reps have. This tool assists them to tackle workplace safety problems. The results are worthy of celebration: fewer work accidents, more safety-consciousness, selfmanaged workplaces, reduced costs, and higher levels of organisational health and productivity. In the end, the three organisational health factors remain system, equipment and people, but the most important of these is people.
*Jürgen Tietz is director of Disruptive Safety, a professional speaker, thought leader and author.
The Safety Rep’s Survival Guide is a unique tool that has been written for, and with the direct input of, health and safety reps. We have combined years of actual industry research and experience of educating and empowering health and safety reps in a wide range of industries, from commercial, construction, government, corporations, engineering, manufacturing and mining to service industries. The creative use of Antzi, our inimitable and novel character, helps to make the learning come alive.
We aim to re-energise and transform health and safety on-site by clarifying the functions, expectations and power of influence that health and safety reps have
The very first International E-Waste Day was held in October to promote the correct disposal of electrical and electronic equipment throughout the world.
Developed by the WEEE Forum, an international association of e-waste collection schemes, International E-Waste Day was hailed as a tremendous success by its organisers. The aim of the event was to raise the public profile of e-waste and encourage consumers to correctly dispose of their e-waste, with the resulting increase in reuse and recycling rates on the day itself and into the future.
The event was celebrated in 30 different countries worldwide with around 50 organisations participating through various campaigns. A wide range of initiatives including conferences, events, school and city collections, in-store promotions and recycling centres as well as online campaigns took place around the world in honour of International E-Waste Day.
Commenting on the event, Karmenu Vella, EU Commissioner for Environment, Maritime Affairs and Fisheries, notes that the event was important and timely because e-waste continues to increase in volume and the materials it contains are essential for manufacturing new products and satisfying consumer demand for e-products.
“Even in the EU, which leads the world in e-waste recycling, only 35% of e-waste is officially reported as properly collected and recycled. Awareness-raising initiatives impacting positively on collection rates will not only help
member countries in achieving the WEEE Directive’s targets but also help Europe in developing the circular economy,” she says. Pascal Leroy, secretary general, WEEE Forum, believes that consumers are key to better management of e-waste: “We have high aspirations that this campaign can have a huge impact on their habits. For example, in each household in Belgium, there is an average of 79 electrical items as well as 47 lamps, which makes getting e-waste out of homes and businesses and into reuse and recycling plants a critical part of the challenge.”
Approximately 50 million tonnes of e-waste is expected to be generated globally in 2018. Half of this, according to the WEEE Forum, is personal devices such as computers, screens, smartphones, tablets and TVs, with the remainder being larger household appliances and heating and cooling equipment.
Even more alarming is that only 20% of global e-waste is recycled each year, which means that 40 million tonnes of e-waste per annum is either placed in landfill, burned or illegally traded and treated in a substandard way, and this is despite 66% of the world’s population being covered by e-waste legislation.
This results in the huge loss of valuable and critical raw materials from the supply chain and causes serious health, environmental and societal issues through illegal shipments of waste to developing countries.
The status of
Approximately 90% of printed circuit boards and 80% of plastic recovered from e-waste in the country are exported for reprocessing
According to 2011 statistics, only 11% of South Africa’s e-waste was being recycled
Each individual in South Africa generates about 6.2 kg of e-waste per year
The Department of Environmental Affairs estimates that South Africans generate around 360 000 tonnes of e-waste annually
Venue: Emperors Palace, Ekurhuleni, Gauteng
Date: 13 – 14 November, 2018
The 13th Southern African Energy Efficiency Confederation Conference is set to take place this November 2018 with a focus on energy management, the environment, facilities building upgrades, energy engineering, cogeneration, power generation, and efficiency improvement industries. The 2018SAEEC Conference has been hailed as an important energy event of national scope
for end-users and energy professionals in all areas of the energy field. Considered a truly comprehensive forum, the event allows stakeholders to fully assess the big picture – and see exactly how all the economic and market forces, new technologies, regulatory developments and industry trends merge to shape the critical decisions on the energy and economic future of your organisation.
The 2018SAEEC Conference features a convention agenda with seminars and exhibition on a variety of current topics.
Venue: Sandton Convention Centre, Johannesburg
Date: 19 – 20 February 2019
Contact: info@energyindaba.co.za
The Africa Energy Indaba Conference is the definitive energy event for Africa, providing an annual programme that shapes energy policy for the continent.
The conference will provide delegates with the opportunity to debate policy, review industrial progress and market trends, discuss the efficiency
Venue: Sandton Convention Centre, Johannesburg
Date: 26 – 27 March 2019
Contact: enquiry.za@terrapinn.com
Power and Electricity World Africa brings together the brightest and most innovative minds that are shaping the way we
Index to Advert I sers
generate energy and meet growing demand across Africa. Delegates can look forward to first-hand knowledge on upcoming projects, investment opportunities across the continent and innovations that will help utilities deliver energy.
The show features Africa’s largest energy exhibition, where leading solution providers showcase a wide range of technologies aimed at helping transform and innovate the African energy sector.
of various public support mechanisms and public-private partnerships across the continent, review new data, and gain insight into the latest technological trends globally.
In addition, companies actively involved in the industry will be showcasing innovative solutions for the benefit of Africa in the exhibition area.
Venue: Gallagher Convention Centre, Johannesburg
Date: 09 – 11 July 2019
Contact: Annalize Cilliers-Eccles at annalize.cillierseccles@mm-sa.com
Trade professionals in water, sewage, refuse and recycling are expected to gather at IFAT Africa 2019. The event will feature presentations from industry experts, trade associations, business partners and exhibitors covering the latest product developments, trends and market analyses in exciting workshops, panel discussions, speakers’
corners and live demonstrations. The event features an extensive range of product categories and topics include: extraction and treatment, sewage treatment, water distribution and sewers, refuse disposal and recycling, generating energy from waste materials, energy-efficiency technologies, decontamination of old sites/soil treatment, air pollution control and noise reduction, control and laboratory technology, environment management and services and science, and research and technology transfer.
BooK your StAnd now