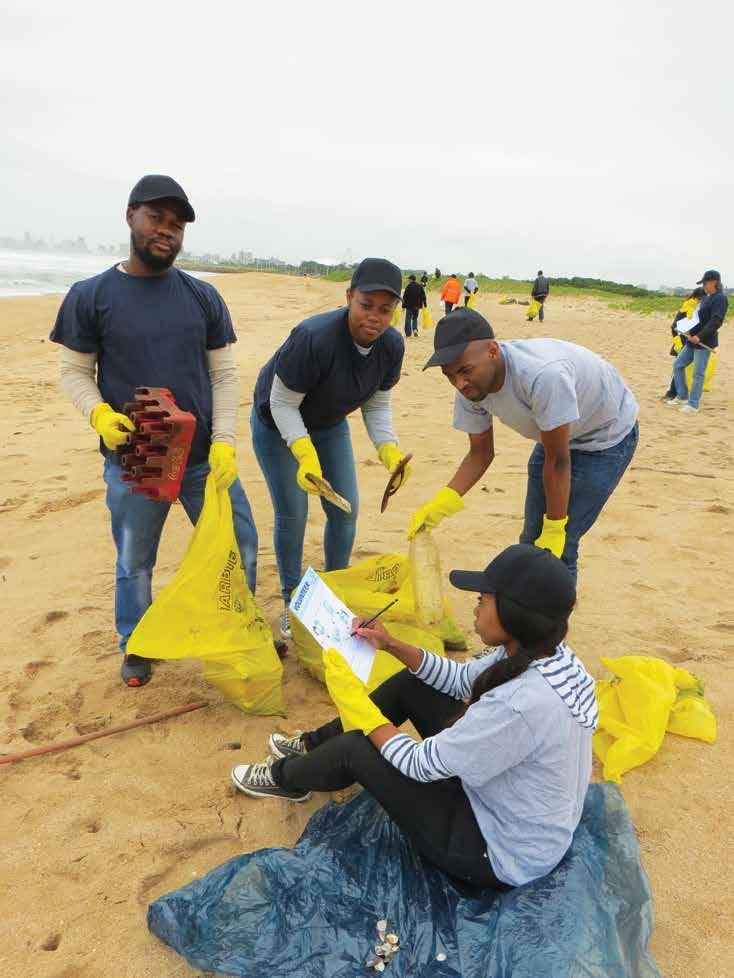
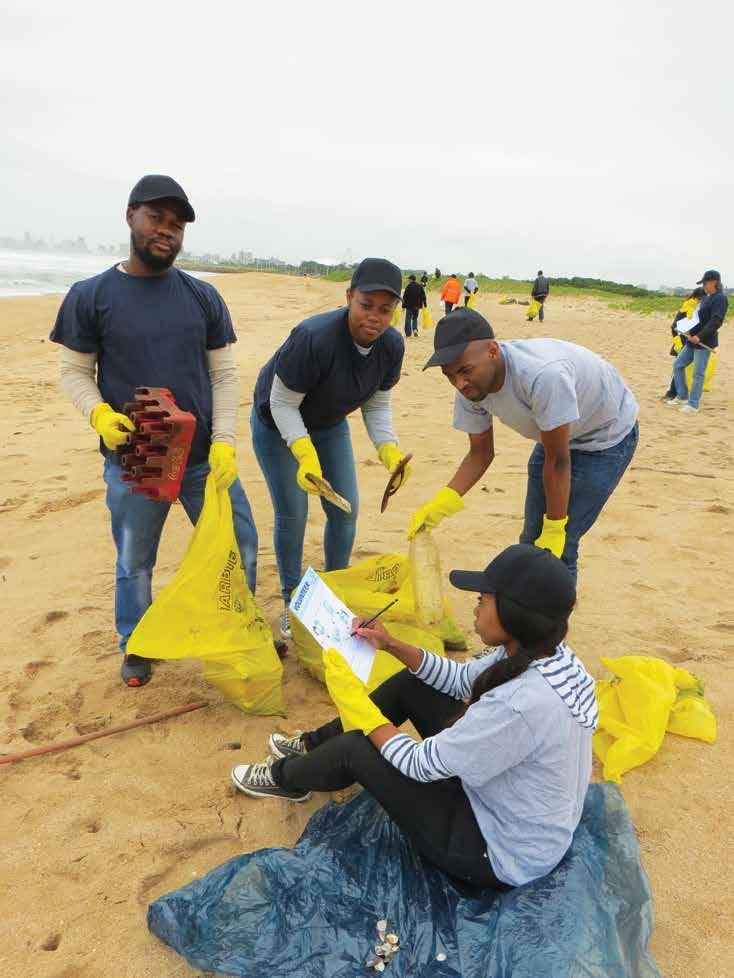
BUILT FOR AFRICA
Truck Traders' four-tonne mini compactors

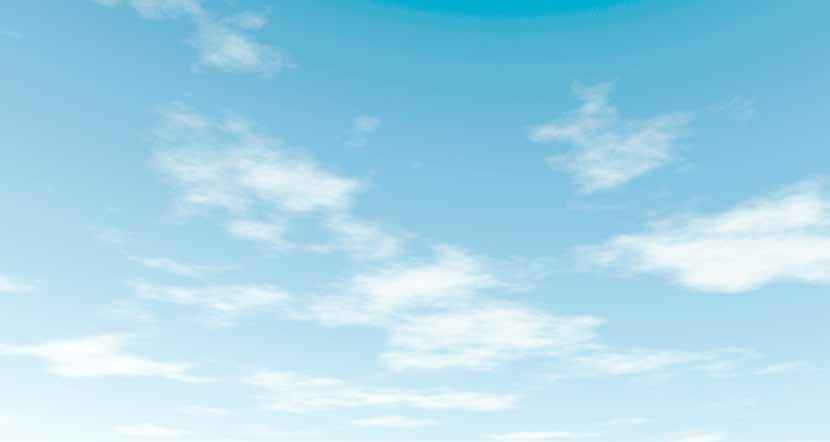
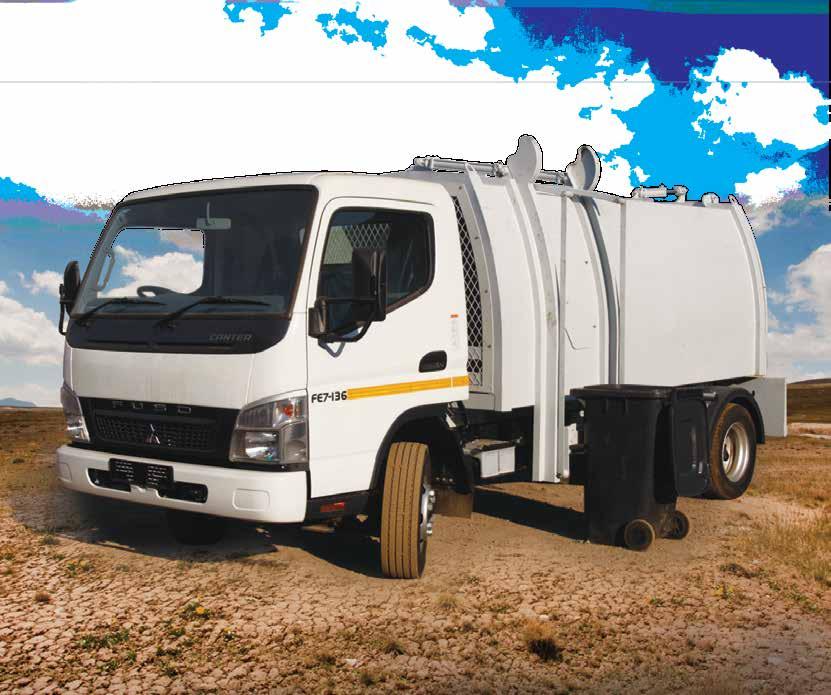
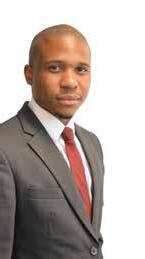
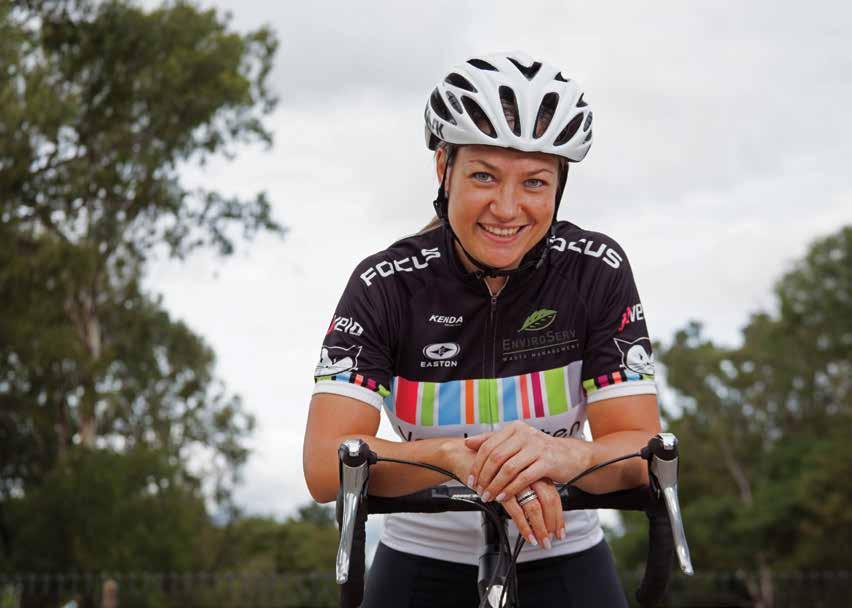
The people keeping it clean
Heavy industry is a critical part of our economy. But disposing of the waste they produce in a way that’s safe for people and the environment takes years of expertise, scientific savvy and biochemistry knowledge.
Not just anyone can do it. That’s why EnviroServ employs qualified professionals for the job.
Like Sales Consultant Yolandi Warmback. A keen cyclist, she’s just as passionate about protecting the planet as you are. Yolandi has participated in five 94.7 Cycle Challenges. She is currently training for the Amashoba Cycling Challenge – a 110 kilometre race in Durban and hopes to this year do her sixth Cycle Challenge in under three hours.
With four years’ experience as a sales consultant at EnviroServ, she’s the right person for this demanding job and takes pride in working for a compliant operation.
Because expertise is one thing, but employees who live the EnviroServ values of passion and integrity are dedicated to working towards delivering waste solutions that are environmentally responsible and effective.
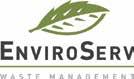
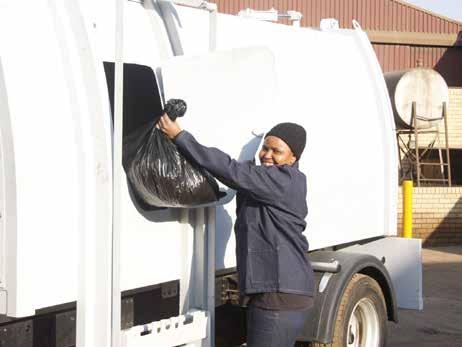
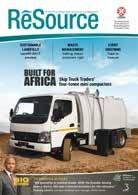
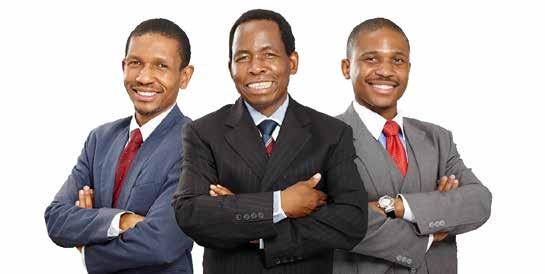
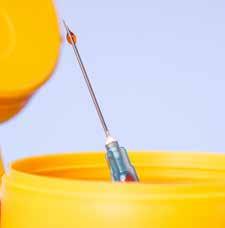
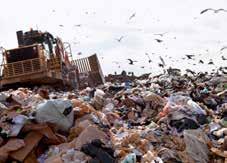
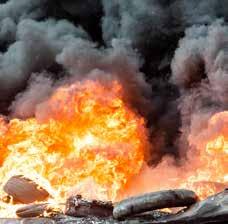
A new mini waste collection vehicle is set to revolutionise urban waste management in Africa through advanced design features and manoeuvrability. John Edwards, MD of Skip Truck Traders, explains what sets these tiny powerhouses apart. P6
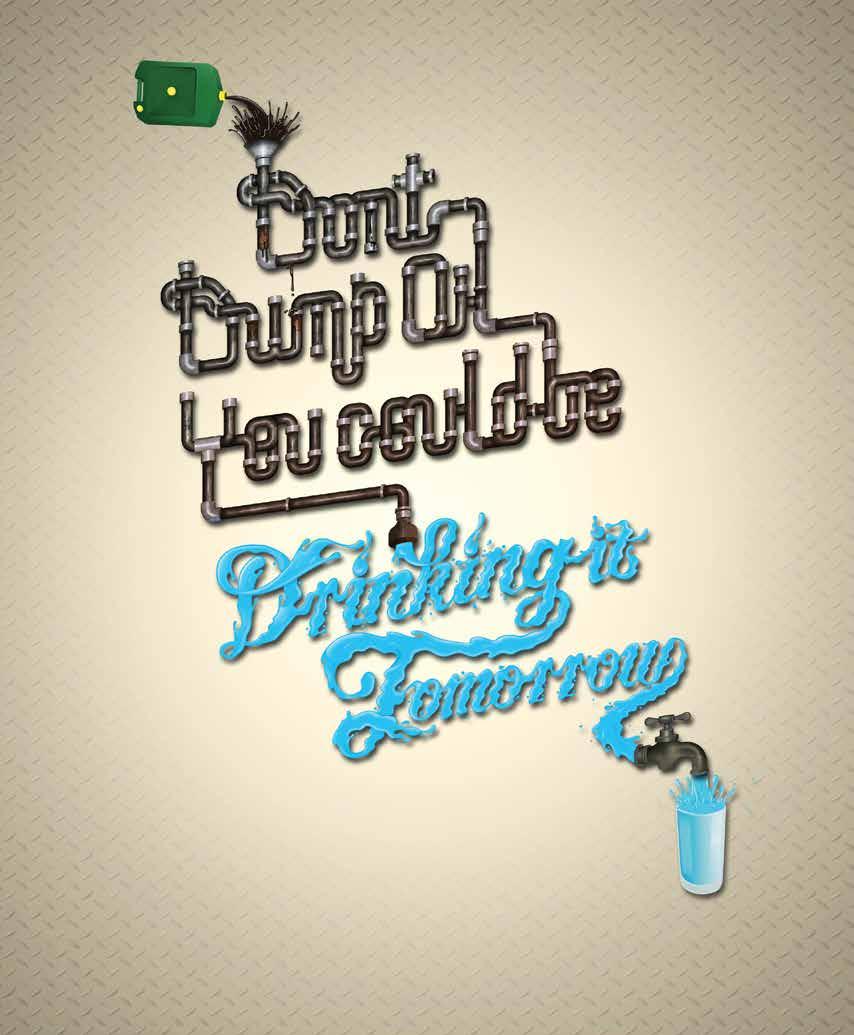

Getting it RIGHT
We are all aware of the legislation controlling the design of landfill liners and of the construction quality assurance effort that is required for the correct installation of those liners.This is all to ensure that the risk to the environment is kept at a minimum. But it comes with a hefty price tag that runs into tens of millions.
Then the landfill starts operating and the only guidelines to assist the operator are the Waste Management Licence conditions and the Minimum Requirements for Waste Disposal by Landfill, with quarterly internal audits and one or two external audits per year. Are these conditions and guidelines followed? Why do we still see large landfills that are poorly operated? Why do we see landfills adjacent to our freeways and in clear view of all road users with vast areas of uncovered waste and windblown litter stuck to the freeway fence for hundreds of meters? Especially when all waste management licences stipulate that waste must be compacted and covered daily? Why do we still see such things in some of our metros?
Sanitary landfills
When witnessing simple conditions like daily compaction and cover material application being ignored, questions are raised immediately about the quality of the groundwater protection and the leachate management system. When are we moving away from dumps to sanitary landfills? What is the point of spending
With World Environment Day having been celebrated in June, it is perhaps appropriate to consider how the waste that we discard impacts the environment.
millions of rands on state-of-the-art basal liner systems when the operation of the landfill is seriously lacking?
When conducting public participation during the licensing application process for the establishment of new landfills, the poor operational standards of existing landfills sustain and support the perception of the public that landfills are dirty and are polluting the environment. For landfilling to be successful, all three elements of landfilling – i.e. basal liner design and installation, operation, and rehabilitation design and installation – need to be successfully implemented.
The right stuff
Waste management licences for landfills should be amended to specify the required experience or qualifications of a landfill operator and the support staff as well as the minimum required landfill equipment. Even though size has been removed from the landfill classification system in the relevant Norms and Standards, size should be a factor when considering the qualification or experience of landfill operators and equipment. Many, maybe even most, landfill operating or supervisory staff are appointed with no prior knowledge or experience in waste management. One of the questions frequently asked
When witnessing simple conditions like daily compaction and cover material application being ignored, questions are raised immediately about the quality of the groundwater protection and the leachate management system
by landfill operators is: “Where can I learn more about landfilling?”
Training courses in waste management are available, both accredited training and Institute-recognised training, which cover a broad spectrum of waste management activities. More details are available at www.iwmsa.co.za.
The Landfill 2017 conference in October will aim to build capacity and technology transfer in the science and practice of waste disposal by landfill.
See you there.
Jan Palm President: IWMSA
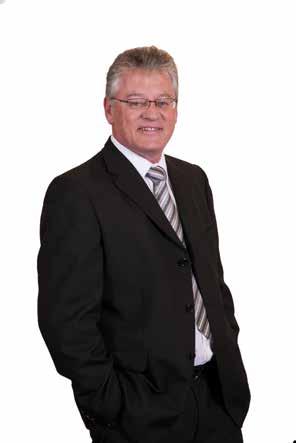

Connect and Create Opportunity
Join the National Cleaner Production Centre South Africa to reduce waste to landfill by enhancing industrial competitiveness and lowering costs through the reduction of materials usage and waste management.
There is mutual benefit in the connections that we make.
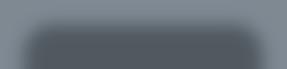
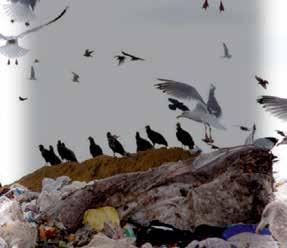
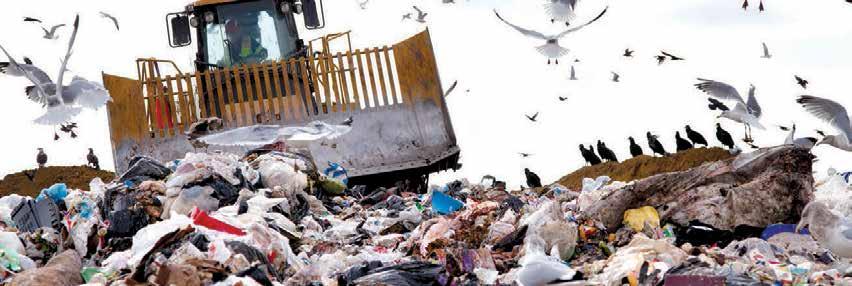
Include the NCPC-SA’s Industrial Symbiosis in your production chain and gain:
What is Industrial Symbiosis (IS)?
IS a resource efficiency approach where unused/residual resources (material, energy, water, waste, assets, logistics, expertise etc.) of one company are used by another. This results in mutual economic, social and environmental benefit.
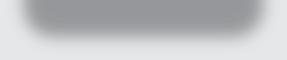
• Profit
• Sales
• Jobs
• Utilisation of assets
• Innovation
• Knowledge transfer
• Transport Increased Decreased
• CO2
• Landfill costs
• Use of virgin resources
• Water usage
• Hazardous waste
The NCPC-SA is a programme of the the dti hosted by the CSIR.
Contact information
Pretoria +27 12 841 3772
Cape Town +27 21 658 2776
Durban +27 31 242 2441
Email: ncpc@csir.co.za www.ncpc.co.za

Publisher Elizabeth Shorten
Managing editor Alastair Currie
Editor Frances Ringwood
Head of design Beren Bauermeister
Design consultant Frédérick Danton
Chief sub-editor Tristan Snijders
Sub-editor Morgan Carter
Contributors Jan Palm, Diedré Penfold, Marilize Worst, Hugh Tyrrell, Oscar Simelane
Client services & production manager
Antois-Leigh Botma
Production coordinator Jacqueline Modise
Financial director Andrew Lobban
Distribution manager Nomsa Masina
Distribution coordinator Asha Pursotham
Printers United Litho Johannesburg
Advertising sales Tazz Porter
Tel +27 (0)11 465 5452
Cell +27 (0)82 318 3908
tazz@connect.co.za
Publisher No.9, 3rd Avenue
Rivonia, 2191
PO Box 92026, Norwood 2117
Tel: +27 (0)11 233 2600
Fax: +27 (0)11 234 7274/5
www.3smedia.co.za
Annual subscription subs@3smedia.co.za
R200.00 (incl VAT) South Africa
ISSN 1680-4902
Institute of Waste Management of Southern Africa
Tel: +27 (0)11 675 3462
Email: iwmsa@telkomsa.net
All material herein is copyright protected and may not be reproduced either in whole or in part without the prior written permission of the publisher. The views and opinions of authors expressed in the magazine do not necessarily reflect those of the publisher, editor or the Institute of Waste Management of Southern Africa.
Copyright 2017. All rights reserved.

A taxing question
The process of manufacturing goods vital to leading a comfortable life is often inherently environmentally unfriendly.
The manufacturing sector is also a job creation powerhouse, boasting a higher job creation multiplier than any other sector. World Bank statistics show that manufacturing makes a 3.4x higher social return for the same private return in mining.
Balancing manufacturing’s social good with its cost to the environment can be a challenge. For some, environmentalism seems like another regulatory hurdle, which appears to be the case in Trump’s USA, given his decision to withdraw from the Paris Climate Agreement. Other nations, however, are embracing the green economy, and new cleaner production and energy-efficiency trends in manufacturing, hailing it as the future of industry.
Politically, South Africa falls into the latter camp, even if, in practice, some industries lag behind.
Given the economic pressures that South Africa has been forced to contend with, the question that arises now is whether South Africa’s environmental policy – which is mostly concretely articulated in its fiscal policy – is supportive of the manufacturing sector.
Packaging and carbon taxes
With the proposed introduction of the carbon tax and the packaging tax, rigorous environmental regulatory measures are in place. The challenge will be for these to be properly implemented. This should mean that at least some portion of the collected funds ought to be reinvested back into the manufacturing value chain. If South Africa is embracing a waste hierarchy where the first imperative is to reduce, alongside a circular economy where manufacturing and a product’s end-of-life are contiguous, then this can be the only conclusion.
When manufacturers are not adequately involved in these processes and targeted financial incentives are not properly disbursed, businesses close and the economy suffers.
In the waste management industry, this point was driven home by the provisional liquidation of the Recycling and Economic Development Initiative of South Africa (Redisa), announced in June this year.
In the waste management industry, this point was driven home by the provisional liquidation of Redisa
Tyre manufacturers were not happy with the plan from its inception in 2012, with concerns being expressed over the plan’s vulnerability to corruption and the briefness of its approval process.
The current economic climate means manufacturers are understandably unhappy about the new taxes. They don’t want to see their money thrown into half-baked plans.
Corruption problem
In spite of these apparent rifts between government and industry, there are many examples of public-private cooperation in the integrated resource management environment. There are many good people from both sides of the divide pouring their energy into making the circular economy concept work.
Corruption counteracts these efforts. When there is a lack of transparency in reporting, the work done towards shoring up the economy is negated.
As above, so below. No environmental programme requiring government input can be successful until the corruption happening at the highest levels is stopped.
Frances Ringwood
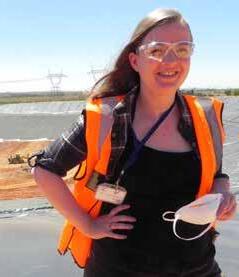











Smaller is better
A new mini waste collection vehicle is set to revolutionise urban waste management in Africa, especially in townships. John Edwards, MD of Skip Truck Traders, explains what makes these four-tonne mini compactors fit for purpose.
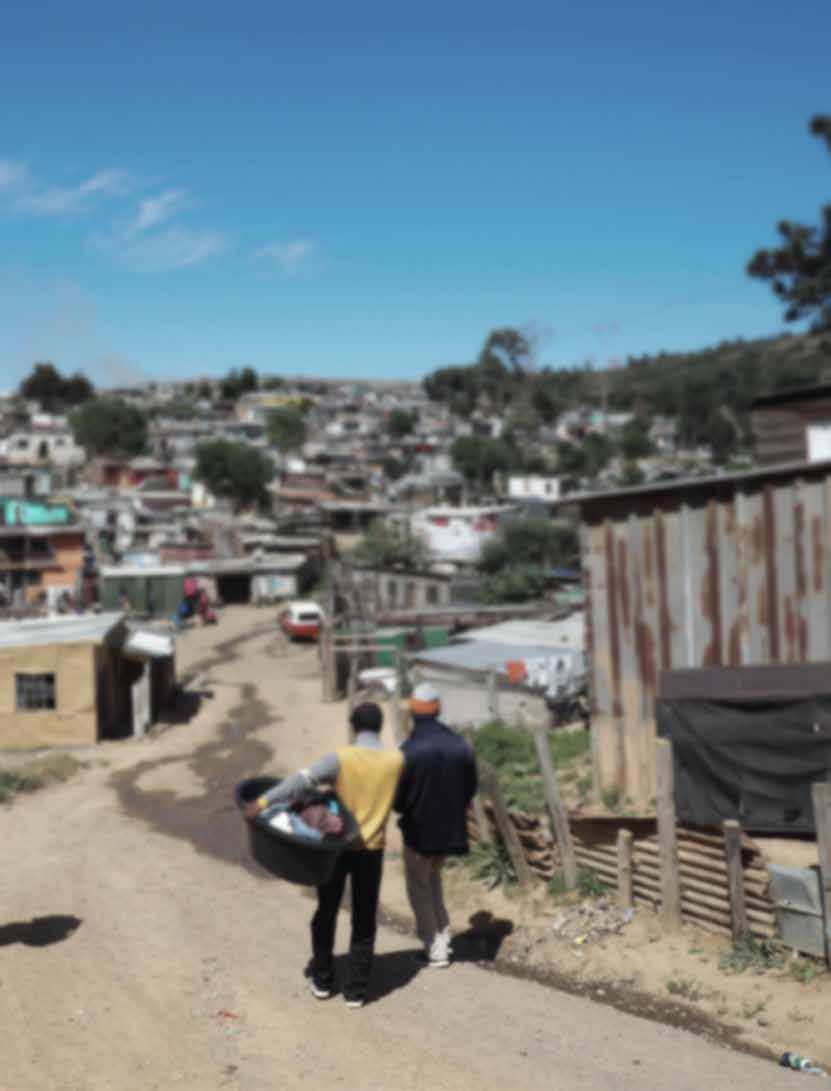
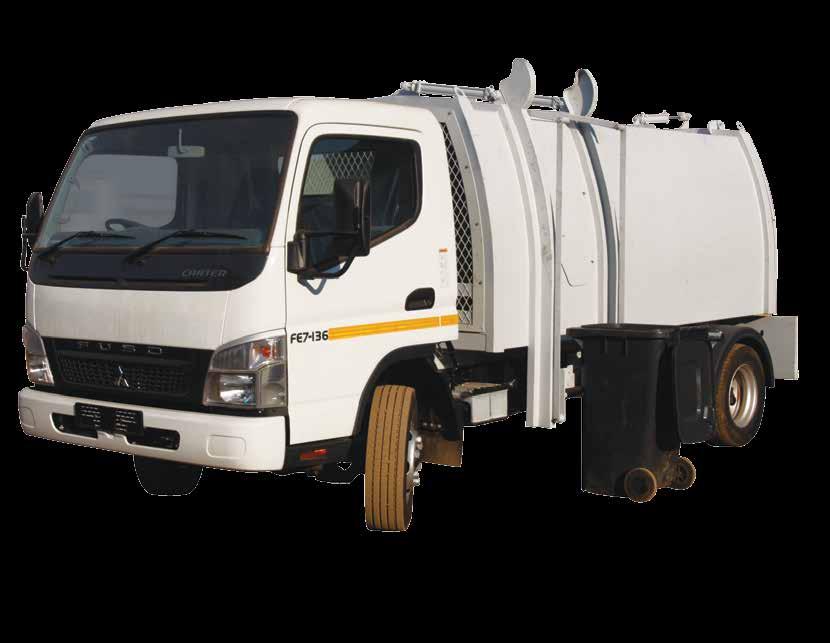
Our new four-tonne mini compactor is designed specifically for waste collection in townships with narrow access roads where manoeuvrability is limited and also other areas such as housing estates where access for large trucks is either limited or not permitted,” says Edwards.
Designed based on the needs of local metros, Skip Truck Traders’ new mini compactor is a side-loader where 240 l wheelie bins are lifted and tipped into an opening at the top of the vehicle. On either side of the unit is a door that is utilised for hand dumping of plastic bags.
The packer blade inside the unit compacts the waste from the front of the unit to the rear using two hydraulic cylinders setup in a scissor format to maximise space. The pressure setting on the hydraulic system is set at 10 bar to allow for partial compaction only in order to eliminate overloading. The back tailgate lifts up and is hinged in the middle for easy unloading.
“The reason for this design, as well as the compactor’s small size, is to allow the vehicle to reverse to the rear of a regular rear-end loader (REL) compactor, then the packer blade is used to push partially compacted waste into the larger vehicle. The waste is then fully compacted into the large REL, accommodating between three and four loads before going to the nearest landfill site for dumping,” says Edwards.
A standard REL can take up to three hours to drive to a landfill, dump its contents and drive back. By having three or four mini compactors offloading their contents into a larger vehicle, the smaller waste collection vehicles are able to keep working whilst the large REL is travelling to the dump site – which results in no downtime.
The other advantage of a smaller vehicle is that it can more easily be repurposed after the end of its prime service life. “There is scope for municipalities to donate these vehicles to com munities for SMME upliftment after a period of five years,” says Edwards.
The
compactor’s design, as well as its small size,
allows the vehicle to be reversed so that its rear meets with the rear of a regular rear-end loader.”
John Edwards, MD, Skip Truck Traders
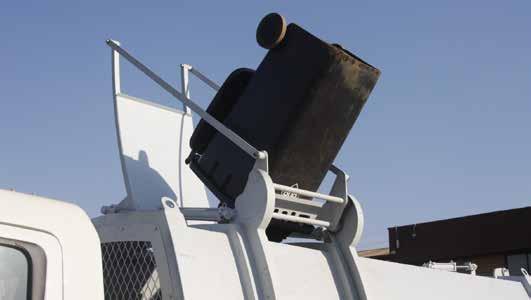
HIGHLIGHTS
• Designed for waste collection in informal settlements and housing estates
• Purchase price is around one-third the price of a regular compactor
• Lower running and maintenance costs
• Can be used for separation-at-source
• No fleet downtime when used in conjunction with a standard REL compactors
• Aligns the clearance distance between mini and
Affordable price
A standard REL will typically cost about R2 million. Skip Truck Traders’ new four-tonne mini compactor costs in the region of R650 000 (including truck), meaning that municipalities can purchase three small vehicles at the same cost as a single large truck.
“The vehicle’s smaller size results in other cost savings as well – these include a two-thirds saving on running costs; smaller and more affordable tyres; a reduced fuel bill; and lower maintenance costs,” says Edwards.
The compactor also comes with the same standard guarantee on all of Skip Truck Traders’ vehicles: “If it breaks down within the first 12 months, we will provide a replacement rental vehicle free of charge for the period that it takes for us to do the required repairs.”
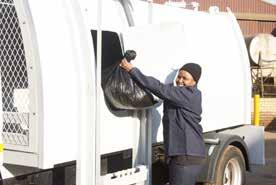
The vehicle could also be used in municipal separation-at-source initiatives, where different waste streams – such as green waste – could be collected and then dropped off at a separate facility not situated at the main landfill.
“One of the design features of the unit is that it does not fully compact the waste, because that would cause it to exceed the vehicles maximum loading capacity. This is calculated based on general waste. Most recyclables are much lighter like plastic bags that can be compacted for optimal loading,” says Edwards.
The mini compactor’s rear is about an inch lower than the rear of a standard REL. To overcome the height difference, a small hydraulic cylinder has been installed to lift the body by about 300 mm, ensuring that the clearances between the two vehicles can be aligned so that waste can be easily transferred from one to the other.
Local manufacturing
nesburg CBD, street sweepers still use plastic bags to collect waste. For this reason, Skip
pactor is designed with side-doors for street
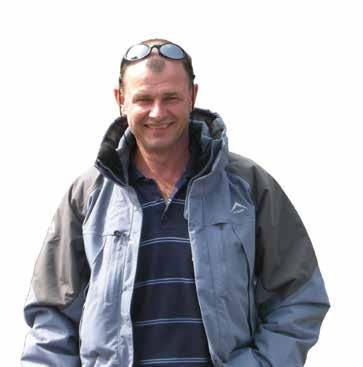
The truck’s lifting system is an all-South African design. “The mini compactor is made in South Africa for Africa,” says Edwards.
Skip Truck Traders has also expanded to begin manufacturing its own cylinders. “We recently purchased a range of fully automated CNC lathes, which produce 100% accurate cylinders to our exact specifications,” he concludes.
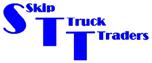
www.skiptrucktraders.co.za
Getting sharps receptacles right
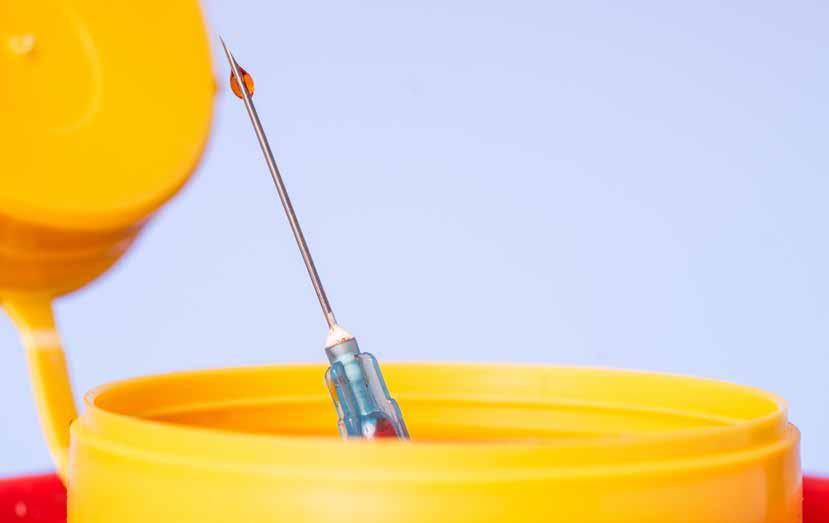
Regulations enforcing the correct composition of sharps containers are there for good reason: mishandling sharps can result in the contraction of infectious diseases such as HIV.
Knowledge is key in protecting the lives of South Africa’s invaluable health workers. By Frances Ringwood
Contaminated sharps pose a risk to the lives of the nurses and doctors who care for the country’s sick and injured. Yet a lack of compliance in the tender documentation process for sharps containers is putting people’s lives at risk.
According to Margaret Lombaard, director of healthcare risk waste canagement (HCRW) company The Waste Wizard, “Staff at healthcare facilities undergo the proper training to be able to identify the correct containers for different types of HCRW. It is a lack of compliance by service providers that puts healthcare workers, visitors, patients and many others at risk.”
Tenders released by public and private hospitals need to comply with the relevant municipal bylaws, as well as provincial and national legislation. In cases where the provincial legislation is not in place, national legislation applies.
Suitable containers
The SABS regulations concerning materials, wall thickness and lid design (among others)
of sharps containers are clear and their testing is rigorous. Yet improper sharps containers continue to find their way into South Africa’s healthcare facilities.
Clifford Durrheim, owner and director of Aids Medical Waste, a company specialising in the supply of medical waste containers, explains that, in some cases, procurement officials are accepting 100% SABS-approved buckets in place of sharps containers.
Visible differences
Comparing a sharps container and a bucket, it is obvious to the naked eye why one is suitable for sharps disposal and the other not. A needle situated diagonally in a bucket could easily penetrate the skin.
By contrast, sharps containers have a lid with a hatch. The hatch can be flipped up and down so that contaminated sharps can be deposited without the lid being removed, preventing airborne infectious agents (microorganisms including bacteria, mycobacteria, fungi, parasites or viruses) from escaping. Those are just the cosmetic differences. Other factors, like the type and thickness of plastic used also play a role in safety. Buckets are much cheaper and made of thinner plastics. A further factor lowering costs is the type of plastic used. The SABS standards dictate the exact types of high-density polyethylene and polypropylene that may be used in the manufacture of sharps containers.
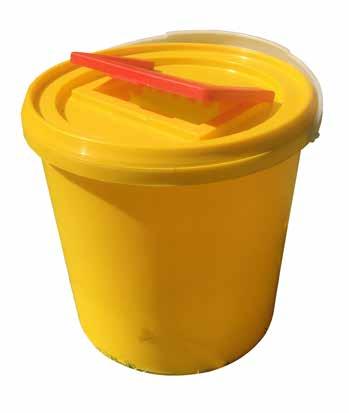
A legally compliant sharps container
“Certain plastics are specified because of the way they react to lower temperatures. Plastics breathe – that is, they expand or contract when exposed to high or low temperatures. When the incorrect plastic is used – especially where fillers have been added to make fabrication cheaper – there is a high risk of cracking
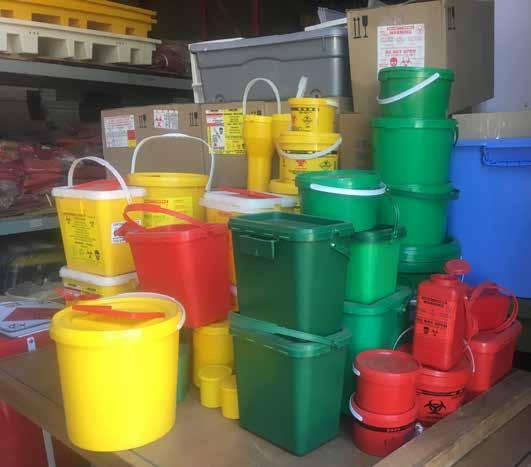
Different HCRW containers used in hospitals are colour coded so that the proper procedure is followed for each waste stream. Yellow is for sharps, red is for infectious human waste and green is for chemical and pharmaceutical waste
when the bins are stored below a certain temperature,” Durrheim explains.
He adds that a further problem introduced by the way plastic breathes is that the bins’ actual molecular structure causes them to retain biological contaminants.
This is why sharps receptacles, as well as sharps, are classified in the relevant legislation as “sharps waste”– requiring disposal that is fully compliant with the law. At issue here is that it’s not only the plastics used in the wrong sort of HCRW containers. “At least two unscrupulous manufacturers
that I am aware of are making cheap sharps containers by using fillers and blended plastics,” says Durrheim.
Legal compliance
The primary technology used in South Africa for handling HCRW is incineration. Other technologies like autoclaving, hydroclaving and microwaving are some of the processes approved by the Department of Environmental Affairs.
“It is illegal to reuse or recycle sharps containers,” Durrheim explains.
Consequences of not following proper HCRW procedures:
• Lack of control over the trafficking of human waste and body parts
• Pharmaceuticals past their sell-by date are being illegally retained and sold cheaply by hospital staff
• Biohazardous spills are being improperly cleaned
“Given the current state of the country’s hospitals – where I have seen buckets being used to transport pathological waste, where spills clean-up crews in hospitals are improperly protected with the incorrect spill clean-up kits and personal protective equipment, and where vehicles are not properly cleaned after internal spills have occurred – I feel strongly that extreme caution needs to be exercised when we talk about recycling plastic HCRW,” he adds.
Systemic issues
The problems in South Africa’s hospitals are tied to larger systemic issues experienced around the country. Government corruption and incompetence and an embattled economy have emboldened certain parties within the HCRW supply chain to believe they can disregard the law.
In light of these challenges, the waste management industry needs to present a united front when it comes to legal compliance, the safe disposal of HCRW and working towards the safety of human lives and health. Given the seriousness of the consequences, should incorrect procedures be followed, healthcare facilities and their waste management companies must have checks and balances in place to ensure that no internal cost-cutting or corruption that might endanger human lives occurs.
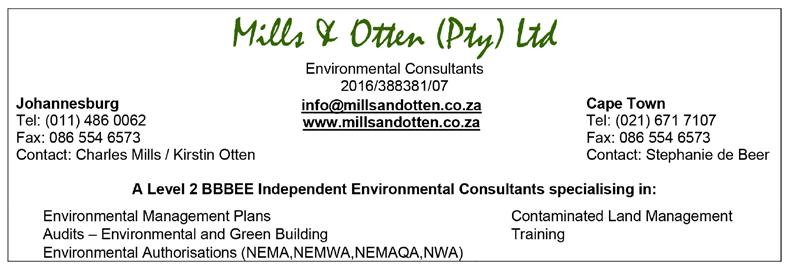
Reducing waste at work
Waste. It’s everywhere and, regardless of modern technology, human society doesn’t seem to be producing less of it. It has been there since the earliest days and no doubt will follow humanity into the future. By Deidré Penfold*
High-paced technological and industrial progress is the main source of the accumulation of hazardous materials. For the Chemical and Allied Industries’ Association (CAIA), hazardous waste is a pressing concern.
Hazardous waste from the chemical industry includes materials that could be corrosive, inflammable, explosive, or react when exposed to other materials. Some hazardous wastes are highly toxic to the environment and its flora and fauna.
Since hazardous waste contains organic or inorganic elements, or compounds that may – owing to the inherent physical, chemical or toxicological properties of that waste – have a detrimental impact on health or the environment, it must be handled with caution and be disposed of at authorised hazardous waste management facilities.
In South Africa, Responsible Care® is a registered trademark of its custodian, CAIA, and undertakes to promote the responsible handling of
chemicals throughout their life cycle, including waste management. Responsible Care® is the chemical industry’s own, unique, global initiative – a voluntary programme that helps it to raise its standards and win greater trust from the public.
Waste management benefits
During the past five years, South Africa’s waste management industry has witnessed updates to the National Environmental Management: Waste Act (No. 59 of 2008). Proper and professional waste management practices are advocated, and the implementation of environmentally conscious waste management operations is required of all organisations dealing with waste. However, reducing waste can be costly and take up a significant amount of time and resources. It is, therefore, necessary to consider the benefits:
All industries find that using more efficient manufacturing processes and better materials will generally
• It enhances companies’ image, attracting new employees as well as customers; customers prefer to do business with companies that are environmentally friendly.
• It saves money on supplies and waste disposal costs.
• It reduces clutter in factories, improving worker safety and the working environment.
• It reduces companies’ environmental impact.
• It increases employee morale; employees take pride in working for a company that takes its social and environmental responsibility seriously.
• It’s cost-effective: waste materials can be used again in new products instead of ending up in landfills where they generate harmful gas emissions.
All industries find that using more efficient manufacturing processes and better materials will generally reduce the production of waste.
Action plan
Companies and the people who staff them can play a huge role in reducing waste by recycling –not only by initiating a recycling plan but also by influencing the behaviour of customers.
This can be achieved by nominating a workplace recycling ambassador. Encouraging colleagues to get serious about recycling will translate into much wider benefits for all.
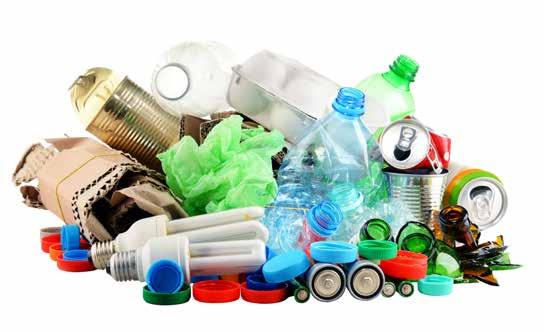
Whether it’s around the water cooler or during a strategy session, employees need to take the opportunity to discuss how to start implementing recycling ideas and programmes at work.
By reaching out to management about getting the message across (through newsletters, posters or brochures, for example), each of us can make difference.
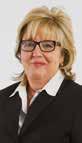
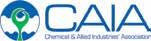

*Deidré Penfold is the executive director of the Chemical and Allied Industries’ Association.
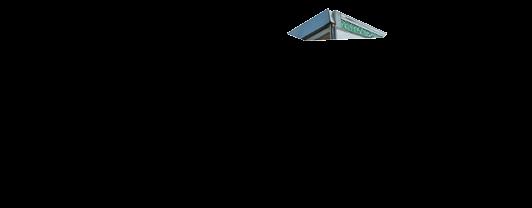

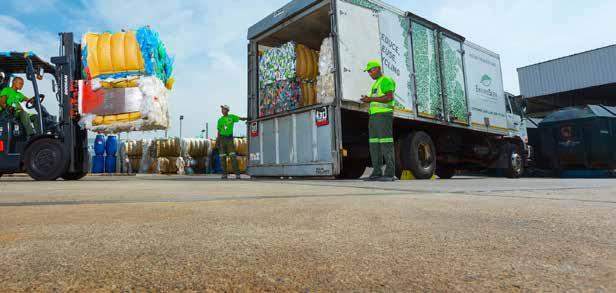
Minimising waste to landfill with recycling solutions
In the very competitive waste market, EnviroServ is always looking for innovative, compliant and affordable landfill alternatives to offer clients and grow the business.
Effective on-site waste management services benefit customers across all industries,” says Juan-Mari Davies, projects manager: On-site Waste Management, EnviroServ.
“On-site service offerings become the centre of integrated waste management solutions and ultimately the reason why we keep on winning new business.
“Our customers are demanding a one-stop-shop solution and a number of new business contracts won in recent months are a result of dedication, passion, planning and attention to detail.”
Waste hierarchy
The company implements awareness programmes for clients to prevent the generation of waste and promote reuse instead. “We also perform food waste recycling for composting and have solutions that cater for small waste producers such as offices with canteens, restaurants or larger producers such as hotels.”
The goal is to assist customers in going green and moving up the waste hierarchy.
Hazardous bulbs
Fluorescent tubes and lamps and energy-efficient lighting contain mercury and, thus, need to be handled and recycled according to legislative requirements. Davies says, “It is estimated that a single fluorescent tube has enough mercury to contaminate 30 000 ℓ of water.”
EnviroServ has specially designed fluorescent tube boxes and bags for the temporary storage of spent lamps and offers peace of mind and a guarantee that all hazardous lamps are handled, transported and recycled correctly.
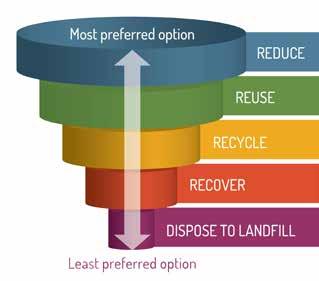
Zero waste
Another green solution is the waste-toenergy project.
“Last year, EnviroServ joined forces with the Bronkhorstspruit Biogas Project, known as Bio2Watt, to enable us to provide a comprehensive, legal and affordable zero waste solution to our customers,” says Davies.
Bio2Watt is the leading industrial-scale biogas waste-to-energy company in South Africa, using organic waste to create a renewable energy source. “EnviroServ takes a waste stream, which might have been landfilled, analyses it and, if it is suitable, takes it to Bio2Watt. A growing number of clients are finding this solution useful. It is cheaper than landfill and more environmentally friendly,” she adds.
On-site offering
In June, 72 employees were deployed at three sites in South Africa to turn waste back into valuable resources using conventional recycling solutions, composting and waste-to-energy.
According to Davies, about 5% of this client’s waste is sent to landfill and there is a zero waste to landfill target set for 2019. Another significant win for EnviroServ’s on-site team saw 25 new sites added. The contract consists of on-site, general waste and safe disposals of off-spec food and pharmaceutical waste.
“Growing accounts is also a strength, and one customer who has merged well with our operations has grown from 1 site to 13 additional sites in just 12 months,” says Davies, adding that the success of this account was based on providing the client with a compliant on-site solution, reacting quickly to their needs and
providing them with a clear picture of waste generated by the group. “On-site has become a new trend in waste management, and is an excellent way not only to win new business but, more importantly, to sustain clients,” he adds. EnviroServ uses specialised equipment to separate waste from its packaging, both solid and liquid. The packaging is then sent for recycling and the organic contents go to a biogas facility. Davies explains, “This means both the contents and packaging are diverted from landfill by implementing an on-site waste solution, which speaks to our goal of trying to recycle as much as we can.”
Waste recycling operations through on-site waste management create jobs, primarily for small business owners who trade in recyclables.
Education and awareness
EnviroServ also plays a role in educating tomorrow’s leaders with its School Recycling Programme. “Dedicated to raising awareness and the promotion of recycling in schools, the programme highlights alternatives to traditional disposal methods and aims to reduce the amount of waste to landfill. We hope that, by the end of our visit to a school, we will have contributed to creating a generation of environmentally conscious citizens,” concludes Davies.
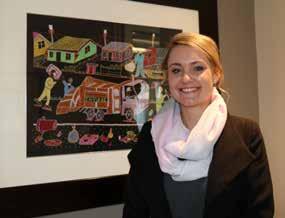
Juan-Mari Davies, projects manager: On-site Waste Management, EnviroServ
Landfill 2017 will be held at the Buffelsdraai Regional Landfill, in the town of Verulam, 27 km north of Durban on 18 to 20 October this year. The biennial conference is held alternatingly in one of South Africa’s three main business capitals, Johannesburg, Cape Town or eThekwini. The theme for the conference is ‘Back to Basics’.
LANDFILL 2017 What to expect
Landfill 2017 will be the first ever South African waste management conference to be held on a live landfill. This not-to-be-missed event will showcase landfilling best practices as well as the basics for legal compliance.
Logan Moodley, senior engineer at Durban Cleansing and Solid Waste (DSW), and chairperson of the KwaZulu-Natal Landfill & Waste Treatment Interest (LaWTIG), explains the decision behind holding the conference at a working landfill, as well as the theme choice.
Landfill venue
“Traditionally, the event has always been in hosted in a well-equipped conference venue, which was good. However, this time around, the local KZN organising committee wanted to bring a landfill to the delegates. As a result, the event will be held on a major landfill – the Buffelsdraai Regional Landfill,” explains Moodley.
Given the site’s close proximity to King Shaka International Airport and surrounding accommodation, the event will provide delegates with both
comfort and convenience while they hear talks from leading local and international specialists.
“The unique location will also provide those from local municipalities with hands-on experience of all facets of landfilling, from engineering design and construction, to operations and best practices,” says Moodley.
Schoolroom-type seating has been arranged at Buffelsdraai Landfill’s Education Centre, capable of accommodating some 130 delegates. However, exhibition, networking and catering areas will be hosted in an outdoor exhibition marquee.
Programme and papers
The three-day programme can accommodate up to 20 papers.
“The programme also allows for delegates to view interactive exhibitor demonstrations or otherwise visit selected areas of interest at the site. These include our leachate treatment, waste disposal operations, landfill gas flaring, and more,” says Moodley.
Keynote address
The keynote speaker is Kelvin Legge, chief engineer of DSW: Engineering Services, and his topic is entitled ‘Lessons Learnt from 1 000 Design Reviews: Raw Truths & Blatant Lies’.
“The presentation comprises a regulator’s perspective of commonly repeated deviations from accepted norms and standards in the engineering profession as they apply to pollution control facilities.
“Criticisms of the regulatory process and responses will be recorded. Emphasis will be placed on the standards of today, with a review through the lens of experience of the past 1 000 design reviews through selected case histories,” says Moodley.
“The presentation will conclude with observations and recommendations for facility owners and practitioners,” he adds.
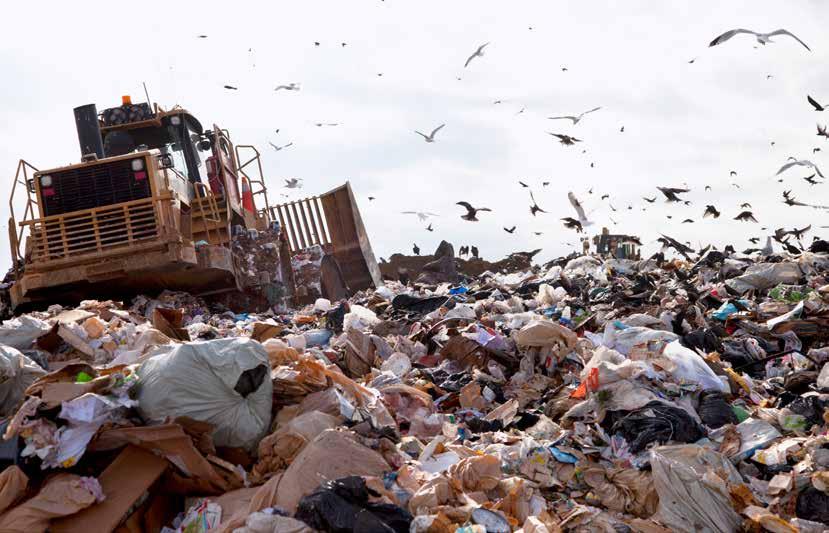
The conference will take place at a live landfill
The presentation promises to chal lenge perceptions and beliefs about waste behaviour and pollu tion control barrier performance, using scientific By attending presentations such as this, landfill own ers and operators will learn how professional con duct enhances revenue generation in the service provider
Sponsorship opportunities
“The organising committee has se cured its main sponsorship from Bell Equipment/Bomag,” says Moodley. Bell will be given a display area on-site, providing delegates with the opportunity to test typical landfill plant equipment first-hand, as well as conducting demonstrations.
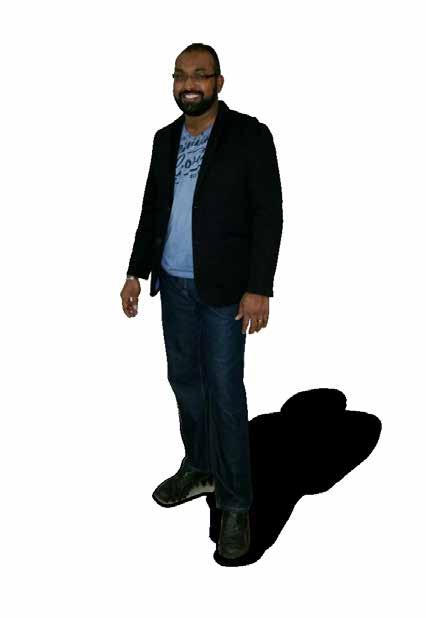
At the time of writing, various other sponsorship opportunities were still available. Those interested to contact the IWMSA’s LaWTIG Division straight away to
Fifteen spaces have been identified for the exhibition and all spaces have been filled. “Interesting to note is that at least a third of the exhibitors are international enterprises,”
LANDFILL 2017 Where
Buffelsdraai Regional
When 18 to 20 October
Keynote speaker
Kelvin Legge, chief engineer of DSW
Main sponsor
Bell Equipment/Bomag
Traditionally, the event was hosted in a conference venue. However, this time, the organising committee wanted to bring a landfill to the delegates. As a result, the event will be held at The Buffelsdraai Regional Logan Moodley, senior engineer at DSW and chairperson of LaWTIG
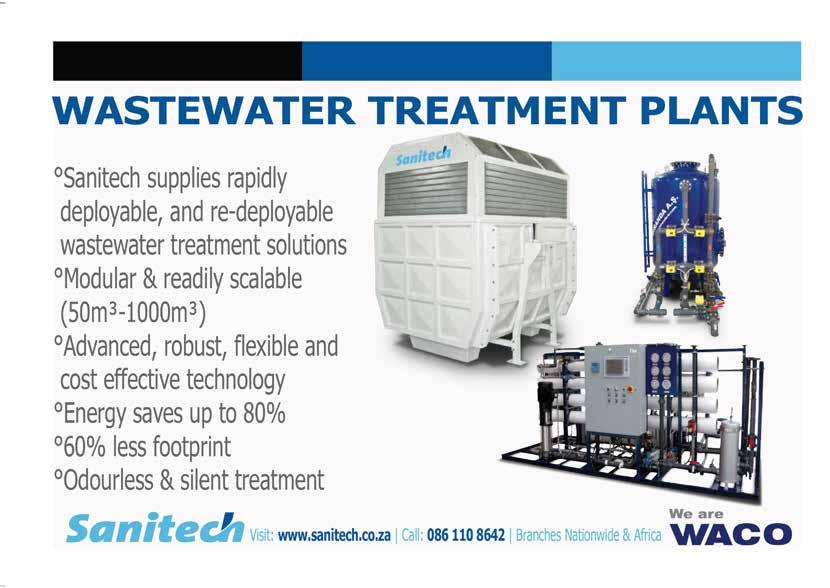
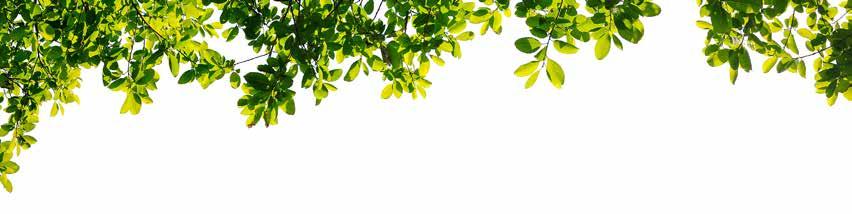
BUHLE WASTE (PTY) LTD
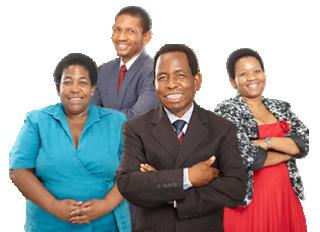
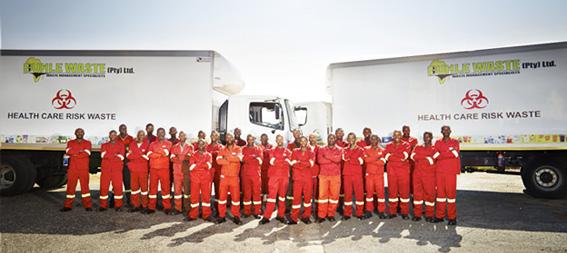
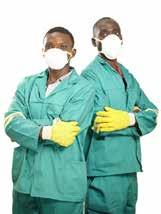
D I S P O S A L S
BUHLE WASTE is a 100% black-owned and -managed company focusing on integrated waste management services throughout Southern Africa.
Collection, transportation, safe treatment and disposal of:
• Healthcare Risk Waste
• General, Domestic Waste
• Hazardous Waste
• Industrial, Commercial waste
• Industrial Cleaning
• Emergency Spill Response
We also provide:
• Scanning and Tracking of Waste Product
• Emergency Response Spillage Kit
• Waste Collection Receptacles
• Waste Disposal Certificate
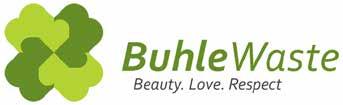
• Putting people first
• Excellent healthcare and hazardous risk waste management
• Environmentally friendly waste treatment technology
• Scanning and tracking waste products
• Comprehensive and accredited onand off-site training for clients’ staff
• Issuing of Waste Disposal Certificates
1634 Canon Crescent, Roodekop, 1401 t 011 866 2316 f 011 866 2321
Info@buhlewaste.co.za
www.buhlewaste.co.za WHAT SETS US APART?
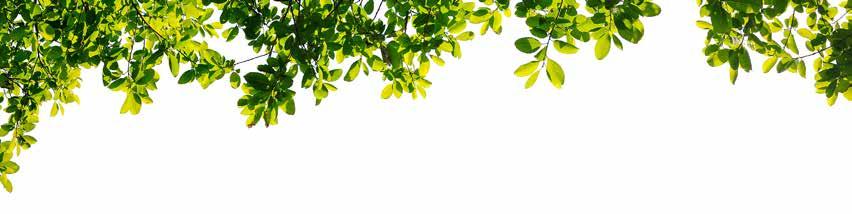
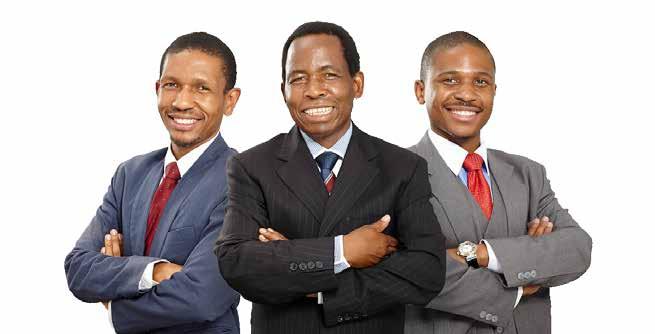
This year, Buhle celebrates its 20th year. How did the company come about?
HEALTH FIRST
Founded by a medical doctor who wanted to improve his township patients’ health, Buhle Waste has its roots in healthcare, and so it was only natural that it should grow to become a leading medical waste management company. Thabang Sekete, business development manager, tells the story.
TS The company was founded in 1997 after medical general practitioner Dr PD Sekete realised that many of his patients in the townships of what was then the East Rand (now Ekurhuleni) were falling ill as a result of poor waste management services. This was and unfortunately continues to be the norm in many informal settlements.
He decided that rather than working in a curative capacity, he could do more good by taking a preventative approach. After purchasing a couple of skip trucks and finding partners with skip waste management experience, Buhle Waste was formed. Soon after, the City of Ekurhuleni began supporting grassroots, black-owned companies and Buhle was awarded its first tender to collect general domestic waste door-to-door in township areas like Katlehong and Vosloorus. It also managed waste from a small number of mini disposal sites.
What are Buhle’s current achievements and scope?
Today we have a national footprint, with about 72 trucks in operation.
Our staff complement numbers more than 350 people and our collections are no longer limited to general domestic waste.
Our main areas of operation are Gauteng, the Free State, Mpumalanga, Limpopo and the North West. We also have operations in KwaZulu-Natal and the Eastern Cape, and are currently in the process of establishing a Western Cape branch. While we do not have a branch in the Northern Cape, we operate in the area through smaller satellite offices.
Buhle Waste’s services have grown to include chemical, hazardous and industrial waste, as well as waste from construction sites and manufacturers. In addition, we also offer industrial cleaning and hygiene services. However, we specialise in medical waste. With the founder having been a doctor, this was a natural evolution for the company.
Through this specialisation, we have gained a number of notable clients, including the Provincial Departments of Health in Gauteng,
We specialise in medical waste. With the founder having been a doctor, this was a natural evolution for the company.”
the Free State, Mpumalanga and Limpopo.
To date, we have purchased an incinerator in Benoni and an advanced converter sited in Seshego, Limpopo.
What are Buhle’s plans for the future? We are
working towards a vision where Buhle Waste will send zero waste to landfill by 2025. This will be achieved through the use of our converter’s neutraliser technology, which was developed in Italy.
A normal incinerator releases toxins into the atmosphere, which poses challenges for environmental regulators like the Department of Environmental Affairs. The converter substantially mitigates risks to the health of surrounding communities and the environment, while also saving on water and energy use.
It uses only five to six litres per 30-day cycle and demonstrates energy savings of about 30% compared to other technologies, including incineration, autoclaving and microwaving.
Not only does this green technology reduce waste by about 70% in terms of volume and 60% in terms of weight, it can also be geared to convert waste to biogas. We are hoping to begin a pilot, towards the middle of next year, for turning the remaining waste into biofuel. This is an extremely exciting development for us and we are proud to have brought the technology to South Africa.
Nkoko Sekete, regional manager
Dr PD Sekete, founder
Thabang Sekete, business development manager
BUFFELSDRAAI The future for eThekwini
Boasting a landfill footprint size of 100 ha, Buffelsdraai
Landfill is set to take over as the main landfill for eThekwini, with the closure of the Bisasar Road site and the imminent closure of Marianhill Landfill.
Commissioned in May 2006, Buffelsdraai has a design life of 75 years, providing landfill airspace to eThekwini Municipality until 2080 and beyond. Buffelsdraai Landfill is classified as a G:L:B+ landfill, therefore the only waste accepted is general municipal solid waste (MSW). FCE was
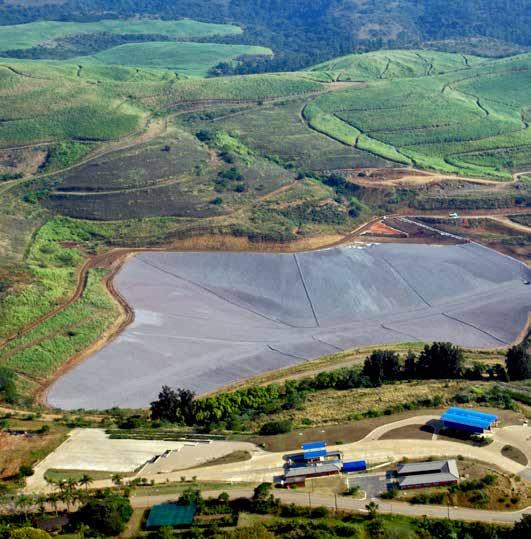
involved in the construction of the landfill, which was designed according to the requirements and policies of Durban Solid Waste. The lining of the base and basin comprise various compacted clay layers with the side slopes having a geosynthetic clay liner, 150 mm clay protection layer, separation geotextile and a leachate drainage layer.
Plant at Buffelsdraai Landfill
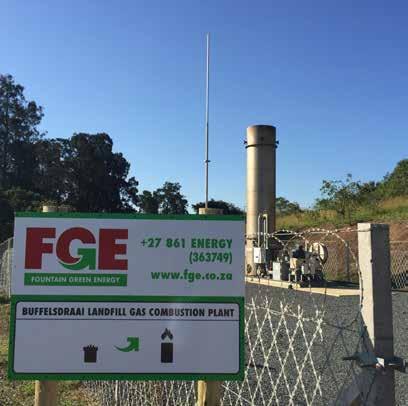
Liquids management
The contaminated stormwater dam has a valve outlet and stored effluent will be monitored. If the quality of the effluent is acceptable, it will be released into the environment. Alternatively, dependant on the level of contamination, it will be used for irrigation of sugar cane or removed for treatment at the plant or off-site.
Collection of the leachate is done through a stone drainage layer between the waste body and the lining
system. The leachate is drained via two 160 mm pipes, through a penetration in the stability berm and is contained in a leachate contaminant area. A two-pipe system was adopted in the basin to prevent blockages and to facilitate the separation of leachate and stormwater during the initial filling of the cell. A leachate detection system of 150 mm HDPE drainage pipes was constructed under the base preparation layer.
Landfill gas
Landfill gas is a form of renewable energy that is produced from the decomposition of the organic fraction of municipal solid waste within the waste body. Landfill gas predominantly consists of carbon dioxide and methane, with smaller amounts of water vapour and organic compounds. Global warming potentials (GWPs) classify the impact a substance will have towards global warming compared to that of carbon dioxide. According to the UN Framework Convention on Climate Change, methane has a GWP of 21, which is an indication of how severely the gas impacts global warming in comparison to carbon dioxide. This indicates the importance of monitoring and extracting it. FCE installed a flare to destroy the effects of the methane, which will be extracted through a blower, under negative pressure, in a small compound on the landfill. The plant is operated and monitored via a Scada system in a small control room. Landfill gas quality and flows are monitored in order to better understand the
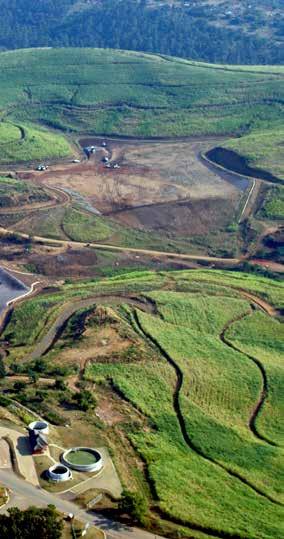
Benefits of extracting landfill gas
Odour Landfill gas has an unsavoury odour that could be carried with a strong wind, affecting surrounding communities. Controlled extraction of the gas limits the quantities available to be transported, improving landfills’ public image.
Safety The heterogeneous nature of waste within a landfill, high temperature within the waste body, and daily site operations can cause a fire to ignite on a landfill. By extracting landfill gas, the presence of fuel to generate large fires or explosions is limited.
Reduction in landfill volumes Due to the fact that the landfill gas has mass, it must also have volume. Extracting the gas reduces the volume of waste on the landfill, thus increasing airspace and the lifespan of the landfill.
landfill gas composition, ensuring its effects can be better controlled while also optimising resource utilisation.
The landfill gas at Buffelsdraai Landfill is extracted through a network of horizontally laid, perforated HDPE pipes known as gas wells. The system forms part of an active landfill management strategy. These horizontal wells lead to two manifold header stations where condensate within the gas falls out of suspension due to the change in flow rate of the gas, and a temperature drop from the warmth
within the landfill to the cooler ambient environment outside. The suction pressure within the 250 mm diameter carrier lines (from the substations to the compound) is maintained through the action of the blower.
Environmental rehabilitation
With the current state of waste management in South Africa depending heavily on landfills, steps need to be taken to alleviate the stigma associated with these facilities. Projects such as Prunit (where plants are grown in nurseries
Specialist Waste Management Consultants
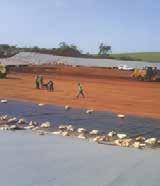
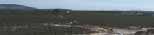
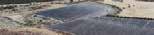
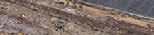
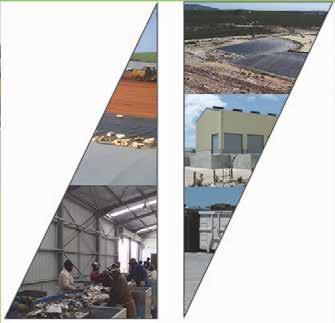
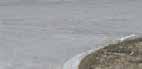
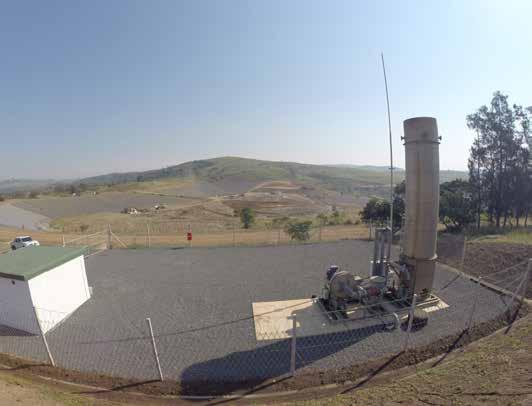
and then relocated to rehabilitate landfill sites) and the Buffelsdraai Community Reforestation Project implemented by the eThekwini Municipality aim to increase any biodiversity that was destroyed in constructing the landfill. This is achieved by both planting flora and relocating fauna within the buffer zone of the
landfill, which will, in turn, increase the wildlife within the area.
These projects also assist with social upliftment for the local community through job creation and a cleaner, healthier environment – as well as improve the visual impact of the landfill.
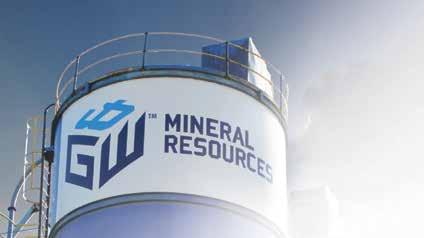
Reducing climate impacts
Landfill gas is an inevitable by-product of the landfilling operation and, like it or not, is here to stay. Landfill managers can choose to leave it and let it vent, or use this resource for energy production, reducing the demand on fossil fuels. The minimisation of global warming is one of the single most important responsibilities in history and it has fallen to today’s waste management professionals to do something about it. It is, therefore, important for each individual to play their part by mitigating risks related to climate change and look towards a cleaner, greener future.
FCE has established itself as a leading landfill gas contractor in Southern Africa, having been involved with landfill gas projects throughout South Africa, principally in the Eastern Cape, Western Cape, KwaZulu-Natal and Gauteng. The company specialises in anaerobic digestion, biogas-to-electricity and biogas upgrading for the production of biomethane and carbon dioxide.

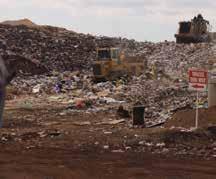
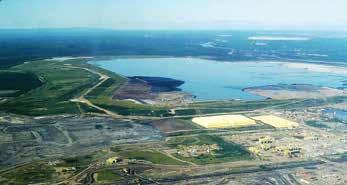

Ethically environmental
Two quotes from Mahatma Gandhi highlight the ethical principles that motivate Engineered Linings (EL), says Hein Jansen van Vuren, business development and marketing manager at EL, a division of PSV Industrial.
The first is: “The earth, the air, the land and the water are not an inheritance from our forefathers but on loan from our children. So we have to hand over to them at least as it was handed over to us.” The second is: “There is a sufficiency in the world for man’s need but not for man’s greed.”
Human and environmental health
EL specialises in the supply and installation of geomembranes and other geosynthetic products for the purposes of containing potentially corrosive or otherwise polluted substances, protecting groundwater and the environment.
“We strive to supply and install the best geosynthetic lining material for our clients for various containment structures, whether it be for mines, landfills, industry or agriculture. We do not compromise on quality and refuse to allow greed or the competitiveness of the market sway us to specify or install products that could result in potential failures that will be detrimental to the protection of human health and the environment,” says Jansen van Vuren.
“Our staff are committed in providing a safe and
We strive to supply and install the best geosynthetic lining material for our clients”
Hein Jansen van Vuren, business development and marketing manager, EL
healthy environment not just for ourselves but also for those to follow in years to come.”
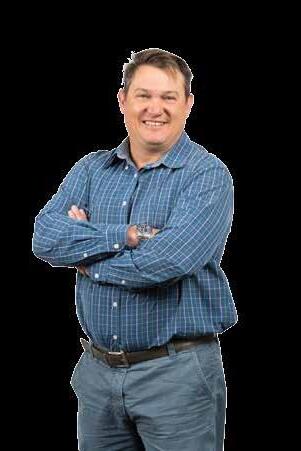
New Johannesburg office
EL started operations in 1984, and since then has installed over 50 million m2 of geomembrane material throughout Africa.
It originally had Johannesburg and Cape Town offices but, in 2015, the Johannesburg office closed so that the company could concentrate on projects in the rest of Africa.
“Now, we are reopening our Johannesburg office so as to concentrate on the business opportunities throughout the Free State, North West, Limpopo, Mpumalanga and, of course, Gauteng,” says Jansen van Vuren.
EL will continue developing new ways to improve the quality of the environment and the sustainability of scarce water resources.
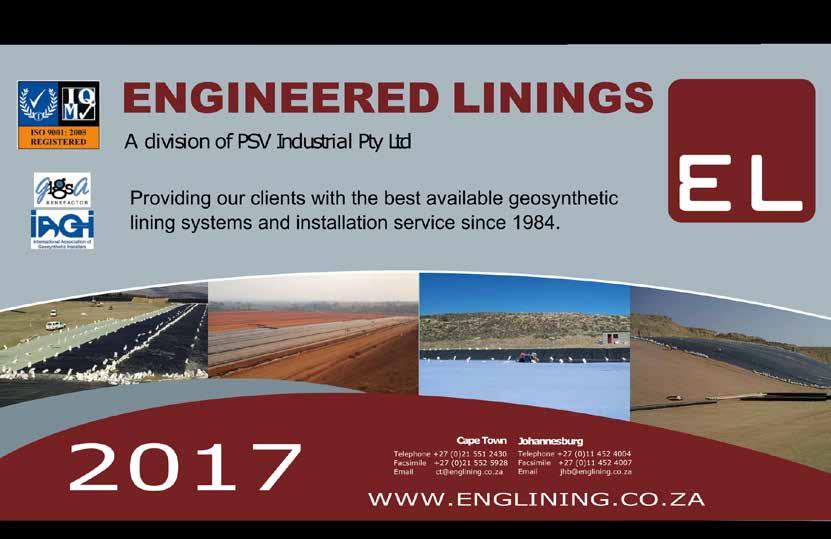
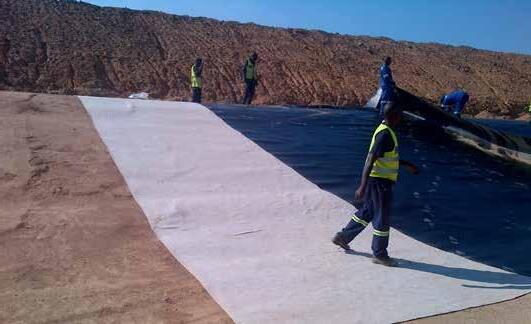
Tomorrow’s liners today
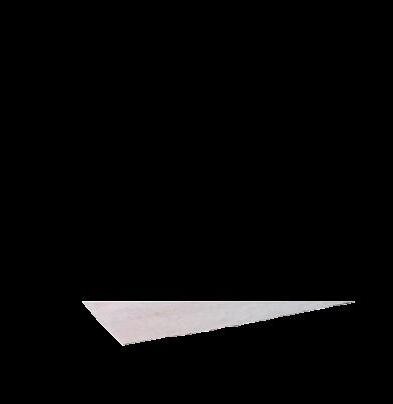
As design engineers encounter new and demanding site conditions, so geosynthetic lining technology develops to anticipate exactly how to deal with the specific challenges of every site effectively. To this end, geotextile company Fibertex SA distributes a wide range of cutting-edge Naue Geosynthetics products, including the trademarked Bentofix and newly launched Bentofix X range of geosynthetic clay liners (GCLs).
Designed for use as efficient sealing barriers in a range of diverse applications, including landfill projects, Bentofix GCLs are needle-punched, reinforced composites that combine two durable geotextile outer layers and a uniform core of high-swelling powder sodium bentonite clay. This forms a uniform, multidirectional,
shear-resistant hydraulic barrier, with self-sealing and re-healing characteristics.
Improved performance
Bentofix GCLs are used as a replacement for conventional compacted clay layers and when hydrated with water, the bentonite swells and forms a low-permeability gel layer, with improved hydraulic performance over traditional, thick compacted clay liners. The needle-punched process and Thermal Lock manufacturing technology increase the internal and external shear strength of GCLs, creating a single, engineered barrier that utilises the best of both synthetic and natural materials and expands the range of applications in which GCLs can be used.
“The Bentofix GCL product is particularly well suited for use in the composite liner and capping systems of landfills, as well as in cut-off trenches and other installations where a reliable barrier system is required,” says Darryn Meisel, national sales manager, Fibertex South Africa. “Bentofix X GCLs represent the latest advancements in GCL products, where the woven geotextile is coated with an additional, low-permeability polyethylene (PE) layer to achieve an immediate barrier prior to hydration. With the additional bonding of a PE coating, the fibre reinforcement
“The Bentofix GCL product is particularly well suited for use in the composite liner and capping systems of landfills, as well as in cut-off trenches and other installations where a reliable barrier system is required.”
is also more permanently locked and further increases the pullout resistance, as well as the internal shear strength of the GCL.
“Bentofix X also enhances the available factor of safety and confidence in products and their applications for design engineers,” he adds.
Application range
Bentofix X GCLs can be installed where a prompt barrier against gas and radon is necessary, where desiccation needs to be permanently avoided, and where protection against root penetration is specifically required. Other applications are where erosion of the bentonite due to high water heads must be avoided and where a supplementary barrier against critical liquid migration is required.
The outer surface structure of the additional PE coating varies according to the thickness of the coating and provides for higher interface friction angles and stability in steep slope applications. This is ideal for maximising the capacity of landfills.
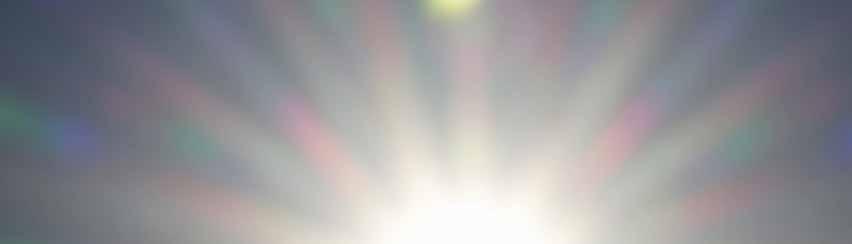
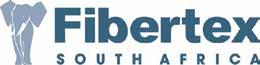
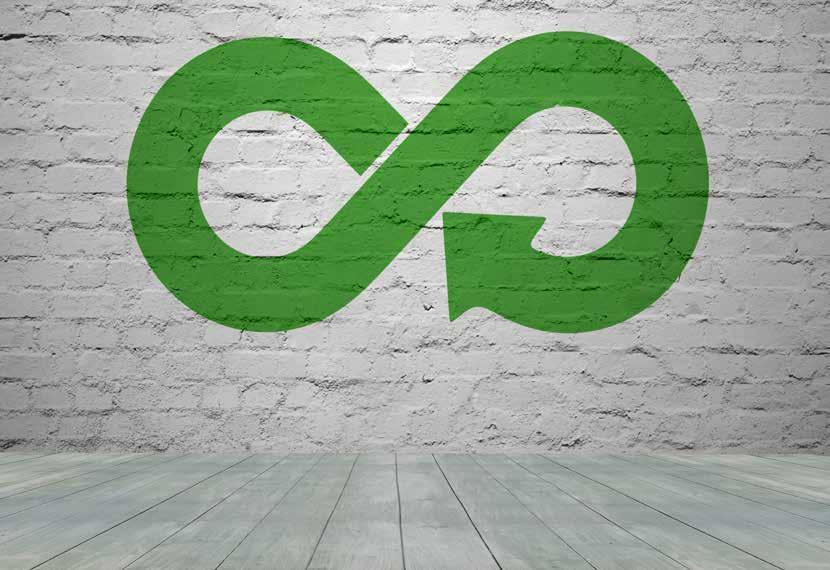
Closing theloop
While many countries have embraced the circular economy, drastically reducing waste to landfill, establishing and developing end markets can still be a challenge. Here is how the local and international vinyls communities are finding solutions.
By Frances Ringwood
This June, leading vinyl experts from around the world gathered at the Hilton Hotel in Sandton for the Vinyls SA Conference, hosted by the Southern African Vinyls Association (SAVA). Environmental sustainability and social responsibility featured high on the agenda, with presentations covering the circular economy, stewardship programmes, and SAVA’s own initiative to recycle non-hazardous healthcare waste, among others.
Dr Brigitte Dero, general manager of the European Council for Vinyl Manufacturers and VinylsPlus, delivered a presentation on Europe’s
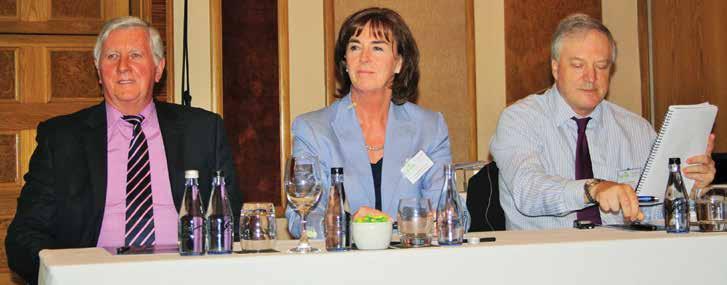
Left to right: Ian Lilja, managing director, Sun Ace South Africa; Brigitte Dero, general manager, European Council for Vinyl Manufacturers and VinylsPlus; and Nigel Sarginson, product stewardship and regulatory affairs manager at ExxonMobil
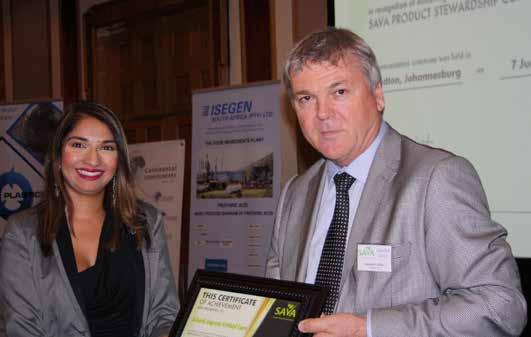
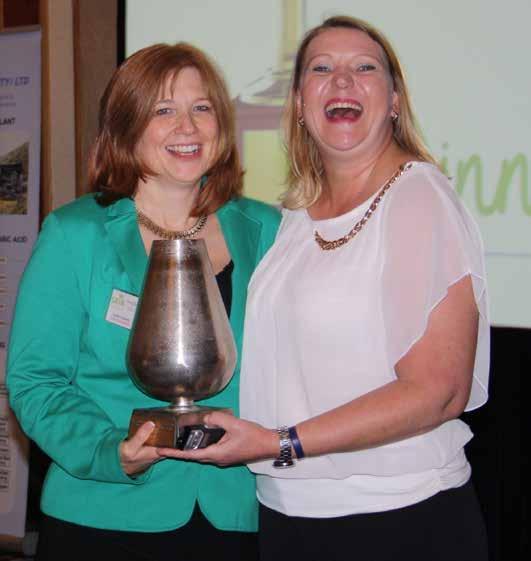
regulatory and policy environment. In it, she emphasised the EU’s Plastics Strategy, which aims to provide a comprehensive plan outlining how plastics should be designed and manufactured sustainably by the end of 2017.
“Much of the discussions around sustainability have been driven by non-governmental organisations (NGOs) who find the concept of a circular economy highly attractive. Different
‘The New Plastics Economy: Catalysing Action’ (2017), takes a hard line against vinyls, saying that “recycling is yet to grow up” and, therefore, recommends that manufacturing using vinyls and other “uncommon plastics”, like polystyrene and expanded polystyrene, should no longer be used in packaging materials.
The reason given for this stance: “Even very small concentrations of PVC lead to significant quality reductions in recycled polyethylene terephthalate (PET).”
“By sorting the reusable PVC fraction out from the healthcare risk waste fraction, the cost of managing this waste stream can be significantly lowered and savings can then be spent on special bins or personnel training.”
Delanie Bezuidenhout, CEO, SAVA
Another reason why PVC is criticised by some environmental organisations is that some legacy stabilisers and phthalates (plasticers that make PVC flexible) include heavy metals and toxic chemicals – these are being phased out under current EU environmental laws.
Dero contests that a blanket dismissal of PVC is unreasonable, given its often overlooked environmentally friendly characteristics. “PVC is a low-carbon plastic, meaning it is not as dependent on fossil fuel feedstocks for its production as other plastics. Additionally, nearly 600 kt of PVC was recycled in 2016 – meaning the equivalent of 30 000 trucks of PVC waste was diverted from landfill in one year.”
Further, there are comprehensive certification mechanisms in place for determining the toxicity of legacy additives in PVC products, even tracing imported products’ certification. One of the websites providing this service in Europe is www.eucertplast.eu.
End-market development
Where does the recyclate go? Dero states, “Knowing your end markets is always important.” Common examples include window profiles, flexible PVC products for road equipment (e.g. traffic cones and plastic speed bumps) and products used in urban agriculture. The latter application requires proof that there is no migration of additives to farmers’ produce.
NGOs are calling for different levels of regulation, and it’s important that the vinyls sector makes itself an active player in these debates,” says Dero.
Circular economy
The most influential NGO with regard to the circular economy is the Ellen MacArthur Foundation. One of the foundation’s published reports,
“Even more impressive, we have made headway in the medical sector. We have 10 hospitals participating in the UK.”
Australian example
Ian Lilja, managing director of Sun Ace South Africa, is also a prominent member of the Vinyl Council of Australia. His presentation outlined PVC stewardship strides in Australia. Briefly, the Vinyl Council of Australia’s stewardship
Tandy Coleman, CEO of Polyfloor, receives the Innovation in Recycling Award from Delanie Bezuidenhout A special
programme is 15 years old and rests on five pillars: best-practice manufacturing, safe and sustainable additives, energy and greenhouse gas management, resource efficiency, and transparency and engagement.
Apart from gaining new signatories to the PVC stewardship programme and improving the environmental performance and product profile of PVC, Australia’s PVC recycling initiatives are also realising success in the healthcare sector.
“We started in 2009 and, today, have more than 50 hospitals on board,” says Lilja.
Local success
Delanie Bezuidenhout, CEO of SAVA, delivered her presentation on the South African PVC industry’s extended producer responsibility. Part of her presentation included an update on SAVA’s own bold initiative to introduce green healthcare at private hospitals. Specifically, this means recycling non-hazardous healthcare PVC from IV bags, tubing and breathing masks and turning it into school shoes.
“My interest in minimising healthcare waste started before I was a member of SAVA, when I was a hospital patient and I witnessed the high volumes of waste being thrown away,” says Bezuidenhout.
After developing the idea over many years, SAVA now has a pilot project with six private South African hospitals. “Our feedback from healthcare waste management companies has been cautiously optimistic. We started rolling the project out to two hospitals at the end of last year and we aim to have no fewer than 20 hospitals on board by the end of this year,” says Bezuidenhout.
Through this initiative, non-risk healthcare waste PVC is separated into blue bins called confidential reputation (CR) bins so that it can be recycled. Statistical results from the first two participating hospitals reveal the following:
“Of the 864.9 kg of potentially recyclable material that was collected at Hospital A via the CR bins, 730.8 kg (85%) was recycled and 118.5 kg (14%) was placed in the healthcare risk waste bin.
“Of the 1065.8 kg of potentially recyclable material collected at Hospital B, 407 kg (38%) was recycled and 623.6 kg (59%) was placed in the healthcare risk waste bin.”
Hospital A proved to be a highly successful case study.
On the other hand, Hospital B exhibited a high contamination rate. It also used IV bags made from layered low-density polyethylene, which is why recycling rates were lower. “This gave us the opportunity to explain that PVC IV bags are highly recyclable and this influenced their procurement policy so that they now purchase more PVC IV bags. The wards where contamination occurred were also easy to trace, so we could then go into those wards and retrain staff,” explains Bezuidenhout.
Cost benefits
Waste management costs for healthcare risk waste are high – up to R20/kg as opposed to normal waste management, which is less than R2/kg. “By advising hospitals that they can minimise their waste management costs, we are not advocating the kind of irresponsible cost-cutting that leads to illegal dumping and other unlawful practices,” assures Bezuidenhout.
“By sorting the reusable PVC fraction out from the healthcare risk waste fraction, the cost of managing this waste stream can be significantly lowered and savings can then be spent on special bins or personnel training. We have, therefore, proved that this model is economically viable in that it is either cost neutral, or it saves participating healthcare facilities’ money,” she concludes.
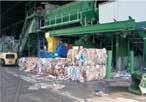
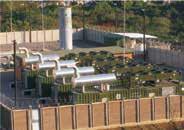
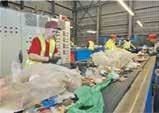
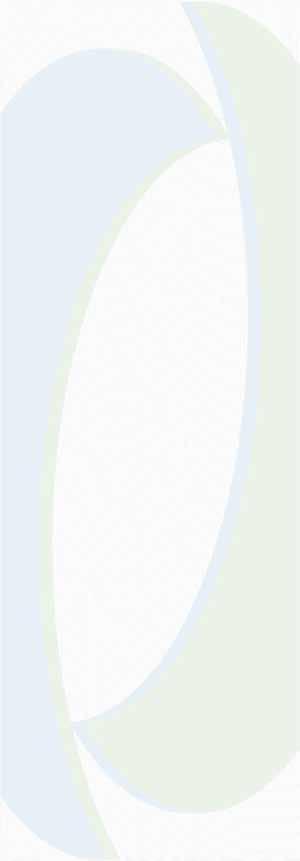
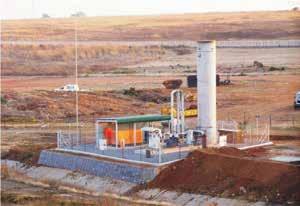
GRAPH 1 The Vinyl Council of Australia’s programme milestones – ongoing improvement

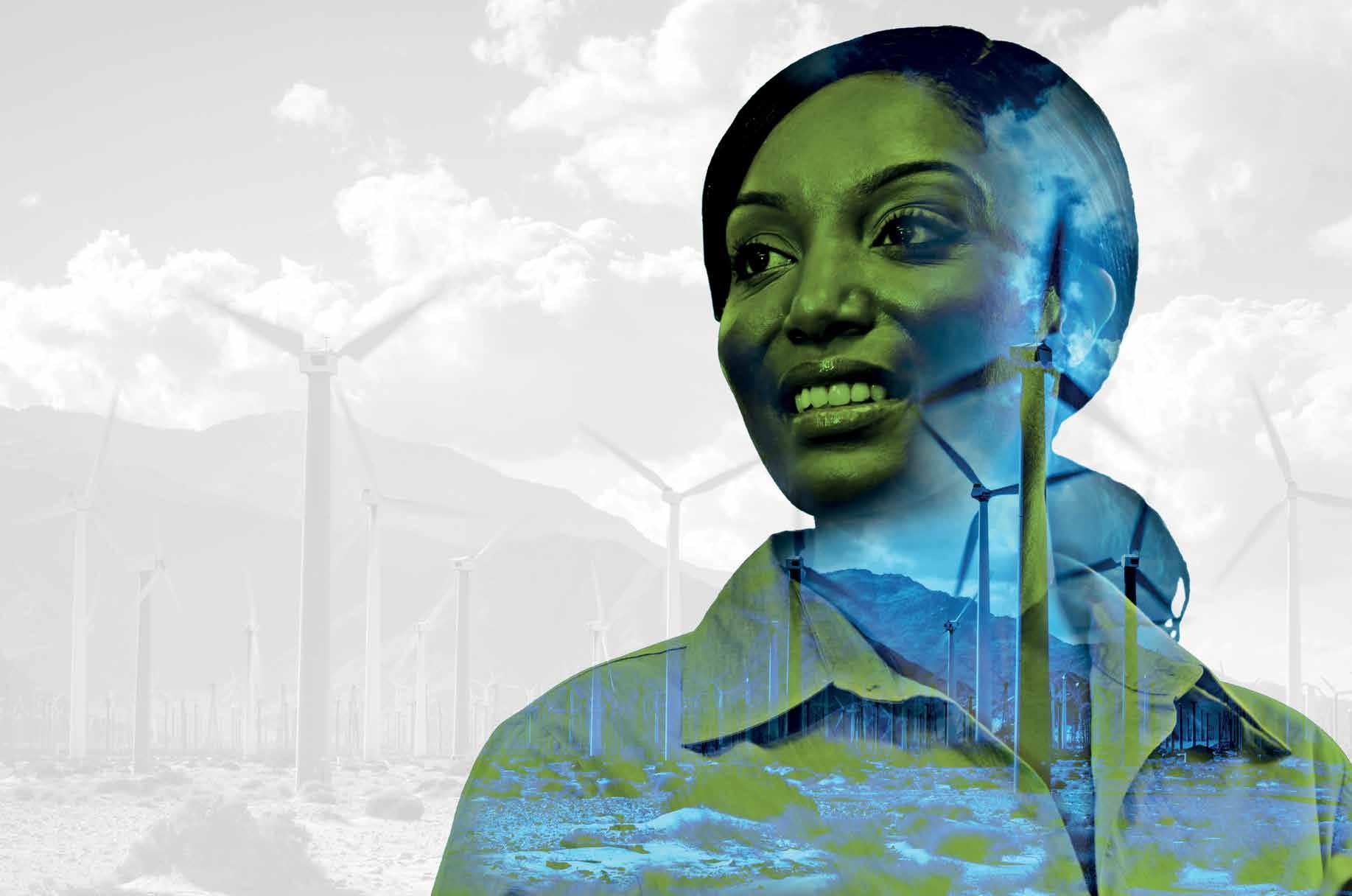













































Leaders are recognising that geopolitical stability and economic growth are intrinsically linked to sound environmental practices – and that ignoring scary statistics is grossly irresponsible. From an industry and private sector point of view, business leaders are under increasing pressure to ensure that they follow sound environmental best practices – or risk severe reputational and financial damage in the long term. In response to the many prods towards sustainability within business and industry, the concept of zero waste to landfill has become paramount.
While it is undoubtedly an ambitious goal (particularly in the local context), business leaders and policymakers need to begin to adopt strategies and processes that take the country closer to zero waste to landfill.
In South Africa, the major barrier to achieving zero waste to landfill is a lack of waste-to-energy plants. Generally speaking, countries close to this goal have access to advanced technology and infrastructure that enables incineration and co-processing, by way of example. Locally, coprocessing is the only currently viable technology, with pyrolysis (decomposing waste by high temperature) technology slowly gaining traction.
The three Rs
Given the local technology and infrastructure restraints, SmartMatta’s zero waste to landfill
ZERO waste to landfill MATTERS
Around the world, environmental sustainability has become a hot-button issue. If Southern African countries are ever to achieve these lofty goals, local innovation will be key.
By Marilize Worst*
solution takes a multifaceted approach, focused on the following: reduction, reuse and recycling – and finally energy recovery through co-processing or other technologies.
In our view, zero waste is not a single exercise, but an iterative process. Waste should
“ZERO WASTE is a goal that is both pragmatic and visionary, to guide people to emulate sustainable natural cycles, where all discarded materials are resources for others to use. Zero waste means designing and managing products and processes to reduce the volume and toxicity of waste and materials, conserve and recover all resources, and not burn or bury them. Implementing zero waste will eliminate all discharges to land, water or air that may be a threat to planetary, human, animal or plant health.”
Zero Waste International Alliance
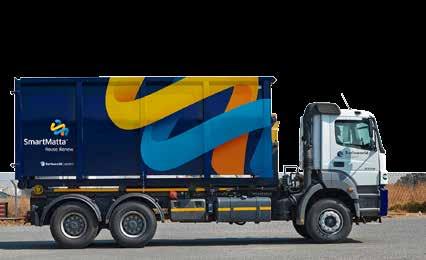
be targeted in a systematic manner to recover all recyclables, and to remove materials that can be reused – thus working towards a sustainable zero waste target.
With the above in mind, we adopt a process-driven approach to clients. Our goal is to re-engineer processes, reduce waste, reuse and recycle waste streams, and recover energy, thereby eliminating waste to landfill sites.
Internal Innovation
As it stands, we believe that the traditional waste hierarchy does not place sufficient responsibility on the waste generator (or client) to innovate internally before the generation of the waste stream. Indeed, moving waste up the hierarchy contributes to the principles of a circular and green economy, by way of:
• reintroduction of resources back into the economy
• contribution to economic growth and job creation
• reducing social and environmental costs
• promoting system effectiveness. Looking ahead, we suggest that there are three critical elements to a sustainable waste management plan: innovation – which focuses on understanding the clients’ processes and how the waste is generated; reduction of the waste – taking a systems approach to minimising the amount of waste generated; and reuse and recycling – which refers to all solutions in place for alternative uses
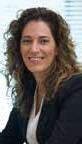
Getting logistics right is an integral part of achieving zero waste to landfill
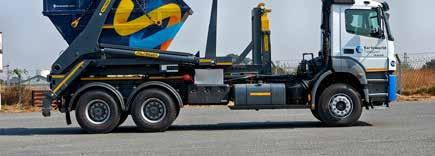
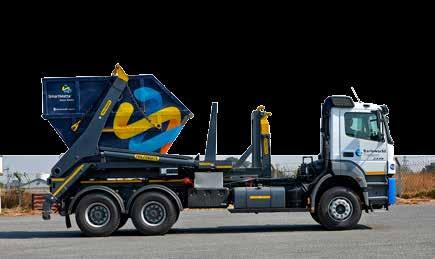
*Marilize Worst is the managing director of SmartMatta, a part of Barloworld
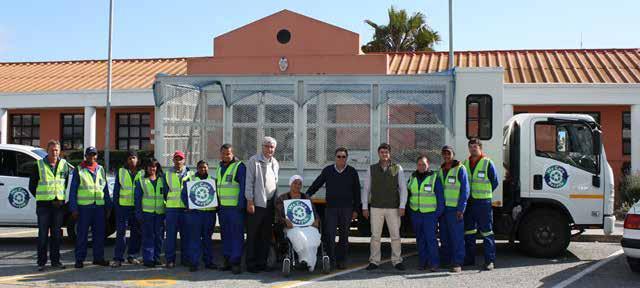
The Saldanha Bay Municipality Household Recycling Project CASE STUDY
Within eight months of the launch of a recycling separation-at-source service at Langebaan in Saldanha Bay, nearly half of the households had started participating. This was partly achieved by using the psychology of recycling to guide public education and the communications campaign that supported it.
Saldanha Bay Local Municipality on the West Coast of South Africa includes resorts, industrial and commercial areas surrounded by farmlands. Its towns of Vredenburg, Saldanha Bay, Langebaan, Hopefield, St Helena Bay, Jacobsbaai and Paternoster consist of some 25 000 households.
Following the national waste man agement strategy, the municipality decided to implement a separa tion-at-source kerbside recycling col lection service aimed at residents in upper-, middle- and lower-income areas. Recycling swap-shops are planned for informal settlements.
The programme is phased over a three-year period to accommo date annual budget allocations, with Langebaan selected as the first area for the launch of the service. Its demographics comprise many retired people with an influx of visitors over holiday periods.
Tenders for collection and marketing
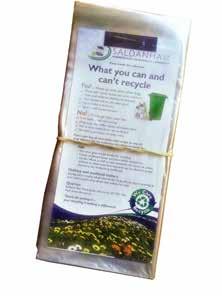
The tender also required a communications subcontractor with proven experience in the recycling behaviour change field to manage public education and marketing to increase householders’ participation. This was awarded to GreenEdge Communications, a Cape Town-based consultancy.
A strategy was then developed that included educational materials for householders and tactical use of local media along with activities to reach schools, housing complexes and shopping centres. Relevant information and FAQs were written up for the municipality’s website.
Starter packs and launch materials
separation system and the convenience of doorto-door weekly collection. On launch day – 5 October 2016 – a photo and article featuring councillors and municipal officials supporting the launch was published.
Schools recycling art competition
In the run-up to and during the launch, a recycling art competition between local schools was organised in partnership with the Cape West Coast Biosphere Reserve. Prizes were donated by shops in the nearby Laguna Mall. This helped raise recycling awareness among children and their families. The prize-giving event was a further opportunity to gain media exposure.
Soon after the launch, a local women’s organisation held a recycling demonstration for their members. Photos were taken and an article was published in Weslander.
The tender for the kerbside recycling collection service required a competent recycling company to transport and sort recyclables to the Saldanha Bay Municipality’s materials recovery facility. This was awarded to Wastegro based in nearby Malmesbury.
Starter packs containing information leaflets, fridge magnet reminder cards and two clear bags to start recycling were distributed to households in the week before launch. All “dry” materials – paper, plastic, glass and tins – were to be put out in clear bags on the pavement for weekly collection on refuse removal day. These would be swopped for fresh ones, so keeping the system moving.
A launch advertisement was created and placed in Weslander, the local community newspaper, and on social media. The emphasis in messaging was the ease of a wet/dry, two-bag
At the nearby mall, a table was set up on Saturday mornings where shoppers were given advice about what and how to recycle. Visits to housing and resort complexes were also undertaken with leaflets and posters handed out to homeowners’ associations and managing agents.
Assessing participation rates and waste sampling
By early December, two months after the launch, the rate of participation by residents could be measured, based on the weight of recyclables collected. Also, a waste sampling exercise was done to determine what kinds of materials were
A wrapped starter pack
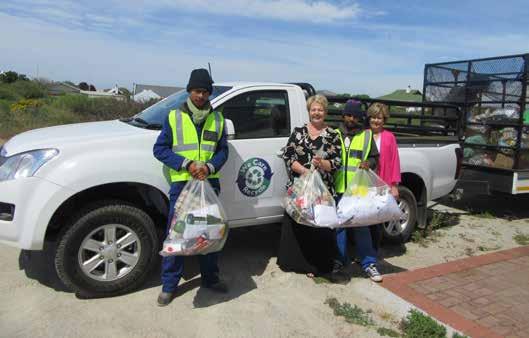
being separated by households and by which income levels.
This revealed, not surprisingly, that the proportion of glass was greatest among upper-income households (who would have higher disposable income to buy bottled beverages), while plastic (especially PET for soft drink bottles) was greatest in the lower-income groups.
Psychology
of recycling
The psychology of recycling behaviour change shows that some people in a community or organisation will only take part in recycling once it has been shown to be working effectively.
The psychology of recycling behaviour change shows that some people in a community or organisation will only take part in recycling once it has been shown to be working effectively
Report-back advertorials were placed in Weslander emphasising that within eight weeks, nearly one out of every two households were already recycling.
The advertorial also used infographics to show recognisable examples of what could be made from the materials recycled so far, and what resources were saved.
Holiday season
Being a coastal resort, Langebaan draws
QP_ad_FA.pdf 1 2017/06/30 10:22 AM
visitors over the holidays. Messaging was also designed to let them know that the recycling service was available and they could get starter bags at the local municipal office. Over Christmas and New Year, there was a spike in the amount of recyclables collected, which reflected the increase in people and the consumption of festive drinks and eats.
The next set of towns
Planning is now under way for the launch into the next set of towns, which will replicate methods and hopefully tonnages achieved in Langebaan.
The Weslander readership covers these towns as well, and many enquiries for the service have been received from their residents.
This bodes well for the expansion of the service. However, these towns have a different demographic and are populated mostly by middle- and lower-income residents employed in commercial, industrial and agricultural enterprises. It remains to
LEFT Community members with their clear bags for recycling
OPPOSITE PAGE Launch of the Saldanha Bay Municipality Household Recycling Project
Elements for success
• Adequate planning and preparation time
• Competent, proactive waste management department
• Helpful municipal Communications Unit
• Strategic behaviour change through marketing and communications
• Efficient, service-oriented recycling collections contractor
be seen how the first and second phases of the services compare. But with the first-phase householders’ participation on trend to exceed 50%, and over 250 t having been collected since launch, while 38 jobs have so far been created in the process, the Saldanha Bay Municipality’s kerbside recycling service can be seen to be on the path to efficient recycling.
“The introduction of the separation-at-source programme in October 2016 has been highly successful and the second and third phases will follow shortly. The success of the programme is dependent on having the correct team players. I want to thank Wastegro and GreenEdge for the effective and efficient services rendered to Saldanha Bay Municipality and our communities,” comments David Wright, waste manager at the municipality.
Secrets to success
Most importantly, the success of the programme has been due to residents answering the call for recycling and being willing to give their voluntary time and energy to get into the routine of separating their domestic waste at source and, in this way, contributing to social and environmental betterment.
*Hugh Tyrrell is the director of GreenEdge Communications.
Separation at source
NOW
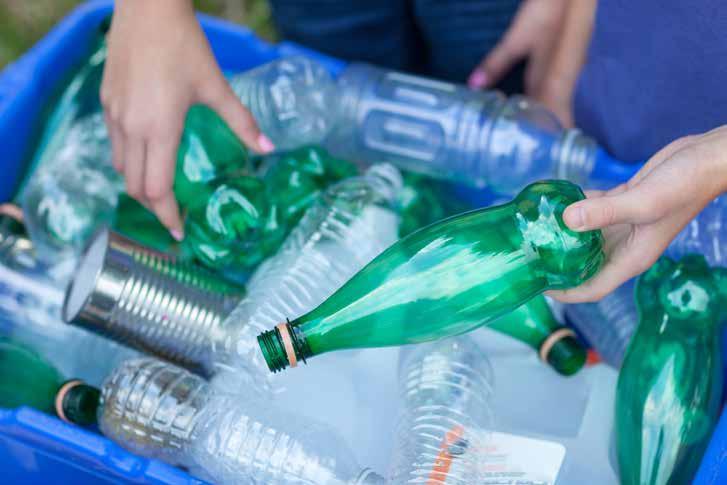
Separation at source has been key to the EU’s success
Johannesburg, Tshwane and Cape Town each have less than 10 years of useful landfill life left. Comparing how alternative waste treatment technologies are being rolled out in South Africa and Europe yields insights into how to buy more time. By Oscar Simelane*
South Africa’s eight Category A metropolitan municipalities have the highest population numbers and generate the biggest waste volumes – at about 20 million and 10 million t of waste per year, respectively. Most of this waste is landfilled.
When landfilling at an average density of 1 t/m3, municipalities need an annual landfill space of about 10 million m3
Investigating alternatives
The City of Johannesburg, eThekwini Metropolitan Municipality, the City of Cape Town and Sedibeng District Municipality have all completed AWTT feasibility studies, while Drakenstein Local Municipality in the Western Cape has finalised a waste-to-energy feasibility study. AWTT feasibility studies are also under way in Tshwane and Ekurhuleni.
Waste management is the least prioritised municipal service in most South African municipalities
While some municipalities, like eThekwini, boast a useful landfill life of 120 years, others – such as Johannesburg, Cape Town and Tshwane – have a very limited useful landfill life of less than 10 years. Therefore, the need to investigate alternative waste treatment technologies (AWTT) is crucial for diverting waste from landfill.
South Africa can learn some lessons from the EU regarding AWTT, although the European and South African waste management styles are not the same. The EU has successfully established some technologies that have been effective in diverting waste from landfills. Implementing separation at source, setting diversion and recycling targets, and diverting biodegradable waste have been key to the EU’s success.
Table 1 outlines some of South Africa’s largest metros’ remaining airspace, according to their Industry Waste Management Plans, compared with available statistics for the EU and UK.
Waste management scenarios
Waste management is the least prioritised municipal service in most South African municipalities. Leading priorities (as can be seen in the capex budgets of most South African municipalities) are housing, water, electricity and road infrastructure.
Further, job creation is a priority for the South African government.
In the EU, there is a greater emphasis on stimulating the transition towards a circular economy. The EU’s proposals on waste are geared towards diverting waste from landfill by setting recycling targets, reducing landfilling, discouraging landfilling and incentivising green products. By contrast, most of South Africa’s municipal
solid waste is still landfilled without any form of treatment or resource recovery).
The Polokwane Declaration of 2001 sets a target of zero waste by 2020. Progress towards the zero waste target is minimal because most South African household waste is still collected without any form of separation and it ends up at landfill.
Alternative technologies
Material recovery facilities (MRFs) have been established in some municipalities to recover recyclables, but some of these have stopped operating. The main cause of this MRF failure is the low rate of recovery of recyclables. The absence of separating waste at source means facilities are operated as “dirty” MRFs (high contamination rates) – with lower recovery rates than “clean” ones (low contamination rates).
Some South African municipalities are piloting separation at source but the response has been minimal. In the EU, separation at source has been key in enabling the diversion of waste from landfill by recycling, composting and incineration.
In South Africa, the incineration of waste happens on a small scale and it is primarily used for the thermal treatment of healthcare waste and some hazardous waste. There are some small-scale initiatives that are meant to divert waste from landfill. For example, Interwaste has launched a plant that produces 12 000 t of refuse-derived fuels annually. These are used as fuel in cement kilns.
While the cement industry offers an opportunity to use refuse-derived fuels, South Africa’s cement factories are located far from its metros.
A composting plant with a 1 t/day capacity has been piloted at the Tshwane Fresh Produce Market to produce compost from food waste and cardboard.
In the Kraaifontein MRF in Cape Town, the Japan International Cooperation Agency is piloting a plant that converts about 500 kg of plastics to 500 ℓ of oil per day.
TABLE 1 Comparison of landfill space, waste tariffs and alternative waste treatment technologies
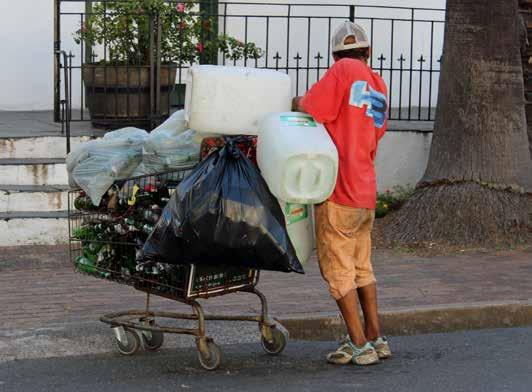
The informal sector is responsible for the majority of South Africa’s recycling
waste, which happens through established companies that usually target specific recyclables like PET plastic, or paper and cardboard.
Cooperatives
Informal collectors (trolley pushers/landfill salvagers)
In the EU
In EU countries, incineration of waste is done at a commercial scale. Since 1995, the amount of municipal solid waste that has been incinerated in the EU has increase by 19.6 million t, or 63.1%, and recycling and composting were used to treat about 42% of solid waste by 2009. South Africa recycles only about 10% of its
Recyclables are mainly collected by informal recyclers from those who generate waste. The informal recyclers sell these recyclables to middlemen, who then sell them to a company that makes the final product (see the South African waste recycling hierarchy to the left). Some South African municipalities have established cooperatives that are meant to recycle waste; however, these cooperatives have a high rate of failure.
Waste generator
There has been a reduction in the landfilling rate in the EU. This has been the result of the combined implementation of recycling, composting and incineration technologies. Additionally, the EU’s landfill taxes are high, playing an important role in incentivising a shift up the waste hierarchy. By 2012, 20 European countries had introduced a landfill tax, which ranged between €50 and €70 per tonne of waste. In South Africa, landfills charge a gate fee that ranges between R180 and R395 per tonne of waste in the metros, and there is also no landfill tax. So, it is still
Recyclers
Middlemen
Van, truck collectors
cheaper to landfill waste than to implement the AWTT in South Africa.
Recycling vs incineration
There is a ceiling for the availability of feedstock for recycling, composting and incineration. For example, Vancouver in Canada has decided to put proposed waste-to-energy developments on hold due to uncertainty over the availability of feedstock and dwindling residual waste. The dwindling supplies of residual waste may be due to the increased recycling rates.
Recycling, however, complements incineration rather than competes with it. The capex for establishing a waste-to-energy plant can be substantial, with the capital costs for establishing an incineration plant in the UK ranging between £145 million and £200 million for a capacity of 150 000 to 350 000 t per year. The cost of maintaining and upgrading incineration plants is soaring, but these costs may be recovered through the sale of electricity and recyclables, as well as gate fees.
Thus, an incineration plant may pay itself off in 15 years.
AWTT challenges
Environmental authorisations, permitting, licensing and social issues are the primary challenges faced by any waste management endeavour. In fact, it can take up to 10 years between identifying a suitable site and actually commissioning a landfill.
Although the capex and maintenance costs of technologies for treating waste are substantial,
Refuse-derived fuels are used in the cement-making industry, but these factories are located far from metros
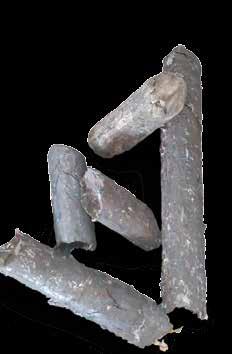
landfilling remains less expensive than AWTT. However, the cost of landfilling may be more than it appears, considering the cost of managing the landfill after closure. The life of a landfill may stretch to about 50 years after it closes. The absence of carbon taxes also makes landfilling attractive compared to AWTT in South Africa.
The slow implementation of separation at source is also an issue but it could potentially be promoted effectively using economic incentives.
There are about 37 000 waste pickers in South African landfills and about 5 000 trolley pushers. The waste pickers and trolley pushers are regarded as informal recyclers. Formalising informal recyclers is a challenge. Some informal recyclers tend to salvage waste that has been separated at source in some piloting households, affecting the performance of formal recycling initiatives.
Also, providing a constant feedstock quality and quantity for the AWTT may not be guaranteed. AWTTs actually need more consistent feedstock quality than incineration. Seasonal variations in waste composition and the absence of separation at source are the main causes of quality variation.
Securing BBBEE partners for waste-to-energy plants is a further challenge.
Conclusion
Separation at source is key to the successful implementation of AWTTs. Financial incentives and overcoming challenges around formalising the informal waste sector will go some way towards achieving this goal.
While the formation of cooperatives seems to be the best available answer to formalising the informal sector for now, it may be that the private sector will need to be involved in metros’ efforts towards formalisation to help them succeed – although how this might be done is yet to be answered.
Introducing landfill and carbon taxes can help to discourage landfilling and make the cost of using AWTTs competitive with landfilling. In the EU, the introduction of landfill taxes can be correlated to a reduction in the rate of landfilling. The true short- and long-term costs of landfilling waste in South Africa should be evaluated.
For a full list of references, please contact the editor: frances@3smedia.co.za.
*Oscar Simelane was a civil engineer at AECOM SA.
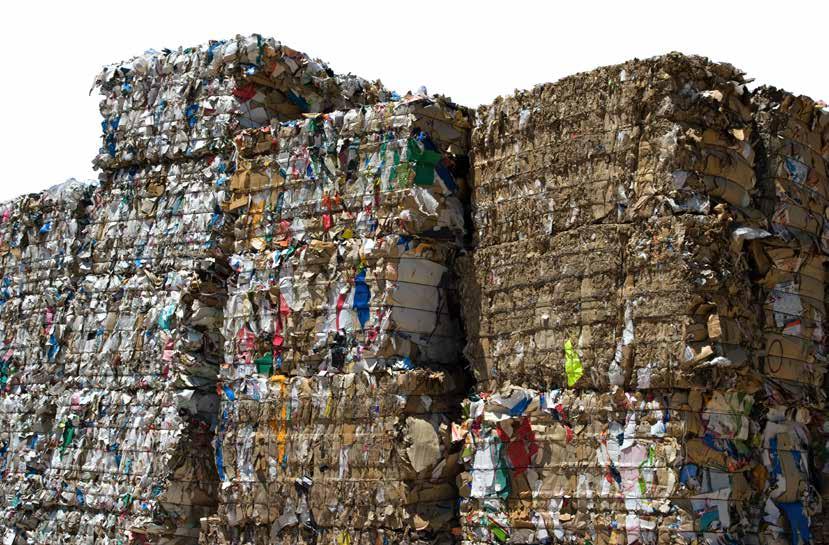
19.6 mt
Amount of municipal solid waste that has been incinerated in the EU since 1995.
+£145 m
Minimum capital costs for establishing an incineration 7 F̰ /
10 mil m3
Annual landfill space needed by municipalites when landfilling at an average density of 1 t/m3
37 000
waste pickers in South African
̽ F 9 pushers.
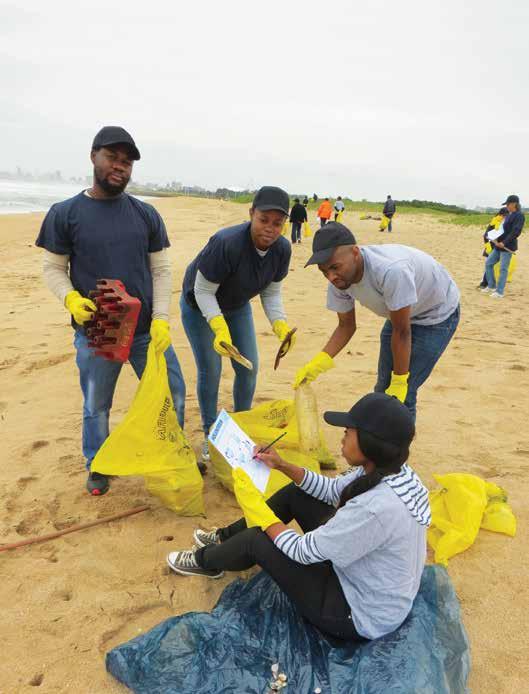
Celebrating 21 years
Harnessing the power of people to fight ocean litter
people flock to beaches to pick up and remove litter found in marine environments.
“Ocean Conservancy is the international coordinator of the ICC, but Plastics|SA coordinates the beach clean-ups that take place in the three Cape provinces, as well as various river clean-ups that take place inland. We are proud to partner with KZN Marine Waste Network members who take responsibility for coordinating beach cleanups at all the major beaches in KwaZulu-Natal. To date, nearly 12 million people have been part of the world’s biggest volunteer effort to protect the oceans, and South Africa is a major part of this success story,” Steyn says.
This year, Plastics|SA is also a proud supporter of one of the biggest national clean-
This year, Clean-up and Recycle SA Week will be celebrating its 21st year of cleaning South Africa’s beaches and environment.
Clean-up and Recycle SA Week will take place this year from 11 to 17 September 2017, with various clean-ups being planned for neighbourhoods, water sources and beaches around the country. One of the highlights of this annual environmental awareness event will be the 21st International Coastal Clean-up Day (ICC) taking place on Saturday 16 September this year.
Background
Clean-up and Recycle SA Week is an annual initiative by the local plastics industry, supported and endorsed by the various packaging streams and retailers. Each year, close to 120 000 volunteers participate in these clean-up activities that take place
along roadsides, rivers, schools, and residential and illegal dumping areas.
The initiative is supported by provincial governments, local municipalities, environmental organisations, businesses, schools and communities.
“The aim of this week is to increase an awareness of the social, environmental and economic benefits of recycling. During this time, we encourage communities, schools and businesses to clean-up the areas where they work, live and play by collecting the litter and ensuring that it gets recycled,” explains Douw Steyn, sustainability director of Plastics|SA.
International event
One of the highlights of Clean-up and Recycle SA Week is South Africa’s participation in the International Coastal Clean-up Day –the world’s biggest annual volunteer effort for ocean health that sees thousands of
“To date, nearly 12 million people have been part of the world’s biggest volunteer effort to protect the ocean, and South Africa is a major part of this success story.”
up collaborations on this day, by partnering with the ‘Let’s Do It!’ Africa campaign and the WESSA Tourism Blue Flag Project (a Department of Tourism-funded coastal conservation and youth development project), to support or implement a number of registered ICC events stretching from the west to the east coasts of South Africa. This collaborative effort will mark one year to the big World Clean-up Day on 15 September 2018.
“We are definitely seeing an increase in the number of clean-ups being organised inland at rivers, streams and other water sources, as the public realises that trash travels. All litter eventually finds its way to our country’s oceans and on to the beaches,” Steyn explains.
Conclusion
About 75% of ocean litter is derived from land-based waste. Without effective waste collection, an avalanche of debris will enter the ocean. To prevent this, Plastics|SA encourages South Africans of all ages, races and backgrounds to participate in this year’s Clean-up and Recycle SA Week activities.
You can play a role in the transformation of used-carton waste into a wide range of useful paper, cardboard and other products with Tetra Pak® and Mpact Recycling.
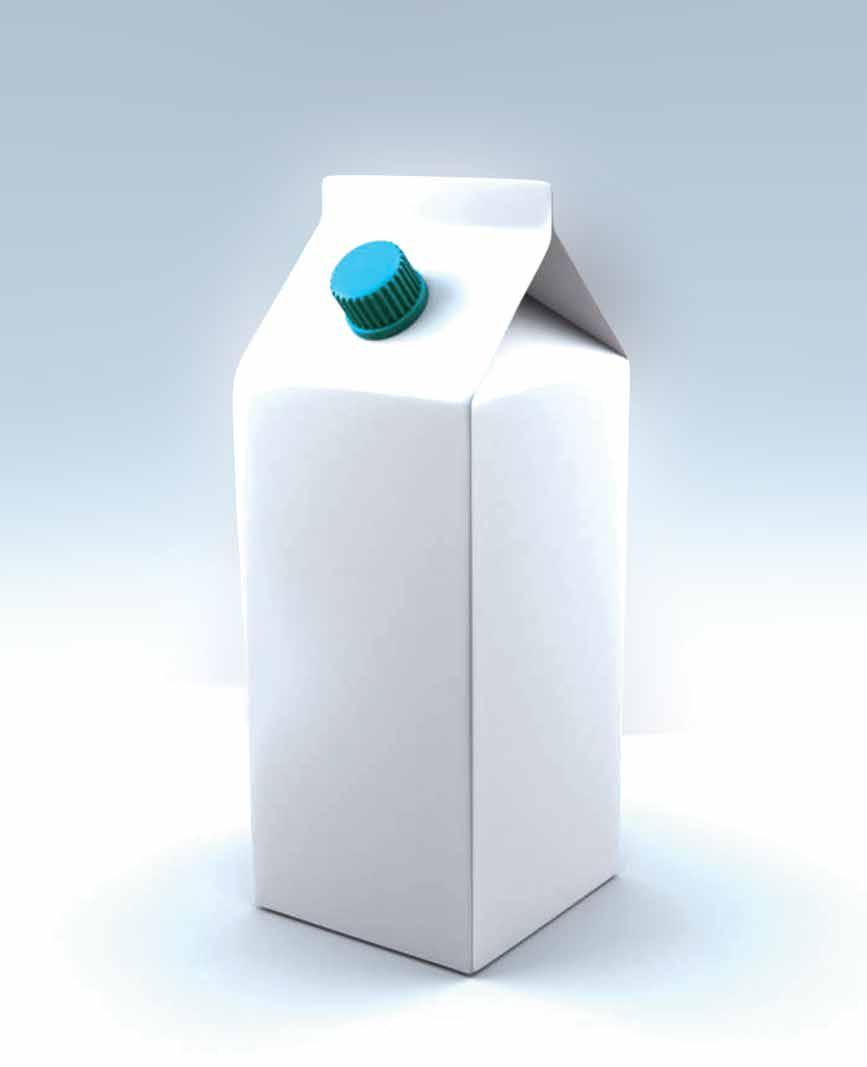
Cartons come in all shapes and sizes, and are generally filled with a variety of food and beverages.
OF EVERY MILK OR JUICE CARTON IS RECYCLABLE
The caps on top are made of recyclable plastic.
The cartons are made up of 75% paperboard from certified and sustainably-managed plantations, which gives them their form and strength.
On the inside, they comprise thin layers of polyethylene and aluminium (polyalu) foil, to keep food safe, seal in liquids and protect the contents from external moisture, oxygen and light.





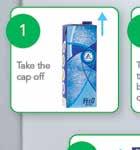
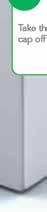
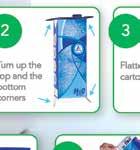
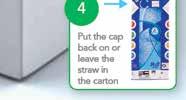
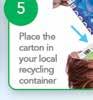
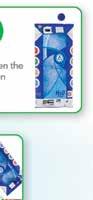

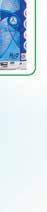
LIQUID PACKAGING RECYCLING
Juice and milk cartons have long been one of the contributors to South Africa’s landfills. A major development for the South African paper and packaging recycling market is Mpact Recycling’s new ability to recycle liquid cartons.
This follows the investment of R46 million in a liquid packaging recycling plant at Mpact’s Springs Paper Mill facility. The investment forms part of Mpact Group’s various recycling initiatives to increase available materials for all its mills.
Container composition
John Hunt, managing director, Mpact Recycling, says it was previously not possible to recycle juice and milk cartons, poly-coated cups and wet-strength bags, as they are not made of typical paperboard.
“Although about 75% of liquid packaging content is paper, in order to make it liquid-proof, the product is lined with: low-density polyethylene (plastic), which acts as a water-tight barrier; a lining of aluminium foil, which serves as a barrier to light, flavour loss and oxygen, enabling the contents to last for months without preservatives or refrigeration; and a coating of kaolin clay to improve the printing surface,” he says.
In the past, the mix of plastic and metal (polyalu) meant that cartons could not previously be recycled, as the polyalu couldn’t be separated from the paper of the carton.
“These need to be removed before the paper can be recycled,” says Hunt. “This was facilitated by two developments. First, local liquid carton manufacturers have, over the years, redesigned their processes to significantly reduce the amount of plastic used in the packaging. Second, Mpact’s new liquid packaging recycling plant has the capacity to recycle 25 000 t of used liquid cartons per annum and will allow us to produce about 18 000 t of recovered fibre, which will be fed directly into our Paper Division for use in new paper products.”
Plastic investment
To complement its initiatives to expand its own collection of recyclable materials, Mpact
Making an impact
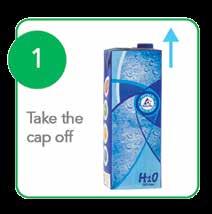
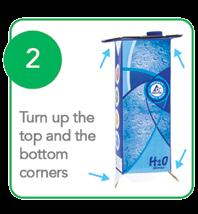
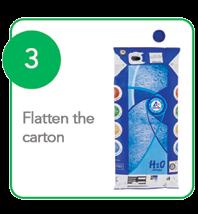
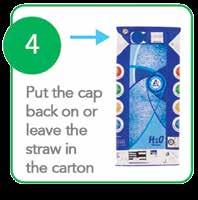
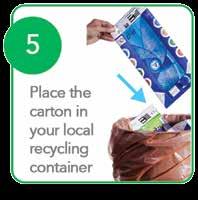
How to recycle liquid packaging
acquired Remade Holdings a year ago. In May 2016, the group invested R350 million into Mpact Polymers to develop a plant that would process up to 29 000 t of PET bottles a year. The company also invested R765 million to upgrade its Felixton mill, which will produce an extra 60 000 t of paper per annum from recycled fibre.
Mpact Recycling’s role – through its extensive collection network of paper, containerboard, PET and now liquid packaging – is to supply its mills with sufficient volume to match capacity.
Awareness campaign
The need for sufficient volumes has galvanised the company to embark on a campaign to raise consumer awareness that juice and milk cartons are now recyclable, and they should put them in
“Mpact’s new liquid packaging recycling plant has the capacity to recycle 25 000 t of used liquid cartons per annum and will allow us to produce about 18 000 t of recovered fibre.”
their Ronnie bags for kerbside collection.
“This new carton waste recycling facility by Mpact is an opportunity for consumers to change their behaviour towards recycling,” says Rodney Reynders, cluster leader: Environment for Greater Middle East and Africa, Tetra Pak. “Mpact’s market-leading recycling facility enables consumers to participate more functionally in green practices through any of Mpact Recycling’s numerous collection facilities, including kerbside, schools and communities to name a few.”
Penny Ntuli, communications director, Tetra Pak SA, says: “We have partnered with Mpact Recycling to raise public awareness about the recyclability of our carton packs, and significantly increase the volume of cartons collected and diverted from landfill sites. This is in line with our global environmental policy that includes minimising our impact on the environment.”
BURN RUBBER THE RIGHT WAY
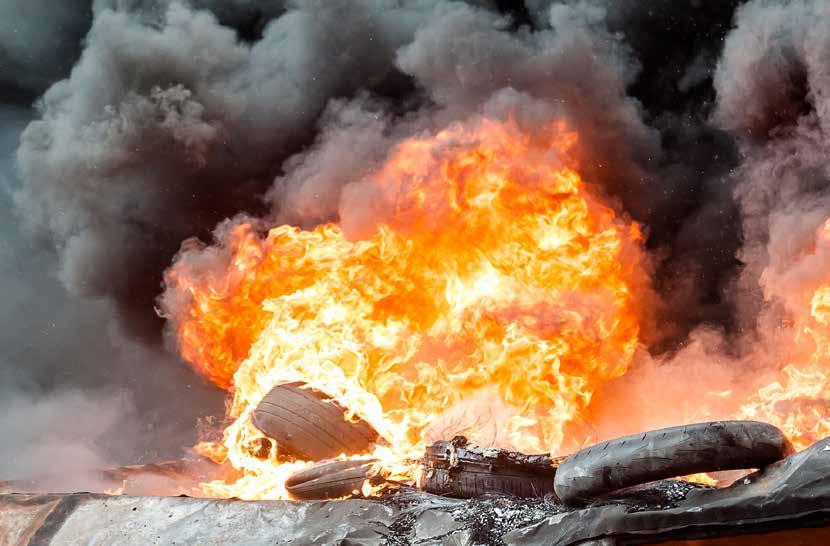
Boasting a landfill footprint size of 100 ha, Buffelsdraai Landfill is set to take over as the main landfill for eThekwini, with the closure of the Bisasar Road site and the imminent closure of Marianhill Landfill.
Despite the Recycling Economic Development Initiative of South Africa (Redisa) being placed under provisional liquidation, tyres will continue to be collected from registered collection points including micro-collectors. An interim liquidator has been appointed by the Western Cape High Court to take control of Redisa’s business, ensuring there’s no impact on collections from subscribers to the Waste Tyre Plan.
In excess of 11 million tyres are thrown away in South Africa each year, weighing about 530 000 t. This is from cars and trucks alone and does not include the large off-the-road (OTR) tyres from mining vehicles and rubber from industrial conveyor belts.
The collection and recycling of tyres is funded through the waste tyre levy, which compels
South African tyre manufacturers to pay R2.30/ kg of tyres manufactured, totalling a whopping R500 to R600 million per annum. This is according to estimates by the South African Tyre Manufacturers Conference.
It’s important that waste tyres are recycled because there are a number of problems associated with landfilling them. The first being that gasses collect in the concave inner lining, which causes them to rise to the top of landfills, even when weighted. This creates an issue when people living on or near landfills burn tyres for warmth, releasing massive amounts of carbon dioxide and other pollutants and volatile organic compounds into the atmosphere.
It’s important that waste tyres are recycled because there are a number of problems associated with landfilling them
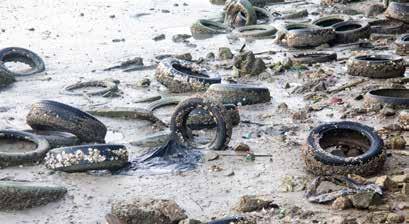
A further problem is that a tyre’s inner cavity collects water, creating the ideal environment for mosquitoes to breed. Malaria has long been one of Africa’s biggest challenges, killing almost a million people each year. Additionally, some unscrupulous motorists retread old tyres that are too worn down or damaged to be on the road. This results in burst tyres and often fatal road accidents.
Given the dangers posed by waste tyres, there have been a number of grand
schemes dreamed up to deal with the problem. One such scheme sought to anchor waste tyres to the sea bed as an artificial reef. These experiments have repeatedly failed. The Osbourn Reef off the coast of Fort Lauderdale, Florida, for example, is now considered a huge environmental disaster, with tyres regularly washing up on the shoreline of adjacent beaches after severe storms.
Looking at pyrolysis
There are two primary ways to recycle tyres effectively. The first is crumbling, which has been extensively covered in other ReSource articles. The second is pyrolysis. Pyrolysis is the breaking down of material in a sealed, oxygen-free environment. There cannot be any oxygen as this can result in fires or potentially an explosion. The by-products of this process include steel (which can be recycled), carbon black, crude oil,and another type of oil that can be blended with diesel for commodity buyers.
One of the biggest problems with pyrolysis in South Africa is there are few facilities able to process tyres at the necessary scale to make it profitable.
Given the obvious need to process waste tyres at scale, Hans Mitchell, director of Innovative Recycling, invented a rubber-to-fuel conversion plant with the capacity to recycle up to 30 000 kg of waste tyres per day. “That’s about 9 000 t per year,” says Mitchell. His plants have an opening of 2.2 m and can readily handle tyres from cars and trucks. For OTR tyres and other unwieldy rubber
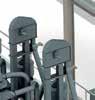





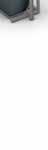
11 million tyres are thrown away in South Africa each year
R500 m – R600 m
Amount paid annually by tyre manufacturers for tyre waste to be managed
30 t of recycled tyres will create 12 t of carbon black
R45 m
The cost of one waste-rubber-to-fuel conversion plant over three years
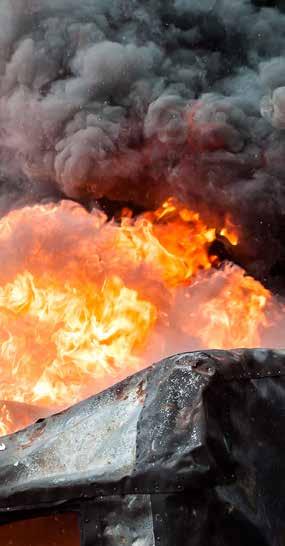
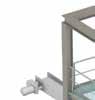
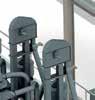



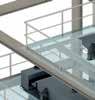
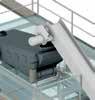
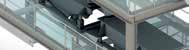



materials, Mitchell recommends shredding prior to feeding them into the plant’s reactor.
Another one of the major problems associated with tyre pyrolysis is the excess production of carbon black. “I’ve seen other pyrolysis technology manufacturers’ sites close down because they had not secured off-take agreements for their carbon black. As a fine powder, carbon black is easily blown away by the wind, making it one of the biggest environmental and business risks that need to be managed. If you recycle 30 tonnes of tyres per day, 12 tonnes of carbon black is produced. This means that, effectively, a new waste stream is produced. Since carbon black smells like rubber and contains ash, it is not suitable for reuse in a number of industries including ink and paint manufacturing and braai briquettes. If others in the industry say this is how they dispose of their carbon black, they may not be telling the truth,” warns Mitchell.
“I designed my process so that there is no smell and the carbon is activated, making it ideal for reuse as braai briquettes,” he adds.
Business model
Mitchell has the distribution rights for his plants in South Africa and the rest of Africa. He has
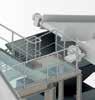
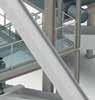
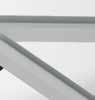
already supplied one of his plants to a landfill in the Netherlands where a zero waste to landfill policy is followed.
“The entire plant operation can be automated; however, for Africa, I have put together a technology selection that’s labour intensive because of the need for job creation. Each plant creates 46 jobs and 200 indirect jobs – for people doing the transport, collection, and so on,” says Mitchell.
One plant costs R25 million with an estimated return of capital layout in 24 months. “We got our tyres for free from Redisa, and will continue to do so under the interim liqudator. Plus, we get a recycling fee for the first two years, making these plants highly profitable,” says Mitchell.
Innovative Recycling will only sell its plants under the condition that purchasers work with the company to acquire the relevant Environmental Impact Assessment and licences. These costs are included in the selling price.
The company already has two plants in operation, one in Klerkshoop, which was bought by Indian technology company Osho, and another in Alrode. “We are also in the final financing process for a number of other plants around the country,” concludes Mitchell.


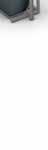
WASTE TYRE

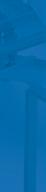
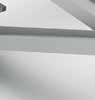
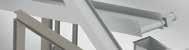
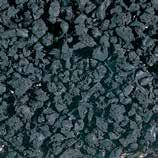
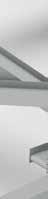
AMANDUS KAHL GmbH & Co. KG Dieselstrasse 5–9 21465 Reinbek Hamburg, Germany
+49 (0) 40 72 77 10 info@akahl.de akahl.de

PLANTS

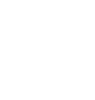




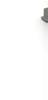
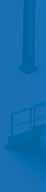
AND MOULDING
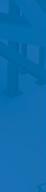
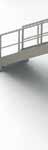
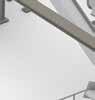
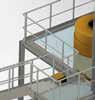

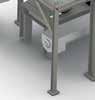
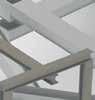
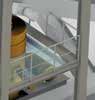
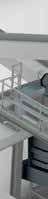
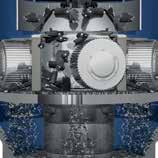
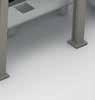
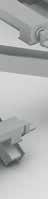
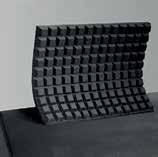
CONSTANT HIGH PRODUCT QUALITY
Integrated rubber granulate production
MOST Advanced Technology, Efficient, Professional
LESS Maintenance, Energy, Spare Parts
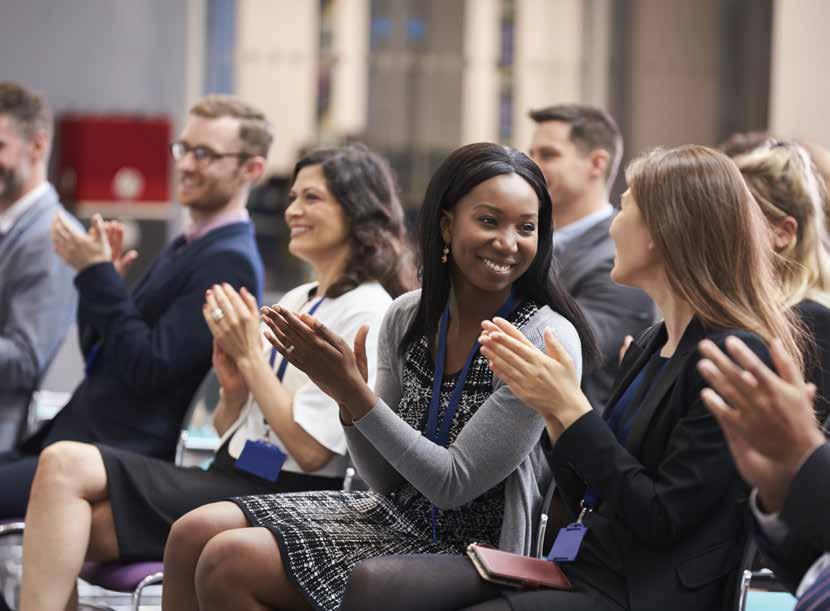
Meeting manufacturers halfway
Manufacturing has been under fire as looming strike action, the technical recession, low business confidence and political uncertainty take their toll. Amid these conditions, Ekurhuleni’s annual Manufacturing Indaba took place, creating a bridge for government and industry to chart the way forward. By Frances Ringwood
On 27 and 28 June this year, Ekurhuleni, South Africa’s manufacturing hub, hosted its fourth annual Manufacturing Indaba. Organised by Siyenza Management, the event brought together strategic partners including the Department of Trade and Industry (dti), the Manufacturing Circle, the City of Ekurhuleni, the National Cleaner Production Centre of South Africa (NCPC-SA) and the Department of Science and Technology.
Economic outlook
One of the key presentations was Ekurhuleni Executive Mayor Mzwandile Masina’s speech on the city’s R2.2 billion investment in energy infrastructure – especially renewable energy – over the next three years. “We are pursuing a renewable energy strategy that will generate 10 MW of energy by 2021. This is part of our local strategy
to ensure energy stability in our region without completely relying on the national grid,” he said.
Masina also emphasised the challenging economic context in which the Indaba took place, noting the national economy’s 0.7% contraction in the second financial quarter of this year. This followed a 0.3% contraction in the first quarter. He also acknowledged the effect the technical recession has had on job creation, saying 48 000 jobs were lost in the first quarter.
“Stats SA also showed us the sectors that lost a lot of jobs: the business services industry, with a 23 000 job decrease; the trade industry, with an 8 000 job decrease; the manufacturing industry, with a 4 000 job decrease; and the transport industry, with a 1 000 job decrease,” he said.
However, it wasn’t all doom and gloom, with Masina emphasising 12 000 jobs created in the construction sector and 8 000 new mining jobs.
Re-industrialisation
Also presenting at the Indaba was Dr Rob Davies, Minister of the dti, who emphasised government’s plans to improve the number of black industrialists across all sectors of the economy, while also promoting regionalism.
“We want a level of empowerment that supports the entry of black companies as real players. Since its establishment last year, the Black Industrialists Programme has supported projects with an investment value of R3.9 billion,” he said. The dti’s target is to have 100 black industrialists up and running before March 2019.
Davies said regionalism was a route to the “deep industrialisation” (some speakers also called it re-industrialisation) needed to prevent Southern Africa and the rest of Africa from becoming a “dumping ground” for the unwanted goods of other nations. He added that the country needs to step up its investor confidence while at the same time reducing its dependence on raw materials.
A million jobs
Delivering one of the keynote addresses was André De Ruyter, Manufacturing Circle chairman
WHAT THEY SAID
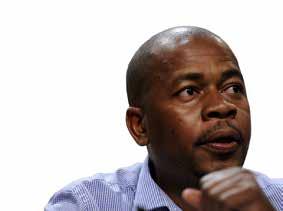
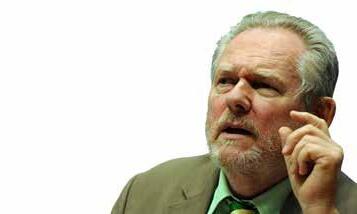
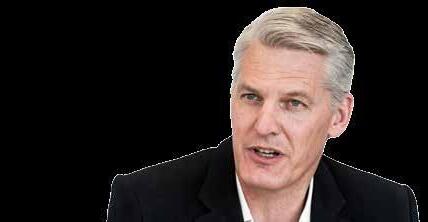
We are pursuing a renewable energy strategy that will generate 10 MW of energy by 2021.”
Executive Mayor of Ekurhuleni Mzwandile Masina
and CEO of Nampak, who looked at whether the current regulatory environment and tax incentives would ultimately help or hinder the manufacturing industry. “Since 1989, South African manufacturing has shed half a million jobs, as manufacturing’s share in GDP has shrunk. If manufacturing were to have an appropriate GDP share for the country’s development stage (28% to 32%), then, theoretically, between 800 000 and 1.1 million jobs could be created,” he said.
Reasons for manufacturing’s shrinking market share included increased imports competition, labour costs and energy costs, in conjunction with infrastructure challenges, policy and regulation uncertainty, and uneven compliance with World Trade Organization rules. “Fiscal challenges remain, placing added pressure on manufacturing. These include new taxes on sugar, carbon and waste management,” he added.
This was followed by an outline of the Manufacturing Circle and partners’ commitment to create a million new jobs in manufacturing within the next 10 years. “Industry is currently identifying investments that could be made by manufacturing firms and also what needs to be resolved, unblocked or addressed in order for these investments to take place,” said De Ruyter. Following this exercise, a public sector engagement process will be conducted to align industry investment in job creation and economic growth with key focus areas. The
Since its establishment last year, the Black Industrialists Programme has supported projects with an investment value of R3.9 billion.”
Minister of Trade and Industry Dr Rob Davies
Manufacturing Circle’s partners in this initiative include the Manufacturing Indaba, the Chemical and Allied Industries’ Association, Plastics|SA and Packaging SA.
Resource efficiency
During a press briefing, De Ruyter was asked about his organisation’s stance on efficient resource use, particularly given the drought afflicting the Western Cape.
He answered that South African manufacturing has done a “pretty good job” in being resource efficient, “For example, in the packaging sector, we’ve achieved some of the highest recycling rates in the world. Just looking at beverage cans – the rate is 72% – and some 56% of glass is recycled. Those numbers compare favourably with the best in the world,” he said.
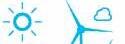
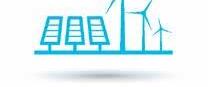
R2.2 billion
The amount Ekurhuleni is investing in 9 F 9 9 9 / F /9 9̽
If manufacturing were to have an appropriate GDP share for the country’s development stage, between 800 000 and 1.1 million jobs could be created.”
Andre De Ruyter, chairman of the Manufacturing Circle and CEO of Nampak
“I think that from an overall life-cycle responsibility point of view, the industry has done a particularly good job. Can we do better? Yes. For instance, there are opportunities in energy management in particular and also water use. We need to pay more attention to how we harness those resources and that has been revealed to us through the recent drought in Cape Town.”
De Ruyter noted the drought’s negative impact on fruit production and its knock-on effects on cardboard box and packaging manufacturers.
“It’s been made clear to the manufacturing sector, by the province, that we need to be a lot more careful about how we use and recycle water. Much effort has gone into ensuring that our water consumption is reduced,” he concluded.
Regulations, renewables
The latest news gathered locally and abroad about how government and industry are embracing new trends in sustainability to create a cleaner, safer and healthier environment.
Packaging
company increases renewable mix
Tetra Pak is using 35% renewable electricity by buying International REC Standard (I-REC) certificates for all of its production facilities in China.
The I-REC certificates Tetra Pak buys are generated by two wind farms – Inner Mongolia Wind and Guangdong Xinyi Wing – and a biomass project, Pizhou Biomass.
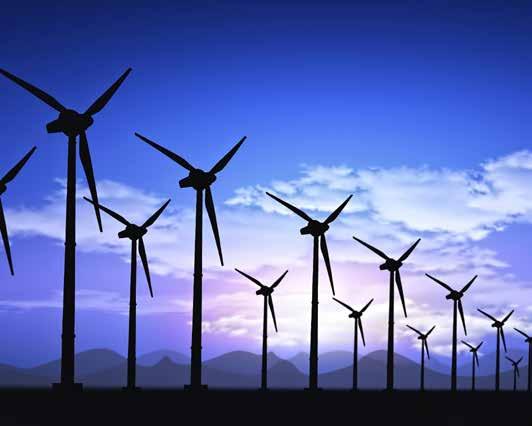
Charles Brand, executive VP: Product Management and Commercial Operations, Tetra Pak, says: “We joined the RE100 last year as a part of our commitment to tackling climate change, pledging to use 100% renewable electricity across all our operations by 2030. This move in China, where we have the largest production footprint, is a solid step forward.”
Getting more from metal
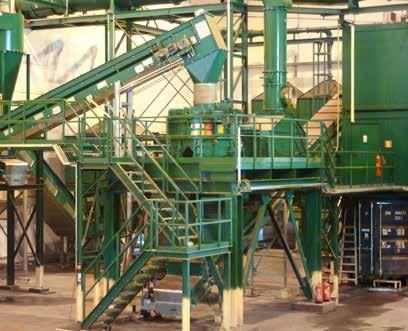
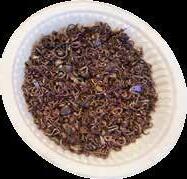
FTetra Pak is also purchasing 100% renewable electricity for all its facilities across Sweden. This includes the use of 60 GWh of green electricity per year from Swedish wind power
Tetra Pak has four conversion plants, one product development centre and one processing equipment factory in China. Since the beginning of this year, the company has procured I-REC certificates equivalent to the total electricity consumption of all these facilities, as well as its regional head office of Greater China in Shanghai.
innish scrap recyclers Kajaanin Romu Oy recently commissioned a BHS-Sonthofen plant for processing automotive shredder residue (ASR) fine fractions of particle sizes between 0 mm and 30 mm. It separates the feed material into “light” and “heavy” fractions in a single pass. This allows the operator to economically produce fractions that can be sold. Moreover, the plant significantly reduces the cost of material disposal at landfills. Heavy non-ferrous fractions of material left over after shredding and processing large automotive or e-waste scrap components still hold value. A tonne can contain up to 20 gof gold and up to 300 gof silver, as well as platinum and other precious metals.
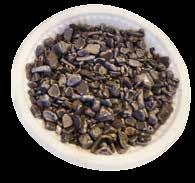
Operators report that they are able to earn about €3 000 per tonne just from selling the heavy fraction. At the end of the process,metal fractions are cleanly separated in silos. This includes heavy ones like copper, gold and silver as well as light fractions like aluminium.
LEFT Output material: non-ferrous metal with a particle size between 6 mm and 12 mm, separated into heavy fraction (above left) and light fraction (left)
FAR LEFT The BHS Rotor Impact Mill is the core component for mechanical crushing undertaken in the first processing stage
and recycling
Residue regulations change
The National Environmental Management Laws Amendment Bill, 2017 seeks to clean up a range of issues associated with the One Environmental System, implemented on 8 December 2014, according to law firm Webber Wentzel.
One such issue is the confusion surrounding the regulation of residue stockpiles and deposits.
As a result, residue stockpiles and residue deposits will no longer be regulated under the National Environmental Management: Waste Act (No. 59 of 2008). They will instead be regulated in terms of the National Environmental Management Act (No. 107 of 1998)(NEMA).
The bill proposes various transitional measures to facilitate this change. First, a waste management licence issued in respect of residue stockpiles and deposits under the Waste Act will remain valid until it lapses, or until it is replaced under NEMA. Second, the regulations regarding the Planning and Management of Residue Stockpiles and Residue Deposits, 2015 that were published under the Waste Act will remain in force and be deemed to have been promulgated in terms of NEMA.
These are welcome amendments given the practical difficulties experienced by miners, particularly in relation to pollution control barrier systems.
Driving Joburg’s renewable uptake
The leadership of the City of Johannesburg has been urged to switch to 100% renewable energy.
The call came from the African Climate Reality Project (ACRP) during a recent meeting with Joburg’s executive director of the Environment and Infrastructure Services Department, Tiaan Ehlers, and the director of Air Quality and Climate Change, Lebo Molefe.
The city’s achievements to date combine work being done by the Joburg Business Forum and includes the city council’s energy framework thatopens the way for introducing renewable energy. The city expressed the view there are economic benefits that can arise from the
Turning breadtags to wheelchairs
The Polystyrene Packaging Council (PSPC) was able to spread some much needed warmth this winter by participating in Smile 90.4 FM’s Winter Wish campaign.
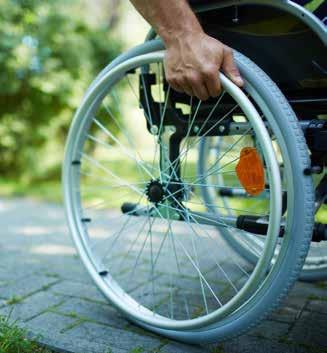
The radio station received an influx of stories from people across the Western Cape, granting 41 wishes in just four weeks. One of the listeners whose life was forever changed was Norman Mayhew, an army veteran who lost the use of his legs due to brain cancer.
“When we heard about Smile 90.4FM’s drive and Norman’s need for a wheelchair, we saw it as an opportunity to
get involved.
Thanks to one of our most passionate collectors of breadtags, DB Janse van Rensburg, a grade 11 pupil at Paul Roos Gymnasium, we had enough bread tags to purchase a brand-new wheelchair for him,” says Adri Spangenberg, director, PSPC.
This year, the Breadtags for Wheelchairs ini tiative is celebrating its 10th year and more wheelchairs will be handed out during a spe cial celebration in August.
Valuing natural capital
Some of the world’s largest companies – including Coca-Cola, Dow, Nestlé, Shell and Tata –recently generated the Natural Capital Protocol as members of the Natural Capital Coalition. The protocol promises
decentralisation of energy, especially as the current business model of City Power is under extreme pressure.
Together with the private sector, the city is generating electricity from methane gas through landfill sites and wastewater treatment works.
Another tier of Joburg’s sustainability drive is the solar photovoltaic systems at some its facilities – with the objective to explore larger-scale generation opportunities in partnership with the private sector.
The ACRP says that solar power can create 12 times the number of jobs when compared to coal per megawatt of power.
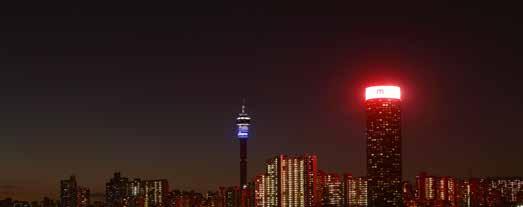
to give business a new appreciation of the ecosys tem services on which they rely.
According to Paul Jor gensen, environmental scien tist at SRK Consulting, the protocol offers a standardising framework for organisations to identify, measure and value their impacts and dependencies on natural capital.
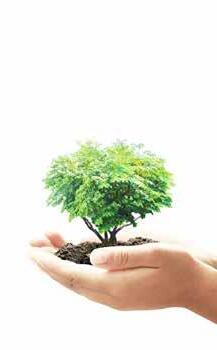
What is natural capital? It is any stock or flow of energy and material that produces ecosystem goods and services. It includes resources in the form of renewable and non-renewable materials, sinks that absorb, neutralise or recycle wastes, and processes such as climate regulation.
Jorgensen describes the protocol as a framework that helps business to practically focus on the natural capital inherent in the surrounding environments, allowing a closer integration of sustainability thinking in business.
“For instance, while mines are generally familiar with their environmental impacts, most do not appreciate how dependent they are on ecological infrastructure. By nurturing this natural capital, there is more scope for them to benefit financially and lower the costs of their built infrastructure.”
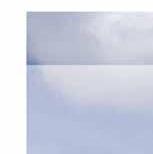
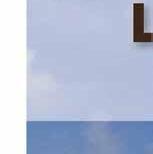
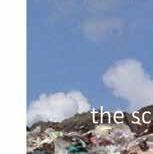
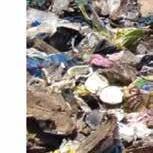
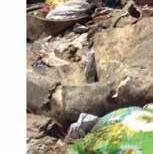
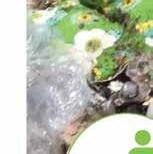
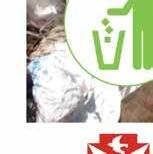
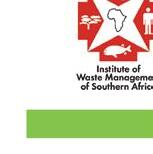
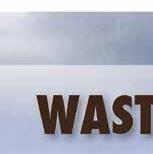
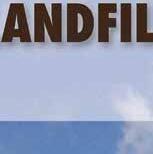
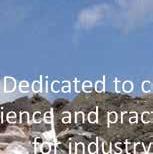
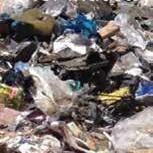
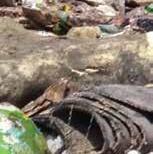
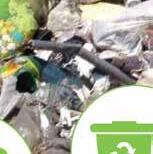
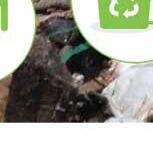
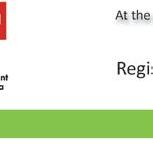
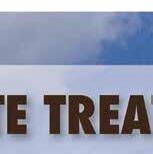
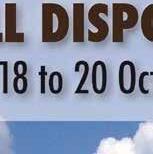
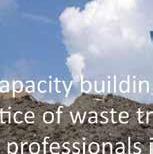
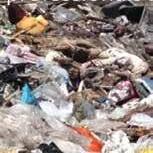
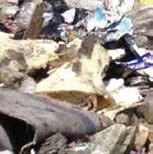
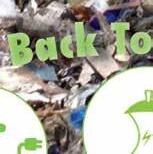
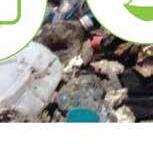

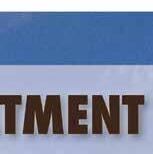
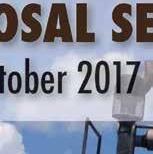
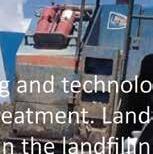
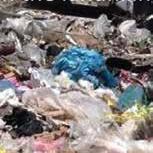
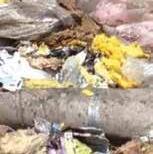
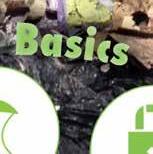
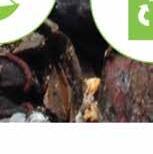
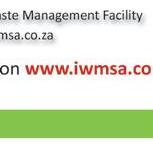
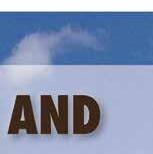
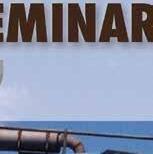
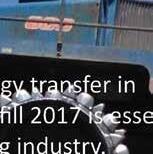
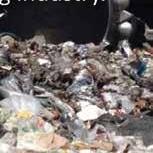
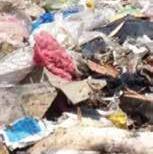
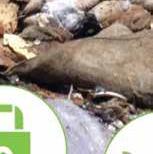
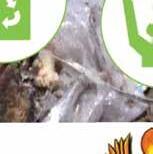

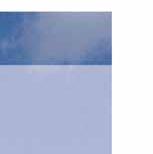
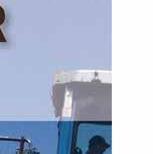
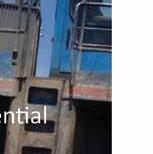
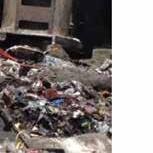
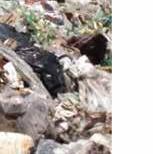
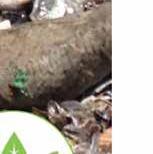
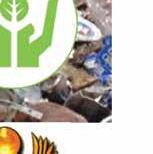
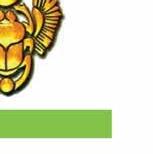
Recycled materials make green events stand out
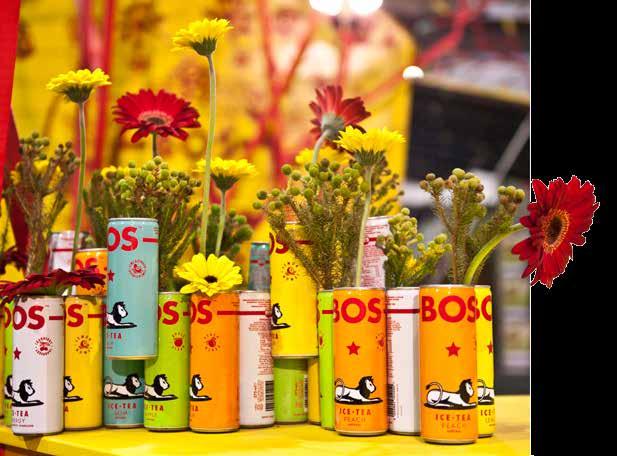
stemmed from his dismay at the huge amounts of waste produced by the events industry.
“I’ve been in the industry for 21 years and event greening is my passion. We follow the waste management hierarchy where we first concentrate on reducing, then reusing and recycling. But there are challenges concerning how you go about hosting a green event. If we were truly to ‘reduce’, we would not be holding this event today, no one would have burned fossil fuels driving here in their cars, and we would not need electricity to run the projector screen. So, sometimes we need to compromise,” says Hawes.
Trash
to treasure
On 24 May this year, Meetings magazine, sister publication to ReSource, hosted its successful Unboxing Series event at On Pointe in Fourways on turning trash into treasure. Renowned guest speakers shared their top tips for creating eco-friendly conferences and expos.
By Frances Ringwood
Meetings magazine’s Unboxing Series is the brainchild of editor Martin Hiller. The series is geared towards inspiring the meetings, conferencing and event planning communities to host gatherings that deliver the ‘wow’ factor when it comes to surprising, delighting and engaging guests.
“We started hosting these events in April with our Unboxing Social Media event at Avianto in Muldersdrift. I’m planning to host six per year on different themes, each one unpacking a practical element in the events industry. I really want these events to turn the industry on its head, forcing people to think differently,” says Hiller.
The “trash to treasure” concept focuses on creating a stylish event while still being green.
Guest speakers included Justin Hawes, one of the founders and current marketing head of the Event Greening Forum; Johann Els, director and the magic man behind Els Event Architects; and the award-winning exhibition designer Nicholas de Klerk, founder of Design and Display.
The event concluded with a practical workshop where participants formed teams, unpacked glue guns, box cutters and string from boxes, and
proceeded to turn recyclable materials such as plastic bottles, brown paper and plastic bags into table decorations. De Klerk judged the teams’ efforts and the winning team won a prize.
Holistic view
Hawes’ presentation was first in the line-up. He says that the idea behind the Event Greening Forum
Going green can save money but it can also be costly. Ultimately, prior to hosting an event, organisers need to look at the different avenues for going green, including energy efficiency and lighting, logistics and transport, the venue, biodiversity, socio-economic responsibility, procurement, catering, recycling, carbon offsetting, decor and waste management, among others.
“You might not be able to have a green event from every perspective but it’s important to plan around which elements you want to concentrate on,” says Hawes.
Hawes stresses that waste management can be one of the more costly elements to implement but it’s also one of the easiest areas in which to make a big difference. “What’s great about waste is that it’s such a high-visibility issue – you can really wow your guests by making your separation at source prominent by having visible recycling bins. If you are planning an event and can choose only one element to concentrate on, I would recommend concentrating on waste because of its high impact,” he says.
Local is lekker
The next speaker, Els, presented about the
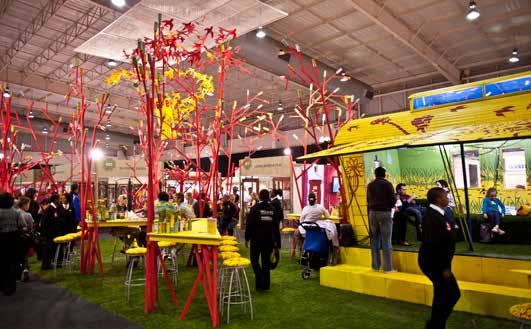
One of Nicholas de Klerk’s event stands created using wool, plastic icon cutouts and rolled cardboard
Top tips for hosting a successful green event
• When purchasing corporate gifts, used local labour and community upliftment initiatives
• Consider giving delegates vouchers for local craft markets, in place of corporate gifts
• Create expo stands with reusable elements
• Use fabric instead of vinyl for expo stands
• Minimise marketing collateral
• Use social media for event promotion
• Have one company business card with a website so old cards don’t need to be thrown away
• Use carbon offsetting, by planting trees or purchasing renewable energy in return for a certificate verifying the exchange
• Try to get exact numbers for catering to reduce food waste
• Prioritise overland transportation rather than airfreighting
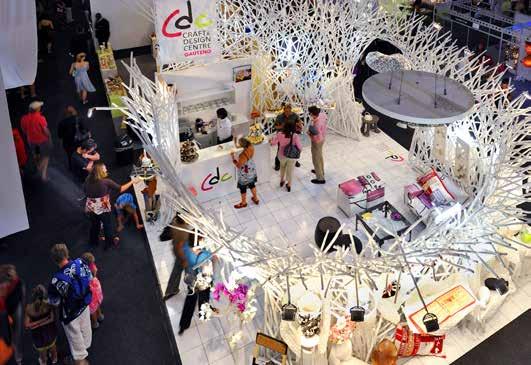
The venue
If you just look at how many flowers the events industry goes through and has to throw away, there is a real opportunity out there for someone to create a business around collecting and managing this waste.”
Johann Els, director of Els Event Architects
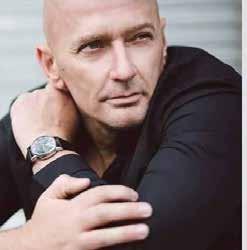
On Pointe in Fourways is a green venue. Its high roof and glass windows mean that daytime electricity use (and the associated carbon cost) is unnecessary. Wide doors and windows negate the need for air conditioning and heating, even on a cold winter’s day. Additionally, the venue’s neutral colours and decor make it highly versatile, so it can be used for anything from glamorous gala banquets to more serious “olde worlde”style gatherings. Capacity ranges between 230 and 400 guests, depending whether it’s a sit-down or more cocktailstyle function.
importance of minimising an event’s carbon footprint by buying local, emphasising the business opportunities that exist for service providers who assist in this regard. “If you look at how many flowers the events
for someone to create a business around col lecting and managing this waste using bokashi earthworms, for example,” he says.
“Another thing to bear in mind is that sourcing locally can reduce costs for both the events company and its clients. I recently provided services at the Nampo Conference in Bothaville where I bought all the flowers for the event at a local nursery. This saved the company from having to hire a vehicle to transport the flowers for three hours,” Else adds.
Artistic flair
De Klerk has been designing award-winning exhibition stands for events since 1975. He has designed stands for private companies as well as various South African government departments. Internationally, he has designed exhibitions and stands in Chile, China, England, Germany and the USA. In South Africa, he has designed stands
I just like to have fun – I don’t really work; I have fun and if I can leave the viewers of my work delighted, then I’ve accomplished what I set out to do.” Award-winning exhibition designer Nicholas de Klerk
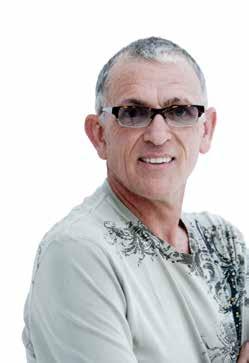
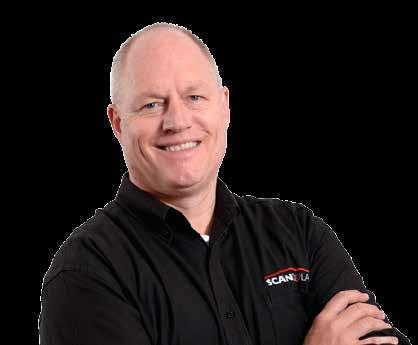
We follow the waste management hierarchy where we first concentrate on reducing, then reusing and recycling.” Justin Hawes, marketing head of the Event Greening Forum
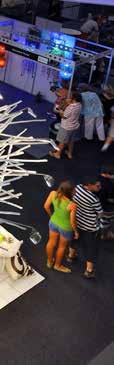
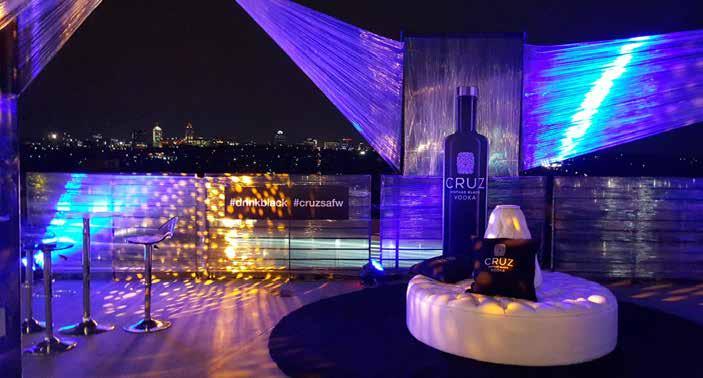
De Klerk uses recycled materials for his engaging exhibition and events décor, this cling film was re-recycled the next day by trolley pullers
for a vast range of industries, from mining to food, and is well known for his exhibitions for the Department of Arts and Culture.
His groundbreaking craft exhibition These Cool Things, for the Department of Arts and Culture at the Johannesburg World Summit on Sustainable Development, was well-received by local and international visitors, to the extent that De Klerk was invited to stage the exhibition at one of the Smithsonian Institution’s museums in Washington DC.
De Klerk uses recyclable materials such as bottles, crates and plastic items in his designs and has become known for his use of experimental materials. In June 2016, he presented the keynote address, Junk Talks to Me, at the International Federation of Events Service World Summit in Istanbul.
“Most of the material I use in my work is recycled. Sometimes I buy plastic but I always organise for it to be recycled afterwards. Above
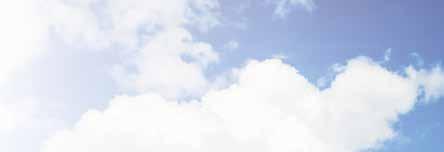
everything else, I look at the carbon footprint in design,” he explains.
The end-result of De Klerk’s designs is breath taking. He plays with light and shadows, developing concepts that become art. “I just like to have fun – I don’t really work; I have fun and if I can leave the viewers of my work delighted, then I’ve accomplished what I set out to do,” he says.
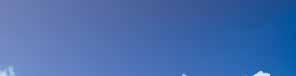

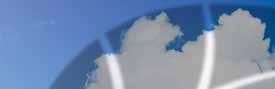
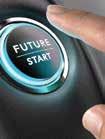
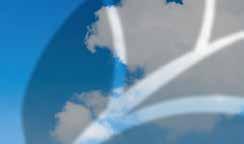
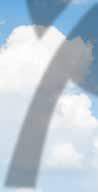
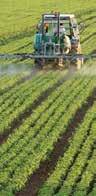





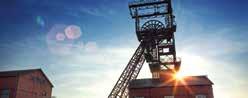



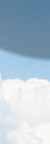







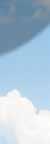



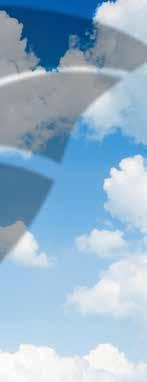
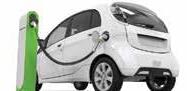
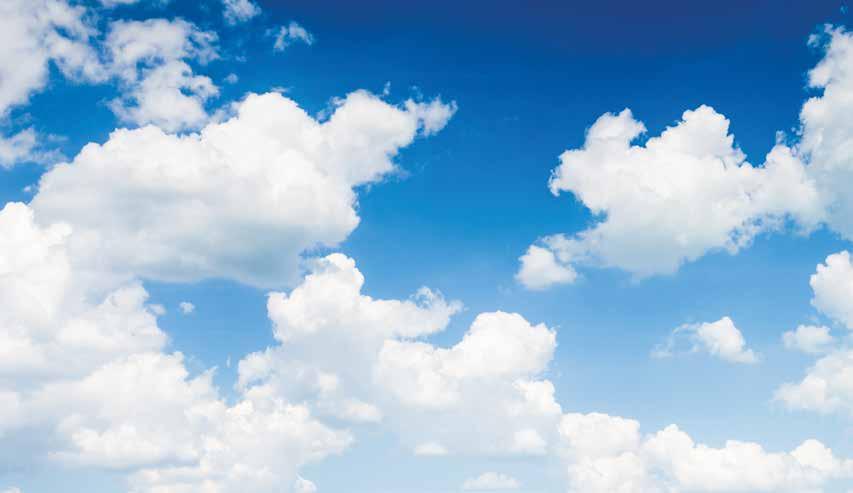

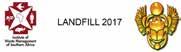
LANDFILL 2017 “BACK TO BASICS”
Date: 18–20 October
Venue: Buffelsdraai Regional Landfill, Verulam, eThekwini
Contact: Reshad Hassan at reshadh@kaytech.co.za
The KwaZulu-Natal Landfill & Waste Treatment Interest Group announces the twelfth biennial seminar dedicated to capacity building and technology transfer in the science and practice of waste treatment and disposal by landfill.
Landfill 2017 continues this highly successful series, and for the first time, it will be held on a major operational landfill. This will give landfill equipment suppliers an ideal opportunity to demonstrate their products in action, and the associated static exhibition will be a good showcase for organisations that have products and services to offer to the waste management fraternity.
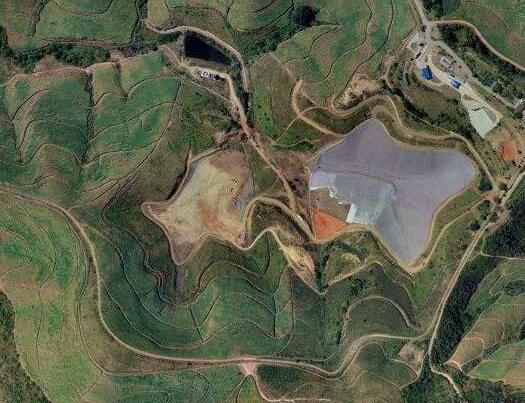
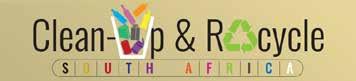
CLEAN-UP AND RECYCLE SA WEEK
Date: 11–17 September
FVarious clean-ups planned for neighbourhoods, water sources and beaches around the country
Contact: www.plasticsinfo.co.za
Clean-up and Recycle SA Week is an annual initiative by the local plastics industry, supported and endorsed by the various packaging streams and retailers. Each year, close to 120 000 volunteers participate in these clean-up activities. This year, one of the highlights of the event will be the 21st International Coastal Clean-up Day that will be taking place on Saturday, 16 September
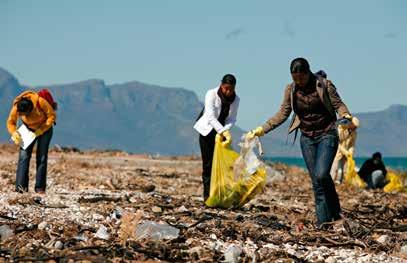
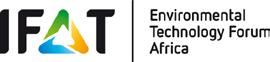
IFAT ENVIRONMENTAL TECHNOLOGY FORUM AFRICA
Date: 12–14 September
Venue: Johannesburg Expo Centre
Contact: Marius Smit on +27 (0)11 476 8093 or marius.smit@mmi-southafrica.co.za
The Internationale Fachmesse für Abwassertechnik (IFAT, translation: the International Trade Fair for Sewage Technology) started its journey in Munich, Germany, more than half a century ago. Since then, it has grown to incorporate water, recycling and other environmental technologies. It is held regularly at different locations around the world. This year, IFAT comes to South Africa’s shores for the second time, promising the same high-quality conference and expo experience that the name has come to represent.
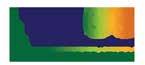
SOUTHERN AFRICAN ENERGY EFFICIENCY CONFEDERATION CONFERENCE
Date: 14–15 November
Venue: Emperors Palace
Contact: Christine Dunbar on +27 (0)63 235 8031 or admin@SAEE.org.za
The Southern African Energy Efficiency Confederation (SAEEC) is hosting the 12th SAEEC Conference to serve the energy management, environmental, facilities building upgrades, energy engineering, cogeneration, power generation and efficiency improvement industries. It is the one comprehensive forum where energy efficiency professionals see exactly how economic and market forces, new technologies, regulatory developments and industry trends merge to shape the critical decisions that shape industry’s energy and economic future.
Buffelsdraai Regional Landfill
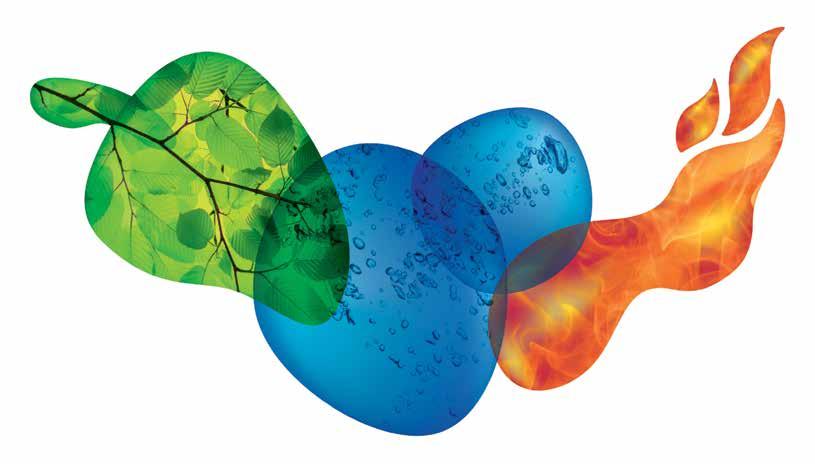
Be part of Africa’s Premier Environmental Technology Trade Fair.
Free entrance for online registrations www.ifat-africa.com/online-registration.php
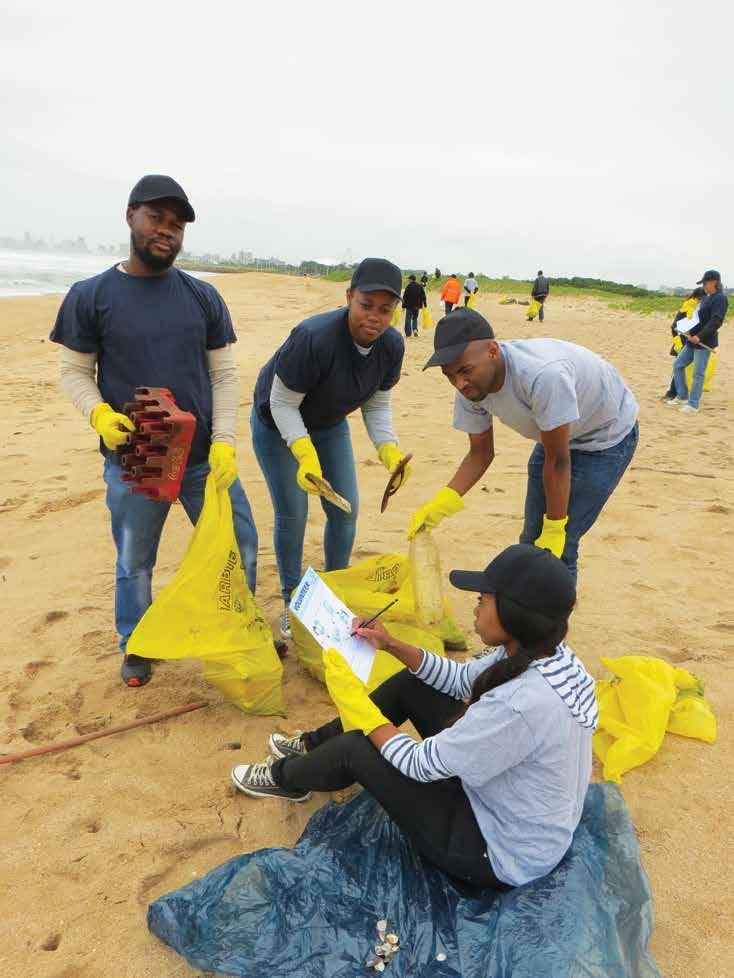
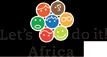



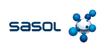
